
Технологическое обеспечение качества поверхностного слоя деталей пр
..pdfния показывает, что износ при микровыглаживании имеет сложный комбинированный характер. В этом процессе можно выделить две основные причины изнашивания алмазных микровыглаживателей.
Первая – это фрикционно-усталостное разрушение. Накопление усталостных повреждений в поликристаллической структуре синтетического алмаза приводит к растрескиванию и выкрашиванию рабочей поверхности. Это основная причина разрушения алмаза. Признаки фрикционно-усталостного разрушения рабочей поверхности
впроцессе микровыглаживания в области пятна контакта появляются первыми. По мере увеличения износа этого вида начинают проявляться признаки износа второго вида – скалывание или хрупкое разрушение. Характерным признаком этого является появление впадин относительно больших размеров. Хрупкий износ, проявляющийся
вскалывании частиц рабочей поверхности алмаза, не характерен для новых микровыглаживателей. Его рабочие поверхности обладают достаточной прочностью и противостоят воздействию твердых включений и карбидов в материале обрабатываемой поверхности и свободного абразива, проникающего в зону обработки из внешней среды. Первичное накопление усталостных повреждений приводит к ослаблению рабочей поверхности синтетического алмаза, и на площадке износа начинают отмечаться признаки хрупкого разрушения. Рабочая поверхность синтетического алмаза в пределах площади пятна контакта, подвергнутая усталостно-фрикционному и хрупкому износу, имеет хорошо выраженное зернистое строение и сохраняет кристаллическую структуру.
Известно, что тепловой фактор, приводящий к графитизации рабочей поверхности алмаза, является одной из вероятных основных причин изнашиванияалмазныхвыглаживателейвпроцессеобычноговыглаживания.
При проведении исследований работоспособности алмазных микровыглаживателей лишь в отдельных случаях на локальных участках рабочейповерхностиалмазав пределахпятнаконтакта былообнаруженокосвенное проявление признаковграфитизации. В данном случаетаким признаком являлось появление пористых участков на площадке износа. Вцелом графитизации поверхности при микровыглаживании не проис-
91
ходит, она встречается лишь в отдельных случаях. Графитизированные участки или участки с пористостью отмечались на площадках износа умикровыглаживателей после прохождения примерно 30–50 % пути тренияLм. Причемихпоявлениепримерносовпадалосвозникновениемпризнаков хрупкого износа – углублений больших размеров, когда наблюдалсяскачоквухудшениишероховатостирабочейповерхностиалмаза.
Основной причиной графитизации алмаза при поверхностном пластическом деформировании является температурный фактор. Вестественных условиях превращение алмаза в графит наблюдается при температуре около 800° C. Однако в условиях трения в присутствии некоторых катализаторов типа железа и никеля графитизация может происходить при сравнительно небольших температурах. Температурный фактор оказывает существенное влияние на протекание процесса обычного выглаживания. Наибольшее влияние на температуру в зоне контакта оказываютскоростьвыглаживанияидавлениевзонеконтакта[39].
При алмазном микровыглаживании проявление температурного фактора незначительно и он не оказывает существенного влияния на износостойкость и работоспособность микровыглаживателей. В сравнении с обычным выглаживанием алмазное микровыглаживание миниатюрных и маложестких деталей осуществляется в значительно более мягких режимах. Так, скорости микровыглаживания на порядок ниже скоростей выглаживания. Если обычное алмазное выглаживание производится со скоростями скольжения около 100 м/мин [40], то скорости микровыглаживания Vм находятся в интервале 15–22 м/мин. Процесс микровыглаживания миниатюрных и маложестких деталей производится при еще более низких скоростях, так как при микровыглаживании поверхностей деталей, диаметры которых находятся в пределах 1–3 мм, даже на максимальных оборотах шпинделей используемых станков (до 2000 об/мин) обеспечиваются скорости микровыглаживания 7…19 м/мин. Контактное давление p в зоне контакта при микровыглаживании также ниже, чем контактное давление при обычном алмазном выглаживании. На понижение контактного давления при микровыглаживании влияет масштабный фактор, так как рабочая поверхность микровыглаживателя малого радиуса, внедряемая
92
вобрабатываемую поверхность, является сама по себе значительным концентратором напряжений, за счет чего упругопластическое деформирование поверхностного слоя при микровыглаживании может производиться при меньших значениях силовых нагрузок.
Появление при микровыглаживании в отдельных случаях локальной пористости на площадке износа, которая может быть признаком графитизации поверхности алмаза, очевидно, может быть объяснено тем обстоятельством, что на этапе развития хрупкого износа скапливающиеся в крупных углублениях площадки износа частицы металла начинают взаимодействовать с обрабатываемой поверхностью. Очевидно, что коэффициент трения по обрабатываемой поверхности таких насыщенных металлом локальных участков рабочей поверхности выше, чем коэффициент трения алмаза по металлу. Соответственно на таких участках рабочей поверхности микровыглаживателя следует ожидать повышения температуры, которая иможет являться причиной появления локальных признаков графитизации поверхности алмаза. Однако
вцелом графитизация алмазных микровыглаживателей не характерна для процесса микровыглаживания и не может лимитировать работоспособность микровыглаживающих инструментов, изготовленных из синтетическихполикристаллическихалмазовтипа АСПК.
Показатели качества (шероховатость, микротвердость, микроструктура, напряжения и т.п.) в поверхностном слое, сформированном
впроцессе микровыглаживания, зависят от характера воздействия на обрабатываемую поверхность микровыглаживающего инструмента. Обрабатываемая поверхность также оказывает воздействие на деформирующий инструмент. Таким образом, износ микровыглаживателя определяется взаимодействием деформирующего элемента – синтетического алмаза – с материалом обрабатываемой поверхности.
Одним из основных и наиболее значимых параметров процесса
микровыглаживания является сила микровыглаживания Fм. Однако сама по себе сила микровыглаживания не может с необходимой полнотой характеризовать процесс микровыглаживания.
Более полной и определяющей характеристикой силового взаимодействия микровыглаживателя и обрабатываемой поверхности, как и при
93
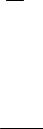
любом другом методе поверхностного пластического деформирования, являетсяконтактноедавлениевобластиконтактаинструментаидетали.
Для характеристики и исследований процесса алмазного микровыглаживания с достаточной точностью значение удельного контактного давления р можно определить по формуле (Па)
p FFм ,
где Fм – нормальная сила микровыглаживания, Н; F – площадь пятна контакта микровыглаживателя и детали, м2.
При микровыглаживании, когда микровыглаживатель и деталь представляют собой скрещивающиеся в пространстве цилиндры, пятно контактаимеетформуэллипсаиегоплощадьопределяетсяпоформуле(м2)
F Aк.и4Bк.и ,
где Ак.и – большая ось эллипса пятна контакта в процессе износа; Вк.и – малая ось эллипса пятна контакта в процессе износа.
Анализ схемы взаимодействия микровыглаживателя и обрабатываемой поверхности (см. рис. 33), пятен контакта нового и изношенного микровыглаживателя (см. рис. 34), а также обследование под микроскопом рабочих поверхностей микровыглаживателей с применением изложенной выше методики определения пятна контакта показывают, что пятно контакта и формирующаяся площадка износа практически равны. Результаты анализа позволяют сделать вывод, что контакт микровыглаживателя и обрабатываемой поверхности происходит по всей площадке износа инструмента.
Характер изменения удельного контактного давления р в зоне контакта микровыглаживателя и обрабатываемой поверхности в зависимости от длины рабочего пути скольжения микровыглаживателя графически представлен кривыми гиперболического типа для сталей на рис. 31 и цветных сплавов на рис. 32.
Очевидно, что увеличение размеров площадки износа приводит к уменьшению удельных контактных давлений в зоне контакта рабочей поверхности микровыглаживателя и обрабатываемой поверхности. Уменьшение контактных давлений в процессе работы инструмента приводит к уменьшению величины износа.
94
3.2.2. Износостойкость алмазных микровыглаживателей
Износостойкость алмазных микровыглаживателей – один из важных аспектов технологического обеспечения качества и производительности алмазного микровыглаживания миниатюрных деталей на основе комплексного критерия. В связи с этим необходимо экспериментально исследовать влияние свойств обрабатываемых материалов на износ инструмента.
Влияние свойств обрабатываемых материалов на износ алмаз-
ных микровыглаживателей. Износ контактирующих поверхностей
впарах трения как деталей машин, так и рабочих поверхностей инструментов, производящих технологические операции обработки деталей, представляет собой процесс, в котором имеют место сложные физические явления. Наиболее значительно износ выражен при взаимодействии двух поверхностей в условиях трения скольжения, т.е. в условиях, типичных для обработки металлов выглаживающими инструментами,
втомчислеимикровыглаживателями. При такомтрении наизнос взначительной степени влияет химический состав иструктурно-механи- ческоесостояниетрущихсяповерхностей взаимодействующейпары.
Износостойкость алмазных микровыглаживателей является интегральной характеристикой сложного взаимодействия различных факторов, влияющих на состояние материала деформирующего элемента микровыглаживателя, и в значительной мере обусловлена внешними условиями трения.
Известно, что твердость материалов является одной из важнейших триботехнических характеристик. При обработке деталей поверхностным пластическим деформированием существует тенденция к увеличению износа инструмента при повышении твердости обрабатываемого материала. При алмазном микровыглаживании также с повышением твердости обрабатываемых миниатюрных деталей наблюдается возрастание износа алмазных микровыглаживателей. Это в первую очередь связано с тем, что для упругопластического деформирования при микровыглаживании твердых материалов требуется увеличение силы микровыглаживания, что соответственно приводит к увеличе-
95
нию контактного давления в зоне контакта инструмента и обрабатываемой поверхности. Это вызывает увеличение интенсивности изнашивания рабочей поверхности микровыглаживателя.
Увеличение нагрузки при обработке более твердых материалов приводит к изменению коэффициента трения, также прямо влияющего на износ инструмента. Коэффициент трения в области упругого
ипластического контактов имеет разнохарактерную связь с нагрузкой. Эта связь объясняется молекулярно-механической теорией трения. В условиях упругопластического контакта инструмента и обрабатываемой поверхности коэффициент трения зависит от изменения соотношения между этими составляющими. Для различных металлов
иих сплавов это соотношение может значительно изменяться. Значительное влияние на интенсивность изнашивания деформи-
рующего элемента оказывает модуль нормальной упругости обрабатываемого материала. Модуль нормальной упругости и коэффициент жесткости кристаллической решетки являются основными характеристиками сил связи в решетке материала, определяющими его сопротивляемость внешнему силовому воздействию. Следовательно, чем выше эти показатели, тем интенсивнее износ обрабатывающего эти материалы инструмента.
Известно, что существует глубокая связь между коэффициентом трения, влияющим на износ инструмента, и физико-механическими свойствами обрабатываемых материалов. На коэффициент трения в области контакта оказывают влияние как твердость обрабатываемого материала, так и его модуль нормальной упругости. Необходимо отметить, что однозначной зависимости между модулем нормальной упругости и интенсивностью изнашивания не существует.
Таким образом, при алмазном микровыглаживании каждого конкретного материала на износостойкость микровыглаживающего инструмента и в конечном итоге на его работоспособность оказывает влияние целый комплекс факторов, определяемых свойствами обрабатываемого материала.
Известны многочисленные работы, в которых рассмотрены процессы износа деталей и выглаживающих инструментов. Проведены
96
исследования различных условий, при которых наблюдается процесс износа. По полученным результатам имеются разнообразные выводы и самые разнообразные суждения и рекомендации.
По условиям своей работы алмазные микровыглаживатели приближаются к условиям работы инструментов, работающих методом выглаживания. Поэтому для этих видов инструментов существует общность параметров, характеризующих износ.
Одной из закономерностей износа выглаживающих инструментов является нелинейность зависимости интенсивности износа от некоторых механических характеристик обрабатываемых материалов, например твердости, а также от удельного давления на контактирующих поверхностях. Из всей совокупности факторов, влияющих на интенсивность и величину износа выглаживающего инструмента, большое значение имеют свойства обрабатываемого материала. Каждый тип материала обладает своими свойствами, определяющими условия упругопластического деформирования металла в поверхностном слое. Установлено, что пластическая деформация в поверхностном слое значительно зависит от свойств обрабатываемого материала.
Работоспособность каждого вида рабочего инструмента, его стойкость определяют практические режимы выполнения технологических операций, потребность в инструментах, производительность труда и экономичность процесса.
Использование синтетических алмазов для изготовления выглаживающих инструментов целесообразно. Исследования и практическое использование алмазных выглаживающих инструментов показали их высокие выглаживающие свойства при обработке большинства металлов и их сплавов [39]. Однако некоторые существующие ограничения вприменении синтетических алмазов вметаллообработке, связанные с износом и склонностью к выкрашиванию [38], вызывают необходимость объективного доказательства пригодности использования синтетических алмазовдляоснащения микровыглаживателей.
Исследования износа и износостойкости алмазных микровыгла-
живателей. Чтобы оценить работоспособность алмазного микровыглаживателя, его способность сопротивляться износу и выдерживать нагруз-
97
ки в процессе микровыглаживания, возникла необходимость выполнить серию исследований износа и износостойкости алмазных микровыглаживателей. Приведем здесь результаты проведенного нами исследования износа цилиндрической рабочей поверхности микровыглаживателя в зависимости от длины пути трения при обработке образцов из четырех типов материалов: конструкционной стали 20, легированной стали 16Х16Н3МАДицветныхсплавов: латуниЛС59-1ТидюралюминияД1Т.
Хорошо налаженное отечественной промышленностью производство синтетических поликристаллических алмазов типа карбонадо и баллас дает возможность изготавливать из них алмазные микровыглаживающие инструменты. Для выполнения процессов алмазного микровыглаживания спроектированы и изготовлены микровыглаживатели из синтетических поликристаллических алмазов АСПК-3 типа карбонадо. Для проведения исследований работоспособности были использованы микровыглаживатели с радиусами Rм цилиндрических рабочих поверхностей 0,1; 0,2 мм. Данные микровыглаживатели были изготовлены путем доработки и переточки из стандартных наконечников для выглаживания, соответствующих ТУ 2-037-100–84.
До начала исследований было проведено обследование деформирующих элементов всех микровыглаживателей, предназначенных для работы. Данные микровыглаживатели представляли собой инструменты, еще не использованные в работе.
Состояние рабочих поверхностей алмазных микровыглаживателей было визуально обследовано сначала с помощью биологического микроскопа МБС-9 при 56-кратном увеличении. Затем более детальное обследование всех микровыглаживателей было выполнено под микроскопом МИМ-7 при 110-кратном увеличении. Все последующие исследования рабочих поверхностей в процессе работы инструментов производились с помощью микроскопа МИМ-7.
Под микроскопом у всех новых микровыглаживателей, полученных после заточки, цилиндрическая рабочая поверхность имеет вид сплошной и гладкой поверхности черного или серого цвета иногда с металлическим блеском без видимых границ между отдельными блоками кристаллов.
98
Исследование позволило установить, что отдельные микровыглаживатели в состоянии поставки имеют следующие дефекты
вцентральных областях рабочих частей деформирующих элементов:
1)одиночные трещины значительных размеров в центральных частях рабочих поверхностей. На трещинах, как правило, просматриваются отдельные локальные микровыкрашивания;
2)обнажения металлических включений на боковых плоскостях деформирующих элементов из поликристаллических алмазов.
Выявленные дефекты являются скрытыми внутренними дефектами синтетических поликристаллических алмазов карбонадо типа АСПК-3 и связаны с технологией их получения. На качество стандартных выглаживателей, изготовленных по ТУ 2-037-100–84, они существенного влияния не оказывают и обнаруживаются только при переточке деформирующих элементов при изготовлении микровыглаживателей, когда для формирования цилиндрической рабочей поверхности верхняя часть алмаза снимается.
Обнаруженные дефекты внутреннего строения синтетических алмазов АСПК-3 не снижают работоспособности стандартных выглаживателей. Однако для микровыглаживателей данные дефекты являются неприемлемыми. Поэтому была выполнена выбраковка дефектных микровыглаживателей по указанным выше признакам, количество дефектных составило примерно 10 процентов.
При изготовлении алмазных микровыглаживателей необходимо обеспечивать надежный контроль рабочих поверхностей для предотвращения поломок инструментов в процессе их дальнейшей эксплуатации и предотвращения брака в работе.
На основании предварительных исследований микровыглаживателей перед их испытаниями на работоспособность были сделаны следующие выводы:
1.Алмазные микровыглаживатели можно изготавливать посредством простой доработки из существующих стандартных выглаживателей, напримернаконечниковдлявыглаживания(ТУ2-037-100–84).
2.Синтетические поликристаллические алмазы карбонадо типа АСПК-3 хорошо выдерживают режимы заточки цилиндрических поверхностей малых радиусов на оптико-заточных станках и обес-
99
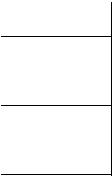
печивают заданное качество рабочих поверхностей микровыглаживающих инструментов.
Для выяснения работоспособности алмазных микровыглаживателей при обработке различных типов материалов были проведены исследования износа, износостойкости, а также сглаживающей и упрочняющей способностей инструментов. Типы обрабатываемых материалов и режимы их обработки представлены в табл. 4. К основным технологическим режимам микровыглаживания в данных исследованиях относятся радиус микровыглаживателя Rм, сила микровыглаживания Fм, скорость микровыглаживания Vм и подача микровыглаживания Sм. Для каждого типа материала образцов, на которых проводились исследования, установлены соответствующие режимы.
Таблица 4 Характеристики образцов для микровыглаживания
Материал |
Диаметр |
Микротвердость |
Шероховатость |
|
D, мм |
HV20, МПа |
Rz, мкм |
||
|
||||
Сталь 20 |
5,0 |
2045 |
7,5 |
|
|
|
|
|
|
Сталь |
5,0 |
3200 |
3,0 |
|
16Х16Н3МАД |
||||
|
|
|
||
Латунь ЛС59-1Т |
6,0 |
1360 |
5,4 |
|
|
|
|
|
|
Дюралюминий |
7,0 |
860 |
11,6 |
|
Д1Т |
||||
|
|
|
Использованные режимы микровыглаживания являются оптимальными, получены на основании результатов проведенных ранее исследований процесса алмазного микровыглаживания и учитывают свойства каждого конкретного обрабатываемого материала. В количественном отношении существенное различие установлено для тех режимов, которые определяют силовое взаимодействие обрабатываемого материала и обрабатывающего инструмента. Для более твердых материалов типа сталей использованы микровыглаживатели с радиусами 0,1 мм, для более мягких цветных сплавов – с радиусами
100