
Технология органического и нефтехимического синтеза
..pdfтвор ацетата одновалентной меди, обладающий высокой поглотительной способностью, стабильностью при нагревании, имеющий низкую температуру застывания, не коррозионно-активный.
Идущая на хемосорбцию бутен-бутадиеновая фракция должна содержать не более 0,05 % ацетиленовых углеводородов, так как из-за поглощения ацетиленов теряются рабочие свойства хемосорбента. В связи с этим перед хемосорбцией исходную фракцию подвергают селективному гидрированию в присутствии катализатора (Рd или Ni на носителях), при температуре10–20 °Си давлении0,29–0,98 МПа.
Комплексообразование бутадиена идет по реакции
(СН3СОО)2Сu(NH3)4 + C4H6 C4H6(NH3)3CH2(CH3COO)2 + NH3 (4.5)
Количество бутадиена, выделяемого на 1 м3 поглотительного раствора, зависит от концентрации бутадиена в исходной смеси
иот температуры хемосорбции. Чем выше концентрация и ниже температура (оптимальная – минус 8 °С), тем выше количество выделяемого бутадиена.
Внастоящее время для выделения бутадиена используется более эффективный метод экстрактивной дистилляции с применением тех же экстрагентов, что и при разделении бутан-бутеновой фракции (ацетонитрил, диметилформамид, N-метилпирролидон). Аналогичны
итехнологические схемы выделения бутадиена из соответствующих фракций.
4.1.1.6.Выделение бутадиена-1,3 из газов пиролиза
Впроцессе пиролиза бензина и более тяжелых нефтепродуктов образуется много бутенов и до 5 % бутадиена. Таким образом, фрак-
ция С4 газа пиролиза является источником получения бутадиена-1,3, изо- и н-бутенов. Причем себестоимость получаемого при этом бутадиена ниже, чем стоимость бутадиена, получаемого дегидрированием. Основная трудность– очистка получаемого бутадиена от примесей.
Выделение бутадиена-1,3 из фракции С4 газа пиролиза в промышленности проводится методами экстрактивной дистилляции (рис. 4.6)
111
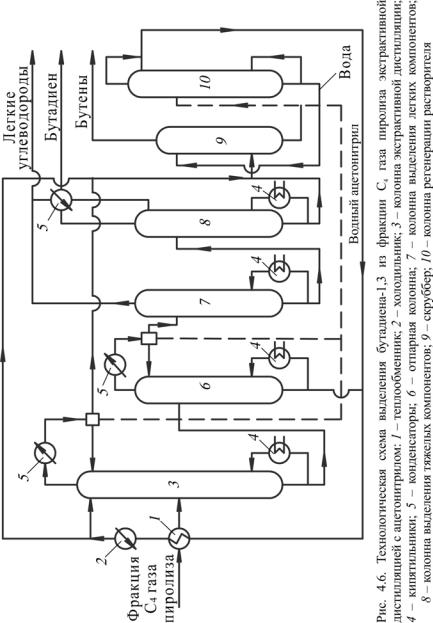
112
и экстракции. В качестве экстрагента высокую эффективность проявил ацетонитрил.
Рассмотрим принципиальную технологическую схему экстрактивной дистилляции при выделении бутадиена-1,3 из фракции С4 газа пиролиза (см. рис. 4.6).
Согласно схеме фракция С4 газа пиролиза нагревается и частично испаряется в теплообменнике 1 за счет тепла регенерированного экстрагента, далее она направляется в среднюю часть колонны экстрактивной дистилляции 3, а охлажденный в холодильнике 2 ацетонитрил поступает в верхнюю часть колонны 3. Колонна снабжена кипятильником 4 и конденсатором 5. Бутадиен и примеси поглощаются экстрагентом, а бутан-бутеновая фракция отбирается из верхней части колонны 3 и конденсируется в конденсаторе 5. Часть конденсата используется в качестве орошения, а балансовое количество поступает на водную отмывку от растворителя в скруббер 9 и выводится с установки.
Насыщенный экстрагент из колонны 3 поступает в отпарную колонну 6 для отпарки углеводородов. Бутадиен-1,3 с примесью других диеновых и ацетиленовых углеводородов, выходящих из верхней части колонны 6, проходит последовательно колонны ректификации 7 и 8. Легкие примеси (пропан, пропилен, пропандиен, метилацетилен) удаляются в виде верхнего продукта колонны 7. Остаток колонны 7 – смесь бутадиена-1,3 с более тяжелыми примесями (бутадиен-1,2 и тяжелые ацетиленовые углеводороды) – подвергается ректификации в колонне 8, где бутадиен выделяется в виде ректификата, а в кубовой жидкости остаются тяжелые примеси.
Вода из скруббера 9 поступает на отпарку ацетонитрила в колонну 10, а вода из нижней части колонны 10 возвращается на орошение скруббера 9. Ацетонитрил из колонн 6 и 10 вновь направляется в колонну 3.
По данной схеме получается бутадиен с чистотой 99,5 %, содержащий не более 0,005 % ацетиленовых углеводородов. Степень извлечения бутадиена 96 %.
113
4.2. ПРОИЗВОДСТВО ИЗОПРЕНА
Изопрен (или 2-метилбутадиен-1,3) является мономером при получении стереорегулярного цисполиизопренового каучука – прототипа натурального каучука. Используется изопрен и для получения бутилкаучука.
Синтез изопрена может быть осуществлен различными методами, из которых промышленное использование получили следующие:
–дегидрирование изопентана и изопентенов;
–синтез из изобутилена и формальдегида;
–синтез из пропилена;
–синтез из ацетона и ацетилена.
В России изопрен получают в основном первыми двумя методами, в США – в основном из изопентана и небольшое количество – из пропилена, в Японии – в основном из смол пиролиза.
Остановимся подробнее на методах получения изопрена, применяемых в нашей стране.
4.2.1. Дегидрирование изопентана и изопентенов
Процесс дегидрирования изопентана и изопентенов осуществляется по той же технологии, что и дегидрирование н-бутана и н-бутенов. Отличие только в стадиях разделения продуктов и более мягких температурных условиях. Промышленное применение нашел только двухстадийный процесс.
В качестве сырья дегидрирования применяются либо изопентановая фракция газовых бензинов, либо изопентан-изопентеновая фракция бензина каткрекинга. Для увеличения ресурса по изопентану подвергают изомеризации н-пентан, получаемый из тех же источников, что и изопентан. Изопентановая фракция должна содержать 97–98 % изопентана.
Дегидрирование изопентана, как и н-бутана, ведут на алюмохромовом катализаторе. В результате первой стадии образуется смесь
114
изомеров изопентена (3 изомера), которая далее дегидрируется в изопрен.
Процессы дегидрирования изопентана и изопентенов проводят при повышенной температуре, в результате чего одновременно с основными протекают и побочные реакции распада (образование углеводородов С1–С4) и уплотнения (так как изопентены и изопрен еще сильнее, чем углеводороды С4, склонны к уплотнению, то количество образующегося кокса еще больше возрастает).
При дегидрировании изопентена более заметна роль реакций изомеризации, приводящих к образованию изомера изопрена– пиперилена (пентадиена-1,3) и циклопентадиена. Кроме того, из-за изомеризующей способности алюмохромового катализатора идет образование н-пентана и н-пентена, которые на второй стадии дают также пиперилен. Выход пиперилена достигает 10–15 % от суммы диеновых, а содержание н-пентенов в изопентеновой фракции составляет 10–12 %. Количество образующегося циклопентадиена не превышает 1 % от прореагировавших изопентенов. При дегидрировании в небольшом количестве образуютсяи ацетиленовыеуглеводороды.
Получаемые побочные продукты нежелательны в изопрене и требуют его специальной очистки для их удаления.
Первую стадию дегидрирования изопентана в нашей стра-
не проводят в псевдоожиженном слое на микросферическом алюмохромовом катализаторе в секционированных реакторе и регенераторе. Условия процесса: давление немного выше атмосферного, температура 525–540 °С, объемная скорость 1,5–2 ч–1. Выход изопентенов 30–32 % на пропущенный изопентан, селективность 68–72 %. Технологическое оформление аналогично схеме дегидрирования н-бутана.
Вторая стадия дегидрирования изопентенов проводится в реак-
торах адиабатического типа с неподвижным слоем катализатора (хромкальцийникельфосфатный). Технологическая схема второй стадии аналогичнасхеме стадиидегидрированиян-бутенов.
Ввиду повышенной склонности изопрена к полимеризации, на второй стадии дегидрирования и на установках разделения в систему вводят ингибиторы полимеризации.
115

4.2.2. Разделение углеводородов С5
Разделение контактного газа первой и второй стадий дегидрирования изопентана и изопентенов аналогично процессу разделения контактного газа дегидрирования н-бутана и н-бутенов. Путем сочетания процессов абсорбции и ректификации можно выделить фракции С5 из контактного газа, однако разделение между собой углеводородов С5 удается только за счет применения экстрактивной дистилляции вследствие близости температур кипения разделяемых углеводородов. При этом в качестве экстрагентов используют: N-метилпирролидон, диметилформамид, диметилсульфолан.
Процесс разделения фракции С5 экстрактивной дистилляцией аналогичен процессам разделения углеводородов С4. В связи с тем, что изопрен после выделения идет на полимеризацию в присутствии комплексных металлорганических катализаторов, его необходимо тщательно отмывать от следов экстрагента.
При экстрактивной дистилляции вместе с изопреном поглощаются и другие диены (пиперилен и циклопентадиен). Очистка изопрена от них проводится четкой ректификацией, однако процесс энергоемкий, таккакприходитсяотгонятьизопренотболеевысококипящихпримесей.
От ацетиленовых углеводородов изопрен очищают селективным гидрированием над никелевым катализатором.
4.2.3.Получение изопрена из 2-метилпропена
иформальдегида
Этот метод разработан в нашей стране Н.С. Немцовым. Метод освоен в промышленном масштабе. Процесс двухстадийный.
Первая стадия – конденсация 2-метилпропена с формальдегидом с образованием 4,4-диметил-1,3-диоксана по реакции:
(4.6)
116
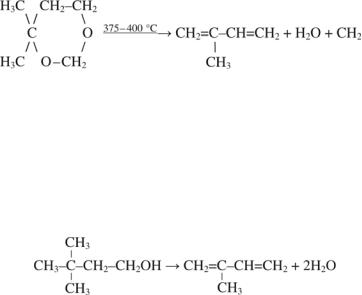
Реакцияпротекает притемпературе70–90 °Сидавлении1–1,6 МПа, катализатор – серная кислота. Выход 4,4-диметил-1,3-диоксана достигает 66–68 %, при конверсии 2-метилпропена – 88–92 %, формальдегида – 92–96 %.
Образуется на данной стадии и ряд побочных продуктов: карбинолы, метилаль, диоксановые спирты, диолы, эфиры и др. Особенно много образуется 3-метилкарбинола (СН3)3СОН (15 %) и 3-метил-
бутандиола-1,3 (5–7,5 %):
CH׀ 3 CH׀ 2–CH2–C–CH׀ 3 OH OH
Вторая стадия представляет собой газофазное каталитическое расщепление 4,4-диметил-1,3-диоксана с образованием изопрена:
(4.7)
Катализатор процесса – фосфорная кислота на алюмосиликате (оксид алюминия с 25 % оксида кремния), смесь фосфатов и другие вещества кислотного характера. Разбавление водяным паром 1 : 2. Глубина расщепления – до 90 %, выход изопрена 83–84 % от разложенного и 70–75 % от пропущенного диоксана.
3-метилбутандиол-1,3 в указанных условиях также превращается в изопрен:
(4.8)
117
В продуктах второй стадии наряду с изопреном содержатся: 2-метилпропен (10–12 %), продукты уплотнения, незначительные количества циклопентадиена (0,0002 %), формальдегид (86–99 % от стихоометрии).
В качестве сырья для получения изопрена используется изобутан – изобутиленовая фракция, содержащая не менее 40 % 2-метилпропена, не более0,0005 % серы и0,001 % ацетиленовых углеводородов.
Формалин должен содержать 37 % формальдегида и не более 1 % метанола.
Рассмотрим принципиальную технологическую схему процесса получения и расщепления диоксана (рис. 4.7).
Согласно схеме изобутан-изобутиленовая фракция направляется в нижнюю часть второго реактора 1 (спаренного), туда же поступает и серная кислота. Смесь свежего и возвратного формалина подвергается очистке и поступает в верхнюю часть первого реактора 1. Реакционная масса из реактора 1 направляется на нейтрализацию и отмывку от формальдегида в нейтрализатор 2, а затем в отстойник 3. Углеводородный слой из отстойника 3 подается в колонну 4 для выделения бу- тан-бутиленовой фракции, которая в колонне 5 разделяется на изобу- тан-изобутиленовую фракцию и бутены-2. Далее в колоннах 6 и 7 из углеводородного слоя отгоняются метилаль-метанольная фракция и триметилкарбинол. В колонне 8 идет отгонка 4,4-диметил-1,3-дио- ксана от высококипящих компонентов.
Водный слой из аппаратов 2 и 3 нейтрализуется щелочью, после чего в колонне 10 отгоняются низкокипящие органические соединения. Ректификат из колонны 10, состоящий из метилаля, метанола, триметилкарбинола и диоксана, присоединяется к углеводородному слою, а остаток – водный слой – направляется в колонны 11 и 12 для выделения возвратного формалина. Диоксан из колонны 8 вместе с возвратным диоксаном поступает на расщепление в реакторы второй стадии 13, куда подается водяной пар и Н3РО4.
Продукты реакции подвергаются ректификации. В колонне 16 выделяются высококипящие продукты, а в колонне 17 – изобутилен. Колонна18 служит дляочистки изопрена от высококипящих побочных
118
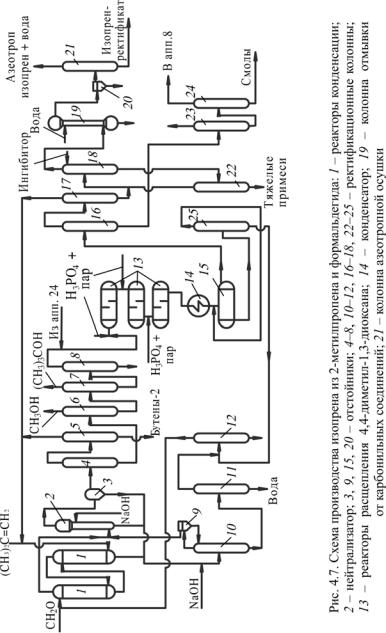
119

продуктов (доочистка). В колонне 19 проводится отмывка карбонильных соединений, в колонне 21 – азеотропная осушка. В колонне 22 идет дополнительное выделение изопрена-сырца из остатка колонны 18. В колоннах 23 и 24 из высококипящих продуктов, выделенных в колонне 16, извлекают непревращенный диоксан. Остатки из колонн 22 и 24 содержат ряд ценных кислородсодержащих продуктов.
Технологическое оформление первой стадии процесса определяется необходимостью вести процесс при высокой концентрации 2-метилпропена. Это обеспечивается применением реактора идеального вытеснения. Для отвода тепла применяют реактор трубчатого типа. 2-Метилпропен и формальдегид подаются вреактор противотоком.
Вторая стадия расщепления диоксана идет с поглощением тепла. Для подвода тепла применяют реакторы полочного типа со стационарным слоем катализатора. В качестве теплоносителя используется перегретый водяной пар, подаваемый в реактор ступенчато, что обеспечивает почти изотермический режим.
Регенерация катализатора осуществляется каждые 5–6 ч в начале работы катализатора и каждые 2–3 ч вконцеего работы.
Продолжительность циклов работы и регенерации катализатора одинакова. Активность катализатора со временем падает из-за отложения кокса (регенерация проводится каждые 3 ч).
4.3. ПРОИЗВОДСТВО ИЗОБУТИЛЕНА
Изобутилен используется при производстве бутилкаучука (сополимера с 2–3 % пропена), полиизобутилена.
Существуют различные методы получения изобутилена. В частности, один из них – дегидратация изобутанола:
(4.9)
Более выгодно получать изобутилен из бутан-бутеновой фракции газов крекинга. При этом из-за близости температур кипения смесь бутенов разделяют химическими методами.
120