
2514
.pdf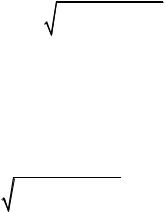
где r – радиус ролика, |
|
|
к |
; |
|
|
|
|
|
|
|
|
|
|
|||
|
|
|
|
|
|
|
|
|
|
|
|||||||
|
|
к |
|
|
|
t |
|
|
|
|
|
|
|
|
|
||
|
|
|
(r |
|
r)(1 cos ) |
|
|
|
|
||||||||
|
|
h |
|
0 |
|
|
|
|
|
|
|
; |
|
|
|
|
|
|
|
|
cos |
|
|
|
|
|
|
|
|
||||||
|
|
т |
|
|
|
|
|
|
|
|
|
|
|
|
|||
|
|
|
|
|
|
|
|
|
|
|
|
|
|
|
|
|
|
|
|
(r r) |
k |
sin |
|
|
(r |
r) |
2 |
(1 sin2 |
) |
|
|||||
V |
|
0 |
|
|
|
|
;J |
|
|
0 |
|
|
к |
|
|
. |
|
|
|
|
|
|
|
|
|
|
cos2 |
|
|||||||
ri |
|
|
2 |
|
|
|
|
ri |
|
|
|
|
|
||||
|
|
cos |
|
|
|
|
|
|
|
|
|
|
|
|
|
||
|
|
|
|
|
|
|
|
|
|
|
|
|
|
|
На участке ВС угол поворота кулачка отсчитывают от обратном направлении, при этом 0 max, где max= ро -
(17.7)
(17.8)
точки С в
max.
|
|
|
|
|
|
|
|
|
|
|
|
|
|
|
|
|
|
|
|
2 |
|
|
|
2 |
|
|
|
|
||||||
|
|
, тогда h |
a cos |
|
|
|
|
1 a1 sin |
|
|
|
(r |
r); |
|||||||||||||||||||||
t |
|
|
|
|
|
|
a1 |
|
|
|
|
|
|
|
||||||||||||||||||||
к |
|
|
T |
|
|
|
|
|
|
|
|
|
|
|
|
|
|
|
|
|
|
|
|
|
|
0 |
|
|||||||
|
|
|
|
|
|
|
|
|
|
|
|
|
|
a |
|
|
|
|
|
|
|
|
|
|
|
|
|
|
|
|
|
|||
|
|
|
|
|
|
a |
|
|
|
|
|
|
|
; |
|
|
|
|
|
|
|
|
|
|
|
|
|
|
|
|||||
|
|
|
|
|
|
|
|
|
|
|
|
|
|
|
|
|
|
|
|
|
|
|
|
|
|
|
|
|
||||||
|
|
|
|
|
|
|
1 |
|
|
|
|
(r r ) |
|
|
|
|
|
|
|
|
|
|
|
|
|
|
|
|||||||
|
|
|
|
|
|
|
|
|
|
|
|
|
|
|
|
2 |
|
|
|
|
|
|
|
|
|
|
|
|
|
|
|
|
|
|
|
|
|
|
|
|
|
|
|
|
|
|
|
|
|
|
a1 sin2 |
|
|
|
|
|
|
|
|
|
|
|
|||||||
|
|
|
|
V a 2 sin |
|
|
|
|
|
|
|
|
|
; |
|
|
|
|
|
(17.9) |
||||||||||||||
|
|
|
|
|
|
|
|
|
|
|
|
|
|
|
|
|
|
|
|
|
|
|
||||||||||||
|
|
|
|
т |
к |
|
|
|
|
|
|
|
1 a2 sin2 |
|
|
|
|
|
|
|
|
|
|
|
||||||||||
|
|
|
|
|
|
|
|
|
|
|
|
|
|
|
|
|
|
1 |
|
|
|
|
|
|
|
|
|
|
|
|
|
|||
|
|
|
|
|
|
|
|
|
|
|
a1 cos |
2 |
|
|
|
|
2 |
sin |
4 |
|
|
|
|
|||||||||||
|
|
j |
т |
a 2 |
cos |
|
|
|
|
a1 |
|
|
|
. |
|
|||||||||||||||||||
|
|
|
|
|
2 |
|
2 |
|
|
|
|
3/2 |
|
|
|
|||||||||||||||||||
|
|
|
к |
|
|
|
|
|
|
|
|
|
|
|
|
sin |
) |
|
|
|
|
|||||||||||||
|
|
|
|
|
|
|
|
|
|
|
|
|
(1 a1 |
|
|
|
|
|
|
|
|
|
При выборе профиля кулачка, образованного дугами окружностей, следует учитывать, что положительное ускорение при вогнутом профиле кулачка выше и он более сложен при изготовлении. Общим недостатком всех трех профилей является наличие скачка ускорений, что вызывает отскок клапана при посадке на седло и усиление колебаний в системе МГР, поэтому они применяются только при nном<2000 мин-1.
Профилирование безударного кулачка Курца
Безударный кулачок Курца обеспечивает в современных быстроходных двигателях непрерывность кривой ускорения хода h толкателя клапана и относительно плавное изменение усилий в звеньях МГР.
На рис. 17.2 приведено построение профиля кулачка Курца с плоским толкателем, а на рис. 17.3 – законы его изменения: высоты подъема (рис. 17.3, а), скорости (рис. 17.3, б) и ускорения (рис. 17.3, в).
Профиль кулачка (см. рис. 17.2) начинают строить с проведения окружности rн, а также окружности с радиусом rк=rн-S, где S суммарный зазор в системе МГР.
100
На этом участке угол поворота Ф0, где происходит выбор теплового зазора МГР по кривой ¼ волны косинусоиды. Затем рабочий угол 0 поворота кулачка и подъема толкателя разделяется на три угла 0=Ф1+Ф2+Ф3: Ф1 – участок положительных ускорений по кривой – ½ синусоиды, Ф2 – начальный участок отрицательных ускорений по кривой ¼ волны синусоиды и Ф3 – основной участок отрицательных ускорений – часть параболы. При этом соотношение между углами: Ф0:Ф1:Ф2:Ф3 0,24:0,2:0,06:0,5 для суммарного угла Ф0+ 0.Участок А0А кулачка строят по ординатам рис. 17.2, а через 1 угла Ф0 или рас-
считывая его по формуле h s |
|
|
|
мм. |
|
1 cos |
|
||||
2 |
|||||
|
|
|
|||
|
|
0 |
|
|
Затем на участках Ф1, Ф2, Ф3 через 1 снимают значения графика hтх и откладывают величины AiBi на соответствующих по углу лучах. В полученных точках проводят перпендикуляры к лучам и получают огибающую профиля кулачка Курца. При этом график на рис. 17.2, а желательно масштабировать, увеличив его размеры в десять раз относительно величины хода толкателя hтх или выполнить расче-
ты по формулам (8.29); (8.30); (8.31) [1, с. 319].
При профилировании данного кулачка исходные параметры:
1.Угол действия кулачка 0.
2.Максимальный подъем клапана hr max.
3.Скорость толкателя в конце участка сбега Vr0k = 0,008…0,022 мм/град).
4.Относительная деятельность участков разгона и замедления:
Ф1= (0,33...0,67)(Ф2 +Ф3); Ф2 = (0,1...0,25) Ф3; (17.10)
0 =2 (Ф1+Ф2 +Ф3) рад.
Кулачки Курца работают с плоским толкателем.
Безударные кулачки с профилем «полидайн»
Чтобы исключить влияние упругих колебаний в приводе МГР, закон подъема клапана задают полиномом, а требуемый для его воcпроизведения закон перемещения толкателя hT, учитывающий наличие упругих колебаний привода, получают путем дифференцирования полинома с учетом податливости элементов МГР и после преобразования имеют
|
|
1 |
|
P |
|
С |
С |
|
|
|
d |
3 |
h |
|
|
|
|
|
|
пр |
пкм |
|
|
2 |
|
|
|
||||
h |
f (h ) |
|
|
0 |
|
|
|
h |
m |
|
|
по |
. |
(17.11) |
|
|
|
|
|
|
|
2 |
|||||||||
T |
т |
|
|
Спк |
|
Спкм |
кпр |
ктк |
|
|
|
|
|
||
|
|
iк |
|
|
|
|
d к |
|
|
101
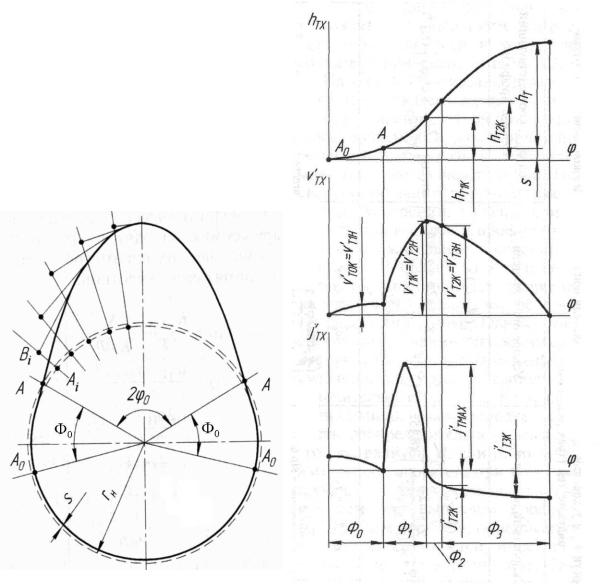
В уравнение входит угловая частота вращения кулачкового валак. Поэтому такие кулачки используются в двигателе с ограниченным диапазоном изменения режимов работы. В уравнение входят силы,
массы, упругие контакты и |
|
|||
ускорения. |
|
|
|
|
Приведенные |
конструкции |
|
||
МГР |
обеспечивали |
работу |
|
|
двигателя с постоянными фазами |
а |
|||
газораспределения |
и |
величины |
|
|
подъема клапана на всех ско- |
|
|||
ростных |
режимах |
работы |
|
|
двигателя. |
|
|
|
б
в
Рис. 17.2. Построение профиля ку- |
Рис. 17.3. Диаграммы пути, скоро- |
сти и ускорения толкателя при ку- |
|
лачка Курца с плоским толкателем |
лачке Курца |
|
|
Современные ДВС, как правило, оснащаются специальными устройствами регулирования фаз газораспределения и подъема клапанов. Регулирование осуществляется командами от электронного блока управления (бортового компьютера) в зависимости от режимов работы двигателя. Применяют либо гидромеханические, либо электромагнитные механизмы.
102
Лекция 18. Система смазки
Система смазки (СС) состоит (рис. 18.1) из маслоприемника, расположенного в поддоне, где находится 2/3 заливаемого масла. Масло масляным насосом подается либо в масляные фильтры, либо в центрифугу. Очищенное масло поступает на смазку шеек коленчатого вала и подшипников распределительных (кулачковых) валов МГР, а также может смазывать разбрызгиванием цилиндры двигателя, шестерни привода топливного насоса, толкатели и коромысла МГР. Применяемые масла разделяются на минеральные из нефти и синтетические, получаемые органическим синтезом. Минеральные более дешевы, синтетические менее вязки при низких температурах, что обеспечивает запуск и сохраняют вязкость при высоких температурах.
|
|
|
|
|
|
|
|
|
Таблица 18.1 |
||
|
|
|
Классификация масел для ДВС |
|
|
||||||
Класс |
Пределы вязкости, |
|
Группы масел по эксплуатационным свойствам |
|
|||||||
вязко- |
мм2/с, |
при темпе- |
|
|
|
В |
|
|
Г |
|
|
сти |
ратуре, С |
|
Б1 |
|
|
|
|
||||
|
|
|
|
|
|
|
|
||||
|
100 |
-18 |
|
|
В1 |
|
В2 |
|
Г1 |
Г2 |
|
6 |
6 0,5 |
– |
|
М6Б1 |
М6В1 |
|
|
|
М6Г1 |
|
|
8 |
8 0,5 |
– |
|
М8Б1 |
М8В1 |
|
М8В2 |
|
М8Г1 |
М8Г2 |
|
10 |
10 1 |
– |
|
М10Б1 |
М10В1 |
|
М10В2 |
|
М10Г1 |
М10Г2 |
|
12 |
12 0,5 |
– |
|
|
|
|
М12В2 |
|
|
М12Г2 |
|
43/6 |
6 0,5 |
1300…2600 |
|
М43/6Б1 М43/6В1 |
|
|
|
|
|
|
|
43/8 |
8 0,5 |
1300…2600 |
|
М43/8Б1 М43/8В1 |
|
М43/8В2 |
|
|
|
|
|
43/10 |
10 0,5 1300…2600 |
|
М43/10Б1 М43/10В1 М43/10В2 |
|
|
|
|
||||
63/10 |
10 0,5 2600…10400 |
|
|
М63/10В1 М63/10В2 |
М63/10Г1 |
М63/10Г2 |
|
Классификация масел проводится по двум признакам: вязкости и группе качества, которая зависит от совокупности эксплуатационных свойств.
Класс вязкости определяет сезон эксплуатации зима – лето, так по американскому стандарту SAE масло 15W-40 – пригодно для -15 °С зимой и +40 °С летом. По стандарту API масла разделяют следующим образом: S – для бензиновых двигателей и С – для дизелей. Вторая буква обозначает уровень эксплуатационных свойств: SA, SD или CA, CE. В России масла классифицируются по ГОСТ 17479-85. Буква М – моторное масло, а цифра после буквы – вязкость масла при 100 °С. Следующая буква характеризует качество, а индекс 1 – для ДиЗ, 2 – для дизелей (табл. 18.1).
103
Расчет масляной системы
Ориентировочно количество масла Vм составляет (0,04...0,09)Nе для бензиновых двигателей легковых автомобилей; (0,07...0,1)Nе для бензиновых двигателей грузовых автомобилей; (0,11...0,16)Nе для дизелей грузовых автомобилей.
Более точно циркуляционный расход Vм масла зависит от количества отводимой теплоты Qм:
Qм= (0,015...0,030) Q0, или Q |
q g |
N |
|
Н |
|
1 |
, (18.1) |
|
м 3,6 106 |
||||||
ом |
м е |
|
ен |
|
|
||
где Q0 – количество теплоты, выделяемой топливом при сгорании в |
|||||||
течение 1с, qм = Qом/Qт – относительный |
теплоотвод |
через СС; |
qм = 0,015…0,02 – ДсИЗ; qм = 0,02…0,025 – дизели; qм = 0,04…0,06 –
дизели с охлаждаемыми поршнями, HT – низшая теплотворная способность топлива, кДж/кг; gе – удельный расход топлива на режиме эффективной мощности; Nе – эффективная мощность.
Циркуляционный расход масла, м3/с, равен |
|
VM = QM/ ( MCM TM), |
(18.2) |
где M – плотность масла, = 900 кг/м3; СМ = 2,094 – теплоемкость масла, кДж/(кг К); TM – температура нагрева масла в двигателе, К, перепад температур между выходом и входом СС t = 10…15 С в ДсИЗ и t = 20…25 С в дизелях.
Этот расход увеличивают в два раза для стабилизации давления в СС, кроме того, для компенсации утечек через зазоры вводят коэффи-
циент М = 0,6...0,8, тогда |
|
VР = 2VМ/ М, |
(18.3) |
где VР – производительность насоса, м3/с; р – давление масла, у карбюраторного двигателя р = 0,3...0,5 МПа, в дизелях р = 0,3...0,7 МПа,Н = 0,85 – 0,9 механический КПД насоса.
Тогда Vр м3/с будет равно: |
|
|
(5,0…6,0)Nе 10-6 |
– ДсИЗ; |
|
(6,0…9,0)Nе 10-6 |
– дизели; |
(18.4) |
(10…11)Nе 10-6 – дизели с охлаждаемыми поршнями.
Vотк= (1,5…2,0) Vнагн,
где Vнагн – подача нагнетательной секции насоса.
104
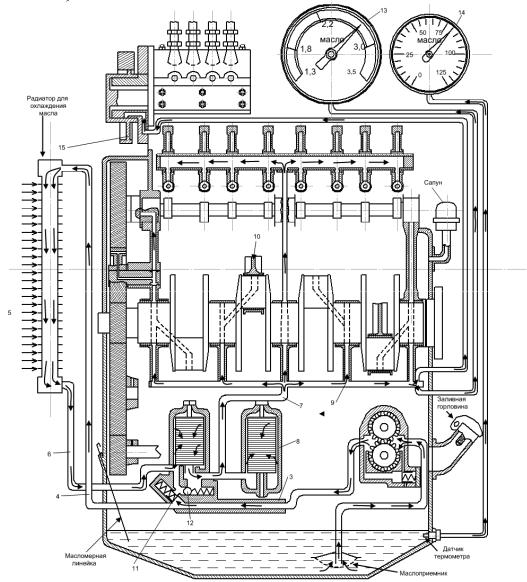
Рис. 18.1. Схема системы смазки дизеля Д-35:
1 – насос; 2 – трубка; 3, 7, 9, 10 – канал; 4, 6 – маслопровод; 5 – радиатор; 8, 16 – фильтр; 11, 12 – клапан; 13 –манометр;14 – термометр; 15 – сверление
Маслонасос
В современных двигателях применяют масляные насосы шестеренчатого типа с внешним (рис. 18.2, а) и внутренним зацеплением.
Во втором случае используют как эвольвентное (рис. 18.2, б), так и эпициклоидальное зацепление (рис. 18.2, в).
105
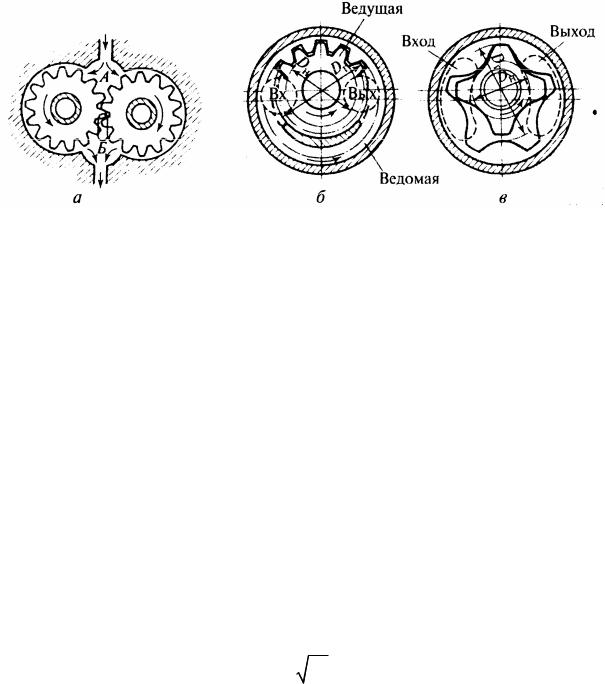
Размеры шестерен, а следовательно, и производительность масляных насосов целесообразно определить исходя из циркуляционного расхода масла через двигатель, необходимого для отвода теплоты Qом, воспринимаемой маслом.
Действительную подачу насоса задают большей величины циркуляционного расхода с целью обеспечения необходимого давления масла в магистрали во всем диапазоне частот вращения и при износе трущихся пар двигателя и насоса, м3/с:
Рис. 18.2. Масляные насосы с внешним (а) и внутренним эвольвентным (б) и эпициклоидальным (в) зацеплением
Размеры шестерен с учетом объемного коэффициента подачи насоса определяют из выражения, м3/с:
V V |
/ |
|
d |
w |
hbn |
1 |
10 9 / н , |
(18.5) |
|
|
|||||||
т д |
|
н |
|
н 60 |
|
где Vт – теоретическая подача насоса, м3/с, необходимая по тепловому расчету;н – объемный коэффициент подачи насоса, равный н = 0,6…0,85;
dw – диаметр начальной окружности ведущей шестерни, мм; h – высота зуба; b – длина зуба, мм;
nн – частота вращения ведущей шестерни, мин-1.
Итак, Vт должно быть равно Vнагн, полученному из теплового расчета по формулам (18.3), (18.4).
Параметры маслонасоса определяют следующим образом [8]. Для современных шестеренчатых насосов с числом зубьев колес
8…14 при окружной скорости 10…20 м/с и при отношении b/m в пределах 6…10 модуль зуба шестерни, мм, равен
m (0,24...0,44) Vд , |
(18.6) |
где Vд – действительная производительность насоса, м3/с.
106
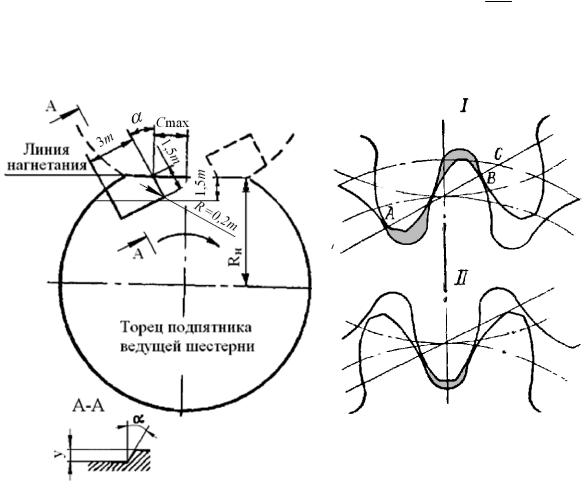
V |
Vт |
|
Vт |
, |
(18.7) |
|
0,85 |
||||
д |
н |
|
|
|
Vт – теоретическая (потребная) производительность насоса, н – механический КПД насоса.
Выбрав число зубьев z и модуль m, находят ширину зуба b и диаметр начальной окружности, мм:
b G |
/2 nm2(z sin |
2 |
) 10 6. |
(18.8) |
д |
|
0 |
|
|
Для некоррегированных зубчатых колесDн m zi , для коррегированных Dн m zi sin 0 .
Затем рассчитывают параметры разгружающей канавки: Глубина канавки, мм, равна
у 0,5(z 1)bnm 10 6. |
(18.9) |
Смещение от межцентровой оси колес (рис. 18.3) Cmax m , или y и
2
Cmax выбирают по табл. 18.2.
Рис. 18.3. Определение размеров разгрузочной канавки
107
Рис. 18.4. Начало зацепления (I) и положение максимального запертого объема (II) при беззазорном зацеплении
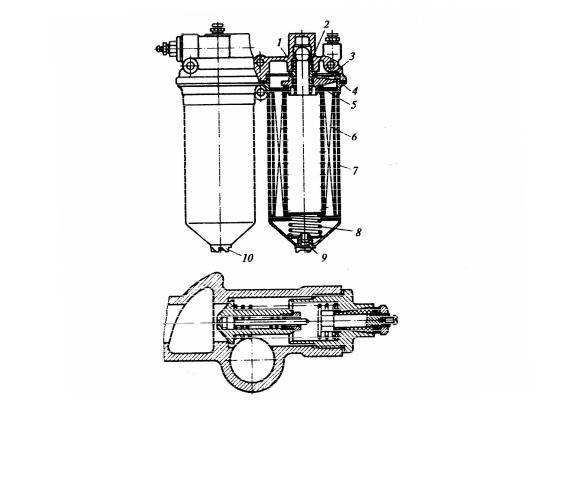
|
|
Значения для m=1 и b=1 |
|
Таблица 18.2 |
|||
|
|
|
|
|
|||
Число зубьев |
z |
8 |
10 |
12 |
14 |
|
|
Расстояние от |
C1max |
1,765 |
1,725 |
1,7 |
1,68 |
Cmax = C1 m |
|
оси до канавки |
|
|
|
|
|
|
|
Глубина канав- |
Y1 |
2 10-6 |
2,5 10-6 |
3 10-6 |
3,5 10-6 |
Y1 =Y1 bm |
|
ки |
|
|
|
|
|
|
|
При принятом боковом зазоре между зубьями, равном 0,08m, площадь канавки (0,08…0,1)m2.
Мощность, кВт, необходимую для привода насоса, находят из выражения:
NН |
|
Vт (Рвых Рвх ) |
103 , |
(18.10) |
|
||||
|
|
м |
|
где Рвых – Рвх = 0,3…0,6 – перепад давлений, МПа;м = 0,85…0,9 – механический КПД насоса.
Рис. 18.5. Полнопоточный фильтр очистки масла:
1 – корпус; 2 – резьбовой штуцер; 3 – замковая крышка; 4 – прокладка клапана; 5 – уплотнитель элемента; 6 – фильтрующий элемент; 7 – колпак; 8 – пружина; 9 – сливная пробка; 10 – храповик
108
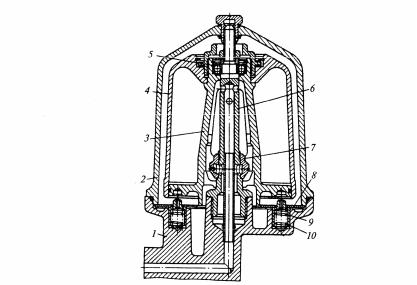
Масляные фильтры
Применяют фильтры грубой и тонкой очистки. Для грубой очистки используют фильтры с сетчатыми, пластинчато-щелевыми и ленточно-щелевыми элементами для задержания частиц 50...120 мкм, а для тонкой очистки частиц 50...40 мкм применяют элементы из бумаги, тканей, картона, хлопчатобумажной пряжи (рис. 18.5).
Центрифуга (рис. 18.6)
Применяют центрифуги с внешним гидравлическим реактивным приводом и с внутренним бессопловым и сопловым приводом.
В современных центрифугах подача масла под давлением 0,25...0,6 МПа обеспечивает вращение ротора со скоростью
5000...8000 мин-1.
Рис. 18.6. Центрифуга:
1 – корпус; 2 – колпак; 3 – корпус ротора; 4 – колпак ротора; 5 – шарикоподшипник; 6 – ось ротора; 7 – форсунка; 8 – пластинка; 9 – стопорный палец; 10 - пружина
Из теорем импульса сил можно определить реактивную силу струи
|
MVp |
Vp |
|
n |
|
|
||
P |
|
|
|
|
|
R , |
(18.11) |
|
2 |
2 F |
30 |
||||||
|
|
|
|
|
||||
|
|
c |
|
|
|
где M – плотность масла, кг/м3;
Vр – расход масла через сопло центрифуги, м3/с;– коэффициент сжатия струи масла; = 0,9...1,1; Fc – площадь отверстия сопла, м2;
109