
ММК Спецтехнология ЛА 2013
.pdf
Размерный износ инструмента u систематически изменяет положение его режущей кромки относительно исходной установочной базы заготовок в процессе обработки. В результате этого выполняемый размер непрерывно изменяется между двумя сменами или подналадками инструмента. Величинаu регламентируется определенными значениями для каждого метода обработки в зависимости от допустимого износа инструмента. Приближенно можно считать, что размерный износ u протекает по закону прямой, а соответствующая кривая распределения имеет вид прямоугольника (кривая равной вероятности).
Погрешности выполняемого размера, вызываемые тепловыми деформациями системы, Т изменяется во времени (или от количества обрабатываемых деталей) по более сложному закону.
Рисунок 21
В первоначальный период работы станка они растут; после того как будет достигнуто тепловое равновесие технологической системы, они стабилизируются (точка А). До момента теплового равновесия системы кривая распределения погрешностей имеет вид, показанный на рисунке внизу). По достижении этого момента данная погрешность превращается в систематическую постоянную погрешность (кривая распределения переходит в вертикальную прямую линию).
Первые пять членов выражения (*) представляют собой пределы изменения погрешностей, вызываемых теми или иными технологическими факторами. Последний, шестой, член ф равен сумме погрешностей формы данного элемента, вызываемых геометрическими неточностями станка, деформациями заготовки под влиянием сил закрепления и неравномерными по различным сечениям заготовки упругим отжатием технологической системы (под действием сил резания).
В случае, например, обтачивания консольнозакрепленной заготовкиф будет выражаться разностью диаметров d2 и d1 (рис. 22).
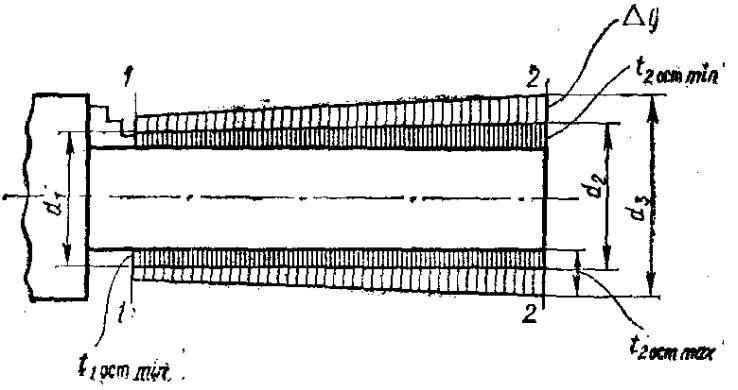
Рисунок 22
Часто заштрихованный участок эпюры характеризует погрешность формы обработанной поверхности, а редко заштрихованный – изменения величины у по различным поперечным сечениям заготовки.
Назад
Задачу определения суммарной погрешности механической обработки можно сравнить с задачей определения допуска на замыкающее звено размерной цепи. При решении этой задачи по максимуму и минимуму члены выражения (*) алгебраически складываются
y н u T ф
Суммарную погрешность диаметральных размеров следует определять без учета величины . Составляющая исключается также при определении суммарной погрешности размера, связывающего два противолежащих элемента, подвергаемых одновременной обработке цельным или наборным инструментом (шпоночные пазы).
Величину ф надо определять с учетом взаимной компенсации ее отдельных составляющих. Например, обтачивая консольно закрепленный в патроне цилиндрический валик, получаем искажение формы поверхности вращения в результате неравномерной жесткости технологической системы в различных поперечных сечениях. В то же время при наличии непараллельности оси шпинделя направляющим станины в горизонтальной плоскости обточенная поверхность получается конической. Если вершина конуса обращена в сторону задней бабки, погрешности формы частично или полностью компенсируются. При обратном положении конуса погрешности формы суммируются.
Рассмотрим определение применительно к случаю обработки приведенному на рисунке, в предположении, что на суммарную погрешность выполняемого размера влияют только два фактора: у и погрешность формы из-за неравномерности упругих отжатий по сечению заготовки. Величину можно определить как разность между диаметрами d3 описанного цилиндра и d1 вписанного:
d3 d1 2* y (d2 d1) 2 y ф
Величину у следует определять по сечению, для которого жесткость системы будет наименьшей, т. е. в данном случае по сечению 2-2 у свободного конца заготовки:
y tост.2 _ max tост.2 _ min
Погрешность формы:
ф 2 * (tост.2 _ max tост.1_ min )
Где индексы 1 и 2 означают сечения в заделке и у свободного конца.
Расчет суммарной погрешности обработке по формуле (*) весьма прост. Однако значение получается завышенным. Даже при большом количестве обрабатываемых заготовок, предельные размеры, соответствующие величине встречаются крайне редко. Принятие технологического допуска по этой величине приводит к увеличению промежуточных общих припусков на обработку.

Рассмотрим другой закон суммирования первичных погрешностей. По аналогии с решением размерных цепей методом неполной взаимозаменяемости суммирование первых пяти членов можно производить по формуле:
t * 1 * y2 2 * 2 3 * н2 4 * u2 5 * T 2
Где t – коэффициент, определяющий процент риска получения брака при обработке: при t=1 процент риска равен 32, при t=2 он равен 4,5, при t=3 он равен 0,27.
1, 2,…- коэффициенты, зависящие от формы кривых распределения соответствующих первичных погрешностей.
Для кривой распределения, близкой к нормальной, =1/9, для кривой равной вероятности и в случае, когда о форме кривой распределения ничего не известно, рекомендуется принимать =1/3. Если кривая распределения близка к треугольнику, то =1/6.
Ранее отмечалось, что распределение величин у, , и Н близко к нормальному, тогда 1= 2= 3=1/9. Распределение величины u подчиняется закону равной вероятности. Следовательно, 4= 1/3. Характер распределения величины Т мало изучен. Поэтому можно принять 5=1/3.

При принятии t=3 можно записать
y 2 2 н2 3 * u 2 3 * T 2
Сучетом погрешностей формы суммарная погрешность выполняемого размера
y2 2 н2 3* u2 3* T 2 ф
При определении суммарной погрешности диаметральных размеров составляющая исключается. В этом случае
y 2 н 2 3 * u 2 3 * T 2 ф

Пример:
Определить , если ф пренебрегается, а у=10мкм, =25 мкм, Н=30 мкм, |
|
u=15 мкм, Т=10 мкм. |
|
=10+25+30+15+10=90 мкм; |
|
102 252 302 3*152 3*102 |
51 мкм |
Если поле допуска на выполняемый размер принять равным 51 мкм, то риск получения брака будет 0,27 %. При поле допуска 90 мкм риск будет ничтожно малым. Коэффициент t риска брака в этом случае вместо 3 равен 5,3. Риск равен 0,00000001 (т. е. из 10 млн. деталей одна может быть бракованной). При поле допуска 51 мкм одна бракованная деталь приходится на партию из 370 деталей.

Определение суммарной погрешности при обработке методом пробных проходов. Рассмотрим суммарную погрешность индивидуально обрабатываемой заготовки методом пробных проходов. В этом случае погрешность выполняемого размера:
y п з u T СТ
Где у – погрешность формы обрабатываемой поверхности, получаемая в результате копирования первичных погрешностей заготовки в условиях упругой технологической системы, жесткость которой различна в отдельных сечениях; п – погрешность установки режущего инструмента на размер (погрешность проверки), зависящая от квалификации рабочего и вида применяемого рабочего инструмента; з
– погрешность формы обработанной поверхности или погрешность ее положения относительно измерительной базы в результате деформации технологической системы от приложения зажимных сил;u – погрешность формы поверхности в результате размерного износа режущего инструмента; Т – погрешности формы, вызываемые тепловыми деформациями технологической системы в процессе обработки одной детали; ст – погрешность формы обрабатываемой поверхности, возникающая из-за геометрических неточностей станка.
Суммирование первичных погрешностей ведется алгебраически, учитывая возможность их частичного или полного перекрытия и взаимной компенсации. Например, при обработке цилиндрической поверхности достаточно жесткой заготовки суммарная погрешность диаметрального размера
y 2 n u T CT
Величина п удваивается в связи с тем, что относится к диаметральному размеру.