
Новые процессы получения металла (металлургия железа)
..pdfPic. 58. Печь сопротивления |
Любатти: |
1 - футерованная чаша; 2 - |
кожух; 3 — смеситель шихты; 4 - питатель- 5 - |
трафитовые электроды; 6 - трансформатор; 7 - медные водоохлаждаемые мектрододержатели; о — колпак вытяжного устройства
зультате ее плавления в высокотемпературной зоне, граничашей со слоем шлака. Образующиеся капли металла проходят через слой шлака и накапливаются на подине печи.
Преимуществом способа Любатти является возможность по лучения металла с низким содержанием серы (0,01—0,03 %), благодаря интенсивному ее удалению во время нагрева, а также возможности десульфурации при прохождении капель металла через слой шлака. В этом процессе можно получать жидкий полупродукт, содержащий 1,3—2,8 % С. Регулируя тепловой и шлаковый режимы плавки, можно обеспечить се лективное извлечение железа при незначительном восстанов лении и переходе в металл Si, Мп и Р.
Недостатком процесса является отсутствие необходимых условий для дожигания выделяющегося при восстановлении газа, утилизации его тепла, высокий расход электроэнергии (2200-3225 кВт • ч/т в зависимости от условий плавки).
Процесс по второму варианту с погружением электродов не в шлак, а в рудно-угольную смесь осуществлен в лабо раторных условиях. Опыты показали, что благодаря выделяю щемуся газу в слое рудно-угольной смеси происходит интенсивное перемешивание частиц этого слоя, что обеспе чивает быстрый его нагрев, выравнивание температур в объеме слоя, облегчается подвод тепла к различным реак ционным участкам. Процесс характеризуется высокой произ водительностью и значительным колебанием состава получае мого жидкого металла (содержание углерода изменяется от
0,5 до 0,4 %). Известны и другие предположения по осу ществлению подобных процессов, которые,однако,не вышли из
стадии |
лабораторного |
опробования. |
|
Все |
рассмотренные |
процессы, основанные |
на использова |
нии рудно-угольных |
смесей, имеют общий |
недостаток - в |
разных участках слоя практически невозможно обеспечить одинаковое соотношение частиц руды и твердого восстанови теля. Это приводит к неравномерности развития восстанови тельного процесса в объеме слоя и, соответственно, тре бует подвода разного количества тепла. Осуществить это в реальных условиях не представляется возможным.
Задача облегчается при использовании рудно-топливных окускованных материалов, в которых при соответствующей подготовке содержание окбидов железа и твердого углерода
вобъеме практически одинаковое.
Вэтом случае потребление тепла при развитии эндотер мических реакций прямого восстановления будет локализо ваться объемами рудно-топливных окатышей или брикетов. Причем подводимое тепло будет обеспечивать развитие реак ций прямого восстановления уже при таких температурах, которые значительно ниже температур плавления руды и золы топлива. В связи с этим особый интерес представляют одно стадийные высокотемпературные процессы прямого получения жидкого металла, основанные на использовании рудно угольных окатышей или брикетов. Такой процесс предложен в
нашей стране и осуществлен в качающейся отражательной регенеративной печи с кипящим шлаковым слоем. Он получил название КШС-процесс (рис. 59).
Для получения рудно-топливных окатышей можно использо вать тонкоизмельченные рудные материалы (руда, концент рат, окалина) в количестве 72—76 %, а также твердые
восстановители (уголь, антрацит, полукокс и |
кокс) - |
20—22%. В качестве связующего— каменно-угольный |
пек в |
количестве 4—5 % от всей массы шихты. На грануляторе получают сырые окатыши размером 20—30 мм, которые затем подвергают сушке при 100—250 °С в течение 5—8 ч.
Подготовительные окатыши непрерывно загружают в печь на поверхность расплавленного шлака (1500—1650 °С). Ока тыши, имеющие объемную массу 2,44—2,48г/смэ, частично погружаются в толщу шлака, где происходит их восстановле ние, которое практически завершается к моменту расплавле282
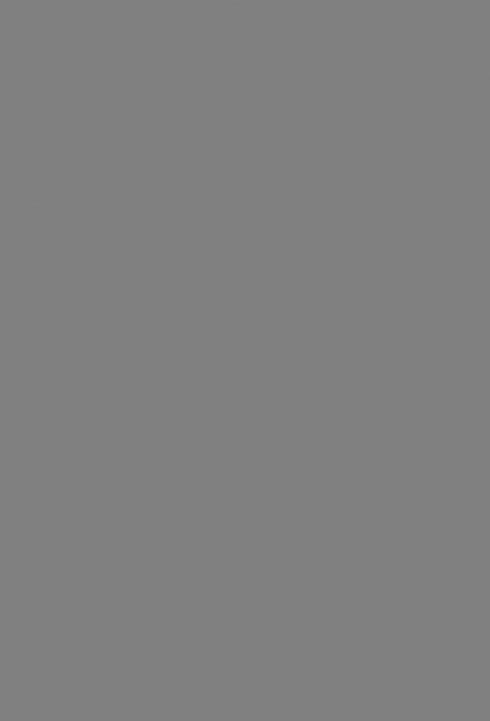
Процесс КШС можно осуществлять по различным схемам: в одной качающейся отражательной печи, где накопленный в ванне металл в последующем доводится до марочной стали и частично выпускается (монопроцесс), либо в отражательной печи получают жидкий полупродукт с контролируемым содер жанием углерода, а доводка металла проводится в электро печи (двухстадийный процесс). Во втором случае операцию перелива полупродукта в электропечь можно сопровождать десульфурацией металла синтетическими шлаками. Удельная
производительность |
|
процесса |
КШС |
составляет |
|
3,2—4,9т/(м2 • сут), |
а |
при |
использовании |
кислорода |
|
(270—-400м3/т) она |
возрастает |
до 4,5—5,5т/(м2 • сут). |
Преимуществом процесса КШС является возможность непре рывного контроля и регулирования технологических парамет ров и получения металла с низким содержанием Si; Mn; Р, примесей цветных металлов и газов. Недостатком процесса является повышенное содержание серы в получаемом продукте (0,058—0,076 %), что требует дополнительной обработки ме талла с целью его десульфурации, а также большие потери железа со шлаком. Аналогичные процессы разрабатываются во многих странах.
Они обладают рядом преимуществ по сравнению с ранее рассмотренными процессами. Для сравнения в табл. 30 при ведены основные показатели процессов, осуществляемых в трубчатых вращающихся печах, во вращающемся конвертере и отражательных печах. Как следует, в агрегатах последнего типа восстановление протекает с большей скоростью при меньших затратах угля, топлива и кислорода.
Одностадийные способы, осуществляемые по схеме плавление—восстановление
Процессы этого типа включают предварительное плавление железорудных материалов с последующим восстановлением оксидов железа из расплава. В качестве восстановителя мо гут быть использованы газы (СО, Н2, СН4), твердый угле род, вдуваемый в расплав, или углерод, растворенный в ме таллической ванне. Основной предпосылкой для разработки таких процессов являлось стремление увеличить скорость восстановления оксидов железа, а следовательно, и произво дительность процессов прямого получения жидкого металла. 284
Т а б л и ц а 30. Основные показатели высокотемпературных
восстановител и ыж процессов
Процесс |
Тип |
Про- |
Проиэво- |
Расход на 1 т продукта |
|||
|
шихты |
дукт |
дитсль- |
|
|
|
|
|
|
|
ность, |
угля, |
газа, |
кисло |
тепла, |
|
|
|
т/(м3х |
КГ |
м3 |
рода, |
МДж |
|
|
|
ХСут) |
|
|
м3 |
|
|
|
Вращающиеся трубчатые печи |
|
|
|||
Бассе |
Рудно- |
Чугун |
0,6—0,9 |
610 |
360* |
|
29,31 |
|
уголь |
|
|
|
|
|
|
|
ная |
|
|
|
|
|
|
|
смесь |
|
|
|
|
|
|
Штюр- |
Рудно- |
То же |
0,9-1,3 |
1500- |
|
37,68+41,87 |
|
цель- |
уголь |
|
|
2000*’ |
|
|
|
берг |
ная |
|
|
|
|
|
|
|
смесь |
|
|
|
|
|
|
Азинкур |
Рудно |
— " — |
0,8 |
Нет св. |
Нет св. |
|
Нет св. |
|
уголь |
|
|
|
|
|
|
|
ная |
|
|
|
|
|
|
|
смесь |
|
|
|
|
|
|
|
|
|
Вращающийся конвертер |
|
|
||
Доред |
Рудно- |
Чугун |
3-5 |
490-737 |
|
415-724 |
Нет св. |
|
уголь |
|
|
|
|
|
|
|
ная |
|
|
|
|
|
|
|
смесь |
|
|
|
|
|
|
|
|
|
Отражательная печь |
|
|
|
|
кшс |
Рудно- |
Сталь |
3—5 |
432 |
279 |
122 |
22,4 |
|
уголь- |
полупро- |
|
319 кг |
|
|
|
|
ные |
дукт |
|
|
мазута |
|
|
окатыши
w *Мазут, кг/т. **Общий расход угля на восстановление и отопление печи. Производительность, т/(м* • сут).
Однако сложность технологической разработки процессов такого типа, отсутствие огнеупорных материалов, способных надежно работать при воздействии на них агрессивных желе зистых шлаков, сдерживают до настоящего времени их опро бование в промышленных условиях. Большинство предложенных процессов опробованы лишь в лабораторных установках.
В 50-е годы в США и нашей стране одновременно были проведены полупромышленные эксперименты по осуществлению процессов, заключающихся в последовательном расплавлении руды и восстановлении оксидов железа и других металлов из рудного или рудно-флюсового расплава вдуваемым твердым углеродом.
Врезультате недостаточно интенсивного подвода тепла в зону реакции восстановление сопровождалось резким вспени ванием расплава и снижением скорости восстановительного процесса особенно на заключительной стадии, когда содер жание FeO в расплаве достигало уровня <10% . Последнее объясняется низкой скоростью подвода реагентов в зону реакции.
ВШвеции опробован на опытном реакторе процесс, осно
ванный на восстановлении оксидов железа из расплава углеродом, растворенным в металлической ванне (рис. 60).
Ряс. 60. Схема реактора для восстановле ния жидких оксидов железа растворенным в металле углеродом:
1 — питатель с быстровращающимся диском;
2 — зона горения; 3 — отходящие газы;
4 —водоохлаждаемые сопла для подачи ма зута или газа; 5 — кислородные фурмы
В качестве топлива-восстановителя можно применять природ ный газ, тонкоизмельченный уголь или мазут, которые непрерывно вдувают в ванну. Здесь происходит их разложе
ние, |
образующийся углерод усваивается металлом, за счет |
чего |
содержание углерода в нем поддерживается на уровне |
3,5 %. Выделяющийся водород, барботируя через расплав, перемешивает его и также участвует в восстановлении. Однако в основном восстановление оксидов железа из расп лава осуществляется прямым путем за счет углерода ванны.
Таким образом, процесс основывается на одновременном протекании реакций:
С™ = [С];
286
FemОHJB - (FetnОn);
(FemO„) + л[С] = mFe* + ttCO.
Монооксид углерода, образующийся при восстановлении, и водород от разложения вдуваемого топлива дожигается непосредственно над ванной в токе кислорода. Кислород вдувают так, чтобы зона высоких температур (~ 2500 °С) была расположена возможно ближе к поверхности ванны, тем
пература |
которой составляет ~ 1350 °С. |
Отходящие |
от |
реак |
||
тора |
газы |
содержат в |
основном С02, их температура дости |
|||
гает |
1500 °С. Благодаря |
окислительной |
атмосфере |
над |
ван |
ной восстановление Si, Мп и Р не происходит.
Загрузка концентрата в реактор осуществляется спе циальным питателем с быстро вращающимся диском. С его по мощью концентрат отбрасывается к стенкам реактора, где направление его потока изменяется с горизонтального на вертикальный. В результате вдоль стен по окружности реак тора образуется вертикальный поток концентрата, отделяю щий огнеупорную кладку от внутренней высокотемпературной зоны. В связи с этим температура футеровки не превышает температуры нагреваемого концентрата. В потоке концентрат
нагревается и плавится прежде, чем |
достигает ванны. |
Ме |
талл и шлак выпускают из реактора |
в виде эмульсии, |
так |
как в условиях интенсивного кипения ванны их разделение в реакторе невозможно.
Преимуществом процесса является высокая теплоотдача от факела к ванне, возможность получения металла с низким содержанием Si, Мп и Р. Недостатком— необходимость внепечной обработки металла с целью его десульфурации.
Аналогичный процесс восстановления железа из расплава растворенным в металле углеродом осуществлен в индукцион
ной печи |
(рис. 61). Индукционная |
печь |
состоит |
из двух |
|
секций 1 и |
2, которые сообщаются |
между |
собой |
каналами 3. |
|
В секции 1 металл науглероживается (до 4% С) |
и |
в резуль |
|||
тате электромагнитного перемешивания поступает по |
каналам |
в секцию 2, где углерод металла расходуется на восстанов ление оксидов железа из расплава. Выделяющийся монооксид углерода используется для нагрева и частичного восстанов ления руды в трубчатой вращающейся печи 5. Регулируя по дачу угля в секцию 1, можно получать металл с различным
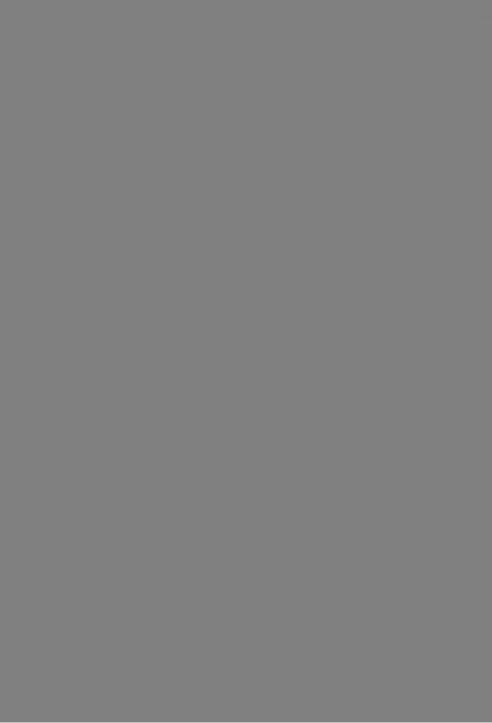
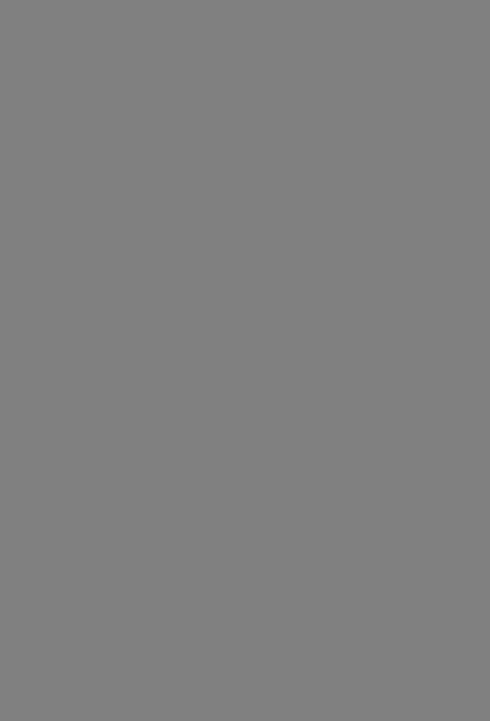
говую электропечь с закрытой дугой либо ВЧ— индукционную электропечь.
В верхнюю камеру сверху по периферии подается концент
рат, |
уголь и известняк, а по окружности тангениально че |
|
рез |
фурмы вдувается технический кислород. За счет сгора |
|
ния |
части угля в |
камере достигается температура порядка |
1900 °С. Происходит |
плавление и частичное восстановление |
окислов железа (до FeO). Оставшийся уголь частично кок суется и вместе с расплавом, содержащим FeO, поступает в нижнюю камеру. Здесь накапливаются чугун и шлак, на по верхности которых образуются слои кокса и губчатого желе за, так как расплавленный монооксид железа при контакте с
коксом |
восстанавливается с понижением температуры до |
1450 °С |
с образованием губчатого железа. |
Горение угля в верхней камере регулируется таким обра зом, чтобы получалось достаточное количество кокса для обеспечения процесса восстановления. Образование чугуна происходит при плавлении губчатого железа вокруг электро дов в дуговой печи, либо за счет нагрева в индукционной электропечи.
Чугун и шлак выпускаются из печи периодически по мере
накопления. Содержание углерода |
в |
чугуне |
составляет |
|||||
~ 3,5 % |
и зависит от высоты |
слоя образовавшегося |
кокса в |
|||||
нижней |
камере. Содержание |
Si |
(~ 1 %) |
|
также |
может |
регули |
|
роваться высотой слоя кокса |
и |
температурой |
в |
печи. Около |
||||
80 % S, поступающей с концентратом |
и |
углем, |
удаляется в |
|||||
виде S02 с отходящими газами. Оставшаяся сера распреде |
||||||||
ляется между шлаком и чугуном (коэффициент |
распределения |
|||||||
~ 25 при содержании железа |
в |
шлаке |
< 1 %). Вместе |
с серой |
с отходящими газами удаляются мышьяк, свинец, цинк, щелочные металлы и частично фосфор. Отходящие газы посту пают в бойлер, в котором вырабатывают пар, используемый в паровой турбине, которая обеспечивает работу компрессора установки для получения кислорода и электрогенератора плавильной печи.
Преимуществами процесса Инред являются: быстрая, с вы соким к.п.д., передача тепла нагреваемым материалам, воз можность использования сернистых углей с высоким содержа нием золы и бедных железорудных материалов. Однако этот
процесс не |
исключает |
двухстадийности при производстве |
стали, что и |
является его |
главным недостатком. |