
1854
.pdfМорозоустойчивость грунтов, укрепленных шлакощелочным вяжущим, в зависимости от места расположения в конструкции дорожной одежды, категории дороги и климатических условий составляет от F10 до F50. Для укрепления грунтов должны использоваться доменные молотые гранулированные шлаки, помолотые до удельной плотности более 300 м2/кг, при этом влажность шлака не должна превышать 1,0 %
Химический состав шлаков должен находиться в следующих пределах
(табл. 3).
|
|
|
|
Таблица 3 |
|
|
|
|
|
Наименование окислов |
Si 02 |
Ca O |
Al2 O3 |
Mg O |
Содержание окислов, % |
36-42 |
39-49 |
8-15 |
2-8 |
Шлаки должны содержать не менее 80 % остеклованного вещества. Ориентировочное содержание молотого шлака в смеси при укрепле-
нии различного вида грунтов для получения марок 20-100 в возрасте 28 суток должно соответствовать значениям, приведенным в табл. 4.
|
|
|
|
|
|
|
Таблица 4 |
|
|
|
|
|
|
||
Вид грунта, |
Расход молотого шлака, % от массы сухого грунта |
||||||
|
|
Марка материала |
|
|
|||
подвергаемого укреплению |
|
|
|
|
|||
20 |
40 |
|
60 |
|
80 |
100 |
|
|
|
|
|||||
Пески |
12-14 |
14-16 |
|
16-18 |
|
18-20 |
20-22 |
Супеси легкие и пылеватые |
14-16 |
16-20 |
|
20-22 |
|
22-24 |
24-26 |
Суглинки легкие |
16-18 |
18-20 |
|
22-24 |
|
- |
- |
Суглинки тяжелые |
18-20 |
20-22 |
|
22-26 |
|
- |
- |
Плотность щелочного раствора при укреплении грунтов составляет
1,14–12,2 г/см3.
Для получения той или иной марки укрепленного грунта, плотности щелочного раствора пользуются табл. 5.
|
Таблица 5 |
|
|
Марка укрепленного грунта |
Плотность щелочного раствора, г/см3 |
20 |
1,14-1,18 |
40 |
1,16-1,20 |
60 |
1,18-1,20 |
80 |
1,18-1,20 |
100 |
1,20-1,22 |
Приготовление щелочного раствора производят в металлических емкостях, оборудованных паровыми регистрами, подогревающими раствор до 60–70 ºС, и барбатацией сжатым воздухом для его равномерного перемешивания. Плотность раствора доводят до рабочей плотности добавлением необходимого количества воды. Контроль плотности щелочного раствора производят при температуре раствора +20 ºС с помощью денсиметра.
Смесь грунта, укрепленного шлакощелочным вяжущим, готовят в грунтосмесительной установке ДС-50А. Готовую смесь доставляют на дорогу автосамосвалами и распределяют либо универсальными укладчиками, либо автогрейдером. Уплотнение слоя грунта, укрепленного шлакощелочным вяжущим, производят самоходными пневмокатками за 12–16 проходов по одному следу. При этом коэффициент уплотнения должен со-
ставлять 0,98–1,0.
За готовым слоем из грунта, укрепленного шлакощелочным вяжущим,
производят уход с помощью розлива жидкого битума в количестве 0,6– 0,8 л/м2.
Вотличие от цементогрунтовых оснований смесь грунта со шлаком до введения в неё щелочного раствора не схватывается и может находиться даже под дождем в течение нескольких дней. Но как только в смесь вводится щелочной раствор, необходимо сразу смесь перемешать, спланировать и уплотнить.
Основание из грунтов, укрепленных шлакощелочным вяжущим, обладает повышенной морозостойкостью и деформативной способностью. Это объясняется особенностью их структуры – она волокнистая. Новообразования в них представлены низкоосновными гидроалюмосиликатами.
ВОмской области силами ДРСУ-6 построено более 14 км дорог IV категории с основаниями из грунтов, укрепленных шлакощелочными вяжущими. Это дороги Иртыш – Великорусское – Калачинск. Эти участки построены в 1985 г. и по сей день находятся в хорошем состоянии.
Рекомендуемые конструкции дорожных одежд представлены в табл.6.
|
|
|
|
|
|
Таблица 6 |
|
|
|
|
|
|
|
|
|
№ |
|
|
|
Толщина |
Категория |
Дорожно- |
|
Конструктивные слои |
|
климатическая |
|||||
слоя |
|
слоя, см |
дороги |
||||
|
|
|
зона |
||||
|
|
|
|
|
|
||
1 |
|
2 |
|
3 |
4 |
5 |
|
1 |
Покрытие из монолитного цементо- |
h1= 20-24 |
|
|
|||
|
бетона М-400 |
|
|
|
|
|
|
2 |
Песок, обработанный 4% цемента |
|
h2= 6 |
I |
II-IV |
||
3 |
Основание из песчаных грунтов, ук- |
h3= 16-18 |
|||||
|
|
||||||
|
репленных шлакощелочным вяжу- |
|
|
|
|||
|
щим, класс прочности А |
|
|
|
|
||
1, 2 |
Покрытие из двухслойного асфаль- |
h1= 5-6 |
|
|
|||
|
тобетона |
|
|
h2= 8-10 |
|
|
|
3 |
Верхний слой основания из грунта, |
h3= 16-20 |
|
|
|||
|
укрепленного |
шлакощелочным |
вя- |
|
I-II |
II-IV |
|
|
жущим, класс прочности А или Б |
|
|
||||
|
|
|
|
|
|||
4 |
Нижний слой основания из грунта, |
h4= 16-18 |
|
|
|||
|
укрепленного |
шлакощелочным |
вя- |
|
|
|
|
|
жущим, классы прочности Б и I |
|
|
|
|

|
|
|
|
|
|
|
|
Окончание табл. 6 |
|
1 |
|
|
2 |
|
|
3 |
4 |
|
5 |
1, 2 |
Покрытие из двухслойного асфаль- |
h1= 8-12 |
|
|
|
||||
|
тобетона |
|
|
|
|
h2= 8-12 |
|
|
|
3 |
Плита из шлакощелочного бетона |
|
h3= 16-18 |
I-II |
|
II-III |
|||
4 |
Песок, обработанный 2% битума |
|
h4= 3-4 |
|
|||||
5 |
Основание из грунтов, укрепленных |
h5= 16-20 |
|
|
|
||||
|
шлакощелочным вяжущим, |
классы |
|
|
|
|
|||
|
прочности А и Б |
|
|
|
|
|
|
|
|
1 |
Покрытие из асфальтобетона |
|
|
h1= 4-6 |
|
|
|
||
2 |
Асфальтобетонные плиты СибАДИ |
h2= 12-16 |
|
|
|
||||
3 |
Песок обработанный 2% битума |
|
h3= 3-4 |
II-III |
|
II-III |
|||
4 |
Основание из грунтов, укрепленных |
h4= 16-20 |
|
||||||
|
|
|
|||||||
|
шлакощелочным вяжущим, |
классы |
|
|
|
|
|||
|
прочности А и Б |
|
|
|
|
|
|
|
|
1, 2 |
Покрытие из двухслойного асфаль- |
h1= 6-8 |
|
|
|
||||
|
тобетона |
|
|
|
|
h2= 6-8 |
|
|
|
3 |
Верхний слой основания из грунтов, |
h3= 16-20 |
|
|
|
||||
|
укрепленных |
шлакощелочным |
вя- |
|
II-III |
|
II-IV |
||
|
жущим, классы прочности Б, I |
|
|
|
|
||||
|
|
|
|
|
|
|
|||
4 |
Нижний слой основания из грунтов, |
h4= 18-22 |
|
|
|
||||
|
укрепленных |
шлакощелочным |
вя- |
|
|
|
|
||
|
жущим, класс прочности I или II |
|
|
|
|
|
|||
1, 2 |
Покрытие из двухслойного асфаль- |
h1= 5 |
|
|
|
||||
|
тобетона |
|
|
|
|
h2= 6 |
|
|
|
3 |
Верхний слой основания из грунтов, |
h3= 12-14 |
|
|
|
||||
|
укрепленных |
шлакощелочным |
вя- |
|
III |
|
II-III |
||
|
жущим, классы прочности I, II |
|
|
|
|
||||
|
|
|
|
|
|
|
|||
4 |
Нижний слой основания из грунтов, |
h4= 16-18 |
|
|
|
||||
|
укрепленных |
шлакощелочным |
вя- |
|
|
|
|
||
|
жущим, классы прочности II, III |
|
|
|
|
|
|||
1 |
Асфальтобетон теплый илихолодный |
h1= 3-4 |
|
|
|
||||
2 |
Основание из грунтов, укрепленных |
h2= 14-18 |
IV |
|
II-III |
||||
|
шлакощелочным |
вяжущим, |
классы |
|
|
||||
|
|
|
|
|
|||||
|
прочности II, III |
|
|
|
|
|
|
|
|
1 |
Двойная поверхностная обработка |
|
h1= 3 |
|
|
|
|||
2 |
Основание из грунтов, укрепленных |
h2= 14-18 |
IV |
|
II-IV |
||||
|
шлакощелочным |
вяжущим, |
классы |
|
|
||||
|
|
|
|
|
|||||
|
прочности II-III |
|
|
|
|
|
|
|
|
1 |
Одиночная поверхностная обработка |
h1= 1,5-2 |
|
|
|
||||
2 |
Основание из грунтов, укрепленных |
h2= 12-14 |
V |
|
II-IV |
||||
|
шлакощелочным |
вяжущим, |
классы |
|
|
||||
|
|
|
|
|
|||||
|
прочности II-III |
|
|
|
|
|
|
|
|
1, 2 |
Покрытие из двухслойного асфаль- |
h1= 5 |
|
|
|
||||
|
тобетона |
|
|
|
|
h2= 5-6 |
III |
|
II-IV |
3 |
Щебеночное основание |
|
|
h3= 18-26 |
|
||||
4 |
Основание из грунтов, укрепленных шлако- |
h4= 12-14 |
|
|
|
||||
|
щелочнымвяжущим,классыпрочностиII,III |
|
|
|
|
Применение в основаниях дорожных одежд цементогрунтов или грунтов, укрепленных шлакощелочными вяжущими, позволяет повысить прочность Е4:
-при укреплении грунтов цементом Е4 = 400–600 МПа;
-при укреплении грунтов шлакощелочным вяжущим Е4 = 400– 800 МПа.
Основания из укрепленных материалов работают как монолитная плита.
Омским дорожникам необходимо либо полностью отказаться от привозного щебня с заменой щебня на местные материалы – грунты, укрепленные различными вяжущими (цементом, шлакощелочным вяжущим и др.), либо частично с экономией его до 60 – 70 % и использованием золоминеральных смесей (ЗМС), в состав которых, кроме щебня и песка, входят отходы промышленности. Наибольшее количество отходов в Омске скопилось в золоотвалах ТЭЦ-2, ТЭЦ-4 и ТЭЦ-5, последние работают на экибастузских углях.
Золошлаковые отходы ТЭЦ относятся к кислым неактивным и не могут использоваться в качестве вяжущего. Химический состав золошлаковых отходов ТЭЦ-2, ТЭЦ-4, ТЭЦ-5 г. Омска указан в табл. 7.
Таблица 7
Золошлаковые отходы |
|
|
Содержание оксидов, % по массе |
|
|
||||
SiO2 |
Fe2O3 |
Al2O3 |
CaO |
MgO |
SO3 |
Na2O |
K2O |
ППП |
|
ТЭЦ-2 |
59,7 |
12,7 |
20,48 |
1,75 |
1,25 |
0,48 |
- |
- |
18,3 |
ТЭЦ-4 |
51,3 |
11,54 |
27,7 |
1,6 |
0,8 |
0,79 |
0,02 |
- |
5,98 |
ТЭЦ-5 |
54,5 |
9,6 |
22,4 |
2,45 |
2,77 |
0,26 |
4,25 |
2,52 |
15,73 |
Золы гидроударения смешивали с известковыми отходами. В качестве таких отходов использовали отход при производстве карбида г. Темиртау. В состав золоминеральных смесей входят: щебень – до 40 %, местные иртышские пески среднезернистые и мелкозернистые – до 35 %, зола гидроудаления – до 17 %, известковые отходы карбидного производства – до 8 % и вода.
Щебень, входящий в состав ЗМС, имел размер зерен 20–40 мм и удовлетворял требованиям ГОСТ 8262-82, песок – ГОСТ 8736-85. В результате исследований, проведенных на кафедре «Строительство и эксплуатация дорог», а также экспериментальных работ, выполненных в ЗАО УМ-7, были разработаны и утверждены технические условия ТУ 5716-001-52-1П- 0117-93 на смеси золоминеральные для дорожного строительства.
В ТУ разработаны четыре состава смесей, удовлетворяющих I, II и III классам прочности. Модуль упругости слоев с использованием золоминеральных смесей составлял от 250 до 800 МПа. Удельная поверхность зол гидроудаления составляла не менее 300 м2/кг.
Оптимальная добавка извести составляет от 4 до 8 % от массы смеси. Оптимальное содержание воды определяли с учетом влажности исходных материалов (песка, щебня, золы). Содержание вяжущего в ЗМС назначали в зависимости от вида материалов и конструкции дорожной одежды. Золоминеральные смеси приготавливали в грунтосмесительной установке
ДС-50А.
Технологический процесс устройства оснований из золоминеральных смесей предусматривает:
-приготовление смеси;
-вывозку смеси на подготовленное земляное полотно или земляное корыто;
-распределение и профилирование смеси;
-уплотнение;
-устройство слоя покрытия из асфальтобетона.
Устройство оснований из ЗМС проводили при положительной температуре воздуха.
Золоминеральные смеси рекомендуется укладывать щебнеукладчиками или универсальными укладчиками сразу на всю ширину и толщину слоя, допускаются разравнивание и планировка слоя из золоминеральной смеси автогрейдерами. Золоминеральные смеси легко уплотняются самоходными пневмокатками массой 15–16 т за 12–16 проходов по одному следу, при этом коэффициент уплотнения составляет не менее 0,98.
Количество проходов катка уточняется в процессе производства работ. На готовый слой из золоминеральных смесей рекомендуется сразу укладывать вышележащий слой дорожной одежды с асфальтобетонным покрытием.
Ежегодно на дорогах в г. Омске укладывали в основание дорожных одежд вместо щебня до 30 тыс. т золоминеральных смесей.
За последние годы построен подъезд к ЦСГПП, автомобильная дорога к д. Николаевка Нижнеомского района, автодороги, проезды и площади на территории ОАО «Техуглерод» и другие дороги, площадки и тротуары в г. Омске с основаниями из ЗМС.
При строительстве таких оснований необходимо производить тщательный лабораторный контроль за:
-качеством исходных материалов и их хранением;
-приготовлением смесей и за дозировкой составляющих смеси;
-подготовкой мест укладки;
-транспортированием, распределением и уплотнением смеси;
-отделкой и уходом за построенным основанием.
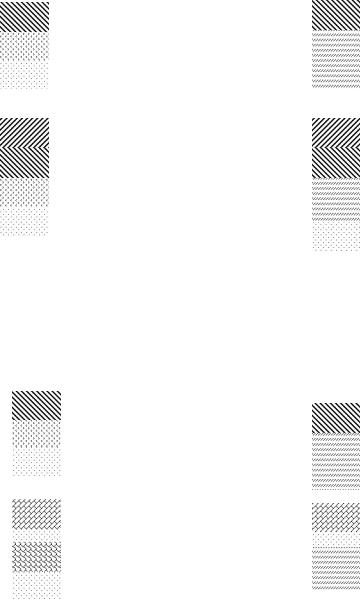
Конструкции дорожных одежд с применением ЗМС
Проектная конструкция |
Конструкция с основанием из ЗМС |
||||
6 см |
|
Асфальтобетон м/з плотный тип А |
6 см |
|
Асфальтобетон м/з плотный |
|
|
||||
22 см |
|
щебень |
|
|
ЗМС |
|
|
|
|||
26 см |
|
песок |
|
|
|
|
|
|
|
||
5 см |
|
Асфальтобетон м/з плотный |
5 см |
|
Асфальтобетон м/з плотный |
|
|
||||
|
|
||||
6 см |
|
Асфальтобетон к/з |
6 см |
|
Асфальтобетон к/з |
|
|
||||
22 см |
|
щебень |
18 см |
|
ЗМС |
|
|
||||
26 см |
|
песок |
|
|
|
|
|
|
|
||
|
|
|
15 см |
|
песок |
|
|
|
|
|
|
Конструкции покрытий тротуаров
Проектная конструкция |
Конструкции оснований из ЗМС |
3 см |
|
Асфальтобетон м/з плотный |
3 см |
|
Асфальтобетон м/з |
12 см |
|
щебень |
|
||
|
14 см |
|
ЗМС |
||
|
|
||||
10 см |
|
песок |
|
||
|
|
|
|
||
9 см |
|
Тротуарная плитка |
8 см |
|
Тротуарная плитка |
|
|
||||
|
|
||||
|
|
||||
|
|
|
|
||
5 см |
|
Песок |
3 см |
|
Песок |
|
|
||||
|
|
||||
12 см |
|
Бетон В 25 |
|
||
|
15 см |
|
ЗМС |
||
|
|
|
|||
10 см |
|
Песок |
|
|
|
|
|
|
|
||
|
|
|
|
|
|
Качество смеси оценивали по результатам испытания образцов экс- пресс-методом (кипячение в воде образцов, изолированных от доступа влаги, в течение не менее 4 ч, охлаждение в течение не менее 1 ч).
При укладке и уплотнении контролировали:
-толщину и ширину укладываемого слоя;
-правильность технологии укатки;
-толщину и плотность уплотненного слоя.
В зависимости от интенсивности движения и категории дороги устраивали основание из золоминеральных смесей от 18 см в один слой до 40–
60 см в два слоя с устройством одноили двухслойного асфальтобетонного покрытия.
Опыт строительства и эксплуатации оснований из ЗМС показал следующее:
1.Необходимо очень тщательно подбирать состав ЗМС и следить за качеством составляющих материалов с соблюдением всех требований ТУ.
2.Приготовленные в установке золоминеральные смеси можно в течение нескольких суток хранить в штабелях, а затем укладывать в покрытие.
3.Золоминеральные смеси продолжают набирать прочность в течение нескольких лет (6 лет и более).
4.Недопустимо пересыхание смеси в период укладки оснований из
ЗМС.
5.Нельзя оставлять основания из ЗМС без покрытия, т.к. это приводит
ких истиранию, пылению и разрушению основания.
6.Асфальтобетонное покрытие должно быть устроено сразу же после устройства основания.
7.Для оснований из ЗМС переувлажненные условия не являются опасными, наоборот, основания из ЗМС более интенсивно набирают прочность. Характерным примером и подтверждением этому служит строительство основания из ЗМС при устройстве разворотной площадки для троллейбусов на левом берегу г. Омска. Эта площадка строилась на заболоченном участке, и сколько туда не отсыпали щебня, основание из него все время просаживалось, т.е. создать плотный слой не удавалось. Устройство же двухслойного основания из ЗМС позволило создать плотное и прочное основание. Причем прочность основания продолжала расти в течение более 6 лет.
Таким образом, исходя из вышеизложенного, строительство оснований из ЗМС экономически выгодно и технологически обосновано. При этом можно экономить до 60 % щебня и использовать отходы промышленности тем самым улучшать экологическую обстановку в г. Омске.
УДК 625
ИСПОЛЬЗОВАНИЕ МЕТОДА ХОЛОДНОГО РЕСАЙКЛИНГА ПРИ КАПИТАЛЬНОМ РЕМОНТЕ АВТОМОБИЛЬНОЙ ДОРОГИ ОМСК – МУРОМЦЕВО – СЕДЕЛЬНИКОВО
В.Г. Степанец, канд. техн. наук, Е.В. Войцеховская студентка
Строительство новых и ремонт существующих дорог в Омской области входит в задачи приоритетных национальных проектов. Отсутствие в Ом-
ской области местных каменных материалов сдерживает строительство новых, а также капитальный ремонт существующих автомобильных дорог.
ВОмской области накоплен опыт ремонта дорожных одежд с применением метода холодного ресайклинга. Эти работы выполнялись под руководством канд. техн. наук, доц. кафедры «Строительство и эксплуатация дорог» СибАДИ С.Ф. Филатова и канд. техн. наук В.В. Шипицына.
Существующая дорожная одежда автомобильной дороги Омск – Муромцево – Седельниково характеризуется следующими факторами: ямочностью, выбоинами, колейностью и другими дефектами асфальтобетонного покрытия.
При капитальном ремонте существующее асфальтобетонное покрытие было восстановлено по технологии холодной регенерации.
Вкачестве ведущей машины был принят комплект машин фирмы «Wirtgen», состоящий из ресайклинга WR-2500 и смесительной установки WM-400. Работы по ремонту вышеуказанной дороги производились в следующей технологической последовательности. Поверхность существующего покрытия очищалась от пыли и грязи поливомоечной машиной ПМ-130, оснащенной щеткой. Устраивался выравнивающий слой из щебня фракции 10–20 мм толщиной 10 см. Затем производили ресайклирование совместно с существующим асфальтобетонным покрытием на общую толщину 16 см. В процессе прохода фрезы с помощью мобильной смесительной установки WM-400 вводили цемент в количестве 4 % и воду. Вместимость двух бункеров цементосмесительной установки составляла 25 т, вместимость бака воды – 8,5 т. Цемент подвозили автоцементовозом ТУ-12 емкостью 16 т, воду – поливомоечной машиной. Скорости рабочего хода ресайклера WR-2500 и мобильной установки WM-400 должны быть синхронными, при этом обеспечивается необходимое дозирование цемента и воды в виде цементной суспензии в распределительную систему ресайклера.
Качественное перемешивание цементоводной суспензии, подача оптимального количества в регенерирующий слой, дозирование цемента и воды
взависимости от влажности материалов и заданной плотности обеспечивает бортовая система ЭВМ установки WM-400. Ресайклер WR-2500 и смесительную установку WM-400 обслуживали два звена. Их состав указан в табл. 1.
После начала работы ресайклера за ним с интервалом 4–5 м по регенерируемой полосе с такой же скоростью движется вибрационный каток BW-161AC для прикатки разрыхлительной смеси и предотвращения интенсивного влагоиспарения, особенно при повышенной температуре воздуха. Одновременно каток подготавливает сфрезерованный слой под профилирование автогрейдером ДЗ-180. Эта технологическая схема осуществляется за два прохода по одному следу.
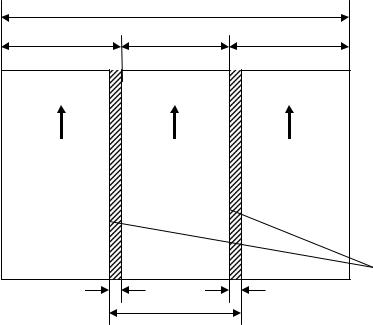
|
|
|
|
Таблица 1 |
|
|
|
|
|
|
|
№ |
Наименование машины |
Марка |
Профессия и разряд |
Кол-во |
|
п/п |
|
|
|
|
|
1 |
Поливомоечная машина |
ПМ-130 |
Машинист 4 раз. |
1 |
|
2 |
Автосамосвал |
КамАЗ-5511 |
Водитель категории С, D |
По расчету |
|
3 |
Автогрейдер |
ДЗ-180 |
Машинист 4 раз. |
1 |
|
|
|
|
Машинист 4 раз. |
|
|
4 |
Ресайклер |
WR-2500 |
дорожный рабочий: |
1 |
|
4 раз. – 1 |
|||||
|
|
|
|
||
|
|
|
3 раз. – 3 |
|
|
5 |
Цементовоз |
ТЦ-12 |
Водитель категории С, D |
1 |
|
6 |
Каток |
BW-216 |
Машинист 4 раз. |
1 |
|
7 |
Вибрационный каток |
BW-261АС |
Машинист 4 раз. |
1 |
|
8 |
Каток |
BW-161АС |
Машинист 4 раз. |
1 |
|
9 |
Пневмокаток |
VP-200 |
Машинист 4 раз. |
1 |
|
10 |
Автогудронатор |
ДС-39Б |
Машинист 4 раз. |
1 |
Длина участка регенерируемого основания, исходя из сроков начала |
||
схватывания цемента, принята 120 м. При ширине старого покрытия 7 м |
||
ресайклер совершает три проходки (рис. 1). |
|
|
|
7,0 м |
|
2,4 м |
2,2 м |
2,4 м |
III |
II |
I |
проход |
проход |
проход |
WR 2500 |
WR 2500 |
WR 2500 |
|
|
Перекрытие следа |
0,1 м |
|
ресайклера |
2,4 м |
0,1 м |
|
|
|
Рис. 1. Схема работы ресайклера RW 2500
По завершении регенерации на одном участке ресайклер передвигается на следующий. Прикатанная поверхность основания профилируется автогрейдером ДЗ-180. Профилирование основания завершается после 8 проходов автогрейдера при рабочем ходе в одном направлении.
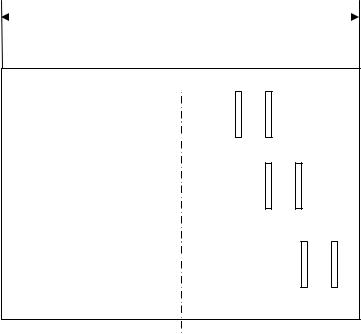
Уплотнение основания осуществляется звеном катка, состоящего из трех механизмов: каток BW-161AC, пневмокаток VP-200, вибрационный каток BW-216. Схема движения катков приведена на рис.2.
7,0 м
BW 161AC
VP 200
BW 216
Рис. 2. Схема уплотнения основания катками
В первую очередь основание уплотняют катки BW-161AC и VP-200. Каток BW-161АС начинает уплотнение от правого края дороги. За ним, левее, с перекрытием следа катка BW-161AC на 1/3 ширины вальца 0,5 м движется каток VP-200. Уплотнив полосу длиной 120 м, катки задним ходом возвращаются к началу полосы и, переместившись к оси основания, продолжают уплотнять основание. При этом каток BW-161AC на 1/3 перекрывает предыдущий след катка VP-200. В это время каток BW-216 продолжает уплотнение основания, ориентируясь на его правый край.
После уплотнения полосы, проходящей через ось основания, катки начинают работу с левого края по прежней схеме.
Каждый каток совершает по 6 проходов по одному следу. При этом каток BW-161AC работает по схеме: первый проход – без вибратора, 2–6 проходы – с включенным вибратором; BW-216: первые и последние два прохода – без вибратора, третий и четвертый проходы – с включенным вибратором.
Для предотвращения образования волосяных трещин на поверхности регенерируемого слоя необходимо готовое основание дополнительно увлажнить водой из расчета 0,6–0,8 л/м2, а затем прикатать катком VP 200 за два прохода по одному следу.