
Справочник по допускам в метрологии
.pdf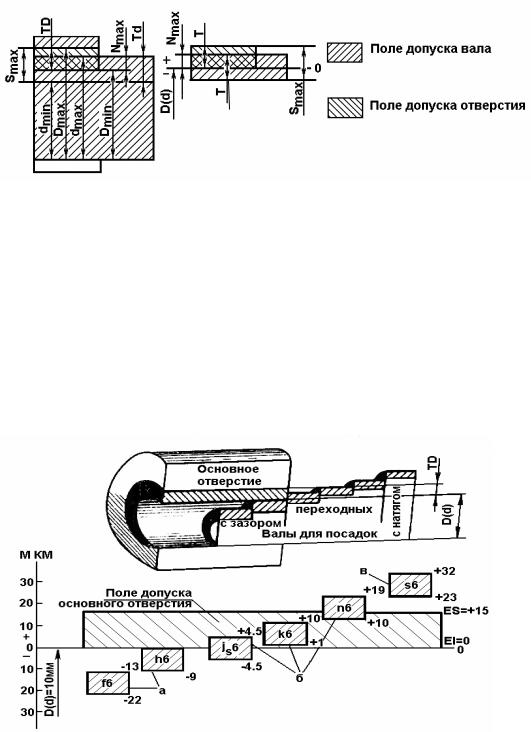
Переходная посадка – посадка, при которой возможно получение как зазора, так и натяга (т.е. когда поля допусков отверстия и вала (рис. 2.8) перекрываются частично или полностью).
Поле допуска посадки – это поле, заключенное между двумя линиями, соответствующими разности между наибольшим и наименьшим допускаемыми зазорами или натягами,
определяется по формулам: |
|
||||
с зазором – TS = S max – S min = TD + Td; |
(2.20) |
||||
с натягом – TN = N max – N min = TD + Td. |
(2.21) |
||||
|
|
|
Td |
|
|
|
|
|
|
||
|
|
|
|
|
|
|
|
|
|
|
|
|
|
|
TD |
|
|
|
|
|
|
|
|
Рис. 2.8. Поля допусков переходной посадки
Впереходных посадках допуск посадки определяется как сумма наибольшего натяга
изазора, взятых по абсолютному значению:
T(SN) = N max + S max = TD + Td. |
(2.22) |
3. СИСТЕМА ОТВЕРСТИЯ И СИСТЕМА ВАЛА
Различают посадки в системе отверстия и системе вала.
Посадками в системе отверстия называют посадки, в которых зазоры и натяги получаются соединением различных по размеру валов (например, поля допусков f6, h6, js6, n6, s6) с основным отверстием H, у которого нижнее отклонение EI = 0, а верхнее отклонение ES – допуску основного отверстия со знаком “плюс” (рис. 3.1).
Рис. 3.1. Расположение полей допусков основного отверстия H
ивалов в системе отверстия для посадок:
а– с зазором; б – переходных; в – с натягом
20

В системе отверстия поля допусков валов (f6, h6) для посадок с зазором расположены ниже нулевой линии, т.е. под полем допуска основного отверстия H (рис. 3.1, а).
Для посадок с натягом поля допусков валов (s6) расположены выше поля допуска основного отверстия H (рис. 3.1, в). В переходных посадках поля допусков валов (js6, k6, n6) перекрывают полностью (k6) или частично (js6, n6) поле допуска основного отверстия H (рис. 3.1, б). Посадками в системе вала называют посадки, в которых различные зазоры и натяги получаются соединением различных по размеру отверстий (например, поля допусков F7, JS7, N7, S7) с основным валом h, у которого верхнее отклонение es = 0, а нижнее отклонение ei – допуску основного вала сознаком “минус” (рис. 3.2).
h6
Рис. 3.2. Расположение полей допусков основного вала “h”
иотверстий в системе вала для посадок:
а– с зазором; б – переходных; в – с натягом
Всистеме вала поля допусков отверстий (F7) для посадок с зазором расположены выше нулевой линии, т.е. над полем допуска основного вала h (рис. 3.2, а). Для посадок с натягом поля допусков отверстий (S7) расположены ниже поля допуска основного вала h (рис. 3.2, в). В переходных посадках поля допусков отверстий (JS7, M7, N7) перекрываются полностью(M7) или частично (JS7, N7) полем допуска основного вала h (рис. 3.2, б). Посадки
всистеме отверстия H предпочтительнее посадок в системе вала h, т.к. более точный вал изготовить легче, чем точное отверстие.
4. КВАЛИТЕТЫ
Градация допусков в системе ЕСДП устанавливается в виде набора степеней или классов точности, под которыми понимается совокупность допусков, соответствующих одному уровню точности для всех номинальных размеров.
Степени точности (квалитеты) обычно обозначают числами – порядковыми номерами. В ЕСДП установлено 20 квалитетов, обозначаемых порядковым номером 01, 0, 1, 2, 3 и т.д. до 18. Наивысшей точности соответствует квалитет 01, а наименьшей – 18-й
квалитет (табл. 4.1).
21

Допуск квалитета условно обозначаeтся латинскими прописными буквами IT и номером квалитета, например, IT7 – допуск 7го квалитета. Допуски квалитета 5…..18 считают по формуле:
ITg = ai, |
(4.1) |
где g – номер квалитета; a – безразмерный коэффициент, установленный для данного квалитета и не зависиящий от номинального размера (табл. 4.2); i – единица допуска (мкм) – множитель, зависящий от номинального размера и подсчитываемый для размеров от 1 до 500 мм по формуле:
i = 0,45 3 D + 0,001D, |
(4.2) |
где D – среднее геометрическое граничных значений интервала номинальных размеров, |
|
вычисляемое по формуле: |
|
D = D min D max, |
(4.3) |
где D min, D max – наименьшее и наибольшее граничные значения интервала номинальных размеров, мм (табл. 4.3).
5. ОБРАЗОВАНИЕ ПОЛЕЙ ДОПУСКОВ
Поле допуска образуется сочетанием основного отклонения (характеристика расположения) и квалитета (характеристика допуска). Поле допуска вала или отверстия обозначают после номинального размера буквой основного отклонения и номером квалитета. Например, Ø 50H7, Ø 50g6 и т. п., означает, в первом случае, отверстие диаметром 50 мм 7го квалитета с основным отклонением H, т.е. основное отверстие в системе отверстия. В случае Ø 50g6, диаметр вала 50 мм 6-го квалитета с основным отклонением g, т.е. вал посадки с зазором в системе отверстия.
Таблица 4.1
Значение допусков для размеров от 1 до 500 мм
Номинальные |
|
|
|
|
|
Квалитеты |
|
|
|
|
|
размеры, |
|
01 |
0 |
1 |
2 |
3 |
4 |
5 |
6 |
7 |
8 |
мм |
|
|
|
|
Обозначение допусков |
|
|
|
|||
|
|
IT01 |
IT0 |
IT1 |
IT2 |
IT3 |
IT4 |
IT5 |
IT6 |
IT7 |
IT8 |
|
|
|
|
|
|
Допуски |
, мкм |
|
|
|
|
До3 |
|
0,3 |
0,5 |
0,8 |
1,2 |
2 |
3 |
4 |
6 |
10 |
14 |
Свыше 3 до 6 |
|
0,4 |
0,6 |
1 |
1,5 |
2,5 |
4 |
5 |
8 |
12 |
18 |
Свыше 6 до 10 |
|
0,4 |
0,6 |
1 |
1,5 |
2,5 |
4 |
6 |
9 |
15 |
22 |
Свыше 10 до 18 |
|
0,5 |
0,8 |
1,2 |
2 |
3 |
5 |
8 |
11 |
18 |
27 |
Свыше 18 до 30 |
|
0,6 |
1 |
1,5 |
2,5 |
4 |
6 |
9 |
13 |
21 |
33 |
Свыше 30 до 50 |
|
0,6 |
1 |
1,5 |
2,5 |
4 |
7 |
11 |
16 |
25 |
39 |
Свыше 50 до 80 |
|
0,8 |
1,2 |
2 |
3 |
5 |
8 |
13 |
19 |
30 |
46 |
Свыше 80 до 120 |
|
1 |
1,5 |
2,5 |
4 |
6 |
10 |
15 |
22 |
35 |
54 |
Свыше 120 до 180 |
|
1,2 |
2 |
3,5 |
5 |
8 |
12 |
18 |
25 |
40 |
63 |
Свыше 180 до 250 |
|
2 |
3 |
4,5 |
7 |
10 |
14 |
20 |
29 |
46 |
72 |
Свыше 250 до 315 |
|
2,5 |
4 |
6 |
8 |
12 |
16 |
23 |
32 |
52 |
81 |
Свыше 315 до 400 |
|
3 |
5 |
7 |
9 |
13 |
18 |
25 |
36 |
57 |
89 |
Свыше 400 до 500 |
|
4 |
6 |
8 |
10 |
15 |
20 |
27 |
40 |
63 |
97 |
|
Количество единиц допуска в допуске данного квалитета |
|
|
|
|||||||
|
|
1* |
1,4* |
2* |
2,7* |
3,7* |
5,1* |
7 |
10 |
16 |
25 |
22
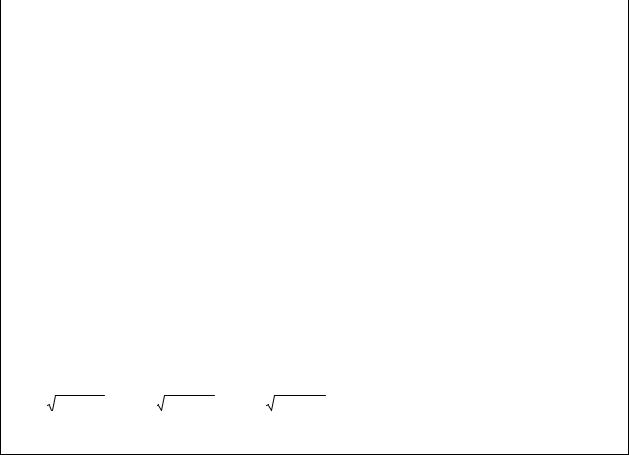
Окончание табл. 4.1
Номинальные |
|
|
|
|
|
|
Квалитеты |
|
|
|
|
|
размеры, |
|
9 |
|
10 |
11 |
12 |
13 |
14** |
15** |
16** |
17** |
18** |
мм |
|
|
|
|
|
|
|
|
|
|
|
* |
|
|
|
|
|
|
Обозначение допусков |
|
|
|
|||
|
|
IT9 |
IT10 |
IT11 |
IT12 |
IT13 |
IT14 |
IT15 |
IT16 |
IT17 |
IT18 |
|
|
|
|
|
Допуски, мкм |
|
|
Допуски, мм |
|
||||
Свыше 3 |
|
25 |
|
40 |
60 |
0,1 |
0,14 |
0,25 |
0,4 |
0,6 |
1 |
1,4 |
Свыше 3 до 6 |
|
30 |
|
48 |
75 |
0,12 |
0,18 |
0,3 |
0,48 |
0,75 |
1,2 |
1,8 |
Свыше 6 до 10 |
|
36 |
|
58 |
90 |
0,15 |
0,22 |
0,36 |
0,58 |
0,9 |
1,5 |
2,2 |
Свыше 10 до 18 |
|
43 |
|
70 |
110 |
0,18 |
0,27 |
0,43 |
0,7 |
1,1 |
1,8 |
2,7 |
Свыше 18 до 30 |
|
52 |
|
84 |
130 |
0,21 |
0,33 |
0,52 |
0,84 |
1,3 |
2,1 |
3,3 |
Свыше 30 до 50 |
|
62 |
|
100 |
160 |
0,25 |
0,39 |
0,62 |
1 |
1,6 |
2,5 |
3,9 |
Свыше 50 до 80 |
|
74 |
|
120 |
190 |
0,3 |
0,46 |
0,74 |
1,2 |
1,9 |
3 |
4,6 |
Свыше 80 до 120 |
|
87 |
|
140 |
220 |
0,35 |
0,54 |
0,87 |
1,4 |
2,2 |
3,5 |
5,4 |
Свыше 120 до 180 |
|
100 |
|
160 |
250 |
0,4 |
0,63 |
1 |
1,6 |
2,5 |
4 |
6,3 |
Свыше 180 до 250 |
|
115 |
|
185 |
290 |
0,46 |
0,72 |
1,15 |
1,85 |
2,9 |
4,6 |
7,2 |
Свыше 250 до 315 |
|
130 |
|
210 |
320 |
0,52 |
0,81 |
1,3 |
2,1 |
3,2 |
5,2 |
8,1 |
Свыше 315 до 400 |
|
140 |
|
230 |
360 |
0,57 |
0,89 |
1,4 |
2,3 |
3,6 |
5,7 |
8,9 |
Свыше 400 до 500 |
|
155 |
|
250 |
400 |
0,63 |
0,97 |
1,55 |
2,5 |
4,0 |
6,3 |
9,7 |
|
|
Количество |
единиц допуска в допуске |
данного квалитета |
|
|
||||||
|
|
40 |
|
64 |
100 |
160 |
250 |
400 |
640 |
1000 |
1600 |
2500 |
*Количество единиц допуска указано для размеров |
св. 500 мм. Для размеров до 500 мм допуски в квалитетах |
от 0,1 до 4 определены по следующим формулам: |
IT01=0,3+0,008 DИ; IT0=0,5+0,012 DИ; IT=0,8+0,020 DИ; |
IT 2 = IT1 IT 3 ; IT 3 = IT1 IT 5 ; IT 4 = IT 3 |
IT 5 ; |
(IT – в мкм; Dи – в мм). **Квалитеты 14–18 для размеров менее 1 мм не предусмотрены.
***Допуски по 18-му квалитету приведены дополнительно к СТ СЭВ 145-754 СТСЭВ 177-75
Таблица 4.2
Число единиц допуска a для квалитетов 5-18
Квалитет g |
5 |
6 |
7 |
8 |
9 |
10 |
11 |
12 |
13 |
14 |
15 |
16 |
17 |
18 |
|
|
|
|
|
|
|
|
|
|
|
|
|
|
|
Число единиц |
7 |
10 |
16 |
25 |
40 |
64 |
100 |
160 |
250 |
400 |
640 |
1000 |
1600 |
2500 |
допуска a |
|
|
|
|
|
|
|
|
|
|
|
|
|
|
|
|
|
|
|
|
|
|
Таблица 4.3 |
|
|
|
|
Интервалы номинальных размеров, мм |
|
|
|
|||
|
|
|
|
|
|
|
|
|
|
Основные |
|
Промежуточные |
Основные |
Промежуточные |
|||||
|
|
|
|
|
|
|
|
|
|
Свыше |
|
До |
Свыше |
До |
Свыше |
До |
Свыше |
До |
|
- |
|
3 |
- |
- |
500 |
630 |
500 |
560 |
|
|
|
|
|
|
|
|
560 |
630 |
|
|
|
|
|
|
|
|
|
|
|
3 |
|
6 |
- |
- |
630 |
800 |
630 |
710 |
|
|
|
|
|
|
|
|
710 |
800 |
|
|
|
|
|
|
|
|
|
|
|
6 |
|
10 |
- |
- |
800 |
1000 |
800 |
900 |
|
|
|
|
|
|
|
|
900 |
1000 |
|
|
|
|
|
|
|
|
|
|
|
10 |
|
18 |
10 |
14 |
1000 |
1250 |
1000 |
1120 |
|
|
|
|
14 |
18 |
|
|
1120 |
1250 |
|
|
|
|
|
|
|
|
|
|
|
18 |
|
30 |
18 |
24 |
1250 |
1600 |
1250 |
1400 |
|
|
|
|
24 |
30 |
|
|
1400 |
1600 |
|
|
|
|
|
|
|
|
|
|
|
|
|
|
|
|
|
|
|
23 |
Окончание табл. 4.3
Основные |
Промежуточные |
Основные |
Промежуточные |
||||
|
|
|
|
|
|
|
|
Свыше |
До |
Свыше |
До |
Свыше |
До |
Свыше |
До |
30 |
50 |
30 |
40 |
1600 |
2000 |
1600 |
1800 |
|
|
40 |
50 |
|
|
1800 |
2000 |
|
|
|
|
|
|
|
|
– |
3 |
– |
– |
500 |
630 |
500 |
560 |
|
|
|
|
|
|
560 |
630 |
|
|
|
|
|
|
|
|
3 |
6 |
– |
– |
630 |
800 |
630 |
710 |
|
|
|
|
|
|
710 |
800 |
|
|
|
|
|
|
|
|
6 |
10 |
– |
– |
800 |
1000 |
800 |
900 |
|
|
|
|
|
|
900 |
1000 |
|
|
|
|
|
|
|
|
10 |
18 |
10 |
14 |
1000 |
1250 |
1000 |
1120 |
|
|
14 |
18 |
|
|
1120 |
1250 |
|
|
|
|
|
|
|
|
18 |
30 |
18 |
24 |
1250 |
1600 |
1250 |
1400 |
|
|
24 |
30 |
|
|
1400 |
1600 |
|
|
|
|
|
|
|
|
30 |
50 |
30 |
40 |
1600 |
2000 |
1600 |
1800 |
|
|
40 |
50 |
|
|
1800 |
2000 |
|
|
|
|
|
|
|
|
50 |
80 |
50 |
65 |
2000 |
2500 |
2000 |
2240 |
|
|
65 |
80 |
|
|
2240 |
2500 |
|
|
|
|
|
|
|
|
80 |
120 |
80 |
100 |
2500 |
3150 |
2500 |
2800 |
|
|
100 |
120 |
|
|
2800 |
3150 |
|
|
|
|
|
|
|
|
120 |
180 |
120 |
140 |
3150 |
4000 |
3150 |
3550 |
|
|
140 |
160 |
|
|
3550 |
4000 |
|
|
160 |
180 |
|
|
|
|
|
|
|
|
|
|
|
|
180 |
250 |
180 |
200 |
4000 |
5000 |
4000 |
4500 |
|
|
200 |
225 |
|
|
4500 |
5000 |
|
|
225 |
250 |
|
|
|
|
|
|
|
|
|
|
|
|
250 |
315 |
250 |
380 |
5000 |
6300 |
5000 |
5600 |
|
|
280 |
315 |
|
|
5600 |
6300 |
|
|
|
|
|
|
|
|
315 |
400 |
315 |
355 |
6300 |
8000 |
6300 |
7100 |
|
|
355 |
400 |
|
|
7100 |
8000 |
|
|
|
|
|
|
|
|
400 |
500 |
400 |
450 |
8000 |
10000 |
8000 |
9000 |
|
|
450 |
500 |
|
|
9000 |
10000 |
Если основным отклонением для отверстия является нижнее EI, а для вала верхнее es, то второе предельное отклонение для отверстия ES и для вала ei подсчитывают по формулам:
ES = EI + IT7; |
(5.1) |
ei = es – IT6. |
(5.2) |
В случаях, когда основное отклонение отверстия является верхнее ES, а для вала нижнее ei, то нижнее отклонение отверстия EI и верхнее отклонение es для вала определяют по
формулам: |
|
EI = ES – IT7; |
(5.3) |
ES = ei + IT6. |
(5.4) |
24
6. ГЛАДКИЕ ЦИЛИНДРИЧЕСКИЕ СОЕДИНЕНИЯ
Гладкие цилиндрические соединения образуются, например, при соединении двух деталей типа вал и втулка. Обеспечение взаимозаменяемости гладких цилиндрических деталей, а также выбор характера их соединения и квалитета (посадки) регламентируется
ECДП.
В основе выбора квалитета лежат методы подобия, аналогов или расчётный. В общих чертах можно указать на следующее применение квалитетов.
4-й и 5-й квалитеты. Применяются сравнительно редко, в особо точных соединениях, требующих высокой однородности зазора или натяга. Например: точные шпиндельные и приборные подшипники в корпусах и на валах, высокоточные зубчатые колёса на валах и оправах, плавающий поршневой палец в бобышках поршня и в шатунной головке и т.п. Если по условиям сборки и эксплуатации соединения нет необходимости в обеспечении полной взаимозаменяемости его деталей, то вместо посадок 4 – 5-го квалитетов прибегают к селективной сборке, применяя более грубые допуски на изготовление деталей. В отдельных случаях, при наивысших требованиях к однородности соединения, допуски 4 – 5-го квалитетов также оказываются недостаточными для обеспечения полной взаимозаменяемости, и требуется дополнительная сортировка деталей перед сборкой (плунжерные пары, посадки подшипников качения наивысшей точности и т. п.).
6-й и 7-й квалитеты. Применяются для ответственных соединений в механизмах, где к посадкам предъявляются высокие требования в отношении определённости зазоров и натягов для обеспечения механической прочности деталей, точных перемещений, плавного хода, герметичности соединения и других служебных функций, а также для обеспечения точной сборки деталей. Примеры: подшипники качения нормальной точности в корпусах и на валах, зубчатые колёса высокой и средней точности на валах, обычные переходные посадки и посадки с натягами средней величины, подшипники жидкостного трения, соединения деталей гидравлической и пневматической аппаратуры, подвижные соединения в кри- вошипно-шатунном механизме ответственных двигателей внутреннего сгорания и т.п.
8-й и 9-й квалитеты. Применяются для посадок, обеспечивающих выполнение деталями определённых служебных функций (передачу усилий, перемещения и др.) при относительно меньших требованиях к однородности зазоров или натягов и для посадок, обеспечивающих среднюю точность сборки. Например: сопрягаемые поверхности в посадках с большими натягами, отверстия в переходных посадках пониженной точности, посадки с зазорами для компенсации значительной погрешности формы и расположения сопрягаемых поверхностей, опоры быстровращающихся валов средней точности, опоры скольжения средней точности в условиях полужидкостного трения и др. Эти квалитеты имеют преимущественное применение для относительно точных соединений в тракторо-, аппарато- и приборостроении и особо ответственных узлов сельскохозяйственных машин.
10-й квалитет. Применяют в посадках с зазором в тех же случаях, что и 9-й, если для удешевления обработки деталей необходимо расширить допуск, а условия сборки или эксплуатации допускают некоторое увеличение колебания зазоров в соединениях.
11-й и 12-й квалитеты. Применяются в соединениях, где необходимы большие зазоры и допустимы их значительные колебания (грубая сборка). Эти квалитеты распространены в неответственных соединениях машин (крышки, фланцы, дистанционные кольца и т.п.), в узлах аппаратов сельскохозяйственных машин, в соединениях штамповых деталей и деталей из пластмасс и др.
Выбор квалитетов для различных размеров деталей во многих случаях определяется соответствующим решением размерных цепей, в состав которых входят длины, толщины, уступы, глубины впадин и другие размеры.
Большое значение имеют также вопросы, касающиеся состояния оборудования, на котором предполагается изготовление деталей, и технологического процесса обработки, осо-
25
бенно для последней операции, которая должна обеспечить заданный допуск размера детали. Ниже приводятся сведения по методам обработки, которые позволяют получить различные квалитеты при средней экономической точности:
– 4…. 5 – для вала; 5…6 – для отверстия
Шлифование круглое тонкое; прошивание тонкое (6–7); развальцовывание тонкое (5–6); полирование тонкое; притирка тонкая; доводка средняя (5–6), тонкая; хонингование цилиндров (6–7); лаппингование тонкое; суперфиниширование; анодно-механическое шлифование притирочное (5–6), отделочное.
– 6…7 – для вала, 7…8 – для отверстия
Обтачивание или растачивание тонкое (алмазное); чистовое (6–9); развёртывание чистовое, тонкое (6–7); протягивание чистовое, отделочное; шлифование круглое чистовое; шлифование плоское чистовое, тонкое; прошивание чистовое (7–9); калибрование отверстий шариком или оправкой после растачивания или развёртывания; обкатывание или раскатывание роликами или шариками (6–9); развальцовывание чистовое; притирка чистовая; полирование обычное; доводка грубая; хонингование плоскостей; лаппингование предварительное и среднее; анодно-механическое шлифование черновое (6–9), чистовое; электрополирование декоративное (6–9); электромеханическое точение обычное (6–9), чистовое; электромеханическое сглаживание; холодная штамповка в вырубных штампах – контурные размеры плоских деталей при зачистке и калибровке.
– 8…9 – для вала, 9 – для отверстия
Строгание тонкое (7…8); фрезерование тонкое (7); обтачивание поперечной подачей тонкое (8–11); развёртывание получистовое (9–10), для чугуна 8; протягивание получистовое; шабрение тонкое; слесарная опиловка (9–11); зачистка наждачным полотном – после резца и фрезы (9–11); шлифование круглое получистовое (8–11); калибрование отверстий шариком или оправкой – после сверления; холодная штамповка в вытяжных штампах – полые детали простых форм по высоте (9–12); холодная штамповка в вырубных штампах – контурные размеры плоских деталей при зачистке; горячая объёмная штамповка без калиб-
ровки (9–11).
– 10 квалитет
Зенкерование чистовое (10–11); холодная штамповка в вытяжных штампах – полые детали простых форм по диаметру (10–11). См. также методы обработки для 9-го квалитета (возможные пределы колебания квалитетов).
– 11 квалитет
Строгание чистовое (11–13), 10; фрезерование чистовое (10); фрезерование скоростное чистовое (11–13); обтачивание поперечной подачей чистовое (11–13); обтачивание скоростное; подрезка торцов (11–13); сверление по кондуктору (11–13); шабрение грубое; анодно-механическое разрезание заготовки обычное (11–13), специальное; электроконтактное разрезание листов (11–13); литьё по выплавляемым моделям – мелкие детали из чёрных металлов (11–13); холодная штамповка в вытяжных штампах – глубокая вытяжка полых деталей простых форм; холодная штамповка плоских деталей при пробивке. См. также методы обработки для 9 и 10-го квалитетов (возможные пределы колебания квалитетов).
– 12….13 квалитеты – строгание черновое (12–14); долбление чистовое; фрезерование черновое (12–14), обтачивание продольной подачей получистовое (12–14); сверление без кондуктора (12–14); рассверливание(12–14); зенкерование черновое, по корке (12–15); растачива-
26

ние получистовое (12–14); литьё в оболочковые формы – детали из чёрных металлов (12–14); холодная штамповка в вырубных штампах – контурные размеры плоских деталей при вырубке; отрезка абразивом (12–15).
– 14…17 квалитеты – автоматическая газовая резка (15–17); отрезка ножницами и пилами (15–17); отрезка резцом и фрезой (14–16); долбление черновое (14–15); обтачивание продольной подачей обдирочное (15–17); обтачивание поперечной подачей обдирочное (16–17), получистовое (14–15); растачивание черновое (15–17); литьё в песчаные формы – черные металлы (14–16); литьё в песчаные формы (большие допуски) – цветные сплавы (16–17); литьё в кокиль – чёрные металлы (14–16), цветные сплавы (большие допуски 14–16); литьё по выплавляемым моделям – цветные сплавы при размерах деталей 30 – 500 мм (14–15); литьё в оболочковые формы (большие допуски) – цветные сплавы (14–15); центробежное литьё (15); горячая ковка в штампах (14–17); горячая вырубка и пробивка (14–16); сварка (16–17).
В гладких цилиндрических соединениях возможно применение любых отклонений полей допусков для создания необходимого характера сопряжения. При номинальных размерах от 1 до 500 мм поля допусков должны соответствовать указанным в табл. 6.1. и 6.2. В первую очередь следует применять предпочтительные поля допусков, выделенные жирным шрифтом. Для общего применения ГОСТ 25347-82 устанавливает рекомендуемые посадки в системе отверстия и в системе вала (табл. 6.3….6.4). Предпочтительно применение системы отверстия. При конструктивном или экономическом обосновании применяется система вала, например, при посадке наружного кольца подшипника в корпус, или, если необходимо, получить различные посадки нескольких деталей с отверстиями на одном гладком валу. При номинальных размерах от 1 до 3150 мм в точных квалитетах 6 и 7 по технологическим соображениям в посадках поле допуска отверстия рекомендуется назначать на один квалитет грубее, чем поле допуска вала, на-
пример Ø 10 Hg67 ; Ø 150 Hk67 .
Кроме посадок, указанных в табл. 6.3, в технически обоснованных случаях допускаются другие посадки, образованные из полей допусков по ECДП и по возможности относящиеся к системе отверстия или системе вала. При неодинаковых допусках отверстия и вала в посадке больший допуск должен быть у отверстия, и допуски отверстия и вала не должны отличаться более, чем на два квалитета. Выбор и назначение посадок осуществляют на основе расчетов с учетом опыта эксплуатации подобных соединений. Некоторые примеры применения предпочтительных посадок EСДП при номинальных размерах от 1 до 500 мм приведены ниже.
27
28
Таблица 6.1
Поля допусков валов при номинальных размерах от 1 до 500 мм
Квали- |
|
|
|
|
|
|
|
|
Основные отклонения |
|
|
|
|
|
|
|
|
|
|||
тет |
|
|
|
|
|
|
|
|
|
|
|
|
|
|
|
|
|
|
|
|
|
a |
b |
c |
d |
e |
f |
q |
h |
js |
k |
m |
n |
p |
r |
s |
t |
u |
v |
x |
y |
z |
|
01 |
|
|
|
|
|
|
|
h01* |
js01* |
|
|
|
|
|
|
|
|
|
|
|
|
0 |
|
|
|
|
|
|
|
h0* |
js0* |
|
|
|
|
|
|
|
|
|
|
|
|
1 |
|
|
|
|
|
|
|
h1* |
js1* |
|
|
|
|
|
|
|
|
|
|
|
|
2 |
|
|
|
|
|
|
|
h2* |
js2* |
|
|
|
|
|
|
|
|
|
|
|
|
3 |
|
|
|
|
|
|
|
h3* |
js3* |
|
|
|
|
|
|
|
|
|
|
|
|
4 |
|
|
|
|
|
|
q4 |
h4 |
js4 |
k4 |
m4 |
n4 |
|
|
|
|
|
|
|
|
|
|
|
|
|
|
|
|
|
|
|
|
|
|
|
|
|
|
|
|
|
|
|
5 |
|
|
|
|
|
|
q5 |
h5 |
js5 |
k5 |
m5 |
n5 |
p5 |
r5 |
s5 |
|
|
|
|
|
|
|
|
|
|
|
|
|
|
|
|
|
|
|
|
|
|
|
|
|
|
|
|
6 |
|
|
|
|
|
f6 |
q6 |
h6 |
js6 |
k6 |
m6 |
n6 |
p6 |
r6 |
s6 |
t6 |
|
|
|
|
|
|
|
|
|
|
|
|
|
|
|
|
|
|
|
|
|
|
|
|
|
|
|
7 |
|
|
|
|
e7 |
f7 |
|
h7 |
js7 |
k7 |
m7 |
n7 |
|
|
s7 |
|
u7 |
|
|
|
|
|
|
|
|
|
|
|
|
|
|
|
|
|
|
|
|
|
|
|
|
|
|
8 |
|
|
c8 |
d8 |
e8 |
f8 |
|
h8 |
js8* |
|
|
|
|
|
|
|
u8 |
|
x8 |
|
z |
9 |
|
|
|
d9 |
e9 |
f9 |
|
h9 |
js9* |
|
|
|
|
|
|
|
|
|
|
|
|
10 |
|
|
|
d10 |
|
|
|
h10 |
js10* |
|
|
|
|
|
|
|
|
|
|
|
|
11 |
a11 |
b11 |
c11 |
d11 |
|
|
|
h11 |
js11* |
|
|
|
|
|
|
|
|
|
|
|
|
12 |
|
b12 |
|
|
|
|
|
h12 |
js12* |
|
|
|
|
|
|
|
|
|
|
|
|
13 |
|
|
|
|
|
|
|
h13* |
js13* |
|
|
|
|
|
|
|
|
|
|
|
|
14 |
|
|
|
|
|
|
|
h14* |
js14* |
|
|
|
|
|
|
|
|
|
|
|
|
15 |
|
|
|
|
|
|
|
h15* |
js15* |
|
|
|
|
|
|
|
|
|
|
|
|
16 |
|
|
|
|
|
|
|
h16* |
js16* |
|
|
|
|
|
|
|
|
|
|
|
|
17 |
|
|
|
|
|
|
|
h17* |
js17* |
|
|
|
|
|
|
|
|
|
|
|
|
28 |
|
|
|
|
|
|
|
|
|
|
|
|
|
|
|
|
|
|
|
|
|

Таблица 6.2
Поля допусков отверстий при номинальных размерах от 1 до 500 мм
Квали- |
|
|
|
|
|
|
|
|
Основные отклонения |
|
|
|
|
|
|
|
|
||||
тет |
A |
B |
C |
D |
E |
F |
G |
H |
JS |
K |
M |
N |
P |
R |
S |
T |
U |
V |
X |
Y |
Z |
01 |
|
|
|
|
|
|
|
H01* |
JS01* |
|
|
|
|
|
|
|
|
|
|
|
|
0 |
|
|
|
|
|
|
|
H0* |
JS0* |
|
|
|
|
|
|
|
|
|
|
|
|
1 |
|
|
|
|
|
|
|
H1* |
JS1* |
|
|
|
|
|
|
|
|
|
|
|
|
2 |
|
|
|
|
|
|
|
H2* |
JS2* |
|
|
|
|
|
|
|
|
|
|
|
|
3 |
|
|
|
|
|
|
|
H3* |
JS3* |
|
|
|
|
|
|
|
|
|
|
|
|
4 |
|
|
|
|
|
|
|
H4 |
JS4 |
|
|
|
|
|
|
|
|
|
|
|
|
|
|
|
|
|
|
|
|
|
|
|
|
|
|
|
|
|
|
|
|
|
|
5 |
|
|
|
|
|
|
G5 |
H5 |
JS5 |
K5 |
M5 |
N5 |
|
|
|
|
|
|
|
|
|
|
|
|
|
|
|
|
|
|
|
|
|
|
|
|
|
|
|
|
|
|
|
6 |
|
|
|
|
|
|
G6 |
H6 |
JS6 |
K6 |
M6 |
N6 |
P6 |
|
|
|
|
|
|
|
|
|
|
|
|
|
|
|
|
|
|
|
|
|
|
|
|
|
|
|
|
|
|
7 |
|
|
|
|
|
F7 |
G7 |
H7 |
JS7 |
K7 |
M7 |
N7 |
P7 |
R7 |
S7 |
T7 |
|
|
|
|
|
|
|
|
|
|
|
|
|
|
|
|
|
|
|
|
|
|
|
|
|
|
|
8 |
|
|
|
D8 |
E8 |
F8 |
|
H8 |
JS8* |
K8 |
M8 |
N8 |
|
|
|
|
U8 |
|
|
|
|
9 |
|
|
|
D9 |
E9 |
F9 |
|
H9 |
JS9* |
|
|
|
|
|
|
|
|
|
|
|
|
10 |
|
|
|
D10 |
|
|
|
H10 |
JS10* |
|
|
|
|
|
|
|
|
|
|
|
|
11 |
A11 |
B11 |
C11 |
D11 |
|
|
|
H11 |
JS11* |
|
|
|
|
|
|
|
|
|
|
|
|
12 |
|
B12 |
|
|
|
|
|
H12 |
JS12* |
|
|
|
|
|
|
|
|
|
|
|
|
13 |
|
|
|
|
|
|
|
H13* |
JS13* |
|
|
|
|
|
|
|
|
|
|
|
|
14 |
|
|
|
|
|
|
|
H14* |
JS14* |
|
|
|
|
|
|
|
|
|
|
|
|
15 |
|
|
|
|
|
|
|
H15* |
JS15* |
|
|
|
|
|
|
|
|
|
|
|
|
16 |
|
|
|
|
|
|
|
H16x |
JS16* |
|
|
|
|
|
|
|
|
|
|
|
|
17 |
|
|
|
|
|
|
|
H17* |
JS17* |
|
|
|
|
|
|
|
|
|
|
|
|
Примечание к табл. 6.1 и 6.2.:
* – поля допусков, как правило, не предназначенные для посадок;
жирным шрифтом выделены предпочтительные поля допусков.
29
29