
Лекции_строительные материалы и конструкции
.pdfИзносостойкость – сопротивление металла или сплава изнашиванию. Может характеризоваться потерей массы, объема, линейных размеров или их отношением ко времени изнашивания, к площади изнашивания, пути трения, выполненной работе и др.
Жаростойкость – свойство сплава сопротивляться окислению в газовой среде при высоких температурах.
Хладостойкость – способность сплава сохранять пластические свойства при температурах ниже 0 °С.
Жаропрочность - способность сплава сохранять механические свойства при высоких температурах. Жаропрочность оценивают испытанием на растяжение при высокой температуре. Испытания производятся на специальных машинах при приложении к образцу постоянной нагрузки. Нагрев образца, укрепленного в резьбовых захватах, производят в круглой муфельной печи, надетой на образец. Температура печи автоматически поддерживается постоянной. Пределом длительной прочности при заданной температуре является максимальное напряжение, которое выдерживает материал, не разрушаясь при заданном времени испытания.
1.4. Технологические свойства
Технологические свойства характеризуют способность материалов к восприятию определенных технологических воздействий.
Свариваемость – это свойство материалов, нагретых до расплавления или до размягчения, после остывания соединяться в монолит с аналогичными им материалами. Это свойство присуще металлам и пластмассам и используется при изготовлении из них изделий и конструкций.
Ковкость - это способность металлов пластично деформироваться в нагретом состоянии под влиянием ударов.
Гвоздимость – это свойство материалов удерживать введенные в
них металлические изделия – гвозди, скобы, шурупы.
Дробимость – это свойство материалов делиться на части при
ударе.
Технология переработки некоторых строительных материалов в изделия предусматривает пребывание их в пластично-вязком состоянии. Пластично-вязкое состояние количественно характеризуется рядом специфических свойств, зависящих от технологических параметров – рецептуры, материала, температуры, времени и др. Для вяжущих
21
веществ такими свойствами являются нормальная густота и сроки схватывания.
Нормальная густота гипсового теста характеризуется таким количеством воды от массы гипса, %, при котором гипсовое тесто при испытании в вискозиметре Суттарда расплывается, выливаясь из цилиндра на поверхность стекла, в виде лепешки диаметром 120 5 мм.
Нормальная густота цементного теста соответствует такому количеству воды, в процентах от массы цемента, при котором пестик прибора Вика за 30 с не доходит до дна в кольце с цементным тестом на 5…7 мм.
Сроки схватывания вяжущих веществ характеризуются началом и концом схватывания теста нормальной густоты. Началом схватывания цементного теста считают время, прошедшее от момента затворения цемента водой до момента, когда игла прибора Вика не доходит до дна в кольце с тестом на 2…4 мм. Концом схватывания цементного теста считают время от момента затворения до момента, когда игла прибора Вика опускается в тесто не более, чем на 1…2 мм.
Консистенцию растворных смесей измеряют подвижностью.
Подвижность растворной смеси устанавливают испытанием
растворной смеси конусом СтройЦНИЛа (рис. |
13). |
Подвижность |
||
измеряют в сантиметрах |
глубиной погружения |
в растворную смесь |
||
конуса массой 300 г с |
углом при вершине |
30 |
. |
Подвижность |
строительного раствора должна обеспечивать качественное проведение технологического процесса по его укладке.
Величину подвижности назначают в зависимости от области и способа применения строительного раствора. Для заполнения швов между элементами сборных железобетонных конструкций применяют растворные смеси с подвижностью 4…6 см. Для кирпичной кладки подвижность растворов составляет 9…13 см. Штукатурные растворы, в зависимости от состава, вида основания и способа нанесения имеют
подвижность от 7…8 до 9…12 см.
Важнейшим технологическим свойством бетонных смесей является удобоукладываемость, которая отражает их способность заполнять форму при укладке. Количественно удобоукладываемость характеризуют подвижностью и жесткостью бетонной смеси.
Подвижность бетонной смеси – это ее способность растекаться под действием силы тяжести. Для измерения подвижности используют форму из листовой стали в виде усеченного конуса высотой 300 мм с диаметром нижнего основания 200 мм и верхнего – 100 мм. На рис. 14а
22
приведена схема определения подвижности. Бетонную смесь
укладывают в форму в три слоя и каждый слой уплотняют |
25-ю |
|
ударами штыковки, а после снятия формы измеряют |
величину осадки |
|
бетонной смеси в сантиметрах. |
|
|
Жесткость бетонной смеси используют |
для |
оценки |
удобоукладываемости смесей, не дающих осадки под действием силы тяжести. Жесткость измеряется временем в секундах, в течение которого, отформованная в виде усеченного конуса бетонная смесь в техническом вискозиметре полностью растекается под влиянием вибрации (рис. 14б). Перед началом вибрации на отформованную смесь опускают диск с 6-ю отверстиями диаметром 5мм. Вибрирование продолжают до момента, при котором из двух отверстий диска начинает выделяться цементное тесто.
Технология применения битума и материалов на его основе в
ряде случаев |
связана с его |
нагревом, |
способствующем |
переходу |
битума в жидко-текучее состояние. |
|
|
||
Температура размягчения |
битума |
определяется в |
приборе |
«Кольцо и шар». Она соответствует той температуре, при которой битум, залитый в латунное кольцо с внутренним диаметром 16 мм, под действием стального шарика массой 3 г выдавливается на глубину 25, 4 мм (рис.15).
Условная вязкость малярного состава измеряется в секундах временем непрерывного истечения 100 мл состава через калиброванное сопло вискозиметра при температуре 20 С. Условную вязкость можно измерять с помощью вискозиметра ВЗ-4, приведенного на рис. 16. Вискозиметр ВЗ-4 представляет собой воронку объемом 100 мл с диаметром сопла 4 мм. Условная вязкость малярного состава должна обеспечивать образование на поверхности окрашиваемых конструкций однородной защитно-декоративной пленки без подтеков и других дефектов.
1.5.Физико-химические свойства
Кгруппе физико-химических свойств принято относить свойства, определяющие такие параметры состояния материалов, которые существенным образом влияют на химическую кинетику и физико-
механические свойства материалов. Ряд технологических свойств, проявляющихся на физическом уровне, объясняется физикохимическими свойствами материалов.
23
Дисперсность – это характеристика степени измельчения материала. Дисперсность является важнейшим свойством порошкообразных материалов, таких, например, как вяжущие вещества, минеральные наполнители, пигменты. С ростом дисперсности увеличивается суммарная площадь поверхности материала. Поверхности твердых и жидких веществ отличаются особыми свойствами, так как поверхностные слои обладают свободной энергией за счет неуравновешенности молекул, образующих границу раздела. Дисперсность порошкообразных материалов может быть оценена рядом показателей. На практике ее часто определяют по остатку на контрольном сите после просеивания пробы, гранулометрическим составом и удельной поверхностью.
Для определения гранулометрического состава порошков с крупностью частиц, не превышающей 100 мкм, предпринимают седиментационный анализ. Седиментационный анализ основан на том, что скорость падения частиц в жидкой среде зависит от их размеров и, согласно закону Стокса, может быть определена по формуле:
V = |
2 |
r 2 g( |
|
|
|
) |
1 |
, м с-1 |
|
1 |
2 |
|
|||||
9 |
|
|
|
где g = 9,81 м/с2 - ускорение силы тяжести ;
1 и 2 - плотности частицы и среды, кг/м3;
- коэффициент вязкости, кг м-1с –1;
Седиментационный метод определения гранулометрического состава порошкообразных материалов заключается в том, что по истечению определенного срока отстаивания суспензии, приготовленной из исследуемого порошка, отбирается проба, которую выпаривают и взвешивают. По известной концентрации начальной пробы и концентрации проб, взятых спустя различное время отстаивания, можно определить содержание отдельных фракций в исследуемом материале.
Удельная поверхность – это суммарная площадь поверхности частиц, приходящаяся на единицу массы порошкообразного материала. Удельную поверхность порошкообразных материалов можно измерять с помощью приборов типа ПСХ-2 и Т-3. Принцип работы этих приборов основан на том, что с уменьшением размеров частиц в материале возрастают силы сопротивления воздухопроницаемости, что связано
24
сростом площади поверхности порового пространства. Возрастание удельной поверхности цемента увеличивает скорость его твердения.
Способность образовывать жидкие дисперсии.
Порошкообразные материалы обладают способностью образовывать с жидкой средой дисперсные системы. Чем выше степень дисперсности, тем выше устойчивость дисперсных систем. При очень высокой степени дисперсности, которая имеет место в коллоидных системах, самопроизвольное осаждение дисперсоида не происходит, так как ничтожно малые силы земного тяготения, действующие на частицы диспергированного вещества, компенсируются броуновским движением, препятствующим осаждению.
Способность образовывать с водой пластично-вязкие системы.
В порошкообразном состоянии материалы способны также образовывать пластично-вязкие системы. Причиной, обуславливающей образование пластично-вязких систем, является наличие в них промежуточной фазы – воды, связанной с поверхностью смежных твердых частиц. При значительной площади поверхности высокодисперсных материалов роль связанной воды сильно возрастает. Оболочки воды на поверхности твердых частиц выполняют двойную функцию: они служат и связующим звеном пластично-вязкой системы, обеспечивающим сохранение сплошности при деформациях, и, вместе
стем, облегчают скольжение твердых частиц друг относительно друга.
Свойства |
образовывать жидкие дисперсные системы и |
|
пребывать в |
пластично-вязком состоянии |
характерны для |
разнообразных композиционных материалов: красок, эмульсий, мастик, грунтовок; растворных, бетонных, керамических смесей и пластмасс на стадии их технологической переработки.
Растворимость - это способность материалов образовывать с жидкой средой однородные прозрачные системы, состоящие из молекул растворителя и частиц растворенного вещества, между которыми происходят физические и химические взаимодействия. Наиболее распространенным растворителем является вода. По степени растворимости вещества делят на хорошо растворимые, малорастворимые и нерастворимые. В практической деятельности возникают задачи определения содержания массовой доли растворенного вещества в единице объема исследуемого раствора. Решение таких задач может быть сведено к использованию таблиц зависимости концентрации вещества от плотности раствора при заданной температуре. Плотность раствора определяют по шкале ареометра, погружаемого в раствор.
25
Когезия – это свойство материала быть прочным под влиянием сил взаимного сцепления частиц. Когезию оценивают энергией когезии, под которой понимают работу образования новых поверхностей или работу разрыва вещества. Косвенно о когезии можно судить по прочности материалов.
Адгезия - это свойство одного вещества прилипать к поверхности другого. Адгезию характеризуют энергией адгезии, оцениваемую работой удаления одного вещества с поверхности другого. Свойство адгезии используют для создания клеящих, герметизирующих и защитно-декоративных композиционных материалов. Адгезия зависит от природы и строения соприкасающихся веществ.
Определение адгезии лакокрасочных покрытий к металлическим поверхностям проводят методом решетчатых надрезов. Метод состоит в нанесении на готовое лакокрасочное покрытие решетчатых надрезов
ивизуальной оценке степени отслоения покрытия от основания по четырехбалльной шкале. Адгезию приклеивающих, герметизирующих
игидроизоляционных мастик оценивают испытанием склеенных мастикой образцов бетона, кирпича, металла на прочность при отрыве, при сдвиге.
Адсорбция – это свойство поверхности материала притягивать к себе частицы из другой фазы за счет свободной энергии поверхности. По величине энергии, выделяющейся вследствие этого физикохимического процесса, различают физическую, активированную адсорбции и хемосорбцию с химическим взаимодействием.
Строение. Известно, что одни и те же материалы могут иметь как кристаллическое, так и аморфное строение. В аморфном состоянии вещества обладают большим запасом внутренней энергии по сравнению с этими же веществами в кристаллическом состоянии и поэтому они более реакционноспособны. Например, аморфный оксид кремния при атмосферном давлении и комнатной температуре химически взаимодействует с известью. Для протекания активной химической реакции между кристаллическим кварцем и известью требуются автоклавные условия.
Минералогический состав является важной характеристикой природных и искусственных каменных материалов. Практика показывает, что материалы, имеющие один и тот же химический состав, но отличающиеся минералогическим составом, могут значительно отличаться и своими свойствами.
Для изучения минералогического состава каменных материалов в
настоящее время используют методы физико-химического анализа.
26
Методы микроскопического анализа позволяют непосредственно наблюдать конфигурацию и свойства кристаллов. Естественные грани
кристаллов очень |
помогают при идентификации минералов: для |
любого минерала |
характерными являются постоянство углов между |
гранями и определенная степень упорядоченности в расположении граней и ребер кристаллов - симметрия. Для идентификации минералов
применяют также методы |
рентгеновской |
дифрактометрии |
и |
|
инфракрасной спектроскопии. Дифференциально-термический |
и |
|||
дифференциально-термогравиметрический |
методы |
анализа |
||
применяются для идентификации |
отдельных минералов в сложных |
|||
смесях. |
|
|
|
|
2.МИНЕРАЛЬНЫЕ ВЯЖУЩИЕ ВЕЩЕСТВА
2.1. Общие сведения
Около трех тыс. лет тому назад в строительстве стали применять вяжущие вещества для связывания отдельных камней. В современном строительстве применяют минеральные и органические вяжущие
вещества. Минеральными |
вяжущими |
материалами |
называют |
порошкообразные вещества, |
которые при |
смешивании |
с водой |
образуют пластичную массу, со временем затвердевающую в прочное камневидное тело. Органические вяжущие материалы представляют собой высокомолекулярные соединения, как правило, не смачивающиеся водой. В рабочее, пластичное состояние они приводятся нагревом или растворением в органических растворителях.
По способности твердеть и сохранять свою прочность в воде или на воздухе минеральные вяжущие вещества делят на воздушные и гидравлические. Воздушные минеральные вяжущие затвердевают, сохраняют и повышают свою прочность только на воздухе. Гидравлические вяжущие обладают такой способностью не только на воздухе, но и в воде. К группе воздушных вяжущих веществ
2.2.Воздушные вяжущие вещества
2.2.1.Основы технологии гипсовых вяжущих веществ
Сырьем |
для производства гипсовых вяжущих является природный |
|
двуводный |
гипс CaSO42H2O |
и природный ангидрит CaSO4. |
27
Технологическая схема производства гипсовых вяжущих состоит в измельчении сырья и последующей тепловой обработке. Двуводный гипс при нагреве дегидратируется. Регулируя температуру и другие условия производства получают различные гипсовые вяжущие. Свойства гипсовых вяжущих регламентированы в государственном стандарте ГОСТ-125-79**.
Термическрой обработкой сырья при температуре 140…180 °С производят низкообжиговые гипсовые вяжущие – строительный гипс и высокопрочный гипс:
CaSO42H2O= CaSO4 0,5 H2O + 1,5H2O. Строительный гипс получают варкой гипсового камня в варочных
котлах или сушильных барабанах. При варке в варочных котлах сырье предварительно сушат и измельчают в порошок. В сушильных барабанах обжигают куски, а тонкому измельчению подвергают полугидрат. Используются и комбинированные схемы, когда операции сушки, помола и варки сырья совмещены. При варке гипса в открытых аппаратах при атмосферном давлении кристаллизационная вода удаляется в виде перегретого пара. При этом происходит сильное механическое диспергирование зерен с образованием кристаллов полуводного гипса -модификации, которыми и представлено
строение строительного гипса. В сравнении с другими гипсовыми вяжущими строительный гипс отличается наиболее высокой водопотребностью (нормальна густота составляет 50…55 %), пониженной прочностью (2…10 МПа) и низкой водостойкостью. Он быстро схватывается и твердеет.
Высокопрочный гипс изготавливают дегидратацией сырья либо в автоклавах в среде насыщенного пара при температуре 120…140 °С под давлением 0,13…0,15 МПа с последующей сушкой полуводного гипса, либо методом кипячения сырья при атмосферном давлении в водных растворах солей СаСl2, MgCl2, NaCl2, Na2CO3. Полученный таким образом полуводный гипс отцеживается или отделяется от жидкой среды центрифугированием, сушится при 110°С, а затем при 70…80°С. После высушивания продукт размалывают в порошок с остатком на сите № 008, не превышающим 5…10 %. Высокопрочный гипс состоит из более крупных и компактных кристаллов - полугидрата, для которых характерна более низкая водопотребность в сравнении со строительным гипсом. В итоге твердение высокопрочного гипса приводит к образованию более прочного гипсового камня 15…17 МПа. Высокопрочный гипс быстро твердеет, что характерно для низкообжиговых вяжущих.
28
С физико-химической точки зрения твердение низкообжиговых гипсовых вяжущих происходит в результате растворения полуводного сульфата кальция, появления насыщенного раствора, в котором протекают реакции гидратации с образованием кристаллов двуводного сернокислого кальция:
CaSO4 0,5 H2O + 1,5H2O = CaSO42H2O.
Высокообжиговые гипсовые вяжущие – ангидритовый цемент и высокообжиговый гипс получают обжигом дробленого гипсового камня или ангидрита при более высоких температурах (600…1000 °С) с последующим размолом продукта обжига. Ангидритовый цемент получают тонким помолом природного ангидрита или обжигом двуводного гипса при 600…700°С до полной дегидратации: в шахтных или вращающихся печах:
CaSO42H2O = CaSO4 + 2 H2O.
Безводный сернокислый кальций с водой практически не реагирует. Химическая реакция между ангидритом и водой активизируется катализаторами: Na2SO4, NaHSO4, K2SO4, FeSO4. процесс твердения ангидритового цемента протекает медленно в сравнении с низкообжиговыми гипсовыми вяжущими и может быть представлен в виде:
CaSO4+ активизатрор +nН2О→Активизатор СаSO4nH2O→
активизатор + (n-2)Н2О + CaSO42H2O.
Для получения гипсового теста нормальной густоты расходуется 30…35 % воды. Начало схватывания наступает не ранее 30 мин конец –
на позднее 24 ч с момента затворения водой. |
|
Высокообжиговый гипс – эстрих-гипс |
получают, обжигом |
гипсового камня при 800…1000°С с последующим тонким помолом. Высокообжиговый гипс состоит из ангидрита CaSO4 и 3..5 % СаО, который формируется вследствие частичной диссоциации CaSO4. СаО выполняет роль катализатора. Схватывание и твердение эстрих-гипса
при затворении |
водой протекает аналогично гипсоангидритовому |
||
цементу. В |
этом |
случае активизатором |
является СаО, всегда |
присутствующая в |
эстрих-гипсе. При твердении высокообжигового |
||
эстрих-гипса |
с водой оксид кальция, переходя в гидроксид, образует |
щелочную среду, способствующую ускорению процесса твердения:
CaSO4+ 2Н2О= CaSO42Н2О.
Водопотребность эстрих-гипса для получения теста нормальной густоты составляет 30…35%. Начало схватывания наступает через 6…8
29
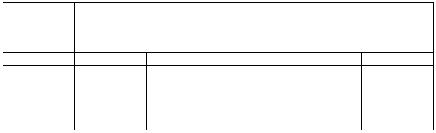
часов с момента затворения водой. Изделия из эстрих-гипса отличаются сравнительно высокой водостойкостью и плотностью. Через 28 суток
образцы имеют прочность |
при |
сжатии |
10…20 МПа и |
высокое |
сопротивление истиранию. |
|
|
|
|
По срокам схватывания |
ГОСТ |
125-79 |
регламентирует |
выпуск |
гипсовых вяжущих: А – быстротвердеющих (начало схватывания не ранее 2 мин, конец – не позднее 15 мин), Б – нормально твердеющих (начало схватывания – не ранее 6 мин, конец – не позднее 30 мин) и В – медленно твердеющих ) начало схватывания – не ранее 20 мин, конец – не нормируется). В зависимости от степени помола, контролируемой остатком на сите №02, различают вяжущие:I – грубого помола (не более 23%); II – среднего помола ( не более 14 %); III – тонкого помола (не более 2 %). Марка гипса назначается по пределу прочности при сжатии и изгибе образцов-балочек размерами 40х40х160 мм, изготовленных методом литья из гипсового теста нормальной густоты в возрасте 2 ч.
|
Маркировка гипсовых вяжущих веществ |
Таблица 2.1 |
|||
|
|
||||
Марка |
Предел прочности МПа |
Марка |
Предел прочности МПа |
||
вяжущего |
|
при: |
вяжущего |
|
при: |
|
сжатии |
изгибе |
|
сжатии |
изгибе |
Г-2 |
2 |
1,2 |
Г-10 |
10 |
4,5 |
Г-3 |
3 |
1,8 |
Г-13 |
13 |
5,5 |
Г-4 |
4 |
2,0 |
Г-16 |
16 |
6,0 |
Г-5 |
5 |
2,5 |
Г-19 |
19 |
6,5 |
Г-6 |
6 |
3,0 |
Г-22 |
22 |
7,0 |
Г-7 |
7 |
3,5 |
Г-25 |
25 |
8,0 |
Для строительных изделий и декоративных деталей рекомендуется применять гипс марок Г-2…Г-7 всех сроков твердения и степеней помола. Для производства штукатурных работ, затирки швов и для специальных целей применяют гипс марок Г-2…Г-25 нормального и медленного твердения, среднего и тонкого помола.
Вяжущие высшей категории для строительных изделий должны иметь прочность не ниже Г-5, максимальный остаток на сите №02 не более 12 %.
2.2.2. Основы технологии гипсовых и гипсобетонных изделий
Гипсовые вяжущие применяют при производстве гипсовой штукатурки, перегородочных стеновых плит (гипсолит) и панелей,
30