
Сборник статей международной лин-конференции От эффективных лин-процессов к идеалам производственной системы
.pdfдо производственного мастера, таким образом, в системе руководитель может отслеживать фактическое выполнение планового задания.
Вусловиях нестабильного рынка и постоянно меняющихся предпочтений потребителей очень важно уметь вовремя реагировать и перестраивать свое производство в соответствии с существующей потребностью. Для того чтобы быть способным вовремя среагировать, многие предприятия создают большие запасы. Но наличие больших запасов совершенно противоречит философии бережливого производства (lean manufacturing). Большие запасы – это замороженные средства, которые предприятие может использовать на свое развитие, вместо этого оно тратит деньги на их содержание: свет, отопление, складские работники, ПО, утилизацию в случае их устаревания. Как уже было озвучено ранее, Cyber-монитор позволил нам увидеть, где происходят максимальные потери, связанные с простоем оборудования. Большую долю занимает время, связанное с переналадкой,
ивопрос снижения времени переналадки был самым важным.
Всвоей работе мы использовали один из инструментов Лин – SMED (single minute exchange of dies – быстрая замена штампа) или быстрая переналадка. Прародителем этого направления был Сигео Синго – японский инженер. Несколько десятков лет ушло у него на формирование данной концепции. Нам осталось взять уже отработанные приемы и применить их к своему производству.
Основными преимуществами, которые получает предприятие после применения быстрой переналадки, являются:
Сокращение времени производственного цикла, продукция быстрее поступает к своему потребителю;
Сокращение запасов продукции, что влечет сокращение затрат на ее хранение. В случае изменения потребительского спроса можно быстро перейти с детали на деталь, и потребность в дополнительных запасах исчезает;
Изготовление продукции малыми партиями, большое разнообразие изготавливаемой продукции.
Первым проектом по быстрой переналадке был реализован на участке станков IVS 200. До начала проекта время, затрачиваемое на переналадку, доходило до целой смены, а это 12 часов.
Проект проходил в несколько этапов. Первым этапом было проведение хронометража операций переналадки с помощью видеокамеры. Были зафиксированы все действия, требуемые выполнения при переналадке, определено время, затрачиваемое на них, кроме того, выделены потери, препятствующие ее быстрому выполнению.
После проведения анализа полученного времени, все действия разделили на две группы: внутренние, те, которые обязательны для выполнения при выключенном оборудовании, и внешние, те, которые допускается выполнять при работающем станке.
71
К внешним действиям отнесли все операции, связанные с подготовкой оснастки, измерительного и режущего инструмента, инструмента, используемого при переналадке, загрузку заготовки на приемник, поиск и подготовку документации. К внутренним отнесли все операции, связанные с заменой оснастки, режущего инструмента, настройкой.
Нужно помнить, что переналадка не считается законченной, пока не будет получена годная деталь.
После проделанных мероприятий по делению действий на внешние и внутренние был проведен повторный хронометраж. Исключение подготовительных действий из времени переналадки уже позволило сократить ее на 30 %. Теперь все подготовительные действия требовалось выполнять еще до остановки станка, во время обработки деталей предыдущего наименования.
Для оптимизации внутреннего времени был организован ряд мероприятий:
Унификация оснастки. Одна и та же оснастка может быть использована для нескольких наименований деталей, что также сокращает время на ее замену.
Использование универсальной управляющей программы СПУ.
Использование мобильных тележек наладчиков, укомплектованных всем необходимым. Сокращает время, затрачиваемое при перемещении от одного станка к другому.
Для оптимизации внешнего времени переналадки:
Расположили оснастку в сортовиках в зависимости от деталей, для которых она используется.
Необходимый измерительный инструмент комплектуется в специальные коробки работниками БИХ заранее, теперь нет необходимости искать его по всему складу.
Весь необходимый режущий инструмент находится под рукой. Результатом проведенной работы стала матрица переналадки, демон-
стрирующая время, затрачиваемое на переходы с детали на деталь, а также стандартный перечень операций наладчика, необходимых для выполнения при переналадке. Это позволило обеспечить единообразие подходов к выполнению переналадки, а также постоянно проводить мониторинг затрачиваемого времени и анализ в случае отклонения от нее.
Важнейшим этапом при реализации проекта «быстрая переналадка» является обучение наладчиков установленной процедуре. Только хорошее обучение может гарантировать соблюдение наладчиками установленных правил и понимание в необходимости деления действий на внешние и внутренние.
Результатом проведенного проекта стало сокращение времени до 16 минут, а по каким-то деталям оно и вовсе равно нулю.
72
Как можно было заметить, внедрение принципов быстрой переналадки требует обязательной организации рабочих мест по принципам 5С.
Для оценки эффективности работы оборудования на нашем предприятии используется показатель ОЕЕ (общая эффективность оборудования). На данный показатель оказывают влияние все виды простоев, будь то ППР, аварийный ремонт, переналадка, плохая эффективность работника, низкое качество продукции. При увеличении времени, затрачиваемого на переналадку, коэффициент ОЕЕ снижается. По результатам 2014 года среднее значение показателя ОЕЕ по станкам IVS-200 составило 87,9 %.
Несмотря на то, что нами были достигнуты значительные результаты в данном направлении, мы не планируем останавливаться на достигнутом, а будем стремиться к их повсеместному внедрению.
Савлов Алексей Николаевич, главный технолог ЗАО «Новомет-
Пермь». E-mail: Savlov@novomet.ru
73
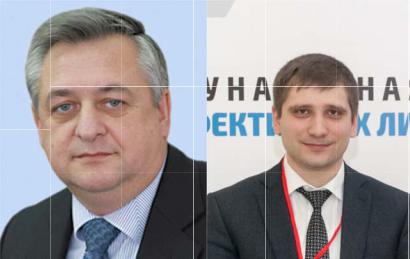
О перац ионнаясистема Мотовилихи нских заводов. Опыт внедрения
Клочков Юрий етрович , Жиленков Арт м Владимирови ч
Суть современ-
ных по |
пулярных под- |
||
ходов по совершен- |
|||
ствованию |
процессов, |
||
в боль шинстве своем, |
|||
заключается в иденти- |
|||
фикации, |
оценке и |
||
устранении |
|
потерь, |
|
возникающих на каж- |
|||
дом этапе |
производ- |
||
ства. В операц онной |
|||
системе |
ПАО |
Мото- |
|
вилихинские |
з воды» |
||
(далее ПАО « МЗ») основными инструментами решения |
таких вопросов |
||
являются следующие выбранные нами направления работ: |
|
|
|
непрерывные улучшения – для развития производственной
культ ры, выявления и устранения пот рь путе вовлечения персонала
подразделений в проце с подачи |
предло жений, н правлен ных на улучше- |
ние рабочих м ст, производстве |
ных процессов, повышения качества про- |
дукции, снижения материальных затрат;
инструмент ы организации рабочих мест с с озданием оптимальных условий выполнения операций – для повышения произво ительности труда и предотвращения возможных травмо пасных ситуаций;
обслуживан е оборудования с вовлечением основного пр изводственного персонала, работающего на данном обор довании – для снижения
длите ьности простоев оборудования и снижения расходов на эксплуатацию и ремонт оборудования на протяжении все о жизненного цикла;
вс роенное качество – для снижения потерь от брака;
|
стандартизированная работа для повышения произво итель- |
|
ности труда; |
|
|
|
картирование процессов – для выявления потер ь в процессах. |
|
Первым шаг, который мы сделали на пути внедрения операц ионной |
||
систе ы – это разработ а стратегию развития OSM до 2020 года. При под- |
||
готовке данного документа мы |
использовали пер довой о пыт отеч ствен- |
|
ных и |
зарубе жных компаний, |
которые имеют высокие достижения во |
внедрении производств нных систем.
Для обеспечения ояльности и вовлечения с трудников ПАО МЗ» в процесс внедр ния и развития O SM была подгот влена и утверждена де-
74
кларация об операционной системе, определяющая основу OSM: постоянное совершенствование процессов на базе новой философии, инструментах и методах бережливого производства.
Декларация содержит основные принципы работы и обязательства администрации перед персоналом компании, важнейшими из которых являются:
Личным примером демонстрировать приверженность принципам операционной системы;
Обеспечивать условия, способствующие постоянному развитию, улучшению всех процессов предприятия;
Мотивировать персонал к достижению целей предприятия.
На основе стратегии в нашей компании ежегодно утверждаются цели развития операционной системы «МЗ» (далее OSM), которые декомпозируются до уровня каждого работника компании, что позволяет повысить вовлеченность персонала компании в судьбу предприятия.
Важным шагом для организации активного участия персонала в OSM организовано непрерывное обучение всех категорий работников основным методам и инструментам OSM.
Инструменты и методы осваиваются персоналом постепенно по схеме «от простого – к сложному». К примеру, проводится обучение по 5S, затем данный инструмент осваивается на практике, внедряется на рабочих местах эталонного участка. После внедрения на эталонном участке команда переходит к следующему инструменту и т.д.
Кроме того, активно используется каскадный метод обучения персонала, когда сотрудники уже прошедшие обучение делятся знаниями и навыками использования инструментов в своих коллективах, тем самым вовлекая и еще не охваченную обучением часть персонала.
Для распространения философии и опыта внедрения инструментов «Бережливого производства» и изучение лучших практик было принято решение организовать ЛИН-клуб. Работа клуба проходит в формате дискуссий, обсуждаются актуальные вопросы внедрения инструментов и методов Бережливого производства. Кроме того работа ЛИН-клуба – это еще и отличная площадка, где можно поговорить о проблемах, с которыми сталкиваются проектные команды внедряя инструменты OSM, а также изучить лучший опыт и решения коллег с других подразделений.
Регулярно проводятся аудиты по культуре производства. Внедрен еженедельный обход ГД эталонных участков. Внедряется система встроенного качества. Внедряется стандарт управления SFM (управление из мест создания ценности).
Работа по внедрению 5S предполагает 3-х ступенчатую систему оценки рабочих мест:
самооценка рабочего места рабочим;
оценка мастером;
75
обход начальника цеха.
В рамках проведенной работы по реализации системы ТРМ (Всеобщего обслуживания оборудования), через вовлечения основного персонала в самостоятельное обслуживание оборудования, а также сокращение всех видов потерь при работе оборудования повышается эффективность работы оборудования.
Организована работа по реализации системы встроенного качества: осуществляется реализация принципа«3НЕ», Не принимай, Не делай, Не передавай брак. Разрабатываются стандартные операционные карты на рабочие места основного персонала и работников службы ОТК.
Одним из основных стандартов, а, может быть, и основополагающим является стандарт управления из мест создания ценности или Shop Floor Management (SFM). Это система оперативного управление предприятием на основе ключевых показателей эффективности (KPI), имеющая несколько уровней управления: бригада, цех, завод, компания. Показатели распределены по пяти основным направлениям: безопасность, качество, исполнение заказа, затраты, корпоративная культура. На каждом уровне управления дважды в день проводятся оперативные совещания, где выявляются отклонения от показателей, определяются основные причины отклонений
ипринимаются оперативные меры по их устранению. Очевидно, что чем раньше выявлена проблема, тем проще и быстрее вернуть процесс к заданным параметрам.
Именно личная заинтересованность и поддержка первых руководителей компании позволяют проводить изменения в компании. На регулярной основе проводятся еженедельные обходы генеральным директором и первыми руководителями компании эталонных участков, где рассматриваются результаты и достижения проектной команды по реализации проектов, обсуждаются дальнейшие шаги реализации проекта, и, что самое главное, рассматриваются проблемы, возникающие при реализации проекта, и оказывается поддержка по их решению.
По каждому внедренному инструменту бережливого производства разрабатывается нормативный документ (положение, методика, процедура).
Т.е. при внедрении инструментов OSM используется принцип PDCA (планирование внедрение и обучение персонала, внедрение инструмента, подтверждение достигнутых результатов, стандартизация лучшей практики), а далее цикл повторяется и мы выходим на следующую ступень.
Как известно, кроме основных 7 видов потерь, можно выделить еще
ивосьмой вид потерь – это неиспользуемый потенциал работников предприятия. Одним из шагов для раскрытия и использования этого потенциала является функционирующая система подачи и внедрения кайдзенпредложений. Что такое кайдзен-предложение? По сути – это мелкие улучшения, которые работник может реализовать на своем рабочем месте,
икоторые приносят небольшой эффект, но при внедрении существенного
76
количества данных предложений (счет идет на тысячи предложений в год) мы можем получить значительный результат по повышению производительности труда, повышению качества выпускаемой продукции, снижении времени выполнения заказа и т.д.
В соответствии со стратегией развития OSM к 2020 году мы планируем достигнуть семи предложений на 1 работника компании в год, а это более 40 тыс. предложений в год.
Клочков Юрий Петрович, Генеральный директор ПАО «Мотовилихинские заводы»,
E-mail: mz1@mz.perm.ru
Жиленков Артем Владимирович, Председатель Комитета развития операционной системы ПАО «Мотовилихинские заводы», г. Пермь.
E-mail: zhilenkov_av@mz.perm.ru
77
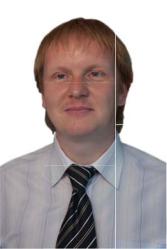
Система моти |
ации персонала в рамках развития |
производс |
венной системы ОА «Сорбент» |
Млахов Дмитрий Аркадьевич
Всентябре 2012 года на предприятии появил-
ся отдел развития производственной системы. Причин появления несколько: научить персонал рационально использовать ресур ы (в то м числе время),
привить и нновационное мышление, направленное на поиск идей для улучше ия, навести порядок во всех подразделениях.
При создании отдела и формировании произ-
водственной системы компании, одним из |
первых |
встал вопрос о том, как вовлечь пер сонал ко |
пании |
в процесс улучшении. |
|
Для этого решили не внедрят ь отдел ные и разрозненные инструменты Бережливого производства. П ошли путем создания нормативной базы, в рам ках развития производственной системы. Был нужен базис. Опора, на которую можно был бы опе реться в работе. Для решения этой задачи отдел м РПС за короткий проме жуток времени был написан стандарт организации «Разв тие производственной системы».
При создании документа была организована дискуссио ная площадка. |
|
Кажд |
й мог вы сказать амечания к документу, ук зать те пункты, которые |
нужно |
внести или доработать. Б ыли случаи, когда приходилось загляды- |
вать в толковые словари и догов риваться о значении слов. Изначал но это сложно было даже представить.
В результате появился жизнеспособный стандарт «Р азвития произ-
водст енной с стемы». В нем описаны различны |
инстру менты бережли- |
вого производства в ви е четких и кратких инстр |
кции. Примеры, шабло- |
ны, графики, показател , организационны е вопросы. Пропи сана четкая ответственность. Весь стандарт по лучился объёмом 55 страниц! Это очень важно для пер онала компании, поскольку объем ые документы («мемуары») трудно читаются и запоминаются.
Далее для закреп ения, изучения и внедрения станд |
арта по разви- |
тию производственной системы» , было дано время для его |
изучения. Был |
проведен срез наний (тестирование) всего ИТР компании |
по знани ю стан- |
дарта. При проведении тестирования пользоваться станд |
артом бы ло за- |
прещено. Таким образом, сформировался первый столб пр |
оизводственной |
систе ы нашей компании. По сути – это конституция ком пании по развитию производственной истемы, фундамент, база.
Встал вопрос: «С андарт – это хорошо, но как запустить в действие то, чт о в нем заложено и написан о?». Для решения этой задачи, пар ллель-
78
но началась работа по созданию положения «О подаче предложении по улучшениям». Более года мы учили персонал компании умению оформлять и подавать свои мысли по улучшению на бумаге. Но самом деле, этот процесс оказался совсем не простым. Нужно было сломать такие стереотипы сотрудников, как: «А для чего писать?», «Зачем, кому это надо?». Первоначально предложение по улучшению, принятое к реализации и реализованное, стоило 100 рублей. Мы принимали любые предложения. Цель была одна – приучить людей к формулированию своих мыслей на бумаге и их подаче. Помимо прочего, с сотрудниками велась разъяснительная работа и пропаганда, что мало написать предложение по улучшению, его нужно суметь реализовать.
Сотрудники часто подавали предложения очень затратные для реализации, а порой – и невыполнимые. Это постройка новых производственных корпусов, покупка дорогостоящего оборудования, всевозможные ремонты, повсеместные системы кондиционирования. Но, к сожалению, такие предложения по улучшениям, даже в долгосрочной перспективе, не принесли бы пользу компании.
После года работы с предложениями по улучшению, когда персонал компании понял и научился писать, подавать и реализовывать их, было принято решение о доработке положения. Ужесточились критерий признания. Возросла и стоимость подачи предложения – 300 рублей. Нужно отметить, что процент реализации предложении по улучшениям – более 95 %. При ежегодной подаче – более тысячи предложений.
Но и этого было мало. Стандарт по развитию производственной системы – это хорошо. Положение «О подаче предложении по улучшениям» – тоже. Но остается вопрос о том, как сделать процесс в рамках развития производственной системы стабильным, постоянным и необратимым? Для решения это задачи была разработана «Методика расчета премии за развитие производственной системы». С помощью положения «О подаче предложении по улучшениям» был реализован принцип подачи идей. Методика стала самым настоящим KPI подразделений. В ней четко прописаны (с помощью балльной системы) все виды деятельности в рамках развития производственной системы.
Каждому подразделению компании, ежемесячно необходимо набрать минимальный нижний порог баллов, максимум – не ограничен. После этого происходит ежемесячная защита подразделений о проделанной работе (в виде презентации Power Point). Руководители подразделений защищаются перед комиссией, в состав которой входят все директора компании.
По результатам защиты руководители подразделений могут поощрять работников, участвующих в реализации мероприятии по развитию производственной системы. Размер поощрения или премии по бережливому производству напрямую зависит от набранных баллов. 1 балл равен одной тысячи рублей. Рекорд одного из рабочих – это 22 тысячи рублей.
79
Данные выплаты полностью контролирует отдел РПС. Это необходимо для того чтобы премия выплачивалась только участникам преобразований, в рамках развития производственной системы.
С помощью трех нормативных документов в компании ОАО «Сорбент» появилась самая настоящая система мотивации персонала в рамках развития производственной системы. Все стало прозрачным, четким и действенным. Появился целый механизм работы. Это позволило запустить процесс преобразований в компании. На данный момент времени система функционирует без сбоев. Тем не менее, отдел РПС, не стоит на месте. Он ищет новые вариации, механизмы, алгоритмы для своей работы и компании в целом. Принцип один - совершенству нет предела.
Малахов Дмитрий Аркадьевич, начальник отдела развития ПС. E-mail: mda@sorbent.su
80