
Технология органического и нефтехимического синтеза
..pdf
11.1.1. Синтез НСООН через формамид
Процесс является трехстадийным. В первой стадии проводят карбонилирование метанола в присутствии щелочного катализатора в метилформиат по уравнению
СН3ОН + СО ↔ НСООСН3, ∆Н298 = –29,3 кДж/моль. (11.1)
Условия реакции на этой стадии (температуру, давление) выбирают с учетом термодинамических и кинетических факторов, поскольку реакция является равновесной. На практике процесс проводят со степенью конверсии метанолане выше70 % (табл. 11.1).
Таблица 1 1 . 1
Влияние температуры и давления на карбонилирование метанола в присутствии метилата натрия
Температу- |
Давление, |
Равновесное |
Температу- |
Давление, |
Равновесное |
ра, °С |
кПа |
превращение |
ра, °С |
кПа |
превращение |
|
|
метанола, |
|
|
метанола, |
|
1960 |
мас. % |
|
|
мас. % |
80 |
20 |
100 |
1960 |
10 |
|
80 |
3920 |
40 |
100 |
3920 |
20 |
80 |
5880 |
62 |
100 |
5880 |
35 |
80 |
7840 |
85 |
100 |
7840 |
52 |
В последующих стадиях метилформиат превращают в формамид, из которого при обработке H2SO4 получают НСООН и сульфат аммония:
НСООСН3 + NH3 → HCONH2 + CH3OH, |
(11.2) |
∆Н298 = –71,2 кДж/моль, |
|
2HCONH2 + H2SО4 + 2Н2О → 2НСООН + (NH4)2SO4, |
(11.3) |
∆Н298 = –100,5 кДж/моль. |
|
Технологическая схема этого процесса показана на рис. 11.1. Метанол и СО после осушки подают в реактор, работающий при
241

температуре 80 °С и давлении 4,5 МПа. Одновременно вводят катализатор со скоростью, обеспечивающей его концентрацию в реакционной смеси, равную 2 мас. %. Степень превращения СО 95 %, метанола 30 %. Выход метилформиата на прореагировавший метанол 99 %, объемная производительность реактора равна 800 г/ч на 1 дм3 объема. Продукты реакции направляют в газожидкостный сепаратор, где для удаления примесей проводят продувку СО. Отходящие газы из сепаратора промывают в скруббере холодным метанолом. Жидкую фазу из сепаратора и скруббера направляют в колонну выделения метилформиата. Метанол, содержащий катализатор, большей частью возвращают в реактор, а частично направляют в колонну для отделения высококипящих продуктов и дезактивированного катализатора.
Рис. 11.1. Принципиальная технологическая схема получения метилформиата карбонилированием метанола: 1 – реактор карбонилирования; 2 – газожидкостный сепаратор; 3 – колонна выделения; 4 – скруббер; 5 – колонна выделения метилформиата; 6 – колонна отделения высококипящих фракций; 7 – приемный резервуар. Потоки: I – СО; II – метанол; III – катализатор; IV – продувка СО; V – СО на рециркуляцию; VI – метанол;
VII – метилформиат
242

Полученный метилформиат направляют на стадию получения формамида (рис. 11.2). Метилацетат и аммиак подают в реактор, работающий при 65 °С и давлении 1,3 МПа. Теплота реакции отводится циркулирующей реакционной смесью через внешний теплообменник. Жидкие продукты реакции направляются в промежуточный сборник, а поток паров из верхней части реактора – в конденсатор, где отделяют метанол. В колонне отгонки легких фракций формамид отделяют от аммиака, метанола и метилформиата и направляют в колонну доочистки.
Рис. 11.2. Принципиальная технологическая схема получения формамида аммонолизом метилформиата: 1 – реактор; 2 – уравнительный резервуар; 3 – колонна отгонки легких фракций; 4 – колонны выделения метанола; 5 – колонна доочистки; 6 – скруббер. Потоки: I – метилформиат; II – аммиак; III – рецир-
кулирующий NН3; IV – метанол; V – отдув; VI – формамид
В последней стадии проводят гидролиз формамида (рис. 11.3). В реактор непрерывно вводят в равных количествах формамид и68–74%-юH2SO4. ТеплотуреакциииспользуютдляиспаренияНСООН. Горячая пульпа, состоящая из сульфата аммония и НСООН, подается во вращающуюся печь. Пары кислоты направляют в колонну, а сульфат аммония выводят из разгрузочного устройства.
243

Рис. 11.3. Принципиальная технологическая схема получения НСООН гидролизом формамида: 1 – колонна для приема формамида; 2 – реактор; 3 – колонна выделения НСООН; 4 – вращающаяся печь; 5 – скруббер; 6 – сборник муравьиной кислоты; 7 – товарная емкость. Потоки: I – формамид; II – серная кислота; III – абгазы; IV – вода; V – отработанная вода;
VI – сульфат аммония; VII – НСООН
Выход метилформиата в таком процессе составляет 98 % в расчете на метанол, и 95 % – в расчете на СО. Выход формамида на метилформиат достигает 98 %, а выход НСООН на формамид– 93 %. Расход сырья в кг на 1000 кг НСООН составляет: метанола – 31, СО – 702, NH3 – 314, серной кислоты – 1010.
11.1.2. Синтез муравьиной кислоты гидролизом метилформиата
По способу фирмы Leonard Process муравьиную кислоту получают в две стадии карбонилированием метанола в метилформиат и гидролизом последнего в НСООН. В 1981 г. в Финляндии по этой технологии пущен завод мощностью 20 тыс. т/год.
Стадию карбонилирования метанола осуществляют по технологии, описанной в предыдущем разделе. Для гидролиза метилформиата предложены два варианта: гидролиз с избытком воды, которая затем удаляется перегонкой или НСООН выделяют экстрактивной перегонкой с N-формилморфолином, либо гидролиз осуществляют в присут-
244
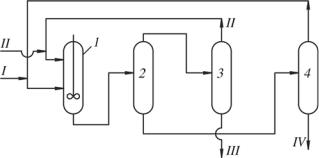
ствии третичного амина (пентилимидазола) со стехиометрическим количеством воды.
Технологическая схема процесса с избытком воды показана на рис. 11.4. Воду и метилформиат непрерывно вводят в реактор, работающий при температуре 80 °С и давлении 2,9 МПа. Гидролиз протекает в жидкой фазе в течение 1 ч. Образующаяся НСООН оказывает на реакцию каталитическое действие. Продукты гидролиза направляют в колонну для отделения водной НСООН. Из верхней части колонны отбирают смесь метанола и метилформиата, которую
Рис. 11.4. Принципиальная технологическая схема получения НСООН гидролизом метилформиата с избытком воды: 1 – реактор; 2 – колонна выделения НСООН; 3 – колонна выделения метанола; 4 – колонна концентрирования НСООН. Потоки: I – вода; II – метилформиат; III – метанол; IV – 82%-я муравьиная
кислота
затем разделяют. Метилформиат возвращают в реактор, а метанол направляют на стадию карбонилирования. Водную НСООН перегоняют в следующей колонне под давлением 0,3 МПа.
11.2. ПОЛУЧЕНИЕ ПРОПИОНОВОЙ КИСЛОТЫ
Одним из промышленных способов получения пропионовой кислоты является карбонилирование этилена (табл. 11.2).
Показано, что пропионовая кислота с селективностью 99 % образуется в мягких условиях (температура 195 °С, давление 7 МПа)
245

из этилена и СО в среде воды в присутствии катализатора СоI2 или Со(АсО)2 с добавкой C2H5I (отношение I : Со = (2,5–3,5) : 1). Предложен способ одновременного получения уксусной и пропионовой кислот карбонилированием этилена в водном метаноле под действием соединений родия и галоидного промотора при температуре 175– 200 °С и давлении до 7 МПа. Эффективными катализаторами синтеза пропионовой и жирных кислот С17–С30 и их эфиров из олефинов, СО и воды или спирта в мягких условиях (температура 80–150 °С, давление 4–15 МПа) являются комплексы Со2(СО)8 с пиридиновыми основаниями, а также комплексы Pd или Pt. Условия получения пропионовой кислоты карбонилирования этилена приведены в табл. 11.2.
Таблица 1 1 . 2
Промышленные и перспективные способы получения пропионовой кислоты карбонилированием этилена
Фирма |
Катализатор |
Температура, |
Давление, |
Выход |
|
|
°С |
МПа |
пропионовой |
|
|
|
|
кислоты, мас. % |
Du Pont |
Карбонил, ацетат, |
280 |
30–35 |
89 |
|
пропионат никеля |
|
|
80 |
Shell |
Н3РО4 + BF3 |
20–80 |
5–10 |
|
BASF |
Карбонил никеля |
230–320 |
30–40 |
95 |
Union Oil |
Соли родия |
170 |
10 |
– |
Monsanto |
Комплексы иридия |
191 |
4,9 |
65 |
Подробныеисследованиясистемы Со2(СО)8 – пиридин (γ-пиколин) позволили разработать промышленный процесс, протекающий в значительно более мягких условиях (температура 150–170 °С, давление 7,5–20 МПа, растворитель ацетон), чем процесс фирмы BASF. Технологическая схема промышленного синтеза пропионовой кислоты по способу фирмыHulls показана нарис. 11.5.
Катализатор готовят из компонентов в отдельном аппарате и подают в реактор одновременно с олефином, СО и водой (спиртом). Продукты реакции затем поступают в реактор окисления, где получаютокисленнуюформу катализаторного комплекса, которая легко
246

Рис. 11.5. Принципиальная технологическая схема производства жирных кислот карбонилированием олефинов по способу фирмы Hulls: 1 – узел приготовления катализатора; 2 – реактор синтеза; 3 – реактор для окисления катализатора; 4 – колонна отделения воды; 5 – сепаратор; 6–8 – ректификационные колонны. Потоки: I – пиридин (γ-пиколин); II – соль Со; III – СО + Н2; IV – катализатор; V – СО; VI – олефин; VII – вода; VIII – воздух;
IX – кислота; X – кубовыйостаток
отделяется от продуктов реакции в сепараторе и возвращается в цикл. Жидкие вещества после отделения катализатора поступают в узел ректификации, где выделяются пиридин (возвращается на приготовление катализатора), олефин (возвращается в реактор синтеза) и целевой продукт. Конверсия этилена достигает 98 мас. %, селективность образования пропионовой кислоты выше 99 %.
11.3. ПРОИЗВОДСТВО АКРИЛОВОЙ КИСЛОТЫ
Основным промышленным способом получения акриловой кислоты является карбонилирование ацетилена в присутствии никелевого катализатора. По технологии высокого давления фирмы BASF процесс осуществляют при температуре 180–205 °С и давлении 4–8 МПа
247

с использованием в качестве катализатора NiBr2 – галогенида меди в тетрагидрофуране (рис. 11.6). Акриловая кислота получается с выходом 90 % на С2Н2 и 85 % на СО. Годовая мощность установок по технологии высокого давления составляет 132 тыс. т/год (фирма
BASF) и 30 тыс. т/год (фирма Dow-Badische, США).
Рис. 11.6. Принципиальная технологическая схема получения акриловой кислоты карбонилированием ацетилена по способу фирмы BASF: 1 – сатуратор; 2 – реактор; 3 – скруббер; 4 – дегазатор; 5 – абсорбер; 6 – ректификационная колонна. Потоки: I – ацетилен; II – вода; III – катализатор; IV – СО; V – абгаз; VI – газ рецикла; VII – свежая вода; VIII – тетрагидрофуран;
IX – акриловаякислота; X – промывочнаявода
Фирмы Rohm and Haas и Toa Gosei разработали процесс, представляющий комбинацию стехиометрического и каталитического способов, что позволяет работать при низком давлении. По этой технологии акриловую кислоту получают при атмосферном давлении и температуре 30–50 °С с выходом 80–90 % на четырех заводах в США (фирма Rohm and Haas) мощностью 140 тыс. т/год и на заводе в Японии (фирма Toa Gosеi) мощностью 36 тыс. т/год.
248
В последние годы фирма Union Oil (Калифорния) разработала новый перспективный процесс получения акриловой кислоты окислительным карбонилированием этилена по реакции
СН2=СН2 + СО + ½ O2 → СН2=СНСООН |
(11.4) |
Процесс проводят при температуре 135–150 °С, давлении СО 7–8 МПа и соотношении СО : С2Н4 = 1 : 1 в среде ледяной уксусной кислоты с добавкой до 20 % уксусного ангидрида, 0,1 % PdCl2
и 0,5 % смеси LiCl, LiOCOCH3 и СuС12.
249
Глава 12 НЕКОТОРЫЕ НОВЫЕ НАПРАВЛЕНИЯ
РАЗВИТИЯ ПРОЦЕССА ОКСОСИНТЕЗА
За годы, прошедшие после открытия реакции гидроформилирования и создания первых промышленных установок оксосинтеза, в этой области развивались не только пути усовершенствования оксопроцесса, но и некоторые реакции, родственные гидроформилированию. Наибольший практический интерес представляла разработка процессов на основе реакций:
– гидрокарбоксилирования (получения кислот):
RCH=CH2 + CO + H2O → RCH2CH2COOH; |
(12.1) |
– гидроалкоксикарбонилирования (получения сложных эфиров):
RCH=CH2 + CO + R OH → RCH2CH2COOR ; |
(12.2) |
– карбонилирования спиртов: |
|
RCH2OH + CO → RCH2COOH |
(12.3) |
Как видно из приведенных реакций, донорами водорода в них (вместомолекулярноговодорода) являютсясоответственноводаиспирты.
Эти реакции открывают прекрасные перспективы для получения на их основе широкого ассортимента кислот и эфиров.
12.1. ПОЛУЧЕНИЕ ВЫСШИХ СИНТЕТИЧЕСКИХ ЖИРНЫХ МОНОКАРБОНОВЫХ КИСЛОТ Н-СТРОЕНИЯ НА БАЗЕ РЕАКЦИИ ГИДРОКАРБОКСИЛИРОВАНИЯ
Высшие жирные кислоты н-строения находят широкое использование в производстве синтетических моющих средств бытового
итехнического назначения, поверхностно-активных веществ, автошин
ирезино-технических изделий, смазок, моторных масел, ингибито-
250