
[SHipinsky_V.G.]_Oborudovanie_i_osnastka_upakovoch2(z-lib.org)
.pdf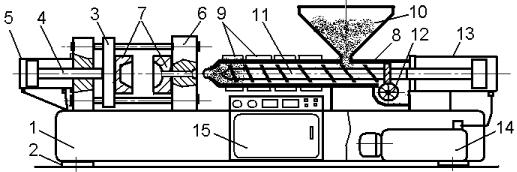
В процессе работы машины гранулированный материал из бункера 10 поступает самотеком в материальный цилиндр 8, где захватывается вращающимся червяком 11 и транспортируется им в переднюю часть цилиндра одновременно нагреваясь от его стенок и трения с червяком до вязкотекучего состояния. При этом червяк отходит назад, а порция пластифицированного материала накапливается перед ним.
Рис.13.1. Схема горизонтальной одночервячной литьевой машины
Далее поступательным движением червяка 11 вперед от штока гидроцилиндра 13 материал впрыскивается через сопло цилиндра в сомкнутую литьевую форму 7, закрепленную на плитах 3 и 6 машины. После охлаждения изделия водой, циркулирующей по каналам формы 7, подвижная плита 3 отводится штоком 4 гидроцилиндра 5 от неподвижной, готовое изделие удаляется из размыкающейся формы 7 и цикл повторяется.
Более подробно рассмотрим устройство и принцип действия пневматического поршневого литьевого термопластавтомата модели АЛТ-5,
применяемого для изготовления элементов упаковки и других деталей объемом до 6 см3 методом литья под давлением из термопластичных материалов. Он состоит из таких основных составных частей (рис.13.2), как станина, дозатор, литьевая головка, пневмопрессовое устройство, механизм запирания прессформы (инструмента), а также пневмосистемы и электрооборудования с пультом управления.
Станина обеспечивает крепление всех составных частей термопластавтомата
исостоит из сварного каркаса 1, регулируемых опор 2, стола 3, полых вертикальных стоек 4, перекладины 5, отводящего лотка 6, а также защитных ограждений 7 с шарнирной дверцей 8.
Дозатор обеспечивает, в свою очередь, порционную подачу гранулированного материала в литьевую головку. Он состоит из бункера 9 со смотровым окном 10, соединяющегося через отверстие с цилиндрическим каналом 11 корпуса 12 (рис.13.3), где установлен поршень 13 с втулкой 14 регулирования его хода, соединённый штоком 15 с тягой 16 качающейся скобы 17, взаимодействующей с кулачком 18 на штоке 19 и преобразующей вертикальное движение штока с кулачком 18 в горизонтальное перемещение поршня 13. В зоне сопряжения канала 11 с загрузочным окном корпуса 20 литьевой головки установлены направляющий лоток 21, а также шторка 22 и перегородка 23, частично перекрывающие это окно и препятствующие самопроизвольному перетеканию гранулированного материала из бункера 9 в полость корпуса 20.
101
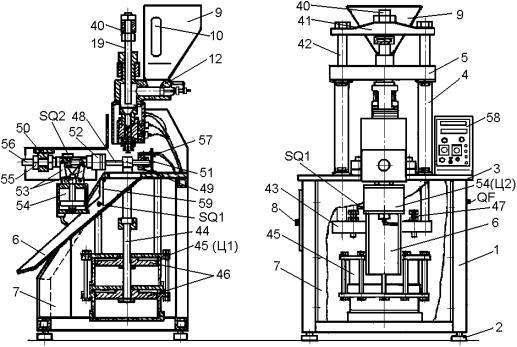
Рис.13.2. Термопластавтомат литьевой модели АЛТ-5
В литьевой головке осуществляется пластификация гранулированного полимерного материала. Она состоит из закреплённого в перекладине 5 станины корпуса 20 (рис.13.3), в котором по направляющей втулке 24 перемещается шток 19 с плунжером 25 пневмопрессового устройства. В нижней части корпуса 20 соосно плунжеру 25 установлены соединенные между собой воронка 26 и инжекционный цилиндр 27, при этом воронка 26 опирается на цилиндрическую пружину 28, располагающуюся в направляющей втулке 29, закреплённой в корпусе 20 фиксирующими винтами 30 и несущей защитный кожух 31. В нижней полости инжекционного цилиндра 27 установлена торпеда 32 с четырьмя симметрично расположенными на наружной поверхности винтовыми канавками, обеспечивающая равномерный нагрев и перемешивание пластифицированного материала при впрыске в пресс-форму. Торпеда закрепляется в цилиндре вворачиваемой снизу втулкой 33, несущей сопло 34, герметично сопрягающееся с ней по коническому притёртому пояску от запирающего усилия пружины 35, поджатой гайкой 36. На инжекционном цилиндре установлены также два электронагревательных элемента сопротивления ЕН1, ЕН2, соединённых через закрытую кожухом 37 клеммную колодку 38 с кабелем питания 39 и два датчика ВК1, ВК2 контроля температуры нагрева цилиндра.
Пневмопрессовое устройство обеспечивает подачу пластифицированного материала под давлением из литьевой головки в пресс-форму и включает в себя шток 19 с плунжером 25, соединённый через винтовой захват 40 с траверсой 41 (рис.13.2), закреплённой на двух вертикальных колонках 42, проходящих через полые стойки 4 станины и соединённых через нижнюю траверсу 43 со штоком 44 пневмоцилиндра 45, несущим поршни 46, расположенные в двух последовательных пневмокамерах. При этом на нижней траверсе 43 содержатся два регулируемых упора 47 ограничения вертикального хода штока пневмоцилиндра 45 и связанного с ним плунжера 25.
102
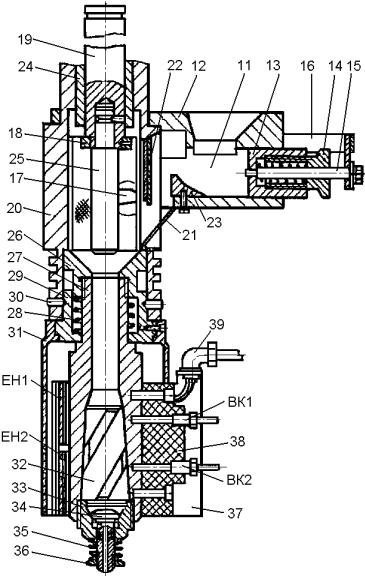
Рис.13.3. Литьевая головка термопластавтомата модели АЛТ-5
Механизмом запирания (закрытия) пресс-формы (инструмента) осуществляется сведение полуформ и удержание пресс-формы в закрытом положении
впроцессе подачи в неё под давлением пластифицированного материала, а также раскрытие пресс-формы для удаления из неё отлитого изделия. Состоит этот механизм из двух горизонтально расположенных направляющих колонок 48 (рис.13.2), закреплённых кронштейнами 49 на столе 3 , и установленных на них трёх плит – неподвижных передней 50 и задней 51, а также подвижной промежуточной 52, перемещающейся по колонкам шарнирно-рычажной системой 53 от пневмоцилиндра 54. Для регулирования расстояния между плитами 51 и 52, по закрытой высоте, закрепляемой на них пресс-формы, в передней плите 50 механизма располагается фиксируемая гайками 55 винтовая опора 56 с датчиком SQ2 контроля закрытия формы.
Пневмосистема обеспечивает подачу сжатого воздуха в силовые пневмоцилиндры 45(Ц1) и 54(Ц2) термопластавтомата по управляющим командам с пульта управления и включает в себя соединённые гибкими трубками в схему (рис.13.4) блок подготовки воздуха Б1; распределители Р1 и Р2; дроссели Др1, Др2 и ДрЗ; пневмоглушители Г1 – Г4; пневмоцилиндры Ц1 и Ц2; а также сопло 57 (рис.13.2) обдува пресс-формы.
103
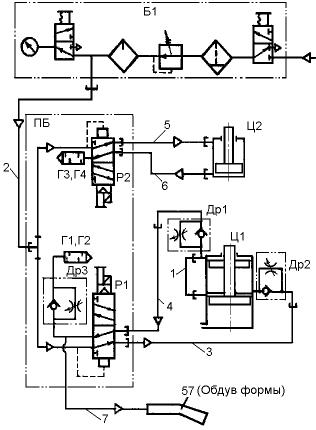
Рис.13.4. Схема пневматическая принципиальная термопластавтомата модели АЛТ-5
Электрооборудование обеспечивает работу термопластавтомата в режимах "НАЛАДКА", "ЦИКЛ", "АВТОМАТ" и содержит пульт 58, на лицевой панели которого располагаются следующие органы управления (рис.13.5):
•регуляторы температуры Р1и Р2 электронагревателей ЕН1 и ЕН2;
•кнопка SB1 включения питания в схему электронагревателей ЕН1 и ЕН2;
•световой индикатор HL2 подачи питания в схему электронагревателей ЕН1 и ЕН2;
•реле КТ1, обеспечивающее установку и выдержку времени впрыска пластифицированного материала в пресс-форму;
•реле КТ2, обеспечивающее установку и выдержку времени охлаждения отливки в пресс-форме;
•тумблер SA1 включения питания в электросхему и сетевой индикатор HL1 наличия напряжения питания в схеме электрооборудования;
•красная кнопка SB2 - "ОБЩИЙ СТОП";
•тумблер SA2 включения механизма впрыска материала в режиме "НАЛАДКА";
•тумблер SA3 включения механизма смыкания пресс-формы в режиме "НАЛАДКА";
•тумблер SA5 включения одного из режимов управления: "НАЛАДКА" или "РАБОТА";
•тумблер SA4 включения режимов работы "ЦИКЛ" или "АВТОМАТ";
•кнопка SB3 поциклового включения в работу; при нажатии этой кнопки автоматически выполняется один законченный рабочий цикл с остановкой работы до следующего нажатия кнопки.
104
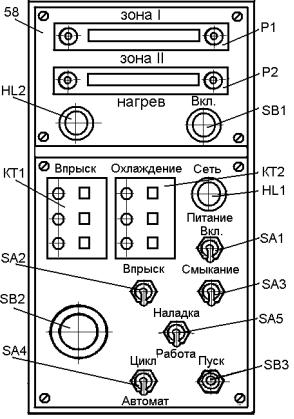
Всё электрооборудование размещается внутри пульта 58 и на исполнительных механизмах термопластавтомата и соединено между собой электромонтажом в соответствии со схемой электрической принципиальной
Рис.13.5. Пульт управления автомата модели АЛТ-5
Работа термопластавтомата осуществляется следующим образом. После загрузки в бункер 9 гранулированного материала, тумблером SA1 включается электропитание, а вентилем на блоке подготовки воздуха Б1 подача в пневмосистему сжатого воздуха. Далее на регуляторах температуры Р1 и Р2 устанавливается требуемая температура нагрева материала, нажатием кнопки SB1 подаётся напряжение питания на электронагреватели ЕН1, ЕН2 и после разогрева ими литьевой головки до заданной температуры термопластавтомат включается нажатием кнопки SB3 "ПУСК" в работу по следующему циклу:
Срабатывает пневмоцилиндр 54 (Ц2) и выдвижением его штока через шарнирно-рычажную систему 53 производится запирание пресс-формы и включение датчика SQ2 контроля закрытия формы.
По сигналу датчика SQ2 включается реле времени КТ1 и распределитель Р1, подающий сжатый воздух в пневмоцилиндр 45 (Ц1), которым при втягивании штока 44 через систему передачи движения плунжер 25 вводится в инжекционный цилиндр 27, заполненный пластифицированным материалом. Здесь материал сжимается плунжером в закрытом объёме и цилиндр 27 начинает опускаться вниз вместе с плунжером, сжимая через воронку 26 пружину 28 до тех пор, пока сопло 34, прижавшись рабочим концом к литниковому каналу пресс-формы, преодолевая усилие пружины 35, не вдавится внутрь цилиндра 27 до открытия в нём канала, по которому пластифицированный материал, обтекая торпеду 32, впрыскивается из цилиндра в пресс-форму, заполняет её и выдерживается под давлением в течение времени, установленного на реле КТ1.
105
При движении плунжера 25 вниз, установленный на штоке 19 кулачок 18 нажимает на нижнюю планку качающейся скобы 17 и, увлекая её за собой, через систему передачи движения отводит поршень 13 дозатора в исходное положение, при этом освобождающаяся полость канала 11 заполняется гранулированным материалом, поступающим из сопрягающегося бункера 9.
По истечении времени впрыска срабатывает реле КТ1, включая питание распределителя Р1, переключающего пневмоцилиндр Ц1 на обратный ход. При этом плунжер 25 перемещается вверх, освободившаяся от нагрузки пружина 28 поднимает инжекционный цилиндр 27 в исходное положение, а приподнявшееся над формой сопло 34 под действием пружины 35 садится по коническому пояску на сопрягающуюся поверхность втулки 33, герметично закрывая канал впрыска. Одновременно кулачок 18 нажимает на верхнюю планку качающейся скобы 17 и, увлекая её за собой вверх, через тягу 16 перемещает поршень 13 дозатора к загрузочному окну корпуса 20, засыпая через него и воронку 26 в открывшийся инжекционный цилиндр 27 новую порцию гранулированного материала. А сбрасываемый из пневмоцилиндра Ц1 сжатый воздух через сопло 57 направляется на охлаждающий обдув пресс-формы.
После истечения времени, необходимого для охлаждения пресс-формы с отливкой и пластикации материала в цилиндре 27, срабатывает реле времени КТ2 и, выключая реле KV2 и распределитель Р2, переключает пневмоцилиндр Ц2 на обратный ход. При этом пресс-форма открывается, отливка выталкивателями удаляется из неё, падает на отводящий наклонный лоток 6 и, перемещаясь по нему, отклоняет перекрывающую канал шторку 59 и падает в тару, а отклонившаяся шторка воздействует на бесконтактный датчик SQ1 контроля удаления детали, включающий реле KV2, и цикл снова повторяется в автоматическом режиме.
Остановка термопластавтомата осуществляется нажатием кнопки SB2 "ОБЩИЙ СТОП".
Техническая характеристика термопластавтомата модели АЛТ-5 Число сухих циклов, мин -1, не менее ………………………………………30 Расчётный объём впрыска за цикл, см3, не более …………………………...6 Давление литья, МПа, не более ……………………………………………120 Усилие запирания инструмента, кН, не более ……………………………..63 Ход подвижной плиты узла запирания при максимальной высоте инструмента, мм, не более ..………………………………………………...80
Высота устанавливаемого инструмента (пресс-формы), мм …………. 80 – 110 Расстояние между колонками в свету узла запирания, мм ………………..110
Температура в зоне пластикации, оС, |
не более..………………… 300 |
Питание: |
|
переменный ток: напряжением, В.................... |
………………………….220 |
частотой, Гц ............................... |
………………………….50 |
сжатый воздух давлением, МПа, ................ ……………………… 0,4 – 0,6 Потребляемая мощность, кВт, не более……………………………………. 1,0
в том числе мощность электронагревателей |
... ………………………… 0,7 |
Габаритные размеры, мм, не более |
|
длина ................................................................. |
………………………… 770 |
ширина .......................................................... |
……………………………720 |
106
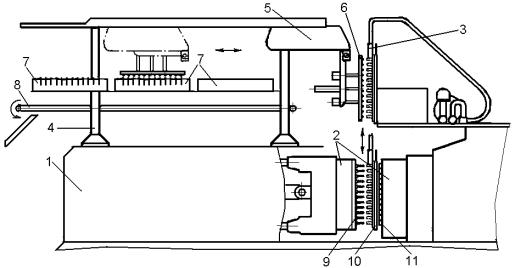
высота.............................................................. |
………………………… 1600 |
Масса, кг, не более................................................ |
…………………………. 220 |
Широко применяемым специализированным технологическим оборудованием являются, например комплексы, обеспечивающие изготовление из термопластов литьем под давлением преформ – ампулообразных заготовок, предназначенных для получения из них раздувной тары. Из большой группы такого оборудования, отличающегося разнообразными вариантами исполнения, рассмотрим устройство и принцип действие комплекса, поставляемого швейцарской фирмой «NETSTAL-MASCHINEN AG». В стандартную комплектацию этого комплекса входят (рис.13.6): сушилка гранулированного сырья (не показана); термопластавтомат 1 с разделенными устройствами пластификации и впрыска; установленная в нем модульная многоместная горячеканальная литьевая форма 2; механизм 3 вертикального перемещения модуля матриц литьевой формы и холодильный агрегат 4. В каркасе же холодильного агрегата, установленном на термопластавтомате, располагаются: робот 5, оснащенный групповым захватом 6 преформ; три станции 7 охлаждения преформ и ленточный выносящий транспортер 8.
Рис.13.6. Функциональная схема комплекса для изготовления преформ швейцарской фирмы «NETSTAL-MASCHINEN AG»
Термопластавтомат 1 содержит устройство пластификации, оснащенное специальным червяком, обеспечивающим более качественное перемешивание расплава в процессе его пластикации с достижением высокой степени однородности, что оказывает существенное влияние на качество изготовляемых преформ. При этом в образующемся расплаве полиэтилентерефталата значительно снижается уровень ацетилальдегида, что крайне важно в изготовлении преформ, предназначенных для раздува бутылок под минеральные воды. Жесткая же конструкция рычажного пятизвенного механизма узла запирания с массивными параллельными плитами обеспечивает высокоточное позиционирование литьевой формы, сокращает время ее смыкания-размыкания и снижает износ, увеличивая тем самым срок службы формы до 4 миллионов циклов. Применяемая система управления на базе микропроцессорного контроллера с замкнутыми обратными связями по всем технологическим параметрам цикла (скорость вращения червяка,
107
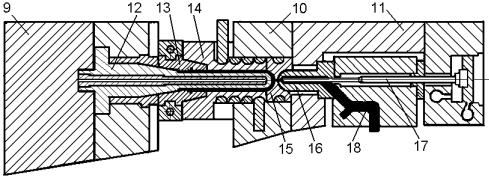
температура пластикации, скорость впрыска, давление выдержки и т. д.), обеспечивает высокую стабильность технологических режимов и, следовательно, идентичность изготовляемых преформ по массе, остаточным напряжениям в материале и другим характеристикам, определяющим их качество.
Установленная в термопластавтомате 48-ми местная горячеканальная литьевая форма 2 состоит в свою очередь из трех сопрягающихся частей: модуля 9 стержней, модуля 10 матриц и модуля 11 горячих каналов, при этом каждая литьевое гнездо в этой форме собирается из отдельных однотипных деталей, в том числе (рис.13.7): стержня 12, формирующего внутреннюю полость преформы; вставок 13 и 14 матрицы, оформляющих наружную поверхность горловины и корпуса преформы; а также литниковой втулки 15, сопла 16 и иглы 17, обеспечивающих подачу устройством впрыска по каналу 18 расплава материала в рабочую полость гнезда. Таким рациональным конструктивным исполнением обеспечивается быстрая замена деталей в литьевых гнездах без снятия формы с термопластавтомата и ее удобное обслуживание.
Рис.13.7. Конструктивное исполнения литьевых гнезд под преформу в модульной 48-ми местной горячеканальной форме
Размещенные над термопластавтоматом механизм 3 и холодильный агрегата 4 обеспечивают быстрый вертикальный подъем модуля 10 матриц формы и надежный захват роботом 5 из его гнезд изготовленных преформ, а также быструю их передачу в ячейки станции 7 холодильного агрегата. Кроме этого при такой компоновке сокращаются и производственные площади, занимаемые комплексом.
В процессе работы комплекса обработанное в сушилке гранулированное сырье перегружается в бункер термопластавтомата 1. Оттуда оно самотеком поступает к вращающемуся червяку пластикационного устройства, где перемещаясь по материальному цилиндру, расплавляется и перемешивается в однородную массу, поступающую и накапливающуюся в полости устройства впрыска. Далее производится цикловое смыкание литьевой формы 2 пятизвенным механизмом узла запирания и подача устройством впрыска по горячим каналам модуля 11 в полости ее гнезд пластифицированного материала под давлением порядка 150 МПа с выдержкой времени, обеспечивающей охлаждение там преформ до достижения материалом механической прочности. Поле этого механизм впрыска приводится в исходное положение, литниковые каналы в соплах 16 закрываются перемещающимися иглами 17 и одновременно пятизвенным механизмом узла запирания форма
108
размыкается. При этом модулем 9 формы стержни 12 выводятся из полости отлитых преформ, и механизмом 3 ее модуль 10 матриц перемещается в верхнее положение, где позиционируется перед захватом робота 5. Далее робот 5 забирает групповым захватом 6 преформы из матриц модуля 10 и укладывает их в свободные ячейки одной из трех станции 7 холодильного агрегата 4, где они окончательно охлаждаются в течение двух технологических циклов. Одновременно с этим модуль 10 матриц механизмом 3 возвращается в нижнее исходное положение, литьевая форма 2 смыкается пятизвенным механизмом узла запирания и цикл повторяется. В это время полностью охлажденные преформы из очередной станции 7 перегружаются на движущуюся ленту транспортера 8, перемещающую их в накопительный бункер, и далее робот 5 укладывает в нее новую партию изготовленных преформ.
Требуемый цвет и прозрачность изготовляемой раздувной тары закладывается при изготовлении преформ их гранул. Для изготовления ПЭТпреформ можно использовать практически любые марки полиэтилентерефталата, но при этом необходимо подбирать оптимальные температурные режимы на различных участках его пластикации. Главное, чтобы технологическое оборудование, применяемое для изготовления ПЭТпреформ, поддерживало перепады температуры пластикации этого материала в очень узком диапазоне. Несоблюдение же температурных режимов переработки сырья, вызывает недопустимые отклонения в преформах, такие как их коробление, наличие нерасплавленных и газовых включений, помутнение материала и другие. Большие проблемы возникают с использованием преформ, при изготовлении которых к исходному гранулированному материалу добавлялся вторичный ПЭТ (полученный, например, из измельченных утилизированных бутылок), применение которого при изготовлении тары для пищевых продуктов жестко регламентируется правовым законодательством. Однако из-за того что по внешнему виду преформы с добавками вторичного ПЭТ ничем не отличаются от преформ, изготовленных полностью из исходного материала, некоторые производители злоупотребляют добавлением в них вторсырья. Тара же, раздуваемая из таких преформ, имеет низкие механические показатели и часто еще при раздуве лопается и даже расслаивается.
13.1. Производство прессованной пластмассовой тары
Прессование пластмассовых изделий осуществляется при воздействии давления на материал, помещенный непосредственно в нагретую пресс-форму. Таким образом, изготовляют отдельные детали упаковки и тару из различных термопластичных и термореактивных пластмасс. При прессовании изделий из термореактивных материалов они отверждаются в горячей пресс-форме и извлекаются в нагретом состоянии. При прессовании изделий из термопластичных материалов требуется попеременный нагрев (для формования) и охлаждение пресс-формы. К основным способам относят прямое (компрессионное) и литьевое (трансферное) прессования.
При прямом прессовании материал загружают в нагретую до заданной температуры пресс-форму, состоящую из пуансона 1 (рис.13.8а), матрицы 2 и выталкивателя 3, которая установлена на плите 4 пресса. Под воздействием давления Р, создаваемого ползуном пресса на пуансон 1, разогреваемый
109
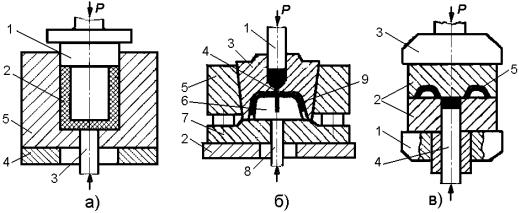
материал растекается по полости формы и отверждается, приобретая конфигурацию изготовляемого изделия 5. Загрузка в пресс-форму предварительно таблетированного материала, вместо порошка или гранул, обеспечивает следующие преимущества: простое и быстрое дозирование; меньшие размеры пресс-формы, так как таблетки имеют большую плотность, чем пресспорошок; выполнение предварительного нагрева таблеток; ускоренное удаление газообразных компонентов из прессуемого изделия; а в итоге – повышение производительности и улучшение физико-механических показателей изготовляемых изделий.
Рис.13.8. Схемы процессов прямого (а) и литьевого (б – в) прессования
Таблетирование, осуществляемое в специальных таблеточных машинах, применяют при изготовлении крупногабаритной прессованной тары и деталей упаковки массой свыше 0,5 кг и с толщиной стенок более 4 мм, а также при использовании волокнистых материалов. Для нагрева таблетированного материала непосредственно перед загрузкой в пресс-форму применяют контактные нагреватели, воздушные термостаты и генераторы ТВЧ.
Полуавтоматические прессы используются для прямого прессования при изготовлении крупногабаритной тары простой формы, а для изготовления небольших изделий массой до 0,2 кг и с толщиной стенки до 4 мм целесообразно применять пресс-автоматы, работающие на порошкообразных или таблетированных материалах. Пресс-автоматы особенно эффективны при изготовлении колпачков, крышек, стаканчиков и других аналогичных изделий. Еще более высокую производительность имеют роторные автоматические линии, состоящие из нескольких синхронно вращающихся роторов, на которых последовательно производится дозирование и таблетирование материала, предварительный подогрев таблеток, компрессионное прессование, съем, механическая обработка и выдача готовых изделий.
Литьевое (трансферное) прессование заключается в предварительном размягчении (пластикации) материала, нагреваемого в камере трансфертного цилиндра или в специальном тигле, и последующем его нагнетании поршнем в закрытую пресс-форму. По применяемому оборудованию и технологии процесса оно занимает промежуточное место между прямым прессованием и литьем под давлением.
Литьевое прессование можно выполнять на универсальных прессах, рабочий поршень 1 (рис.13.8б) которых замыкает установленную на плите 2 пресс-форму, состоящую из матрицы 3 с литниковым каналом 4, обоймы 5,
110