
Тут есть жесткость воды
.pdfВ химических производствах используют три схемы водооборота в зависимости от тех изменений, которые претерпевает вода в процессе производства:
вода только нагревается и должна быть перед возвращением в цикл охлаждена, например, в градирнях (рис. 2.0., схема А);
вода только загрязняется и должна быть перед возвратом очищена в специальных очистных сооружениях (рис.2.0., схема Б);
вода в процессе и нагревается, и загрязняется; в этом случае используют комбинацию водооборотов первого и второго типов.
Водооборотные циклы технологических установок, цехов и химических предприятий в целом являются важнейшим фактором рационального использования водных ресурсов. В этих циклах осуществляется многократное использование воды без выброса загрязненных стоков в водоемы, а потребление свежей воды для ее восполнения ограничено только технологическими превращениями (в качестве компонента сырья) и естественными потерями.
30
2.3.ВОЗДУХ В ХИМИЧЕСКОЙ ПРОМЫШЛЕННОСТИ
Воздух – сырьё практически неисчерпаемое. Воздух в химической промышленности применяют в основном как сырье или как реагент в технологических процессах, а также для энергетических целей.
Технологическое применение воздуха обусловлено химическим составом атмосферного воздуха (таблица 2.3).
Таблица 2.3. Состав сухого воздуха
Вещество |
Химическая |
Содержание по |
Содержание по |
|
формула |
объёму, % |
массе, % |
Азот |
N2 |
78,08 |
75,52 |
Кислород |
O2 |
20,95 |
23,15 |
Аргон |
Ar |
0,93 |
1,29 |
Диоксид углерода |
CO2 |
0,038 |
0,058 |
Неон |
Ne |
0,0018 |
0,0013 |
Гелий |
He |
0,000524 |
0,000073 |
Криптон |
Kr |
0,000114 |
0,003 |
Ксенон |
Xe |
0,0000087 |
0,00004 |
Чаще всего используют кислород воздуха в качестве окислителя. Воздух широко применяют для проведения окислительных реакций в производстве серной, азотной и фосфорной кислот. Неполным окислением углеводородов получают спирты, альдегиды, уксусную кислоту.
Воздух – сырьё для получения кислорода, азота, аргона и других газов. Замена воздуха кислородом позволяет значительно интенсифицировать производственные процессы. Кислород, выделяемый ректификацией жидкого воздуха, в больших количествах расходуют для кислородной плавки металлов, в доменном процессе и т.п. При ректификации получают также азот и инертные газы, в основном аргон. Азот используют в качестве сырья в производстве синтетического аммиака и других азотсодержащих веществ и как инертный газ. Аргон применяют для создания инертной атмосферы в ходе химического промышленного или лабораторного синтеза, если необходимо исключить процессы окисления. Сжиженные газы (азот, кислород, аргон и др.) широко используют в криогенной технике для получения глубокого холода и в процессах криохимической технологии (например, для получения чистых и сверхчистых продуктов).
Воздух, применяемый в качестве реагента, подвергается, в зависимости от характера производства, очистке от пыли, влаги и контактных ядов (веществ, отравляющих катализаторы). Для этого воздух пропускают через промывные башни с различными жидкими поглотителями (вода, щелочи и др.), мокрые и сухие электрофильтры, аппараты с влагопоглотительными сорбентами и пр.
Энергетическое применение воздуха связано, прежде всего, с использованием кислорода как окислителя для получения тепловой энергии при сжигании различных топлив.
Воздух используется также как хладагент при охлаждении газов и жидкостей в воздушных холодильниках или в аппаратах прямого контакта (например, охлаждение воды в градирнях), при грануляции расплавов некоторых соединений (например, карбамида). В других случаях нагретый воздух применяют как теплоноситель для нагрева газов или жидкостей.
В пневматических барботажных смесителях используют сжатый воздух для перемешивания жидкостей и пульпы, в форсунках - для распыления жидкостей в реакторах и топках.
31
Сжатый воздух применяется при пневматическом способе транспортирования сыпучих продуктов. Пневмотранспортирование используют при необходимости подачи сырья, материалов, продукции на большие расстояния, в условиях сложной производственной компоновки.
2.4.ПОДГОТОВКА И ОБОГАЩЕНИЕ СЫРЬЯ
Сырьё, предназначенное для переработки в готовую продукцию, должно удовлетворять определённым требованиям. Это достигается комплексом операций, составляющих процесс подготовки и обогащения сырья. Методы подготовки и обогащения сырья зависят от его агрегатного состояния.
Подготовка твёрдого сырья включает измельчение, классификацию, сушку.
Подготовка жидкого сырья заключается в его очистке от твёрдых и газообразных примесей. В качестве методов очистки от твёрдых примесей применяют отстаивание, фильтрование, центрифугирование. Газообразные примеси могут быть удалены нагревом или интенсивным механическим перемешиванием.
Газообразное сырьё подвергают предварительной очистке от жидких и твёрдых примесей. Для этого применяют методы, аналогичные методам очистки жидкого сырья от твёрдых примесей, а также очистку в электрофильтрах.
Обогащением сырья называется процесс отделения полезной части сырья (полезного компонента) от пустой породы (балласта) с целью повышения концентрации полезного компонента. Обогащение позволяет получать концентрированное сырьё.
Если обогащают твёрдые материалы, то полученный продукт, обогащённый полезной составной частью, называют концентратом, а отходы, содержащие пустую породу, -
хвостами.
Если в сырье содержится несколько полезных компонентов, его делят на составные части (фракции), обогащённые тем или иным компонентом.
Обогащение необходимо также потому, что запасы концентрированного сырья в природе постепенно истощаются, и промышленность вынуждена отделять полезные компоненты бедного сырья от большого количества еще не используемой пустой породы. Обогатительные фабрики обычно строят в местах добычи сырья. При обогащении сырья на месте его добычи сокращаются транспортные расходы на перевозку его к месту переработки.
Обогащение полезных ископаемых осуществляют с помощью ряда последовательных операций, составляющих схему обогащения (рис.2.2.). При обогащении получают две или более фракций. Фракцию, обогащенную полезным компонентом горной породы, называют концентратом. Фракции, состоящие из минералов, не используемых в данном производстве, называют хвостами.
Методы обогащения основаны на различии физических и физико-химических свойств компонентов сырья, таких как размеры частиц, плотность, электропроводность, магнитная проницаемость, свойства поверхности (гидрофильность, гидрофобность), температуры плавления, сжижения и т.д. Методы обогащения разнообразны и принципиально различны для твёрдого, жидкого и газообразного сырья.
Методы обогащения твёрдого сырья подразделяют на механические (физические), физикохимические, химические и термические.
32

Механические методы основаны на различии физических свойств компонентов сырья, таких как размер частиц, плотность, твёрдость, электропроводность, магнитная проницаемость и др. Важнейшими механическими способами обогащения твёрдого сырья являются рассеивание (грохочение), гравитационное разделение, электромагнитная и электростатическая сепарация.
ИСХОДНОЕ СЫРЬЁ
(полезные ископаемые)
ПОДГОТОВКА
(измельчение, промывка, сушка)
ОБОГАЩЕНИЕ
КОНЦЕНТРАТ |
|
ХВОСТЫ |
|
|
|
|
|
(полезный компонент) |
|
(пустая порода) |
Рис. 2.2. Схема обогащения сырья
К физико-химическим методам относится флотация.
Химические методы обогащения основаны на применении реагентов, которые избирательно (селективно) растворяют одно из веществ, входящих в состав смеси, или на образовании и осаждении новых соединений. К химическим методам обогащения относится выщелачивание. Выщелачивание – это метод извлечения ценных компонентов путём их растворения в воде, растворах кислот, щелочей, солей с окислителями или восстановителями, а также в органических растворителях. Методом выщелачивания извлекают из руд и концентратов цветные металлы, уран, золото, хлорид калия из сильвинита и др.
Методы термического обогащения основаны на различии температуры плавления отдельных составляющих сырья. Эти методы используются в промышленности сравнительно редко. Таким методом осуществляют выплавку серы (температура плавления 113 С) непосредственно из подземных залежей.
Химические и термические методы обогащения имеют ограниченное применение в химической технологии и являются объектом изучения спецкурсов.
Для твёрдого сырья чаще всего применяют механические способы обогащения – рассеивание (грохочение), гравитационное разделение, электромагнитную сепарацию, а также физикохимический метод – флотацию. Исходный материал вначале дробят и измельчают с целью доведения его до размеров, пригодных для осуществления обогатительных процессов. Для дробления применяют дробилки, доводящие материал до крупности частиц 20-30 мм. Тонкое измельчение осуществляют в мельницах. Ниже будут рассмотрены наиболее широко применяемые механические и физико-химические методы обогащения твёрдых материалов.
33

2.4.1. Грохочение
Грохочение – процесс классификации частиц по их геометрическому размеру. Форма частиц и плотность материала, из которого они состоят, могут иметь определённое значение, но в гораздо большей степени разделение зависит от размера частиц.
Рассеивание (грохочение) применяют для разделения твёрдой породы, содержащей минералы различной прочности и образующей при измельчении зёрна разной величины. При последовательном пропускании измельчённого сырья через грохоты - металлические сита с отверстиями разных размеров – происходит разделение на фракции, обогащённые определённым минералом. Рассеиванием обогащают, например, сланец, разделяя его на концентрат и пустую породу (содержащую в основном известняк), фосфатное сырьё и др.
Грохот представляет собой механическое вибрационное сито (рис. 2.3). Свое необычное название он получил из-за характерного звука (грохота), издаваемого в процессе работы. Минералы, входящие в состав сырья, имеют различную прочность. При дроблении менее прочные (хрупкие) материалы дробятся на более мелкие зёрна, чем более прочные. Если после измельчения такое сырьё просеять через сита с различной величиной отверстий, то с отдельных сит можно получить фракции, обогащённые тем или иным минералом.
Грохочение часто производят и для разделения однородного материала на куски или зёрна определённого размера.
Рис. 2.3. Схема грохота
Грохот – один из основных видов технологического оборудования обогатительных фабрик.
Рис. 2.4. Вибрационный грохот с одним и двумя ситами
Грохоты могут быть плоскими и цилиндрическими (барабанными). Плоские грохоты состоят из одного или нескольких сит. Сита имеют небольшой наклон для скольжения крупной фракции и снабжены механизмами для сотрясения, вибрации или качания (на рис. 2.4 и 2.5 вибрационный и дисковый грохоты). Материал, двигаясь по ситу грохота, расслаивается: чем
34
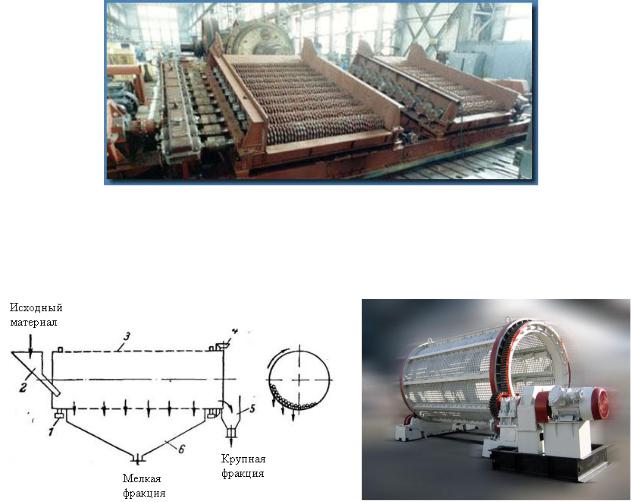
крупнее частицы, тем выше слой, в котором они движутся. Частицы, размер которых в поперечнике меньше размера отверстия сита, достигнув его поверхности, проваливаются через отверстие, т.е. просеиваются (в нижний, подрешётный, продукт). Более крупные частицы скатываются по ситу и образуют верхний, надрешётный, продукт.
Рис. 2.5. Дисковый грохот
Барабанный грохот (рис. 2.6. и 2.7.) представляет собой наклонный вращающийся барабан с отверстиями. Исходный материал поступает внутрь барабана. При движении происходит разделение материала на фракции.
Рис. 2.6. Схема барабанного грохота |
Рис. 2.7. Грохот цилиндрический |
|
вращающийся |
Эффективность грохотов зависит от многих факторов: крупности, формы частиц исходного материала и его нагрузки на грохот; типа грохота; размера и формы отверстий сита, его длины и угла наклона. Максимальная эффективность у барабанных грохотов 60-70%, качающихся 70-80%, вибрационных 90-98%.
2.4.2. Гравитационное обогащение
Гравитационное обогащение (мокрое и сухое) основано на разной скорости падения частиц разной плотности и крупности в потоке жидкости или газа или на действии центробежной силы. Чаще всего проводят мокрое обогащение. Гравитационные способы применяют для обогащения сырья в производствах силикатных материалов, минеральных солей, в металлургии, а также при обогащении углей и сланца.
Принципиальная схема мокрого гравитационного обогащения приведена на рис. 2.8., а внешний вид аппарата – на рис. 2.9. Измельченный материал, перемешанный с водой в
35

смесителе, подается в виде пульпы в отстойник, разделенный вертикальными перегородками на три осадительные камеры. Каждая камера снабжена в нижней части бункером (конусообразным днищем). Самые крупные и тяжелые частицы оседают наиболее быстро в камере I, средние – в камере II, легкие – в камере III. Наиболее мелкие и легкие частицы породы уносятся водой из отстойника.
Рис. 2.8. Принципиальная схема мокрого гравитационного обогащения: I, II, III – осадительные камеры;
1 – выпуск тяжёлой (крупнозернистой) фракции; 2 - выпуск средней фракции; 3 - выпуск лёгкой (мелкозернистой фракции.
Рис. 2.9. Машина для гравитационного обогащения полезных ископаемых
К аппаратам мокрого гравитационного обогащения, основанного на действии центробежной силы, относится гидроциклон. Корпус гидроциклона имеет цилиндрическую и коническую части (рис. 2.10.). Через боковой патрубок по касательной к цилиндрическому корпусу подается под давлением разделяемая пульпа. При вращении пульпы тяжёлые частицы под действием центробежной силы отбрасываются к стенкам, уплотняются, движутся по спиральной траектории вниз и выводятся из нижней части гидроциклона. Взвешенные в жидкости лёгкие частицы, передвигаясь во внутреннем спиральном потоке, поднимаются по шламовому патрубку в камеру слива и удаляются из неё.
Габариты гидроциклонов по сравнению с габаритами осадительных камер меньше, а производительность больше.
36

Рис. 2.10. Схема и общий вид гидроциклона
Обогащение в тяжёлой среде. Метод обогащения в тяжёлой среде основан на различной плотности разделяемых компонентов и тяжёлой среды (плотность которой больше плотности воды, обычно 2,5 – 3,5 г/см3). Применяется для всех видов твёрдых горючих ископаемых (углей, антрацитов, горючих сланцев), руд чёрных и цветных металлов, фосфатных руд.
Сущность процесса обогащения в тяжёлых средах заключается в том, что если компоненты обогащаемых полезных ископаемых (например, сланец и известняк) различаются по плотности, то при погружении этих полезных ископаемых в среду промежуточной плотности получаются две фракции – осевшая и всплывшая. В одной из фракций сосредотачиваются полезные минералы, а в другой - пустая порода. Частицы, плотность которых выше плотности суспензии, погружаются на дно, менее плотные всплывают на поверхность и удаляются гребками. Плотность известняка больше, чем плотность сланца, поэтому более тяжёлые частицы известняка оседают на дне, а более лёгкие частицы сланца всплывают на поверхность. Известняк образует остаток обогащения и вывозится в отвал. Тяжёлые суспензии готовят из смеси тонкоизмельчённых твёрдых частиц (утяжелителей) и воды. В качестве утяжелителей применяют магнетит, ферросилиций, неорганические соли. Плотность суспензии регулируется концентрацией в ней утяжелителя.
Рис. 2.11. Сепаратор для обогащения в тяжёлой среде
Сухое гравитационное обогащение.
воздушные сепараторы (рис. 2.12.).
Основное преимущество обогащения в тяжёлых средах в том, что этот метод позволяет достичь чёткого разделения компонентов даже при небольшом различии их плотности. Недостатком является необходимость регенерации суспензий.
Аппараты для обогащения в тяжёлых средах - сепараторы (рис.2.11) - представляют собой ванны различных конфигураций (конусные, пирамидальные, барабанные и др.), с устройствами для вывода продуктов обогащения.
При сухом гравитационном обогащении применяют
37

Сепаратор состоит из цилиндра 1, который заканчивается конусом 2. В цилиндр 1 помещён внутренний цилиндр 3 с конусом 4. Во внутреннем цилиндре имеется тарелка 6 и крыльчатка вентилятора 5, приводимые в движение от электромотора. При вращении тарелки и крыльчатки вентилятора внутри сепаратора образуются воздушные потоки, показанные на схеме голубыми стрелками.
|
Измельчённый |
материал, |
подаваемый |
на |
|
|
вращающуюся тарелку, разбрасывается по сечению |
||||
|
внутреннего цилиндра. |
|
|
||
|
Мелкие |
частицы |
материала |
подхватываются |
|
|
воздушным потоком и выносятся в пространство |
||||
|
между внешним и внутренним цилиндрами, где, |
||||
Рис. 2.12. Схема сепаратора |
ударяясь о стенки (теряя скорость движения), |
||||
1 – внешний цилиндр; 2 – конус; 3 – |
опускаются вниз и выводятся через конус 2 в виде |
||||
внутренний цилиндр; 4 – конус; 5 – |
тонкоизмельчённой фракции. |
|
|
||
крыльчатка вентилятора; 6 – тарелка. |
Крупные |
частицы падают и |
выводятся |
через |
|
|
внутренний конус 4.
2.4.3. Флотация
Флотация – широко распространённый и универсальный способ обогащения. Она основана на различии в смачиваемости минералов, входящих в состав руды.
Схема процесса флотации приведена на рис. 2.13.
Рис. 2.13. Схема процесса флотации
Частицы несмачиваемого (гидрофобного) минерала прилипают к пузырькам воздуха и всплывают на поверхность воды. Частицы смачиваемого (гидрофильного) материала
38

обволакиваются плёнкой жидкости и, преодолев силы поверхностного натяжения жидкости, опускаются на дно аппарата (рис. 2.14.).
Рис. 2.14. Движение частиц в жидкости: 1 – несмачиваемая (гидрофобная) частица, 2- смачиваемая (гидрофильная) частица.
Прилипание к пузырькам усиливается при селективном покрытии частиц одного из минералов поверхностноактивным веществом.
Большинство минералов природных руд мало отличаются по смачиваемости друг от друга. Для их разделения нужно создать условия неодинаковой смачиваемости водой отдельных компонентов породы. Для этого применяют различные флотационные реагенты. Они избирательно усиливают или ослабляют смачиваемость водой, а также прилипаемость к пузырькам воздуха взвешенных минеральных частиц.
К веществам, понижающим смачиваемость, относятся т.н. собиратели, или коллекторы. К ним относятся олеиновая кислота, нафтеновые кислоты, парафин и др. Собиратели покрывают поверхность частиц гидрофобной плёнкой, чем и объясняется их всплывание. Чтобы затруднить всплывание частиц отдельных минералов, в суспензию вводят подавители, или депрессоры (щёлочи, соли щелочных металлов и др.). Подавители повышают гидрофильность поверхности частиц минералов и затрудняют их всплывание.
Флотацию проводят во флотационных машинах различного типа. Различия в конструкциях флотационных машин в основном определяются способом аэрации пульпы.
По этой характеристике машины делят на три группы:
1)механические (перемешивание пульпы, засасывание и диспергирование воздуха осуществляется импеллером);
2)пневмомеханические (воздух подаётся воздуходувкой, диспергирование и перемешивание пульпы выполняются импеллером);
3)пневматические (перемешивание и аэрация пульпы осуществляется подачей сжатого воздуха через аэраторы различных конструкций).
Рис. 2.15. Схема флотационной машины 1 – камера; 2 – коллектор воздуха; 3 – воздушные трубки; 4 – пенный продукт; 5 – жёлоб; 6 –
перегородки.
39