
МАТЕРИАЛОВЕДЕНИЕ Лабораторный практикум 1
.pdf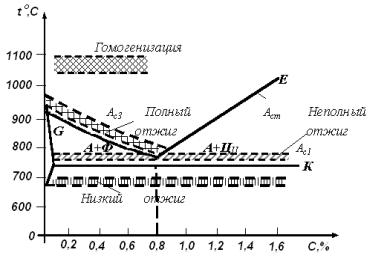
Вторая группа включает нагрев металла выше некоторой критической температуры – температуры фазовых превращений и охлаждение с малой скоростью. При этом происходит фазовая перекристаллизация (нормализация).
Ктретьей группе относится нагрев металла до температуры фазовых превращений и быстрое охлаждение. Такая операция называется закалкой. Структурное состояние сплава после закалки неустойчиво.
Кчетвёртой группе относится вид термической обработки, направленный на перевод неустойчивой структуры закалённого сплава в устойчивую. Нагрев закалённого сплава ниже температуры фазовых превращений называется отпуском.
Отжиг – термическая обработка, при которой сталь нагревается до или выше критических температур с последующим медленным охлаждением (вместе с печью). Отжиг бывает: низкий, неполный, полный и диффузионный (гомогенизация) (рис. 6.1). При низком отжиге (отжиг первого рода) изделия нагревают ниже Ас1. Он применяется в том случае, если
сталь имеет хорошую структуру и требуется только снизить внутренние напряжения.
Неполный отжиг (отжиг второго рода) осуществляется путём нагрева изделий выше Ас1, но ниже Ас3. В этом случае происходит перекристаллизация только перлита и частично устраняются внутренние напряжения.
Рисунок 6.1 – Температуры нагрева стали при отжиге
Полный отжиг доэвтектоидных сталей достигается за счёт нагрева изделий выше Ас3 с последующим медленным охлаждением. Ферритоперлитная структура превращается в аустенит, а затем при охлаждении
41

аустенит превращается в структуру с более мелкими зёрнами феррита и перлита. При полном отжиге происходит перекристаллизация стали и полностью устраняются внутренние напряжения. Он применяется для устранения некоторых дефектов предыдущих операций горячей обработки (литья, ковки, штамповки и т.д.).
Заэвтектоидные (инструментальные) стали не подвергаются полному отжигу. Это обусловлено тем, что при нагревании происходит рост зёрен аустенита, а при охлаждении они не измельчаются. Поэтому при полном отжиге зёрна перлита будут крупными. Наличие крупнозернистой структуры отрицательно влияет на эксплуатационные свойства изделий – снижается их ударная вязкость, повышается порог хладноломкости.
Диффузионный отжиг (гомогенизация) применяется для литых изделий с целью устранения дендритной ликвации. При нагреве до 1000– 1100 С и длительной выдержке наблюдается сильный рост зёрен и выравнивание по химическому составу. После такой обработки структура получается крупнозернистой. Для измельчения зёрен требуется провести полный отжиг.
Нормализация – термическая обработка, при которой сталь нагревают выше критической температуры Ас3 или Аст (рис. 6.2) с последующим охлаждением на спокойном воздухе. Это более дешёвый и простой вид термообработки.
Свойства малоуглеродистых нелегированных сталей при нормализации и отжиге почти одинаковы. У среднеуглеродистых сталей (0,3–0,5 % С) различие в свойствах более значительно.
Нормализованная сталь имеет более высокую твёрдость, прочность. Это связано с тем, что охлаждение происходит быстрее. При распаде аустенита образуется более дисперсный перлит (тоньше пластинки ферри- то-цементитной смеси). В заэвтектоидных сталях нормализация устраняет цементитную сетку.
Рисунок 6.2 – Температуры нагрева стали при нормализации
42
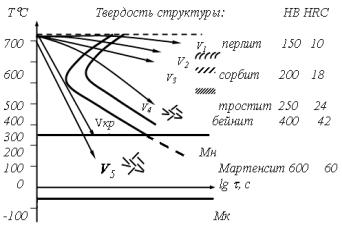
Если легированную сталь после нагрева выше критической точки охлаждать в струе воздуха, то аустенит частично превращается в мартенсит – образуется структура закалённой стали. Поэтому нормализация занимает промежуточное положение между отжигом и закалкой.
От скорости охлаждения изделий, нагретых выше критических температур, зависит структура, получаемая при распаде аустенита. На рисунке 6.3 показана диаграмма изотермического превращения аустенита. Кривые на диаграмме имеют вид буквы «С», поэтому их часто называют С-кри- выми. Свойства и строение продуктов распада аустенита зависят от температуры и времени. На рисунке 6.3 время представлено в виде логарифмической шкалы.
Рисунок 6.3 – Диаграмма изотермического распада аустенита с наложенными на неё кривыми охлаждения, схемы структур и примерная их твёрдость
Это сделано для удобства, так как при распаде аустенита в перлит около критической точки для углеродистых сталей требуется несколько десятков минут (тысячи секунд), а при образовании мартенсита – одна-две секунды. Горизонтальные линии Мн и Мк показывают соответственно температуры начала и конца бездиффузионного мартенситного превращения.
На диаграмму нанесены кривые охлаждения, а также показаны схемы образующихся при этом структур и их примерная твёрдость.
При небольших скоростях охлаждения (V1;V2;V3;V4 ) аустенит превращается в структуру перлитного типа. По мере увеличения скорости охлаждения (от V1 до V4 ) образуются более мелкие пластинки ферритоцементитной смеси. Твёрдость и прочность повышаются, пластические свойства стали снижаются. При значительных скоростях охлаждения (V5 ) происходит бездиффузионное превращение аустенита в мартенсит. Мартенсит стали представляет собой пересыщенный твёрдый раствор внедрения
43

углерода в -железе. Минимальная скорость охлаждения, при которой аустенит переходит в мартенсит, минуя феррито-цементитные превращения, называется критической скоростью охлаждения (Vкр).
Рисунок 6.4 – Температура нагрева стали при закалке
Доэвтектоидные стали обычно подвергают полной закалке – нагрев выше температуры Ас3 на 30–50 С (см. рис. 6.4). После закалки с охлаждением в воде структура стали представляет собой мелкоигольчатый мартенсит.
Нагрев доэвтектоидной стали выше Ас1 (но ниже Ас3) приводит к неполной закалке. В структуре такой стали наряду с мартенситом наблюдаются участки феррита.
Заэвтектоидные стали обычно подвергаются неполной закалке. При этом в структуре стали сохраняется вторичный цементит, который повышает твёрдость и износостойкость изделий.
Если заэвтектоидную сталь подвергнуть полной закалке, то структура будет состоять из мартенсита и остаточного аустенита. Устраняют остаточный аустенит дополнительной обработкой холодом (до -80 С). В качестве охлаждающих сред при закалке используют воду (иногда с добавками солей, щелочей, кислот), растительные и минеральные масла, расплавы солей и металлов. Для углеродистых сталей в качестве охлаждающих сред обычно используют воду, для легированных – минеральные масла. Чтобы уменьшить хрупкость и напряжения, вызванные закалкой, и получить требуемые механические свойства, сталь после закалки обязательно подвергают отпуску.
Отпуск закалённой стали состоит из нагрева её до температуры ниже Ас1, выдержки во времени и последующего охлаждения с любой скоростью. Структура и свойства стали зависят в большой мере от температуры нагрева.
44
Низкий отпуск производится при температурах 150–220 С и назначается для уменьшения внутренних напряжений и хрупкости без значительного снижения твёрдости. Этому виду отпуска подвергают мерительный и режущий инструменты, а также детали, прошедшие поверхностную закалку или цементацию, от которых требуется твёрдость и износостойкость. Структура закалённой и низкоотпущенной стали – отпущенный мартенсит.
Средний отпуск производится при температурах 300–450 С и назначается, в основном, для пружин и рессор. При среднем отпуске мартенсит превращается в тростит отпуска, который обладает хорошей упругостью при достаточно высокой твёрдости и прочности.
При высоком отпуске закалённая сталь нагревается до температуры 500–600 С, что обеспечивает полное снятие внутренних напряжений. Мартенсит, распадаясь, превращается в дисперсную феррито-цементитную смесь – сорбит. Сталь приобретает хорошую прочность, пластичность и вязкость. Сочетание закалки с высоким отпуском называется улучшением.
1. Порядок выполнения работы
Предварительно термически обработанные образцы подвергают испытанию для определения механических свойств:
предел прочности σв, МПа;
условный предел текучести σ0,2 , МПа;
относительное удлинение , %;
относительное сужение , %;
ударная вязкость КСU, МДж/м2;
твёрдость по Роквеллу, измеренная по шкале С, HRC. Характеристики прочности и пластичности определяются при стати-
ческих испытаниях на растяжение на разрывной машине Р – 5.
Твёрдость HRC определяется при статических испытаниях на твердомере типа ТК – 2М.
Ударная вязкость определяется при динамических испытаниях на ударный изгиб образцов с U-образным концентратором напряжения на маятниковом копре типа Шарпи.
Результаты испытаний оформляют в виде таблицы 6.1.
Т а б л и ц а 6.1 – Результаты испытаний образцов из стали 45
t, C |
HRС |
в , |
0,2 , |
,% |
,% |
KCU, |
Структура |
Характер |
отпуска |
МПа |
МПа |
МДж/м2 |
излома |
||||
|
|
|
|
|
|
|
|
|
|
|
|
|
|
|
|
|
45 |
Вопросы для самоконтроля
1.Сущность процесса термической обработки.
2.Классификация видов термической обработки.
3.Превращения в конструкционных сталях при нагреве и охлаждении.
4.Технология термической обработки стали.
5.Отжиги первого и второго рода.
6.Полная и неполная закалки. Закалочные охлаждающие среды.
7.Способы объёмной закалки.
8.Способы поверхностной закалки.
9.Отпуск. Отпускная хрупкость первого и второго рода.
10.Влияние температуры отпуска на свойства закалённой стали.
Лабораторная работа № 7 ФОРМООБРАЗОВАНИЕ ЗАГОТОВОК ЛИТЬЁМ В ПЕСЧАНЫЕ ФОРМЫ
Цель работы: ознакомление с технологией и получение навыков изготовления литых металлических деталей в песчано-глинистых формах; изучение влияния формы на величину усадки отливки.
Задание
1.Дать характеристику технологии изготовления литых металлических деталей в песчано-глинистых формах.
2.Изготовить отливки из легкоплавкого металла для определения величины свободной и затруднённой усадок.
3.Провести анализ результатов работы, сформулировать выводы.
4.Оформить письменный отчёт по работе.
Общие сведения из теории
1. Литейный комплект
Литьё в песчаные формы является самым распространённым способом изготовления отливок. Этим способом изготовляют разнообразные по конфигурации и массе отливки из чугуна, стали и сплавов цветных металлов.
Сущность литья в песчаные формы заключается в получении отливок из расплавленного металла, затвердевшего в формах, изготовленных из формовочных смесей (основной составляющей которых является песок) путём уплотнения с использованием модельного комплекта.
46
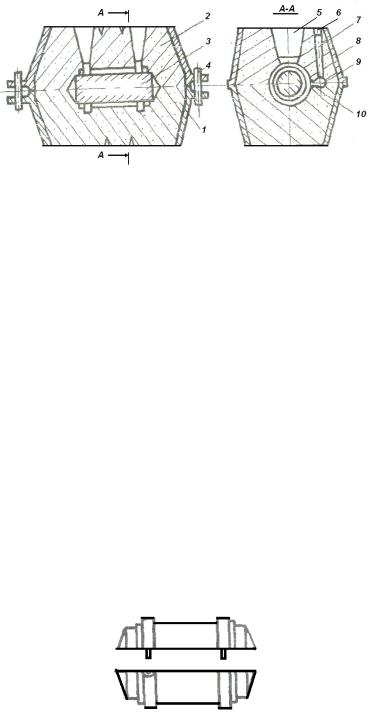
Литейная форма (см. рис. 7.1) состоит из нижней 1 и верхней 2 полуформ, которые изготовляют в опоках 8 – приспособления для удержания формовочной смеси.
1 – нижняя полуформа; 2 – верхняя полуформа; 3 – литейный стержень; 4 – штырь; 5 – выпор; 6 – литниковая чаша; 7 – стояк; 8 – опока; 9 – шлакоуловитель; 10 – питатель
Рисунок 7.1 – Литейная форма
Литниковая система – совокупность каналов и резервуаров, по которым расплав поступает из разливочного ковша в полость формы.
Основными элементами литниковой системы являются литниковая чаша 6 (см. рис. 7.1), которая служит для приёма расплавленного металла и подачи его в форму, стояк 7 – вертикальный или наклонённый канал. Для подачи металла из литниковой чаши непосредственно в рабочую полость или к другим элементам, шлакоуловитель 9, с помощью которого удерживается шлак и другие неметаллические примеси, в также питатель 10 (один или несколько), через который расплавленный металл подводится в полость литейной формы. Для вывода газов, контроля заполнения формы расплавленным металлом и питания отливки при её затвердевании служат прибыль или выпор 5.
Модельный комплект – совокупность приспособления, включающих литейную модель, модели литниковой системы, стержневые ящики (один или несколько), модельные плиты, контрольные или сборочные шаблоны, используемые для образования при формовке рабочей полости литейной формы.
Литейная модель (см. рис. 7.2) – приспособление, с помощью которого в литейной форме получают отпечаток, соответствующий конфигурации и размерам отливки. Модели бывают неразъёмные, разъёмные и специальные.
Рисунок 7.2 – Литейная модель
47
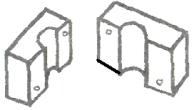
Стержневой ящик (см. рис. 7.3) – формообразующее изделие, имеющее рабочую полость для получения в ней литейного стержня из стёршейся смеси. Стержневые ящики бывают разъёмные и неразъёмные.
Рисунок 7.3 – Стержневой ящик
Модельные плиты формируют разъём литейной формы, на них закрепляют части модели, включая модели литниковой системы. Эти плиты используют для изготовления опочных и безопочных полуформ.
Формовочные смеси – многокомпонентное сочетание материалов, соответствующее условиям технологического процесса изготовлений литейных форм. В качестве огнеупорной составляющей смеси используют кварцевый песок. Для соединения частиц песка между собой применяют формовочные глины, различные смолы и другие связующие. Кроме того, используют различные добавки (мазут, графит, древесная мука) для придания формовочным смесям специальных свойств. Формовочные смеси подразделяют на облицовочные, наполнительные и единые.
Облицовочная смесь используется для образования рабочей поверхности формы, непосредственно контактирующей с расплавленным металлом. Её наносят на поверхность модели слоем толщиной 15–30 мм. Смесь содержит 50–90 % свежих формовочных материалов и 10–50 % смеси повторного употребления.
Наполнительная смесь используется для заполнения опоки после нанесения облицовочного слоя на поверхность модели. Смесь содержит в основном формовочные материалы повторного употребления.
Единая смесь применяется одновременно в качестве облицовочной и наполнительной смеси. В состав единой смеси входит 10–20 % свежих формовочных материалов, а остальное – оборотная смесь.
Стержневые смеси представляют собой многокомпонентное сочетание формовочных материалов. Они приготовляются из кварцевого песка с добавкой различных связующих материалов – олифы, сульфитно-спирто- вой барды, синтетических смол, а также глины. Чтобы стержень не пригорел к отливке, в смесь вводят уголь, графит, мазут, а для обеспечения податливости стержней – древесные спилки и торф.
Жидкие и самотвердеющие смеси обладают способностью течь по-
сле приготовления и самопроизвольно отвердевать и упрочняться по всему объёму. Такие смеси через 26–30 минут после заполнения формовочного
48

или стержневого ящика приобретают достаточную для извлечения формы или стержня прочность. Формовочные и стержневые смеси должны обладать достаточной прочностью, огнеупорностью и податливостью, высокой газопроницаемостью и пониженной газотворной способностью.
Формовка – совокупность технологических операций изготовления литейных форм и стержней, способных выдерживать воздействие расплавленного металла и сообщать ему свои очертания. Основными операциями формовки являются наполнение опоки формовочной смесью, уплотнение её, извлечение модели и сборка формы. При формовке в форме предусматривают вентиляционные каналы для выхода газов, образующихся при заливке расплавленного металла. В зависимости от заливаемого металла, размеров и массы отливки применяют сырые, сухие, химически твердеющие и другой формы. Формы изготавливают вручную, на формовочных машинах и на автоматических линиях формовки. Изготовление стержней осуществляется вручную и на специальных стержневых машинах.
Сборка литейных форм включает установку стержней, скрепление полуформ перед заливкой, контроль размеров основных полостей формы.
Заливка форм расплавленным металлом производится из конических, барабанных и других ковшей, футерованных огнеупорным материалом и высушенных до полного удаления влаги. Температура заливаемого металла зависит от рода сплава, толщины стенок отливки, их конфигурации и т.п. Заливка форм осуществляется посредством ковшей, ведётся непрерывно без прерывания струи до полного заполнения литниковой чаши.
Продолжительность процесса охлаждения отливок может колебаться от нескольких минут до суток в зависимости от их массы, состава сплава и свойств формовочных материалов.
Выбивка отливок из литейных форм осуществляется на вибрационных решётках, а затем отливки очищаются в очистных барабанах или дробемётными установками. Обрубка и зачистка отливок от остатков питателей, заусенцев и заливов производится шлифовальными кругами или на обрезных прессах.
2.Определение усадки отливки
Впроцессе охлаждения залитого в полость формы жидкого металла происходит уменьшение его объёма, а в процессе кристаллизации и последующего охлаждения отливки меняется не только объём, но и линейные размеры. Это изменение называется усадкой.
За величину усадки обычно принимают относительные величины, выражающие в процентах изменение объёма или длины при охлаждении
V0 V1100%, (7.1)
V |
V1 |
|
|
|
49 |
|
|
|
Л |
l0 l1 |
100%, |
(7.2) |
|
|
|
|
|
||||
|
|
|
|
l1 |
|
|
|
где |
V |
– |
объёмная усадка отливки; Л |
– линейная |
усадка отливки; |
||
V0 |
– объём отливки при температуре t0 ; V1 |
– объём отливки при темпера- |
|||||
туре t1; |
l0 |
– длина отливки при температуре t0; l1 – длина отливки при |
температуре t1.
Относительная разница между линейными размерами модели (lмод) и отливки (lотл) называется литейной усадкой и определяется по формуле
лит |
|
lмoд lотл |
100%. |
(7.3) |
|
||||
|
|
lотл |
|
Литейная усадка определяется не только коэффициентом линейной усадки металла отливки, но и конструкцией отливки, условиями извлечения модели из формы, методом её изготовления т.д.
3.Оборудование и материалы
Влабораторной работе используются следующее оборудование и инструмент: лабораторная муфельная печь СНОЛ-1,6. 3,0, опоки модельный комплект, набор формовочного инструмента, измерительный инструмент, сплав АК 5М2 ГОСТ 1583–93, наполнительная формовочная смесь.
4.Методика и порядок выполнения работы
Различие между литейной и линейной усадками легко установить, заливаяформу, модели которой приведены на рисунке 7.4. В моделях для определения свободной (см. рис. 7.4а) и затруднённой (литейной) (см. рис. 7.4б) усадок имеются отверстия, расстояния между центрами которых равны 200 мм. Через эти отверстия с помощью керна в стенке формы делаются углубления для определения разницы между соответствующими размерами отливки и модели.
При охлаждении отливок от температур заливки до нормальных температур, в зависимости от состояния металла, условно можно наблюдать три вида усадки:
а) усадка в жидком состоянии Vж происходит по мере понижения температуры от температуры заливки до температуры кристаллизации (ликвидус);
б) усадка в жидко-твёрдом состоянии Vж-т происходит по мере охлаждения отливки от температуры ликвидуса до температуры солидус;
в) усадка в твёрдом состоянии Vт происходит по мере охлаждения отливки от температуры солидус до температуры окружающей среды.
50