
Актуальные проблемы повышения эффективности и безопасности эксплуат
..pdfWITH RESPECT TO HARDNESS DISPERSION OF THE PIPELINE STEELS DEPENDING ON THE LOAD VALUE DURING MEASUREMENT
V.I. Bolobov, M.N. Nazarova, A.V. Kasyanov
Saint-Petersburg Mining University, Saint-Petersburg, Russia
Recently, as a method of nondestructive testing of the condition of long-operated main gas and oil pipelines have found a use method for the assessment of damage by increasing the degree of hardness dispersion (σ2) of the pipeline materials. However, there are no evidence-based recommendations on the choice of the magnitude of the applied load (P) in the measurement of hardness.
When using the test samples of steel grades and Ст3Гсп and 17ГС it was found that in the case of measuring hardness with a slight stress on the metal (HV0.1, HV0.01) values of the hardness dispersion for the test samples of both steels are several orders of magnitude exceed the values set under heavy loads (HRB, HV10, HV5). The resulting difference in magnitude σ2 was explained by the ratio of the size of the fingerprint is obtained by measuring the hardness and grain size of the structural components of steels that was set by microstructural analysis.
It is concluded that the magnitude of the hardness dispersion that was set by low loads (HV0.1 and HV0.01) is determined by the value of this parameter for individual structural components of these steels and the location of the measuring point of microhardness in the structure that does not allow to recommend use σ2 as criterion of the material damage of the pipelines.
Keywords: hardness dispersion, applied load, size of the impression, grain size, structural components.
Влияние металлургических, конструктивных, технологических и эксплуатационных факторов придлительнойэксплуатации магистральных трубопроводов приводит к накоплению деградационных микроструктурных изменений, сопровождающихся увеличением рассеянияосновных механических свойств их материала [1].
В связи с этим для неразрушающего контроля состояния магистральных трубопроводов и оценки основных физико-механических свойств его материала необходимы методы, позволяющие учитывать протекающие в материале микроструктурные процессы. К таким методам может быть отнесено измерение твёрдости в силу существования корреляции между величиной этого параметра и другими механическими свойствами металлического материала [2], однако в качестве характеристики, более чувствительной к трансформации структуры металла, в последнее время предпочитают использовать [3] дисперсию σ2 твердости. При этом отсутствуют научно-обоснованные рекомендации по выбору используемой при
81
измерении твердости величины нагрузки Р, которая в работах различных авторов [3-7] изменяется от 0,1 до 150 Н.
Объектом анализа являлись образцы 140x12x8 мм из сталей марок Ст3Гсп и 17ГС, вырезанные поперек проката из труб 720×8 мм, подвергнутые фрезерованию и полировке. Замеры твердости проводили на различных уровнях: макротвердость определяли с использованием универсального твердомера Zwick/Roell ZHU методами Роквелла (HRB) и Виккерса при нагрузках 100 Н (HV10) и 50 Н (HV5), микротвердость – при помощи микротвердомера Buehler по методу Виккерса c нагрузками 1 Н (HV0,1) и 0,1 Н (HV0,01). Распределение поверхностной твердости по длине образцов для каждого способа замера устанавливали с шагом 5 мм. Для каждого способа замера определяли среднюю величину отпечатка h, которую сопоставляли с размеромзернаd структурных составляющих анализируемых сталей.
Для сопоставления результатов все полученные величины твердости переводили в их значения по Бринеллю, по которым для каждой серии замеров рассчитывали дисперсию σ2:
|
|
|
n |
|
|
2 |
|
(HBcp HBi )2 |
, |
||
i 1 |
|||||
|
n 1 |
||||
|
|
|
|
||
|
|
|
n |
|
|
|
2 |
HBср HBi 2 |
|
||
|
i 1 |
|
|
||
n 1 |
|
||||
|
|
|
|
где HBcp, HBi – среднее и i-e значение твердости соответственно; n – количество замеров (24 – для HV0,01 и 27 – для HRB, HV10, HV5, HV0,1, HV0,01).
По результатам 12 замеров твердости с использованием микротвердомера Buehler аналогичный параметр (σ2) рассчитывали и для отдельных структурных составляющих сталей.
Результаты измерения макро- и микротвердости образцов сталей представлены в табл. 1.
Результаты замеров микротвердости отдельных составляющих иллюстрирует табл. 2.
В соответствии с микроструктурным анализом структуру сталей составляют равноосные зерна феррита и конгломератов перлита размером 4…40 мкм, 2…10 мкм и твердостью ~ 240 НВ, ~ 310 НВ соответственно.
Как следует из представленных данных (табл. 1), средние значения твердости HBcp для образцов каждой стали, как и их дисперсии σ2, установленные при сравнительно высоких нагрузках (HRB, HV10, HV5), существенно не отличаются друг от друга. В то же время, при незначительных нагрузках фиксируются большие
82
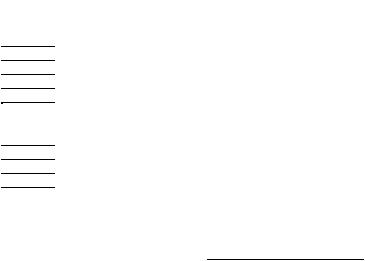
значения этих показателей, особенно для HV0,01: HBcp возрастает на 64 % (для стали Ст3Гсп) и 52 % (17ГС), σ2 увеличивается на несколько порядков.
Таблица 1
Дисперсия твердости по длине образца в зависимости от способа замера
Марка |
Способ |
Значение твердости по Бринеллю, HB |
Дисперсия |
||
стали |
замера |
|
|
|
σ2, ед. |
Минимальное |
Максимальное |
Среднее |
|||
|
HRB |
|
|
|
|
|
162,5 |
183,0 |
170,5 |
35,9 |
|
Ст3Гсп |
HV10 |
156 |
177,4 |
167,0 |
30,9 |
HV5 |
155,8 |
178,3 |
167,3 |
44,5 |
|
|
HV0,1 |
169,2 |
217,3 |
193,1 |
152,6 |
|
HV0,01 |
211 |
350 |
278,5 |
2747,6 |
|
HRB |
165,5 |
191,0 |
179,2 |
23,7 |
17ГС |
HV10 |
174 |
195,9 |
184,8 |
37,2 |
HV5 |
171,6 |
199,6 |
181,5 |
29,3 |
|
|
HV0,1 |
179 |
252,2 |
206,3 |
257,5 |
|
HV0,01 |
205 |
384 |
276,3 |
1402,7 |
|
|
|
|
|
Таблица 2 |
|
|
Микротвердость структурных составляющих сталей и ее дисперсия |
|||||
|
|
|
|
Дисперсия σ2, ед. |
|
|
Марка стали |
Микротвердость Hср, HB |
|
||||
феррита |
перлита |
феррита |
перлита |
|
||
|
|
|
||||
|
|
|
|
|
|
|
Ст3Гсп |
|
230 |
327 |
246 |
302 |
|
17ГС |
|
251 |
302 |
360 |
1166 |
|
Зафиксированное возрастание твердости при малых нагрузках находится в соответствии с общеизвестной [8] закономерностью повышения чисел твердости при переходе от макро- к микротвердости. Существенное возрастание дисперсии твердости по длине образца при этих нагрузках находится в соответствии с результатами определения параметра σ2 для индивидуальных составляющих сталей (~ 300 ед.), высокие значения которого объясняются анизотропией механических свойств различных граней кристаллов [8].
Другая причина различия в величине σ2по длине образца при определении его макро- и микротвердости заключается в соотношении величин отпечатка h при том или ином замере и зерна d структурных составляющих стали: при измерении макротвердости (HRB, HV10, HV5), проводимом при значительных нагрузках (1000, 100 и 50 Н), величина h ( 500 мкм) существенно превышает величину d зерен
83
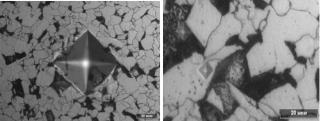
отдельных составляющих (рис. а). Ввиду этого замеряемая твердость отражает осредненные свойства конгломерата различных зерен, что и определяет малые значения σ2. При измерении микротвердости (при HV0,1 Р = 1 Н, h ≈ 30 мкм, при HV0,01 Р = 0,1 Н, h ≈ 8 мкм) фиксируются свойства в пределах одного зерна отдельных составляющих (рис. б) и значения твердости зависят от того, на какую структурную составляющую – мягкий феррит, более твердый перлит или их границу – пришлась точка замера, что и обуславливает значительный разброс в замеряемых значениях твердости и, как следствие, большие значения σ2.
а |
б |
Рис. Микроструктура стали Ст3Гсп с отпечатками замеров макро- (а) и микротвердости (б)
Для объяснения большого разброса в значениях микротвердости (большой дисперсии) перлита стали 17ГС требуется дополнительная информация о микроструктуре этого эвтектоида.
Таким образом, показано, что величина дисперсии σ2 твердости по длине образца трубопроводных углеродистых и низколегированных сталей, установленная при малых нагрузках (HV0,1, HV0,01), определяется величиной этого параметра для индивидуальных структурных составляющих этих сталей и местоположением точки замера микротвердости в их структуре, что не позволяет рекомендовать использование σ2 в качестве критерия оценки повреждаемости материала трубопроводов.
Список литературы
1.Махутов Н.А., Зацаринный В.В., Базарас Ж.Л. Статистические закономерности малоциклового разрушения. – М.: Наука, 1980. – 253 с.
2.Дрозд М.С. Определение механических свойств металла без разрушения. – М.: Металлургия, 1965, 171 с.
84
3.Патент 52107А, МКИ7, G 01 N 3/40. Спосіб оцінки деградації матеріалу внаслідок накопичення пошкоджень у процесі напрацювання. "LM-метод твердості"/ А.О. Лебедєв, М.Р. Музика, Н.Л. Волчек. Опубл. 16.12.02. – Бюл. № 12.
4.Лебедев А.А., Музыка Н.Р., Волчек Н.Л. Определение поврежденности конструкционных материалов по параметрам рассеяния характеристик твердости // Проблемы прочности. – 2003. – № 3. – С. 5–11.
5.Кузьбожев А.С., Агиней Р.В., Смирнов О.В. Исследование вариации твердости трубной стали 17ГС в ходе статического нагружения // Заводская лаборатория. Диагностика материалов. – 2007. – Т.73, № 12. – С. 49–53.
6.Левин Д.М., Муравлева Л.В., Имули Д.А. Энтропия как мера структурного состояния материала // Многомасштабное моделирование структур, строение вещества, наноматериалы и нантехнологии: материалы II Междунар. конф., посвященной памяти проф. А.Н. Никитина. – Тула, 2013. – С. 135–139.
7.Патент РФ 2536783 Способ определения ресурса металла трубопроводов / А.Ф. Пужайло, С.В. Савченков, Р.В. Агиней. Опубл. 27.12.2014. – Бюл. № 36.
8.Григорович В.К. Твердость и микротвердость металлов. – М.: Наука, 1976. – 231 с.
Об авторах
Болобов Виктор Иванович, доктор технических наук, профессор, СанктПетербургский горный университет, Санкт-Петербург, Россия. boloboff@mail.ru.
Назарова Мария Николаевна, кандидат технических наук, доцент, СанктПетербургский горный университет, Санкт-Петербург, Россия. nmn_oilrb@mail.ru.
Касьянов Александр Владиславович, аспирант, Санкт-Петербургский горный университет, Санкт-Петербург, Россия. kasyanov.alx@gmail.com.
About the authors
Bolobov. V.I., Doctor of eng.sc, professor, Saint-Petersburg Mining University, Saint-Petersburg, Russia. boloboff@mail.ru.
Nazarova M.N., PhD in eng.sc., associate professor, Saint-Petersburg Mining University, Saint-Petersburg, Russia. nmn_oilrb@mail.ru.
Kasyanov A.V., postgraduate student, Saint-Petersburg Mining University, SaintPetersburg, Russia. kasyanov.alx@gmail.com.
85
УДК 620.172.2
ОБРАБОТКА ХОЛОДОМ КАК СПОСОБ ПОВЫШЕНИЯ ИЗНОСОСТОЙКОСТИ ПИК ГИДРОМОЛОТОВ
Ле Тхань Бинь, В.И. Болобов, Г.А. Юсупов
Санкт-Петербургский горный университет, Санкт-Петербург, Россия
Показано, что обработка холодом материалов пик гидромолотов – сталей 38ХМ, 40ХН, 55С2, У8 и Х12МФА (5-часовая выдержка образцов при –75°С) приводит к снижению содержания остаточного аустенита (на 44–88 %) и увеличению содержания карбида (на 15–98 %) в закаленной стали, что сопровождается существенным повышением абразивной износостойкости материалов (на 11–49 %) при изнашивании по граниту, как основному материалу нерудного сырья Вьетнама.
Ключевые слова: пики гидромолотов, углеродистые и легированные стали, обработка холодом, повышение износостойкости.
COLD TREATMENT – METHOD OF IMPROVING WEAR RESISTANCE
OF HYDRAULIC BREAKER CHISELS
Le Thanh Binh, V. I. Bolobov, G. A. Yusupov
Saint-Petersburg Mining University, Saint-Petersburg, Russia
It has been shown that cold treatment of materials of hydraulic breaker chiselssteels 38ХМ (AISI P20), 40ХН (AISI 3140), 55С2 (AISI 9255), У8 (AISI W1-A) and Х12МФА (AISI D2) (5 hours holding at –75°C) reduces amount of retained austenite (44–88 %) and increases amount of carbide (15–98 %) in hardened steel, which is accompanied by a substantial increase in abrasive wear resistance of materials (11–49 %) in wear on granite as the main non-metallic raw materials in Vietnam.
Keywords: hydraulic breaker chisels, carbon and alloy steels, сold treatment, increase in wear resistance.
При эксплуатации гидромолотов активного действия по крепким и абразивным породам, свойственным месторождениям нерудного сырья Вьетнама, основной причиной выхода из строя рабочего инструмента – пик является их предель-
86
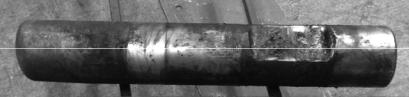
ный износ (рис. 1), обусловленный недостаточной износостойкостью использованных материалов – высокоуглеродистых и легированных сталей.
Рис. 1. Пика гидромолота ATLAS COPCO из стали 40ХН с изношенной головной частью (левая часть пики) после 58 дневной работы по разрушению негабаритного гранитного камня на карьере района Бинь Динь (Вьетнам)
Известно [1–3], что если точка конца мартенситного превращения Мк стали ниже комнатной температуры, то после закалки в структуре материала остается остаточный аустенит, количество которого возрастает с увеличением содержания углерода и легирующих элементов в стали. Присутствие в структуре материала закаленных деталей остаточного аустенита отрицательно влияет на его физикомеханических свойствах и сказывается, прежде всего, в понижении твердости и, как следствие, износостойкости.
Обработка холодом, заключающаяся в охлаждении закаленной стали ниже ее температуры конца мартенситного превращения Мк, способствует превращению остаточного аустенита в мартенсит и образованию при последующем отпуске большого количества очень мелких частиц карбида, что также способствует улучшению эксплуатационных свойств стали [8, 13]. По этой причине обработка холодом широко используется в качестве дополнительной операции после закалки для улучшения износостойкости инструментальных сталей [1, 4–7, 9–12, 14]. В то же время сведений о ее применении для повышения эксплуатационных свойств материалов горного инструмента, подвергающихся абразивному изнашиванию, в литературе не обнаружено. В настоящей работе сравниваются структура, механические свойства (σ0,2, σВ, KCV, HRC) и стойкость к абразивному изнашиванию (Rw) некоторых, наиболее широко используемых в качестве материалов пик, сталей (38ХМ, 40ХН, 55С2, У8 и Х12МФА) после обычно применяемой на практике их термической обработки (закалка в масле с необходимой температуры аустенизации плюс низкий отпуск при 200оС) и дополнительно подвергнутых обработке холодом. В последнем случае образцы непосредственно после закалки перед отпуском помещались в криостат с охлаждающей жидкостью с температурой –75 °С, где выдерживались в течение 5 часов.
С использованием микроскопа Axioplan-2 с программным обеспечением KS 300 3.0 определяли долю площади SК шлифа стали, занимаемую зернами кар-
87
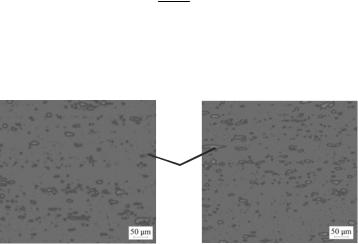
бида, которую принимали за процентное содержание этой фазы. Затем устанавливали суммарную долю S∑ площади зерен карбида и остаточного аустенита SА, откуда, вычитывая величину SК, рассчитывали содержание последнего (SА = S∑ – SК). Физико-механические характеристики определяли на стандартных пятикратных образцах с использованием разрывной машины Zwick/Roell Z100, маятникового копра Zwick/Roell RKP450 и твердомера Zwick/Roell ZHU. Опыты по износостойкости проводили по методике американского стандарта ASTM G99 [5] (метод «pin-on-disk») на штифтах-образцах сталей цилиндрической формы (диаметр 4 мм, высота 14 мм), которые с использованием штифтодисковой машины TE97 изнашивали при постоянной нагрузке (P = 40 Н) со скоростью 0,257 м/с по диску из гранита, как основному материалу нерудного сырья Вьетнама. По результатам взвешивания образцов до- и после воздействия абразива значение износостойкости рассчитывали по формуле [5]:
Rw .mP.L , Нм/мм3
где ρ – плотность материала штифта, г/мм3; m – убыль массы штифта в результате износа, г; L – путь изнашивания (1000 м).
Результаты микроструктурных исследований представлены на рис. 2, 3 и в табл. 1.
Карбид
а |
б |
Рис. 2. Содержание карбида в стали Х12МФА без обработки (а) и с обработкой (б) холодом
Установленные значения физико-механических характеристик и износостойкости сталей, как среднее арифметическое из результатов 3-х экспериментов, представлены в табл. 2.
88
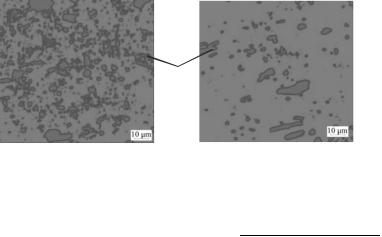
Карбид и остаточный аустенит
а |
б |
Рис. 3. Суммарное содержание карбида и остаточного аустенита |
|
в стали Х12МФА без обработки (а) и с обработкой (б) холодом |
|
|
|
|
|
Та бл ица 1 |
|
|
|
|
|
|
|
|
Марка |
Температура |
% карбидов |
% остаточного аустенита |
|||
аустенизации |
|
|
|
|
|
|
стали |
без холода |
с холодом |
без холода |
|
с холодом |
|
перед закалкой |
|
|||||
|
|
|||||
|
|
|
|
|
|
|
38ХМ |
950оС |
0,152÷0,182 |
0,281÷0,397 |
|
|
|
0,333 |
- |
|
- |
|||
0,168 |
|
|||||
|
|
(+98,2 %) |
|
|
|
|
|
|
|
|
|
|
|
У8 |
800оС |
- |
- |
2,110÷2,314 |
|
1,258÷1,230 |
|
1,244 |
|||||
2,212 |
|
|||||
|
|
|
|
|
(–43,8 %) |
|
|
|
|
|
|
|
|
Х12МФА |
1000оС |
4,429÷5,847 |
6,095÷6,986 |
|
|
1,893 |
6,461 |
15,446 |
|
||||
5,616 |
|
(–87,7 %) |
||||
|
|
(+15,0 %) |
|
|
||
|
|
|
|
|
|
Примечание: числитель дроби – граничное содержание анализируемой фазы, знаменатель – среднеарифметическое из 3-х ее значений.
Таблица 2
|
|
|
Значение параметров |
|
|||
Марка |
|
|
|
|
|
|
|
Вид обработки |
Предел |
Предел |
Ударная |
Твёрдость, |
Износос- |
||
стали |
|||||||
|
текучести |
прочности |
вязкость KCV, |
тойкость RW, |
|||
|
|
HRC |
|||||
|
|
σ0,2, МПа |
σВ, МПа |
Дж/см2 |
|
Нм/мм3 |
|
|
Закалка c 870оС |
1478 |
1933 |
40,6 |
51,1 |
19075 |
|
38ХМ |
+ отпуск |
||||||
|
|
|
|
|
|||
Закалка с 870оС |
1529 |
1953 |
33,0 |
51,6 |
22763 |
||
|
|||||||
|
+ холод + отпуск |
(+3,5%) |
(+1,0%) |
(-18,7%) |
(+1,0%) |
(+19,3%) |
89
|
|
|
|
О к о н ч а н и е |
табл . 2 |
||
|
|
|
|
|
|
|
|
|
|
|
Значение параметров |
|
|||
Марка |
|
|
|
|
|
|
|
Вид обработки |
Предел |
Предел |
Ударная |
Твёрдость, |
Износос- |
||
стали |
|||||||
|
текучести |
прочности |
вязкость KCV, |
тойкость RW, |
|||
|
|
HRC |
|||||
|
|
σ0,2, МПа |
σВ, МПа |
Дж/см2 |
|
Нм/мм3 |
|
|
Закалка c 820оС |
1759 |
2060 |
18,7 |
54,2 |
21 889 |
|
40ХН |
+ отпуск |
||||||
|
|
|
|
|
|||
Закалка с 820оС |
1719 |
2140 |
14,5 |
55,0 |
26240 |
||
|
|||||||
|
+ холод + отпуск |
(–2,3 %) |
(+3,9 %) |
(-22,5 %) |
(+1,5 %) |
(+19,9 %) |
|
|
Закалка с 870оС |
*) |
*) |
5,6 |
59,6 |
22 542 |
|
55С2 |
+ отпуск |
||||||
|
|
|
|
|
|||
Закалка с 870оС |
*) |
*) |
4,8 |
60,5 |
25 220 |
||
|
|||||||
|
+ холод + отпуск |
(–14,3 %) |
(+1,5 %) |
(+11,9 %) |
|||
|
|
|
|||||
|
Закалка с 870оС |
*) |
*) |
5,1 |
60,4 |
13 163 |
|
У8 |
+ отпуск |
||||||
|
|
|
|
|
|||
Закалка с 870оС |
*) |
*) |
3,9 |
60,9 |
14 582 |
||
|
|||||||
|
+ холод + отпуск |
(–23,5 %) |
(+0,8 %) |
(+10,8 %) |
|||
|
|
|
|||||
|
Закалка с 870оС |
*) |
*) |
3,1 |
59,8 |
54 740 |
|
Х12МФА |
+ отпуск |
||||||
|
|
|
|
|
|||
Закалка с 870оС |
*) |
*) |
2,5 |
60,4 |
81 722 |
||
|
|||||||
|
+ холод + отпуск |
(–19,4 %) |
(+1,0 %) |
(+49,3 %) |
|||
|
|
|
Примечание: *) – хрупкое разрушение образцов в широком интервале напряжений.
Как следует из рис. 2, 3 и табл. 1, 2, обработка холодом, как и в [1, 2, 3], приводит к значительному снижению содержания остаточного аустенита (на 44–88 %) и увеличению содержания карбида (на 15–98 %) в закаленной стали. Такое изменение в структуре приводит к существенному повышению износостойкости исследованных сталей (на 11–49 %) и сопровождается незначительным повышением прочностных характеристик (σ0,2, σВ, НRC) испытанных материалов при одновременном снижении ударной вязкости. (Значения σ0,2, σВ сталей 55С2, У8 и Х12МФА определить не представилось возможным, из-за большого разброса в результатах эксперимента, вызванного охрупчиванием материала образцов в результате термической обработки).
Из представленных результатов исследования можно заключить, что обработка холодом может рассматриваться в качестве перспективной дополнительной операции термической обработки для увеличения износостойкости сталей, применяемых для изготовления пик гидравлических молотов, работающих по крепким высокоабразивным породам. При этом следует найти наиболее оптимальные режимы термической обработки, при которых негативное влияние обработки холодом на ударную вязкость стали будет минимальным.
Список литературы
1. КлименкоA.П. Холодвмашиностроении. – М.: Машиностроение, 1969, – 247 с.
90