
2514
.pdfдеформированного состояния деталей производят на следующих режимах:
1.Режим номинальной мощности при частоте вращения nном. На этом режиме, как правило, возникает максимальное значение температур наиболее нагруженных деталей, а в случае с наддувом добавляется максимальное давление газов.
2.Режим максимального крутящего момента, когда при частоте вращения n = (0,5…0,7) nном силы давления газов становятся максимальными, в особенности для двигателей наземного транспорта. Здесь силы инерции существенно ниже, что повышает нагрузки от газовых сил.
3.Режим холостого хода для высокооборотных двигателей при максимальной частоте вращения, допускаемой регулятором, достигает для дизельных двигателей nхол = (1,05…1,07) nном, для двигателей с принудительным воспламенением nхол = (1,1…1,15) nном, а для двигателей без ограничения регулятором – nхол = (1,4…1,6) nном.
4.Проверочные расчеты при неустановившихся режимах во время пуска и сброса нагрузки, когда в некоторых рабочих циклах давление газа может превышать в 1,5 раза расчетное значение на установившихся режимах, а при сбросе нагрузки, когда угловая скорость значительно превосходит nном, возрастают силы инерции поступательно движущихся масс. Для деталей таких двигателей вводят коэффициент перегрузки 1,3…1,5.
Оценка прочности деталей ДВС
При оценке прочностной надежности ДВС применяют метод определения коэффициентов запаса прочности.
Под коэффициентом запаса прочности принимается отношение величины предельного допустимого напряжения пред в эксплуатации при работе детали ДВС к максимальному расчетному значению напряжения max, при заданных условиях.
n |
пред |
|
(2.9) |
|
max |
||||
|
|
|||
Условие прочностной надежности имеет вид: n [n], |
(2.10) |
где [n] – допустимое значение запаса прочности.
Здесь нужно отметить, что значение max – это величина напряжений, полученных для определенного сечения детали по выбранной расчетной методике.
20
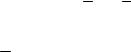
При постоянных по времени нагрузках рекомендуется [n] брать около 1,8…2,0, а при случайных переменных нагрузках [n] принима-
ют 3…5.
Следует заметить, что коэффициентом запаса [n] оценивают неточность методики расчета напряжений в деталях. Они устанавливаются для каждой типовой детали ДВС на основании обработки результатов эксплуатации с помощью теории надежности.
Модель прочностной надежности детали двигателя включает модель материала, модель нагружения, модель формы детали и модель разрушения. Как показала практика, наиболее точно определить напряжения в деталях с учетом температурных и динамических воздействий позволяет применение метода конечных элементов.
Для предварительных расчетов вариантов конструкций допустимо использование типовых стержней, пластинок и оболочек. Но при практической оценке необходимо рассматривать материал детали как сплошной среды.
Многочисленные эксперименты показали, что использование модели сплошной среды при прочностных расчетах деталей двигателей правомерно, и применение метода конечных элементов для оценки напряжений позволяет снижать запасы прочности в 2…3 раза.
Оценка прочности деталей связана с видом разрушения. По излому судят или это хрупкий мгновенный излом, или это усталостный от многоциклового нагружения, или это малоцикловый излом, или разрушение от ползучести материала при высоких температурах, или это термическая усталость при переменных тепловых нагрузках. Виды разрушения зависят также от свойств материала, главным образом, от упругости и пластичности.
Взависимости от условий эксплуатации эти все характеристики могут быть постоянными или статистическими, т.е. имеющими значительный разброс значений, действующих нагрузок и температур.
Вэтом случае принимают для расчетов средние значения и учитывают закон распределения случайной величины. Обычно принимают нормальный закон распределения. На рис. 2.2 представлены нор-
мальные распределения плотности фактора прочности материала и напряженности . Приняв средние значения и за наиболее вероятные в эксплуатации, получим наиболее вероятный запас прочности,
|
|
|
, |
(2.11) |
|
n |
|||||
|
21
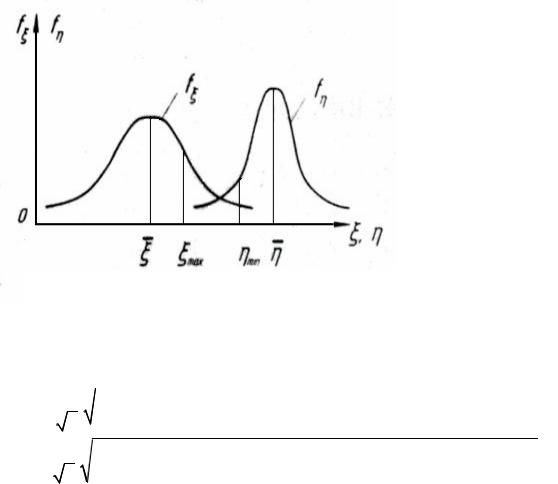
который зависит от величины разброса случайных величин. Как показывает практика, на вероятность разрушения больше влияет разброс значений прочности, чем разброс значений разрушений. Теория надежности машин и механизмов изучает методы повышения стабильности прочностных свойств материалов и действующих в эксплуатации нагрузок. По ней также оценивают необходимые запасы прочности по результатам длительной эксплуатации каждого элемента конструкции.
Прочностные свойства материалов для различных условий нагружения изучают по специальным стандартным методикам. В условиях одноосного напряженного состояния на гладких цилиндрических образцах как при однократной или длительной постоянной нагрузке растяжения, так и при циклическом нагружении.
При многоосном напряженном состоянии вычисляют эквивалентные напряжения i и эквивалентную деформацию i.
|
|
1 |
|
|
|
|
|
|
|
|
|
|
2 |
|
|
|
|
|
2 |
|
|
|
|
|
2 |
|
|
2 |
|
2 |
|
2 |
(2.12) |
|||||
i |
|
|
|
|
|
|
|
|
|
( x y) |
|
( y z) |
|
( z x) |
|
6( xy |
yz zx) |
|||||||||||||||||||||
|
|
|
|
|
|
|
|
|
||||||||||||||||||||||||||||||
|
|
|
|
|
|
|||||||||||||||||||||||||||||||||
|
|
2 |
|
|
|
|
|
|
|
|
|
|
|
|
|
|
|
|
|
|
|
|
|
|
|
|
|
|
|
|
|
|
||||||
|
|
|
1 |
|
|
|
|
|
|
|
|
|
|
|
|
|
|
|
|
|
|
|
|
|
|
|
|
|
|
|||||||||
|
i |
|
|
|
|
|
( |
|
|
|
)2 |
( |
|
|
|
)2 ( |
|
|
|
)2 6( |
2 |
|
2 |
|
2 |
). |
(2.13) |
|||||||||||
|
|
|
|
|
|
|
|
|
|
|
||||||||||||||||||||||||||||
2 |
|
x |
y |
y |
z |
z |
x |
xy |
yz |
zx |
||||||||||||||||||||||||||||
|
|
|
|
|
|
|
|
|
|
|
|
|
|
|
|
|
|
|
|
|
|
|
|
В поршневых двигателях коэффициенты запаса прочности крепежных деталей, нагруженных постоянными усилиями затяжки, где кроме растягивающих напряжений существуют касательные напряжения от момента затяжки, следует рассчитывать по максимальному эквивалентному напряжению или максимальной интенсивности напряжений imax. Для деталей, работающих при высокой температуре, принимают предел длительной прочности дл.
n |
|
дл |
. |
|
|
||||
дл |
|
max |
||
|
|
|
22
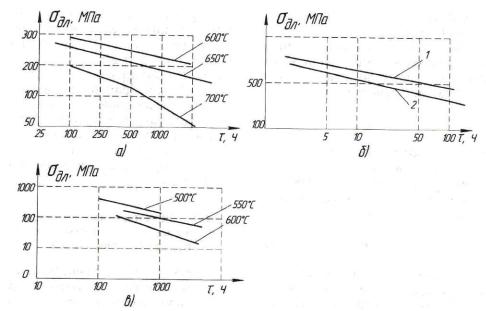
Рис. 2.3. Изменение предела длительной прочности различных материалов в зависимости от времени:
а – стали 45Х14Н14В2М (ЭИ69); б – стали 20Х3МВФ (ЭИ415)
при Т = 550 С; в – высокопрочный чугун; 1 – гладкие образцы; 2 – образцы с концентраторами
Зависимость дл удовлетворительно описывается степенной зави-
симостью |
А длm , |
(2.14) |
где А и m параметры материала, зависящие от температуры и характеристик разрушения. В логарифмических координатах эта зависимость имеет вид ломаной линии (рис. 2.3).
Кроме nдл определяют коэффициент запаса по долговечности
n |
раз |
, |
(2.15) |
|
где раз – время до разрушения; – заявленный ресурс двигателя; nдл – рекомендуется выбирать не менее 1,5.
Большинство деталей ДВС работают при переменных нагрузках. При этом детали кривошипно-шатунного механизма и привода клапанов подвергаются механическим нагрузкам, а детали цилиндропоршневой группы, турбокомпрессора, выпускной системы – как механическим, так и переменным тепловым нагрузкам. В этом случае, при высоких температурах форсирования ДВС, в деталях возникают деформации ползучести и релаксации температурных напряжений и происходит накопление остаточных напряжений, особенно в крышках цилиндров и поршнях, что может явиться причиной их разрушения.
23
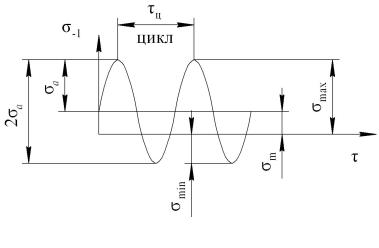
Многоцикловая усталость и оценка выносливости деталей поршневых двигателей
Доля усталостных поломок деталей ДВС достигает 20 %. Поэтому для деталей криво- шипно-шатунного механизма, механизма газораспределения, элементов корпуса двигателя, силовых шпилек и болтов необходим расчет на
Рис. 2.4. Переменные циклические напряжения выносливость. При пе-
ременных напряжениях разрушения возникают при меньших значениях, чем при статических. Обычно они возникают в местах концентрации напряжений по нормали к поверхности трещины. Изменение напряжений за один период называется циклом (рис. 2.4) и характеризуется максимальными ( max,max ), минимальными ( min, min ) и средними ( m, m ) напряжениями, а также амплитудой a, и a.
m = 0,5( max + min ), min = 0,5 ( max+ min), |
(2.16) |
a = 0,5( max - min ), a = 0,5 ( max - min). |
(2.17) |
Кроме того, вводится коэффициент асимметрии цикла r = ( max/min). Различают симметричный цикл при r = -1, m = 0, пульсирующий min = 0, m = a = 0,5 max; при r<0 цикл знакопеременный.
Предел выносливости -1 определяют экспериментально на гладких цилиндрических образцах на базе числа циклов нагружения N = =(1…2)107 для сталей, N = (0,1…1)108 для легких сплавов. Для сталей с в (400…1500) МПа -1 (0,45…0,5) в при изгибе, или более точно -1 (0,55-0,0001 в) в, для стального литья и чугуна -1 0,45 в, для цветных металлов -1 (0,25…0,5) в, для касательных напряжений -1 0,6 -1. Обычно полученные экспериментально значения предельных напряжений и амплитуд схематизируют. На рис. 2.5 приведена диаграмма предельных напряжений.
Кроме этого, учитываются коэффициенты асимметрии цикла
|
|
2 1 0 |
; |
|
|
2 1 0 |
, |
(2.18) |
|
||||||||
|
|
|||||||
|
|
0 |
|
|
0 |
|
||
|
24 |
|
|
|
|
|
|
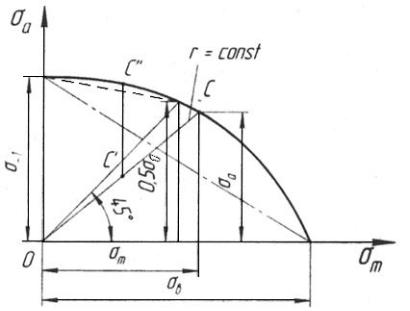
(табл. 2.2) коэффициенты концентрации напряжений k , k , коэффициенты масштабного фактора и поверхностной обработки м,п. Значения коэффициентов и физи- ко-механические свойства материалов берут из табл.
П.1 – П.8.
Рис. 2.5. Диаграмма предельных амплитуд напряжений
Таблица 2.2
Коэффициент чувствительности к асимметрии цикла
|
Коэффициент чувствитель- |
|
|
|
|
в, МПа |
|
|
|
|
|
|
|
ности к асимметрии цикла |
150-520 |
520-720 |
720-1000 |
1000-1200 |
1200-1400 |
||||||
|
|
|
0 |
0,05 |
|
0,10 |
0,20 |
|
0,25 |
|
||
|
|
|
0 |
0 |
|
0,05 |
0,10 |
|
0,15 |
|
||
|
|
|
|
|
|
|
|
|
|
Таблица 2.3 |
||
|
Коэффициенты запасов прочности для типовых деталей ДВС |
|||||||||||
|
|
|
|
|
|
Диапазон [n] |
|
Диапазон [n] |
|
|||
|
Деталь |
Материал детали |
|
|
для инженерных |
|
||||||
|
|
|
|
|
|
для МКЭ |
|
методик |
|
|||
|
|
|
|
|
|
|
|
|
|
|||
|
Блок-картер |
Сталь 20, 20Л |
|
|
1,8...2,2 |
|
|
3,5…5 |
|
|||
|
|
Чугун ЧШГ |
|
|
1,9…2,2 |
|
|
4…5 |
|
|||
|
Коленчатый вал |
Сталь (кованая) |
|
|
1,6…1,9 |
|
|
3,5…5 |
|
|||
|
|
Чугун (ЧШГ) |
|
|
1,7…2,0 |
|
|
3,5…4 |
|
|||
|
Поршень (голов- |
Сталь |
|
|
1,5…1,9 |
|
|
3…4 |
|
|||
|
ка) |
Чугун |
|
|
1,6…2,0 |
|
|
3,5…4 |
|
|||
|
Поршень (тронк) |
Алюмин. сплав (АК) |
|
1,4…1,7 |
|
|
3…3,5 |
|
||||
|
Поршневой палец |
Сталь (ГОСТ 4543-71) |
|
1,6…2,0 |
|
|
3,5…4 |
|
||||
|
Шатуны |
Сталь (ГОСТ 4343-71) |
|
1,6…2,0 |
|
|
3,5…4 |
|
||||
|
Втулка цилиндра |
Чугун (ХНМ) |
|
|
1,5…1,8 |
|
|
3…4 |
|
|||
|
Головка цилиндра |
Чугун (ЧШГ) |
|
|
1,4…1,6 |
|
|
3…3,5 |
|
Все эти сведения нужны при расчетах напряжений по инженерным методикам. При квалифицированных расчетах МКЭ автоматически учитываются и масштабный фактор, и концентрация напряжений,
25
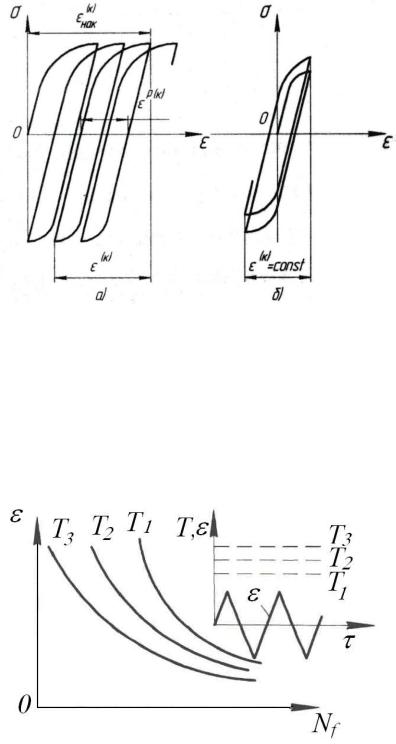
и поверхностная обработка, и особенности нагружения в эксплуатации, поэтому коэффициенты запаса n для типовых деталей ДВС берут из табл. 2.3.
Детали форсированных двигателей работают в условиях переменных по длительности циклов нагружения с выдержками при максимальной температуре, что приводит к резкому уменьшению числа циклов до разрушения. Могут возникать неизотермически мягкое (рис. 2.6, а) и не-
изотермически жесткое (рис. 2.6, б) нагружения. При высоких циклических температурах появляется малоцикловая усталость (рис. 2.7), которая резко снижает долговечность вследствие возникающих процессов ползучести в материале.
В этих случаях необходимо решать упругопластические задачи. На практике эти задачи решаются двумя методами – с применением метода переменных параметров упругости или с использованием теории ползучести.
В случае многоосного напряженного состояния обычно ис-
пользуют энергетические условия начала пластической деформации Максвела – Хубера i= т, по которому пластическая деформация возникает при интенсивности напряжений i, достигающей предела
26
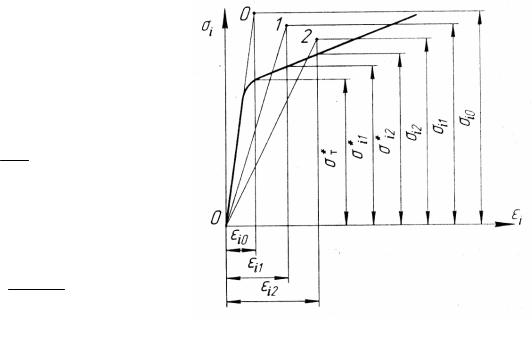
текучести при растяжении т. Здесь по теории малых упругопластических деформаций изменение деформаций от напряжения рассматривается в виде обобщенного закона Гука:
|
' |
|
|
|
1 |
|
|
|
|
|
|
' |
|
|
|
|
|
|
T, |
|
|
||||||||||
|
|
|
|
|
|
|
|
|
|
|
|
|
|
||||||||||||||||||
|
|
|
|
|
|
|
|
|
|
|
z |
|
|
||||||||||||||||||
|
|
x |
|
|
|
|
E' |
|
x |
|
|
|
|
|
y |
|
|
|
|
т |
|
||||||||||
|
' |
|
|
|
|
1 |
|
|
|
|
|
|
|
|
|
|
|
|
|
|
|
|
|
|
|
|
|
||||
|
|
|
|
|
|
|
|
|
|
|
|
|
|
|
|
|
|
|
|
|
|
|
|
||||||||
|
y |
|
|
|
|
|
|
|
|
|
y |
' |
|
x |
|
|
z |
|
|
T, |
|
|
|||||||||
|
|
|
|
|
|
|
|
|
|||||||||||||||||||||||
|
|
|
|
E |
|
|
|
|
|
|
|
|
|
|
|
т |
|
|
|||||||||||||
|
|
|
|
|
|
' |
|
|
|
|
|
|
|
|
|
|
|
|
|
|
|
|
|
(2.19) |
|||||||
|
|
|
|
|
|
|
1 |
|
|
|
|
|
' x |
y |
|
|
|
|
|
||||||||||||
|
z' |
|
|
|
z |
тT, |
|
||||||||||||||||||||||||
|
|
|
|
|
|||||||||||||||||||||||||||
|
|
|
|
|
|
|
E' |
|
|
|
|
|
|
|
|
|
|
|
|
|
|
|
|
|
|
|
|||||
|
|
|
|
|
|
|
|
|
|
xy |
|
|
|
|
|
yz |
|
|
|
|
|
|
zx |
|
|
|
|||||
|
|
|
xy |
|
|
; |
yz |
|
; |
zx |
|
|
, |
|
|
||||||||||||||||
|
|
|
|
|
|
|
|
||||||||||||||||||||||||
|
|
|
|
|
|
|
|
|
|
G' |
|
|
|
|
G' |
|
|
|
|
|
G' |
|
|
где Е,G – модули упругости материала первого и второго рода; , т – соответственно коэффициент Пуансона и коэффициент линейного расширения; Т – изменение температуры в рассматриваемой точке детали. Принимается, что параметры упругости E , G , являются переменными для каждой точки тела и определяются следующими зависимостями:
E' |
i / i |
; G' |
i |
; ' |
1/2 a |
, где a |
1 2 i |
. |
(2.20) |
|
|||||||||
|
1 a |
3 i |
|
1 a |
|
3E i |
|
На рис. 2.8 схематично показан процесс последовательных приближений при решении упругопластической задачи. Вначале по фор-
мулам (2.12) и (2.13) вычис-
ляются интенсивности деформаций i0 и напряженийi0. В первом приближении величина точки 01 заменяется на
3G* i0 ( i0 т), при
i0
этом интенсивность напряжений равна * 3G* i0;
E= 3G*;
* 0,5 a, 1 a
а *= т материала.
Рис. 2.8. Схема расчета по методу переменных параметров упругости
27
Ползучесть
Основные детали двигателя, в том числе детали цилиндропоршневой группы, работают при повышенных температурах. При этом в конструктивных материалах проявляются свойства ползучести и длительной прочности.
Под ползучестью понимают пластическую остаточную деформацию детали в зависимости от рабочей температуры, действующих нагрузок и времени. При этом в связи с протекающими остаточными деформациями в детали уменьшаются усилия, которые вызвали деформацию, и дальнейшая деформация при данной температуре прекращается. Это явление называется релаксацией напряжений. Оба процесса обычно происходят одновременно. На рис. 2.9 показаны деформации ползучести сплава АК4-Т, который часто применяется для поршней, для различных случаев приложения нагрузок.
Вкривой ползучести можно выделить три участка (рис. 2.9, а – участок упругого деформирования не учитывается): I – участок, где скорости деформирования за счет упрочнения уменьшаются до скорости, которая сохраняется на протяжении второй стадии деформирования (II – участок), на третьем участке (III) скорость ползучести возрастает и заканчивается разрушением, причем при вязком разрушении образуется шейка на образце растяжения, а при хрупком – образуются внутренние трещины. Для вязкоупругих материалов кривая ползучести сохраняет свой вид и при постоянном нагружении, и при пульсирующем, или синусоидальном, переменном во времени нагружении. Исследования О.В. Соснина, Б.В. Горева, А.Ф. Никитенко
[5]показали, что продолжительность процесса ползучести не зависит от чередования и времени приложения к образцу нагрузок и температур, а зависит от общей работы разрушения (или разупрочнения), которая определяется площадью под кривой ползучести (рис. 2.9, а – площадь заштрихована).
Вобщем случае скорость разрушения вязкоупругого материала в процессе ползучести может быть описана уравнением
dA |
|
B эn |
|
|
|
|
|
, |
(2.21) |
dt |
A A* 1 A 1 m |
где A* – энергия разрушения данного материала;э – эквивалентное напряжение
э |
(1 sin3 bsin3 ) i. |
(2.22) |
|
28 |
|
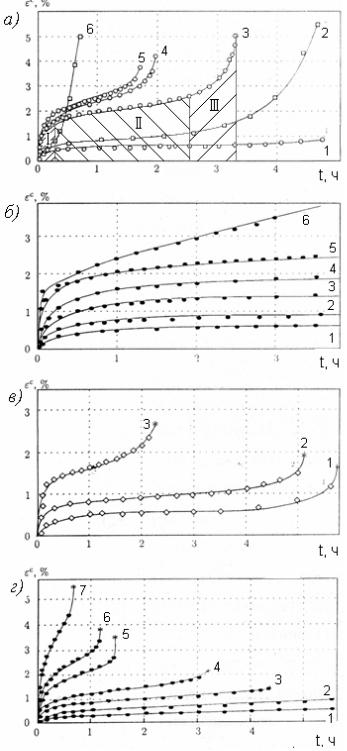
1 = 200 МПа; 0 = 13 % 2 = 250 МПа; 0 = 20 % 3 = 280 МПа; 0 = 8,9 % 4 = 310 МПа; 0 = 9,7 % 5 = 315 МПа; 0 = 7,8 % 6 = 320 МПа; 0 = 7,3 %
1 = 290 МПа
2 = 300 МПа
3 = 310 МПа
4 = 320 МПа
5 = 340 МПа
6 = 345 МПа
1 = 260 МПа
2 = 270 МПа
3 = 290 МПа
1 = 230 МПа; t0 = 11 ч, 0 = 1,3 % 2 = 250 МПа; t0 = 11 ч, 0 = 1,3 %
3 = 260 МПа
4 = 270 МПа
5 = 290 МПа
6 = 300 МПа
7 = 310 МПа
Рис. 2.9. Диаграммы деформирования образцов из сплава АК4-Т на растяжение и сжатие при постоянном напряжении для различных направлений (звездочки – разрушение): а) растяжение в продольном и поперечном направлениях; б) сжатие в поперечном направлении; в) растяжение по нормали; г) растяжение под углом 45 к нормали
29