
2514
.pdfСуммарные напряжения, вызываемые в сечении А – А газовыми и инерционными силами и запрессованной втулкой, изменяются по асимметричному циклу, и минимальным запасом прочности обладает наружное волокно головки.
Запас прочности принимают 2,5...5,0. Снижение напряжений достигают за счет смещения расчетного сечения А-А до ш3 = 90° и увеличения радиуса сопряжения головки со стержнем шатуна.
Лекция 10. Расчет кривошипной головки
Соотношения размеров в кривошипной головке приведены в табл. 10.1.
Приближенный расчет кривошипной головки сводится к определению напряжения изгиба в среднем сечении II-II крышки головки от центробежных сил (МН), имеющих максимальное значение в начале пуска ( =0°) при работе дизеля на режиме максимальной частоты вращения холостого хода.
Pjp= - 2xx maxR[(mп+mшп)(1+ ) + (mшк-mкр)] 10-6,
где mп – масса поршневой группы;
mшп, mшк – соответственно массы шатуна, прилегающего к поршневой головке и к кривошипной; mш = mшп + mшк – масса шатуна, совершающая возвратно-поступательное движение, кг;
mкр (0,20 ... 0,28) mш – масса крышки кривошипной головки, кг. Напряжение изгиба крышки с учетом совместной деформации
вкладыша равно
|
0,023C |
|
0,4 |
|
, МПа, |
(10.1) |
||
кг Рjp |
|
|
|
|
|
|
||
(1 J |
п |
/J)W |
F |
|||||
|
|
из |
|
г |
|
|
|
где С – расстояние между шатунными болтами, м (рис. 8.1),
JB tB3 м4; ( – длина крышки, tB – толщина стенки вкладыша, м); J= а[(0,5(C – d1)]3 – момент инерции расчетного сечения II-II, м4; Wиз = а [(0,5(C – d1)]2/6 – момент сопротивления сечения II-II крышки без учета ребер жесткости, м3;
r1=0,5 (dшш+2tв) – внутренний радиус кривошипной головки, м; dшш – диаметр шатунной шейки, м; tв – толщина вкладыша, м. FВ= а 0,5(C - dшш) – суммарная площадь крышки и вкладыша в расчетном сечении, м2.
[ ] = 100…300 МПа.
Конструктивно вкладыши выполняют биметаллическими, имеющими стальную основу и антифрикционный слой. Общая величина
60
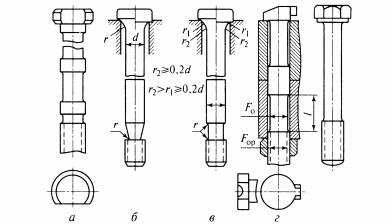
вкладышей = 1,3...2,0 мм для ДсИЗ, с антифрикционным слоем 0,2...0,4 мм, а для дизелей = 2,5...3,0, с антифрикционным слоем 0,3...0,7 мм. Применяют сплав СОС-6-6 (по 5...6 % олова и сурьмы, 88...90 % свинца) для ДсИЗ, алюминиевый сплав АО20-1 (20 % олова, по 1% меди и никеля и 78 % алюминия). Вкладыши дизелей выполняют из свинцовистой бронзы БрС-30 (30 % свинца, 70 % меди), она плохо прирабатывается, подвержена коррозии, в связи с этим в моторное масло вводят присадки, а поверхность покрывают тонкой пленкой сплава свинца с оловом, свинца с индием или свинца с кадмием, толщиной 0,015...0,04 мм. Для тракторных двигателей применяют сплав АО 20-1 для верхнего вкладыша и АСМ для нижнего (алюминиевый сплав 0,7 % меди, 6 % сурьмы, 93,3 % алюминия).
Расчет шатунных болтов
На болты действует та же сила инерции РJP, что и на крышку кривошипной головки. На каждый болт действует сила
PJP' PJP /iб,
где iб – число болтов и дополнительно сила затяжки болтов при монтаже Pз.
С учетом податливости элементов стыка головки возникают дополни-
Рис. 10.1. Конструкции шатунных болтов: а) с головкой несимметричной формы с вертикальным срезом; б) с уменьшенными опорными поверхностями головок; в) со сферическими поверхностями контакта головки болта и его посадочного места в шатуне;
г) с установочным элементом
тельная циклическая нагрузка на болт P' |
, |
|
Кш |
|
, (10.2) |
|
|
||||
JP |
|
|
Кш |
Кб |
|
|
|
|
где – коэффициент податливости соединения, Кш и Кб – податливость (деформация сжатия) соответственно болта и крышки головки. Обычно принимают = 0,15...0,25.
Сила предварительной затяжки находится из условия нераскрытия стыка между крышкой головки и кривошипной головкой шатуна:
Pз m(1 )PJP' ; m – коэффициент запаса; m = 2...2,5.
61
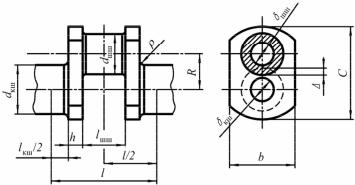
Максимальная и минимальная силы, нагружающие болт, равны:
P |
|
P |
P' |
; |
(10.3) |
max |
3 |
JP |
|
|
|
P |
P m(1 )P' . |
(10.4) |
|||
min |
|
3 |
|
JP |
|
Напряжения в болте
max = Pmax/Fпр; |
min = Pmin/Fпр, |
(10.5) |
где Fпр – площадь минимального сечения болта по резьбе.
Расчет на прочность резьбы ведется с определением запаса прочности по переменным напряжениям, с учетом концентрации напряжений в резьбе:
К / = 5...5,5; [n]=2. (10.6)
Для повышения усталостной прочности зоны перехода от головки к стержню резьбы выполняются в виде галтелей с возможно большим радиусом 0,15...0,5d, поверхность шлифуется или полируется, а резьба выполняется с мелким шагом. Наиболее часто стержень болта имеет участок с повышенной податливостью (уменьшением диаметра) и призонный поясок для фиксации крышки относительно шатуна.
Болты изготавливаются из хромистых и хромоникельмолибденовых сталей 30Х, 40Х, 45Х, 40ХНМА штамповкой на автоматах с последующей накаткой резьбы и термической обработкой (закалка и отпуск).
Лекция 11. Коленчатые валы
Коленчатые валы ДВС преобразуют возвратно-поступательное движение поршня во вращение с определенной круговой частотой и крутящим моментом. При этом они подвергаются деформации изгиба и кручения, а также изгибным и крутильным колебаниям нагрузки. Поэтому они рассчитываются на усталость.
Рис. 11.1. Размеры элементов коленчатого вала
62
Для коленвалов ДсИЗ широко используют серые и ковкие чугуны, при этом снижаются припуски на обработку, экономится металл, снижается стоимость. Для дизелей применяют стали
45, 45Х, 40ХФА, 42ХМФА, 18Х2Н4ВА, так как предел усталости чугуна значительноменьше, чем стали.
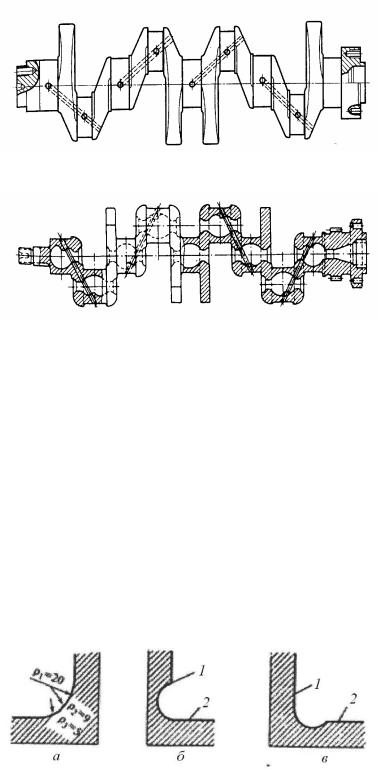
На рис. 11.1 приве- |
|
|
||||
дены буквенные обозна- |
|
|
||||
чения |
характерных раз- |
|
|
|||
меров коленвалов, а в |
|
|
||||
табл. |
7.1 |
соотношения |
|
|
||
этих размеров к диамет- |
|
|
||||
ру D поршня. На рис. |
|
|
||||
11.2 |
показан |
стальной |
|
Рис. 11.2. Стальной коленчатый вал |
|
|
коленвал |
четырехци- |
|
|
|
||
|
|
|
||||
линдрового |
|
четырех- |
|
|
||
тактного двигателя, а на |
|
|
||||
рис. 11.3 – чугунный ли- |
|
|
||||
той вал. Обычно колен- |
|
|
||||
валы |
устанавливают на |
|
|
|||
подшипниках |
скольже- |
Рис. 11.3. Чугунный вал |
||||
ния. При этом уменьша- |
|
|
||||
|
|
|||||
ется вес и габариты ДВС. |
|
|
Кривошипный вал состоит из нескольких кривошипов (по числу поршней) и двух хвостовиков, на одном из которых крепится маховик, а на другом звездочка или шкив привода распределительных валов клапанного механизма. Количество коренных шеек равно i+1, где i – число кривошипов или поршней. Это обеспечивает большую жесткость валу. У двигателей КамАЗ и ЯМЗ с двумя совмещенными шатунами на поршневой шейке всего пять коренных, но восемь поршневых шеек. Особое значение имеет несоосность коренных опор, при эксцентриситете 0,1...0,15 мм запас прочности вала уменьшается на 30...50 %. Исследования НАТИ показали, что при неравномерности износа подшипников 0,05...0,06 мм возникает опасность поломки ко-
ленвала. |
|
|
|
У |
современных |
|
|
ДВС коренные и шатун- |
|
||
ные шейки делают по- |
|
||
лыми с увеличением по- |
|
||
садочного диаметра, что |
Рис. 11.4. Формы галтелей: |
||
приводит к перекрытию |
|||
а – многорадиусная; б – с поднутрением в ще- |
|||
шеек. Это повышает из- |
|||
гибную прочность вала и |
ку; в – с поднутрением в шейку; 1 – щека; 2 – |
||
снижает вес. |
шейка |
||
|
|||
|
|
63 |
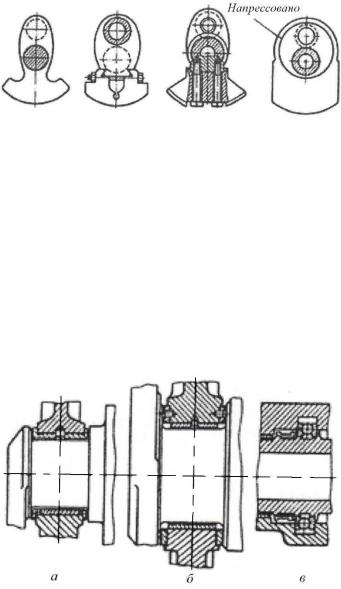
Рис. 11.5. Формы щек и противовесов коленчатого вала
Полости шатунных шеек используют для подачи масла к подшипникам и для улавливания металлических продуктов износа в масле.
Переходы от щек к шейкам выполняются плавными радиусами 0,05...0,07 dш.
Иногда их делают двумя ра-
диусами или с поднутрением (рис. 11.4).
Для снижения динамических нагрузок большое значение имеет выбор расположения кривошипов и их относительного смещения в плоскостях вращения, а также выбор количества, размеров и размещения противовесов (рис. 11.5).
У ЯМЗ – КАЗ 642 это V – образный 6-цилиндровый двигатель, шатунные шейки смещены на 30°.
|
Осевая |
фиксация |
ко- |
|||
|
ленвала относительно |
кар- |
||||
|
тера |
обеспечивается |
упор- |
|||
|
ными |
кольцами, |
бортами |
|||
|
вкладышей |
или |
упорным |
|||
|
подшипником (рис. 11.6). |
|||||
|
Упорные кольца изготавли- |
|||||
|
вают из бронзы, стали или |
|||||
|
металлокерамики. Стальные |
|||||
|
кольца и борты вкладышей |
|||||
|
покрывают |
антифрикцион- |
||||
Рис. 11.6. Упорные подшипники коленчато- |
ными сплавами и от прово- |
|||||
го вала: а – вкладыши с буртиками; б – |
рачивания |
удерживают |
||||
упорные кольца; в – упорный подшипник |
штифтами, |
осевые |
зазоры |
|||
|
0,05...0,15 мм. |
|
|
|
Масло в подшипники подводится к коренным шейкам от главной магистрали в малонагруженную зону и затем через отверстия в щеках к шатунной шейке или через стержень шатуна.
Расчет коленчатого вала на прочность
Коленчатый вал является сложной многоопорной статически неопределимой конструкцией, нагруженной пространственной системой переменных сил.
64
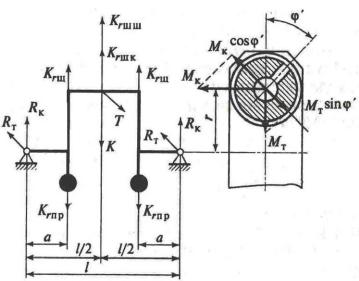
Рассмотрим вначале разрезную схему, для которой вырезается
кривошип по серединам |
|
|
|
|
||
коренных шеек и рас- |
|
|
|
|
||
сматривается |
как двух- |
|
|
|
|
|
опорная балка. |
|
|
|
|
||
Р.С. Кинасошвили |
|
|
|
|
||
установил, что при рас- |
|
|
|
|
||
чете вала на |
прочность |
|
|
|
|
|
не имеет существенного |
|
|
|
|
||
значения результат, по- |
|
|
|
|
||
лученный по |
разрезной |
|
|
|
|
|
схеме и по неразрезной. |
|
|
|
|
||
Необходимый |
расчет- |
|
|
|
|
|
ный запас прочности ко- |
|
|
|
|
||
ренных шеек получается |
|
|
|
|
||
практически |
одинако- |
|
Рис. 11.7. Расчетная схема кривошипа |
|||
вым, а для шатунных |
|
|
|
|
||
шеек на 5...10 % мень- |
|
|
|
|
||
ше, чем при разрезной схеме. |
|
Таблица 11.1 |
||||
|
|
|
|
|
|
|
Соотношение размеров коленчатого вала к диаметру D поршня (рис.11.1) |
||||||
|
|
|
|
|
|
|
Размеры |
|
|
|
Двигатель |
|
|
|
с искровым зажиганием |
Дизель |
||||
|
|
линейный |
|
V - образный |
линейный |
V – образный |
dк.ш/D |
|
0,65…0,80 |
|
0,63…075 |
0,72…0,90 |
0,70…0,75 |
dш.ш/D |
|
0,60…0,70 |
|
0,57…0,66 |
0,64…0,75 |
0,65…0,72 |
lк.ш/ dк.ш* |
|
0,5…0,60 |
|
0,40…0,70 |
0,45…0,60 |
0,40…0,55 |
|
0,74…0,84 |
|
0,70…0,88 |
0,77…0,85 |
0,65…0,86 |
|
|
|
|
||||
lш.ш/ dш.ш |
|
0,45…0,65 |
|
0,80…1,00 |
0,50…0,65 |
0,80…1,00 |
b/D |
|
1,00…1,25 |
1,05…1,30 |
|||
h/D |
|
0,20…0,22 |
0,24…0,27 |
|||
/ dш.ш |
|
|
– |
0,30…0,40 |
||
p/h |
|
0,15…0,20 |
0,15…0,23 |
|||
ш.ш/ dш.ш |
|
|
– |
0…0,5 |
Однако учесть все концентраторы напряжений, местное изменение характеристик материала -1, -1, т и т и др. в зависимости от технологических методов упрочнения, несоосность опор и коренных шеек, неравномерность износа и деформаций опор невозможно. Поэтому рассмотрим расчет по разрезной схеме. Размеры элементов коленвала можно принимать из соотношений табл. 11.1 по диаметру
65
поршня или по размерам вала двигателя прототипа.
Расчет коренных шеек
Коренные шейки нагружаются главным образом крутящим моментом из-за малой их длины, поэтому оцениваются по касательным напряжениям. Итак:
Первый шаг. По данным динамического расчета составляют таблицу или строят графики набегающих моментов кручения вала и выбирают наибольшую амплитуду.
Второй шаг. Определяют максимальное и минимальное значение касательных напряжений (МПа) при моменте сопротивления W(м2):
|
max |
|
Mкрmax |
; |
min |
|
Mкрmin |
, |
|
(11.1) |
|||||||||
|
|
W |
|
|
|
|
|
W |
|
|
|
|
|||||||
|
|
|
|
|
кш |
|
|
|
|
|
|
|
кш |
|
|||||
|
|
|
|
|
|
|
|
|
|
|
|
4 |
|
|
|||||
где |
|
W |
|
d |
3 |
1 |
|
кш |
|
. |
|
||||||||
|
|
|
|||||||||||||||||
|
|
|
кш |
16 |
|
|
кш |
|
dкш |
|
|
||||||||
|
|
|
|
|
|
|
|
|
|
|
|
|
|
|
|
|
|
||
Третий шаг. Определяют амплитудное и среднее напряжения |
|||||||||||||||||||
цикла нагружения (МПа). |
|
|
|
|
|
|
|
|
|
|
|
|
|||||||
а |
max min |
; |
m |
max min |
. |
(11.2) |
|||||||||||||
|
|
||||||||||||||||||
|
|
|
|
2 |
|
|
|
|
|
|
|
2 |
|
|
|
|
Четвертый шаг. Определяют запас прочности nт. Для этого найдем отношение эффективного коэффициента концентрации напряжений К к произведению масштабного м и технологического факторов К = =к / м.
Затем находят запас прочности Т:
п |
|
|
|
|
|
1 |
. |
(11.3) |
K |
|
а Т |
||||||
|
|
|
|
|
|
|
|
|
|
|
|
м |
|
|
|
|
|
|
|
|
|
п |
|
|
-1 берут из табл. П.5, K – из табл.П.2, П.7, м п – из табл. 2.3 и табл. 2.1, – из табл. 2.2.
Полученные по (11.3) значения сравниваются с минимальными допускаемыми значениями, принятыми в машиностроении. Необходимо, чтобы Т Т .
Для расчетов Р.С. Кинасошвили рекомендует принимать К = 2,5. По опыту эксплуатации принимают: для автомобильных двига-
телей [nт] =3...4, тракторных [nт] = 4...5.
66

Лекция 12. Расчет шатунных шеек
На шатунные шейки действуют в основном переменные изгибающие моменты и небольшие крутящие от трения в подшипнике шатуна.
Запасы прочности по касательным напряжениям определяются в местах галтелей у щек, работающих на срез от набегающих крутящих моментов.
Изгибающие моменты возникают от шатуна, центробежных сил щек и противовесов и набегающих крутящих моментов.
От этих сил создаются изгибающие моменты в плоскости кривошипа Мк и в перпендикулярной плоскости Мт (т.е. в плоскости вращения). Расчеты выполняются по табл. 12.1 с учетом табл. 12.2.
|
|
|
К |
К |
|
К |
|
|
L |
|
|
Т |
L |
|
|
|||
M |
|
|
|
|
|
шш |
|
шк |
|
|
( Кщ |
Кпр )а; |
Мт |
|
|
|
. |
(12.1) |
2 |
|
|
2 |
|
2 |
2 |
2 |
|||||||||||
|
|
|
|
|
|
|
|
|
|
|
|
|
|
Для этой же шатунной шейки и для тех же углов поворота вала находим значения К (силы давления на кривошип, МН) и затем по урав-
нению (12.1) вычисляем изгибающий момент Мк (Н м), где
(Кшш+Кшк)=(mшш+ mшк) 2R 10-6; (12.2) Кщ = mщ 2(R/2) 10-6;
Кпр = mпр ) 2Z 10-6;
Z – расстояние до центра тяжести противовеса. Суммарный изгибающий момент (Н м) равен
М |
МТ2 МХ2 . |
(12.3) |
Плоскость его действия и значения при вращении вала будут меняться.
Крутящие моменты МТ по углу мы уже подсчитали в табл. 12.1, там же рассчитана сила К, действующая на кривошип. На коленвал действуют центробежные силы, которые зависят только от массы детали, частоты вращения и радиуса от оси вращения до центра массы детали и не зависят от угла поворота кривошипа. Поэтому, вычислив их один раз, можно подсчитать суммарные изгибающие моменты по углу поворота кривошипа и найти максимальный, одинаковый для всех цилиндров. Так как максимальная концентрация напряжений шейки имеет место у маслоподводящего отверстия, то усталостное разрушение шатунной шейки наиболее вероятно в этом сечении, по которому проводят расчет.
67

1
Таблица 12.1
Расчет изгибающих и крутящих моментов в коленвале
0 |
30 |
60 |
90 |
120 |
150 |
180 |
210 |
240 |
270 |
300 |
330 |
360 |
390 |
420 |
450 |
480 |
510 |
540 |
570 |
600 |
630 |
660 |
690 |
720 |
|
|
|
|
|
|
|
|
|
|
|
|
|
|
|
|
|
|
|
|
|
|
|
|
|
2 |
Рr, МПа |
Рr - Рост |
|
|
|
|
|
|
|
|
|
|
|
|
|
|
|
|
|
|
|
|
|
|
|||||||
3 |
cos + |
1,2800 |
1,0060 |
0,3600 |
|
0,2800 |
0,6400 |
0,7260 |
0,7200 |
0,7260 |
0,6400 |
0,2800 |
0,3600 |
1,0060 |
1,2800 |
1,0060 |
0,3600 |
0,2800 |
0,6400 |
0,7260 |
0,7200 |
0,7260 |
0,6400 |
0,2800 |
0,3600 |
1,0060 |
1,2800 |
||||
|
+ cos 2 |
|
|
|
|
|
|
|
|
|
|
|
|
|
|
|
|
|
|
|
|
|
|
|
|
|
|
|
|||
|
|
|
|
|
|
|
|
|
|
|
|
|
|
|
|
|
|
|
|
|
|
|
|
|
|
|
|
|
|
|
|
4 |
Pj, МПа |
Pj = (-m R 2/Fn)x (3) |
|
|
|
|
|
|
|
|
|
|
|
|
|
|
|
|
|
||||||||||||
5 |
Р , МПа |
P = (2) + (4) |
|
|
|
|
|
|
|
|
|
|
|
|
|
|
|
|
|
|
|
|
|||||||||
6 |
tg |
0,000 |
+0,144 |
+0,253 |
|
+0,295 |
+0,253 |
+0,144 |
0,000 |
0,144- |
0,253- |
0,295- |
0,253- |
|
0,144- |
0,000 |
+0,144 |
+0,253 |
+0,295 |
+0,253 |
+0,144 |
0,000 |
0,144- |
0,253- |
0,295- |
0,253- |
0,144- |
0,000 |
|||
|
|
|
|
|
|
|
|
|
|
|
|
|
|
|
|
|
|
|
|
|
|
|
|
|
|
|
|||||
|
|
|
|
|
|
|
|
|
|
|
|
|
|
|
|
|
|
|
|
|
|
|
|
|
|
|
|
|
|
|
|
7 |
Nr, МПа |
Nr = |
(5) (6) |
|
|
|
|
|
|
|
|
|
|
|
|
|
|
|
|
|
|
|
|
||||||||
8 |
1/ cos |
1,000 |
1,010 |
1,031 |
|
1,043 |
1,031 |
1,010 |
1,000 |
1,010 |
1,031 |
1,043 |
1,031 |
|
1,010 |
1,000 |
1,010 |
1,031 |
1,043 |
1,031 |
1,010 |
1,000 |
1,010 |
1,031 |
1,043 |
1,031 |
1,010 |
1,000 |
|||
|
|
|
|
|
|
|
|
|
|
|
|
|
|
|
|
|
|
|
|
|
|
|
|
|
|
|
|||||
|
|
|
|
|
|
|
|
|
|
|
|
|
|
|
|
|
|
|
|
|
|
|
|
|
|
|
|
|
|
|
|
9 |
S, МПа |
S = |
(5) (8) |
|
|
|
|
|
|
|
|
|
|
|
|
|
|
|
|
|
|
|
|
|
|||||||
10 |
|
cos ( + ) |
|
+1 |
+0,794 |
+0,281 |
|
0,295- |
0,719- |
0,938- |
1- |
0,938- |
0,719- |
0,295- |
+0,281 |
|
+0,794 |
+1 |
+0,794 |
+0,281 |
0,295- |
0,719- |
0,938- |
1- |
0,938- |
0,719- |
0,295- |
+0,281 |
+0,794 |
+1 |
|
|
|
|
|
|
|
|
|
|
|
|
|
|
|
|
|
|
|
|
|
|
|
|
|
|
|
|
|
||||
|
(cos ) |
|
|
|
|
|
|
|
|
|
|
|
|
|
|
|
|
|
|
|
|
|
|
|
|
|
|
|
|||
|
|
|
|
|
|
|
|
|
|
|
|
|
|
|
|
|
|
|
|
|
|
|
|
|
|
|
|
|
|||
|
|
|
|
|
|
|
|
|
|
|
|
|
|
|
|
|
|
|
|
|
|
|
|
|
|
|
|
|
|||
11 |
K, МПа |
K = |
(5) (10) |
|
|
|
|
|
|
|
|
|
|
|
|
|
|
|
|
|
|
|
|
||||||||
12 |
|
sin( + ) |
|
0 |
+0,625 |
+0,993 |
|
+1 |
+0,740 |
+0,376 |
0 |
0,376- |
0,740- |
1- |
0,993- |
|
0,625- |
0 |
+0,625 |
+0,993 |
+1 |
+0,740 |
+0,376 |
0 |
0,376- |
0,740- |
1- |
0,993- |
0,625- |
0 |
|
|
|
|
|
|
|
|
|
|
|
|
|
|
|
|
|
|
|
|
|
|
|
|
|
|
|
|
|
||||
|
(cos ) |
|
|
|
|
|
|
|
|
|
|
|
|
|
|
|
|
|
|
|
|
|
|
|
|
|
|
|
|||
|
|
|
|
|
|
|
|
|
|
|
|
|
|
|
|
|
|
|
|
|
|
|
|
|
|
|
|
||||
13 |
Т, МПа |
T = |
(5) (12) |
|
|
|
|
|
|
|
|
|
|
|
|
|
|
|
|
|
|
|
|
||||||||
14 |
Мкр, Нм |
Mт кр = |
(13) Fn R |
|
|
|
|
|
|
|
|
|
|
|
|
|
|
|
|
|
|
||||||||||
15 |
Мкр-1р, Нм, |
0 |
223,3- |
127,6- |
|
+97,4 |
+165,2 |
+94,6 |
0 |
94,6- |
165,2- |
103,9- |
+97,0 |
|
+137,8 |
0 |
+176,6 |
+124,8 |
+234,3 |
+229,3 |
+115,3 |
0 |
97,4- |
169,7- |
103,5- |
+121,4 |
+219,6 |
0 |
|||
ра |
|
|
|||||||||||||||||||||||||||||
1-го цилинд- |
|
|
|
|
|
|
|
|
|
|
|
|
|
|
|
|
|
|
|
|
|
|
|
|
|
|
|
||||
16 |
Мкр-2, Нм, |
0 |
94,6- |
165,2- |
|
103,9- |
+97,0 |
+137,8 |
0 |
+176,6 |
+124,8 |
+234,3 |
+229,3 |
|
+115,3 |
0 |
97,4- |
169,7- |
103,5- |
+121,4 |
+219,6 |
0 |
223,3- |
127,6- |
+97,4 |
+165,2 |
+94,6 |
0 |
|||
ра |
|
|
|||||||||||||||||||||||||||||
2-го цилинд- |
|
|
|
|
|
|
|
|
|
|
|
|
|
|
|
|
|
|
|
|
|
|
|
|
|
|
|
||||
17 |
Мкр-3, Нм, |
0 |
+176,6 |
+124,8 |
|
+234,3 |
+229,3 |
+115,3 |
0 |
97,4- |
169,7- |
103,5- |
+121,4 |
|
+219,6 |
0 |
223,3- |
127,6- |
+97,4 |
+165,2 |
+94,6 |
0 |
94,6- |
165,2- |
103,9- |
+97,0 |
+137,8 |
0 |
|||
ра |
|
|
|||||||||||||||||||||||||||||
3-го цилинд- |
|
|
|
|
|
|
|
|
|
|
|
|
|
|
|
|
|
|
|
|
|
|
|
|
|
|
|
||||
18 |
Мкр-4, Нм, |
0 |
97,4- |
169,7- |
|
103,5- |
+121,4 |
+219,6 |
0 |
223,3- |
127,6- |
+97,4 |
+165,2 |
|
+94,6 |
0 |
94,6- |
165,2- |
103,9- |
+97,0 |
+137,8 |
0 |
+176,6 |
+124,8 |
+234,3 |
+229,3 |
+115,3 |
0 |
|||
ра |
|
|
|||||||||||||||||||||||||||||
4-го цилинд- |
|
|
|
|
|
|
|
|
|
|
|
|
|
|
|
|
|
|
|
|
|
|
|
|
|
|
|
||||
19 |
М , Нм |
М = (15)+(16)+(17)+(18) |
|
|
|
|
|
|
|
|
|
|
|
|
|
|
|
68

Примечания:
1.Данная таблица предназначена для расчета крутящих моментов
сучетом воздействия инерционных масс поршневой группы и части шатуна.
2.Обозначения действующих сил приняты по рис. 1.1. R – радиус кри-
вошипа; Fп – площадь днища поршня; n – средняя угловая скорость вра-
30
щения, мин-1; m = mп +0,275 mшп – сумма массы поршневой группы u 0,275 массы шатуна, отнесенной к пальцу.
3. Значения моментов Мкр-1, Мкр-2, Мкр-3, Мкр-4 даны для углов кривошипа вала, приведенных в табл. 12.1.
|
|
|
|
Таблица 12.2 |
|
|
Первый |
Второй |
Третий |
Четвертый |
|
|
0 |
180 |
360 |
540 |
|
|
30 |
210 |
390 |
570 |
|
|
60 |
240 |
420 |
600 |
|
|
90 |
270 |
450 |
630 |
|
|
120 |
300 |
480 |
660 |
|
цилиндра. |
150 |
330 |
510 |
690 |
|
180 |
360 |
540 |
720 |
|
|
|
|
||||
|
210 |
390 |
570 |
30 |
|
|
240 |
420 |
600 |
60 |
|
кривошипа |
270 |
450 |
630 |
90 |
|
390 |
570 |
30 |
210 |
|
|
|
300 |
480 |
660 |
120 |
|
|
330 |
510 |
690 |
150 |
|
|
360 |
540 |
720 |
180 |
|
|
|
|
|
|
|
420 |
600 |
60 |
240 |
|
|
Значения |
|
||||
510 |
690 |
150 |
330 |
|
|
|
450 |
630 |
90 |
270 |
|
|
480 |
660 |
120 |
300 |
|
|
|
|
|
|
|
|
540 |
720 |
180 |
360 |
|
|
570 |
30 |
210 |
390 |
|
|
600 |
60 |
240 |
420 |
|
|
630 |
90 |
270 |
450 |
|
|
660 |
120 |
300 |
480 |
|
|
690 |
150 |
330 |
510 |
|
|
720 |
180 |
360 |
540 |
|
Такты |
Впуск |
Сжатие |
Выпуск |
Рабочий ход |
|
Сжатие |
Рабочий ход |
Впуск |
Выпуск |
|
|
Рабочий ход |
Выпуск |
Сжатие |
Впуск |
|
|
|
Выпуск |
Впуск |
Рабочий ход |
Сжатие |
|
|
|
69 |
|
|
|