
Учебное пособие 1720
.pdf
|
|
l x |
|
|
x |
||
|
|
|
|
|
|
|
2 |
|
|
|
|
|
|
з.б |
|
п.б |
|
l |
|
l |
|||
|
|
|
|
|
|
|
|
x |
|
l x |
|
|
|
2 |
2 |
|
|
|
|
|
|
|
|
|
|
суп |
|
|
|
3EJl |
|
|
|
|
. (13)
Уравнение (10) показывает, что податливость системы по длине обработки изменяется.
Жесткость обрабатываемых деталей, элементов станков и оснастки может определяться экспериментально, а также может быть рассчитана по формулам сопротивления материалов и теории упругости.
Например, при обтачивании гладкого вала в центрах (рис. 12) его можно рассматривать как балку, лежащую на двух опорах. В этом случае максимальная деформация будет при нагружении посередине, а величину ее можно определить из выражений:
где l
E –
|
|
|
Р l |
3 |
|
l |
2 |
|
|
|
|
|
|
|
|
|
|||
|
|
|
|
|
|
|
|
||
|
у |
y |
|
; |
|
, |
(14) |
||
|
|
|
|
||||||
|
48EJ |
48EJ |
|||||||
|
|
|
|
|
|
||||
– длина вала; |
J |
– момент инерции поперечного сечения; |
модуль упругости. Отсюда:
|
|
j |
|
Рy |
|
48ЕJ |
. |
||
|
|
|
|
|
3 |
||||
|
|
в |
|
|
у |
|
l |
|
|
|
|
|
|
|
|
|
|
||
С учетом того, что для стального вала |
|||||||||
J 0,05D |
4 |
, формулы (14) |
для гладкого |
||||||
|
посередине будут иметь вид:
|
|
(15) |
E |
5 |
МПа и |
2 10 |
||
вала, |
с нагрузкой |
|
|
D |
4 |
|
j |
2, 4E |
|
||
|
3 |
|||
в |
|
l |
||
|
|
|
|
48000 D
D l
|
3 |
|
|
|
|
|
|
;
(16)
51

|
|
|
1000 |
|
|
В |
j |
||||
|
|
|
|||
|
|
|
|
||
|
|
|
в |
|
1 |
|
|
|
48D |
|
|
l D
|
3 |
|
|
|
|
|
|
.
(17)
Расчет ступенчатого вала можно произвести, определив прогибы всех его ступеней. Для ступенчатости, сужающейся от середины к обоим концам, приближенная формула определения жесткости и податливости имеет вид:
|
|
ЕD |
4 |
|
j |
1,6 |
|
||
|
3 |
|
||
в |
|
l |
|
|
|
|
|
|
32000 D
D l
3
;
(18)
|
|
|
1000 |
|
1 |
|
|
l |
|
3 |
|
|
|
|
|
. |
|||||
В |
|
32D |
|
D |
|
|||||
|
|
|
в |
|
|
|
|
|
||
|
|
|
j |
|
|
|
|
|
Для вычисления деформации гладкого вала, закрепленного в патроне, используется формула:
(19)
консольно
у |
Рyl3 |
|
|
|
, |
(20) |
|
|
|||
|
3EJ |
|
Откуда:
|
|
Р |
j |
|
y |
|
||
в |
|
у |
|
|
|
3ЕJ |
|
ED |
4 |
||
|
0.15 |
|
||||
l |
3 |
l |
3 |
|
||
|
|
|
||||
|
|
|
|
|
1000 1
Вjв 3D
|
|
|
|
3000D |
|||
|
|
|
|
|
l |
3 |
|
. |
|||
|
|
||
|
|||
|
D |
|
D l
|
3 |
|
|
|
|
|
|
;(21)
(22)
Вал, закрепленный в патроне и поддерживаемый центром задней бабки, является статически неопределимой системой. Если считать заделку конца вала в патроне и задний центр абсолютно жесткими, то формула для расчета деформаций при нагрузке посередине будет иметь вид:
|
Рyl3 |
|
|
ув |
|
, |
(23) |
|
|||
|
110EJ |
|
52
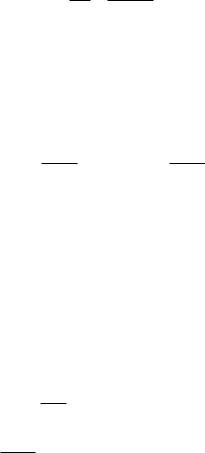
Откуда:
|
|
Р |
j |
|
y |
|
||
в |
|
у |
|
|
|
110ЕJ |
||
l |
3 |
||
|
|||
|
|
.
(24)
Вследствие упругости заделки и податливости заднего центра действительные деформации вала получаются большими, а жесткость меньшей. По данным В. Г. Подпоркина и А. Б. Шраера [13], деформацию можно определить по выражениям:
где
C
90
ув 100 .
|
Р l |
3 |
|
|
СЕJ |
|
||
|
|
|
|
|
||||
|
y |
|
; |
ув |
, |
|||
|
|
|
||||||
СEJ |
l |
3 |
||||||
|
|
|
|
|||||
|
|
|
|
|
Давление на задний центр
(25)
равно
(0,35 ... 0,40)Py
, где
Рy
– усилие, приложенное к середине
детали.
Пример. Определить жесткость и податливость стального ступенчатого вала диаметром 50 мм и длиной 500 мм, установленного в центрах токарного станка, при нагружении посередине.
По формулам (21) и (22) имеем
|
|
|
50 |
|
3 |
|
j |
32000 50 |
16000 |
||||
|
|
|
||||
в |
|
500 |
|
|||
|
|
|
|
|
Н/мм;
|
|
|
1000 |
0,0625 |
|
В |
1600 |
||||
|
|
|
|||
|
|
|
|
мкм/Н.
Деформации режущего инструмента играют весьма важную роль при растачивании. При обработке сравнительно глубоких отверстий консольно закрепленные расточные скалки обычно являются наиболее слабыми звеньями технологической системы, а их низкая жесткость лимитирует режимы резания.
При наружном обтачивании прогибы резцов мало
53
отражаются на точности обработки, так как вершина резца при его изгибе перемещается по касательной к обрабатываемой поверхности, а такое перемещение, как известно, вносит лишь очень малую погрешность.
2.6. Определение суммарной погрешности обработки
Процесс формообразования деталей, как было отмечено выше, является сложным многофакторным, а каждый фактор вызывает образование характерных первичных погрешностей. Определение первичных погрешностей имеет важное значение, но нахождение (расчет) суммарной погрешности обработки является основой расчета технологического процесса на точность. Следует также учесть, что факторы могут действовать как по одному, так и вместе, и влиять как на один параметр, так
ина несколько, потому что параметры точности (размер, форма
ивзаимное расположение поверхностей) взаимосвязаны. Для определения расчетной точности ТП операции необходимо суммировать первичные погрешности. Эта задача с учетом всех перечисленных обстоятельств и того, что первичные погрешности, взаимодействующие в процессе обработки, неоднородны по своему содержанию, становится более сложной. Погрешности могут быть случайные, систематические (постоянные) и комплексные (совокупность случайных и систематических). Поэтому, во-первых, несмотря на значительное количество погрешностей, в расчете суммарной погрешности рассматриваются только основные, позволяющие получить удовлетворительные результаты, а вовторых, для определения суммарной погрешности используется
54
различный математический аппарат, особо для каждого случая обработки и в зависимости от того, какую сущность в данном процессе имеет каждая погрешность. Несмотря на то что на ожидаемую точность оказывают влияние многие факторы, суммирование в большинстве случаев можно проводить по первичным погрешностям, рассмотренным выше. Эти погрешности отражены в структурной формуле (26).
Рассмотрим вопрос суммирования при обработке заготовок на предварительно настроенных станках с использованием приспособлений. Предположим, что имеется такой случай обработки, когда каждая из первичных погрешностей представляет собой звено размерной цепи. Тогда ожидаемую точность Д можно представить как замыкающее звено цепи, и суммирование первичных погрешностей производить алгебраически:
|
y |
|
и |
|
н |
|
T |
|
|
|
|
ф
,
(26)
где |
|
– погрешность |
приспособление или станок; у
установки заготовки на
– погрешность, вызванная
упругими деформациями технологической системы;
и
–
погрешность от размерного износа режущего инструмента;
н
– погрешность, связанная с настройкой режущего инструмента;
T
– погрешность от тепловых деформаций технологической
системы;
ф
– погрешность, связанная с геометрическими
отклонениями оборудования.
Задачу следует решать методом "максимума – минимума". При этом нужно сделать ряд оговорок. Все первичные погрешности здесь отнесены к направлению выдерживаемого размера. Значение ф необходимо
55
определять с учетом взаимной компенсации погрешностей технологической системы. При обработке тел вращения значение для диаметральных размеров нужно определять без учета значения , равно как и для случая двухсторонней обработки элементов изделия набором режущих инструментов.
Анализ конкретного ТП показывает, что в отдельных случаях следует пренебречь и другими слагаемыми.
Расчет значения по формуле (26) является достаточно простым. Вместе с тем точность расчета оказывается низкой, а результат почти всегда завышенным. Даже для случаев обработки большой партии заготовок рассчитанное значение встречается редко, что характерно для расчетов по методу «максимума – минимума».
Возможен и другой метод расчета. Каждую первичную погрешность можно представить как вектор, модуль которого характеризует поле рассеяния погрешности или (что менее точно) разность предельных значений погрешности. Тогда
значение |
следует определять в векторной форме: |
|
|||||||||||
|
r |
r |
r |
|
r |
|
r |
|
r |
|
r |
|
|
|
|
у |
|
и |
|
н |
|
Т |
|
ф . |
(27) |
||
|
|
|
|
|
|
|
|
Этот метод лишь в исключительных случаях можно применять на практике, поскольку необходимо знать направление, в котором проявляется данная погрешность, что связано с трудностями в практической работе технолога. Если каждый вектор, входящий в формулу (27), спроектировать на направление выдерживаемого размера, то задача сложения упростится, так как придется иметь дело уже с коллинеарными векторами:
|
у |
|
и |
|
н |
|
Т |
|
|
|
|
|
|
|
0 |
ф
,
(28)
где индекс "ноль" означает проекцию вектора первичной
56

погрешности. Последняя формула по своей сути аналогична формуле (26).
Каждый из предложенных выше методов суммирования имеет существенные недостатки, которые могут быть в значительной степени ослаблены, если первичные погрешности рассматривать как случайные величины. Такой подход вполне соответствует сути расчетно-статистического метода определения точности.
Как правило, первые пять слагаемых в формуле (26) представляют собой случайные величины. Поэтому суммировать их нужно по закону квадратного корня:
|
p |
|
2 |
|
2 |
|
2 |
|
2 |
|
2 |
, (29) |
||
|
|
у |
и |
н |
Т |
|||||||||
|
|
|
|
2 |
|
1 |
3 |
4 |
5 |
|
||||
где |
p |
– коэффициент, |
определяющий процент риска |
|||||||||||
получения брака при обработке; |
|
|
|
|
|
|
|
|||||||
|
|
– |
коэффициенты, характеризующие |
|
законы |
|||||||||
1 |
5 |
|
|
|
|
|
|
|
|
|
|
|
|
распределения каждой из первичных погрешностей.
Риск возникает в связи с тем, что нельзя утверждать с полной определенностью, что рассеяние данной первичной погрешности соответствует данному закону распределения. При p 1 вероятность брака составляет 32 %, при p 2 она
снижается до 4,5 %, а при |
p 3 доходит до 0,27 % [14]. |
|
Коэффициенты |
|
имеют вполне определенные |
значения для каждого закона распределения. Так, для закона нормального распределения 1/ 9, распределения Симпсона
1/ 6, закона равной вероятности, а также для случаев, когда
озаконе распределения данной первичной погрешности ничего
неизвестно (либо мало известно), Из практики известно,
что
1/ 3. |
|
|
п , |
|
и н имеют |
57

распределение, |
|
|
близкое |
к |
нормальному, |
поэтому |
|||||
|
|
1/ 9 |
. Распределение |
п |
близко к закону равной |
||||||
1 |
2 |
3 |
|
|
|
|
|
|
|
|
|
вероятности, |
|
следовательно, |
|
|
1/ 3 . |
Характер |
|||||
|
|
|
|
|
|
|
|
|
4 |
|
|
распределения |
|
Т |
мало изучен, поэтому |
1/ 3 |
. При p 3 |
||||||
|
|
|
|
|
|
|
|
|
5 |
|
формула (29) имеет вид:
р
|
2 |
|
2 |
|
2 |
3 |
2 |
3 |
2 |
|
у |
н |
и |
Т |
|||||
|
|
|
|
|
|
.
(30)
Величина
ф
не является случайной, поэтому ее
нельзя суммировать под знаком корня. С учетом этой погрешности ожидаемая погрешность:
|
2 |
|
2 |
|
2 |
3 |
2 |
3 |
2 |
|
у |
н |
и |
Т |
|||||
|
|
|
|
|
|
Ф
. (31)
Формулой (31) можно широко пользоваться на практике. Значения первичных погрешностей, суммируемых под знаком корня, представляют собой поле рассеяния этих величин.
Допустим, что в конкретном |
случае |
обработки |
ф 0 , |
|||||||||||
у 10 |
мкм, |
|
25 |
мкм, |
н 30 мкм, |
у 15 |
мкм, |
|||||||
|
Т |
10 |
мкм. Согласно формуле (4.29): |
|
|
|
|
|
||||||
|
|
|
|
|
|
|
|
|
|
|
|
|
|
|
|
|
|
10 25 30 15 10 90 мкм. |
|
|
|||||||||
|
|
Расчет по формуле (4.31) дает: |
|
|
|
|
|
|||||||
|
|
10 |
2 |
2 |
|
2 |
|
2 |
3 10 |
2 |
51 |
мкм. |
|
|
|
|
|
25 30 |
|
3 15 |
|
|
Сравнение результатов этого расчета подтверждает различие в оценке ожидаемой точности.
58
|
|
Проанализируем формулу (31). Погрешность формы |
|
ф |
, вызываемая различными причинами (геометрические |
|
|
погрешности станков, динамические погрешности, деформации заготовок под действием сил закрепления и др.), входит в состав
значения |
, так как допуск на размер, как правило, охватывает |
и отклонение формы. Размер же с учетом отклонений формы измеряют в различных сечениях детали. Предположим, что заготовки обрабатывают на нескольких станках. Тогда геометрические погрешности станков будут иметь рассеяние, и
погрешность ф из систематической превращается в
случайную. В этом случае |
|
ф |
следует суммировать под |
|
|
|
|
знаком корня. |
|
|
|
В другом случае может оказаться, что партия заготовок невелика и может быть обработана при постоянной настройке
системы. Тогда погрешность настройки |
|
н |
следует |
|
|
|
рассматривать как систематическую и не суммировать под знаком корня. Ее нужно исключить из состава значения , но, как было показано выше, поле рассеяния размеров при регулировке этого инструмента будет смещаться.
При обработке малых партий заготовок может слабо проявиться и размерный износ инструмента. Этот же эффект может наблюдаться и при малых колебаниях припусков или твердости заготовок, а следовательно, это повлияет и на
значение |
|
у |
. Таким образом, при малых партиях заготовок |
|
|
|
фактическая суммарная погрешность может оказаться меньше расчетной, что следует иметь в виду.
При обработке одной или нескольких заготовок используют метод пробных ходов и измерений. В этом случае ожидаемую погрешность рассчитывают по формуле:
59
|
|
|
|
|
|
2 |
|
у |
|
и |
|
н |
|
Т |
|
СТ |
..., (32) |
|
|
|
|
1 |
|
|
|
|
|
|
|
||||||
|
|
где |
1 |
– погрешность установки режущего инструмента; |
|||||||||||||
|
|
|
|
|
|
|
|
|
|
|
|
|
|
|
|
|
|
|
2 |
– погрешность |
формы обработанной поверхности или |
||||||||||||||
|
|
|
|
|
|
|
|
|
|
|
|
|
|
|
|
|
погрешность ее положения относительно измерительной базы;
|
y |
– погрешность формы обрабатываемой поверхности из-за |
|||
|
|
|
|
|
|
копирования первичных погрешностей заготовки; |
|
и |
– |
||
|
|
|
|
|
погрешность формы поверхности в результате износа режущего
инструмента; |
Т |
– погрешность формы одной детали из-за |
|||
|
|
|
|
|
|
тепловых деформаций системы; |
|
СТ |
– погрешность формы |
||
|
|
|
|
|
обрабатываемой поверхности, вызываемая геометрическими погрешностями станка.
2.7. Способы достижения заданных размеров
Достижение заданных размеров при обработке на станках обеспечивается двумя способами:
1)способом индивидуального получения размеров путем пробных проходов и измерений;
2)способом автоматизированного получения заданных
размеров.
Достоинством первого способа является возможность получить на станках нормальной точности высокую точность обработки. Например, на универсальном токарно-винторезном
станке можно получить размеры по
5 ... |
7 |
квалитетам. Из-за
значительных потерь времени на пробные проходы и измерения при обработке каждой детали данный способ отличается высокой трудоемкостью и низкой производительностью возможно получение брака. Способ используется в единичном и мелкосерийном производствах. Когда из-за незначительных
60