
Актуальные проблемы повышения эффективности и безопасности эксплуат
..pdfРазработка и внедрение системы мероприятий по оценке технического состояния подъемных комплексов, важнейшей составной частью, которой является технология динамических испытаний действующего стволового оборудования, позволяет своевременно осуществить профилактические меры и обеспечить необходимый уровень эксплуатационного состояния шахтных стволов в соответствии с современными требованиями безопасности.
Список литературы
1.Методические указания по проведению экспертных обследований шахтных подъемных установок (РД 03-422-01) / Государственное унитарное предприятие «Научно-технических центр по безопасности в промышленности Госгортехнадзора России». – М., 2001. – 172 с.
2.Динамика канатных и гидротранспортных подъемных комплексов горных предприятий / В.И. Самуся, С.Р. Ильин, В.Е. Кириченко, И.С. Ильина. – Днепропетровск: Изд-во Нац. горн. ун-та, 2015. – 302 с.
3.Ильин С.Р., Трифанов Г.Д., Воробель С.В. Комплексные экспериментальные исследования динамики скипов рудоподъёмного ствола // Горное оборудование и электромеханика. – 2011. – № 5. – С. 30–35.
Об авторах
Трифанов Геннадий Дмитриевич, доктор технических наук, доцент, заведующий кафедрой ГЭМ, Пермский национальный исследовательский политехнический университет, Пермь, Россия. kanat@pstu.ru.
Ильин Сергей Ростиславович, кандидат технических наук, заведующий лабораторией проблем диагностики и испытаний шахтных подъемных комплексов, Институт геотехнической механики им. Н.С. Полякова НАН Украины, Днепр, Украи-
на. iljin_sr@mail.ru.
Воробель Сергей Викторович, кандидат технических наук, доцент кафедры ГЭМ, Пермский национальный исследовательский политехнический университет,
Пермь, Россия. sergey@vetlan.ru.
About the authors
Trifanov G.D., Doctor of technical sciences, Associate Professor, Head of еру Department of mining electrical engineering, Perm, Russia. kanat@pstu.ru.
Iljin S.R., Ph. D. in Technical Sciences, chief of the laboratory of diagnostics and tests of mining hoisting plants problems, Institute of geotechnical mechanics naimed by N.S. Polyakov NAS of Ukraine, Dnepr, Ukraine. iljin_sr@mail.ru.
Vorobel S.V., Ph. D. in Technical Sciences, Associate Professor of the Department mining Electromechanics of Perm National Research Polytechnic University, Perm, Perm, Russia. sergey@vetlan.ru.
41
УДК 622.67
ОПРЕДЕЛЕНИЕ РЕЗЕРВОВ ПРОИЗВОДИТЕЛЬНОСТИ ПОДЪЕМНЫХ УСТАНОВОК
В.Ю. Зверев1, Г.Д. Трифанов1, С.А. Бут2
1Пермский национальный исследовательский политехнический университет, Пермь,
2ПАО «Уралкалий», Березники, Россия
Изложена методика проведения исследования подъемных установок с целью определения резервов производительности. Описаны параметры, влияющие на интенсивность работы комплекса. Приведены результаты экспериментального исследования по повышению производительности эксплуатируемых подъемных установок.
Ключевые слова: шахтная подъемная установка, производительность, режим работы, нормы проектирования, кинематические параметры, пауза.
THE DETERMINING OF HOIST PLANTS PRODUCTIVITY RESERVES
V.Yu. Zverev1, G.D. Trifanov1, S.A. But2
1Perm National Research Polytechnic University, Perm,
2Public company «Uralkali», Berezniki, Russia
In this paper the methodology of the study of hoist plants to determine the productivity reserves was set out. The authors described the parameters that affect at intensity of the facility work. The results of experimental studies were adduced for improving a productivity of the operated hoist plants.
Keywords: mining hoist plant, productivity, operation mode, design standards, kinematic parameters, pause.
Являясь заключительным звеном в технологической цепочке добычи и транспортировании полезного ископаемого до фабрики, шахтная подъемная установка предопределяет производительность всего рудника.
При проведении реконструкции рудника и увеличении добычи руды необходимо увеличивать производительность подъема. Для этого оборудование подъемного комплекса должно иметь резервы, при использовании которых возможно увеличить интенсивности его работы.
42
Согласно теории шахтного подъема, под производительностью скиповой подъемной установки понимается объем полезного ископаемого, транспортируемый на земную поверхность за год [1]:
A |
mп b tсут n |
, |
(1) |
|
|||
год |
c |
|
|
|
|
|
где b – число рабочих дней в году; c – коэффициент резерва и неравномерности работы скиповой подъемной установки; tсут – время работы подъемной установки в сутки, ч; mп – грузоподъемность скипа, кг; n – количество скипов, выдаваемых в час.
Для выявления резервов и разработки мер по их использованию проанализированы вышеперечисленные параметры и определены их фактические, соответствующие работе подъемных установок рудников Верхнекамского калийного месторождения, и возможные величины.
1.Из перечисленных аргументов представляется наиболее затруднительным увеличить количество рабочих дней подъемной установки в году (b). На каждом подъеме число рабочих дней обуславливается графиком работы, учитывающим простои, во время которых проводится техническое обслуживание и ремонт оборудования. Количество отведенных на это рабочих дней определяется правилами безопасности и техническим регламентом предприятия [2, 3].
Уменьшение времени, отведенного на проведение осмотров и ремонта, без внедрения дополнительных средств контроля состояния оборудования не возможно, так как окажет отрицательное влияние на безопасность и надежность работы подъемного комплекса.
2.Коэффициент резерва (c) учитывает неравномерность поступления руды к подъёмной установке, а так же возможность увеличения производственной мощности рудника при его последующей реконструкции.
В условиях действующего предприятия для уменьшения коэффициента резерва необходимо в первую очередь рассмотреть факторы, влияющие на бесперебойность поступления руды к подъёмной установке. В первую очередь это конвейерный транспорт и рациональная схема его установки, на этапе проектирования оборудования следует учитывать необходимый объём бункера, обеспечивающий не менее одного часа непрерывной работы подъёма [2].
В пример реализации мер по обеспечению равномерного и непрерывного поступления руды можно привести один из рудников Верхнекамского калийного месторождения. Равномерный поток руды в подземные бункеры обеспечивается магистральными конвейерами с шириной ленты 1,2 м с дополнительно установленными передаточными конвейерами и шиберами для подачи руды с одного крыла шахтного поля в бункер другого и обратно. Принятая на руднике схема распределения грузопотоков обеспечивает постоянную выдачу руды на поверхность
43
даже при изменении объемов добычи крыльев шахтного поля. Кроме того, стабильность работы шахтных подъемных установок обеспечена большой вместимостью подземных общешахтных бункеров и возможностью их равномерного заполнения при изменении грузопотоков. В этих условиях коэффициент резерва производительности и неравномерности работы подъемных установок после соответствующего исследования в связи с увеличением производственной мощности рудника при реконструкции был принят равным 1,1.
Описанные выше меры по нормализации равномерности поступления руды к подъемной установке возможно реализовать и на других рудниках, что будет способствовать увеличению производительности их подъемов. При снижении коэффициента резерва и неравномерности работы скиповой подъемной установки с 1,25 [2] до 1,1 производительность будет увеличена на 13,6 %. Заключение о положительном влиянии реализации вышеописанных мер на производительность подъемной установки должно быть обосновано на результатах соответствующих исследований.
3.Время работы (tсут) обусловлено необходимостью проведения ежесуточного технического обслуживания и ремонта оборудования подъема. В соответствии с ВНТП 1–92 при трехсменном режиме работы время работы подъемной установки не должно превышать 18 часов [2].
Увеличение времени работы подъемной установки возможно за счет внедрения современных систем мониторинга. В соответствии с правилами безопасности, периодичность осмотров крепи и армировки вертикальных стволов, оборудованных системами непрерывного контроля (мониторинга) плавности движения скипов
ипротивовесов, устанавливаются техническим руководителем шахты, но не реже 1 раза в неделю [3].
При внедрении отмеченной системы время работы подъема может быть увеличено с 18 до 23 часов в сутки – 1 час необходимо предусмотреть на передачу смены, проверку защит и устранение мелких неисправностей. Увеличение времени работы подъема в неделю составит 30 часов. В соответствии с правилами безопасности, в один день за неделю продолжительность осмотров займет большее время. Авторами одной из систем непрерывного контроля плавности движения скипов для проведения осмотра и ремонта всего оборудования подъемного комплекса рекомендуется уделить при этом порядка 16 часов [4]. В итоге, средняя продолжительность работы подъема составит порядка 21 ч, производительность при этом увеличится на 16 %. За счет исключения влияние человеческого фактора на оценку состояния оборудования и режима его работы повышается эффективность эксплуатации подъемной установки.
4.Грузоподъемность скипов (mп) определяется параметрами шахтных подъемных установок – максимально возможным статическим натяжением каната и разностью натяжений груженой и порожней ветвей. В условиях действующего предприятия масса груза в скипе не может быть увеличена без замены подъемных
44
машин и усиления армировки шахтного ствола. Так как описанная реконструкция подъемного комплекса требует больших капитальных затрат, меры по увеличению производительности за счет применения более грузоподъемных скипов для предприятий является нецелесообразным.
5. Количество выдаваемых скипов с грузом в час (n) определяется временем одного полного цикла подъема (Tц) [1]:
n |
3600 |
; |
(2) |
|
T |
|
|
|
ц |
|
|
Тц tд , |
(3) |
гдеtд – времядвиженияскипов, с; θ– продолжительностьпаузымеждуподъемами, с. Оценить резервы в работе подъемных установок можно при анализе параметров, определяющих время движения скипов (tд) и продолжительности паузы
между подъемами (θ).
5.1. Продолжительность подъема груза (tд) зависит от заданной подъемной машине диаграммы скорости и кинематических параметров движения скипа.
Величина и возможность изменения параметров движения скипа с целью сокращения времени цикла подъема исследовались на подъемных установках рудников Верхнекамского калийного месторождения. Исследования включали в себя определение фактических параметров работы подъемной установки, проектных и расчетных в соответствии с ВНТП 1–92.
Фактические данные получены по регистраторам параметров, которыми в соответствии с правилами безопасности оборудованы все подъемные установки. Проектные параметры взяты из проектов подъемных установок. Параметры, рассчитанные по ВНТП 1–92, определены с учетом регламентированных величин. При сборе данных получены графики движения скипов, их кинематические параметры и время цикла подъема.
Врезультате сравнительного анализа полученных данных предложены следующие меры, обеспечивающие уменьшение времени подъема скипов и увеличение производительности:
1) Сократить количество периодов движения скипов, исключив обособленные периоды движения в разгрузочных кривых. Увеличить скорость, при которой груженый скип входит в разгрузочные кривые, а порожний выходит из них с 0,5 м/с до
1,2 м/с.
Внормах проектирования параметры движения скипа в разгрузочных кривых были заложены исходя из условий снижения динамической нагрузки на кривые. Опыт эксплуатации показывает, что увеличение скорости движения скипа на данном участке практически не оказывает влияния на нагрузки на канат, скип и разгрузочные кривые. Оборудование некоторых подъемных установок по проекту изна-
45
чально рассчитано на исключение периода движения в разгрузочных кривых, успешно эксплуатируется в данном режиме, а техническое обслуживание кривых при этом производится в штатном порядке и выхода их из строя не происходило.
2) Увеличить значение основного замедления скипов до 1 м/с2.
В период замедления нагрузки на канат груженой ветви и привод меньше статических, а величина замедления оказывает наименьшее влияние на техническое состояние и режим работы оборудования подъемной установки [5]. В связи с чем возможно увеличить значение замедления.
3) Следует отметить возможность увеличения максимальной скорости скипа, если она ниже проектной. Это возможно только после проведения профилировки армировки ствола, ее ремонта и исследования динамического состояния системы «скип–армировка», по результатам которой будет определена возможность увеличения скорости движения скипов в стволе.
При изменении тахограммы движения скипов в соответствии с предложенными изменениями необходимо произвести перенастройку защитной диаграммы и ограничителя скорости. Данные рекомендации предложены с учетом опыта эксплуатации подъемных установок, в соответствии с имеющимися проектами подъемов и результатами современных исследований процессов подъема грузов ски-
пами [4, 5].
5.2. Пауза между поочередными подъемами скипов (θ) обусловлена происходящими в этот момент процессами загрузки и разгрузки скипов.
В расчетах продолжительность паузы принимается по таблицам в зависимости от емкости скипа. Фактически же при загрузке скипа рудой выполняется ряд операций, каждая из которых занимает или косвенно влияет на продолжительность паузы. При исследовании процессов загрузки скипов рудников Верхнекамского калийного месторождения были определены следующие технические операции, формирующих паузу: срабатывание системы управления дозатором, t0-t1; открытие затвора дозатора, t1-t2; истечение руды в скип, t1-t3; закрытие затвора дозатора, t3-t4; задержка отправки скипа, t4-t5.
Моменты начала выполнения каждой операции отмечены на рисунке, на котором показан полный цикл подъёма груза с диаграммой движения скипа, регламентированной ВНТП 1–92, и паузой.
Как правило, задержка отправки скипа после завершения истечения руды обусловлена работой привода подъемной машины. После завершения истечения руды подъемной машине подается сигнал на отправку и запуск подъемного двигателя, барабан подъемной машины при этом заторможен и скип не тронется до тех пор, пока ток двигателя не будет максимален. В результате от момента окончания загрузки до растормаживания машины и трогания скипа проходит порядка 2–4 с. Данная задержка присутствует в режиме работы всех исследуемых подъемных установок и обусловлена необходимостью исключения обратного хода груженого скипа при снятии тормозного момента с подъемной машины.
46
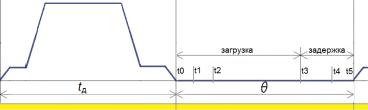
Рис. Полный цикл подъёма
Таким образом, в теоритическом определении паузы не учитывается ряд технологических операций, выполняемых при загрузке. Расчетная пауза меньше фактической, которая может быть реализована на практике. Это обуславливает меньшее фактическое число скипов, выдаваемых за час.
Для уменьшения времени паузы в соответствии с результатами анализа полученных данных и учетом вышеизложенного рекомендуется принять следующие меры:
1)Отрегулировать место установки датчиков нижнего положения скипа так, чтобы затвор дозатора начинал открываться незамедлительно после остановки подъемной машины.
2)Сигнал на отправку скипа необходимо подавать при непосредственном окончании истечения руды, не дожидаясь закрытия затвора дозатора.
Исключение задержки скипа перед отправкой из-за взаимосвязи с работой привода может оказать отрицательное влияние на безопасность работы подъема. Устранение данного процесса при эксплуатируемой системе автоматизации нежелательно. Возможность совмещения времени окончания загрузки скипа и его отправки должно быть изучено дополнительно с точки зрения автоматизации производства.
Разгрузка скипов в виду того, что является более простым технологическим процессом, реже оказывает влияние на продолжительность паузы.
По полученным параметрам исследуемых подъемных установок определено
полное время цикла (Tц) и количество выдаваемых скипов в час (n). С учетом описанных выше рекомендаций по увеличению производительности при уменьшении времени подъема скипов и паузы между подъемами были рассчитаны производительности, которые больше фактических в среднем на 14 %.
В заключение следует отметить, что требуемая на рудниках оптимизация работы подъемных установок возможна в процессе выявления резервов производительности при проведении обследования имеющегося парка оборудования, определения его фактического режима работы и разработки мероприятий по их изменению. По результатам исследования получено, что описанные выше параметры подъема могут включать в себе резервы порядка 43,6 % от годовой производительности установки. Разработанные рекомендации актуальны для рудников, для
47
которых подъемные установки являются узким местом в технологической цепочке добычи полезного ископаемого.
Список литературы
1.Песвианидзе А.В. Расчет шахтных подъемных установок: учеб. пособие для вузов. – М.: Недра, 1992. – 250 с.
2.Временные нормы технологического проектирования угольных и сланцевых шахт. ВНТП 1–92.: утв. Комитетом угольной промышленности Министерства топлива и энергетики РФ) / Минтопэнергетики РФ. – М., 1993. – 111 с.
3.Правила безопасности при ведении горных работ и переработке твердых полезных ископаемых: Федеральные нормы и правила в области промышленной безопасности. Серия 03. Выпуск 78. – М.: Научно-технический центр исследований проблем промышленной безопасности, 2015. – 276 с.
4.Трифанов Г.Д., Микрюков А.Ю. Повышение эффективности эксплуатации шахтных подъемных установок, оборудованных системами мониторинга плавности движения скипов // Горный информационно-аналитический бюллетень. – М.: Горная книга, 2016. – № 5.
5.Трифанов Г.Д., Зверев В.Ю., Стрелков М.А. Экспериментальные исследования влияния режима работы шахтных подъемных установок на динамические нагрузки в канате // Горное оборудование и электромеханика. – 2015. – № 6. –
С. 21–25.
Об авторах
Зверев Валерий Юрьевич, аспирант, Пермский национальный исследовательский политехнический университет, Пермь, Россия. zvva92@mail.ru.
Трифанов Геннадий Дмитриевич, доктор технических наук, доцент, заведующий кафедрой ГЭМ, Пермский национальный исследовательский политехнический университет, Пермь, Россия. kanat@pstu.ru.
Бут Сергей Анатольевич, главный специалист по стационарным установкам ПАО «Уралкалий», Березники, Россия. sergey.but@uralkali.com.
About the authors
Zverev V.Y., postgraduate student, Perm National Research Polytechnic University, Perm, Russia. zvva92@mail.ru.
Trifanov G.D., doctor of technical sciences, associate professor, head of department of mining electrical engineering, Perm National Research Polytechnic University, Perm, Russia. kanat@pstu.ru.
But S.A., chief specialist for fixed installations of public company Uralkali, Berezniki, Russia. sergey.but@uralkali.com.
48
УДК 622.258
ПОВЫШЕНИЕ ЭФФЕКТИВНОСТИ ЭКСПЛУАТАЦИИ ШАХТНЫХ ПОДЪЕМНЫХ УСТАНОВОК НА ОСНОВЕ МОНИТОРИНГА ПЛАВНОСТИ ДВИЖЕНИЯ СКИПОВ
Г.Д. Трифанов, А.Ю. Микрюков
Пермский национальный исследовательский политехнический университет, Пермь, Россия
Приведено описание системы непрерывного контроля движения подъемного сосуда в шахтном стволе. Представлены результаты комплексных экспериментальных исследований динамикисистемы«подъемныйсосуд – жесткаяармировка».
Ключевые слова: непрерывный контроль, шахтный ствол, шахтная подъемная установка, скип, динамические нагрузки, регистрация параметров.
INDUSTRIAL DEVELOPMENT EXPLOITATION BASED MONITORING
SYSTEM LIFTING VESSELS IN THE SHAFTS
G.D. Trifanov, A.Yu. Mikryukov
Perm National Research Polytechnic University, Perm, Russia
Powered description system continuous control of movement lifting vessel in the mine shaft. The results of complex experimental studies dynamics system “Lifting vessel – a rigid reinforcement”.
Keywords: continuous controls, mine hoisting plants, mine hoist installation, shaft skip, dynamical force, registration of parameters.
Шахтный ствол любого горнодобывающего предприятия является важнейшим технологическим звеном, от исправного состояния шахтного ствола и непрерывной работы шахтной подъемной установки зависит работа всего предприятия.
Оборудования шахтного ствола как объекта контроля обладает рядом особенностей. Во-первых, ограниченность доступа для осмотра или контроля за его состоянием. Большую часть времени до 20–22 часов используют для выполнения своих основных технологических операции – выдача полезного ископаемого. Во
49
вторых многоэлементность конструкции практически исключает возможность оценки состояния каждого из них в отдельности.
Необходимость увеличения пропускной способности шахтных стволов на калийных рудниках, с учетом повышенных требований безопасности работы подъемной установки предполагает осуществление постоянного контроля параметров подъемной установки. Методы контроля постоянно совершенствуются, все более распространения получают непрерывный контроль технических параметров работы оборудования и инструментальный контроль.
Существующие методы контроля. Контроль за состоянием ШПУ и оборудования стволов определяются Правилами безопасности [1]. Для получения информации о техническом состояния оборудования шахтной подъемной установки проводят: ежесуточные осмотры – контроля состояния крепи, направляющих шахтных подъемных сосудов, армировки шахтного ствола; периодический маркшейдерский контроль – проверки соответствия армировки шахтного ствола требованиям соотношений геометрических параметров подъема; инструментальный контроль – проверка ширина колеи направляющих проводников, износ проводников, величина уступов на стыках проводников, износ контактных поверхностей, эксплуатационные зазоры между максимально выступающими частями подъемных сосудов, крепью и расстрелами в вертикальных стволах.
Контроль указанными методами проводится на неработающем подъеме и причины динамических явлений в системе «подъемный сосуд - жесткая армировка» ими выявить практически не возможно. Кроме того, выравнивание проводников по данным маркшейдерской съемки не всегда позволяет снизить динамические нагрузки. Профилировка характеризует состояния армировки шахтного ствола в статике. Для предотвращения аварийной ситуации на шахтном стволе необходимо обладать как можно большим объемом информации о состоянии армировки. Наиболее информативным является контроль динамики взаимодействия сосудов с армировкой во время их движения на рабочих скоростях при подъеме и спуске.
Опыт создания и эксплуатация систем автоматического контроля. Для предотвращения аварийной ситуации на шахтном стволе необходимо иметь систему мониторинга основных параметров подъемной установки, а так же данных динамики движения подъемного сосуда. На основе опыта эксплуатации регистраторов параметров подъемной установки [2], а так же применение систем контроля оборудования шахтной подъемной установки [3], разработана система непрерывного контроля динамики движения подъемного сосуда.
Принцип построения системы непрерывного контроля. Система включает в себя трехосевой датчик ускорения, блок обработки информации и антенну, установленные на скипе. Информация со скипа передается на приемник, установленный на копре, и далее поступает на панельный компьютер. На компьютере информация с датчиков обрабатывается, визуализируется и записывается в архив рис. 1.
50