
Технология органического и нефтехимического синтеза
..pdf10.4.КАТАЛИЗАТОРЫ ПРОЦЕССА
Воснове селективных катализаторов синтеза углеводородов из оксида углерода и водорода, созданных для данной технологии, лежат кобальтовые системы [19–12], в присутствии которых образуются преимущественно линейные алканы, что обеспечивает высокие моторные и экологические характеристики топлив. Выход и состав целевых продуктов синтеза зависят от состава катализатора и условий проведения синтеза [14–18], в частности, от температуры, давления, о6ъемной скорости подачи синтез-газ. Катализаторы Со/носитель готовились согласно разработанному регламенту приготовления катализатора методом пропитки носителя водным раствором нитрата кобальта. Для приготовления катализаторов в качестве
носителей использвали силикагель (SiO2) марки КСК и γ-Аl2О3. Содержание кобальта в катализаторах не превышало 15 мас.%. Носители предварительно прокаливали в потоке воздуха 5 ч при температуре 45 °С, катализатор предварительно восстанавливался в потоке водорода в течение 5 ч при Р = 10 атм и t = 45 °С. Синтез углеводо-
родов из СО и H2 осуществляется в интервале температур 190– 240 °С, в интервале давлений 1–15 атм и в интервале относительных объемных скоростей подачи синтез-газа 100–1200 ч–1. Расчет моле- кулярно-массового распределения жидких продуктов синтеза осуществляется нахождением вероятности роста углеводородной цепи из уравнения Шультца–Флори:
lg(mN/N) = lg(ln2α) + (lgα)N,
где mN – массовая доля парафина с углеродным номером N, рассчитанная по хроматограмме. Экспериментальные данные по молеку- лярно-массовому распределению линеаризовывались по методу наименьших квадратов, величина определялась из угла наклона прямо на оси N.
Анализ влияния давления на синтез углеводородов из СО и Н2 в присутствии кобальтового катализатора проводился при оптимизированных предварительно двух других параметрах – при температуре 190–200 °С и объемной скорости подачи синтез-газа 300 ч–1 .
221
Согласно полученным данным, представленным на рис. 10.2, а, конверсия монооксида углерода равномерно возрастала с 20 до 86 % с ростом давления от 1 до 15 атм. Аналогичным образом изменялась удельная активность катализатора, отражающая количество монооксида углерода, прореагировавшего за единицу времени на 1 г активного компонента катализатора (Со). Продуктами синтеза углеводородов являются жидкие углеводороды (С5+), газообразные углеводороды (С1–С4), СО2, Н2О. Повышение активности катализатора, обусловленное ростом давления в системе, привело к увеличению выходов всех продуктов синтеза. Однако если выход жидких углеводородов увеличивается значительно (при повышении давления с 1 до 15 атм этот показатель вырос в 4,7 раза, т.е. с 35 до 167 г/м3), то общий выход газообразных продуктов (углеводородов С1–С4 и СО2) возрос лишь с 7 до 15 г/м3 (рис. 10.2, б). Это привело к тому, что селективность катализатора в отношении образования жидких углеводородов повысилась с 83 до 93 % (рис. 10.2, в). Селективность в отношении газов (например, метана) немного понизилась.
Таким образом, производительность кобальтового катализатора значительно возросла (рис. 10.2, г). При повышении давления с 1 до
15 атм этот показатель увеличился в 4,6 раза, т.е. с 12,6·10–3 до
58,5·10–3 г Кат.ч.
Повышение давления в системе приводило также к увеличению вероятности роста углеводородной цепи, выражаемой показателем в уравнении Шультца–Флори. Этот фактор увеличивается с 0,62 до 0,83–0,84 при повышении давления с 1 до 10 атм и затем несколько снижается (до 0,74) при дальнейшем росте давления до 15 атм. Таким образом, оптимальная полимеризующая активность катализатора достигается при 10 атм, что составляет оптимизированную величину для процесса по давлению (рис. 10.2, д).
Анализ влияния относительной объемной скорости подачи син- тез-газа на синтез углеводородов из СО и Н2, определяющий эффективность всего процесса в целом, осуществлялся в интервале 100– 200 ч–1, т.е. при условиях, заведомо удовлетворяющих любую перспективу развития процесса. Поскольку увеличение объемной скорости
222
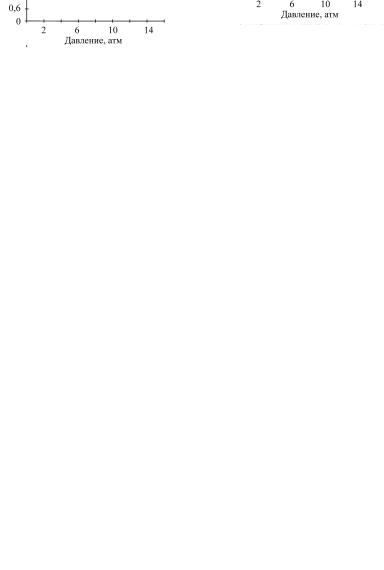
а |
б |
в |
г |
д
Рис. 10.2. Анализвлияниядавлениянахарактеристикипроцесса
223

подачи синтез-газа приводило к заметному снижению конверсии СО, одновременно с объемном скоростью осуществлялось повышение температуры синтеза с целью осуществления постоянной конверсии СО. При увеличении объемной скорости до 300, 600, 1200 ч–1 соответственно температура составляла 190, 210, 220 °С.
Установлено, что повышение объемной скорости приводит к снижению образования жидких и повышению газообразных продуктов синтеза (рис. 10.3, а). Причем оба эти показателя изменились незначительно, в интервале 300–1200 ч–1 выход жидких углеводородов снизился на 13 г/м3, а выход газов возрос на 10 г/м3.
а |
б |
в
Рис. 10.3. Влияниеобъёмнойскоростинахарактеристикипоцессасинтеза
224
Таким образом, селективность в отношении образования жидких углеводородов уменьшилась с 89 до 76 % (рис. 10.3, б), а селективность в отношении образования газообразных продуктов повысилась, например, селективность в отношении образования метана возросла с 6 до 14 %. Естественно, что объемная скорость не оказывала влияния на производительность катализатора при условии, что кон-
версия СО поддерживалась постоянно. Производительность составляла ≈30·10–3 г/гКат·ч.
Как и следовало ожидать, с увеличением объемной скорости подачи синтез-газа с 300 до 1200 ч–1 уменьшилась вероятность роста углеводородной цепи: фактор снизился с 0,89 до 0,83 (рис. 10.3, в).
Анализ влияния температуры синтеза углеводородов из СО и Н2 на его основные показатели было целесообразно провести, как следует из изложенного выше, при наибольшей скорости подачи синтезгаза (1200 ч–1); температурный предел был повышен до 240 °С.
Как видно из рис. 10.4, а, повышение температуры синтеза с 210 до 240 °С приводит к увеличению удельной активности катализатора в 2,5 раза. Конверсия СО на катализаторе также равномерно возрастала с повышением температуры синтеза и при 240 °С в 2,5 раза превысила значение, соответствующее 210 °С.
Повышение активности катализатора приводило к увеличению выхода всех продуктов синтеза (рис. 10.4, б). Так, общий выход газообразных продуктов (т.е. С1–С4, и СО2) равномерно возрастал во всем интервале температур и в целом повысился втрое (с 16 до 50 г/м3). Выход жидких углеводородов, составлявший 26 г/м3 при 210 °С, при 220 °С вырос в 2,5 раз (до 64 г/м3), а затем изменялся мало и составил 64–67 г/м3.
В результате селективность катализатора в отношении образования жидких углеводородов была максимальной (76 %) при 220 °С (рис. 10.4, в). При этой же температуре наблюдается минимальная селективность в отношении газообразования, например, этот показатель для метана составил 14 %.
Производительность кобальтового катализатора при повышении температуры с 210 до 220 °С возросла в 2,5 раза, т.е. с 12 до
225
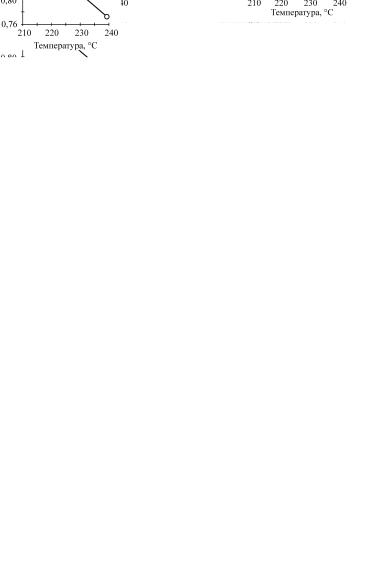
а |
б |
в |
г |
д
Рис. 10.4. Анализвлияниятемпературынахарактеристики процессасинтеза
226
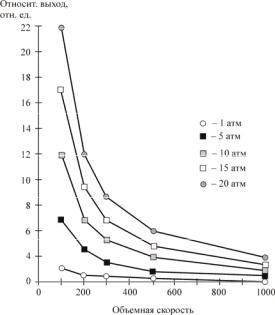
30 г/кгКат·ч (рис. 10.4, г). Дальнейшее повышение температуры синтеза практически не оказывало влияния на этот показатель.
Как и следовало ожидать, повышение температуры синтеза привело к снижению вероятности роста углеводородной цепи (рис. 10.4, д). При температуре 210 °С фактор α был довольно высоким и составил 0,88. При этом около 56 % жидких углеводородов приходилось на дизельную фракцию С11–С18. Однако повышение температуры на 30 °С привело к заметному снижению этого показателя, и доля этой фракции уменьшилась до 29 % (доля бензиновой фракции, т.е. угле-
водородов С5–С10, возросла с 30 до 66 %).
Обобщенные результаты представлены на рис. 10.5, где наглядно отражено, что выход жидких углеводородов (г/м3 синтез-газа) возрастает при повышении давления и снижается при увеличении объемной скорости синтез-газа.
Рис. 10.5. Влияниедавленияиобъёмнойскорости наотносительныйвыходжидких углеводородов
227
Показано, что при каждом давлении и каждой объемной скорости подачи синтез-газа существует оптимальная температура синтеза углеводородов из СО и Н2 в присутствии кобальтовых катализаторов, при которой наблюдаются наибольшие выход жидких углеводородов и селективность их образования.
Разработана модель, позволяющая оценить (прогнозировать) основные показатели процесса (выход жидких углеводородов, реальную и максимальную производительность) при различных условиях синтеза, не только включающих, но и существенно расширяющих условия испытаний, что повышает перспективные возможности технологии.
10.5. ТЕХНОЛОГИЧЕСКАЯ СХЕМА ПЕРЕРАБОТКИ ПРИРОДНОГО ГАЗА В ЖИДКОЕ ТОПЛИВО
Полученные результаты обеспечили следующие характеристики процесса, которые были положены в основу разработки технологической схемы:
–высокие выходы углеводородов 80–85 %, что исключает необходимость рециклинга;
–максимальная селективность в области вероятности роста
цепей (ВРЦ) распределения Шультца–Флори = 0,82…0,86, соответствующая наибольшим относительным выходам по дизельно-реактив- ным фракциям С7–С20 (более 75 %), что исключает необходимость блока гидрокрекинга (в отличие от технологии Shell, где высокие выходы достигаются в области тяжелых парафинов, требующих для перевода их в моторные фракции дополнительной стадии гидрокрекинга);
–высокие цетановые числа дизельного топлива за счет низкого содержания олефинов (основной компонент –н-парафины), что позволяет исключить блок гидростабилизации продуктов синтеза;
–возможность регулирования содержания изопарафинов для существенного понижения температуры застывания и «холодной» вязкости топлива и получения зимних сортов дизельного топлива без дополнительного блока гидроизомеризации;
228
–выявленная в процессе испытаний возможность исключения
вряде случаев также и блока ректификации, т.е. сведение технологии к двухстадийному однопроходному режиму;
–высокая термостабильность каталитической системы с сохранением данных характеристик в течение года в условиях эксплуатации в Arge-реакторе с неподвижным слоем.
Технологическая схема установки для получения широкой дизельной фракции (двухстадийсный режим) представлена на рис. 10.6, а. Стадия фракционирования, необходимая при выделении отдельно реактивной (керосино-лигроиновой) и бензиновой фракции, представлена на рис. 10.7.
Стадия конверсии природного газа в синтез-газ. Природный газ с давлением до 1,2 МПа поступает в змеевиковый подогреватель Т1 (см. рис. 10.6) печи конверсии П, где нагревается дымовыми газами, отходящими от этой печи, до температуры 350–400 °С (все параметры технологических потоков указаны на схеме). Далее нагретый природный газ поступает в смеситель пара и газа М2, куда подается пар с давлением 1,5 МПа и температурой 200 °С из оборотной замк-
нутой системы. Из смесителя М2 парогазовая смесь поступает в змеевиковый подогреватель Т3 печи конверсии, где нагревается за счет тепла дымовых газов до температуры 500–570 °С. Углекислый газ давлением 1 МПа из системы выделения СО2 поступает в змеевиковый подогреватель Т2, где нагревается за счет тепла дымовых газов до температуры 500–570 °С. Из подогревателя Т2 углекислый газ поступает в смеситель М1, куда подается также парогазовая смесь из подогревателя Т3.
Полученная парогазоуглекислотная смесь направляется из смесителя М1 в коллектор исходной смеси печи конверсии, из которого распределяется по 6 реакционным трубам. В реакционных трубах на никелевом катализаторе типа ГИАП-3-6Н (6 % Ni), ГИАП-18 и других происходит реакция взаимодействия метана (CH4) с углекислым газом (СО2) и водным паром (Н2О) с образованием водорода (Н2) и монооксида углерода (СО). Полученный конвертированный газ (синтез-газ) выходит из реакционных труб с температурой 750–850 °С
229

230
Рис. 10.6. Технологическаясхемаустановки(двухстадийныйрежим) переработкиприродногогаза