
[SHipinsky_V.G.]_Oborudovanie_i_osnastka_upakovoch2(z-lib.org)
.pdf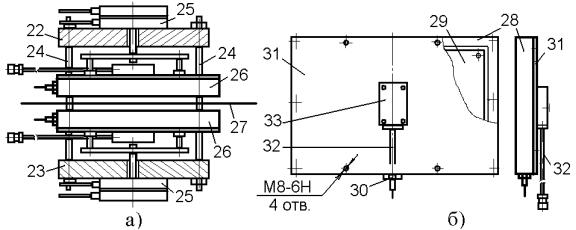
Рис. 11.18. Конструктивная схема блока нагрева формуемого полотна: а) – блок нагрева; б) – контактный электронагреватель
Электронагревательные элементы 29, закрепленные в соответствующих выемках плиты, закрываются плоской стеклотекстолитовой крышкой 31, содержащей в центре две латунные штыревые клеммы, обеспечивающие соединение элементов 29 с кабелем питания 32. Выступающие над крышкой части клемм закрываются при этом стеклотекстолитовым диэлектрическим кожухом 33, к которому дополнительно закрепляется и кабель питания 32. Для крепления электронагревателя к штоку диафрагменного пневмоцилиндра в нем со стороны крышки выполнены четыре резьбовых отверстия М8-6Н.
Суммарное количество энергии, которое необходимо подвести к контактному электронагревателю 26, определяется из следующего уравнения энергетического баланса:
Q = Qм + Qл + Qк |
(11.2) |
где Qм – количество энергии, затрачиваемой на нагрев полимерного материала; Qл – количество энергии, отдаваемой нагревателем в окружающую среду
лучеиспусканием;
Qк – количество энергии, отдаваемой нагревателем в окружающую среду конвекцией.
Количество энергии, затрачиваемой на контактный нагрев полимерного полотна за единицу времени, определяется по формуле:
Qм = m · C · (Тк – То) · n, кДж/час |
(11.3) |
где m – масса полимерного материала, нагреваемого за один цикл, кг; C – удельная массовая теплоемкость материала, кДж/кг·град;
Тк и То – конечная и начальная температуры нагреваемого материала соответственно, К;
n – количество полных рабочих циклов совершаемых в течение часа, при непрерывной работе линии, циклов/час.
Количество энергии, отдаваемой нагревателем в окружающую среду лучеиспусканием, определяется по формуле:
Qл = σ · ε · F · T4, Вт |
(11.4) |
где σ – постоянная Стефана-Больцмана; σ = 5,67 · 10-8 Вт/м2 · К4; ε – степень черноты (излучающая способность) поверхности нагревателя;
61
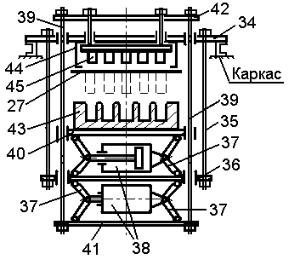
F – площадь поверхности нагревателя, м2;
T – средняя абсолютная температура нагревателя, К.
Количество энергии, отдаваемой нагревателем в окружающую среду конвекцией, определяется по формуле:
Qк = αк · F · (Т – Тв), Вт |
(11.5) |
где F – площадь поверхности нагревателя, м2;
T – средняя абсолютная температура нагревателя, К; Тв – температура окружающего воздуха, К; αк – коэффициент теплоотдачи конвекцией, Вт/м2 · К.
Суммарная мощность электронагревателя Q является в свою очередь исходной величиной для расчета конструктивных параметров электронагревательных элементов 29 или их выбора из числа стандартных; она определяется сложением вычисленных значений Qм , Qл и Qк с учетом следующего коэффициента соотношения величин: 1 кДж/час = 0,278 Вт. Следовательно:
Q = 0,278 · Qм + Qл + Qк, Вт |
(11.6). |
Блок 11 пневмомеханического термоформования, содержащий закрепленную на каркасе секции 1 неподвижную плиту 34 (рис. 11.19), соединенную шпильками 35 с промежуточной плитой 36, на которой попарно сверху и снизу шарнирно закреплены двухзвенные механизмы 37, приводимые в движение от установленных между ними пневмоцилиндров 38. При этом от верхнего пневмоцилиндра осуществляется вертикальное перемещение по колонкам 39 подвижной плиты 40, а от нижнего пневмоцилиндра – траверсы 41, жестко соединенной колонками 39 с подвижной верхней траверсой 42. Применяемая же технологическая оснастка состоит из формы 43, закрепленной на подвижной плите 40, и пневмокамеры 44, установленной на неподвижной плите 34. Внутри пневмокамеры в свою очередь располагается подвижная плита с пуансонами 45, соединенная штоками с верхней траверсой 42.
Рис. 11.19. Конструктивная схема блока пневмомеханического термоформования
В процессе работы разогретое полотно 27 подается в блок 11 на уровне нижней плоскости пневмокамеры 44. Далее от срабатывающего верхнего
62
пневмоцилиндра 38 разгибающимися двухзвенными механизмами 37 плита 40 с формой 43 перемещается вверх и, герметично смыкаясь с пневмокамерой 44, зажимает по периметру формуемое полотно 27. Затем от срабатывающего нижнего пневмоцилиндра 38 опускается траверса 42 и перемещающимся вместе с ней пуансонами 45 вначале производится предварительная вытяжка материала, а затем подаваемым в пневмокамеру сжатым воздухом формуемый материал окончательно прижимается к поверхности формы 43 и, охлаждаясь от нее, оформляется в изделия (стаканы). Форма при этом постоянно охлаждается циркулирующей по ее каналам проточной водой. После охлаждения стаканов в обратной последовательности действий форма раскрывается и цикл повторяется.
Усилие, обеспечивающее смыкания формы и пневмокамеры (усилие запирания Рз), должно быть несколько большим усилия (Рф), создаваемого в процессе формования в пневмокамере сжатым воздухом, то есть
Рз ≥ Рф = р · Fф, Н |
(11.7) |
где р – удельное давление превмоформования, МПа;
Fф – площадь полости формы в плоскости разъема, мм2.
Проектным усилием запирания определяется механическая прочность конструктивных элементов блока формования и усилие, развиваемое пневмоцилиндром 38. Вычисляется проектное усилие запирания по формуле:
Рз = k · pm · Fm, Н |
(11.8) |
где pm – максимальное удельное давление пневмоформования, МПа;
Fm – максимальная проектная площадь полости формы в плоскости разъема, мм2;
k – коэффициент запаса усилия запирания; принимается k = 1,2 – 1,3.
Блок 16 укупоривания тары, содержащий закрепленную на каркасе секции неподвижную плиту 46 (рис. 11.20), на которой попарно сверху и снизу шарнирно закреплены двухзвенные механизмы 47, приводимые в движение от установленных между ними пневмоцилиндров 48. При этом от верхнего пневмоцилиндра осуществляется вертикальное перемещение по колонкам 49 подвижной плиты 50, а от нижнего пневмоцилиндра – траверсы 51, жестко соединенной колонками 49 с подвижной верхней плитой 52. Применяемая же в нем технологическая оснастка состоит из плоского контактного электронагревателя 53, закрепленного через тарельчатые пружины на верхней плите 52, и импульсного нагревателя 54, располагающегося на рабочей плоскости охладителя 55, установленного на подвижной плите 50. Нагреватель импульсный содержит в свою очередь закрепленный на тепло- и электроизолирующей плоской подкладке нагревательный элемент сопротивления, представляющий собой рамку с контуром свариваемых швов, покрытую по рабочей поверхности фторопластовой пленкой. В процессе работы линии полотно 27 с отформованными и заполненными стаканами накрывается покровной пленкой 56 и подается в блок на укупоривание, которое производится встречным перемещением плит 50 и 52 разгибающимися двухзвенными механизмами 47 от срабатывающих пневмоцилиндров 48. При этом нагреватели 53 и 54 в конце хода смыкаются, прижимают по контуру
63
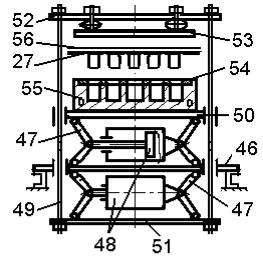
сварки покровную пленку к фланцам стаканов, нагревают в зоне контакта материалы до пластичного состояния и они герметично свариваются между собой. Для соединения разнородных материалов, например, полистирольных стаканов с покровной пленкой из алюминиевой фольги, сопрягающаяся поверхность последней покрывается термоклеем. В процессе работы электронагреватель 53 постоянно нагрет до температуры сварки, а нагреватель импульсный 54 кратковременно нагревается только при сварке, обеспечивая (при необходимости) дополнительный нагрев обычно более толстого термоформуемого материала. Укупориваемые стаканы во время сварки располагаются в гнездах охлаждаемого проточной водой охладителя 55, предохраняющего их от нагрева. После истечения заданного времени сварки нагреватель импульсный выключается, механизмы блока возвращаются в исходное положение, полотно 27 с укупоренными стаканами перемещается на шаг и цикл повторяется.
Рис. 11.20. Конструктивная схема блока укупоривания тары Усилие, требующееся для сжатия нагревателями свариваемых
материалов, определяется по формуле: |
|
Рпр = qпр · Fш, Н |
(11.9) |
где qпр – удельное давление в зоне сварки, МПа;
Fш – суммарная площадь свариваемых швов, мм2.
Установка вычисленного усилия в блоке 16 осуществляется соответствующим предварительным поджатием тарельчатых пружин, располагающихся между плитой 52 и электронагревателем 53.
Блок 17 отделения готовых упаковок от полотна, содержащий закрепленную на каркасе секции верхнюю плиту 57 (рис.11.21) и подвижную плиту 58, перемещающуюся по колонкам 59, соединяющим плиту 57 с траверсой 60, на которой шарнирно закреплены двухзвенные механизмы 61, шарнирно связанные с плитой 58 и приводимые в движение от установленного между ними блока пневмоцилиндров 62. При этом верхняя плита 63 штампа вырубного, несущая пуансоны с подпружиненным прижимом, неподвижно закреплена на плите 57, а нижняя плита 64 штампа, содержащая вырубную матрицу и направляющие колонки 65, закреплена через кронштейны 66 на подвижной плите 58 блока. В пространстве же между кронштейнами 66
64
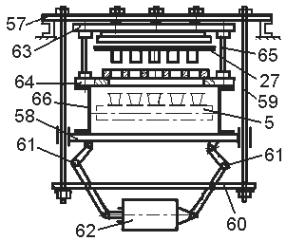
располагается транспортер 5 линии, выводящий отделенные упаковки из машины.
Рис. 11.21. Конструктивная схема блока отделения готовых упаковок
В процессе работы линии шаговым перемещением полотна 27 укупоренные стаканы подаются в блок на уровне нижней плоскости прижима штампа. Далее разгибающимися двухзвенными механизмами 61, от срабатывающего блока пневмоцилиндров 62, подвижная плита 58 перемещается вверх вместе с нижней частью штампа. При этом в конце хода полотно зажимается между матрицей и прижимом штампа, а затем пуансоны врезаются в материал и отделяют упаковки от полотна по контуру сопрягающихся окон матрицы. Далее отделенные упаковочные единицы падают через окна матрицы на транспортер 5, плита 58 возвращается в исходное положение и цикл повторяется.
Вертикальное усилие Рв, которое должен создавать привод 62 блока 17 при вырубке в штампе упаковочных единиц из полотна, определяется по формуле:
Рв = К · (Рр + Рпрж + G), Н |
(11.10) |
где К – коэффициент запаса усилия привода; К = 1,2 – 1,3; Рр – технологическое усилие разделительной операции, Н;
Рпрж – усилие, создаваемое прижимом штампа в момент вырубки, Н; G – вес вертикально перемещающихся частей штампа и блока 17, Н.
Технологическое усилие Рр разделительной операции определяется по формуле:
Рр = k · L · δ · σср, Н |
(11.11) |
Усилие Рпрж, создаваемое прижимом штампа в момент вырубки, |
|
определяется по формуле: |
|
Рпрж = L · δ · qпрж, Н |
(11.12) |
где в данных формулах:
L – общий периметр контура вырубки (отрезки), мм;
δ – суммарная толщина формуемого и покровного полотна, мм;
k – коэффициент, учитывающий допустимое притупление режущих кромок пуансона и матрицы, отклонения оптимального зазора и другие факторы; принимается k = 1,25;
65
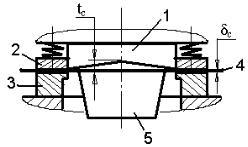
σср – сопротивление материала резанию, МПа;
qпрж – удельное давление прижатия материала, МПа.
Технологическое усилие разделительной операции можно существенно уменьшать за счет выполнения на пуансоне режущих кромок со скосами на величину tc (рис. 11.22).
Рис. 11.22. Схема штампа со скосами на пуансоне: 1 – пуансон; 2- прижим; 3 – матрица; 4 – упаковочное полотно; 5 – отделяемая упаковочная единица.
Экспериментально установлено, что при катете tc скоса соизмеримом с толщиной разделяемого материала δс, требуемое усилие Ртр разделительной операции составляет: Ртр = 0,6 · Рр. Если же tc > 2δс, то Ртр = 0,4 · Рр.
Транспортная система линии, состоящая из кинематически связанных с общим приводом (рис. 11.17) цепного транспортера 4 шагового перемещения упаковочного полотна, ленточного транспортера 5 вывода готовых упаковок из машины, а также устройства 14, обеспечивающего наматывание на вращающуюся катушку отходов упаковочного полотна 15. При этом транспортер 4 шагового перемещения упаковочного полотна содержит установленные на концах линии натяжной 67 и приводной 68 валы (рис.11.23) со звездочками 69, на которых натянуты две параллельные бесконечные пластинчатые цепи 70 с зажимами 71, движущиеся вдоль линии в профильных направляющих 72. Шаговое же движение транспортера осуществляется поворотом приводного вала 68 на полный оборот от обгонной муфты 73, связанной зубчатой передачей с выдвигаемой рейкой-штоком приводного пневмоцилиндра 74. При этом точное позиционирование вала осуществляется путем западания в выемку на диске 75 ролика, установленного на конце штока поджимающего пневмоцилиндра 76. Для ручного привода транспортера на конце валов 67 и 68 закреплены штурвалы 77. От приводного вала 68 движение передается также через цепную передачу 78 на приводной барабан ленточного транспортера 5, выводящего готовые упаковки из машины, и через цепную передачу 79 на вал 80 устройства 14, обеспечивающего наматывание отходов упаковочного полотна на вращающуюся катушку 81, связанную с валом 80 через фрикционную муфту 82. В начале цикла по команде системы управления пневмоцлиндр 76 втягивает шток и выводит ролик из выемки диска 75, расфиксируя тем самым вал 68. Далее срабатывает пневмоцилиндр 74 и от его выдвигающейся рейки-штока через зубчатое зацепление вместе с обгонной муфтой 73 на полный оборот проворачивается вал 68 со звездочками 69, синхронно протягивающими цепи 70 на заданный шаг вместе с закрепленным в их зажимах 71 термоформуемым полотном. Одновременно на шаг перемещается лента транспортера 5, выносящего готовые упаковки из машины,
66
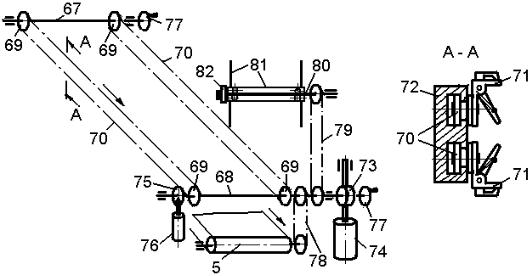
и вращается катушка 81, наматывающая на себя отходы упаковочного полотна, освобождающегося из самораскрывающихся на звездочках зажимов 71.
Рис. 11.23. Кинематическая схема транспортной системы линии
Во время вращения вала 68 выдвигающимся штоком пневмоцилиндра 76 ролик поджимается к цилиндрической поверхности диска 75 и катится по ней, а
вконце проворота вала западает в выемку диска и с высокой точностью фиксирует перемещение транспортера на заданный шаг. Затем на всех позициях линии исполнительными устройствами выполняются соответствующие технологические операции. В это же время пневмоцилиндром 74 в исходное положение возвращается рейка-шток и находящийся с ней в зацеплении свободно вращающийся в обратную сторону корпус обгонной муфты 73 и далее цикл повторяется.
Данная линия может работать с производительностью от 15 до 30 циклов
вминуту в зависимости от толщины термоформуемого полотна и обеспечивает упаковывание пастообразной продукции в полимерную тару, формуемую на рулонном материале шириной до 400 мм и толщиной от 0,14 до 1 мм. В частности, в приведенном исполнении упаковывание осуществляется одновременно в пять формуемых в одном ряду полистирольных стаканов прямоугольной формы размерами 105 х 62 х 40 мм порциями по 0,25 кг с производительностью 20 циклов в минуту. Потребляемая мощность составляет 7 КВт. Габаритные размеры линии: длина – 3800 мм; ширина – 850 мм; высота
– 1700 мм. Масса линии – 1200 кг. Ее разработчиком и изготовителем является ОАО «Гомельский техноприбор» (Беларусь).
Формовочно-упаковочные автоматические линии изготовляются также в конструктивных исполнениях, обеспечивающих вакуумирование внутренней полости упаковки и, при необходимости, ее заполнение модифицированной газовой средой (МГС), благодаря чему существенно увеличиваются сроки хранения упаковываемой продукции. Для этого в блоке укупоривания тары (рис. 11.20) плоский контактный электронагреватель 53 размещается внутри герметизирующей камеры (не показана), сопрягающейся своим нижним торцом с термоформуемым полотном 27 и соединенной трубопроводом с вакуумным насосом и баллоном с МГС. В процессе укупоривания поднимающейся плитой
67
50 через охладитель 55 и импульсный нагреватель 54 полотно 27 прижимается по периметру к торцу этой камеры и герметизирует ее. Далее камера соединяется с вакуумным насосом, удаляющим из нее и тары воздух, а затем через открывающийся пневмоклапан ее рабочая полость и внутренняя полость упаковок заполняются из баллона МГС. В это же время опускающимся электронагревателем 53 покровная пленка 56 прижимается по контуру сварки к фланцам стаканов и в процессе совместного нагрева герметично приваривается (приклеивается) к ним контактирующей поверхностью. После этого баллон закрывается, герметизирующая камера заполняется атмосферным воздухом, все механизмы блока укупоривания тары возвращаются в исходное положение и цикл повторяется.
Такие формовочно-упаковочные автоматические линии производятся и поставляются во многие страны, например, фирмой «WEBOMATIC» (Германия).
Формовочно-упаковочные автоматические линии широко применяются и для упаковывания разнообразных малогабаритных штучных изделий (портмоне, зубных щеток, одноразовых шприцов, ампул, таблеток, карманных фонариков, ножей, фенов и т. д.) в так называемую блистер-упаковку. Блистерупаковка (англ. blister – прозрачный колпак, купол) состоит из сохраняющего форму термоформуемого полимерного футляра, повторяющего в общих чертах конфигурацию упаковываемых изделий, который после укладки в него продукции герметично укупоривается привариваемой (приклеиваемой) к отбортовке крышкой (платинкой), выполняемой из пленки, алюминиевой фольги с термолаковым покрытием, а также ламинированной бумаги или картона. В таких футлярах часто содержатся конструктивные элементы, повышающие их жесткость, а также обеспечивающие дополнительную фиксацию и амортизацию упакованных изделий.
Известными в мире поставщиками широкого модельного ряда формовочно-упаковочных линии, предназначенных для блистер-упаковки разнообразных изделий, являются, например, фирмы «BOSCH» и «MULTIVAC» (Германия). В Беларуси автоматические формовочноупаковочные линии, обеспечивающие многорядную блистер-упаковку одноразовых шприцев в комплекте с иглами, серийно выпускались РУП «Гомельский завод станочных узлов» (Беларусь) по конструкторской документации, разработанной Санкт-Петербургским НПО «Прогресс» (Россия). Термоформуемым материалом в этой блистер-упаковке является полиэтиленполиамидная рулонная пленка шириной 420 мм, а укупоривающие платинки выполняются из ламинированной полиэтиленовой пленкой рулонной бумаги.
Для поштучного упаковывания таблеток, драже, капсул и других аналогичных изделий в групповую ячеистую блистер-упаковку созданы и широко применяются вертикальные роторные формовочно-упаковочные автоматы, работающие с двух рулонов. В этих автоматах рулон 1 (рис. 11.24) термоформуемого ленточного материала устанавливается на оправке 2 одного механизма размотки, а рулон 3 покровного ленточного материала – на оправке 4 второго механизма размотки. Далее ленты этих рулонов через систему роликов механизмов амортизации и натяжения ленты (не показаны) сводятся и
68
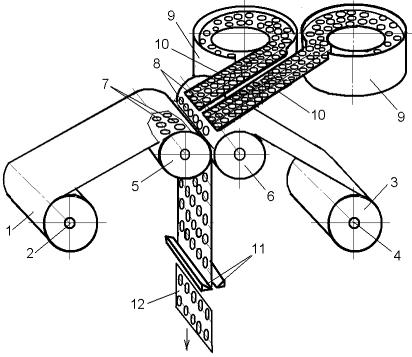
совместно подаются в роторное устройство, состоящее из пары сопрягающихся и синхронно вращающихся формующе-сваривающих валков 5 и 6.
Рис. 11.24. Функциональная схема роторного блистер-упаковочного автомата
На поверхности же этих валков, нагреваемых электрическим током до температуры термоформования и сваривания протягиваемых ими упаковочных лент, содержатся углубления (ячейки) 7, которые по форме и шагу адекватны расположению упаковываемых изделий в формируемой групповой ячеистой блистер-упаковке. В процессе работы автомата упаковываемые изделия (таблетки) 8 подаются из вибробункерных питателей 9 по направляющим лоткам 10 рядами и с заданным шагом между сходящимися на валках 5 и 6 лентами термоформуемого и покровного упаковочного материала в момент схождения в этой зоне ячеек 7 валков. Далее таблетки вместе с протягиваемыми лентами проходят между сопрягающимися поверхностями этих синхронно вращающихся валков, располагаясь при этом внутри их ячеек и создавая давление на разогретую до пластичного состояния от валка 5 термоформуемую ленту, обеспечивая тем самым ее вытяжку с формированием ячеек адекватной формы. Одновременно с этим вторым разогретым валком 6 покровная лента прижимается к контактирующей поверхности термоформуемой ленты и герметично соединяется с ней вокруг таблеток, активирующимся термоклеевым покрытием. После этого соединенные ленты вместе с упакованными таблетками выводятся из роторного устройства и, непрерывно перемещаясь между лезвиями периодически срабатывающих ножниц 11, разрезаются ими на отдельные групповые блистер-упаковки 12, содержащие в своих ячейках необходимое количество таблеток. Подобная функциональная схема реализована, например, в изготовляемых и поставляемых фирмой «NOACK» (Германия) вертикальных роторных формовочно-упаковочных автоматах модели «Stripmatic TN220».
Приведенные формовочно-упаковочные линии, роторные и другие высокопроизводительные автоматы характеризуются конструктивно сложным
69
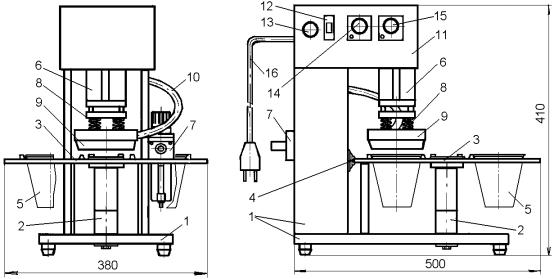
исполнением и соответственно относительно высокой стоимостью. Поэтому они эффективны при упаковывании больших объемов продукции, производимой в условиях крупносерийного и массового производства.
В условиях мелкосерийного производства при упаковывании небольших объемов продукции в готовые полимерные стаканы, поставляемые специализированными предприятиями-изготовителями, для их герметичного укупоривания платинками можно, например, применять полуавтоматическое термоукупоривающее устройство модели АДНК 19У12, которое создано и серийно изготовляется ООО «ПРОФИТЭКС» (Россия). Данное устройство обеспечивает герметичное термоприклеивание к отбортовке стаканов, изготовляемых из полистирола, полипропилена и других термопластов, укупоривающих платинок, выполняемых из алюминиевой фольги или валкилида.
Рис. 11.25. Общий вид полуавтоматического термоукупоривающего устройства модели АДНК 19У12
На основании 1 (рис. 11.25) этого устройства вертикально крепится ось 2, несущая карусельный стол 3. В карусельном же столе, циклически поворачивающемся на 90о и фиксируемом при этом механизмом 4 сблокированным с кнопкой включения, содержится четыре симметрично расположенных отверстия, в которые вставляются повисающие на отбортовке укупориваемые стаканы 5. В свою очередь над карусельным столом соосно с укупорочной позицией к основанию устройства вертикально прикреплен пневмоцилиндр 6, рабочие полости которого через распределитель и блок подготовки воздуха 7 соединяются с питающей магистралью сжатого воздуха. На штоке же этого пневмоцилиндра через блок амортизирующих пружин сжатия 8 крепится контактный электронагреватель 9, соединяющийся кабелем 10 с пультом управления 11, содержащим на своей лицевой панели выключатель 12, лампочку 13 световой индикации наличия напряжения «Сеть», а также реле времени (таймер) 14 и регулятор 15, поддерживающий заданную температуру на контактном электронагревателе 9. К источнику питания в свою очередь пульт управления присоединяется сетевым кабелем 16.
В процессе работы наполненный стакан устанавливается оператором в отверстие первой позиции карусельного стола и накрывается сверху платикой.
70