
2514
.pdf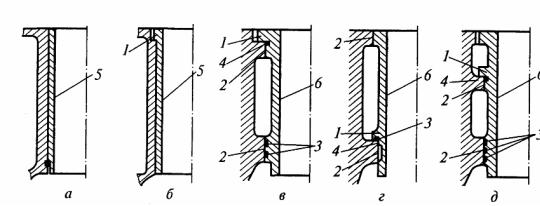
ников обычно расположены ниже линии разъема с поддоном и крепятся болтами или шпильками (рис. 14.1, б). Иногда крышку или подвеску стягивают горизонтальными шпильками (рис. 14.1, в) для увеличения жесткости. На нижнем фланце картера расположены четыре прилива, которыми двигатель опирается на раму автомобиля через амортизационные подушки. При нижнем расположении кулачкового валика механизма газораспределения в картере размещены его подшипники.
Рис. 14.2. Основные типы гильз цилиндров:
а – сухая без опорного бурта; б – сухая с верхним опорным буртом; в – мокрая с верхним опорным фланцем; г – мокрая с нижним опорным фланцем; д – мокрая со средним опорным фланцем; 1 – опорный фланец; 2 – направляющие (центрирующие) пояса; 3 – уплотнительные кольца; 4 – опорный бурт; 5 – сухая гильза; 6 – мокрая гильза
Поддон обычно штампуют из листовой стали. Иногда крышку коренных опор коленчатого вала объединяют в монолитную конструкцию коробчатой формы, называемую постельной плитой.
При жидкостном охлаждении цилиндров применяют конструкции с несущей рубашкой, несущими силовыми шпильками или с несущим блоком цилиндров.
Применение цельнолитого блока цилиндров с рубашкой водяного охлаждения обеспечивает высокую прочность и жесткость блоккартера, уменьшает габариты и массу, сокращает объем механической обработки. Однако необходимо обеспечить повышенную износостойкость зеркала цилиндра за счет хонингования и особых покрытий для удержания масла на поверхности зеркала. Выход из строя одного цилиндра приводит к необходимости замены всего блока. Блоки цилиндров с вставными гильзами, сухими и мокрыми представлены на рис. 14.2. Сухие гильзы с опорными буртами запрессовывают в блок или устанавливают по скользящей посадке.
Мокрые гильзы (см. рис. 14.2) также запрессовываются в блок до
80
опорного фланца 1, который может быть в верхней, средней или нижней части гильзы. Более низкое расположение фланца улучшает охлаждение наиболее нагруженной термически верхней части гильзы. Для уменьшения деформации от боковой силы поршня N служат два пояска 2, а для герметизации рубашки в канавках у поясков помещают уплотнительные кольца из фторкаучука, фторугольноводородного каучука или из резины.
Верхний посадочный пояс располагают так, чтобы при положении поршня в ВМТ его днище находилось на уровне жидкости в рубашке.
Верхний торец гильзы должен выступать на 0,05…0,15 мм над поверхностью блока для обеспечения надежной герметизации газового стыка.
Толщина стенок гильз 5…8 мм. Длина цилиндра должна обеспечивать движение противовесов и шатуна, допускается выход нижнего края юбки в НМТ на величину 0,2D, если это не мешает нижнему маслосъемному кольцу. Высота водяной рубашки ограничивается осью пальца, что составляет около 70 % хода поршня S. Гильзы цилиндров изготавливают центробежным литьем из серых малолегированных чугунов перлитной структуры со среднепластинчатым графитом с добавками хрома, молибдена, фосфора, меди, ванадия для повышения износокоррозионной стойкости или из азотируемых сталей.
Для снижения угара масла и повышения износостойкости на зеркале цилиндра создают особый рельеф методом накатки или хонингования.
Коренные подшипники
Это наиболее нагруженные элементы, они должны обеспечивать соосность коренных опор и отсутствие деформаций. Поэтому крышки подшипников фиксируются в перегородке картера по боковым и торцевым поверхностям с обеспечением натяга вертикальными и горизонтальными шпильками или болтами. Кроме того, крышки иногда фиксируют штифтами или призонными втулками. В алюминиевых картерах для фиксации анкерных шпилек устанавливают бронзовые футорки. Вкладыши подшипников устанавливают с натягом и фиксируют штифтами. В картере расположена масляная магистраль 10-14 мм и каналы 3 - 5 мм подачи смазки к подшипникам коленвала.
Картеры изготавливают из чугуна или алюминиевого сплава. Алюминиевые картеры уменьшают массу на 30 % и массу всего дви-
81
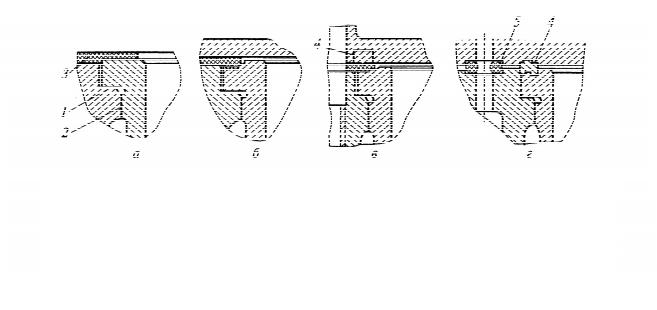
гателя на 12...20 %, они обеспечивают лучший теплоотвод, но имеют большие температурные расширения, которые надо учитывать. Цилиндры также изготавливают из алюминиевого сплава, содержащего 30 % кремния. Перспективен для картеров чугун с перлитным коагулярным графитом, имеющий в два раза большую прочность по сравнению с серым чугуном, что позволяет снизить вес и приблизиться к алюминию.
Головка цилиндров кроме уплотнения газового стыка, размещения клапанов, свеч, форсунок, впускных и выпускных каналов и необходимой формы камеры сгорания обеспечивает режим теплоотвода и снижение тепловой напряженности. В дизелях с разделенными камерами сгорания вихревые камеры сгорания (КС) и предкамеры располагают в головке, причем нижняя часть изготавливается из жаростойкой стали.
Головка является наиболее нагруженной деталью от анкерных болтов и термических напряжений. При неудачно организованном охлаждении в перемычках между клапанами образуются трещины, а иногда – прогар. При больших деформациях может появиться разгерметизация клапанов и газового стыка.
Уплотнение газового стыка осуществляется специальными прокладками и резиновыми кольцами (рис. 14.3).
Прокладки бывают:
1.Из тонкого листа мягкой стали, меди или алюминия.
2.Наборно - металлические, набор или пакет тонких листов мягкого металла.
3.В виде сетки или перфорированного листа стали или алюминия с наполнителем из листов графитизированного термостойкого картона с пропиткой резиной. Иногда на каждом цилиндре устанав-
Рис. 14.3. Уплотнение газового стыка:
а – с уплотняющей прокладкой и плоским торцом гильзы; б – с прокладкой и выступающим буртиком верхнего торца гильзы; в – с прокладкой и
уплотняющим кольцом; г – с уплотняющим кольцом; 1 – опорная плос82
кость; 2 – центрирующий пояс; 3 – прокладка; 4 – уплотняющее кольцо; 5 – резиновое кольцо уплотнения жидкостного стыка

ливают кольца из красной меди или алюминия, заполняющие канавки торца гильзы при затяжке анкерных болтов. Для уплотнения водо - масляных каналов устанавливают резиновые кольца.
У двигателей с воздушным охлаждением корпус состоит из картера с установленными на нем отдельными цилиндрами. Для интенсификации теплоотвода наружную поверхность цилиндров и головок оребряют. Ребра обычно выполняют длиной 50...60 мм с шагом 3,5...8 мм. Допустимая температура 215...230 °С.
Оценка работоспособности газового стыка
Герметичность газового стыка в основном зависит от действующих в нем сил:
Рш – силы предварительной затяжки шпилек или болтов; Рг – газовых сил;
Рт – термических сил, возникающих при нагреве из-за разницы коэффициентов линейного расширения стягиваемых деталей: блока цилиндров или цилиндра, уплотняющей прокладки, головки и шпильки или болта.
Газовая сила Рг сжимает головку, прокладку, цилиндр или блок цилиндров и растягивает шпильку дополнительно к силе Рш, возникшей при сборке газового стыка от затяжки шпилек (болтов). При нагреве шпильки усилие затяжки стыка ослабевает, а при нагреве головки, блока цилиндров (цилиндра) и прокладки увеличивается (рис. 14.4).
Максимальная сила давления газов Рг берется из теплового расчета. Усилие, растягивающее шпильку, равно
Р |
|
1 |
Р D2 |
Р |
|
|
||
|
|
|
|
г п |
, |
(14.1) |
||
|
|
4 |
||||||
ш |
|
|
i |
зат |
|
|
где i – число шпилек, приходящихся на один цилиндр; Dп – диаметр поршня; Рзат – усилие затяжки шпилек (болтов) при сборке;
Рзат l EшFш ; l – вытяжка шпильки. l
Максимальная сила, сжимающая головку, равна
|
Ргол Рш i Рг . |
(14.2) |
Минимальная сила, сжимающая прокладку и блок цилиндров, |
||
|
Pш i Pг , а максимальная Pсж |
Pш i. |
равна Pсж |
В соответствии с законом Гука, каждая из сил вызывает в стягиваемых деталях упругие деформации:
83
в шпильке |
|
Рш |
|
|
|
|
|
|
, |
(14.3) |
|
E F |
|
||||
ш |
|
/l |
|
||
|
|
ш ш |
ш |
|
где ш – упругая деформация шпильки; Eш – модуль упругости шпильки; Fш – минимальная площадь сечения шпильки; lш – деформируемая длина шпильки; Рш – сила, растягивающая шпильку.
Аналогично: деформация головки равна
гол |
|
|
|
|
|
Ргол |
|
|
|
, |
(14.4) |
E |
гол |
F |
/l |
||||||||
деформация прокладки равна |
гол |
|
гол |
|
|
||||||
|
Рсж |
|
|
|
|
|
|||||
|
|
|
|
|
, |
|
|
(14.5) |
|||
E F /l |
|
|
|||||||||
п |
|
|
п |
|
|
||||||
деформация блока цилиндров |
|
п |
п |
|
|
||||||
|
|
Рсж |
|
|
|
|
|
||||
|
|
|
|
. |
|
(14.6) |
|||||
|
|
|
|
|
|||||||
|
б |
|
E F /l |
|
|
||||||
|
|
|
|
|
|
б б |
|
б |
|
|
Тогда взаимодействие деформаций всех деталей газового стыка можно записать ш гол п б , где ш – упругая деформация растяжения одной шпильки; гол и б – упругие деформации головки и блока цилиндров соответственно; п – упругие деформации прокладки.
При нагреве деталей газового стыка возникают тепловые деформации:
шт шlш tш – тепловая деформация шпильки;
гол.т голlгол tгол – тепловая деформация головки;пт пlп tп – тепловая деформация прокладки;
бт бlб tб – тепловая деформация блока цилиндров. Примечание. Знак у t берется +при нагреве и – при охлаждении. Условие совместности деформаций газового стыка при нагреве
принимает вид
( ш шт ) гол гол.т п пт б бт ,
ш шт гол п б гол.т пт бт .
|
|
(14.7) |
|
Деформации: упругая |
тепловая |
||
|
|||
84 |
|
|
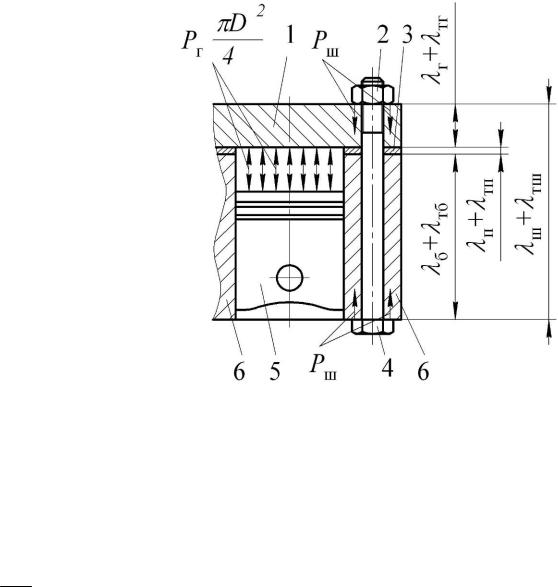
Пусть |
|
Т |
|
|
|
|
|
|
. |
(14.8) |
|
|
|
|
|
гол |
п |
б |
гол.т |
пт |
бт |
|
|
Тогда |
|
|
|
|
|
Т . |
|
|
|
|
|
Из (14.3) Рш ш |
|
ш |
|
шт |
|
|
|
|
|||
Eш Fш /lш , разделив на Fш , получим |
|
||||||||||
Т |
E |
|
|
|
|
|
|
|
|
|
|
ш ш |
ш |
. (14.9) |
|
|
|
|
|
|
|
||
l |
|
|
|
|
|
|
|
||||
|
ш |
|
|
|
|
|
|
|
|
|
Порядок расчета:
1.Определяют напряжения в резьбовой части шпильки по ее минимальному диаметру для максимального нагружения шпильки по параметрам цикла.
2.Увеличивают диаметр шпильки, умножая на коэффициент концентрации напря-
жений K / м п , который для шпилек из легированных сталей ра-
вен 4…5,5.
3. Дополнительно увеличивают диаметр на коэффициент запаса =1,3…2, но при этом обеспечивают вытяжку шпильки (ее относительнуюдеформацию) .
lш 0,06...0,07 lш
(до 0,15) для коротких (жестких) шпилек, по-
следние, как правило, используются для деталей из алюминиевого сплава. l – фактическое упругое удлинение шпильки после затяжки
Т
гаек. l должно превышать в 2…2,5 раза шт , не вызывая остаточных деформаций во всех деталях газового стыка.
85
Возникающие дефекты разгерметизации стыка связаны с неправильной затяжкой шпилек из-за трения в резьбе и по торцу гайки. Поэтому необходимо контролировать удлинение шпильки после затяжки по ее торцу.
Важно, чтобы упругая деформация шпильки или болта была больше деформаций сжатия всего набора газового стыка при охлаждении деталей и не вызывала пластических деформаций при нагреве.
Лекция 15. Механизм газораспределения (МГР)
Механизм газораспределения современного двигателя не только обеспечивает поступление необходимой массы свежего воздуха в цилиндры, но и участвует в оптимизации наполнения воздухом на нескольких режимах или во всем рабочем диапазоне частот вращения. Эти функции МГР приобретает с помощью устройства управления фазами газораспределения и регулирования высотой подъема клапанов.
Механизм газораспределения состоит из клапанов, пружин клапанов с опорными тарелками и сухариками, рычагов или коромыслов, кулачковых или распределительных валиков, цепных или зубчатых приводов вращения кулачковых валиков, а также механизмов управления фазами газораспределения и высотой подъема клапанов.
Конструкции современных МГР различаются:
1.Количеством клапанов на один цилиндр.
2.Системой размещения клапанов в головке цилиндра.
3.Способом привода клапанов.
4.Количеством и расположением распределительных валов.
5.Конструкцией привода распределительных валов.
6.Способом и конструкцией устройств изменения фаз газораспределения и подъема клапанов.
При выборе размещения клапанов учитывают:
1.Исключение зон головки цилиндров, где контрастные темпера-
туры.
2.Упрощение технологии изготовления головки цилиндров за счет объединения каналов одноименного газоснабжения.
Наиболее применяемые 2-, 3-, 4-, 5- клапанные механизмы представленынарис.15.1, где показано ихрасположение в головкецилиндра.
Рассмотрим привод клапанов. Основное требование к конструкции – минимальная масса движущихся частей при максимальной жесткости. Верхние распределительные валы: один (рис. 15.2) или два (рис. 15.3) размещаются на головке блока цилиндров.
86
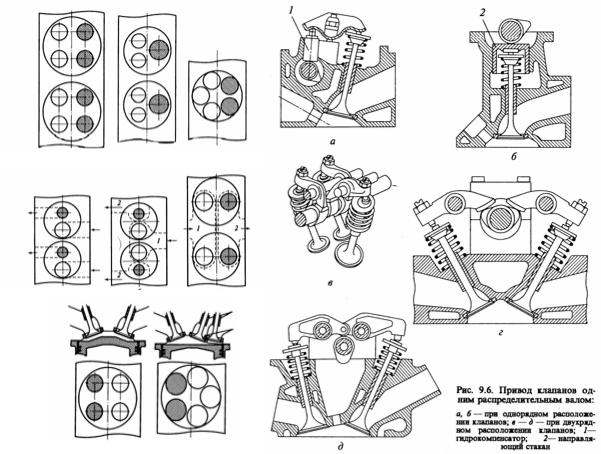
|
|
|
Рис. 15.1. Расположение кла- |
Рис. 15.2. Привод клапанов одним |
|
панов многоклапанных ме- |
распределительным валом |
|
ханизмов в головке цилиндра |
|
|
Привод клапанов при расположении клапанов в один ряд выполняется или через коромысло 1 (рис. 15,2, а) или непосредственно от кулачка через стакан 2. При двух или трех клапанах, расположенных в двух рядах: при одном распределительном вале (рис. 15.2 в, г) – через коромысла, а при двух распределительных валах (рис. 15.3) либо от кулачков, через направляющие стаканы (б), либо с помощью рычагов (а), при пяти – от кулачков (г). На рис. 15.4 приведен привод с нижним или средним расположением распределительного вала. Он содержит коромысло 1, штангу 2, толкатель 3 и кулачок.
Такая конструкция имеет большую массу при малой жесткости, поэтому применяется ограниченно и при частотах вращения менее 4000 мин-1. При этом нижний распределительный вал размещается либо в картере, либо в развале блока цилиндров V-образного двигателя. Нижний распределительный вал приводится во вращение косозубыми шестернями или цепной передачей.
В случае использования в МГР специальных систем управления применяют индивидуальный привод.
87
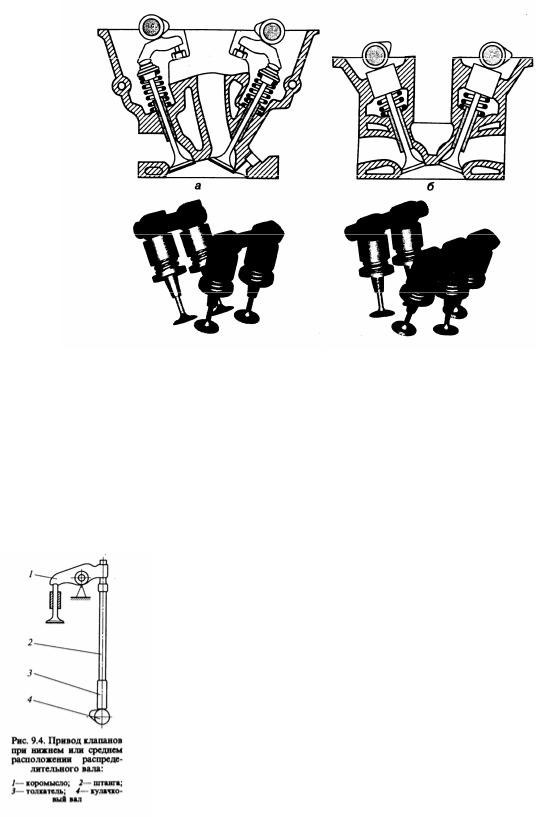
Рис. 15.3. Привод клапанов двумя распределительными валами
Распределительные валы изготавливают из малоуглеродистой стали (12ХН3А, 15Н2М, 20Х) или из среднеуглеродистой стали (45, 45Х). Заготовку получают ковкой в штампах и фрезеруют опорные шейки и кулачки по копиру, после чего проводится цементация малоуглеродистых сталей и закалка ТВЧ на глубину 2...6 мм до твердости 50...60 HRC. Затем опорные кулачки и шейки шлифуются и полиру-
|
ются. При нижнем расположении распредели- |
|
тельного вала подшипники опорных шеек изго- |
|
тавливаются из биметаллических втулок с залив- |
|
кой сплавом СОС6-6 или из алюминиевых вту- |
|
лок, которые запрессовываются в картер или |
|
блок цилиндров. При размещении вала в алюми- |
|
ниевой головке цилиндров используются разъ- |
|
емные подшипники на опорных стойках. В чу- |
|
гунные стойки устанавливают вкладыши с анти- |
Рис. 15.4. Привод |
|
клапанов при |
фрикционной заливкой. Масло подается к под- |
нижнем или сред- |
шипникам нижних распределительных валов по |
нем расположе- |
каналам в перегородках картера, а к подшипни- |
нии распредели- |
кам верхних валов – через внутреннюю полость |
тельного вала |
вала и систему поперечных отверстий в опорных |
|
шейках и кулачках. В осевом направлении вал |
|
88 |
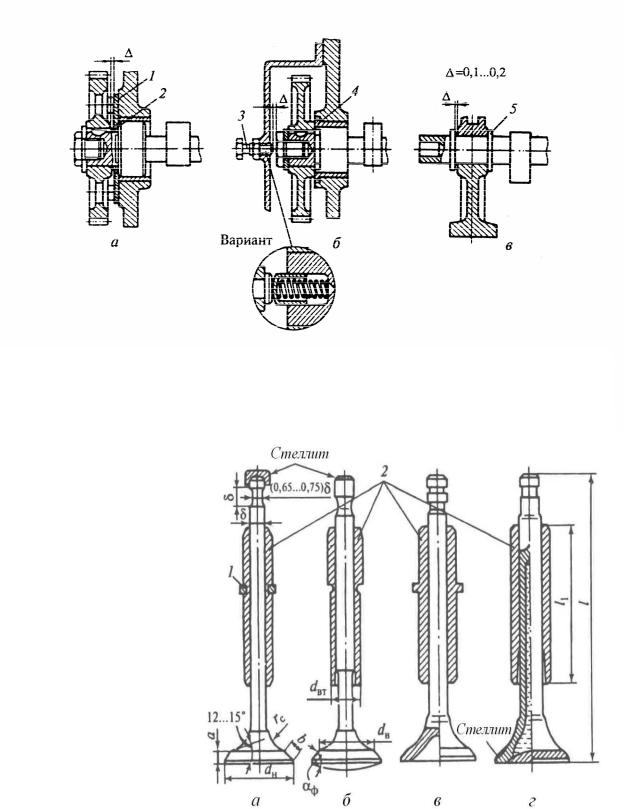
Рис. 15.5. Фиксация распределительного вала от осевых перемещений: а – бронзовым упорным фланцем; б – буртиком подшипника и регулировоч-
ным болтом; в – буртиками; 1 – упорное кольцо; 2 – дистанционная втулка; 3 – регулировочный винт; 4 – подшипниковая втулка; 5 – упорный буртик
фиксируется стальным или бронзовым фланцем 1 (рис. 15.5), или может фиксироваться буртиком подшипника 4, а с другой стороны болтом 3. При разъемных подшипниках вал фиксируется буртиками 5.
Клапаны (рис. 15.6) изготавливают из сталей 38ХС, 40ХН, 40Х9С2, 40ХН2МА.
Средняя температура впускных клапа-
нов300…400°С,авы-
пускныхвДсИЗдости-
Рис. 15.6. Клапаны двигателей:
а, г – плоские; б – выпуклые; в – тюльпанообразные; 1 – стопорное кольцо; 2 – направляющая втулка
89