
[SHipinsky_V.G.]_Oborudovanie_i_osnastka_upakovoch2(z-lib.org)
.pdf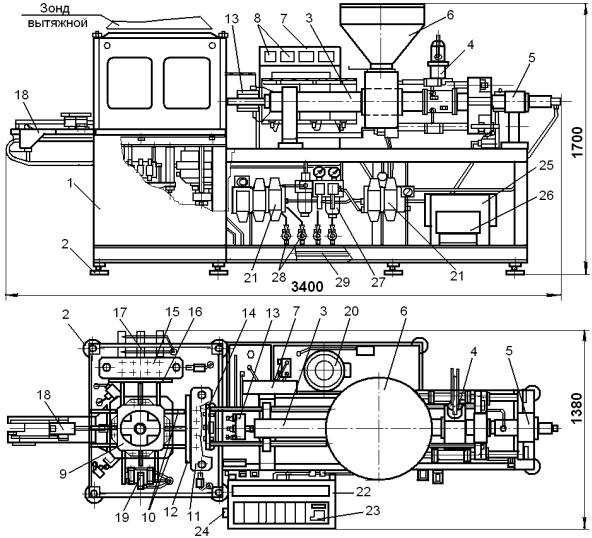
Рис. 12.15. Четырехпозиционный многоместный инжекционно-раздувной агрегат модели АИПТ-0,5
Механизм 18, который своим вилочным захватом, перемещающимся с кареткой от гидромотора через зубчатую передачу шестерня – рейка, снимает с третьего комплекта оправок 10 готовые изделия и направляет их в технологическую тару;
Блок 19, контролирующий своими щуповыми датчиками исправность четвертого комплекта оправок 10, а также отсутствие на них изделий и их частей;
Гидростанция 20, обеспечивающая подачу масла под заданным давлением из бака через коммутационные и регулирующие гидроустройства, находящиеся на панели 21, к гидроприводам всех исполнительных устройств и механизмов агрегата;
Стойка управления 22, содержащая контроллер 23 микропроцессорный МКП-
1и пульт наладочный 24;
Блоки распределительные 25 и 26, содержащие электромонтажные соединительные элементы, платы, коммутационные и другие электрические устройства агрегата;
Пневмосистема с блоком подготовки воздуха 27, распределительными и другими пневмоустройствами, обеспечивающая очистку и подачу сжатого воздуха в раздувную форму 16;
91
Напорный 28 и сливной 29 коллекторы, обеспечивающие подачу проточной воды к охлаждаемым узлам и формам агрегата.
Впроцессе работы агрегата гранулированный материал из бункера 6 поступает самотеком в материальный цилиндр 3, где захватывается вращающимся червяком и транспортируется им в переднюю часть цилиндра, одновременно нагреваясь от его стенок и трения до вязкотекучего состояния. При этом червяк отходит назад, а порция пластифицированного материала накапливается перед ним. Затем поступательным движением червяка вперед от штока гидроцилиндра 5 материал впрыскивается через сопло цилиндра, а также закрепленную на нем обогреваемую головку 13 и стыковочную колодку 14 в формующие полости сомкнутой трехместной литьевой формы 12 и там из него на оправках 10 под давлением формуются ампулообразные заготовки, охлаждаемые до пластичного состояния водой, циркулирующей по каналам формы 12.
Одновременно в сомкнутой выдувной форме 16, размещенной в механизме смыкания 15, ранее отлитые в форме 12 заготовки раздуваются в готовые изделия. Для этого в осевой канал каждой оправки 10 второго комплекта подается сжатый воздух, под давлением которого ее головка, преодолевая усилие возвращающей пружины, смещается вперед и продольно растягивает пластичную заготовку, а также открывает на корпусе оправки поясок с радиальными отверстиями, через которые сжатый воздух поступает внутрь заготовки и раздувает ее в изделие по конфигурации оформляющей полости формы, которая охлаждается при этом проточной водой, циркулирующей по ее каналам.
Вэто же время механизм 18 своим вилочным захватом, перемещающимся с кареткой от гидромотора, снимает с третьего комплекта оправок 10 готовые изделия, сбрасывает их в технологическую тару и возвращается в исходное положение.
Одновременно щуповые датчики блока 19, контактирующие с четвертым комплектом оправок 10, проверяют отсутствие на них неудаленных частей от бракованных изделий и налипшей пластмассы, а также работоспособность самих оправок. При выявлении этих факторов на оправках блок 19 останавливает работу агрегата для их устранения, а затем он оператором с пульта управления снова включается в автоматическую работу.
После завершения приведенных действий на всех четырех технологических позициях агрегата срабатывает механизм запирания 11 и, перемещая вверх подвижную плиту, раскрывает литьевую форму 12, а механизмом 15 и блоком 17 в это же время раскрывается выдувная форма 16. Далее штоком приводного гидроцилиндра револьверный стол 9 перемещается в верхнее положение, затем гидромотором поворачивается в плане на 90о с фиксацией положения и снова возвращается в нижнее исходное положение, перенося при этом на оправках 10 отлитые ампулообразные заготовки на вторую технологическую позицию, а готовые изделия – на третью позицию. После этого механизмами 11, 15 и 17 формы 12 и 16 снова смыкаются и цикл повторяется. Агрегат может работать в наладочном, полуавтоматическом и автоматическом режимах.
Техническая характеристика у агрегата модели АИПТ-0,5 следующая: Производительность, изделий/ч., не менее .………………………. 500; Усилие запирания инструмента, кН, не менее:
литьевого ……………………………………………….. 250;
92
раздувного ………………………………………………... 30;
Наибольший ход подвижных плит механизмов запирания инструмента, мм ………………………………………. 200;
Высота устанавливаемого инструмента, мм, не менее…………… 200; Наибольшее давление литья, МПа ………………………………… 120; Наибольший объем впрыска за цикл, см3………………………….. 130; Наибольшая температура в зоне пластикации, оС ………………... 330; Питание: переменный ток: частотой, Гц ………………………….. 50;
напряжением, В …………………………………………. 380;
сжатый воздух под давлением, МПа .……………. 0,4 – 0,6; Потребляемая мощность, кВт, не более …………………………… 15; Габаритные размеры, мм …………………………..3400 х 1380 х 1700;
Масса, кг, не более …………………………………………………2000;
Агрегат обслуживается одним человеком.
В трех- и четырехпозиционных инжекционно-раздувных агрегатах достигается более высокая цикловая производительность в сравнении с двухпозиционными за счет того, что съем готовых изделий с оправок осуществляется на отдельной технологической позиции одновременно с процессами формования заготовок и раздува готовых изделий. А из этих агрегатов самую высокую производительность обеспечивают многоместные, так как в них изделия изготовляются еще и несколькими параллельными потоками, при минимальном количестве отходов. Инжекционно-раздувным формованием получают изделия и более высокого качества в сравнении экструзионно-раздувным формованием, за счет выполнения у них калиброванной горловины; отсутствия сварных швов; более равномерной толщины стенок, а также их большей прочности, прозрачности, гладкости и уменьшенной газопроницаемости, из-за применения продольного и тангенциального растяжений заготовки при формовании, что приводит к возникновению двухосной ориентации полимера. Однако инжекционно-раздувные агрегаты нельзя применять для переработки высоковязких полимерных материалов.
12.4. Оборудование для раздува изделий из преформ
Из-за очевидной неэффективности транспортировки готовых пластмассовых бутылок, занимающих большие объемы, производители жидкой продукции обычно изготовляют их из ампулообразных заготовок (преформ) на своих предприятиях. Сами же преформы, в десятки раз меньшие по объему, при этом поставляются им специализированными предприятиями. Широкому распространению таких технологий способствует несложное и относительно доступное оборудование, применяемое для раздува из преформ, а также высокое качество изготовляемой тары. Наиболее широко применяемым материалом в производстве такой тары является полиэтилентерефталат (ПЭТ) и ассортимент выпускаемых из него ПЭТ-преформ чрезвычайно велик. Достаточно сказать, что только одна фирма «RESILUX» выпускает более 12 типоразмеров ПЭТ-преформ, семь из которых предназначены для раздува бутылок под газированные напитки. Кроме того, преформы одинаковой массы, но различных фирм-изготовителей имеют различия, как по конфигурации, так и размерам. Выбор типа и массы преформы регламентируется объемом тары,
93
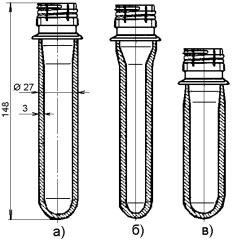
которую намерены формовать, а также ее конфигурацией и заданными барьерными свойствами, зависящими от материала и толщины стенок тары. Например, в зависимости от степени насыщения содержимого углекислотой, составляющей от 2 до 10 г на 1 дм3, толщину стенок бутылок увеличивают до 0,2 мм для слабогазированных минеральных и фруктовых вод, не предназначенных для длительного хранения, и до 0,36 – 0,38 мм для сильногазированных напитков типа «Coca-Cola». Еще более увеличивают толщину бутылок, предназначенных для многоразового использования. Так, например, фирма «SIDEL», специализирующаяся на выпуске бутылок, близких по форме к стеклянным, выбирает массу преформы, обеспечивающую толщину стенок не менее 0,5 мм. Чем толще стенка бутылки, тем лучше ее показатели, однако и стоимость бутылки при этом возрастает почти прямо пропорционально увеличению массы преформы.
В идеале, под каждую разновидность тары и тип применяемого для ее изготовления раздувного оборудования должна разрабатываться своя с оптимальными параметрами преформа, чем и объясняется существующее многообразие их форм и размеров. Однако на практике далеко не каждый производитель бутылок может позволить себе заказать оптимальные преформы и поэтому вынужден довольствоваться теми, что есть на рынке. По своей же конфигурации все разновидности применяемых преформ можно разделить на следующие три основные группы (рис.12.16): универсальные, толстостенные и укороченные.
Рис. 12.16. Конструктивные исполнения преформ
Универсальная преформа при качественном изготовлении достаточно хорошо и быстро (за 3 – 4 мин) прогревается, не разрушается при продольном растяжении и пригодна к окончательному формованию сжатым воздухом давлением около 1 МПа. Типичным образцом универсальной преформы является широко распространенная преформа «ОПТИМУМ» (рис.12.16а), которая при массе 42 г выполняется длинной 148 мм и с толщиной стенки 3 мм. Толстостенная преформа (рис.12.16б) по сравнению с универсальной проще в изготовлении. Однако она требует более длительного нахождения в зонах разогрева, что невозможно реализовать, например, на полуавтоматах типа «HFB2H» из Гонконга и аналогичном оборудовании фирм «ENITAL», «STECA» и др. Укороченная преформа (рис.12.16в) предназначена для раздува тары только на мощном оборудовании с давлением воздуха до 4 МПа. Поэтому изготовить,
94
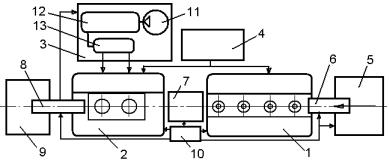
например, на полуавтоматах качественную бутылку из таких преформ чрезвычайно сложно.
Раздувное технологическое оборудование, различающееся по производительности, универсальности, уровню автоматизации процесса и, соответственно, стоимости производится во многих странах, в том числе Франции, Италии, Германии, Польше, Бельгии, Китае, России и других. В частности такие мощные специализированные автоматы производительностью до 12 тысяч бутылок в час, например, французской фирмы «STECA» предлагаются за 60 000 USD, а дешевые китайские полуавтоматы производительностью 500 – 600 бутылок в час можно приобрести менее чем за 20 000 USD. При этом широкому распространению таких полуавтоматов способствует не только низкая стоимость и простота в эксплуатации, но и их пригодность для работы практически в любом электрифицированном помещении, включая мобильный вариант – в прицепе, например, автомашины типа КамАЗ. Кроме этого малогабаритные и экономичные полуавтоматы позволяют в кратчайшие сроки заменять в них формы для выпуска бутылок разных объемов, форм и назначения, в то время как высокопроизводительное автоматическое раздувное оборудование такими возможностями не обладает.
Автоматизированные комплексы для раздува бутылок, отличающиеся большим количеством вариантов исполнения, могут включать в себя такие функциональные устройства, как: станция 1 (рис.12.17) разогрева преформ, раздувной агрегат 2, станция 3 подготовки сжатого воздуха, система охлаждения 4, бункер 5 с преформами, загрузочно-ориентирующее устройство 6, манипулятор 7 переноса преформ, отводящий транспортер 8, накопительный бункер 9 и электрооборудование 10 с микропроцессорным контроллером.
Рис. 12.17. Функциональная схема автоматизированного комплекса для раздува бутылок
При этом станция 1 осуществляет разогрев помещенных в нее преформ до рабочей температуры Тр, соответствующей пластичному состоянию материала и поддерживаемой с точностью до 3 оС. По принципу действия их можно разделить на две группы. Первую группу составляют станции разогрева конвейерного типа. В них преформы двигаются вдоль ТЭНов и равномерно вращаются. При этом ТЭНы, разнесенные по высоте, образуют от 4 до 6 зон управляемого разогрева, что позволяет работать с преформами практически любой конфигурации. Вторую группу составляют станции разогрева погружного типа. В них преформы размещаются в гнездах разогретых плит и находятся там неподвижно в течение 10 – 16 мин. Такие станции имеют не
95
более 3 – 4 зон разогрева. Они просты и надежны. Однако работают эффективно лишь с преформами одного типоразмера.
Раздувной агрегат 2 в свою очередь обеспечивает формование тары (бутылок, банок) из предварительно разогретых преформ. Он включает в себя механизм запирания раздувной формы, устройство формования, оправками которого осуществляется продольное растяжение пластичных заготовок и раздув их в изделия по конфигурации оформляющей полости формы, а также систему подачи сжатого воздуха в исполнительные устройства, систему охлаждения раздувной формы и электронный блок управления. Количество оформляющих полостей в сменных раздувных формах, состоящих обычно из трех частей, зависит от типа машины. Как правило, применяются двухместные формы. Изделия в них раздуваются сжатым воздухом, подаваемым под давлением более 1,1 МПа. И чем большее допустимое давление раздува, тем шире потенциальные возможности агрегата в изготовлении тары сложных форм и больших объемов. Процесс раздува заготовок, закрепляемых в смыкающейся форме за венчик горловины, включает в себя следующие стадии: установка преформы, смыкание раздувной формы, введение в преформу оправки с герметизацией горловины, механическое продольное растяжение преформы оправкой, предварительная и окончательная раздувка заготовки в изделие, охлаждение, размыкание формы и удаление из нее готового изделия. В результате же продольного и тангенциального растяжений заготовки при формовании повышается прочность, прозрачность и гладкость стенок изготовляемой тары, а также снижается их газопроницаемость и разнотолщинность.
Станция 3 подготовки сжатого воздуха содержит компрессор 11, ресивер 12 и блок 13 подготовки воздуха, последовательно соединенные между собой. Компрессор 11 при этом обеспечивает питание агрегата сжатым воздухом. Его производительность, рабочее давление и надежность во многом определяют эффективность работы всего комплекса. Например, для раздува качественных бутылок со сложным дном (под газированные жидкости) вместимостью 1,5 дм3 он должен создавать давление не менее 1,6 МПа с производительностью не ниже 0,4 м3/мин. В ресивере же 12 создается необходимый запас сжатого воздуха и чем больше его объем, тем уже диапазон изменений давления при раздуве тары. Для стабильной работы оборудования объем ресивера должен быть не менее 250 дм3. В блоке 13 подготовки воздуха производится очистка и осушение подаваемого в раздувную форму сжатого воздуха и тем самым достигается соблюдение санитарно-гигиенических требований, предъявляемых к изготавливаемой таре.
Система охлаждения 4 обеспечивает в станции разогрева охлаждение горловин преформ, а в агрегате выдува – охлаждение раздувной формы и соответственно изготовляемых изделий. Выполняются эти системы как жидкостными, так и воздушными. При этом недостаточное охлаждение венчиков преформ приводит к появлению бракованных бутылок с деформированными горловинами, а неэффективное охлаждение раздувной формы может привести к искажению конфигурации готовых бутылок.
Бункер 5 служит для хранения запаса преформ, обеспечивающего непрерывную работу комплекса в течение определенного интервала времени.
96
Из бункера преформы захватываются и транспортируются элеваторным загрузочным устройством 6 в ориентирующий механизм, который приводит преформы в заданное положение и устанавливает в гнезда распределительного диска, поштучно загружающего их в станцию разогрева.
Манипулятор 7 обеспечивает цикловую подачу преформ со станции 1 разогрева и их установку в форму раздувного агрегата с одновременным удалением из нее готовых изделий на отводящий транспортер.
Отводящий транспортер 8 выводит в свою очередь готовые изделия из раздувного агрегата 2, поднимает их на заданную высоту и затем сбрасывает в накопительный бункер 9. В состав таких комплексов могут входить и транспортеры, обеспечивающие горизонтальное перемещение изготовляемых бутылок, например к установке контроля качества, удаляющей из потока бракованную тару, и далее к технологическому оборудованию, упаковывающему продукцию. Состоят такие транспортеры из отдельных легко монтируемых и быстро переналаживаемых унифицированных секций.
Электрооборудование 10 обеспечивает питание исполнительных устройств комплекса электрическим током, включая и их электродвигатели с частотными регуляторами скорости, позволяющие в широком диапазоне устанавливать требуемую производительность комплекса непосредственно с пульта управления, а с микропроцессорного контроллера с LED-дисплеем осуществляется установка, автоматическое поддержание и оперативный контроль всех параметров технологического цикла.
Вполуавтоматических комплексах для раздува бутылок все манипуляции
спреформами осуществляются, как правило, вручную, поэтому они
выполняются более простыми и |
дешевыми. В частности |
такой |
полуавтоматический комплекс модели |
«NORLAND BM-8L», изготовляемый |
американской компанией «NORLAND Int l. Inc.», в стандартной комплектации включает в себя блок 1 (рис.12.18) разогрева преформ, раздувной агрегат 2, станцию 3 подготовки сжатого воздуха и элеваторный транспортер 4, уносящий готовые изделия.
Блок 1 разогрева преформ содержит конвейер с регулируемой скоростью движения, который изготовлен из нержавеющей стали и оснащен термостойкими держателями преформ, обеспечивающими их вращение для равномерного нагрева. Область разогрева разделена в нем на шесть зон, в каждой из которых установлено по четыре Ni-Cr нагревательных элемента, обладающих высокой надежностью и стойкостью к скачкам напряжения. Каждая зона содержит также свой микропроцессорный контроллер с LEDдисплеем, обеспечивающий индивидуальную регулировку, и термодатчики поверхности нагревателей, что позволяет устанавливать оптимальные режимы нагрева для конкретного типа преформ и конструктивного исполнения тары.
В раздувном агрегате 2 станина выполнена из конструктивных элементов, отлитых из высокопрочного алюминиевого сплава, что снижает ее вес и исключает коррозию. А применяемые направляющие с хромовым покрытием и уплотнительные втулки, выполненные из материала «Frelon», обеспечивают их высокую износостойкость, а также облегчают движение и смыкание выдувной формы, повышая тем самым производительность и качество изготовляемых бутылок. Повышенной надежностью и эксплуатационным ресурсом обладают
97
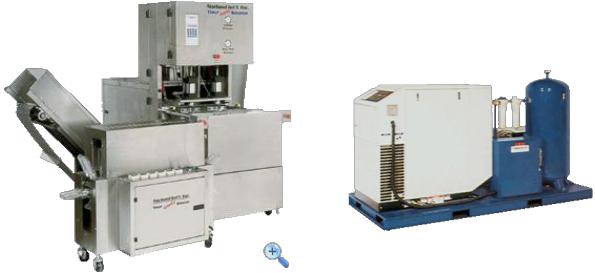
также превмоцилиндры высокого давления и другое превмооборудование агрегата. Имеющийся микропроцессорный блок управления с дисплеем и клавиатурой позволяет оперативно устанавливать и контролировать в процессе работы все параметры технологического цикла. Безопасную же работу оператора обеспечивают оптические датчики, которые прерывают цикл при приближении его рук к смыкающейся раздувной форме. Кроме этого агрегат оборудован всеми необходимыми защитными ограждениями.
Рис. 12.18. Полуавтоматический комплекс для раздува бутылок модели
«NORLAND BM-8L» американской компании «NORLAND Int l. Inc.»
В станции 3 подготовки сжатого воздуха на общем основании установлены: компрессор высокого давления модели 250PSI, создающий давление до 1,7 МПа с производительностью 17,5 дм3/с, а также бак-ресивер, автоматический рефрижераторный осушитель воздуха, сепараторный и угольный фильтры, фильтр очистки сжатого воздуха от паров масла и фильтр тонкой очистки (до 3 мкм). Таким образом, эта станция обеспечивает агрегат чистым и сухим сжатым воздухом, необходимым для изготовления качественных PET-бутылок. Питание ее осуществляется от сети 3-фазного переменного тока напряжением 380 В и частотой 50 Гц, а потребляемая мощность составляет 10 – 20 кВт.
Элеваторный транспортер 4, оснащенный электрическим приводом, обеспечивает отвод сбрасываемых оператором готовых бутылок от агрегата с их подъемом на высоту 1,2 м и подачей в накопительный бункер.
При работе оператор поштучно устанавливает преформы в держатели конвейера блока разогрева, а также снимает с него уже разогретые преформы и размещает их в соответствующих гнездах раздувной формы. Затем нажатием двух кнопок он включает цикл автоматического биаксиального раздува, а после его завершения забирает готовые бутылки из размыкающейся раздувной формы и сбрасывает вниз на транспортер, уносящий готовые изделия в накопительный бункер. Данный комплекс позволяет одному оператору изготовлять 500 – 600 бутылок в час вместимостью от 120 см3 до 8,0 дм3, круглой, квадратной и прямоугольной формы, из преформ различного размера с горловиной диаметром 28 – 43 мм. Технические характеристики блока разогрева преформ и раздувного агрегата этого комплекса приведены в таблице 12.2.
98
Таблица 12.2 – Технические характеристики:
|
|
|
|
|
Показатели |
|
Блок разогрева преформ |
|
Раздувной агрегат |
|
|
|
|
|
Габаритные размеры, |
|
1140 х 510 х 920 |
|
2300 х 2000 х 1900 |
мм, (Д х Ш х В): |
|
|
||
|
|
|
|
|
|
|
|
||
Масса, кг : |
|
70 |
|
1800 |
|
|
|
|
|
|
|
переменный ток до 40 А, |
|
переменный ток до 10 А, |
Электропитание: |
|
однофазный, напряжением |
|
однофазный, напряжением |
|
|
220 В и частотой 50 Гц. |
|
220 В и частотой 50 Гц. |
|
|
|
|
|
Средняя потребляемая |
|
8 |
|
1 |
мощность, кВт |
|
|
||
|
|
|
|
|
|
|
|
|
|
Сжатый воздух: |
|
- |
|
Чистый, сухой, давлением |
|
|
до 1,7 МПа. |
||
|
|
|
|
|
|
|
|
|
|
Потребление сжатого |
|
- |
|
17,5 |
воздуха, дм3/с, не более |
|
|
||
|
|
|
|
|
Специализированное же технологическое оборудование, применяемое для изготовления преформ, приводится в следующем разделе.
13. ПРОИЗВОДСТВО ЛИТЬЕВОЙ И ПРЕССОВАННОЙ ПЛАСТМАССОВОЙ ТАРЫ
Основным методом изготовления литой тары является литье под давлением.
Литье под давлением – способ формования, который заключается в нагреве пластмассы до вязкотекучего состояния и впрыске ее в форму, где материалу и придается конфигурация изготавливаемого изделия.
При переработке термопластов разогретый материал литьевой машиной подается в холодную форму, где остывая, полимер затвердевает, переходя в стеклообразное или кристаллическое состояние.
При литье реактопластов материал впрыскивается и выдерживается некоторое время в обогреваемой форме. При этом в нем протекают химические реакции с образованием трехмерной (сшитой) молекулярной структуры и отверждением отливки.
В силу конструктивных особенностей инструмента литьевая и прессованная тара выполняется без поднутрений, препятствующих извлечению готового изделия после его формования. По технологическим причинам затруднено изготовление этими методами тары с тонкими стенками. Этими методами изготовляется в основном прочная многооборотная тара, такая как ящики, лотки, и т. д., а также укупорочные средства (крышки, колпачки, пробки, бушоны и др.), функциональные устройства и приспособления.
На современных литьевых машинах изделия изготовляют литьевым, интрузионным и инжекционно-прессовым способами.
Литьевой способ заключается во впрыске материала в литьевую форму поступательно перемещающимся поршнем или червяком и выдержке материала в форме под давлением до его отвердевания.
99
Интрузионный способ состоит в заполнении литьевой формы жидким полимером, подаваемым вращающимся червяком или червяком, совершающим одновременно вращательное и поступательное движения и выдержке под давлением, создаваемым вращающимся червяком.
Инжекционно-прессовый способ заключается в заполнении расплавленным полимером (пластмассой) не полностью сомкнутой формы литьевым или интрузионным способами и дальнейшем формовании в ней изделия под действием усилия, создаваемого прессовым механизмом, полностью смыкающим форму. При этом частичное размыкание формы осуществляется при впрыске материала и сопровождается незначительным перемещением подвижной плиты. После инжекции, под действием механизма замыкания, полуформы снова полностью смыкаются, материал при этом дополнительно подпрессовывается, а его излишки могут выдавливаться через литниковый канал обратно в пластикационный цилиндр. Используется метод для получения тонкостенной, преимущественно крупногабаритной транспортной тары и обеспечивает повышенную точность выполнения размеров.
В литьевых машинах основными являются устройства пластикации материала, а также инжекции и замыкания форм. Классификация литьевых машин осуществляется по следующим признакам:
по объему отливки в см3;
по принципу действия инжекционного механизма – поршневые, червячнопоршневые, червячные; с предварительной пластикацией и без нее;
по виду перерабатываемых материалов – для термопластов, реактопластов, эластомеров; порошкового или гранулированного материала;
по назначению – универсальные и специализированные;
по виду привода – механические, гидромеханические, гидравлические, пневматические;
по взаимному расположению инжекционной и прессовой частей – горизонтальные, вертикальные, угловые и комбинированные;
по количеству инжекционно-прессовых частей – одно- и многоместные.
Основные параметры литьевых машин: максимальный объем отливки; усилие запирания формы; максимальные размеры формы; диаметр червяка или поршня; развиваемое инжекционное давление; мощность привода и нагревательных элементов; габаритные размеры и масса машины.
В частности, горизонтальная одночервячная литьевая машина состоит из (рис.13.1):
литой или сварной станины 1, устанавливаемой на виброопорах 2;
подвижной плиты 3, перемещающейся штоком 4 гидроцилиндра 5, и неподвижной плиты 6, на которых крепится литьевая форма 7;
материального цилиндра 8 с установленными на нем электронагревателями 9
ибункером 10;
располагающегося внутри цилиндра червяка 11, приводимого во вращение гидромотором 12 и продольно перемещающегося штоком гидроцилиндра 13;
а также гидростанции 14 и шкафа управления 15 с электрооборудованием.
100