
Производственный (операционный) менеджмент - В.А.Василенко, Т.И.Ткаченко
.pdfтить существующий запас с одного рабочего места к следующему или необходимости произвести детали, комплекты деталей или узлы.
Карточка является разрешением на следующую партию (ее получение или производство).
Система была модифицирована во множество различных подходов, в результате чего в большинстве этих подходов сама карточка отсутствует. В некоторых случаях кусок материи, флажок или сигнальный маркер в определенном месте используется для того, чтобы известить, что подошло время подачи следующей партии.
Партии, как правило, очень малы и обычно требуют несколько часов для их изготовления. Такая производственная система требует четкого планирования и частых переналадок машин. Небольшие количества всех деталей должны быть произведены несколько раз в день. Эта система должна функционировать ритмично и слаженно, либо возникновение дефицита в любой ее части почти немедленно сказывается на работе системы в целом.
Подсистема «канбан» явилась следствием развития системы «точно-вовремя». При практическом использовании этих программ следует учитывать, что разработаны они были на поточном автомобилестроительном производстве завода Toyota. Канбан (kanban) – японское слово, означающее «сигнал» или «визуальная запись». Когда рабочему нужны материалы или комплектующее изделие с предыдущего участка, он использует карточку канбан.. Канбан – покрытая пластиком карточка или иное устройство, посредством которого передают запрос на работу или материалы с предыдущего участка, например: «Сделайте 500 продуктов X». В сущности, эта карточка – сигнал к движению или к работе над деталью. В системе канбан ни одна деталь или партия не может перемещаться или обрабатываться без такой карточки [2].
Представьте себе следующую ситуацию. Клиент делает заказ на 10 продуктов X. Заведующий складом вынимает карточку канбан из ящика продукта Х и передает ее мастеру на сборочной линии. Сначала у рабочих на сборке есть другие небольшие партии продуктов для производства, а затем они могут приступить к продукту X.
Мастер на сборочной линии проверяет компоненты, необходимые для производства продукта X. Некоторые компоненты уже есть, но другие необходимо произвести. Мастер берет карточку канбан для этих частей и передает мастеру по их производству.
Эти мастера проверяют все необходимое для производства требуемых компонентов. Карточка канбан будет послана поставщикам и магазинам на те требуемые части и материалы, которых нет на складе.
Одним из преимуществ системы канбан является немедленная видимость проблем. Если на одной из стадий процесса происходит задержка, останавливается вся линия, поскольку у последующих стадий не будет материалов, а у предшествующих – карточек. Они не смогут делать детали про запас, поскольку сверху на это не пришло разрешение. Проблему приходится решать, а не откладывать на потом.
Сложность заключается в том, что для нормальной работы вся линия должна быть полностью укомплектована необходимыми деталями. Если на последней стадии есть детали только для шикарных синих штучек, там не смогут собрать стандартные зеленые, чего бы ни
241
требовали карточки. Соотношение выпуска различных продуктов должно быть заложено заранее и остается неизменным в течение всего производственного цикла.
«Канбан» усиливает исполнение планов в нужный срок и понижает время и затраты на требуемые переналадки.
Преимущество от небольших заделов велико. Например, небольшие партии позволяют ограничить количество некачественного материала, дают возможность выявить недостатки в организации производственного процесса, уменьшить время транспортировки и контроля, время очередей, непредусмотренные технологией организационные перерывы и т.д.
Если учесть, что положительным аспектом повышенных запасов является лишь один – доступность, то отрицательных – множество. Среди них отметим следующие:
•низкое качество запасов;
•устаревание;
•разрушение;
•необходимость в площадях;
•замораживание материальных средств;
•увеличение страховки;
•рост объемов перемещаемых материалов;
•увеличение количества несчастных случаев,
Затраты, вызванные перечисленными факторами, называют затратами хранения. Эти затраты являются еще одним аргументом в пользу внедрения в практику системы «Точно вовремя».
В этой связи, представляется целесообразным дать краткую, хотя бы фрагментную, характеристику системы «Канбан», принципиальная схема которой приведена на рис.3.16
Основные параметры системы «Канбан» включают:
•размер партии;
•число карточек (заказа, отбора);
•емкость конвейера (оборудования, производства);
242
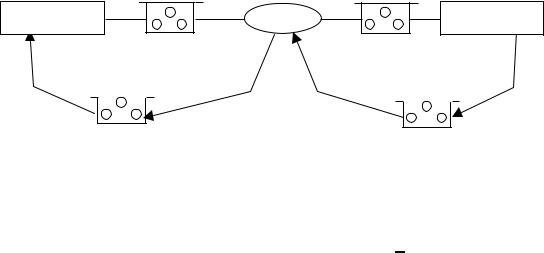
•время заказа партии;
•запас на складе.
Участок |
Склад |
Участок |
Карточка отбора
Рис.3.16. Принципиальная схема функционирования системы "Канбан"
Правила функционирования системы «Канбан» заключаются в следую-
щем:
•последующий участок «вытягивает» изделия;
•предшествующий участок выпускает изделия, число которых равно числу ранее «вытянутых» изделий;
•бракованная продукция не поступает на последующий участок;
•число карточек «Канбан» должно быть минимальным;
•запас изделий на складе должен быть минимальным;
•колебания спроса компенсируются изменением интенсивности потока карточек «Канбан»;
•производственные мощности участков должны быть сбалансированы;
•дисциплина поставок не допускает никаких отклонений в сроках. Типы системы «Канбан» имеют следующие разновидности:
•поставка равными партиями при определенном варьировании времени между партиями;
•поставка через равные промежутки времени при варьировании размера партии;
•варьирование размерами партии и времени поставки в заданных пределах;
243
•варьирование типами заготовок в партии при многономенклатурном производстве.
Обобщая изложенное, можно заключить – система «Канбан» включает в себя и базируется на четырех основных составляющих:
•минимальные затраты;
•оптимальные сроки;
•оптимальные партии;
•отличное качество.
Иначе говоря, потребителю нужен качественный товар в нужном количестве, в нужном месте, в нужное время и доставленный с минимальными затратами.
Т-В – это бесконечный процесс, который нельзя внедрить и забыть. Большинство из описанных выше этапов на самом деле должны постоянно повторяться. Организация развивается постепенно, учится сокращать или вовсе обходиться без наладки, работать гибко, прогрессивно улучшать качество и надежность оборудования. Основная идеология системы – постоянное улучшение, а не случайное изменение.
12.3. Преимущества и недостатки системы «Точно в срок»
Организация может добиться конкурентного преимущества, используя следующие факторы:
•скорость поставки;
•надежность поставки;
•качество;
•дизайн/инженерное решение;
•более высокая маржа;
•более низкое вложение в расчете на каждую единицу.
Некоторые из этих факторов трудно измерить в финансовом отношении (например, скорость и надежность доставки, качество и дизайн/инженерное решение), так как они не связаны напрямую со стоимостью продукта. Однако они составляют основу международной конкуренции и используются в конкурентной борьбе.
Четыре критерия – скорость и надежность поставки, качество и дизайн – нацелены скорее на увеличение продаж, чем на простое сокращение затрат, так как трудно определить рост продаж, вызванный изменениями, оценить финансовые преимущества. Снижение запасов (сырья, полуфабрикатов и готовой продукции) фактически позволяет снизить затраты.
Как подход к производственной деятельности, основанный на принципе непрерывного улучшения и сокращения потерь, Т-В может быть применен в любых условиях, однако в своей наиболее вероятной форме, а именно в виде поточного производства без запасов, система становится несколько более ограниченной по сфере применения. В принципе, производственная система Т-В должна обладать крайне высокой реакционной способностью, поскольку все задержки сведены к минимуму и нет никаких отставании в виде невыполненной работы. На практике короткое время цикла достигается только при точном соответствии производственных мощностей и потребностей рынка и при стабильной работе поставщиков.
244
В том виде, как система Т-В была описана выше, она эффективно работает только в условиях стабильного и предсказуемого спроса.
Т-В не учитывает проблем сезонности и практически не оставляет возможности для метода погони за спросом. Это означает, что как бы не велась работа в цехах, будет оставаться потребность в хранении запасов готовой продукции. Увы, но наличие склада в конце производственной линии никак не способствует желанию сокращать потери – отношению, крайне необходимому при Т-В. Именно поэтому компании, перенявшие данную систему работы, часто имеют отдельные склады готовых товаров или даже прибегают к субподряду, когда вся продукция продается агентам, которые потом занимаются ее распределением.
Парадокс Т-В в том, что, устраняя запасы – в идеале на всем протяжении цепочки поставок, – система дает возможность работать очень гибко и отзывчиво, но – только в условиях рынка с низким разнообразием и высокой стабильностью.
И последнее, за что критикуют Т-В, это непрерывные улучшения. По своей природе такие улучшения происходят медленно и на первый взгляд незаметно, так что сразу после внедрения каких-либо существенных перемен не наблюдается. А изменения, с самого начала проводимые принудительно, могут продолжаться лишь до определенного предела.
Порой предлагается альтернативный способ, известный как реинжиниринг бизнес процессов (Business Process Re-engineering, BPR). Данный метод заключается в переоценке компании в целом или отдельной ее части, при этом во главу угла ставятся цели, а текущее состояние роли не играет. Иными словами, происходит поиск оптимальной структуры. Это, конечно, ничем не отличается от системного инжиниринга – подхода, появившегося еще в 1960-х гг., и новый метод имеет те же недостатки, а именно:
•Умение проектировать. Постепенное изменение чего-то, что работает, скорее всего, не приведет к катастрофе. Полностью новая разработка вполне может оказаться неудачной.
•Сопротивление переменам. Продиктованные изменения редко когда принимаются столь же охотно, как принятые путем переговоров. Сопротивление может быть достаточно сильным, чтобы загубить все новшества, даже если теоретически они верны.
•Скорость обучения. Даже при активной поддержке и участии персонала совершенно новой организации требуется время, чтобы прийти в себя и успокоиться.
В любом случае, за незаметность изменений критикуют только внедрение Т-В на оперативном уровне. Если идея сокращения потерь в самом широком их понимании и принцип непрерывных улучшений применяются на стратегическом уровне, во многих организациях произойдут заметные, кардинальные перемены [1].
Многое из рассмотренного материала можно отнести к преимуществам системы Т-В, некоторые моменты были отмечены как недостатки. Тем не менее, для полной ясности рассматриваемой проблемы желательно их конкретизировать.
Преимущества системы «точно в срок»:
•сокращение запасов (сырья, полуфабрикатов и готовой продукции);
•сокращение площадей;
•высокая пропускная способность;
•активное участие и повышенная мотивация рабочего;
•спокойный ритм работы;
•высокие прибыль и производительность;
•высокое качество обслуживания;
•высокая гибкость системы;
•своевременная доставка.
Недостатки системы «точно в срок» количественно менее выражены, но их качественная сторона настолько серьезна, что в нынешних экономических условиях в нашей стране их применение ставится под сомнение:
245
•низкие запасы означают, что такие сбои, как поломка станка, могут вызвать остановку всего процесса. Необходимо придерживаться установки на техническое обслуживание всех станков, которое гарантирует сведение всех проблем к минимуму;
•введение системы может потребовать огромных изменений, достичь которых на практике трудно. Система ставит серьезные задачи перед всеми сотрудниками, наделяя полномочиями и ответственностью операторов, полагая, что они могут овладеть многими навыками и будут охотно помогать друг другу в случае возникающей необходимости; роль менеджеров претерпевает такие изменения, которые многие расценят как потерю личной власти.
Опыт показывает, что стратегия JIT является универсально применимой в условиях стабильного и предсказуемого спроса. Система не учитывает сезонности и не оставляет возможности для метода погони за спросом. Ее реализацию сдерживают такие важные факторы, как неудовлетворительное качество продукции, нарушение сроков поставки и оплаты за товар, ошибки и сбои в передаче информации между заказчиком и поставщиками, что в условиях Украины в настоящий период встречается довольно часто.
Вследствие слабости контрольной системы в Украине стратегия кратковременных запасов характеризуется высокой степенью риска, хотя и минимизирует размер оборотных средств. Рассчитывать на реализацию в Украине систем типа «точно в срок» вряд ли возможно при сложившемся уровне договорно-правовой культуры менеджмента и требований производственного поведения работника. Успех в реализации стратегии зависит также от количества и территориальной дислокации поставщиков, уровня их ответственности при выполнении договорных обязательств. Поэтому многие компании, несмотря на привлекательность стратегии JIT, пользуются иными стратегиями, обеспечивающими управление материальными и товарными ресурсами.
Данному суждению в значительной мере способствует и другая система, получившая широкое распространение в последние годы, – логистика, объединяющая в себе комплекс проблем материально-технического обеспечения и управления.
12.4. Логистические решения и процессы материального обеспечения
Одним из приемов, направленных на сокращение производственных потерь, является совершенствование и развитие цепочек материально-технического снабжения и производственных процессов на базе применения современных логистических методов. Процесс перехода на новые изделия или новые технологии весьма болезненный период в жизни организации. В этот период любые неувязки производственного характера, а таковых на данном, не отлаженном, этапе предостаточно, что моментально отражаются на общем экономическом состоянии организации.
Эффективность проведения в предпринимательской деятельности теории логистики ложится, в первую очередь, на ускорение материальных потоков и возможности снижения совокупных затрат на производство и реализацию продукции.
Логистика (logistics) – наука о планировании, контроле и управлении транспортированием, складированием и другими материальными и нематериальными операциями, совершаемыми в процессе доведения сырья и материалов
246
до производства, внутрипроизводствен внутрипроизводственной переработки сырья, материалов и полуфабрикатов. Она решает вопросы доведения готовой продукции до потребителя в соответствии с его интересами и требованиями, а также передачи, хранения и обработки соответствующей информации. Это одно из определений логистики как новой отрасли знаний в области менеджмента, получившей широкое распространение в последнее время.
Основное внимание практического использования логистики должно концентрироваться на ключевых фазах производственного процесса, то есть на материальных поставках, транспортировке и производстве. Это означает, что именно эти функциональные сферы способствуют проектированию новых логистических решений.
Роль материально-технического снабжения постоянно возрастает в последние годы, усиливается также его влияние на все сферы хозяйственной деятельности производства особенно в период перехода на новые продукты и технологии. Связано это с повышением требований потребителей к цене и качеству, с возросшим количеством многих ресурсов, с увеличением требований большего объема информации о соответствующих рынках для прогнозирования цен на материалы и их предложение.
Изменились также условия поиска и выбора поставщиков. Менеджеры отдела мате- риально-технического снабжения участвуют в заключении долгосрочных союзов с поставщиками и оценке их возможного вклада в развитие производства на перспективу. Профессиональные менеджеры службы снабжения участвуют в обсуждении новых технологий производства и продуктов с точки зрения новых возможностей и принятия решений.
Все эти особенности требуют дальнейшего развития цепочек материальнотехнического снабжения и создания бизнес процессов, базирующихся на систематизированном методе вовлечения отдельных взаимосвязанных элементов в общий логистический процесс для предотвращения неэффективного использования всех видов ресурсов [3].
Логистический процесс охватывает широкий спектр функциональных областей – от управления закупками сырья и материалов до передачи готовой продукции заказчику.
Объекты упомянутых функциональных сфер, способствующих проектированию и внедрению логистических решений, приводятся в таблице 3.6, с указанием их применимости в процессе менеджмента.
Таблица 3.6.
Перечень объектов логистических решений в менеджменте
247
|
Основные объекты логистических |
Применимость в менеджменте |
||
|
Стратегиче- |
Тактиче- |
Оператив- |
|
|
решений |
|||
|
ский |
ский |
ный |
|
|
|
|||
1. |
Выбор материалов, частей и узлов |
++ |
+ |
– |
2. |
Выбор технологий |
++ |
+ |
+ |
3. |
Выбор поставщиков |
+ |
++ |
+ |
4. |
Концепция транспортировки и складирова- |
+ |
++ |
+ |
|
ния в поставках |
+ |
+ |
++ |
5. |
Планирование производственного процесса |
|||
6. |
Управление и регулирование производст- |
– |
+ |
++ |
|
венного процесса |
|
|
|
|
|
|
|
|
Перечисленные объекты в большей или меньшей мере рассматриваются на различных стадиях менеджмента. Наибольшая значимость тех или иных объектов для указанных видов менеджмента помечена двумя крестиками.
Отмеченные процессы (объекты), которые рассматриваются на различных временных отрезках, не дублируются, а углубляются и уточняются в зависимости от назначения того или иного вида менеджмента. Больше того, трудно однозначно и четко выделить, что именно этот процесс является объектом, например, тактического менеджмента. Это происходит потому, что объекты находятся под влиянием целого ряда слабо структурированных факторов, например:
•время реакции конкурентов на запросы клиентов;
•смена уровня промежуточного снабжения;
•колебание жизненного цикла изделия под воздействием поведения потребителей;
•формирование предложений логистических услуг;
•рост уровня затрат собственного производства;
•динамика цен в снабжении, инвестиционных процессах, в сфере ло-
гистических услуг.
Слабая структуризация перечисленных факторов влечет за собой интуитивные подходы к решению ряда логистических задач. В то же время, по мне-
248
нию многих специалистов логистики, компьютеры – один из факторов, который в значительной мере содействовал побуждению интереса к логистике.
В этой связи, считаются эффективными методы оптимального взаимодействия – человек-машина, которые базируются на использовании интуиции, знаний и опыта человека, его понимание проблемы и способности компьютеров быстро обрабатывать имеющуюся информацию.
Практически любая задача, изложенная в таблице 3.6 в качестве объекта логистических решений, требует такого единения и применения на практике, поэтому имеется прямой смысл попытаться сформировать основные цели и инструменты (средства) их достижения в отдельную таблицу (табл. 3.7).
Таблица 3.7.
Цели и средства объектов логистических решений
Объекты логистиче- |
|
Цели решений |
Методические средства (инструменты) |
ских решений |
|
проектирования логистических решений |
|
|
|
|
|
1 |
|
2 |
3 |
1. Выбор материалов, |
Выбор для: |
АВС – анализ |
|
частей и узлов. |
• |
Собственного производства; |
XYZ - анализ |
|
• |
Производства со стороны; |
Методы математического программиро- |
|
Балансовое использование производст- |
вания |
|
|
венных мощностей. |
Балансовый метод расчета и использо- |
|
|
|
|
вания мощности |
|
|
|
|
2. Выбор технологии. |
Ресурсосберегающие технологии. |
Организационно-экономическое сравне- |
|
|
Ресурсы в зависимости от среднего |
ние технологий |
|
|
размера заказа. |
|
|
3. Выбор поставщи- |
Установление надлежащего произво- |
Расчетная матрица стоимостных оценок, |
|
ков. |
дителя (поставщика). |
методы математического программиро- |
|
|
|
|
вания |
|
|
|
Экспертные оценки |
|
|
|
|
4. Концепция транс- |
Формирование грузопотоков. |
Матрицы |
|
портировки и склади- |
Маршрутизация перевозок. |
Линейное программирование (транс- |
|
рования в поставках. |
Подбор транспортных средств. |
портная задача) |
|
|
График движения транспорта. |
Матричный метод |
|
|
Оптимизация складских операций. |
Математическое программирование |
|
|
|
|
|
5. Планирование про- |
Установление заказа внутри предпри- |
Оптимизация величины партии |
|
изводственного про- |
ятия. |
Табличные методы расчета стоимостных |
|
цесса. |
Выбор и формирование заказов: |
оценок |
|
|
• |
по желанию клиентов |
Матричные методы |
|
• |
блочные (партионные) заказы кли- |
Анализ ситуации |
|
• |
ентов |
|
|
безымянные заказы |
|
|
6. Управление и регу- |
Сокращение технологического про- |
Разделение партий |
|
лирование производ- |
цесса. |
Система «Канбан» |
|
ственным процессом |
Сокращение и гармонизация производ- |
Операционный и ситуационный анализ |
|
|
ственного процесса. |
|
|
|
|
|
|
249

Оптимизация и решение этих задач зависит от конкретной ситуации, исходных данных, условий и требований к эффективной работе логистической системы, а также проблем, связанных с обеспечением производства сырьем и полуфабрикатами, с устранением узких мест в технологии доставки различных видов продукции в пункты производства, складирования и сбыта. Например, на предприятиях с конвейерной системой технологического процесса установленный темп производства сохраняется при условии, если на входе сырье подается на поточную линию постоянно в нужном количестве и отсутствуют сбои в транспортировке, которые могут быть вызваны скоплением готовой продукции на выходе. Здесь примером могут служить заводы фирмы TOYOTA, на которых запас комплектующих позволяет проработать 2 часа при возможных сбоях. На предприятиях, работающих в дискретном режиме, необходимо также учитывать колебания поставок, создавая гарантийный запас для сглаживания этих колебаний.
Компьютеризация различных звеньев логистической системы, подключение их к единой информационной сети (обладающей высокой скоростью передачи данных и позволяющей эффективно работать с удаленными терминалами) позволяет отслеживать движение груза, контролировать транспортные потоки и доставлять груз точно по графику. А модернизация и компьютеризация системы «Канбан» позволяет более эффективно управлять самим производством, что является весьма важным обстоятельством на стадии оперативного управления производством*.
Функции логистики формируются из логистических элементов (мероприятий), которые образуют структуры логистических цепей, объединяемых общим управлением. Основными в логистике являются координационные функции, помогающие не увеличивать дохо ды, а сокращать затраты на основе их системного анализа и выбора оптимальных логистических решений из множества возможных вариантов.
Менеджерам по логистике ставится цель: обеспечить такое управление всеми звеньями технологического потока переработки исходных ресурсов в товары, чтобы каждая единица товара была поставлена покупателям в полном соответствии с договором, кон-
трактом. Критерий достижения цели – обеспечение требуемого рынком уровня обслужива-
ния потребителей.
* Здесь подробно рассмотрены лишь отдельные фрагменты логистики. Более подробно с данной проблемой можно ознакомиться в источниках [4,5] прилагаемого перечня литературы.
250