
Технология органического и нефтехимического синтеза
..pdfние катализатора, разделение продуктов синтеза и гидрирование альдегидоввсоответствующиеспирты).
В настоящее время ассортимент вырабатываемых промышленностью оксопродуктов превышает 50 наименований: пропанол, бутанолы, спирты С7–С19, изодеканол, тридециловый спирт, адипиновая кислота и многие другие.
Крупнейшие фирмы-производители оксопродуктов: Union Carbide, Monsanto, Shell, Mitsubishi и др.
Первая промышленная установка оксосинтеза по производству 2-этилгексанола и изодецилового спирта была пущена в 1948 г. в США. Мировое производство оксопродуктов в настоящее время превышает 7 млн т/год.
Большое количество оксопродуктов производит и Россия – около 400 тыс. т/год.
Из продуктов гидроформилирования наиболее значимые – спирты С3–С19, применяемые в качестве растворителей, стабилизаторов. Оксоспирты применяются при производстве пластификаторов ПВХ, моющих средств, синтетических смазочных масел, фармацевтических препаратов, лакокрасочных покрытий.
Реакция гидроформилирования – присоединение СО и Н2 по двойной связи к олефину. При этом образуются альдегиды н- и изостроения:
RСН=СН2 + СО + Н2 → RСН2СН2СНО; |
(5.9) |
|
RСН=СН2 + СО + Н2 |
→ RСНСН3 |
(5.10) |
|
|
|
СНО В зависимости от используемого катализатора реакция протека-
ет при температуре 120–200 °С и давлении 1–30 МПа.
Из получаемых альдегидов наибольшее практическое применение имеют продукты нормального, а не изостроения.
131
5.3.1. Катализаторы реакции гидроформилирования
Реакцию гидроформилирования в той или иной степени катализируют соединения Fe, Mn, Ru, Co, Rh и др.
Впромышленности в процессе гидроформилирования получили применение гомогенные системы, содержащие комплексы переходных металлов трех видов:
1) гидрокарбонил кобальта НСо(СО)4;
2) гидрокарбонил кобальта, модифицированный третичными
фосфинами, например трибутилфосфинами НСо(СО)3РБут3; 3) гидрокарбонильные комплексы родия с координированным
третичным фосфином, например, [HRh(CO)(PБут3)3].
Процесс гидроформилирования на катализаторе НСо(СО)4 характеризуется температурой 140–180 °С, давлением 25–30 МПа (соотношение продуктов н- и изостроения (3–4) : 1, из которых 80 % – альдеги-
ды, 10 % – спирты); на катализаторе НСо(СО)3РБут3 процесс протекает при температуре 160–200 °С, давлении 5–10 МПа (соотношение продуктов н- и изостроения составляет (6–8) : 1, из которых 80 % – спирты
и10–20 % – альдегиды); на катализаторе [HRh(CO)(PБут3)3] процесс идет при температуре 80–100 °С, давлении 1,5–2,5 МПа (соотношение продуктов н- и изостроения составляет (15–20) : 1, из которых 96 % – альдегиды).
Внастоящее время 50 % оксопродуктов в мире вырабатывается
с использованием катализатора НСо(СО)4.
Выбор условий проведения процесса гидроформилирования диктуется не термодинамикой, а необходимостью перевода катализа-
тора в активную форму, в частности, Со2(СО)8 в НСо(СО)4, высокое же давление стабилизирует эту активную форму.
Реакция гидроформилирования экзотермична. Скорость реакции пропорциональна концентрации олефина, катализатора и температуре. Зависит она и от строения олефина.
Из большого числа побочных реакций лишь гидрирование протекает параллельно основной реакции:
RСН=СН2 + Н2 → RСН2СН3 |
(5.11) |
132
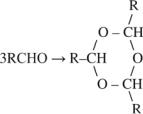
Остальные побочные реакции идут с участием образующихся альдегидов и протекают последовательно по отношению к реакции гидроформилирования.
Основные побочные реакции:
– гидрирование альдегидов в спирты:
RСНО + Н2 → RСН2ОН; |
|
(5.12) |
– альдольная конденсация: |
|
|
2СН3(СН2)2СНО → СН3(СН2)2СН=С–СНО + Н2О; |
(5.13) |
|
С |
2Н5 |
|
– образование ацеталей: |
|
|
RСНО + 2НОСН2R → RСН(ОСН2R)2 + Н2О; |
(5.14) |
|
– сложноэфирная концентрация: |
|
|
2RСНО → RСООСН2R; |
|
(5.15) |
– реакция уплотнения: |
(5.16) |
Поскольку среди продуктов оксосинтеза наиболее предпочтительны продукты с прямой цепью, то при использовании того или иного катализатора определены наиболее оптимальные условия его применения, так как выход продуктов нормального строения зависит от температуры и давления.
В качестве растворителей реакции гидроформилирования обычно используют: толуол, кубовые продукты самого оксопроцесса, простые эфиры, алифатические спирты, кетоны, пентан-гексановую фракцию.
133
5.3.2. Влияние примесей на процесс гидроформилирования
Как олефиновое сырье, так и синтез-газ могут содержать примеси, влияющие на протекание основной реакции. Основные из них: диеновые, ацетиленовые, сернистые и перекисные соединения, кислород, аммиак.
Так, кислород окисляет карбонилы кобальта до СоО (аналогично ведут себя и перекисные соединения):
Со2(СО)8 + О2 → 2СоО + 8СО |
(5.17) |
Несмотря на то, что СоО вновь переходит в условиях процесса в Со2(СО)8:
2СоО + 8СО + 2Н2 → Со2(СО)8 + Н2О, |
(5.18) |
реакция протекает медленно, а это сказывается на скорости самого процесса.
Диеновые и ацетиленовые углеводороды оказывают ингибирующее действие на реакцию гидроформилирования, образуя комплекс диолефина с НСо(СО)4 → С4Н6 НСо(СО)4.
Аналогично ведут себя и ацетиленовые соединения:
RC≡CR + Со(СО)8 → RC–CR + 2CO |
(5.19) |
(СО)3Со Со(СО)3
Примеси аммиака образуют с НСо(СО)4 соль, неактивную в реакции гидроформилирования:
NH3 + HCo(CO)4 → NH4Co(CO)4 |
(5.20) |
Сернистые соединения тормозят реакцию гидроформилирования, связывая Со в сульфаты:
Co2(CO)8 + 2H2S → 2CoS + 8CO + 2H2; |
(5.21) |
Co2(CO)8 + C2S → 2CoS + 8CO + C |
(5.22) |
134
До настоящего времени механизм реакции гидроформилирования еще полностью не выяснен. Общепризнанной считается схема механизма, предложенная Бреслоу и Хеком в 1961 г. Согласно данной схеме реакция гидроформилирования протекает по механизму цепного типа, при этом роль активных частиц, ведущих цепь, играют координационно-ненасыщенные соединения.
5.3.3. Реакционные устройства процесса гидроформилирования
Основное требование к реакционным устройствам – это обеспечение минимального выхода побочных продуктов. Максимально это достигается при проведении реакции в реакторе идеального вытеснения, в котором обеспечивается минимальная средняя концентрация альдегидов, а следовательно, создаются условия для минимального образования побочных продуктов.
По способу съема тепла применяемые реакторы делятся:
–на реакторы с внутренним теплосъемом;
–реакторы с внешним теплосъемом;
–реакторы комбинированного типа.
В реакторах с внутренним теплосъемом тепло снимается за счет подачи холодного сырья или продуктов гидроформилирования прямо
взону реакции. Все компоненты реакции подаются в зону реакции сни-
зу (рис. 5.2).
Достоинством аппаратов данного типа является простота конструкции и изготовления, недостатком – повышенный выход побочных продуктов.
Реакторы с внешним теплосъемом (рис. 5.3). Наиболее опти-
мальны в процессе гидроформилирования колонные аппараты со встроенными трубчатками либо теплообменные аппараты типа «труба
втрубе». В качестве охлаждающей жидкости используется деминерализованная вода. Такие аппараты, в частности, работают в Перми и Салавате. Преимущество таких аппаратов – близость к реактору идеального вытеснения, а значит, пониженный выход побочных продуктов.
135

Рис. 5.2. Реактор с внутренним теплосъемом
Рис. 5.3. Реактор с внешним теплосъемом
Реакторы комбинированного типа (рис. 5.4) позволяют совмес-
тить достоинства рассмотренных реакторов с внутренним и внешним теплосъемом. В этом аппарате первая зона (нижняя) работает как аппарат идеального перемешивания, а вторая зона (верхняя) – как аппарат идеального вытеснения. В первой зоне осуществляется первая часть реакции гидроформилирования до степени превращения олефина 50–70 %. Во второй зоне реакция проходит окончательно, наиболее рационально, с минимальным выходом побочных продуктов.
136
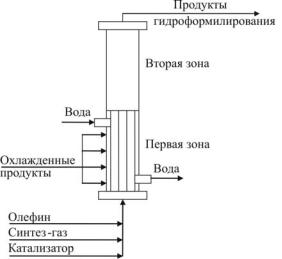
Рис. 5.4. Реактор комбинированного типа
Реакторы изготавливаются из обычной углеродистой стали, а их внутренняя часть футеруется тонким (2–3 мм) слоем хромоникелевой стали Х18Н9Т, устойчивой к СО, Н2 и гидрокарбонилу кобальта.
5.3.4. Технологические схемы процесса оксосинтеза
Классический процесс оксосинтеза включает в себя следующие стадии:
1) кобальтизацию (карбонилобразование) – получение карбонилов кобальта из металлического кобальта или из его солей:
2Со + 8СО → [Со(СО)4]2 ↔ 2НСо(СО)4; |
(5.23) |
2) гидроформилирование – взаимодействие олефина с СО и Н2 в присутствии карбонилов кобальта:
137

(5.24)
3) декобальтизацию – разложение карбонилов кобальта и выделение его из продуктов гидроформилирования:
2НСо(СО)4 ↔ [Со(СО)4]2 + Н2 → 2Со + 8СО + Н2 |
(5.25) |
Далее идут стадии гидрирования альдегидов в соответствующие спирты и ректификация продуктов оксосинтеза с выделением альдегидов и спиртов.
Технология процесса оксосинтеза в целом определяется принципами осуществления отдельных стадий. В настоящее время нет единой, общепринятой технологии оксопроцесса не только в России, но и в мире, поэтому эксплуатируются различные схемы:
–триадная;
–кизельгурная;
–нафтенатно-испарительная.
Они отличаются способами декобальтизации (извлечения кобальта из продуктов реакции и возвращения его в цикл).
5.3.4.1. Схемы с термической декобальтизацией
Схемы с термической декобальтизацией продуктов гидроформилирования (разложение карбонилов кобальта под действием температуры и давления водорода) осуществляются по трем вариантам:
1. Кобальт осаждается на развитой движущейся поверхности (обычно кизельгур), возвращаемой обратно на стадию кобальтизации – кизельгурная схема (рис. 5.5).
Основные недостатки схемы:
–эрозия аппаратуры;
–сложность отделения суспензии катализатора от продуктов синтеза на магнитных сепараторах.
138

Рис. 5.5. Кизельгурная схема оксопроцесса: 1 – реактор карбонилобразования и гидроформилирования; 2 – реактор гидроформилирования; 3, 4 – сепараторы; 5 – реактор декобальтизации; 6 – магнитный сепаратор; I – олефин; II – синтез-газ; III – катализатор; IV – продукты синтеза; V – горячий водород; VI – декобальтизированный продукт
нагидрирование
Процесс осуществляется в двух последовательно работающих реакторах. В первом реакторе 1 при температуре 150–170 °С и давлении 25–30 МПа идет образование карбонилов кобальта и частично реакция гидроформилирования. Заканчивается реакция во втором реакторе 2, в котором поддерживается температура на 10–15 °С выше по сравнению с первым реактором. Далее продукты гидроформилирования в сепараторах 3 и 4 отделяются от непрореагировавшего синтез-газа и поступают в реактор декобальтизации 5, которая идет при температуре 120–130 °С и давлении водорода 2,5–3 МПа. Осажденный на кизельгуре кобальт отделяется от продуктанамагнитном сепараторе6.
2.Кобальт выделяется в виде суспензии порошка в жидком продукте. Далее, после отделения от продуктов реакции, суспензия кобальта возвращается на стадию кобальтизации – порошковая схема. Эта схема практическиидентичнакизельгурнойи обладает теми же недостатками.
3.Триадная схема. В схему входят три основных аппарата – кобальтизер, где образуется раствор карбонилов кобальта в инертных углеводородах, реактор гидроформилирования, декобальтизер, где
139

разрушаются карбонилы кобальта и металлический кобальт отделяется от продукта (рис. 5.6).
Рис. 5.6. Триадная схема процесса: 1 – реактор гидроформилирования; 2, 5, 6 – сепараторы; 3а, 3б – реакторы кобальтизации и декобальтизации; 4 – реактор гидрирования; 7, 8 – ректификационные колонны; I – синтез-газ; II – пропилен; III – раствор катализатора; IV – декобальтизированный продукт; V – инертный растворитель; VI – водород; VII – изобутанол; VIII – н-бутанол;
IX – продуктыуплотнения
Согласно схеме синтез-газ, пропилен и раствор катализатора из реактора 3б подаются в реактор гидроформилирования 1. Процесс идет при температуре 170 °С и давлении 30 МПа. После отделения продуктов гидроформилирования от непрореагировавшего синтезгаза в сепараторе 2 они поступают на декобальтизацию в реактор 3а в токе водорода с осаждением кобальта на пемзе. Декобальтизация идет при температуре 100–130 °С и давлении 30 МПа. Продукты декобальтизации идут на гидрирование в реактор 4, туда же подается водород. Гидрирование масляных альдегидов проводят при температуре 150 °С и давлении водорода 30 МПа. Продукты гидрирования в сепараторах 5 и 6 отделяются от непрореагировавшего водорода и поступают на разделение в колонны 7 и 8. Водород из сепараторов 5 и 6 возвращается в рецикл.
140