
ММК Спецтехнология ЛА 2013
.pdf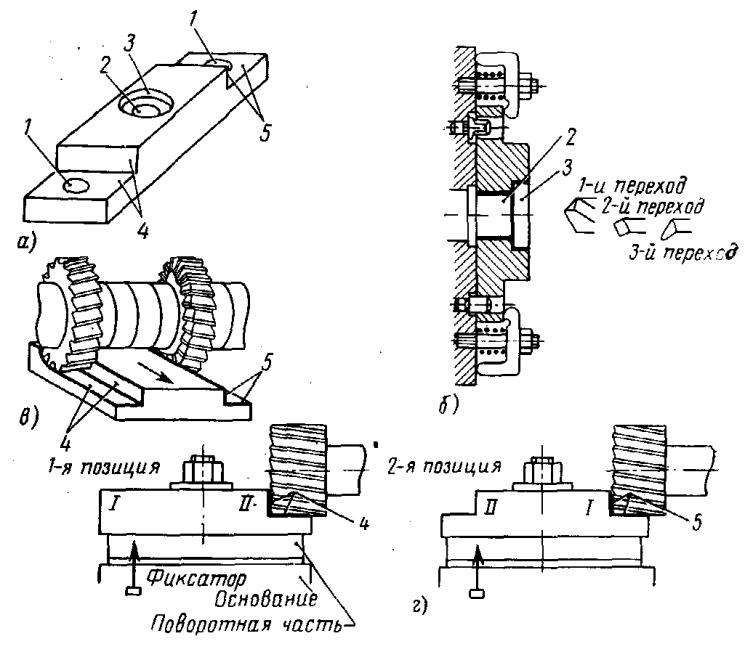
Рисунок 2 |
Назад |
Для повышения производительности часто объединяют несколько
переходов в один сложный переход (совмещение переходов) характеризующийся одновременной обработкой нескольких поверхностей. (Рис.2,в)
Проход – часть перехода, при котором снимается один слой материала. При этом все проходы, если их несколько, выполняют без изменения режима станка.
Приём – совокупность отдельных движений в процессе выполнения операций. Станочная операция по сверлению отверстий в вале (или другой детали) состоит из следующих приёмов: взять вал и установить в приспособление; закрепить вал; включить станок; подвести сверло к валу; включить подачу; выключить подачу; отвести шпиндель в исходное положение; остановить станок; открепить вал; взять вал и положить на стеллаж.
При изменении положения обрабатываемой заготовки (собираемого узла или изделия) операция может состоять из нескольких установок и позиций.
Установом называется часть операции, выполняемая при неизменном закреплении обрабатываемой заготовки (собираемого узла). Например, одновременная центровка обоих торцов вала на двустороннем центровальном станке является одной операцией, выполняемой за один установ. Последовательная центровка торцов такого вала на одностороннем центровальном станке является также одной операцией, но выполняемой уже за два установа.
Обрабатываемая заготовка и собираемое изделие, находясь в приспособлении, могут менять своё положение относительно рабочих элементов оборудования путём поворотных устройств, в этом случае они будут занимать различные позиции.
Позицией называется каждое из различных положений неизменно закреплённого предмета, над которым производится работа. Например, заготовка, обрабатываемая на многошпиндельном токарном автомате, при каждом повороте шпиндельного барабана занимает новую позицию. Установы и позиции влияют на производительность и точность выполняемых технологических процессов.
На рис. 2,г показано фрезерование плоскостей 4 и 5 детали в двух позициях с помощью приспособления. Обработав одну сторону, деталь, не открепляя, поворачивают на 1800 , так что место стороны II занимает сторона I; иначе говоря, деталь из одной позиции переводят в другую. Для этого верхняя часть приспособления, несущая деталь, сделана поворотной и может изменять свое угловое положение относительно нижней части - основания, закрепленного на станке.
Операция является основным расчетным элементом технологического процесса. Время и себестоимость выполнения операции служат критерием, характеризующим целесообразность ее построения в условиях заданной производственной программы.
Технически обоснованной нормой времени называют время, необходимое для выполнения технологической операции в определенных организационно-технических условиях, наиболее благоприятных для данного производства. Технически обоснованную норму времени устанавливают в соответствии с эксплутационными возможностями оборудования, инструментов и других средств производства, при условии применения методов работы, соответствующих современным достижениям производственной техники. На основе технически обоснованных норм времени устанавливают расценки, определяют производительность оборудования, осуществляют календарное планирование производства, выявляют возможность организации многостаночного обслуживания.
Технической нормой времени выработки называют величину, обратную норме времени; выражают ее количеством изделий в единицу времени.
Различают три метода нормирования: метод технического расчета норм по нормативам, метод расчета норм на основе изучения затрат рабочего времени наблюдением и метод сравнения и расчета по укрупненным типовым нормам. При первом методе определение длительности нормируемой операции производят расчетным путем по элементам, используя нормативы, представляющие собой расчетные величины продолжительности выполнения отдельных элементов работы. Норму времени устанавливают в результате анализа последовательности и содержания действий рабочего и машины-орудия при наивыгоднейшем использовании ее эксплуатационных свойств. При втором методе норму времени устанавливают на основе изучения затрат рабочего времени наблюдением непосредственно в производственных условиях. Этот метод имеет особое значение для изучения и обобщения передовых приемов труда, а также для разработки самих нормативов, необходимых для установления технически обоснованных норм расчетным путем. При третьем методе норму времени определяют более приближенно по укрупненным типовым нормативам, которые разрабатывают на основе составления и расчета типовых операций и процессов по отдельным видам работ. Этот метод нормирования применяют при единичном и мелкосерийном изготовлении продукции.
Технически обоснованную норму времени и техническую норму выработки устанавливают на каждую операцию. Для неавтоматизированного производства норма штучного времени:
tш=to+tв+tт+tорг+tп
где to –основное (технологическое)время, tв- вспомогательное время,
tт – время технического обслуживания, tорг – время организационного обслуживания, tп – время перерывов работы.
Основное (технологическое) время учитывает изменение состояния продукта производства в процессе механической обработки или сборки. При станочной обработке основное время определяют расчётом для каждого технологического перехода по формуле:
t0=(L*i)/SM
где L- расчетная длина обработки, мм, i- число проходов в данном переходе; SM – минутная подача инструмента, мм, равная произведению скорости вращения шпинделя n в об/мин на подачу за один оборот (Sоб)
SM=n* Sоб
Величины Sоб и n берутся по нормативам или рассчитываются.
При ручном подводе инструмента величина L получается прибавлением к основной длине обработки l пути врезания lвр и схода lсх режущего инструмента.
L=l+lвр+lсх
При автоматическом цикле обработки к величине L прибавляют небольшой путь подвода инструмента к заготовке lпд для предупреждения удара в начале резания
L=lпд+lвр+l+lсх
Величины lпд и lcх берут порядка 1 мм. Величину lвр определяют из геометрических соотношений. Длину l берут из чертежа заготовки.
Например, на рис.5 показаны составляющие L при сверлении сквозного отверстия (для стандартного сверла lвр=0,3d, где d-диаметр сверла).
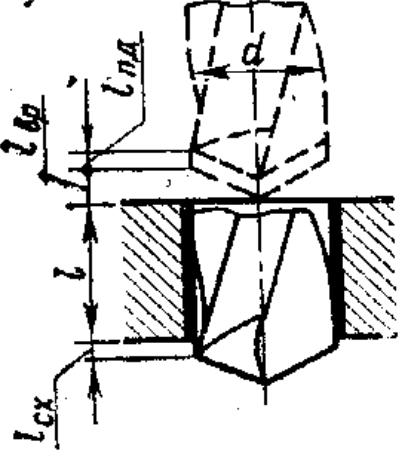
Рисунок 5
Назад

Или, например, при прорезке паза дисковой фрезой (lвр= t * (d t) , где d-диаметр фрезы и t- глубина паза).
Рисунок 6

Для многоинструментальной обработки путь l находят по длине наибольшего участка обрабатываемой поверхности (рис. 7). Величины l вр и l сх в отдельных случаях равны 0 (прорезка узких канавок резцом на шейках вала, проточка шейки до уступа на рис. 7)
Рисунок 7