
Сборник статей международной лин-конференции От эффективных лин-процессов к идеалам производственной системы
.pdfразных подходов дают разные решения вопросов снижения себестоимости и повышения прибыли. Рассмотрим различия двух подходов.
Подход неизменной себестоимости
Это наиболее простой и распространенный способ формирования и оценки прибыли компании, когда в зависимости от имеющихся затрат и желаемой прибыли формируется цена на продукцию и продукт с определенной таким образом ценой выходит на рынок.
Цена продажи = Себестоимость + Прибыль, где
Прибыль определяется из желаний компании и рынка К сожалению, в условиях современной экономики и развивающегося
рынка, данный подход не раскрывает внутренний потенциал компании для ее дальнейшего роста и развития. В результате компании не зарабатывают прибыль, а начинают постепенно её терять, теряя потенциальных клиентов своего сектора рынка.
Подход управляемой себестоимости
В данном подходе формирование цены на продукт происходит после анализа цен на рынке в соответствии с покупательским ожиданием клиента. После определения цены на продукт, в соответствии с диктуемыми условиями рынка, идет оценка всех затрат и соответственно считается та прибыль, которая получится в результате реализации продукции.
Прибыль = Цена продажи – Себестоимость, где
Прибыль – получаемая величина в зависимости от затрат компании Мы понимает, чем ниже будет себестоимость (затраты) компании при изготовлении продукции, тем, соответственно, больше будет прибыль
от реализации. Но как этого достигнуть?
Здесь тоже есть несколько вариантов решения, и компании вправе сами выбирать тот путь, по которому двигаться дальше, но надо понимать, что результаты будут тоже различные.
Первый вариант – снижение цены на закупное сырье, материалы и комплектующие. Снижение цены на закупной материал может привести к ухудшению качества или срыву сроков поставки и, в реальности привести не к сокращению затрат, а к их увеличению.
Второй вариант – сокращение накладных расходов: сокращение затрат, связанных с поддержанием чистоты, сокращение затрат на ремонт и обслуживание оборудования и инструментов, оснастки и т.д. Это также приводит к тому, что на бумаге сокращение затрат приводит к большим затратам на производстве (ухудшается качество продукции, простои оборудования, связанные с его поломками и т.д.)
Третий вариант – сокращение фонда оплаты труда сотрудников компании. Менеджмент компаний довольно часто идёт по этому пути, так как доля заработной платы в общей себестоимости составляет 20-40 %. В итоге, компания лишается самых квалифицированных работников. Начинаем
61
тратить дополнительные деньги на исправление, доработку процессов на обучение нового сотрудника.
Четвертый вариант – сокращение времени цикла изготовления продукции. Влияние цикла изготовления деталей на затраты рассмотрим на примере следующей задачи:
Коммерческое подразделение заключает договор на изготовление детали А за 10 дней. Затраты на сырье и зарплату основных рабочих (условно переменные затраты) составляют 100 рублей. Затраты на электроэнергию, аренду, зарплата вспомогательных работников, ИТР и руководителей (условно постоянные затраты) составляют 10 рублей в день. Цена реализации по договору 220 руб.
Какую прибыль получит компания при выполнении заказа в срок, в случае задержки и выполнении только к 13 дню и с опережением?
Решение:
Формула себестоимости следующая:
Себестоимость = Пост +Пер, где
Пост – условно постоянные затраты, Пер – условно переменные затраты, тогда:
Если компания выполнит договор в срок: Себестоимость = 100+10х10=200 руб. Прибыль = 220 руб.-200 руб.= 20 руб.
Если компания выполнит договор за 13 дней, то: Себестоимость = 100+10х30=230 руб. Прибыль = 220 руб.-230 руб.= -10 руб. Такой результат получается за счет увеличения условно постоянных затрат или увеличения времени цикла изготовления продукции (вместо 10 дней продукция изготавливалась 13).
Если компания изготовила продукцию раньше за 8 дней:
Если договор уже заключен, несмотря на то, что мы изготовили продукцию раньше, она все равно до 10 дня будет находиться на территории компании и компания будет два дня нести условно постоянные затраты. Поэтому себестоимость будет учитывать условно постоянные затраты из расчета количества дней до отгрузки клиенту.
Себестоимость = 100+10х10 = 200 руб. Прибыль = 220 руб.-200 руб. = 20 руб.
Но мы видим, что если мы сократим время цикла изготовления продукции (общее время прохождения продукции через все стадии производственного цикла от начала работы с сырьем и материалами до стадии готовности к отгрузке продукции) до 8 дней и при заключении следующего договора учтем полученный результат, это позволит нам получить увеличение прибыли компании до 40 рублей.
Себестоимость = 100+10х8 = 180 руб. Прибыль = 220 руб.-180 руб. = 40 руб.
62
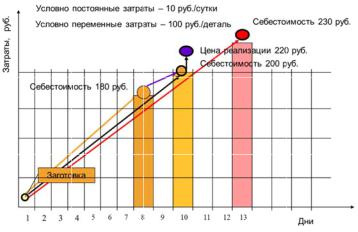
Рис. 1. Расчет себестоимос и
Таким образом, д я увеличения прибыли компании необходи о уделять особое внимание снижени ю себестоимости (сокращению издержек)
путем сокращения врем ени цикла изготовления |
родукции. Чем быстрее |
|
компания изготавливает |
продукц ию, тем меньше |
ебестои мость изделия и |
тем больше разница ме |
ду цено й реализации и себестоимостью, а значит и |
|
прибыль компании. |
|
|
В таком случае в зникает вопрос о том, что влияет на время производст енного ц икла и какие действия позволяют его сократить? Рассмотрим формулу времени производственного цикла изготовления продукции:
Время производственного цикла = время обработки + время задержки дви жения продукции по процессу (ме жоперационные о жидания и запасы, переналадка обору ования, транспортировка, поломка оборуд вания, исправление дефектов и т.д.) + время задержки информации (подготовка производственного задания).
Рассматривая данную формулу, мы видим , что не все действия направлены на основной процесс изготовления изделия. Существу т действия, не создающие ценность в работе – время задержки продукции и информации по процессу. Такие действия азываются потерями, они и увеличивают время производственного цикл . Выявление и устранение потерь в процессе изготовления продукции поз олит в будущем выпуска ь продукцию быстр е и соответствен о, полож ительным образом влиять на сокращение себе тоимости и увеличение прибыли компании.
Устранение потер и сокращение производственного цикла позволяет, также, повлиять на производительность п оцесса. Она возрастет, т.к. становится возможн ым изготавливать ольший объем продукции за тот же промежуток времени. Данный подход к повыш нию производительности азывается результативным – максимальный результат приминимальных усилиях.
К сожалению, в настоящее время в вопроса повышения про зводительности прим еняют продуктивный подход – дов льно крупный результат при н померно тяжелых усилиях (сверхурочная работа, работа быстрее лю-
63
быми путями, работа без выходных). Такой подход позволяет получить результат в сиюминутный момент времени, но в перспективе на стабильный результат данный подход оказывает только обратный эффект. Изношенное оборудование, измождённые сотрудники – вот результат такой работы.
Поэтому цель повышения производительности состоит в снижении себестоимости выпускаемой продукции путем устранения потерь и сокращения цикла изготовления, а не беспощадной эксплуатацией оборудования и людей. Однако, занимаясь повышением производительности процессов, необходимо применять комплексный подход, учитывать влияние человека, оборудования и всей системы управления. Поэтому на производительность
вкомпании будут оказывать влияние индивидуальная производительность (Пи), организационная производительность (По) и техническая производительность (Пт).
Втаком случае Производительность можно выразить с учетом трех составляющих:
П= Пи х По х Пт
Данный подход к производительности позволяет понять, что повысить производительность в компании, воздействуя лишь на какой-то один ресурс – невозможно, например, только оборудование, закупая новое оборудования повышать техническую производительность, а необходимо уделять внимание и индивидуальной и организационной производительности
втом числе.
Впервые такую задачу повышения производительности смогли решить в японской компании «Тойота» благодаря тому, что сформировали и внедрили свою Производственную системы T-TPS (Всеобщая производственная система Тойоты), где активное применение персоналом инструментов Бережливого производства позволяет воздействовать на все три направления и получать максимальный эффект.
Также необходимо учитывать, что Производительность процесса – это произведение производительности всех рабочих мест, поэтому для получения большей результативности необходимо начинать работу по совершенствованию с так называемых «узких мест» (рабочие места, имеющие самую низкую производительность). Производительность, в свою очередь, прямым образом оказывает влияние на общую эффективность компании.
Если переходить к вопросу повышения эффективности компании и учитывать влияние производительности на эффективность, то важно учитывать основную формулу общей эффективности:
Эобщая= Э внешняя х Э внутренняя, где
Эвнешняя – эффективность использования внешних возможностей компании. Организации не существуют в замкнутом пространстве, она взаимодействует с внешней средой внешнего рынка. Внешняя эффективность характеризуется внешними факторами и измеряется такими показателями как доля рынка, объем продаж, величиной товарооборота и т.д. Од-
64
нако победа в современных подходах маркетинга может быть достигнута лишь при способности организации гибко реагировать на изменения внешних факторов (гибкость и мобильность производственных процессов, оптимальный уровень себестоимости и т.д.)
Э внутренняя – эффективность использования внутренних возможностей компании. Как раз Внутреннюю эффективность и принято выражать через производительность. Чем выше уровень внутренней эффективности, тем выше уровень производительности и наоборот.
Можно сделать вывод – чем ниже себестоимость выпускаемой продукции, тем выше Э внутренняя.
С учетом рассмотренной формулы мы видим, что для повышения общей эффективности компании, необходимо заниматься, во-первых, расширением доли рынка, повышать уровень продаж, во-вторых, повышать производительность внутри самой компании путем внедрения Производственной системы (ПС).
Производственная система – это система, где происходит улучшение текущей ситуации (достижение конкретных поставленных целей в компании) путем активизации персонала и рабочих мест через кайдзен – работу с участием всех сотрудников, обеспечение трудовой мотивации, визуализацию ситуации на рабочих местах, а также проведение опережающего совершенствования при разработке и проектировании новой продукции. Отличия концепции Бережливого производства и Производственной системы подробно раскрываются в таблице 1.
Таблица 1
Сравнение концепции Бережливого производства и Производственной системы
|
Содержание |
|
|
Бережливое производство |
|
|
Производственная система |
|
|
|
|
|
|
|
|||
|
|
|
|
|
|
|
|
|
|
Цель внедрения |
|
Попробовать, модно, |
|
Для достижения стратегических |
|||
|
|
|
|
есть у других |
|
целей компании |
||
|
|
|
|
|
|
|||
|
Работа по совершен- |
|
Определены рабочие места и |
|
Проведение кайдзен - работы во всех |
|||
|
ствованию |
|
пилотные проекты |
|
подразделениях компании |
|||
|
|
|
|
|
|
|||
|
Способ управления |
|
Сверху вниз |
|
Система самостоятельных исследо- |
|||
|
|
|
|
(административный) |
|
ваний, участие всех сотрудников |
||
|
|
|
|
|
|
|||
|
Метод продвижения |
|
Принудительный с применением |
|
Через личностные цели и результат |
|||
|
|
|
|
наказаний и штрафов и т.д. |
|
работы. Руководители оценивают |
||
|
|
|
|
Недоверие между руководством |
|
результаты сотрудников. Принцип |
||
|
|
|
|
и сотрудниками |
|
положительной мотивации |
||
|
|
|
|
|
|
|||
|
Реакция линейного |
|
Недружественная (работа по |
|
Обеспечение трудовой мотивации |
|||
|
Персонала |
|
совершенствованию процессов = |
|
через кайдзен – работу. |
|||
|
|
|
|
интенсификация труда) |
|
|
|
|
|
|
|
|
|
|
|||
|
Результаты |
|
Сокращение численности |
|
Активизация персонала и |
|||
|
кайдзен -работы |
|
работников и запасов |
|
производственных участков |
|||
|
|
|
|
(нацеленность на результат) |
|
|
|
|
|
|
|
|
|
|
|
|
|
65
|
|
Окончание табл. 1 |
Обучение |
Обучения только на рабочих |
Система обучения смежным специ- |
|
местах пилотного проекта |
альностям и дополнительным навы- |
|
|
кам, командная работа, лидерство |
|
|
|
Сфера применения |
Только производственная сфера |
Использование кайдзен - работы на |
кайдзен - работы |
|
стадиях проектирования, подготовки |
|
|
производства и т.д. |
|
|
|
Как организовать работу по внедрению Производственной системы, с чего необходимо начать, как выстроить плановую работу и сколько по времени будет занимать тот или иной этап работы?
Всю работу по внедрению ПС можно разбить на 5 этапов (Формирование, Введение в процесс совершенствования, Развертывание, Распространение, Совершенствование). Первые четыре этапа имеют конечный результат – Самостоятельное функционирование ПС внутри компании. Данный процесс занимает для компаний по срокам от двух до десяти лет, в зависимости от объективных условий рынка, интенсивности внедрения, выделяемых ресурсов, заинтересованности и вовлеченности руководства и др. факторов. Важно не пытаться искусственно ускорять процесс внедрения ПС, чтобы быстрее получить результат от внедрения. Основное в данном процессе – результативность выполняемых действий, а не нацеленность на временный результат любой ценой. Только качественная реализация каждого этапа может гарантировать вам успех, а не просто потраченные деньги.
Как только руководство компании принимает решение о начале внедрения – пути назад уже нет. Если вы бросите внедрение на половине пути, начать заново будет намного сложнее.
Рассмотрим основные направления работы по каждому этапу внедрения ПС в компаниях.
1 этап – Формирование.
Самый важный подготовительный этап, поскольку здесь необходимо продумать концепцию и модель ПС вашей компании, спланировать процесс внедрения, наметить последовательность необходимых действий и систему оценки результативности внедрения. От правильного планирования, зависит результат, который вы сможете получить, а также срок каждого этапа работы.
2 этап – Внедрение.
На втором этапе уже происходит процесс внедрения ПС по утвержденному плану: Обучение персонала компании и организация рабочих мест по 5С. Для понимания и вовлечения в процесс совершенствования сотрудников проводится обучение всего персонала. В основе всех перемен лежит мышление людей, а система и инструменты – вторичны.
3 этап - Развертывание.
Развертывание Производственной системы – это самый большой по продолжительности и объему предстоящей работы этап внедрения. Здесь
66
компания проводит анализ своих процессов, определяет проблемные места и совершенствует их состояние. Улучшения охватывают следующие направления деятельности:
Совершенствование процессов (стандартизация и управление)
Организация и совершенствование рабочих мест
Совершенствование логистики (поставка сырья, материалов и комплектующий)
Совершенствование оборудования
Повышение уровня качества
Опережающий инжиниринг
Активизация персонала
Каждое направление требует тщательного анализа, составления плана работ и дополнительного обучения всех сотрудников компании.
Но, не следует останавливаться на достигнутом, необходимо двигаться дальше, ставить новые цели и показатели, выявлять «узкие места» и разрабатывать новый план совершенствования. Подход – постоянно двигаться вперед и не останавливаться на достигнутом носит названия цикл PDCA (Plan – планируй, Do – делай, Check – проверяй, Act – воздействуй)
– цикл Деминга, с дополнением еще одного шага – процедура стандартизация полученного результата.
Успех внедрения Производственной системы в компании зависит от слаженной, активной и командной работы всех сотрудников. Причем, в формировании эффективной производственной системы существенную роль играют менеджеры всех уровней компании. Необходимо строить систему самодостаточную и саморазвивающуюся, а этого можно достичь только при доверительном отношении сотрудников компании, при правильном взаимодействии, воспитании не просто руководителей – начальников, а руководителей – лидеров, при формировании командной работы. Все это называется – Активизация персонала компании. Процессы в компании делают люди и от того, как настроены сотрудники к взаимодействию с руководством, как взаимодействуют они между собой, какой компетентностью и знаниями они владеют, будет завесить многое.
Первое, что необходимо предпринимать в вопросах активизации персонала – обучение руководителей всех уровней и обучение их навыкам лидерства, коммуникаций и командообразованию, второе – это формирование команды руководителей. Очень важно продвигать процесс активизации поэтапно, необходимо тщательно спланировать направление и четко контролировать процесс. Процесс активизации напрямую приведет к позитивным результатам во всей системе управления т.к. сотрудники компании начинают ощущать значимость своей работы и возможность действовать самостоятельно. Только за счет активизации персонала можно высвободить время для работы по совершенствованию рабочих процессов и одновременно повысить производительность практически на 25 %.
67
4 этап – Распространение.
Цель данного этапа – распространение уже сформированной и успешно функционирующей культуры и идеологии производственной системы повсеместно во все, еще неохваченные до настоящего момента подразделения компании (работа со сторонними предприятиями, которые выполняют работы по аутсорсингу), внедрение программы развития отношений с поставщиками и включение поставщиков в логистическую цепочку предприятия.
5 этап – Совершенствование.
Пятый этап – постоянное совершенствование и развитие существующей ПС для достижения стратегических целей развития компании. Он бесконечен для тех компаний, которые выбирают для себя путь постоянного развития и расширения. Самое главное, что на этапе совершенствования компания уже приобретает модель автономного внутреннего механизма развития.
Особо хотелось остановиться на роли руководителя в формировании и внедрении Производственной системы в компании. Активное участие руководства является основным условием успешной работы. Руководство должно разбираться в основных направлениях совершенствования, встречаться с сотрудниками, активно решать важнейшие задачи и вопросы. Самый важный принцип руководителя – уважительное и положительное отношение к персоналу.
В заключение хотелось вспомнить А.В. Суворова. Его крылатая фраза: «Недорубленный лес всегда вырастает», не дает повода руководителю останавливаться на полпути, а побуждает постоянно двигаться вперед, развиваться и совершенствоваться, достигая все новые и новые вершины экономических высот.
Решетникова Ирина Юрьевна, директор по обучающим программам Центра "Кайдзэн", директор ООО «Центр развития Производственных си-
стем». E-mail: ireshetnikova@yandex.ru
68
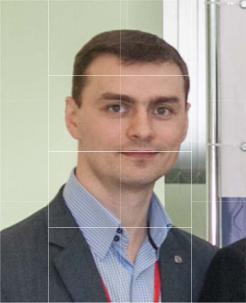
П роизводствен ная система Н овомет. Примеры эффективных реш ений с применением
инструментов бе режливого производства
Савлов А лексей Николаевич
Компания |
« Новомет» – один из |
крупнейших в |
оссии производителей |
нефтепог ужного |
борудования. На иная с |
разработки новых видов установок ля добычи нефти и заканчивая супервайзингом и подбором установки к скважине – весь
ж изненный цикл |
борудования находится |
под тщательным |
онтроле м специалистов |
компании. |
|
Самая широкая линейка типоразмеров
ступеней, |
нацеленность на |
инновации, на |
|
производство оборудования |
именно |
для |
|
осложненных условий эксплуатации |
– ха- |
||
рактерные |
черты сегодняшнего пр извод- |
ственного процесса в компании «Нов мет».
Компания, созданная в 1991 году, насчитывает на данный |
момент |
персонал 5000 человек. |
|
В 2004 году с ро том объемов производства морально и физически |
|
устаревшее оборудование перестало удовлетворять требованиям |
изго- |
товле ию ступеней по производительности и по качеству обработки. Поэтому было принято решение п о приобретению современн ых высокопроизводительных роботизированны х японских лини IVS-200 фирмы Мазак. На данный момент участок оснащен 18 автоматическими линиями. Одна линия предста ляет собой два токарных станка с ЧПУ, соединенных между со ой транспортной системой. Результатом внедрения было сн жение цикла изготовления деталей, повышение качеств , уменьш ение обслужи-
вавшего персо ала и, как следствие, повышение э |
фективности за счет ав- |
|
томатизации. |
|
|
Достигнув максимального уровня |
загрузк |
оборудования, настал |
момент, когда мы начали анализировать потери |
просто и. Начал я этап |
|
внедрения вспомогательных процессов, позволяю |
их выявить узки места |
|
и пов сить эф ективность использования |
оборудования. |
|
Первым инструм нтом повышения |
эффективности стало освоение |
программного продукта Cyber Monitor.
Выполнение планов произ одства зависит от многих факторов, в том числе и от того, наскол ко эффективно работает оборудование. Для управ-
69
ления его работой всегда применялись различные системы мониторинга, хронометраж нормировщика, установление дополнительных датчиков для определения времени вращения шпинделя и т.д. Мониторинг дает возможность увидеть, насколько загружено оборудование, в каком режиме оно эксплуатируется, что необходимо сделать для того, чтобы улучшить его работу. Ключевым моментом любой системы мониторинга является оперативность и достоверность данных.
Данная программа дистанционно контролирует рабочее состояние станков, благодаря этому любой руководитель со своего рабочего места в режиме реального времени может наблюдать за работой оборудования. Более того, по результатам работы станка за интересующий период времени (сутки, недели, месяцы и даже годы) можно вывести диаграмму, показывающую, как отработал за данный период тот или иной станок. Для более подробного анализа существует возможность разделения диаграммы на трехсменный график работы оператора, где видно, в какое время, в какую смену случилось то или иное изменение режима его работы.
Данная программа также позволяет отследить, на каких режимах резания происходит обработка деталей, что, в свою очередь, влияет на стойкость инструмента и качество обрабатываемой поверхности. Если во время работы возникают аварийные сообщения, станок их фиксирует и сохраняет в памяти. После чего, пользуясь «классификатором ошибок», можно определить, чем была вызвана данная ошибка, и что необходимо предпринять для ее устранения. Для более оперативного устранения неисправностей возможна автоматическая передача информации со станка на рабочее место ремонтной службы посредством электронной почты.
Благодаря вышесказанному появляется возможность принятия обоснованных решений, связанных с загрузкой и режимами эксплуатации дорогостоящего высокопроизводительного оборудования. Время работы станка в автоматическом режиме – универсальный показатель, демонстрирующий, насколько эффективно используется оборудование, на данный момент показатель по работе участка составляет 92 % работы в автоматическом режиме.
Внедрение модуля Sheduler
Cyber Scheduler – система производственного планирования, позволяющая осуществлять выдачу сменно-суточного задания оператору. А именно руководитель цеха с помощью этого продукта производит планирование своих ресурсов на неделю, месяц и т.д. После чего данные отправляются непосредственно на ЧПУ. Таким образом, потери, которые раньше были связаны со своевременной выдачей сменно суточного задания, были исключены. Оператор получил всю необходимую информацию заранее, когда начать работу, – сколько изготовить деталей и, соответственно, может заранее подготовиться к предстоящей переналадке. По завершению того или иного задания, выполнив действия на ЧПУ, информация доходит
70