
5679
.pdf
вается глубина резания t = 4,25 мм для обработки |
по наружному диаметру 81,5 |
мм; для обработки шейки 71,5 мм и шейки 61,5 |
мм. |
Определение подачи
При черновой обработке выбор подачи производится всегда в два этапа: а) определяется величина подачи по нормативам;
б) производится уточнение подачи после проверки её по целому ряду ограничений (таких как прочность державки резца, прочность пластинки твёрдого сплава; усилие, допускаемое механизмом подач станка; крутящий момент или эффективная мощность резания, допускаемые механизмом главного движения станка; жёсткость системы станок – приспособление – деталь – инструмент (СПИД); заданная точность и шероховатость обработанной детали).
В зависимости от глубины резания, свойств обрабатываемого и режущего материала, геометрических параметров резца по нормативной таблице (приложение А таблица А2) определяется подача на 1 оборот детали, величина которой для обработки стали резцом с размером державки 25 х 25 мм при точении детали диаметром до 100 мм с глубиной резания = 5 мм рекомендуется в пределах 0,7 – 0,9 мм/об.
Принимается среднее значение подачи S = 0,8 мм/об. Выбранная подача сопоставляется с паспортными данными по приложению А таблице А1. Ближайшее значение подачи по паспорту станка S = 0,78 мм/об., которое и принимается для работы.
Выбор скорости резания
Исходя из принятой стойкости режущего инструмента и установленных значений глубин резания и подачи, а также учитывая механические свойства обрабатываемого материала, определяется нормативная скорость резания по таблицам. В них для каждого вида обрабатываемых материалов и применяемых режущих инструментов приводятся значения скорости резания.
По приложению А таблице А3 определяется скорость резания. Для обработки стали σв = 72 кг/мм2 с t = до 8 мм, S = 0,78 мм/об скорость резания для обработки резцом с углом в плане γ = 45˚ составляет V = 58 м/мин и для работы с резцом γ = 90˚, V = 51 м/мин.
71

Определение числа оборотов шпинделя в минуту
С учётом найденной скорости производится расчёт числа оборотов шпинделя: а) для первого перехода, при D = 90 мм
б) для второго перехода, при D = 81,5 мм
в) для третьего перехода, при D = 71,5 мм
Расчётное число оборотов корректируется по паспортным данным станка nn и берётся ближайшее меньшее n (приложение А таблица А1).
Подбирается ближайшее значение для каждого перехода. В данном примере для всех трёх переходов число оборотов n = 200 об./мин.
Отсюда после корректировки находим фактическую скорость резания: а) для первого перехода;
б) для второго перехода D = 81,5 мм
в) для третьего перехода D = 71,5 мм
Проверка выбранного режима по мощности
Согласно паспорту, станок в пределах выбранного режима имеет постоянную мощность на разных числах оборотов. Проверку режима производим по мощности.
По приложению А таблице А4 определяется мощность, потребная на резание. При обработке стали σв = 72 кг/мм2, t = 4,25 мм, S = 0,78 мм/об. и V = 57 м/мин мощность на резание (по наиболее загруженному переходу) составляет 5,8 кВт.
Согласно паспортным данным, мощность на шпинделе по приводу станка при работе с числом оборотов шпинделя n = 200 и минуту составляет 8,0 кВт, т.е.
72
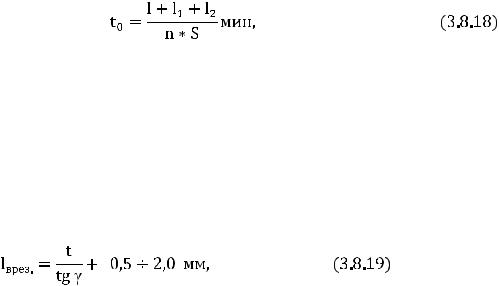
больше мощности, потребной на резание. Следовательно, установленный режим резания по мощности осуществим.
Расчёт составных частей нормы времени
Определение основного (технологического времени) Основное технологическое время определяется по формуле
где l – длина обрабатываемой поверхности;
– величина врезания и перебега резца, в мм;
– дополнительная длина на взятие пробной стружки, в мм; n – число оборотов в минуту;
S – подача на один оборот шпинделя, в мм/об.
Длиной врезания называется путь, который проходит режущий инструмент от момента начала резания до момента, когда достигнута полная глубина резания:
где γ – главный угол в плане резца в градусах; t – глубина резания.
Чем больше глубина резания, тем больше величина врезания.
Может быть такая обработка, когда нет выхода (перебега) резца из зоны резания (при обработке валов упорно-проходными резцами). Величина перебега при обработке на проход (т.е. с выходом из зоны резания) составляет 1 – 5 мм в зависимости от размеров обработки.
Длина проходов при взятии пробных стружек определяется так. Вначале протачивается небольшой кусок и проверяется, обеспечивается ли нужный размер. Если нет, то протачивается ещё кусок, пока не достигнут заданного размера. На настроенных станках работа ведётся без пробных стружек, поэтому в формулу основного времени величину l2 не включают. Она имеет место при точной обработке или при грубой обработке в условиях единичного производства. В зависимости от точности l2 берётся в пределах 5 – 10 мм.
73
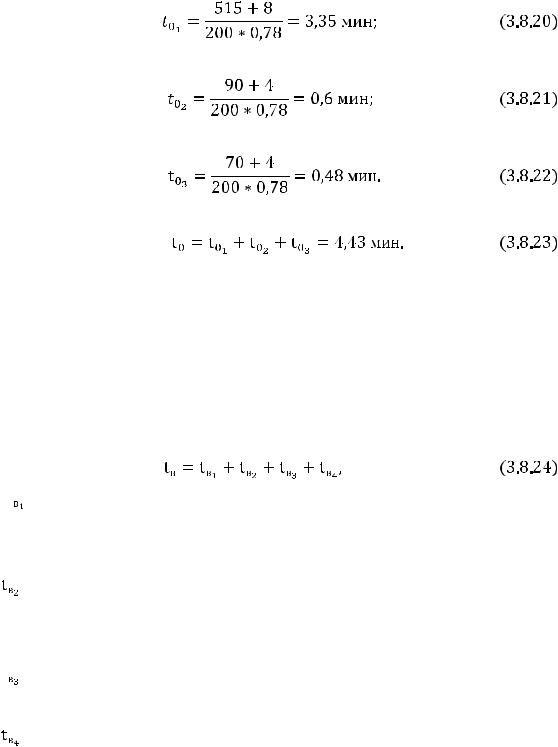
Согласно приложению А таблице А5 величина врезания и перебега для резца с углом в плане γ = 45˚ принимается равной 8 мм и для резца с углом γ = 90˚ равной 4 мм.
Обработка детали производится с установкой резца по лимбу без пробных стружек, поэтому дополнительная длина на взятие пробной стружки не учитывается. Тогда для поверхности 1:
для поверхности 2:
для поверхности 3:
Основное технологическое время на операцию равно:
Определение вспомогательного времени
Элементы вспомогательного времени повторяются с каждой обрабатываемой деталью либо в определённой последовательности через некоторое количество деталей. При работе на токарных станках вспомогательное время, как правило, ручное или машинно-ручное включает в себя следующие элементы:
где – время на установку и снятие детали (время на установку, закрепле-
ние, выверку, раскрепление и снятие детали; в этот комплекс входит время на пуск и остановку станка);
– время, связанное с переходом (время на подвод инструмента, уста-
новку на размер по лимбу или по пробной стружке, включение и выключение подачи, отвод инструмента в исходное положение);
– время на контрольные измерения (время на окончательные и пробные измерения);
– время на межоперационные действия.
74
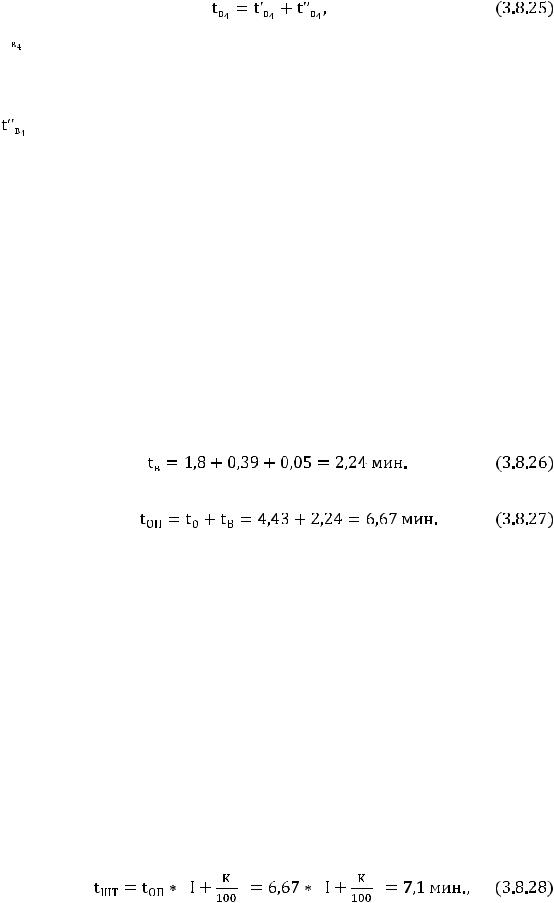
где – время смены инструмента (время на смену инструмента или на изме-
нение положения инструментальной (резцовой) головки, если многоинструментальная операция);
– время изменения режима (время на смену режимов, оно не повторя-
ется с каждым режимом).
Все эти затраты времени указаны в нормативах вспомогательного времени. По приложению А таблице А6 время на установку и снятие детали массой 30
кг с креплением в центрах с надеванием хомутика при установке подъёмником составляет 1,8 мин.
Вспомогательное время, связанное с переходом для станков II группы при диаметре обработки до 100 мм, составляет 0,13 мин (приложение А таблица А6).
На три перехода время составит 0,39 мин.
Время на приёмы, не вошедшие в комплекс (поворот резцовой головки), равно 0,05 мин (приложение А таблица А6).
Вспомогательное время на операцию составит:
Зная основное и вспомогательное время, находим оперативное время:
Время на обслуживание рабочего места определяется в зависимости от типа производства в процентах от основного или оперативного времени. По приложению А таблице А8 время на обслуживание рабочего места равно 2,5% от оперативного времени.
Время перерывов на отдых и личные надобности устанавливается по нормативам в зависимости от условий производства и работы оборудования.
Время на отдых и личные надобности рассчитывается в процентах от оперативного времени, в том числе время на личные надобности для всех видов работ предусматривается в среднем 2 % от времени смены. По приложению А таблице А8 для нашего примера время на отдых и личные надобности равно 4 % от оперативного времени.
Штучное время определяется по формуле
75
где К – время на обслуживание рабочего места, отдых и личные надобности в % от оперативного времени.
Подготовительно-заключительное время затрачивается станочником только в начале и в конце работы над данной партией деталей, и его продолжительность не зависит от числа штук в партии. Оно зависит от сложности деталей от зажимного приспособления, от количества инструментов, от размеров станка.
Подготовительно-заключительное время входит в состав нормы времени, если станочник сам выполняет накладку станка, пробную обработку деталей, получает и сдает инструмент. Такой порядок характерен для мелкосерийного, реже для серийного и главным образом для единичного производства. Подготовительнозаключительное время устанавливается в абсолютном значении по нормативам на партию деталей или на смену, реже – в процентах от оперативного времени.
Норма подготовительно-заключительного времени для расчётных условий по приложению А таблице А8 составляет 7 мин.
Зная подготовительно-заключительное время, определяют норму времени. Норма времени может быть установлена на партию деталей (tпарт) или при подетальной калькуляции – на одну штуку – штучно-калькуляционное время (tшт-к).
Результаты выбора режима резания и расчёта основного времени используются в дальнейшем для практической деятельности.
Выбор режимов резания и расчёт нормы времени для операции «Подрезка торцов» проводится аналогично. Для выбора режима резания используются соответствующие нормативные таблицы.
Содержание задания
Рассчитать норму времени на выполнение операции «Обработка втулки на токарном станке» в соответствии с заданием таблицы 40.
Станок – токарно-винторезный 1К62. Деталь – втулка.
Материал детали – сталь СТ5.
Режущий инструмент – резец проходной. Материал режущей кромки резца – Т15К6. Количество деталей в партии – 100 штук. Производство серийное.
Группа станков – 2.
76
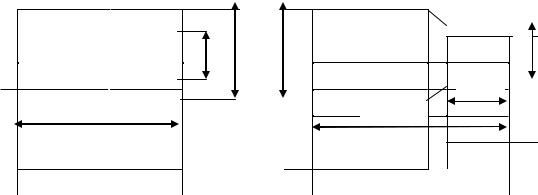
Количество режущего инструмента – 1.
Установка резца на размер производится по лимбу.
Обработка производится без изменения оборотов, подачи и без поворота резцедержателя. Время вспомогательное, связанное с переходом, не вошедшее в комплексы работ – не считать.
Типовой технологический процесс обработки втулки
А. Установить заготовку в 3-кулачковом самоцентрирующем патроне. 1. Обточить Dз до D.
Б. Переустановить втулку. 2. Обточить Dдо dна l.
В. Снять втулку.
Паспортные данные станка 1К62 (выписка неполная)
Число оборотов шпинделя η в минуту: 80, 100, 125, 160, 200, 250, 315, 400,
500, 530, 690, 800, 1000, 1100.
Продольные подачи Sмм в минуту: 0,47; 0,52; 0,57; 0,61; 0,78; 0,87; 0,95; 1,04;
1,14; 1,21; 1,40; 1,56; 1,74.
Наибольшая сила, допустимая механизмом продольной подачи γx = 360 кг. Мощность электродвигателя 10 кВт.
Варианты задания для расчёта норм на токарные работы
Заготовка |
Деталь |
3 |
D |
D |
d |
d |
|||
|
X |
|
|
|
|
|
l |
|
|
|
Z |
d3 |
|
|
|
Рисунок 5 – Геометрические параметры изделия
77
Таблица 40 – Параметры детали по вариантам задания
|
Размер заготовки |
|
Размер детали |
|
|
|
||
Вариант |
ДЗ |
LЗ |
D |
d |
L |
|
l |
Вес заготовки, кг |
|
|
|
||||||
1 |
30 |
50 |
28 |
22 |
45 |
15 |
|
2,16 |
2 |
32 |
55 |
30 |
24 |
50 |
20 |
|
2,65 |
3 |
34 |
60 |
32 |
26 |
88 |
25 |
|
3,06 |
4 |
36 |
65 |
34 |
28 |
60 |
30 |
|
3,57 |
5 |
38 |
70 |
36 |
30 |
65 |
35 |
|
4,11 |
6 |
40 |
75 |
38 |
32 |
70 |
40 |
|
4,40 |
7 |
42 |
80 |
40 |
34 |
75 |
40 |
|
5,33 |
8 |
44 |
85 |
42 |
36 |
80 |
40 |
|
5,99 |
9 |
46 |
90 |
44 |
38 |
85 |
40 |
|
6,70 |
10 |
48 |
95 |
46 |
40 |
90 |
40 |
|
7,45 |
11 |
50 |
100 |
48 |
42 |
95 |
40 |
|
9,04 |
12 |
30 |
40 |
28 |
22 |
35 |
10 |
|
1,72 |
13 |
32 |
45 |
30 |
24 |
40 |
15 |
|
1,88 |
14 |
34 |
50 |
32 |
26 |
45 |
20 |
|
2,55 |
15 |
36 |
55 |
34 |
28 |
50 |
25 |
|
3,02 |
16 |
38 |
60 |
36 |
30 |
55 |
30 |
|
3,53 |
17 |
40 |
65 |
38 |
32 |
60 |
35 |
|
4,08 |
18 |
42 |
70 |
40 |
34 |
65 |
40 |
|
4,53 |
19 |
44 |
75 |
42 |
36 |
70 |
40 |
|
5,29 |
20 |
46 |
80 |
44 |
38 |
75 |
40 |
|
5,96 |
21 |
48 |
85 |
46 |
40 |
80 |
40 |
|
6,66 |
22 |
50 |
90 |
48 |
42 |
85 |
40 |
|
8,13 |
23 |
30 |
60 |
28 |
22 |
55 |
20 |
|
2,69 |
24 |
32 |
65 |
30 |
24 |
60 |
25 |
|
3,06 |
25 |
34 |
70 |
32 |
26 |
65 |
25 |
|
3,57 |
26 |
36 |
70 |
34 |
28 |
65 |
25 |
|
3,84 |
27 |
38 |
70 |
36 |
30 |
65 |
25 |
|
4,11 |
28 |
40 |
75 |
38 |
32 |
70 |
30 |
|
4,70 |
29 |
42 |
75 |
40 |
34 |
70 |
30 |
|
4,99 |
30 |
44 |
80 |
42 |
36 |
75 |
30 |
|
5,64 |
3.9. Определение величины Нвр на основе аналитического расчётного метода нормирования труда
Используя отраслевую или межотраслевую базу норм и нормативов по труду, определите фактические затраты рабочего времени на выполнение различных видов работ. Номер индивидуального задания определяется порядковым номером в списке группы.
Содержание задания
Вариант 1 1. Укладка паркетных полов с фризом с линейкой и двумя жилками из дуба.
Количество планок на 1 м2– 80 шт. Площадь – 1116 м2.
78
2. Очистка паркетных полов мокрыми опилками. Площадь – 1116 м2.
Вариант 2 1. Установка силового трансформатора с помощью крана. Масса трансформа-
тора – до 5 т. Количество – 1 шт.
2.Монтаж оборудования, приборов в камерах с масляными выключателями. Количество – 1 камера.
3.Зачистка, регулировка и смазка контактов рубильников.
Количество – 20 ножей.
Вариант 3
1.Ручная дуговая сварка труб до 200 мл в горизонтальное неповоротное положение без скоса кромок в траншеях в условиях болотистой местности.
Количество – 73 стыка.
2.Угловое соединение фланца с трубой без скоса кромок на лесах: вертикальное неповоротное положение шва, наружный диаметр труб – до 60 мм, шов до 12 мм.
Количество – 9 фланцев.
3.Нагрев сварных соединений труб до 200 мм токами частотой 50 Гц, при толщине стенки до 20 мм в траншеях в условиях болотистой местности.
Количество – 73 стыка.
Вариант 4
1.Кладка стен зданий наружных средней сложности под штукатурку в 2 ½ кирпича.
Количество: глухие – 18 м3, сложные с проёмами – 46 м3.
2.Кладка цилиндрических сводов в 1 кирпич с опусканием опалубки.
Объём –27 м3.
3.Ручное приготовление раствора из глины с добавлением песка . Объём – 8 м3.
4.Кладка печных труб прямоугольного сечения без расшивки швов в 1 ½
кирпича.
Объём – 3 м3.
79
Вариант 5
1.Нанесение простой штукатурки на стены и перегородки вручную. Площадь – 1800 м2.
2.Штукатурная обработка швов цементным раствором.
Площадь : стен – 300 м2, потолков – 40 м2.
3. Окрашивание масляными красками кистью (два окрашивания). Площадь: стены по дереву – 1600 м2, потолки по дереву – 800 м2.
Вариант 6
1.Погружение свай-оболочек вибропогружателями длительностью до 170 минут.
Количество – 76 свай.
2.Наклонное погружение одиночных свай универсальными плавучими копрами, длительностью погружения 140 мин.
Количество – 24 сваи.
3.Наращивание обсадной трубы буровой установки.
Количество – 4 секции.
Вариант 7
1.Погрузка и укладка в штабель груза в мешках с перемещением до 70 м на высоту 3,5 м автопогрузчиком.
Количество – 900 т.
2.Перемещение песка ленточным транспортёром с набрасыванием на ленту вручную лопатами.
Объём – 60 м3.
3.Перевозка грузов ручными тележками, погрузка – накладыванием, разгрузка – складыванием на расстоянии до 50 м.
Количество – 1200 кг.
Вариант 8
1.Срубка наплывов бетона вручную на лестничных маршах. Площадь – 40 м2.
2.Отделка откосов декоративной штукатуркой по бетонным поверхностям. Площадь – 40 м2.
3.Обработка декоративной штукатуркой под борозчатую фактуру на колоннах. Площадь – 18 м2.
4.Окраска окон масляными составами с частичной шлифовкой, кистью. Площадь – 38 м2.
80