
Управление техногенными отходами
..pdfи для их извлечения необходимо применять дорогие реагенты [49]. Пирометаллургические способы извлечения цветных металлов из шлаков основаны на восстановлении оксидов углем, коксом, карбидом кальция, чугуном, природным газом и другими материалами. При этом расходуется значительное количество энергоресурсов, а аппаратурное оформление процесса сложно и дорого, в результате чего эти способы не всегда эффективны [4].
Переработка шлаков цветной металлургии на песок и щебень после извлечения ценных металлов представляется наиболее оптимальным путем решения проблемы их утилизации, поскольку потребность в песке и щебне (гравии) очень велика.
С использованием вяжущего из шлаков цветной металлургии при автоклавном твердении можно получать бетоны. По физикохимическим свойствам бетоны автоклавного твердения на вяжущих из гранулированных шлаков цветной металлургии мало чем отличаются от автоклавных бетонов на клинкерных цементах и могут быть применены при изготовлении бетонных и железобетонных изделий практически всей номенклатуры [43].
В связи с тем что доменные шлаки содержат соединения фосфора, кальция, магния, различные микроэлементы, их используют для производства минеральных (в частности фосфатных) удобрений в форме муки [4]. Так, например, измельченные сталеплавильные шлаки после магнитной сепарации металла содержат до 12 % фосфорного ангидрита [8]. Представляет интерес использование в качестве удобрений гранулированных шлаков, так как такое удобрение будет разлагаться в почве в течение 10–15 лет, передавая все это время растениям необходимые питательные вещества. Такие гранулы не пылят, не слеживаются и не смерзаются, а потому их можно вносить в почву и летом, и зимой. Стоимость гранулированного шлака ниже стоимости муки [4]. Однако здесь следует обратить внимание на то, чтобы в таких шлаках не содержались канцерогенные вещества и особенно диоксиноподобные вещества. Поэтому при использовании шлаков всех видов необходимо знать предысторию и экогеографию добычи исходного топлива, которое служит сырьем для получения шлака [48].
301
Шламы черной металлургии
Железосодержащие пыли и шламы составляют до 75 % всех отходов данного передела. Выход железосодержащих пылей и шламов составляет 100–350 кг/т стали [8].
Основными характеристиками шламов являются химический и гранулометрический состав, однако при подготовке шламов к утилизации необходимо знать такие параметры, как плотность, влажность, удельный выход и др. Шламы – тонокодисперсный материал (около половины массы приходится на частицы размером от 0,016 до 0,032 мм и лишь порядка 10 % – на частицы крупнее – 0,063 мм). Содержание полуторных оксидов железа составляет от 30 до 50 %, оксида алюминия – от 1 до 30 %, оксида кремния – от 6 до 12 %, сумма оксидов кальция и магния – от 6,5 до 10,5 %. Содержание общего углерода изменяется в очень широких преде-
лах – от 2,5 до 30 %.
В настоящее время эти шламы используются в основном как добавка к агломерационной шихте (аглошихте). Сравнительно низкий уровень их использования (порядка 10–20 %, в отдельных производствах – до 80 %) объясняется относительно невысокой долей железа в них, а также повышенным содержанием цинка в шламах доменных газоочисток (более 1 %), что требует предварительного обесцинкования шламов [18]. Обесцинкование шламов может проводиться как пиро-, так и гидрометаллургическими способами. При содержании в шламах цинка > 12 % они могут использоваться как сырье для его получения [24].
Шламы, прежде чем их использовать (например в качестве компонента шихты), необходимо подвергнуть обезвоживанию (сгущению, фильтрованию, сушке). Сгущение – процесс повышения концентрации твердой фазы в сгущаемом продукте (шламе), протекающий под действием гравитационных и (или) центробежных сил. Поскольку количество воды в сгущенном продукте составляет 30–60 %, то использовать такой обводненный материал в качестве добавки к аглошихте или окомковывать его с целью получения окатышей практически невозможно, поэтому сгущенный продукт необходимо профильтровать, чтобы содержание влаги
302
в нем снизить до 8–10 %. При фильтровании шламов происходит процесс разделения жидкого и твердого под действием разрежения или давления, сопровождающийся удалением влаги через пористую перегородку (обычно фильтровую ткань и частично осадок). Нафильтрование обычно подают шламы, частицы которых имеют размер < 1 мм, так как обезвоживать такие дисперсные системы другими методами нецелесообразно из-за малой скорости удаления влаги и, как следствие, значительнойвлажности получаемогоосадка[24].
Пыли черной металлургии
Пыли металлургического производства обычно не требуют какой-либо предварительной подготовки перед утилизацией. Так, уловленная в газоочистках пыль ферросплавных печей после брикетирования возвращается в основное производство. Желательно, чтобы все пыли, улавливаемые всевозможными способами, полностью утилизировались в процессах производства целевых продуктов. Так, из мировой практики известно, что в ряде стран Европы пыль из рукавных фильтров ферросплавных печей используется для выплавки углеродистого ферромарганца [8, 24, 48].
Стружка и окалина
Металлическая стружка – отходы, образующиеся при резке металла. Переработка стружки заключается в ее очистке от посторонних примесей и кусков металла, промывке от масла и смазочноохлаждающих жидкостей и брикетировании с помощью брикетировочных прессов. Стружку высоколегированных сталей перед брикетированием необходимо отжечь для снижения прочности [4]. Существует также способ горячей штамповки стружки (при Т = 1000– 1200 °С), позволяющий получать монолитные детали, не требующие дальнейшей обработки. Кроме того, металлическая стружка после механической обработки является хорошим материалом для приготовления шихты. При этом количественное содержание отходов, вводимых в плавку, не должно превышать 35–40 % от общей массы шихты (во избежание повышения газонасыщенности металла и увеличения содержания в нем окислов) [48].
303
Лом и крупнокусковые отходы от обработки металлов
Лом и отходы черных, цветных и редких металлов образуются в том числе при производстве металлов (45 % от всех объемов данной категории отходов) и обработке заготовок и деталей (20 % от всех объемов данной категории отходов). Это наиболее ценный из всех видов отходов, поскольку является конечным продуктом сложных технологий и содержит максимальную долю овеществленного труда. Наиболее логичный способ утилизации этих отходов – использование в материнских металлургических процессах. Использование черного металлолома резко снижает расход других шихтовых материалов, уменьшает энерго- и трудозатраты и увеличивает выход металла из печи. При этом себестоимость металла снижается за счет исключения затрат на осуществление предшествующих операций подготовки сырья и выплавки металла. В целом капиталоемкость получения металла из вторсырья на порядок ниже, чем из руд. Экономия энергии при производстве металлов приобретает особое значение в условиях энергетического кризиса, поскольку большинство металлов получают с использованием энергоемких пирометаллургических или электрохимических процессов. За счет использования металлолома она составляет (%): при получении алю-
миния– 94, меди– 83, цинка– 78, стали – 74, свинца – 64 [4, 49].
Взавершение данного пункта следует подчеркнуть теснейшую связь комплексного использования сырья с безотходной технологией. Более полное и комплексное извлечение ценных компонентов из сырья имеет первостепенное значение. При этом одним из эффективных путей решения проблемы комплексного использования сырья служит организация комбинированных производств [43].
6.3.Управление отходами энергетики
Вмировом масштабе более 80 % тепловой и электрической энергии получают путем сжигания органического топлива и превращения его химической энергии в тепловую и электрическую [8]. Работа электроэнергетических предприятий представляет собой процесс сжигания топлива, выработки и транспортировки электрической энергии от генерирующих источников к потребителям. Со-
304
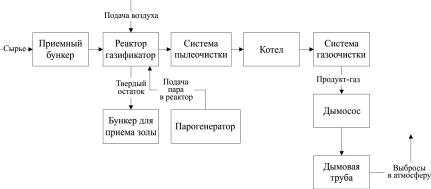
ответственно, к основным отходам энергетики относятся золошлаковые отходы от сжигания твердого топлива и отработанные трансформаторные масла. На рис. 6.3 представлена технологическая схема работы реактора-газификатора с образованием золы.
Рис. 6.3. Технологическая схема работы реактора-газификатора [50]
Отработанные трансформаторные масла либо утилизируют, либо регенерируют. После очистки или регенерационной переработки из отработанных масел получают либо трансформаторное масло для дальнейшего использования, либо другие виды машинного масла: автомобильные масла, гидравлические, различные виды смазок [24]. В дальнейшем в данном пункте будут рассмотрены вопросы обращения только с золошлаковыми отходами.
Количество образующихся золошлаковых отходов зависит от вида топлива и составляет: для природного газа – менее 0,01 %, для мазута – 0,2 %, для дров – 0,5–1,5 %, для торфа – от 2 до 30 %, для каменного угля – от 3 до 30 %, для бурого угля – от 10 до 15 %, для горючих сланцев – от 50 до 80 %.
Внастоящее время на большинстве ТЭЦ топливо сжигают
впылевидном состоянии при температурах 1200–1600 °С. При этом конгломераты различных соединений, образующихся из минеральной части твердого топлива, выделяются в виде пылевидной массы. Мелкие и легкие частицы (размером от 0,005 до 0,1 мм), содержа-
305
щиеся в золе в количестве до 80–85 %, уносятся из топок конгломератов дымовыми газами, образуя так называемую золу-унос. Более крупные частицы оседают в топках, оплавляются в кусковые шлаки или спекаются в стекловидную, достаточно прочную массу.
Зола-унос представляет собой тонкодисперсный материал с малым размером частиц, что позволяет использовать ее для ряда производств без дополнительного помола. Характерной особенностью золы является присутствие в ней около 5–6 % несгоревшего топлива (в пересчете на углерод). Зола-унос чувствительна к влаге, имеет кислую реакцию.
Топливные шлаки, напротив, отличаются почти полным выгоранием углерода топлива и присутствием железа преимущественно в закисной форме. Частицы шлака имеют размеры от 0,2 до 20– 30 мм. По аналогии с металлургическими топливные шлаки можно разделить на кислые, нейтральные и основные. Большинство топливных шлаков относится к классу кислых или нейтральных, в которых велика доля SiO2 и Al2O3. Шлаки каменных углей отечественных месторождений большей частью являются кислыми. К основным шлакам, содержащим повышенное количество закиси железа и до 40 % СаО и MgO, относятся шлаки некоторых бурых углей и сланцев [43].
Топливные шлаки и зола-унос различаются по составу и свойствам в зависимости от вида топлива и способа его сжигания. Усредненный химический состав золошлаковых отходов следую-
щий: от 45 до 85 % – SiО2, до 25–35 % – А12О3, от 6 до 15 % – Fe2О3,
от 3 до 20 % – СаО, до 2,5–3,0 % – MgO, до 4 % – оксиды щелочных металлов и другие вещества (соединения титана, ванадия, германия, галлия, серы и урана) [3, 43, 48].
Количественное соотношение между образующимися шлаками и золой-уносом различно, оно зависит от конструкции топки на ТЭЦ и ГРЭС. Так, в топках с твердым шлакоудалением в шлак обычно переходит 10–20 % всей золы топлива, в топках с жидким шлакоудалением – 20–40 %, в циклонных топках – до 85–90 % всей золы топлива. В топках с жидким шлакоудалением шлак по-
306
лучается в гранулированном виде. Для него характерна стекловидная структура.
Основным способом удаления золошлаковых отходов предприятий теплоэнергетики является их складирование в отвалах (в том числе в гидрозолоотвалах, куда они транспортируются в виде пульпы системами гидрозолоудаления). Однако это приводит к большим потерям земельных ресурсов; так, например, только за одни сутки работы ТЭЦ средней мощности (1 млн кВт) образуется 1000 т шлака и золы. Складирование отходов в отвалах вследствие их раздувания и размывания приводит к загрязнению водного и воздушного бассейнов. Существует опасность необратимого радиационного загрязнения биосферы вследствие распыления золы ТЭЦ при хранении в отвалах, поскольку при сгорании угля в золе остаются радиоизотопы уран-радиевого и ториевого рядов, содержащиеся в исходном угле. Они не разбавлены массой углерода, т.е. находятся в концентрированном, а следовательно, в более опасном виде [43]; при этом радиационный фон на золошлакоотвалах может достигать 20 микрорентген в час [49]. Перемещение золошлаковых отходов в отвалы требует очень больших финансовых затрат, не принося при этом никакой прибыли. Кроме того, при гидравлическом способе удаления золы и шлаков (а именно этот способ остается пока доминирующим на современных ТЭС) весьма значителен расход воды, загрязняемой в процессе удаления золы (до 30–40 м3/т отхода). Вода после контакта с золой имеет рН выше 10, содержит фтор, мышьяк и ванадий в концентрациях, превышающих предельно допустимые [5].
Всего на ТЭС России ежегодно накапливается более 50 млн т золошлаковых отходов [3]. Объем топливных шлаков и зол за предыдущие 30–40 лет непрерывно уменьшался из-за перевода большинства крупных ТЭС и ТЭЦ с торфа, угля и мазута на газ, однако проблема их утилизации остается актуальной из-за необходимости утилизировать старые запасы, накопившиеся за более ранний период. К тому же в последние годы из-за стремительного роста цен на газ наблюдается тенденция возвращения к использованию в энерге-
307
тике твердых и жидких топлив, что приведет к возобновлению роста шлаковых и золовых отвалов [49].
Между тем золы и шлаки ТЭЦ при правильном и эффективном их использовании представляют собой богатый источник расширения сырьевых ресурсов различных отраслей народного хозяйства, в первую очередь промышленности строительных материалов [43]. Западные страны, где очень развит промышленный симбиоз, используют около 70 % образующихся золошлаковых отходов (ЗШО). В Польше очень высоки цены на землю, отводимую под золоотвалы, поэтому ТЭС доплачивают потребителям золы для снижения затрат на ее хранение. В Великобритании и Германии действуют специализированные фабрики по сбыту золы и шлаков [8].
Основная масса используемой части шлаков и зол служит сырьем для производства строительных материалов.
Так, золу ТЭС используют для производства искусственных пористых заполнителей – зольного и аглопоритового гравия, получаемых путем агломерации (гранулирования) и обжига исходного вещества. Возможно использование зол ТЭС и для производства керамзитового гравия.
Золы и шлаки, содержащие не более 5 % частиц несгоревшего топлива, могут использоваться для производства силикатного кирпича в качестве вяжущего (при содержании в них оксида кальция в количестве не менее 20 %) или заполнителя (при содержании в них оксида кальция в количестве не более 5 %).
Золы с высоким содержанием частиц угля с успехом используются для производства глиняного (красного) кирпича (зола в этом случае играет роль отощающей или топливной добавки).
Кислые золошлаковые отходы (а также основные с содержанием свободной извести менее 10 %) используют как активную минеральную добавку при производстве цемента (содержание горючих веществ не должно превышать 5 %). Эти же отходы можно использовать в качестве гидравлической добавки к цементу. В общем случае замена песка в цементных смесях золой ТЭС ускоряет твер-
308
дение этих смесей. В ФРГ 80 % промышленных зданий сооружено с использованием золы ТЭС.
Золу с содержанием свободной негашеной извести не более 3 % используют для замены части цемента в процессе приготовления различных бетонов.
При производстве ячеистых бетонов автоклавного твердения
вкачестве вяжущего используют сланцевую золу (содержание негашеной извести более 14 %), а в качестве кремнеземистого компонента – золу сжигания углей (содержание горючих менее 5 %). Так, использование золы ТЭС в производстве ячеистых бетонов снижает массу стеновых панелей в 2–4 раза. В настоящее время более 2 млн т/г. золы ТЭС используют в мировой практике для производства ячеистых бетонов.
Использование золошлаковых отходов по указанным направлениям не только является экономически выгодным (вследствие сокращения потребления гипсового камня, песка, цемента, извести, топлива), но и позволяет повысить качество соответствующих изделий.
Золошлаковые отходы используются в дорожном строительстве, в частности, кусковой шлак используют как заполнитель для бетона. Зола-унос может применяться при строительстве автомобильных дорог для укрепления грунтов. Золу также используют
вкачестве инертного наполнителя в асфальтах.
Нелетучая зола может использоваться в гранулированном виде в дорожном строительстве для изготовления основания участков парковки автомобилей, велосипедных дорожек, дорог, набережных. Ее можно применять в качестве покрытия на полигонах ТКО.
Золошлаковые отходы служат хорошим сырьем для производства минераловатных изделий, а также используются в качестве теплоизоляционной засыпки.
Топливные шлаки жидкого удаления можно использовать
впроизводстве отделочной керамической плитки: при содержании
всмеси до 30 % шлаков плитка имеет отличные физико-механичес- кие свойства и хороший внешний вид.
Большие возможности утилизации золы связаны с ее сорбци-
онными свойствами. По составу зола близка к неорганическим
309
катионообменникам – цеолитам. Несгоревшие частицы угля, присутствующие в золе, также являются активным адсорбентом по отношению к органическим малодиссоциирующим веществам. Благодаря этим свойствам золу можно применять для очистки слабозагрязненных сточных вод [4, 8, 51].
В последние годы все большее значение приобретает изготовление на основе топливных зол и шлаков таких материалов, как золоситаллы и шлакоситаллы.
Зола углей содержит практически все металлы. В ряде случаев концентрации металлов в золе таковы, что становится экономически выгодным их извлечение. В.Е. Лотош приводит данные, согласно которым в золе, образовавшейся от сжигания 1 т угля,
всреднем содержится 0,2 кг Zn, 0,7 кг Ni, 0,3 кг Со, 0,2 кг Sn, 0,5 кг Ge, 0,1 кг Pb, 0,3 кг Be [3]. Содержание урана в золе бурых углей некоторых месторождений может достигать 1 кг/т. В связи с этим извлечение металлов является еще одним направлением переработки таких отходов. Из золы некоторых углей в настоящее время извлекают редкие и рассеянные элементы (германий, галлий), из золы мазутов – ванадий, никель. Кроме того, в настоящее время считается возможным извлечение из зол углей U, Mo, Pb, Zn, Ba, Au, Be, Ag, Fe и других металлов. Причем их стоимость значительно превышает стоимость самого угля [46].
Исследования показывают, что применение золы в сельском хозяйстве улучшает агрофизические свойства почвы, пополняет ее микро- и макроэлементный состав (зола содержит значительные количества калия и фосфора, а также такие микроэлементы, как B, Mo и др.), нейтрализует кислотность (ввиду высокого содержания СаО в золе сланцев и торфа). В связи с тем что шлаки также содержат соединения фосфора, кальция, магния, различные микроэлементы, их используют для производства минеральных удобрений
вформе муки [8, 51]. При этом основным препятствием для применения золошлаковых отходов в сельском хозяйстве является их потенциальная радиоактивность и высокое содержание загрязняющих примесей [8].
310