
Учебное пособие 1720
.pdf−измерение точности кинематических цепей и точности абсолютных перемещений по шкалам;
−исследование статической жесткости;
−температурные испытания:
−испытания станка на виброустойчивость.
При испытании станка на холостом ходу производится:
−проверка работы механизмов главного движения
иподач в рабочем диапазоне;
−оценка быстродействия и переходных режимов привода главного движения;
−проверка действия и точности работы автоматических устройств, упоров и другие;
−проверка мертвого хода подающих винтов ручного управления;
−проверка работы системы смазки и охлаждения;
−проверка работы электрооборудования и гидрооборудования;
−проверка надежности действия защитных
устройств;
−измерение мощности приводов в режиме холостого хода.
При испытании станка на геометрическую точность руководствуются следующими стандартами:
−ГОСТ 22267-76. Станки металлорежущие. Схемы и способы измерений геометрических параметров.
−ГОСТ 25443-82. Станки металлорежущие. Образцы-изделия для проверки точности обработки. Общие технические требования.
−ГОСТ 30527-97. Станки металлорежущие. Методы проверки точности обработки образца-изделия.
111
Исследование статической жесткости станка является достаточно трудоемкой операцией. Суммарную жесткость станка можно характеризовать смещением вершины режущего инструмента относительно жесткой обрабатываемой детали вследствие упругих перемещений элементов под действием силы резания. Поэтому проводят измерение жесткости в процессе обработки. Для этого на станок устанавливают специальную оправку и обрабатывают деталь на различных режимах. По отклонениям от правильности формы обработанной поверхности путем пересчета сил резания оценивают жесткость станка в процессе обработки.
Температурные испытания производятся по стандартным методикам с использованием специальных термометров, терморезисторов, термопар и других устройств. Подробное температурное исследование станка производится, как правило, в тех случаях, когда взаимное положение отдельных узлов и деталей станка непрерывно меняется с момента пуска в процессе работы, стремясь к некоторому относительному положению и вызывая соответствующие изменения размеров и формы обрабатываемых деталей, причем после остановки станка и его остывания все узлы возвращаются в первоначальное положение.
Испытания станка на виброустойчивость проводят с целью:
−оценить виброустойчивость как критерий правильности работы узлов станка;
−установить характер колебаний (вынужденные, автоколебания);
−разработать мероприятия по устранению колебаний
ирассчитать фундаменты для монтажа станков.
112
Преимуществом испытаний станка на виброустойчивость является то, что они производятся, как правило, непосредственно в процессе резания. Основными экспериментальными данными для определения характера и уровня колебаний являются амплитуды и частоты колебаний. В процессе испытаний могут быть установлены возбудители колебаний по близости и кратности частот наблюдаемых колебаний собственным частотам узлов станка. Поэтому обязательным предварительным этапом испытаний является определение собственных частот колебаний узлов станка по главным направлениям. Испытания проводятся при обработке специальных образцов или типичных для данного станка заготовок. Регламент экспресс-испытаний может быть реализован за четыре часа для станков токарной и фрезерной групп, что является приемлемым при проведении испытаний через каждые 6 ... 12 месяцев.
3.6. Жесткость станков
Общие условия испытания станков на жесткость выполняются по ГОСТ 7035-75. Перемещение под нагрузкой стола относительно оправки, закрепленной в шпинделе. Значения допусков перемещения под нагрузкой стола должно соответствовать указанным в табл. 25.
Для широкоуниверсальных станков нормы жесткости указанного класса точности относят только к основному шпинделю. Для универсальных станков с поворотным столом допуск может быть увеличен в 1,12 раза.
Между столом и оправкой создают плавно возрастающую до заданного значения силу F , направление
113

которой определяют углами
,
и |
в соответствии с рис. 35. |
Нагружающую силу прилагают к конусной части диска оправки и направляют через ось оправки.
Таблица 25 Допуски на перемещения стола под нагрузкой
Ширина |
Класс точности |
Нагружающа |
Допуск, мм |
|
стола, мм |
станка, мм |
я сила, кН |
||
|
||||
|
|
|
|
|
200 |
Н |
5 |
0,32 |
|
|
|
|
||
П |
4 |
0,20 |
||
|
||||
|
|
|
|
|
250 |
Н |
8 |
0,40 |
|
|
|
|
||
П |
6,3 |
0,25 |
||
|
||||
|
|
|
|
|
320 |
Н |
12,5 |
0,50 |
|
|
|
|
||
П |
10 |
0,32 |
||
|
||||
|
|
|
|
|
400 |
Н |
20 |
0,63 |
|
|
|
|
||
П |
16 |
0,40 |
||
|
||||
|
|
|
|
Одновременно при помощи индикатора измеряют перемещение оправки относительно стола в направлении поперечной подачи. Проводят двукратные испытания. Наибольшее допускаемое перемещение определяют как среднее арифметическое результатов двух испытаний.
Расположение точки приложения нагружающей силы (табл. 26) по отношению к деталям станка должно соответствовать указанным на рис. 36 и 37 для станков с горизонтальным и вертикальным шпинделями соответственно.
В отверстие шпинделя |
устанавливают оправку 1 |
(рис. 36, 37) и закрепляют. В |
станках с горизонтальным |
шпинделем на свободный конец оправки надевают серьгу 3 и закрепляют на хоботе в заданном положении.
На столе закрепляют устройство для создания
114

нагружающей силы |
F |
используют динамометр.
(рис. 35), для измерения которой
Рис. 35. Направление сил:
α – угол между проекцией нагружающей силы на горизонтальную плоскость и направлением продольной
o |
|
|
|
подачи стола: 40 ; |
|
|
|
β – угол между направлением нагружающей силы и ее |
|||
|
o |
; |
|
проекцией на горизонтальную плоскость: 30 |
|
||
γ – для станков с горизонтальным шпинделем: |
o |
; γ – для |
|
34 |
|||
станков с вертикальным шпинделем: |
o |
|
|
30 ; |
|
|
|
η – угол между проекцией нагружающей силы на |
|
вертикальную плоскость и направлением продольной подачи стола: 37o.
Шпиндельную гильзу или ползун в станках с вертикальным шпинделем устанавливают в верхнее положение, поворотную головку – в нулевое положение. Хобот устанавливают заподлицо с задней стенкой станины.
115

Таблица 26 Расположение точки приложения нагружающей силы
по отношению к деталям станка
Размер, определяющий расположение |
Нормы при ширине стола, мм |
|||||||||||
|
|
|
|
|||||||||
точки приложения силы |
F |
|
|
|
|
|||||||
200 |
250 |
320 |
400 |
|||||||||
|
|
|
|
|
|
|
|
|||||
|
|
|
|
|
|
|
|
|
|
|
|
|
|
|
|
|
|
1 |
|
|
2 |
3 |
4 |
5 |
|
|
|
|
|
|
|
|
|
|
||||
Расстояние |
l |
от |
оси |
шпинделя до |
125 |
140 |
160 |
180 |
||||
рабочей поверхности стола, мм |
||||||||||||
|
|
|
|
|||||||||
|
|
|
|
|
|
|
||||||
Расстояние |
l1 |
от торца шпинделя до |
160 |
180 |
200 |
224 |
||||||
рабочей поверхности стола, мм |
|
|
|
|
||||||||
|
|
|
|
|
|
|
|
|
||||
Расстояние |
l |
2 |
от торца шпинделя до |
52 |
67 |
80 |
95 |
|||||
|
|
|
|
|
|
|||||||
|
|
|
|
|
|
|
|
|||||
точки приложения силы, мм |
|
|
|
|
||||||||
|
|
|
|
|
|
|
|
|
|
|||
Расстояние |
|
|
l |
от |
вертикальных |
|
|
|
|
|||
|
|
|
|
3 |
|
|
|
270 |
280 |
320 |
450 |
|
направляющих |
станины |
до точки |
||||||||||
|
|
|
|
|||||||||
приложения силы, мм |
|
|
|
|
|
|
||||||
|
|
|
|
|
|
|
|
|
|
|||
Расстояние |
l |
4 |
от |
точки |
приложения |
132 |
140 |
160 |
224 |
|||
|
|
|
|
|
|
|
||||||
|
|
|
|
|
|
|
|
|||||
силы до торца подшипника серьги, мм |
|
|
|
|
||||||||
|
|
|
|
|
|
|
|
|
||||
Расстояние |
l |
|
|
от вертикальных |
|
|
|
|
||||
|
5 |
|
|
|
|
305 |
315 |
375 |
505 |
|||
направляющих станины до первого |
||||||||||||
|
|
|
|
|||||||||
паза стола, мм |
|
|
|
|
|
|
|
|
||||
|
|
|
|
|
|
|
|
|
||||
Расстояние |
l |
|
|
от вертикальной оси |
|
|
|
|
||||
|
6 |
|
|
|
|
60 |
67 |
95 |
106 |
|||
|
|
|
|
|
|
|
|
|||||
шпинделя до первого паза стола, мм |
|
|
|
|
||||||||
|
|
|
|
|
|
|||||||
Диаметр D |
конусной части |
|
|
|
|
|||||||
испытательной оправки в точке |
80 |
100 |
125 |
160 |
||||||||
приложения нагружающей силы, мм |
|
|
|
|
||||||||
|
|
|
|
|
||||||||
Диаметр цилиндрической части |
|
|
|
|
||||||||
испытательной оправки, мм: |
|
|
|
|
||||||||
|
|
|
|
d |
|
|
45 |
55 |
65 |
75 |
||
|
|
|
|
|
|
|
|
|||||
|
|
|
|
d1 |
|
|
45 |
55 |
60 |
71 |
||
|
|
|
|
|
|
|
|
|
|
|||
|
|
|
|
|
|
|
|
|
|
|
|
116

Рис. 36. Расположение точки приложения нагружающей силы по отношению к деталям станка
Рис. 37. Расположение точки приложения нагружающей Силы по отношению к столу
117

Перед каждым испытанием хоботу с серьгой, консоли, салазкам, столу и шпиндельной гильзе сообщают перемещения с последующей установкой их в заданное положение, а шпиндель поворачивают. При этом консоль подводят в положение проверки перемещением снизу вверх, салазки – перемещением к зеркалу станины, хобот с серьгой – перемещением от зеркала станины, а стол устанавливают в среднее положение перемещением справа налево.
При испытаниях консоль, поворотный стол, хобот и шпиндельную гильзу закрепляют. Показывающий прибор 2 устанавливают на столе так, чтобы его измерительный наконечник касался:
1)торца диска оправки в точке, расположенной у периферии в горизонтальной плоскости, проходящей через ось оправки – на станках с горизонтальным шпинделем;
2)образующей цилиндрического пояска, лежащей в плоскости, проходящей через ось оправки и перпендикулярной зеркалу станины – на станках с вертикальным шпинделем.
3.7 Средства виброизоляции
Виброизоляция станков может осуществляться установкой их на упругие опоры на полу цеха или на упругоопертый фундаментный блок. При установке станков на полу используются виброизолирующие опоры и накладки, которые могут размещаться непосредственно под станиной.
Виброизоляцию с помощью упруго-опертого вспомогательного блока осуществляют в 2-х вариантах –
опорном и подвесном (рис. 38).
118
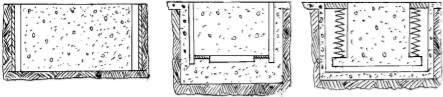
Применяют различные способы опирания блока – по всей длине или в отдельных точках (на стальных пружинах, на резиновых, резинометаллических и других виброизоляторах).
а б в
Рис. 38. Упруго-опертый вспомогательный блок:
а – опорный по всей длине; б – опорный на отдельных участках-ковриках; в – подвесной на стальных пружинах
Из всего разнообразия средств виброизоляции и виброизолирующих материалов наибольшее распространение получают те, для которых можно заранее надежно определить и реализовать заданные параметры виброизоляции.
Рассмотрим только основные рекомендуемые средства виброизоляции станков, в объеме, необходимом для общего представления и для непосредственного решения основных практических задач.
В настоящее время известно большое количество виброизолирующих опор, различающихся материалом упругого элемента (резиновые, резинометаллические, металл с пружинами, из фетра, пробки др.).
Такие конструкции обеспечивают частоту колебаний Fz 10 Гц при нагрузке 100 – 4000 кгс. Основные конструкции отечественных опор – резинометаллических ОВ-
31 и ОВ-33.
119
Для равночастотных опор жесткость примерно пропорциональна нагрузке и поэтому частота собственных колебаний станка мало зависит от нагрузки на опору. Это существенно упрощает подбор опор, так как не нужно вычислять опорные реакции от веса станка, и требуется только определить, не превышает ли нагрузка на опору предельно допустимую. Преимущества равночастотных опор по сравнению с опорами с линейными характеристиками проявляются и в том, что изменение веса детали или перемещение тяжелых узлов станка не вызывает перегрузки опор, один типоразмер может использоваться для установки разных машин и т. п.
Опоры ОВ имеют устройство для выверки станка по уровню. Величина регулирования по высоте для опоры ОВ-1 8 мм и для опоры ОВ-31 15 мм. Специальная конструкция нижнего основания опор обеспечивает хорошее его сцепление с поверхностью пола; срок службы опор ОВ не менее 10 лет.
Однако при установке станка на опоры ОВ-31 и ОВ-33 в результате ползучести резины точность установки станка с течением времени теряется.
Для уменьшения потери точности установки необходимо надежно закреплять контргайки на опорах и повторно выверять станки по уровню через 3 – 4 дня после установки. Выверка станка производится при среднем положении узлов.
В связи с тем, что при установке станка на упругих опорах наблюдаются большие его наклоны при перемещении подвижных узлов, при проверках станка по нормам точности, связанным с использованием уровней, необходимо использовать два уровня:
120