
Лекции_строительные материалы и конструкции
.pdf
Повышенной крупности, |
Класс I |
|
|
|
0,5 |
5 |
5 |
||
крупный и средний |
||||
|
|
|
||
Мелкий |
0,5 |
5 |
10 |
|
Очень крупный и |
Класс II |
|
|
|
5 |
20 |
10 |
||
повышенной крупности |
||||
|
|
|
||
Крупный и средний |
5 |
15 |
15 |
|
Мелкий и очень мелкий |
0,5 |
10 |
20 |
|
Тонкий и очень тонкий |
Не допускается |
Не нормируется |
- |
В табл. 3.3 приведены требования к мелкому заполнителю по содержанию пылевидных и глинистых частиц.
|
Содержание пылевидных и глинистых частиц |
Таблица 3.3 |
|||
|
|
||||
|
Содержание пылевидных и |
Содержание глины в комках |
|||
|
глинистых частиц |
||||
|
|
|
|||
Класс и |
в песке |
в песке из |
в песке |
в песке из |
|
отсевов |
отсевов |
||||
группа песка |
природном |
природном |
|||
дробления |
дробления |
||||
|
|
|
|||
Очень |
|
Класс I |
|
|
|
- |
3 |
- |
0,35 |
||
крупный |
|||||
|
|
|
|
||
Повышенной |
|
|
|
|
|
крупности, |
2 |
3 |
0,25 |
0,35 |
|
крупный и |
|||||
|
|
|
|
||
средний |
3 |
|
0,35 |
|
|
Мелкий |
5 |
0,50 |
|||
Очень |
|
Класс II |
|
|
|
- |
10 |
- |
2 |
||
крупный |
|||||
|
|
|
|
||
Повышенной |
|
|
|
|
|
крупности, |
3 |
10 |
0,5 |
2 |
|
крупный и |
|||||
|
|
|
|
||
средний |
|
|
|
|
|
Мелкий и |
5 |
|
0,5 |
|
|
очень |
10 |
2 |
|||
мелкий |
|
|
|
|
|
Тонкий и |
|
Не |
|
|
|
очень |
10 |
1,0 |
0,1* |
||
нормируется |
|||||
тонкий |
|
|
|
||
|
|
|
|
Примечание 1. *Для песков, получаемых при обогащении руд черных и цветных металлов и неметаллических ископаемых других отраслей промышленности.
Примечание 2. В очень мелком природном песке класса II по согласованию с потребителем допускается содержание пылевидных и глинистых частиц до 7% по массе.
51

Для бетонов рекомендуют применять крупные и средние пески. Мелкие пески с модулем крупности менее 1,8 вызывают перерасход цемента в бетоне. К числу вредных химических примесей в песке относят органические, сернокислые и сернистые соединения, слюды, аморфные разновидности кремнезема.
В качестве крупного заполнителя в бетонах применяют щебень и гравий. Крупный заполнитель представляет сыпучий природный или искусственный материал с размером частиц 5…150 мм. Щебень из горных пород - неорганический зернистый сыпучий материал с зернами крупностью св. 5 мм, получаемый дроблением горных пород. Щебень получают также дроблением искусственных материалов. Зерна щебня имеет чистую поверхность с многочисленными гранями, выступами и впадинами. Гравий из горных пород - неорганический зернистый сыпучий материал с зернами крупностью св. 5 мм, получаемый рассевом природных гравийно-песчаных смесей. Гравий является продуктом естественного разрушения горных пород окатанной формы. Щебень относится к более качественному виду заполнителя по сравнению с гравием, так как благодаря своей развитой поверхности он надежнее сцепляется в бетоне с растворной частью.
ГОСТ8267-93 регламентирует зерновой состав крупного заполнителя, его прочность, наличие пылевидных и глинистых примесей. Щебень и гравий выпускают в виде следующих основных фракций: от 5 (3) до 10 мм; свыше 10 до 20 мм; свыше 20 до 40 мм; свыше 40 до 80 (70) мм и смеси фракций свыше 5 (3) до 20 мм. По согласованию изготовителя с потребителем выпускают щебень и гравий в виде фракций от 10 до 15 мм; свыше 15 до 20 мм; свыше 80 (70) до 120 мм и свыше 120 до 150 мм, а также смеси фракций свыше 5 (3) до 15 мм; свыше 5 (3) до 40 мм; свыше 20 до 80 (70) мм. Полные остатки на контрольных ситах при рассеве щебня и гравия фракций от 5 (3) до 10 мм, св. 10 до 20 мм, св. 20 до 40 мм, св. 40 до 80 (70) мм и смеси фракций от 5 (3) до 20 мм и от 5 до 15 мм должны соответствовать указанным в табл. 3.4 , где d и D - наименьшие и наибольшие номинальные размеры зерен. Прочность крупного заполнителя должна соответствовать прочности бетона, в котором он будет использоваться.
|
|
|
|
Таблица 3.4 |
Полные остатки крупного заполнителя на контрольных ситах |
||||
Диаметр |
|
|
|
|
отверстий |
|
|
|
|
контрольных |
d |
0,5(d+D) |
D |
1,25D |
|
52
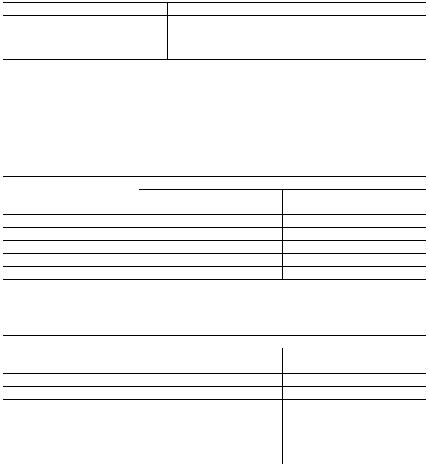
сит, мм |
|
|
|
|
Полные остатки |
|
|
|
|
на ситах, % по |
|
|
|
|
массе |
От 90 до 100 |
От 30 до 80 |
До 10 |
До 0,5 |
|
Прочность заполнителя оценивается сдавливанием отдельных фракций в цилиндре диаметром 150 мм под нагрузкой 20 в течение 2 мин по массе раздробившихся и прошедших через контрольное сито частиц, %, табл. 3.5-3.6.
|
|
Таблица 3.5 |
Марка по дробимости щебня из изверженных пород |
||
Марка по дробимости |
Потеря массы при испытании щебня, % |
|
щебня из изверженных |
из интрузивных пород |
из эффузивных пород |
пород |
(глубинных) |
(излившихся) |
1400 |
До 12 включ. |
До 9 включ. |
1200 |
Св. 12 до 16 |
Св. 9 до 11 |
1000 |
Св. 16 до 20 |
Св. 11 до 13 |
800 |
Св. 20 до 25 |
Св. 13 до 15 |
600 |
Св. 25 до 34 |
Св. 15 до 20 |
|
|
Таблица 3.5 |
Марка по дробимости щебня из осадочных и метаморфических пород |
||
Марка по дробимости |
Потеря массы при испытании щебня, % |
|
щебня из осадочных и |
в сухом состоянии |
в насыщенном водой |
метаморфических пород |
|
состоянии |
1200 |
До 11 включ. |
До 11 включ. |
1000 |
Св. 11 до 13 |
Св. 11 до 13 |
800 |
Св. 13 до 15 |
Св. 13 до 15 |
600 |
Св. 15 до 19 |
Св. 15 до 20 |
400 |
Св. 19 до 24 |
Св. 20 до 28 |
300 |
Св. 24 до 28 |
Св. 28 до 38 |
200 |
Св. 28 до 35 |
Св. 38 до 54 |
В крупном заполнителе ограничивается также содержание зерен игловатой и пластинчатой (лещадной) формы Группы щебня по содержанию зерен игловатой и пластинчатой формы приведены в табл.(табл.3.6.). К пластинчатым зернам относят плоские частицы, максимальный размер которых в 3 раза и более превышающий их толщину. К игловатым зернам относят вытянутые по форме частицы, у которых соотношение максимального размера к минимальному (поперечному) размеру ≥ 3.
Таблица 3.6
Группы щебня по содержанию зерен игловатой и
53
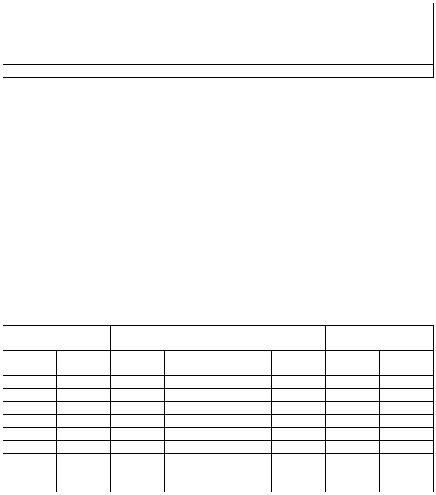
|
пластинчатой (лещадной) формы |
|
||
Содержание |
|
|
|
|
зерен |
До 15 |
Свыше 15 до |
Свыше 25 до |
Свыше 35 до |
игловатой и |
включительно |
25 |
35 |
50 |
лещадной |
|
|
|
|
формы, % |
|
|
|
|
Группа щебня |
1 |
2 |
3 |
4 |
3.2.Классификация бетонов
Взависимости от средней плотности бетон делят на марки. Условно
марку бетона по плотности обозначают символом D, после которого указывается значение средней плотности в сухом состоянии (кг/м3). По
средней плотности различают особо тяжелый ( 0 = свыше 2500 кг/м3),
тяжелый ( 0 св. 1800 до 2500 кг/м3), легкий ( 0 свыше 500 до 1800
кг/м3) и особо легкий бетоны ( 0 ≤500 кг/м3). По гарантированному
пределу прочности при сжатии (МПа) кубов из бетона с ребром 150 мм в возрасте 28 суток нормального твердения (при влажности 95±5 % и температуре 20±2°С) бетон делят на классы.
|
|
|
Классы бетона по прочности |
|
Таблица 3.7 |
||
|
|
|
|
|
|||
Предел прочности |
Маркировка бетона |
Предел прочности |
Маркировка бетона |
||||
при сжатии |
|
|
при сжатии |
|
|
||
кг/см2 |
МПа |
Марка, |
Класс, |
кг/см2 |
МПа |
Марка, |
Класс, |
|
|
кг/см2 |
МПа |
|
|
кг/см2 |
МПа |
10 |
1,0 |
М10 |
В0,4 |
250 |
25 |
М250 |
В20 |
15 |
1,5 |
М15 |
В1 |
300 |
30 |
М300 |
В25 |
25 |
2,5 |
М25 |
В1,5 |
350 |
35 |
М350 |
В27,5 |
35 |
3,5 |
М35 |
В2,5 |
400 |
40 |
М400 |
В30 |
50 |
5,0 |
М50 |
В3,5 |
450 |
45 |
М450 |
В35 |
75 |
7,5 |
М75 |
В5 |
500 |
50 |
М500 |
В40 |
100 |
10,0 |
М100 |
В7,5 |
600 |
60 |
М600 |
В50 |
150 |
15,0 |
М150 |
В12,5 |
700 |
70 |
М700 |
В55 |
200 |
20,0 |
М200 |
В15 |
800 |
80 |
М800 |
В60 |
По степени морозостойкости бетоны делят на марки F10…F300. Марка по морозостойкости определяется количеством циклов замораживания и оттаивания, которое выдерживает бетон в насыщенном водой состоянии, не теряя более 15 % прочности и более 5 % средней плотности. Замораживание кубов из бетона с ребром 100 мм проводят при температуре «-15°С±2°С».
54
По назначению бетон классифицируют на конструкционный, теплоизоляционный, и кострукцонноо-теплоизоляционный.
По области применения бетон классифицируют на обычный и специальный (рентгенозащитный, гидротехнический, жаростойкий, дорожный и кислотоупорный). По водонепроницаемости бетон делят на марки W2…W6. Марки бетона по водонепроницаемости показывают максимальное давление. которому может сопротивляться бетон, не пропуская воду.
3.3. Структура и свойства бетона
Важнейшей характеристикой структуры бетона является соотношение растворной части бетона и заполнителя. Относительное содержание заполнителя может быть таково, что его частицы (зерна) раздвигаются цементным тестом и практически не касаются друг друга. Схема, при которой цементное тесто заполняет поры между зернами заполнителя, но их не раздвигает, носит название контактной. Третья схема структуры - с незаполненной или частично незаполненной межзерновой пустотностью – крупнопористая. Степень и характер пористости оказывают существенное влияние на важнейшие свойства бетона: среднюю плотность, теплопроводность, прочность, морозостойкость и водонепроницаемость. В бетоне различают поры трех видов: в цементном геле, в растворной части и в заполнителе.
При смешивании компонентов бетона образуется бетонная смесь. Бетонная смесь обладает свойством тиксотропии: при воздействии вибрации она становится более подвижной, уподобляется жидкости. В состоянии покоя он приобретает некоторую структурную прочность. Для обеспечения качественного уплотнения при укладке для различных условий технологии приготавливают смеси разной консистенции – от жестких до литых.
Для характеристики консистенции бетонной смеси используют показатели подвижности и жесткости. Подвижность измеряют по осадке конуса. Подвижность – это способность отформованной в виде усеченного конуса бетонной смеси перемещаться под действием собственной силы тяжести.
Для смесей, не дающих осадки конуса, применяется оценка консистенции по показателю жесткости. Жесткость измеряется временем (сек), необходимом для растекания отформованной бетонной смеси под действием вибрации. Значения подвижности и жесткости
55
определяются |
технологией укладки бетонной смеси. В связи с этим на |
практике возникает необходимость корректировать их значения. |
|
Подвижность |
бетонной смеси можно увеличить за счет увеличении |
содержания цементного теста или снижения относительного содержания крупного заполнителя. Известно, что применяемые цементы могут отличаться показателями нормальной густоты, то есть показателями водопотребности. Соответственно, цемент с высокой водопотребностью понижает подвижность.
Основной технической характеристикой бетона является прочность. Прочность бетона Rб зависит от цементноводного отношения Ц/В, качества заполнителей и цемента (коэффициент А), активности цемента Rц, условий и времени твердения
Rб = А Rц(Ц/В ±С),
где А и С –эмпирические коэффициенты.
Класс бетона устанавливают в возрасте 28 суток. При твердении в нормальных условиях взаимосвязь прочности бетона в возрасте 28 суток и n cуток (где 3 ≤n≤28), определяется выражением
lg28
R28 = Rn |
|
. |
|
lgn
Понижение Ц/В снижает прочность бетона так как снижается концентрация цементного клея.
Прочность бетона определяют разрушающим и безразрушающими методами. Рост прочности бетона во многом определяется температурно-влажностным режимом твердения. Повышение температуры влажной среды ускоряет рост прочности. Разработана технология ускорения твердения введением химических добавок - ускорителей твердения.
Мероприятия, направленные на создание благоприятных условий твердения в начальный период называется уходом за бетоном. В условиях сухого жаркого климата поверхность бетона укрывают пленкообразующими покрытиями, пленками, орошают водой. В условиях пониженных температур поверхность бетона утепляют препятствуя переохлаждению и замерзанию, в бетон вводят противоморозные добавки, используют методы прогрева и обогрева бетонных конструкций.
3.4. Технология бетона
56
Технология изготовления бетонных изделий состоит в дозировании компонентов, приготовлении бетонной смеси, ее транспортировке и укладке, уплотнении в формах и твердении.
Дозирование компонентов должно осуществляться с помощью весовых дозаторов по массе с точностью 1 % для цемента и воды и 2 % для заполнителей. Бетонную смесь приготавливают в смесителях непрерывного и периодического действия. По способу перемешивания смесители делят на гравитационные и принудительные.
В гравитационном смесителе на стенках смесительного барабана укреплены лопасти, которые при вращении корпуса поднимают бетонную смесь в верхнюю часть корпуса, откуда под влиянием сил гравитации она падает на дно смесителя. Таким, образом, перемешивание происходит под влиянием сил гравитации. Достоинство гравитационных смесителей определяется их экономичностью, простотой конструкции. Перемешивание жестких смесей в них затруднено. Гравитационный смеситель может работать по непрерывной схеме. Для этого его изготавливают в виде вращающегося горизонтального цилиндра, с одного торца которого идет загрузка материалов, а с другого – выгрузка бетонной смеси. В принудительном смесителе бетонная смесь приготавливается в неподвижном корпусе, в полости которого вращаются лопасти, жестко закрепленные на вертикальном или горизонтальном валу. В таких смесителях достигается качественное перемешивание как жестких, так и литых смесей, с применением тяжелых и легких заполнителей.
Продолжительность перемешивания зависит от вида смеси, объема смеси и типа смесителя и обычно составляет от 50 с до 5 мин. Применение поверхностно-активных химических добавок – суперпластификаторов расширяет возможности внедрения новых видов смесителей, обеспечивающих интенсивное перемешивание компонентов и активацию цемента – турбулентных, струйных, в вибросмесителях и ультразвуковых виброактиваторах. Интенсивное перемешивание активирует растворение цементных частиц, повышает скорость нарастания прочности, сокращает время перемешивания.
Уплотнение при укладке бетона – необходимое условие получения заданной прочности. В зависимости от принятых условий технологии уплотнение осуществляют прессованием, вибрацией, вибропрессованием, вакууммированием с вибрацией, центрифугированием. Для укладки весьма подвижных смесей применяют литье. Вибрация при укладке осуществляется с помощью поверхностных, навесных и глубинных вибраторов, работающих от
57
тока промышленной частоты 50 Гц (3000 кол/мин) с амплитудой около 0,3 мм. Для интенсификации уплотнения применяется высокочастотное и поличастотное вибрирование, а также ударное уплотнение с высокой амплитудой (3 мм) и низкой частотой (60…120 кол/мин). Центрифугирование основано на уплотнении бетонной смеси центробежными силами в процессе ее вращения. Его применяют для формовки безнапорных труб и других «кольцевых» конструкций. Вакууммирование основано на создании разницы между атмосферным давлением и давлением в порах бетона. Вакууммирование удаляет воздух и избыток воды из бетонной смеси, значительно уплотняя структуру бетона.
Твердение бетона на портландцементе – длительный процесс. Наиболее интенсивно он протекает в первые сутки. Проектную прочность бетона устанавливают в возрасте 28 суток. В благоприятных условиях набор прочности бетона может продолжаться в течение года и дольше. Интенсивность набора прочности зависит от минералогического состава цемента, от применения ускорителей твердения и условий твердения. Существует ряд технологических приемов ускоренного твердения бетона.
1 - тепловлажностная обработка (ТВО) – пропаривание насыщенным водяным паром атмосферного давления в пропарочных камерах. Цикл пропаривания включает выдержку бетонных изделий в течение 2…4 часов после изготовления в условиях комнатной температуры; нагрев до температуры 80…90 °С со средней скоростью 30 °С/ч, изотермическую выдержку в течение 8…12 часов, понижение температуры пара со средней скоростью 30 °С/ч. Общая продолжительность цикла составляет приблизительно 12…16 часов;
2 – контактный обогрев – состоит в обогреве бетонных изделий через плотные непроницаемые перегородки. Контактный обогрев выполняют с помощью теплоэлектронагревателей, размещаемых на опалубке. Контактный обогрев происходит, например, при производстве сборного железобетона в кассетах при циркуляции в их изолированных от бетона отсеках насыщенного водяного пара с температурой 90…100°С. В последнее время на строительных объектах внутрь бетонных конструкций закладывают изолированные греющие провода, нагреваемые пропусканием электрического тока. В дальнейшем провода обрезают, оставляя их в бетоне. Распространен также обогрев бетона с помощью теплоэлектронагревателей размещаемых на поверхности бетонной конструкции;
58
3 – электропрогрев – состоит в пропускании через бетон переменного тока напряжением 60…127 В. При этом бетонная смесь, оказывая сопротивление току, разогревается и до 60…80 °С. Так, панели наружных стен из легких бетонов рекомендуют прогревать в горизонтальных формах. В качестве одного электрода используют стальной поддон, в качестве другого – арматурную сетку, ближайшую к
свободной поверхности изделия; |
|
|
|
4 – автоклавная |
обработка |
применяется для производства |
|
силикатных бетонов |
и заключается в запаривании |
изделий |
насыщенным водяным паром повышенного давления в течение 8…12 часов при температуре 175…200 °С и давлении 0,9…1,6 МПа.
3.5. Железобетонные конструкции
Железобетон – композиционный материал, состоящий из бетона и стальной арматуры, работающих совместно. Прочность бетона при растяжении значительно (в 10…15 раз) меньше, чем при сжатии.
Затвердевая, бетон прочно сцепляется со стальной арматурой. При температурах до 100 °С бетон и стальная арматура обладают относительно близкими коэффициентами линейного расширения: для бетона
– (7…14) х10 -6, а для стали – 12х10-6. С изменением температуры возникают незначительные внутренние напряжения в материале, чему способствует пониженная теплопроводность бетона, препятствующая резкому изменению температуры стали. Кроме того, щелочная среда бетона плотной структуры обеспечивает защиту стальной арматуры от коррозии.
Благодаря совместной работе в железобетоне удачно сочетаются свойства бетона и стальной арматуры: бетон воспринимает преимущественно сжимающие усилия, а арматура, в основном, - растягивающие. В некоторых железобетонных конструкциях арматура совместно с бетоном воспринимает и сжимающие усилия.
Для увеличения сцепления арматуры с бетоном на концах гладких стержней арматуры устраивают крюки, арматуре придают периодический профиль, осуществляют армирование сварными сетками и каркасами. В целях предохранения арматуры от коррозии и повышения сцепления с бетоном предусматривается защитный слой бетона на поверхности арматуры толщиной 20…30 мм. Железобетонные конструкции отличают сравнительно высокие огнестойкость и механическая прочность, возможность изготовления изделий различной формы, незначительные затраты на эксплуатацию.
59
Одним из существенных недостатков железобетона является возможность образования трещин вследствие усадки и при деформировании под нагрузкой. Стремление повысить трещиностойкость бетона привело к созданию предварительно напряженного железобетона. Его получают искусственным обжатием бетона в тех местах, где под действием нагрузки возникают растягивающие напряжения. Обжатие бетона достигается предварительным натяжением арматуры в пределах упругих деформаций. Упруго растянутая арматура, стремясь вернуться к первоначальному состоянию, увлекает за собой бетон, создавая в нем предварительное сжатие.
По методу изготовления различают сборные, монолитные и сборно-монолитные конструкции. К монолитным железобетонным конструкциям относят конструкции, изготавливаемые непосредственно на строительной площадке в проектном положении. Монолитные конструкции позволяют создавать сооружения повышенной жесткости, оптимальных размеров. Монолитные конструкции, выполненные индустриальными методами, экономичнее сборных.
Сборные железобетонные конструкции изготавливают в заводских условиях в виде отдельных элементов: фундаментных и стеновых блоков, свай, фундаментных балок, стеновых панелей, плит покрытия и перекрытия, балок, ригелей, прогонов. Перемычек,колонн, ферм, лестничных маршей, площадок и др. Готовые изделия поставляются на стройплощадку при достижении отпускной прочности и устанавливаются в проектное положение монтажными механизмами, после чего закладные детали сопрягаемых элементов соединяются сваркой, а стыки между элементами сборных конструкций замоноличиваются. Применение сборных конструкций базируется на типизации и унификации их размеров, позволяющих уменьшить число типоразмеров, что существенно облегчает процесс изготовления конструкций и их сборки. Производство сборного железобетона обычно дороже монолитного, его преимущество определяется значительным ускорением темпов строительства сооружений.
Технология производства монолитного железобетона включает:
-установку опалубки;
-размещение в ней арматуры;
-приготовление бетонной смеси;
-транспортировку смеси;
-укладку в опалубку и уплотнение бетонной смеси;
-твердение и уход за твердеющим бетоном. Опалубку по виду материала подразделяют
60