
[SHipinsky_V.G.]_Oborudovanie_i_osnastka_upakovoch2(z-lib.org)
.pdf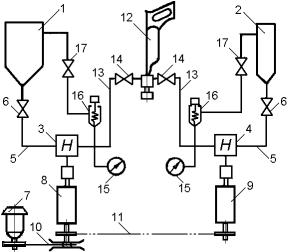
к которым, в частности, относится автомат модели ГМ-985, обеспечивающий изготовление пенопластовых коробок диаметром до 60 мм и высотой до 115 мм с производительностью до 800 штук в час.
14.3. Метод смешения компонентов заливочных компаундов
Методом смешения компонентов заливочных компаундов производятся пенопласты из термореактивных полимеров. Такие композиции применяются для изготовления тары и амортизирующих элементов упаковки сложной конфигурации в формах, а также для заполнения тары с упаковываемым изделием и для напыления пенопластов непосредственно на поверхность изделий с целью их термоизоляции и защиты от механических повреждений при транспортировании.
В частности, при использовании фенолформальдегидных заливочных масс (пен) непрерывное смешение их компонентов и подача в формы осуществляется установками типа УЗФП-1, которые состоят:
из двух емкостей 1 и 2 (рис.14.5) для полимера и катализатора соответственно;
двух дозирующих шестеренчатых насосов 3 и 4, присоединенных к емкостям трубопроводами 5 через пробковые краны 6;
приводного электродвигателя 7, связанного с насосами через универсальные регуляторы скорости 8 и 9, а также клиноременную 10 и цепную 11 передачи вращения;
смесительной головки 12, присоединенной к шестеренчатым насосам трубопроводами 13 через пробковые краны 14;
а также манометров 15, соединенных с емкостями через вентили 16 и рециркуляционные клапаны 17.
Рис.14.5. Функциональная схема заливочной установки модели УЗФП-1
В процессе работы установки фенолформальдегидная композиция и катализатор непрерывно подаются по трубопроводам из емкостей 1 и 2 дозирующими насосами 3 и 4 в смесительную головку 12, где, перемешиваясь между собой в течение 1-2 секунд, вспениваются и далее направляются через выходное сопло головки на заливку. При производстве тары из пенополиуретана применяется аналогичная установка, например, модели УЗП- 1, емкость 1 которой заполняют полиэфирной смесью, содержащей выбранный
121
олигоэфир, вспенивающий агент и другие добавки, вторым же компонентом, размещаемым в ее емкости 2, является изоционат. В процессе работы установки эти компоненты подаются дозирующими насосами 3 и 4 в смесительную головку 12, где при перемешивании вспениваются с образованием пенополиуретана, поступающего затем через выходное сопло головки на заливку.
Тару, амортизирующие элементы упаковки и другие изделия из эластичного или жесткого пенополиуретана изготовляют путем заливки получаемого в установке пеноматериала при комнатной температуре в закрытые герметичные формы, внутренняя поверхность которых предварительно обрабатывается антиадгезионным составом, предотвращающим прилипание к ним формуемых изделий. Сами же формы могут выполняться из металла, древесины, стеклопластика и других конструкционных материалов.
При заливке в таре пенополиуретаном упаковываемого изделия, последнее заворачивается в пленку и подвешивается внутри, например, картонного ящика, вставленного в ограничительную оснастку, предотвращающую его деформацию от давления газов, выходящих из вспененной композиции. Затем свободный объем внутри тары заливается пенополиуретановой композицией и, после ее отверждения, изделие оказывается внутри пенополиуретановой амортизирующей и термоизолирующей оболочки.
Для напыления же пенопластов непосредственно на поверхность изделий с целью их термоизоляции и защиты от механических повреждений можно применять, например, серийно изготовляемую установку модели «Пена-2», содержащую расходную емкость объемом 40 дм3. Она обеспечивает нанесение пенополиуретана на изделия с производительностью 0,6 – 4,0 кг/мин, при соотношении потоков полиэфира и изоционата 1/1 – 1/1,9. Масса этой установки – 200 кг.
14.4. Экструзия листовых упаковочных материалов
Из листовых пеноматериалов, получаемых методом экструзии, для упаковки наиболее часто применяются пенополиэтилен и пенополистирол. В частности, вспененные полиэтиленовые листы получают на обычных экструзионных листовых агрегатах, предназначенных для переработки термопластов. На этом оборудовании изготовляют листы с кажущейся плотностью 400 – 550 кг/м3, шириной 1500 мм и толщиной от 1 до 6 мм. Такие листы затем можно сваривать и формовать, чем определяются широкие возможности их применения для упаковывания.
Для упаковывания продукции применяют также комбинирование пенопластов с другими материалами: бумагой, картоном, фольгой, полимерными пленками. В частности, процесс получения комбинированного листового упаковочного материала, состоящего из внутреннего слоя пенополистирола и двух наружных слоев бумаги, называемого карпеном, осуществляется следующим образом. Полотно бумаги, разматываясь с рулона 1 (рис.14.6), поступает в устройство 2, увлажняющее его внутреннюю поверхность, и далее проходит через дозирующий бункер 3, где на
122
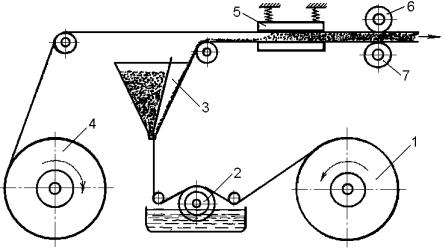
увлажненную поверхность налипает необходимый слой вспенивающихся гранул полистирола.
Рис.14.6. Функциональная схема установки для производства карпена
При дальнейшем продвижении на это полотна накладывается второй наружный слой бумаги, разматывающейся с рулона 4, а затем они совместно продвигаются через устройство 5 двухстороннего нагрева, где под воздействием тепла, получаемого от образующегося пара, происходит вспенивание полистирольных гранул внутреннего слоя и соединение с бумагой. Далее комбинированное трехслойное полотно проходит между двумя продвигающими его калибровочными валками 6 и 7, а затем подается в ножницы, разрезающие полученный материал на мерные листы, или движется на технологическую линию, изготовляющую из этого материала тару, амортизирующие и другие элементы упаковки.
15. ПРОИЗВОДСТВО КРУПНОГАБАРИТНОЙ ПЛАСТМАССОВОЙ ТАРЫ
Крупногабаритную пластмассовую тару (ящики, канистры, фляги, бочки, баки, цистерны, поддоны-резервуары, контейнеры) можно изготовлять литьем под давлением, прессованием, экструзионно-раздувным и центробежным формованием, а также намоткой, ротационным формованием и некоторыми другими способами.
В частности литьем под давлением в серийном производстве обычно изготовляют прочные многооборотные пластмассовые ящики, плоские поддоны и другие аналогичные изделия на специальных литьевых машинах, обеспечивающих максимальный объем впрыска (отливки) от 1 до 40 дм3. Например, одна из самых мощных таких машин модели 26/2500 фирмы «Триульци» (Италия), характеризующаяся максимальным объемом впрыска 32,5 дм3, усилием запирания формы 25,0 МН, установленной мощностью в 900 кВт, имеет габаритные размеры 21,8 х 3,4 х 3,9 м и весит 240 т.
Для прессования же под низким давлением крупногабаритных изделий, например, таких как стеклопластиковые плоские поддоны, выпускаются специальные гидравлические прессы с облегченной рамной или колонной конструкцией станины и индивидуальным приводом, отличающиеся большой
123
площадью стола и подвижной плиты. На столе такого пресса обычно располагается две плиты для нижних полуформ, которые, циклически перемещаясь по направляющим, поочередно занимают рабочую позицию, при этом на его подвижной плите крепится одна верхняя полуформа. Во время прессования изделия в нижней полуформе, расположенной на рабочей позиции, из нижней полуформы, расположенной на второй плите пресса, производится удаление изготовленного изделия и загрузка новой порции материала, а затем плиты с нижними полуформами сменяются на рабочей позиции и цикл повторяется. Тем самым обеспечивается более высокая производительность, и создаются условия для безопасной загрузки и разгрузки пресс-формы. Такой пресс обслуживается с двух сторон одним оператором.
Экструзионно-раздувные агрегаты применяются для изготовления крупногабаритных объемных полых изделий (бочек, барабанов, фляг, канистр) вместимостью до 5000 дм3. Поскольку в таких агрегатах подача заготовок большой массы и длины в раздувную форму должна осуществляться с высокой скоростью, то они обязательно выполняются с поршневым копильником (аккумулятором) расплава, наполнение которого может осуществляться одним или несколькими одновременно работающими экструдерами. Располагаются копильники у них как в материальном цилиндре экструдера между экструзионной головкой и червяком, так и вне материального цилиндра (рис.12.10). Выполняются такие агрегаты, как правило, однопозиционными, поскольку время заполнения копильника пластифицированным материалом из экструдера у них соизмеримо с суммарным временем выполнения всех последующих стадий технологического цикла. Например, такой агрегат модели ВЕКВ-2500 фирмы «Баттенфельд – Фишер» (ФРГ), обеспечивающий изготовление пластмассовой тары максимальным объемом до 2500 дм3, имеет следующие технические характеристики: диаметр червяка экструдера – 140 мм; отношение длины червяка к диаметру – 16; усилие смыкания раздувной формы
– 3250 кН; потребляемая мощность – 330 кВт; его габаритные размеры – 11 х 17,4 х 12,5 м и масса – 108 т.
Намоткой можно изготовлять прочные корпуса крупногабаритной тары, с круглым, овальным, прямоугольным, шестигранным и другими поперечными сечениями (обечайки барабанов, бочек, баков, цистерн, контейнероврезервуаров), а также оболочки с замкнутыми (закрытыми) торцами, близкие, например, к шаровидной или эллипсовидной форме. При этом способе армирующий наполнитель, в виде ленты, нитей, полотна или матов, пропитанный полимерным связующим, наматывают по определенной схеме на вращающуюся оправку, имеющую конфигурацию изготовляемого изделия. Изделия таким образом можно изготовлять сухим, мокрым и комбинированным методами формования.
Сухой метод заключается в том, что армирующий наполнитель на отдельной машине предварительно пропитывается полимерным связующим с его высушиванием, а затем полученный материал наматывается на оправку при формовании изделий. Выделение пропитки в самостоятельную операцию позволяет значительно расширить диапазон применяемых полимерных связующих за счет использования летучих растворителей (толуола, ацетона и других), а также обеспечить более равномерную пропитку им армирующего
124
наполнителя за счет уменьшения вязкости связующего. При этом упрощается конструкция намоточных станков, обеспечивается более стабильное послойное содержание связующего в изготовляемом изделии, улучшается гигиеничность процесса и условия работы. В обобщенном виде технологический процесс формования изделий по сухому методу включает в себя следующие операции: получение пропитанного полимерным связующим и высушенного рулонного материала; формование изделия намоткой полученного рулонного материала на оправку; термообработка полученной оболочки по специальному режиму и ее охлаждение; выпрессовка из оболочки оправки; механическая доработка отформованного изделия; его испытание и приемка. Для выпрессовки же оправки применяют гидравлические домкраты, механические лебедки и другие аналогичные устройства.
При мокром методе процессы пропитки армирующего наполнителя и его намотки на оправку совмещаются в одной операции формования изделия, и тем самым сокращается производственный цикл. Связующее при этом может наноситься напылением из пульверизатора, нагнетанием или засасыванием, а также пропусканием наматываемого армирующего наполнителя через ванну со связующим.
Комбинированный же метод заключается в том, что при намотке формуемого изделия по сухому методу к уже нанесенному на армирующий наполнитель и высушенному связующему между наносимыми слоями дополнительно вводится некоторое количество жидкого термореактивного связующего, не имеющего летучих растворителей. Этим обеспечивается более высокая монолитность и герметичность стенок в формуемых изделиях.
Установки для изготовления изделий намоткой обычно состоят из механизмов, обеспечивающих вращение оправки (формы) по заданной траектории и раскладчика армирующего наполнителя, который при необходимости оснащается пропиточной ванной или другими устройствами, наносящими на наполнитель связующее. В установке при этом должно обеспечиваться вращение оправки по такой траектории, при которой наматываемый на нее по заданной схеме раскладки наполнитель находился бы в состоянии естественного равновесия и не проскальзывал бы по оправке от натяжения укладки.
В зависимости от конфигурации изготовляемого изделия, его размеров и толщины стенок, вида армирующего наполнителя (нити, лента, полотно) и исполнения оправки, намотка при формовании изделия может быть прямой кольцевой, спиральной или сложнопрофильной, требующей одновременного вращения оправки в двух плоскостях по сложной траектории.
При наиболее простой прямой кольцевой намотке ширина армирующего материала должна соответствовать высоте формуемого изделия, а подача его на оправку производится при этом со стационарного раскладчика под углом ~90о к оси ее вращения.
При спиральной намотке раскладчик армирующего материала перемещается возвратно-поступательно вдоль оси вращения оправки с отношением один шаг намотки на один оборот оправки. Шаг же намотки обычно принимается адекватным ширине армирующего материала, укладываемого при этом на оправку под углами 25 – 85° к оси ее вращения.
125
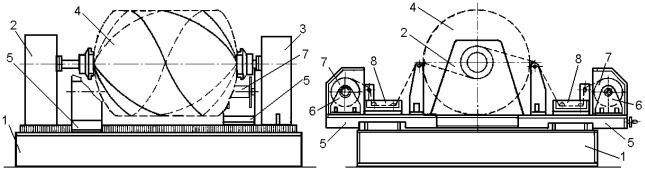
Этим способом получают оболочки, работающие при высоких поперечных и продольных нагрузках, причем за счет изменения угла намотки можно обеспечить и требуемое соотношение между их кольцевой и продольной прочностью.
При сложнопрофильной намотке зависимость между вращающейся в двух плоскостях по заданной траектории оправкой и перемещающимся раскладчиком должна быть таковой, чтобы наполнитель наматывался на оправку по требуемой схеме раскладки в состоянии естественного равновесия, то есть без проскальзывания по ее поверхности от натяжения укладки. Таким способом на конструктивно более сложных машинах обычно изготовляют оболочки с замкнутыми (закрытыми) торцами.
В частности станок, обеспечивающий формование, как замкнутых оболочек, так и корпусов с открытыми торцами их спиральной навивкой, состоит из станины 1 (рис.15.1), несущей стойки 2 и 3 во вращающихся шпинделях которых устанавливается съемная оправка 4. По направляющим же станины возвратно-поступательно перемещаются две каретки 5, каждая из которых содержит шпулярник 6, в котором устанавливается взаимодействующая с фрикционным тормозом сменная катушка 7 с намотанным армирующим материалом, а также ванну 8, заполненную полимерным связующим. От привода станка, расположенного внутри станины, через соответствующие передаточные и настроечные механизмы осуществляется вращение оправки 4 и взаимосвязанные с ней возвратнопоступательные перемещения кареток 5 по направляющим.
Рис.15.1. Станок для спиральной намотки замкнутых оболочек
В процессе работы этого станка непрерывный стекловолокнистый армирующий материал, разматывающийся с катушек 7, проходит через ванну 8, где пропитывается связующим, и после отжима его излишков наматывается под определенным натяжением на вращающуюся оправку 4, а каретки 5 возвратнопоступательно перемешаются при этом по направляющим станины, обеспечивая тем самым спиральную или более сложную схему его раскладки по поверхности оправки. После нанесения на оправку заданного количества слоев материала, зависящего от требуемой толщины и прочности оболочки, намотка прекращается, и сформированная оболочка подвергается отверждению холодному или при повышенной температуре, создаваемой, например, инфракрасными излучателями. Вместо мокрой пропитки в машине могут применяться и предварительно пропитанные ровинги, которые размягчают перед намоткой на оправку 4 между направляющими валками. После отверждения отформованной оболочки, она удаляется со снятой оправки 4 и
126
цикл повторяется. Для формования изделий намоткой применяются и другие разнообразные станки, как с горизонтальной, так и вертикальной осями вращения оправок.
Оправки являются важнейшим элементом намоточных станков. Их размеры, конфигурация и конструктивное исполнение определяются размерами
иформой внутренней поверхности изготовляемых изделий, а также схемой намотки на нее армирующего наполнителя; они должны иметь достаточную для формования прочность, а также легко отделяться от изготовляемого изделия без какого-либо его повреждения. При проектировании оправок необходимо учитывать все усилия и напряжения, воздействующие на них в процессе формования, в том числе: усилие и давление, создаваемые натяжением наматываемого наполнителя; сжатия, обусловленные усадкой оболочки в процессе отверждения полимерного связующего; а также силовые воздействия
инапряжения, связанные с выполнением различных доводочных операций (шлифование наружной поверхности отформованного изделия, обработка его торцов и т. д.). В зависимости от этих факторов оправки могут состоять:
из деревянной или металлической формы, которая выпрессовывается из изготовленного изделия по завершении его отверждения;
из надувных (например, резиновых) форм, в которых по окончании операций формования снимают давление для их удаления;
из сердечников, изготовленных из металлического сплава с низкой температурой плавления, специального воска или твердых легкорастворимых солей; после завершения отверждения такой сердечник удаляется из отформованной оболочки путем плавления при повышении температуры или путем промывки;
из тонкостенных форм, которые остаются в изделии.
Оправки диаметром до 600 мм выполняются, как правило, монолитными, а превышающие этот размер – складными или разборными. При изготовлении же закрытых оболочек применяют оправки надувные, а также разборные или удаляемые разрушением (выплавляемые, вымываемые и т. д.). Оставляемые в изделии тонкостенные формы в зависимости от их назначения могут изготовляться из резины, поливинилхлорида, нержавеющей стали, а также алюминия и его сплавов. В этом случае получаются изделия с двухслойными стенками, где оставляемая форма обеспечивает герметичность, химическую или коррозионную стойкость их внутренней поверхности, а внешняя оболочка, сформированная, например, из стеклопластика придает корпусу необходимую механическую прочность. Для повышения адгезии наружную поверхность оставляемых форм при необходимости покрывают соответствующими клеями или специальными смолами.
Центробежное формование применяется для изготовления корпусов крупногабаритной тары и других изделий, имеющих форму тел вращения (цилиндрическую, бочкообразную, усеченного конуса и т. п.). При изготовлении изделий этим способом в нагретую форму, торцы которой закрыты фланцами, загружают порцию расплава термопластов или жидкой смолы с отвердителем реактопластов, а затем форму приводят во вращение со скоростью в пределах от 280 до 1000 оборотов в минуту. При этом находящийся
127
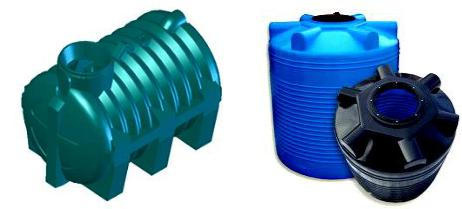
вней материал под действием центробежных сил равномерно распределяется по поверхности формы и, прижимаясь к стенкам, уплотняется, а затем в процессе охлаждения термопластов или полимеризации реактопластов затвердевает, образуя отливку. Так как процесс осуществляется при высоких частотах вращения формы, то под действием центробежных сил в материале развивается достаточно большое давление и поэтому усадка изготовляемого изделия невелика. После этого вращение прекращается, с формы снимаются торцевые фланцы, полученная отливка удаляется из нее и цикл повторяется. Обычно внутренний слой у изготовленного таким образом изделия имеет более рыхлую структуру, чем наружный, поэтому его при необходимости механически обрабатывают для получения требуемого внутреннего диаметра. С учетом такой обработки порция загружаемого в форму материала увеличивается на 10 – 15%. При загрузке в форму термопластичного материала
ввиде порошка или гранул продолжительность формования изделия существенно возрастает, так как затрачивается дополнительное время на его плавление и гомогенизацию в обогреваемой форме.
Этим способом обычно изготовляют изделия из полиамидов, полиэфиров и других термопластов с низкой вязкостью расплава, при этом из-за склонности
этих полимеров к окислению полость формы заполняют защитным газом (СО2, аргоном, азотом). Полуавтоматические установки центробежного формования применяются, в частности, для изготовления крупногабаритных изделий из стеклопластиков на полиэфирных смолах, а в качестве армирующего наполнителя используется при этом рубленое стекловолокно.
Наиболее же рациональным и экономичным способом, обеспечивающим получение самых крупногабаритных объемных полых изделий, в том числе предназначенных для упаковывания и пакетирования продукции, является ротационное формование, которое было разработано и впервые применено в Италии в 50-е годы ХХ века.
15.1. Ротационное формование
Ротационным формованием изготовляют крупногабаритные емкости (баки, цистерны, чаны, бочки, фляги, канистры, контейнер-цистерны, бункерные поддоны, поддон-резервуары) и разнообразные другие изделия, представляющие
собой замкнутые оболочки (рис.15.2) объемом от 0,25 до 40 м3 и более (рекорд
150 м3).
Рис.15.2. Примеры тары, изготовляемой ротационным формованием
128
К изготовляемым этим способом оболочкам с помощью сварки и склеивания присоединяются затем горловины, люки, сливные и наполнительные штуцеры, превращающие их в тару, а также сегменты, шпангоуты, опорные лапы и другие конструктивные элементы, повышающие прочность, жесткость и устойчивость этих изделий. К другим изготовляемым этим способом изделиям можно отнести, например, корпуса приборов, детские игрушки, манекены, буи и поплавки, дорожные ограждения, кабины биотуалетов, корпуса лодок и т. д.
Ротационное формование – способ изготовления тонкостенных полых изделий из пластмасс, при котором герметично закрытую металлическую форму, загруженную порцией полимерного материала, в зависимости от конфигурации изготовляемого изделия вращают в одной или двух взаимно перпендикулярных плоскостях с одновременным ее нагревом и последующим охлаждением. При этом материал, нагреваясь от стенок формы, плавится, гомогенизируется и равномерным слоем распределяется по ее поверхности, а затем в процессе охлаждения переходит в твердое состояние и образует полое изделие, удаляемое из раскрываемой формы после ее остановки. Приемлемая же равнотолщинность стенок у формуемых изделий достигается при оптимальной частоте вращения формы. Она должна быть таковой, при которой окружная скорость движения точек, лежащих на оформляющей поверхности формы, была бы равна скорости стекания находящегося расплава под воздействием сил тяжести. При этом полимерный материал удерживается на стенках полости формы преимущественно силами адгезии и инерции, в отличие от центробежного формования, при котором он прижимается и удерживается на стенках центробежными силами.
Этим способом формуют полые изделия из термопластичных и термореактивных пластмасс, изготовляют емкости с двух- и трехслойными стенками, а также наносят покрытия из порошкообразных полимеров и пластизолей на их внутренние поверхности. При этом изделия можно изготовлять практически из любого полимерного сырья, которое при нагревании переходит в вязкотекучее состояние или которое в исходном состоянии представляет собой пасту (пластизоли) или жидкость. В формы могут загружаться порошки с размером частиц 50 – 200 мкм или мелкие гранулы (размерами менее 1 мм) термопластов (полиэтилена, поливинилхлорида, полиамида, полистирола, поликарбоната, акрилонитрилбутадиенстирола и т. д.) и реактопластов, а также пластизоли, жидкие термореактивные олигомеры и даже мономерные композиции с инициаторами или катализаторами полимеризации.
Доминирующее же положение занимает полиэтилен, из которого выполняется 70 – 75 % от всех изготовляемых этим способом изделий, причем применение находят практически все виды этого полимера, в том числе сшивающийся. Широкое применение полиэтилена обусловлено, прежде всего, его относительно низкой стоимостью, высокой термостабильностью при формовании, хорошей перерабатываемостью гранул в порошок в специальных мельницах, а также приемлемыми эксплуатационными свойствами. Разработана, например, специальная марка полиэтилена, показатель текучести расплава которой при переработке уменьшается с 5 до 1,5. Этот материал также характеризуется повышенным значением ударной вязкости при низких температурах (до -30°С). За порошкообразным полиэтиленом следуют
129
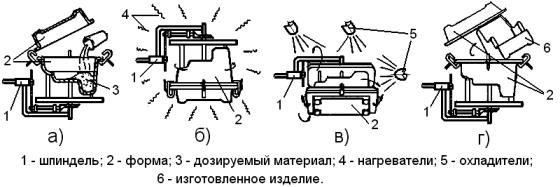
пластизоли на основе поливинилхлорида, (от 10 до 13%), среди которых имеются марки, специально предназначенные для ротационного формования. Для ротационного формования разработаны также специальные марки полиамидов, поликарбонатов, полипропилена, полистирола. Возможно изготовление этим методом изделий из термореактивных полимеров – полиуретанов, эпоксидных композиций и др., а также совмещение процесса полимеризации и формования (например, при полимеризации капролактама). В этом случае в форму загружают композицию на основе капролактама и катализатор.
Из смесей полимеров, отличающихся друг от друга значениями температуры плавления, получают двухслойные изделия с различными свойствами слоев. Для предотвращения окисления некоторых термопластов (например, полиамидов) в форму нагнетают инертный газ. Для модификации свойств материалов, перерабатываемых ротационным формованием, широко используются различные добавки, такие как термо- и светостабилизаторы, вспенивающие агенты, наполнители (в том числе волокнистые) и др. Иногда ротационное формование осуществляют с применением жестких металлических и пластмассовых закладных элементов, различных вкладышей и вставок.
Процесс изготовления изделий ротационным формованием включает нанесение на поверхность полости формы антиадгезива, дозирование сырья, загрузку отмеренной дозы в форму и ее закрытие, приведение формы во вращение, нагрев формы и материала, охлаждение формы и находящегося в ней изделия, остановку и раскрытие формы, а также извлечение из нее отформованного изделия. Весь этот процесс обычно разделяют на следующих четыре характерных этапа.
На первом этапе на поверхность полости формы наносится антиадгезив, затем дозируется порошкообразный или жидкий полимерный материал 3 (рис.15.3а), загружается в полую форму 2, закрепленную на шпинделе 1 формовочной машины, и форма герметично закрывается. Толщина же стенок у изготовляемого изделия будет зависеть при этом от количества находящегося в форме материала.
Рис.15.3. Этапы изготовления изделий ротационным формованием
На втором этапе производится формование изделия. Для этого форма 2 (рис.15.3б) шпинделем 1 формовочной машины приводится во вращение относительно двух взаимоперпендикулярных осей и одновременно нагревается. При этом материал, нагреваясь от стенок формы, плавится, гомогенизируется и распределяется равномерным слоем по ее поверхности, формируя изделие,
130