
МАТЕРИАЛОВЕДЕНИЕ Лабораторный практикум 1
.pdfковкий, большая часть углерода в этом чугуне находится в свободном состоянии в виде графита, имеющего хлопьевидную форму (углерод отжига);
высокопрочный, в нём большая часть углерода находится в свободном состоянии в виде графита, имеющего шаровидную форму.
Структура серого, ковкого и высокопрочного чугунов состоит из графитовых включений и металлической основы, которая может быть ферритной, феррито-перлитной и перлитной.
Вопросы для самоконтроля
1.Фазы и структуры в железоуглеродистых сплавах.
2.Точки и линии диаграммы состояния железо – цементит.
3.Построение схематических кривых охлаждения сплавов.
4.Классификация сталей и чугунов по структуре в равновесном состоянии.
5.Виды металлической основы и графитных включений в чугунах со свободным углеродом.
6.Превращения в сталях при охлаждении.
Лабораторная работа № 5 МЕТОДЫ ИЗМЕРЕНИЯ ТВЁРДОСТИ МЕТАЛЛОВ
Цель работы: изучение основных свойств металлов, ознакомление с методами и приборами для измерения твёрдости металлов, приобретение навыков в определении твёрдости.
Задание
1.Изучить свойства металлов и сплавов: физические, химические, механические, технологические.
2.Ознакомиться с методами статических и динамических испытаний металлов и сплавов.
3.Ознакомиться с устройством и работой твердомеров типа ТШ и ТК.
4.Измерить твёрдость предложенных образцов стали и цветных металлов и их сплавов.
5.Определить по полученным результатам испытаний приблизительные значения прочностных характеристик испытанных образцов.
6.Оформить письменный отчёт по работе.
31
Общие сведения из теории
Свойства металлов и сплавов принято разделять на физические (плотность, температура плавления, тепловое расширение, теплопроводность, электропроводность и др.), механические (прочность, упругость, пластичность, твёрдость, вязкость, выносливость), химические (стойкость против коррозии) и технологические (вытяжка, изгиб, перегиб, резание, сварка и т.д.). Из большого количества свойств, которыми обладают металлы и сплавы, механические свойства в большинстве случаев являются важнейшими.
Механические свойства металлов определяют на специальных стандартных образцах. В зависимости от характера нагружения механические испытания могут быть статическими (скорость нагружения образца2 см/мин) и динамическими ( >2 cм/мин). К статическим методам на-
гружения относятся испытания: на растяжение, сжатие, изгиб, кручение, на срез, устойчивость, смятие, на твёрдость, на трещиностойкость. К динамическим относятся испытания: на ударную вязкость, хладноломкость и критическую температуру хрупкости, испытания на усталость, а также некоторые методы испытания металлов на твёрдость.
Для определения механических свойств в последние годы используется также безобразцовый метод. Он основан на инденторных испытаниях материалов, в результате которых определяют специальные характеристики твёрдости и пересчитывают их на показатели других механических свойств. Главное его достоинство заключается в возможности ускоренной оценки механических характеристик металла готовых изделий, не выводя их из строя и не вырезая из них образцов.
Из всех видов механических испытаний металлов испытание на твёрдость проводится чаще всего. Это объясняется простотой и быстротой испытания, портативностью приборов, а также тем, что по показателям твёрдости можно косвенно оценить прочность металла и прогнозировать его поведение при эксплуатации.
Наибольшее применение в технике получили статические методы испытания на твёрдость при вдавливании в поверхность материала твёрдосплавного наконечника, называемого индентором: метод Бринелля, метод Роквелла и метод Виккерса, а также определение микротвёрдости по Хру- щёву-Берковичу. Динамические методы определения твёрдости по Шору, Польди и царапанием используются сравнительно редко.
Твёрдость – это свойство материала оказывать сопротивление контактной деформации или хрупкому разрушению при внедрении индентора в его поверхность.
32
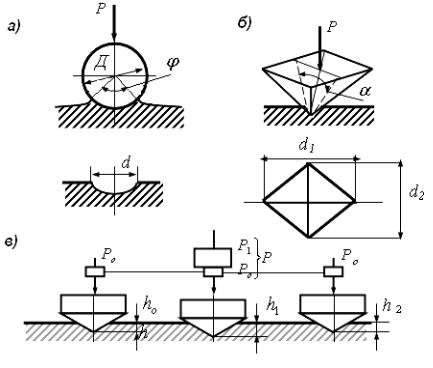
а) по Бринеллю; б) по Виккерсу; в) по Роквеллу
Рисунок 5.1 – Схемы испытаний на твёрдость
1. Определение твёрдости металлов по Бринеллю
При испытании на твёрдость по методу Бринелля в поверхность материала вдавливается твердосплавный шарик диаметром Д под действием нагрузки Р, после снятия нагрузки измеряется диаметр отпечатка d
(см. рис. 5.1а).
Процесс измерения твёрдости по Бринеллю состоит из следующих основных последовательно выполняемых операций:
а) подготовка образцов материала к испытанию. Образец материала должен иметь параллельные поверхности (испытуемую и опорную), без окалины, ржавчины или каких-либо неровностей. При необходимости эти поверхности подвергают специальной зачистке при обработке наждачной бумагой, шлифовальным кругом или напильником, при этом образец не должен нагреваться выше 120–150 С. Минимальная толщина образца материала должна быть не менее десятикратной глубины отпечатка;
б) находят по таблице 5.1 диаметр шарика Д, нагрузку Р и время выдержки под нагрузкой t;
33
Таблица 5.1 – Рекомендуемые параметры испытаний по Бринеллю
Материал |
Интервал твёрдости в числах Бринелля |
Толщина испытуемого образца, мм |
Соотношение между нагрузкой Р и диаметром шарика Д |
Диаметр шарика, мм |
Нагрузка Р, числитель кГс, знаменатель Н |
Выдержка под нагрузкой, с |
|
|
|
|
|
|
|
Чёрные |
140–150 |
6-3 |
Р 30Д2 |
10 |
3000/29400 |
10 |
металлы |
|
4-2 |
|
5 |
750/7358 |
|
|
|
<2 |
|
2,5 |
187,5/1839 |
|
То же |
<140 |
>6 |
Р 10Д2 |
10 |
1000/9810 |
10 |
|
|
6-3 |
|
5 |
250/2459 |
|
|
|
<2 |
|
2,5 |
62,5/613 |
|
Цветные |
>130 |
6-3 |
Р 30Д2 |
10 |
3000/29400 |
30 |
металлы |
|
4-2 |
|
5 |
750/7358 |
|
|
|
<2 |
|
2,5 |
187,5/1839 |
|
То же |
35–130 |
9-3 |
Р 10Д2 |
10 |
1000/9810 |
60 |
|
|
6-3 |
|
5 |
250/2459 |
|
|
|
<3 |
|
2,5 |
62,5/613 |
|
То же |
8–35 |
>6 |
Р 2,5Д2 |
10 |
250/2453 |
60 |
|
|
5-3 |
|
5 |
62,5/613 |
|
|
|
<3 |
|
2,5 |
15,6/153 |
|
в) подготовка твердомера ТШ к испытаниям. Шарик, выбранный по таблице 5.1, закрепляют в держателе 3 (см. рис. 5.2) и устанавливают необходимую нагрузку Р на приборе. Нагрузка создаётся массой рычажной системы 13, подвески 11 и сменными грузами 12. В зависимости от формы испытуемого образца подбирают опорный столик 6. Твёрдость плоских образцов измеряют на плоском столике, а цилиндрических – на призматическом. После этого соответствующим перемещением подвижной чашки 8 по отношению шкалы, расположенной на станине прибора, устанавливают время выдержки образца под нагрузкой. Чашку 8 в нужном положении закрепляют винтом 9;
г) работа с прибором при испытании. Испытуемый образец материала 5 устанавливают на столике 6 таким образом, чтобы центр отпечатка располагался от края образца на расстоянии не менее 2,5 диаметра, а от центра соседнего отпечатка – не менее двух диаметров отпечатка. Затем подводят образец к шарику, для чего вращают маховик 10 до упора образца в ограничитель 4, а при отсутствии последнего – до сжатия пружины 20. Нажатием кнопки 7 включают электродвигатель 17, который через червячный редуктор 18, кривошипный вал 16 и шатун 15 отводит вниз ролик 14. Вследствие этого действие нагрузки Р через систему рычагов 13, стержень 19, шпиндель 21 сообщается шариковому наконечнику 22. Этот момент фиксируется загоранием лампочки 1. После соответствующей выдержки испытуемого образца под действием нагрузки Р вращение электродвигателя
34

переключается автоматически на обратное: ролик 14 перемещается вверх, возвращает рычаг 13 в исходное до нагрузки шарика положение, электродвигатель автоматически отключается, и лампочка гаснет;
Рисунок 5.2 – Схема устройства твердомера ТШ
д) определение показателя твёрдости. Для определения числа твёрдости НВ по диаметрам отпечатка d пользуются специальной таблицей. Максимальная твёрдость испытуемых образцов металлов и сплавов не должна превышать 450 НВ. Испытание более твёрдых металлов повлечёт за собой деформацию шарика, твёрдость которого 650 НВ.
Испытание на твёрдость одного и того же образца производится дважды, при этом при каждом испытании диаметр отпечатка измеряется в двух взаимно перпендикулярных направлениях с помощью специального отсчётного микроскопа МПБ-2 с точностью до сотых долей миллиметра. Схема измерения диаметров d1 и d2 приведена на рисунке 5.3.
При Д=10 мм, Р=29400Н и времени выдержки под нагрузкой 10 с твёрдость по Бринеллю обозначается символом НВ с указанием числа твёрдости. При этом размерность (кГс/мм2) не ставится, например 200 НВ.
При использовании шариков других диаметров (2,5 и 5 мм) изменяется нагрузка вдавливания, а символ твёрдости НВ дополняется тремя индексами.
Например, 180НВ2,5/187,5/30 обозначает, что при Д=2,5 мм, Р=187,5 кГс (1839 Н) и времени выдержки под нагрузкой 30 с число твёрдости по Бринеллю равно 180.
35
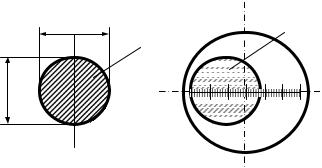
d1 |
2 |
|
1 |
d2 |
|
|
0 |
1 |
2 3 4 5 6 7 |
Рисунок 5.3 – Схема измерения диаметра отпечатка c помощью отсчётного микроскопа
2. Определение твёрдости металлов по Виккерсу
При испытании на твёрдость по методу Виккерса в поверхность материала вдавливается алмазная четырёхгранная пирамида с углом при вершине =136 (см. рис. 5.1б). После снятия нагрузки вдавливания измеряются диагонали отпечатка d1 и d2 и определяется среднее арифметическое значение d. Число твёрдости по Виккерсу HV подсчитывается как отношение нагрузки Р к площади поверхности пирамидального отпечатка М:
|
P |
|
2P sin |
|
|
|
P |
|
HV |
|
2 |
|
1,854 |
. |
|||
M |
d 2 |
|
|
|
||||
|
|
|
|
|
d 2 |
Число твёрдости по Виккерсу обозначается символом HV с указанием нагрузки Р и времени выдержки под нагрузкой, причём размерность числа твёрдости (кГс/мм2) не ставится. Продолжительность выдержки индентора под нагрузкой принимают для сталей 10–15 с, а для цветных металлов – 30 с. Например, 450 HV10/15 означает, что число твёрдости по Виккерсу 450 получено при Р=10 кГс (98,1 Н), приложенной к алмазной пирамиде в течение 15 с. Методом Виккерса можно испытывать материалы очень высокой твёрдости, а также тонкие ленты, полосы, фольгу и прочные слои на поверхности металлов, например, после азотирования.
3. Определение твёрдости металлов по Роквеллу
Измерение твёрдости по методу Роквелла производят на приборах типа ТК. Твёрдость металла определяется путём вдавливания в его поверхность алмазного конуса с углом при вершине 120 С или стального шарика диаметром 1,588 мм. Однако, согласно этому методу, за условную меру твёрдости принимается глубина отпечатка. Схема испытания по методу Роквелла показана на рисунке 5.1в. Для испытания изделий, имеющих твёрдость HRC 20–50, допускается применение конуса из твёрдого сплава. Прибор Роквелла в зависимости от прилагаемой нагрузки в 588,6, 981 или 1471,5 Н имеет соответственно шкалы А, В, С. При работе с твердомером ТК соблюдают такую последовательность операций.
36
3.1. Подготовка образцов к испытанию
Испытываемая поверхность образца должна быть параллельна опорной поверхности, не иметь царапин и забоин. С этой целью испытываемую и опорную поверхности образца обрабатывают наждачной бумагой или мелкозернистым шлифовальным кругом, не допуская нагревания образца более чем до 120–150 С. После установки образца на приборе он не должен сдвигаться, качаться или деформироваться.
Минимальная толщина испытываемого образца в зависимости от его твёрдости составляет 0,7–2,0 мм при испытании по шкале В и 0,7–1,5 мм – по шкале С.
3.2.Определение параметров испытаний
Всоответствии с установленным пределом измерения для каждой шкалы (см. табл. 5.2) следует выбрать вид наконечника и общую нагрузку.
Та б л и ц а 5.2 – Выбор параметров испытаний на твердомере ТК
Шкала |
|
Общая |
Обозначение |
Допускаемые |
|
Вид наконечника |
нагрузка Р, |
пределы |
|||
твёрдости |
|||||
|
Н |
|
шкалы |
||
|
|
|
|||
В |
Стальной шарик, Д=1,588 мм |
981 |
HRB |
25–100 |
|
С |
Алмазный конус с углом при вер- |
1471,5 |
HRC |
20–67 |
|
|
шине 120+1,5 . Радиус закругления |
|
|
|
|
|
вершины конуса 0,2+0,002 мм |
|
|
|
|
А |
То же |
588,6 |
HRA |
70–85 |
Шкалой В пользуются при измерении твёрдости мягких металлов (сырых, незакалённых сталей, цветных металлов и их сплавов); шкалой С – при измерении твёрдости закалённых сталей; шкалой А – при измерении твёрдости изделий с твёрдым поверхностным слоем, полученным в результате химико-термической обработки (цементации, цианирования и др.), а также твёрдых сплавов.
3.3.Подготовка прибора ТК к испытаниям
Всоответствии с выбранной шкалой устанавливают в шпинделе индентор и закрепляют его с помощью винта. С помощью сменных грузов устанавливают необходимую величину основной нагрузки. В зависимости от формы испытываемого образца выбирают и устанавливают сменный предметный столик.
37
3.4. Измерение твёрдости
Образец помещают на столик прибора и вращением маховичка поднимают до соприкосновения с вдавливаемым наконечником до тех пор, пока малая стрелка шкалы индикатора не совместится с красной точкой на циферблате.
При этом пружина прибора обеспечит предварительную нагрузку Ро =98,1Н. Затем циферблат поворачивают за накатной ободок индикатора до совмещения с нулевым делением шкалы С или, что то же самое, с цифрой 30 красной шкалы В.
Включив двигатель, прикладывают основную нагрузку Р1, которая затем автоматически снимается. Величина твёрдости определяется показаниями большой стрелки индикатора. При вдавливании алмазного конуса отсчёт производят по чёрной, а при вдавливании шарикового наконечника – по красной шкале. Для измерения твёрдости более тонких образцов, а также упрочнённых тонких поверхностных слоёв используют метод суперРоквелла, отличающийся меньшими нагрузками: Ро=29,4 Н, Р=147,2; 294,3
и441,5Н.
4.Оборудование и материалы
Экспериментальная часть работы выполняется путём измерения твёрдости отожжённых и закалённых стальных образцов и образцов из цветных сплавов (бронза, латунь, дюралюминий). Для измерения твёрдости используются твердомеры типов ТШ (метод Бринелля) и ТК (метод Роквелла).
Порядок выполнения работы
1.Изучить основные статические методы измерения твёрдости.
2.Ознакомиться с устройством твердомера ТШ-2М.
3.Определить параметры испытаний для определения твёрдости предложенного образца.
4.Установить на твердомере индентор нужного диаметра, необходимые величины нагрузки и времени испытания.
5.Провести испытание в соответствии с вышеизложенной методикой.
6.Измерить диаметр полученного отпечатка при помощи отсчётного микроскопа, определить число твёрдости по Бринеллю и записать его в соответствии с ГОСТ 9012–59.
7.Ознакомиться с устройством твердомера ТК-2М.
8.Определить параметры испытаний для определения твёрдости предложенного образца и установить их значения на твердомере.
9.Провести испытание, записать полученный результат.
38
Вопросы для самоконтроля
1.Свойства металлов и сплавов: физические, химические, механические, технологические.
2.Статические и динамические методы определения механических свойств.
3.Методы измерения твёрдости, их характеристика; выбор метода и условий испытания.
4.Соотношение чисел твёрдости, измеренных различными методами.
5.Примерные соотношения между твёрдостью по Бринеллю и характеристиками прочности сплавов.
Лабораторная работа № 6 ВЛИЯНИЕ ТЕРМИЧЕСКОЙ ОБРАБОТКИ НА МЕХАНИЧЕСКИЕ СВОЙСТВА КОНСТРУКЦИОННОЙ СТАЛИ
Цель работы: ознакомиться с влиянием отжига и закалки на механические свойства и структуру стали, а также изучить влияние температуры отпуска на механические свойства предварительно закалённой конструкционной стали.
Задание
1.Дать характеристику основным видам термической обработки.
2.Дать краткую характеристику метода испытания стандартных образцов из стали на растяжение и метода испытания образцов с надрезом на удар.
3.Вычертить «стальной» участок диаграммы Fe Fe3C и указать критические точки для стали 45.
4.Провести испытания на растяжение, на удар и определить твёрдость по Роквеллу (шкала С) образцов из стали 45, предварительно подвергнутых закалке с последующим отпуском.
5.Результаты испытаний записать в таблицу.
6.Представить результаты эксперимента в графическом виде, выполнить их анализ.
7.Составить письменный отчёт по работе.
Общие сведения из теории
Одним из основных требований, предъявляемых к конструкционной стали, являются высокие механические свойства.
39
Так, например, углеродистая конструкционная сталь 40 после нор-
мализации должна иметь предел прочности в 580МПа (58кГс/мм2),
предел текучести |
|
340МПа (34кГс/мм2), |
относительное |
сужение |
|
|
Т |
|
19% |
|
|
45 % , относительное удлинение |
и ударную |
вязкость |
ан 0,6 МДж/м2(6кГс/см2).
Однако эти механические свойства могут быть значительно изменены термической обработкой. В зависимости от условий термической обработки для стали одного химического состава можно получить самые различные соотношения характеристик прочности, пластичности и вязкости.
Термическая обработка заключается в нагреве, выдержке и охлаждении стали и сплавов по определённым режимам с целью изменения структуры и получения заданных свойств. К основным факторам воздействия на процесс термической обработки относятся температура и время.
Параметрами, с помощью которых можно регулировать режим термической обработки, служат: максимальная температура нагрева сплава, время выдержки при этой температуре, скорости нагрева и охлаждения.
Температуру нагрева конкретного сплава определяют по диаграмме «железо-цементит». Критические точки, характеризующие температурные границы фазовых превращений, обозначаются буквой «А».
Нижняя критическая точка обозначается «А1». Она лежит на линии PSK (см. рис. 6.1). Верхняя критическая точка «А3 » расположена на линии
GSE.
Чтобы отличить критическую точку при нагреве от критической точки при охлаждении, рядом с буквой «А» ставят соответственно букву «с» или «r».
Это значит, что при нагреве критическая температура « Ас1» характеризует превращение перлита в аустенит, а при охлаждении температура «Аr1» – превращение аустенита в перлит. Конец растворения феррита в аустените при нагреве обозначается критической температурой «Ас3», а начало выделения феррита из аустенита при охлаждении – температурой
«Аr3».
Начало выделения вторичного цементита из аустенита при охлаждении обозначается также «Аr3», а конец растворения вторичного цементита в аустените при нагреве – «Ас3» (очень часто эту точку обозначают Аст ).
Все виды термической обработки разбиты на четыре основные группы (по А.А. Бочвару).
К первой группе относится такой вид термической обработки, при котором металл из неустойчивого состояния, полученного в результате предшествующей обработки, переводится в устойчивое. Эта обработка осуществляется путём нагрева металла и называется отжигом.
40