
ММК Спецтехнология ЛА 2013
.pdfТочность сборочных работ. При сборке машин могут иметь место ошибки взаимного положения их элементов; некачественные сопряжения, а также деформации соединяемых деталей. Погрешности сборки вызываются:
отклонениями размеров, формы и взаимного расположения поверхностей сопрягаемых деталей – эти отклонения влияют на зазоры и натяги, ухудшая заданные посадки, вызывая торцевые и радиальные биения при сборке узлов вращения, несоосности и другие погрешности взаимного положения элементов машины; некачественной обработкой сопрягаемых поверхностей, в результате чего возникает их неплотное прилегание, снижение контактной жесткости стыков и герметичности соединений; неточной установкой и фиксацией элементов машины в процессе ее сборки; некачественной пригонкой и регулировкой сопрягаемых элементов машины; нарушениями условий и режимов выполнения сборочных операций (неравномерная затяжка резьбовых соединений, вызывающая перекосы и деформации при закреплении деталей и узлов в сборочных приспособлениях); геометрическими неточностями сборочного оборудования, приспособлений и инструментов; неточной настройкой сборочного оборудования; тепловыми деформациями элементов технологической системы (сборочное оборудование – приспособление – инструмент – собираемый объект). Погрешности сборки могут возникать также в результате действия остаточных напряжений в материале деталей, не проявившихся полностью при механической обработке.
Точность сборки обеспечивается 4 методами.
Индивидуальной пригонкой сопрягаемых деталей и узлов изделия. Для этой цели применяют припиливание, шабрение, притирку, а также совместную обработку сопряженных поверхностей (растачивание или развертывание отверстий для обеспечения их соосности). Метод применяется в условиях единичного и мелкосерийного производств, а также в тех случаях, когда конструктивные допуски уже технологических.
Регулирование зазоров или взаимного положения элементов изделия. Регулирование осуществляют при помощи компенсаторов (прокладки, клинья, винты), которые должны быть предусмотрены в конструкции изделий. Сопряженные детали обрабатывают по широким допускам, а требуемый зазор обеспечивается индивидуальной установкой или регулированием соответствующего компенсатора.
Выполнением соединений по принципу полной или частичной взаимозаменяемости. Метод применяется в тех случаях, когда конструктивные допуски равны или шире технологических. Сборка ведется без пригоночных и регулировочных работ.
Выполнением соединений по принципу групповой взаимозаменяемости. Детали изделия обрабатывают с широкими допусками, а заданная точность сопряжения обеспечивается непосредственным подбором или предварительной сортировкой деталей на размерные группы. Метод применяется при сборке изделий, имеющих сопряжения высокой точности.
Статистические методы исследования точности.
Погрешности, возникающие при выполнении заготовки, мех. обработки, техническом контроле, сборке и других видах обработки, можно разбить на три вида: систематические постоянные, систематические закономерно изменяющиеся и случайные.
Систематические постоянные погрешности не изменяются при обработке одной или нескольких партий заготовок. Они возникают под влиянием постоянно действующего фактора. Примером подобных погрешностей могут служить: неперпендикулярность оси просверленного отверстия и базовой плоскости заготовки из-за неперпендикулярности оси шпинделя плоскости стола вертикально-сверлильного станка; ошибки межосевого расстояния растачиваемых отверстий из-за неправильно выдержанного расстояния между осями направляющих втулок расточного кондуктора; погрешность формы обтачиваемой поверхности (конусность) в результате непараллельности оси шпинделя направляющим станины токарного станка. Систематические постоянные погрешности могут быть выявлены пробными измерениями нескольких обработанных деталей. Эти погрешности сводятся к желаемому минимуму соответствующими технологическими мероприятиями.
Систематические закономерно изменяющиеся погрешности могут влиять на точность обработки непрерывно или периодически. Примером непрерывно влияющей погрешности может служить погрешность, вызванная размерным износом режущего инструмента. Примером периодически действующей погрешности может служить погрешность, возникающая в результате тепловой деформации станка в период его пуска до достижения теплового равновесия.
Знание закона изменения этих погрешностей позволяет применять меры для их устранения или уменьшения при построении станочных операций.
Случайные погрешности возникают в результате действия большого количества несвязанных между собой факторов. Случайная погрешность может иметь различное значение; определить заранее момент появления и точную величину этой погрешности для каждой конкретной детали в партии не представляется возможным. Случайные погрешности чаще всего являются непрерывными. Непрерывная случайная погрешность может иметь любые численные значения в границах определенного интервала. Примерами непрерывных случайных погрешностей могут служить погрешности положения заготовки на станке, а также погрешности обработки, вызываемые упругими отжатиями технологической системы под влиянием нестабильных сил резания.
Причинная связь между случайной погрешностью и вызывающими ее появление факторами может быть: 1) известной (явной) и 2) не вполне выясненной. Например: для конкретного случая обработки может быть выявлена зависимость упругих отжатий технологической системы от величины снимаемого припуска. Факторы, вызывающие разброс диаметров отверстий, обработанных одной разверткой, является в настоящее время полностью невыясненными.
Несмотря на то, что определение случайной погрешности для каждой детали в партии практически неосуществимо, можно тем не менее установить пределы изменения этой погрешности. При явно выраженной связи между случайной погрешностью и вызывающими ее появление факторами пределы изменения случайной величины могут быть определены аналитическими расчетами. Например: разность предельных расстояний от измерительной базы до обрабатываемой поверхности, представляющую собой погрешность базирования, можно заранее вычислить, зная допуски на размер заготовки. При неявной (невыявленной) связи между случайной погрешностью и влияющими на ее появление факторами пределы изменения случайной величины могут быть установлены на базе экспериментальных исследований.
В процессе изучения явлений невыявленные ранее связи становятся явными. В результате этого можно более полно учитывать влияние различных технологических факторов на точность мех. обработки при разработке технологических процессов.
Статистические методы оценки точности применимы в условиях производства большого количества одинаковых деталей, обрабатываемых как на предварительно настроенных станках, так и методом пробных проходов.
Математическая статистика была той научной базой, на которой начали проводить первые исследования точности технологических процессов. Первым шагом в этом направлении было изучение и анализ кривых распределения.
Построение кривых распределения производится следующим образом. Всю совокупность измерений интересующей величины (например, какого-либо размера в партии заготовок, обработанных при определенных условиях) разбивают на ряд групп. В каждую группу входят величины, результаты измерений которых находятся в пределах установленного интервала. Интервалы, число которых обычно берут в пределах 7-11, откладывают по оси абсцисс, а количество замеров, приходящееся на каждый интервал, по оси ординат. После соединения нанесенных на графики точек получают ломанную, называемую полигоном распределения.

На рис. 12 показан полигон распределения диаметральных размеров колец, подвергнутых предварительному обтачиванию; из него видно, что на средние интервалы размеров приходится большее количество колец. При увеличении количества деталей в партии, сужении интервалов и увеличении их числа ломаная линия приближается к плавной кривой.
Вместо абсолютного количества m деталей в каждом интервале взяли отношение этого количества к общему количеству n деталей в партии (относительная частота).
Рисунок 12
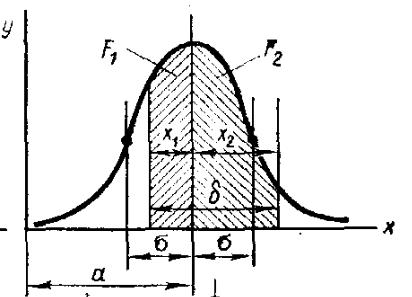
В качестве самой приближенной меры точности исследуемого процесса обработки может служить поле рассеяния размеров. Величину поля рассеяния можно брать по полигону распределения или по таблице измерения исследуемых размеров. Чем уже поле рассеяния, тем точнее исследуемый технологический метод.
Вид кривой распределения определяется количеством и характером факторов, влияющих на исследуемую величину. Многочисленные исследования показали, что в технологии машиностроения распределение размеров чаще всего происходит по так называемому нормальному закону или закону Гаусса. Соответствующая кривая распределения имеет симметричную шатрообразную форму.
Рисунок 13
Кроме закона Гаусса встречаются и другие законы распределения размеров обработанных деталей в партии (з-н равной вероятности, з-н треугольника (Симпсона), з-н эксцентриситета (з-н Релея), з-н распределения модуля разности r двух сходных величин x1 и x2).
Другой метод исследования точности основан на построении точечных диаграмм. По горизонтальной оси откладывают номера обрабатываемых деталей в той последовательности, как они сходят со станка. По вертикальной оси в виде точек откладывают результаты измерений деталей. Подобные диаграммы можно строить как для одной, так и для нескольких последовательно обрабатываемых партий деталей (рис. 14,а). Длину подобных диаграмм можно значительно сократить, если по горизонтальной оси откладывать не номера заготовок, а номера групп деталей, причем в каждую группу входит одинаковое количество последовательно снимаемых со станка деталей (рис. 14,б). На рис 14,в показана диаграмма, по вертикальной оси которой откладываются средние арифметические значения размеров деталей, входящих в каждую группу. На данной диаграмме хорошо видна периодичность изменения размеров в результате непрерывно протекающего износа режущего инструмента и периодически производимых поднастроек станка.

Рисунок 14
Назад