
2514
.pdf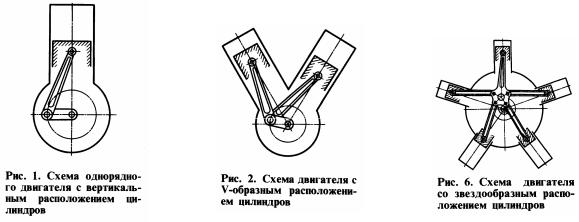
Лекция 5. Основы конструирования двигателей внутреннего сгорания. Конструирование поршней
Рассмотрим процессы создания двигателя для нового легкового автомобиля. Какими перспективными свойствами автомобиль должен обладать? Высокой скоростью и маневренностью или высокими тяго- во-динамическими свойствами. Для повышения скорости необходим двигатель с высокой частотой вращения, а это значит, что масса кри- вошипно-шатунного механизма должна быть небольшой, ход поршня тоже уменьшается, уменьшается и размер кривошипа, а мощность должна оставаться достаточной. Кроме того, для обеспечения маневренности у двигателя должна быть хорошая приемистость, т.е. быстрое увеличение и сброс оборотов. Очевидно, с увеличением оборотов уменьшаются габариты и масса двигателя, увеличивается динамика, что потребует специальных мер по увеличению прочности и уравновешиванию механизма. Так как время каждого такта двигателя будет уменьшаться, то необходимо переходить на четырехклапанные газораспределительные механизмы, повышать скорость газа впускных и выхлопных патрубков. Все это учитывается при составлении технического задания на проектирование нового двигателя.
Рис. 5.1. Схема одно- |
|
Рис. 5.2. Схема |
|
Рис. 5.3. Схема дви- |
рядного двигателя с |
|
двигателя с V- |
|
гателя со звездооб- |
вертикальным распо- |
|
расположением |
|
разным расположе- |
ложением цилиндров |
|
цилиндров |
|
нием цилиндров |
|
|
|
|
|
Остановимся на общих компоновках двигателей внутреннего сгорания. Из всех имеющихся в промышленности компоновок в основном применяются три:
1.Рядные двигатели, когда все цилиндры расположены в ряд вдоль коленчатого вала (двигатели ВАЗ) (рис. 5.1).
2.Двигатели с V-образным расположением цилиндров и с совмещенными двумя шатунами на одной шатунной шейке (двигатели КамАЗ, ЯМЗ) (рис. 5.2).
40
3. Двигатели со звездообразным расположением цилиндров, с одним главным шатуном и остальными прицепными (рис. 5.3). Это авиационные двигатели типа АШ-82Т для самолетов или АШ-82В для вертолетов, а также для подводных лодок.
|
|
Таблица 5.1 |
|
Средние соотношения размеров деталей двигателя к диаметру D |
|||
|
|
|
|
Название параметра |
ДсИЗ |
Дизели |
|
Высота поршня H/D |
0,60...0,80 |
0,80...1,20 |
|
Толщина днища поршня /D |
0,06...0,09 |
0,15...0,22 |
|
Высота жарового пояса hг/D |
0,03...0,08 |
0,06...0,18 |
|
Высота первой кольцевой перемычки hп/D |
0,04...0,05 |
0,05...0,08 |
|
Толщина стенки головки поршня s/D |
0,05...0,10 |
0,05...0,10 |
|
Расстояние до оси пальца h1/D |
0,30...0,50 |
0,50...0,62 |
|
Толщина стенки юбки поршня ю, мм |
1,50...3,00 |
1,50...3,50 |
|
Радиальная толщина кольца t: |
|
|
|
компрессионного tк/D |
0,040...0,045 |
0,040...0,045 |
|
маслосъемного tм/D |
0,038…0,043 |
0,038…0,043 |
|
Высота кольца ак, мм |
1,00...1,75 |
1,75...3,00 |
|
Радиальный зазор кольца в канавке поршня t, мм: |
0,70...0,95 |
0,70...0,95 |
|
компрессионного |
|
||
маслосъемного |
0,9…1,10 |
0,90…1,10 |
|
Разность между величинами зазоров замка кольца |
2,5...4,0 |
3,2...4,0 |
|
в свободном и рабочем состоянии S/t |
|
||
|
|
|
|
Количество масляных отверстий в поршне iмо |
6...12 |
6...12 |
|
Диаметр отверстия масляного канала dм/b |
0,30...0,50 |
0,30...0,50 |
|
Наружный диаметр пальца dп/D |
0,20...0,28 |
0,32...0,40 |
|
Внутренний диаметр пальца dв/dп |
0,65…0,75 |
0,50…0.70 |
|
Длина пальца lп/D |
0,85…0,90 |
0,85…0,90 |
|
Расстояние между торцами бобышек b/D |
0,25…0,40 |
0,25…0,40 |
|
Диаметр бобышки dб/D |
0,30…0,50 |
0,40…0,50 |
|
Длина головки шатуна lш/D |
0,28…0,45 |
0,28…0,32 |
|
При проектировании конструктор учитывает следующие параметры: Сп – скорость поршня; n – частоту вращения вала;
S/D – отношение хода поршня к его диаметру; Pг – среднее эффективное давление;
i – число цилиндров; D –диаметр цилиндров.
С увеличением диаметра поршня повышается эффективный КПД, но повышается нагрузка на кривошипно-шатунный механизм и подшипники. Обычно диаметры поршня не превосходят D=150 мм. Выбрав компоновку двигателя, приступают к проектированию цилиндропоршневой группы.
41
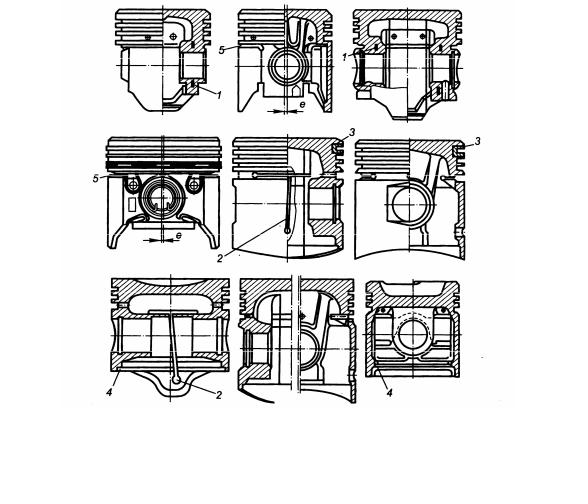
Конструкции поршней
Поршень состоит из головки и юбки. Головка – это верхняя часть поршня. Поверхность, прилегающая к газам, называется днищем. В нем располагается обычно камера сгорания, через него отводится основная доля теплоты сгорания газов. Ниже днища в головке находятся жаровой и уплотнительный пояса. Юбка поршня содержит бобышки, в отверстиях которых размещается палец, и цилиндрическую боковую поверхность для направления движения поршня. В двигателях с искровым зажиганием наиболее распространены поршни с плоским днищем, бывают также выпуклые и вогнутые (рис. 5.4, 6.1). В дизелях плоское днище применяется с раздельными камерами сгорания. С объемным и пристеночным смесеобразованием камера сгорания расположена в головке поршня (рис. 6.1). Конфигурация камеры сгорания согласуется с расположением форсунки, факелом распыленного топлива и вихрями воздуха, определяющими испарение, перемешивание и подготовку рабочей смеси к сгоранию. Особое внимание уделя-
Рис. 5.4. Поршни двигателей с искровым зажиганием:
1 – терморегулирующая вставка; 2 – Т-образная прорезь; 3 – вставка канавки под первое компрессионное кольцо; 4 – зона выборки металла для подгонки по массе; 5 – поперечная прорезь; е – дезаксил
42
ется теплоотводу, причем обеспечивается отвод в охлаждаемую стенку цилиндра через первое компрессионное кольцо 60…70 %, через юбку поршня 20…30 % и в систему смазки через внутреннюю поверхность днища 5…10 %. Среднестатистические соотношения элементов поршня приведены в табл. 5.1 (буквенные обозначения по рис. 6.3).
Примечание. Внутренний диаметр поршня, мм: di=D-2(s+t+ t).
Основные дефекты поршней автотранспортного двигателя:
1.Износ и разрушение поверхности верхней кольцевой канавки.
2.Разрушение и прогар днища поршня. Для устранения дефекта часто поршни делаются составные с днищем из чугуна или из легированной стали.
3.Трещины на днище и обгорание кромок у камеры сгорания.
4.Перегрев канавки верхнего компрессионного кольца с потерей подвижности кольца.
5.Интенсивное отложение нагара (дефект камеры сгорания).
6.Наволакивание металла и задиры на боковой поверхности поршня и поверхности цилиндра.
7.Износ боковой поверхности юбки.
8.Трещины в бобышках.
Поршни изготавливают литьем в кокиль (металлическая форма) или штамповкой из следующих материалов: при литье АЛ 25 ГОСТ 2685-73, при штамповке АК 4 или АК 6 ГОСТ 4784-97, для дизельных двигателей и быстроходных применяют легированные чугуны СЧ 24, СЧ 45, ВЧ 45-5. В составных поршнях для головки поршня применяют легированные стали типа 20Х3МВФ, тогда температура днища может превышать 450 °С.
Лекция 6. Расчеты поршня
Наилучшим методом расчета температурных полей и напряжений служит метод конечных элементов. Существующие программные комплексы Cosmos Works, Cosmos/M, Nastran, Ansys и другие позво-
ляют с высокой точностью определять напряженно-деформируемое состояние поршня от всех видов механических и тепловых нагрузок. Предварительно познакомимся с упрощенными инженерными методами:
1. Определение износостойкости юбки поршня (рис. 6.3). При рабочем ходе поршня возникает боковая сила, которая прижимает юбку поршня к цилиндру. Определим номинальную мощность и найдем
43
максимальную боковую силу Nmax из динамического расчета. Что нужно сделать для этого? Из индикаторной диаграммы найдем величину давления для номинальной мощности и, умножив на площадь днища поршня, найдем силу, приложенную к поршню. Затем разложив эту силу на две составляющие вдоль шатуна и по нормали к цилиндру, получим Nmax. После этого, по приближенной формуле определим величину давления юбки поршня на стенку цилиндра.
q |
|
Nmax |
, |
(6.1) |
|
||||
ц |
|
h D |
|
|
|
|
п п |
|
где Dп – диаметр поршня, hп – высота поршня или длина юбки поршня.
Допустимое давление для поршней двигателей с искровым зажиганием (ДсИЗ) qц 0,5...0,8 МПа. Для поршней дизелей qц 0,7...1,2 МПа.
2. Оценка влияния температурных расширений. Чтобы сохранить подвижность поршня, необходимо обеспечить диаметральный зазор между боковой поверхностью поршня и цилиндра. Вспомним о продольной и диаметральной бочкообразности поверхностей поршня (рис. 6.2). Эта бочкообразность в основном зависит от температурных расширений поршня и на каждом двигателе устанавливается практически на основании целого ряда экспериментов. Для оценки используем приближенную формулу
|
Dц ц tц t0 Dп п tп t0 , |
(6.2) |
где – монтажный зазор между поршнем и цилиндром, мм; |
|
|
ц и п – коэффициенты линейного расширения материала ци- |
||
линдра и поршня, 1/К; |
|
|
tц |
и tп – температуры цилиндра и соответствующего пояса порш- |
|
ня; |
|
|
t0 |
– начальная температура поршня и цилиндра, К. |
|
Зазоры проверяют для верхнего торца головки поршня и для юбки. Относительный диаметральный зазор для данных зон должен обеспечивать следующее отношение: D= 0,002…0,003 для жарового пояса и 0,0005…0,001 для низа юбки.
3. Расчет днища поршня на изгиб под действием газовых сил. Для бензиновых двигателей наибольшее давление газа наступает
на режиме максимального крутящего момента. Для дизелей максимум давления достигается на режиме максимальной мощности.
44
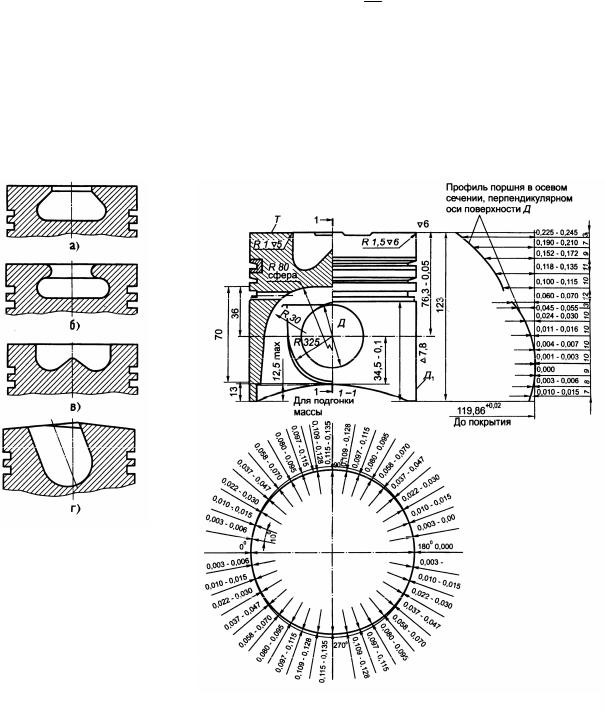
Тогда напряжения изгиба в днище поршня, МПа, равны
|
|
|
|
|
|
из |
|
Mиз |
, |
(6.3) |
||
|
|
|
|
|
|
|||||||
|
|
|
|
|
|
|
W |
|
|
|
||
|
|
|
1 |
|
|
|
|
из |
|
1 |
|
|
где M |
|
|
P |
r2, МН; |
|
W |
|
r 2 , м3; |
||||
|
|
|
|
|||||||||
|
из |
|
3 mах |
|
|
|
|
из |
3 |
Pmах – максимальное давление в камере сгорания;
r – внутренний радиус поршня, м, r D S l l , (рис. 6.3) 2
S – толщина поршня в кольцевой канавке под первое компрессионное кольцо;
l l – глубина кольцевой канавки под первое компрессионное кольцо;
– толщина днища поршня.
Рис. 6.1. Типы камер сгорания в поршнях дизелей: а – ЦНИДИ; б – НАТИ; в – ЯМЗ; г – ДЕЙТЦ
Рис. 6.2. Профиль поршня по его высоте и по окружности
45
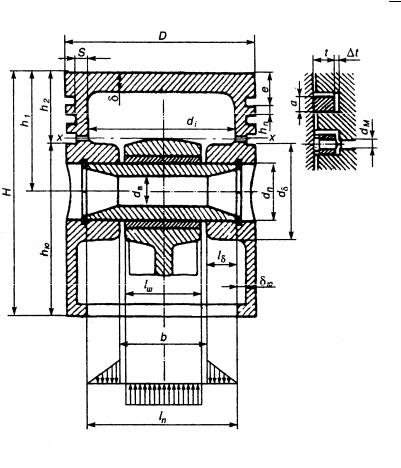
После подстановки имеем:
Рис. 6.3. Схема поршня
2
из Pmах r , МПа. (6.4)
В расчетах поршня действие переменных нагрузок учитывается с помощью допускаемых напряжений. При отсутствии ребер жесткости для поршней из алюминиевых сплавов допускаемые напряжения
20...25 МПа;
для поршней из чугуна
– =40…50 МПа. При
наличии ребер жесткости соответственно для алюминиевых сплавов
=50…150 МПа; для чугуна – =80…200
МПа.
Температурные напряжения из-за разности температур внутренней и наружной поверхности находят только для чугунных поршней
Т Eq / 200 Т , (6.5)
где α –коэффициент линейного расширения,равный 11 10 61/град;
Е – модуль упругости, МПа, E 1...1,2 103;
q– удельная тепловая нагрузка, Вт/м2;
– толщина днища, м;
Т – коэффициент теплопроводности чугуна, Вт/(мК), Т =58. Для четырехтактных двигателей
q 11,63 6000 26n Pi ,
где n – частота вращения, мин-1; Pi – среднее давление, МПа.
Допускаемые напряжения 150...250 МПа.
Для алюминиевых поршней вследствие высокой теплопроводно-
46
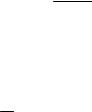
сти металла температурные напряжения не определяют.
4. Расчет поршня на сжатие и на разрыв от инерционных сил. Расчет ведем по сечению X – X (рис. 6.3)по впадине маслосъем-
ного кольца, где сечение ослаблено маслоотводящими отверстиями.
р Pmax ,
Fх х
где Pmах – сила давления, действующего на днище поршня, МН; Fх х – площадь сечения X – X, Pmах PиFп.
Fх х di2 dв2 nотFот ;
4
Fот – площадь диаметрального сечения отверстия для отвода масла; nот – число отверстий;
di – диаметр впадины кольцевой проточки под маслосъемное кольцо; dв – диаметр внутренней стенки поршня;
ал 30...40 МПа; чуг 60...80 МПа; сталь 100...150 МПа.
Расчет напряжений отрыва головки поршня
|
р |
|
Pц |
; |
P m |
x x |
R 2 |
1 , |
(6.6) |
|
|||||||||
|
|
F |
ц |
max |
|
|
|||
|
|
|
х х |
|
|
|
|
|
где mx x – масса головки поршня над сечением Х – Х с кольцами, mx x 0,4...0,6 mп ;
R– радиус кривошипа, м; max |
– максимальная угловая скорость хо- |
|||||
лостого хода двигателя, рад/с; |
R |
; lш – длина шатуна, м. |
|
|||
|
|
|||||
|
|
l |
|
|
|
|
|
|
ш |
|
|
|
|
Допускаемые напряжения |
растяжения: |
ал |
4...10 |
МПа; |
||
|
|
|
|
|
|
чуг 8...20 МПа.
Лекция 7. Расчеты поршневого пальца
Впроцессе работы в пальце возникают напряжения изгиба, среза
иовализации.
Пальцы устанавливают в отверстие поршневой головки шатуна либо с зазором (плавающий палец), либо с натягом (защемленный палец). У плавающего пальца поршня (рис. 7.1) износостойкость втулки верхней головки шатуна выше, чем у бобышек поршня, и обеспечить
47
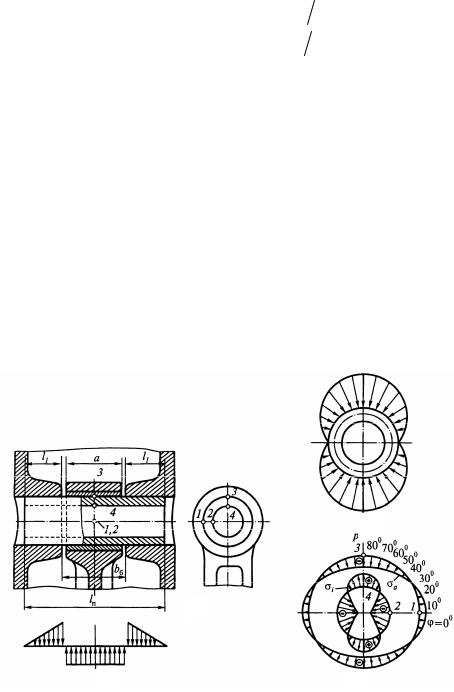
ее смазку легче. Поэтому опорную длину втулки шатуна делают меньше, чем суммарную длину бобышек. Соотношение между dп, lб и a находят из условий равнопрочности.
Износостойкость пальца
Оценивают по удельным давлениям между втулкой шатуна qш и бобышками поршня.
qш Pг Pи dпa, |
|
qб Pг Pи 2dпlб , |
(7.1) |
где Pг сила давления газа, МН;
Pи – сила инерции поршневой группы, действующая на втулку шатуна, МН.
Pи mпR 2 1 ,
где mп – масса поршневой группы (масса поршня с кольцами и верхней части шатуна);
Pи – сила инерции поршневой группы без массы шатуна и без массы
пальца, Pи mпR 2 1 ; |
|
mип– масса пальца, mп mп mип. |
|
Для алюминиевых поршней ДсИЗ mп |
0,7mп , для дизелей |
mп 0,6mп. |
|
в
а
б г
Рис. 7.1. Расчетная схема поршневого пальца: а – основные геометрические соотношения; б – схема нагружения пальца при изгибе;
в– косинусоидальное распределение нагрузки по поверхности пальца;
г– напряжения на внутренней48 и наружной поверхности пальца

– выбирают из условия. Для ДсИЗ nmax ; для дизелей
30
nном .
30
Допустимые нагрузки:
Для ДсИЗ qи =35…40 МПа и qб =30…35 МПа.
Для дизелей qи =45…55 МП и qб =40…45 МПа.
Расчет пальца на изгиб и овализацию
Расчет выполняется как для балки, нагруженной распределенной нагрузкой (рис. 7.1).
и |
Mmax |
|
Pг Pи lб 2b 1,5a |
, |
(7.2) |
W |
1,2dп3 1 4 |
где – отношение внутреннего диаметра пальца к наружному.
lб ,bи a берутся с чертежа (см. рис.7.1), dп –наружный диаметр пальца. Для автотракторных двигателей допускаемые напряжения равны
и 120…160 МПа.
Расчет пальца на срез
|
|
0,85P |
1 2 |
|
|
||
ср |
|
|
|
|
, |
(7.3) |
|
dн2.п |
1 4 |
||||||
|
|
|
|
|
где P Pг Pи .
Допускаемые напряжения – ср 80…120 МПа.
Овализация пальца
Овализация пальца происходит, когда от действия вертикальных сил (рис. 7.1, в) возникает деформация с увеличением диаметра в поперечном сечении. Максимальные приращения диаметра пальца в средней части:
dmax |
0,09P 1 3 |
K , |
(7.4) |
||
E l |
1 3 |
||||
|
|
|
|||
|
п п |
|
|
|
гдеK – коэффициент, полученный из эксперимента,
К=1,5…15( -0,4)3;
Eп – модуль упругости стали пальца, МПа.
49