
- •Вид економічної діяльності
- •Сільське господарство, мисливство
- •Раны и кровотечения.
- •Вывихи, растяжения связок.
- •Переломы, ушибы.
- •Повреждение головы и глаз.
- •Острые отравления.
- •Ожоги.
- •Обморожения.
- •Обмороки, солнечные и тепловые удары.
- •Электротравмы.
- •Проведение искусственного дыхания и непрямого массажа сердца.
- •Параметры безопасности в доменном производстве
- •Меры безопасности при ведении доменного процесса
- •МАРТЕНОВСКОЕ ПРОИЗВОДСТВО
- •Основные нарушения параметров безопасности
- •Экстремальные отклонения мартеновского процесса
- •КОНВЕРТОРНОЕ ПРОИЗВОДСТВО
- •Требования безопасности к технологическому процессу
- •Параметры безопасности
- •Основные нарушения и экстремальные отклонения процесса
- •Нарушения процесса
- •Экстремальные отклонения процесса
- •ЭЛЕКТРОСТАЛЕПЛАВИЛЬНОЕ ПРОИЗВОДСТВО
- •Нарушения работы электрооборудования
- •Экстремальные отклонения
- •ПРОКАТНОЕ ПРОИЗВОДСТВО
- •Нарушения, экстремальные отклонения и меры безопасности
46
мероприятий, способствующих локализации взрыва при случайном возникновении его очага в аварийных ситуациях.
К числу мероприятий по предотвращению образования взрывоопасной концентрации относится сокращение операций процесса, связанных с пересыпкой металлических порошков. Операции пересыпки порошков проводят в изолированных, закрытых помещениях. Важной мерой снижения пожаровзрывоопасности ряда операций является предварительное смешивание порошков с инертными добавками. Так, помол силикокальция ведут совместно с бурой или силикатной глыбой, которые измельчаются предварительно, а затем подвергаются помолу совместно с силикокальцием.
Снижению взрывоопасности аэровзвесей способствует и применение легких мелкодисперсных негорючих материалов, например технической кальцинированной соды. При смешении компонентов экзотермических смесей в смеситель загружают сначала горючий порошок, затем все инертные компоненты, далее проводят предварительное смешивание, в последнюю очередь добавляют окислитель.
Для предотвращения загорания готовых экзотермических смесей от брызг металла и других воздействий смеси в разливочном пролете сталеплавильного цеха временно хранят в металлических контейнерах, полностью закрытых для доступа посторонних веществ и частиц металла. Наиболее эффективным способом снижения пожароопасности смесей является применение компонентов, обеспечивающих горение смесей лишь при повышенных температурах. Одним из таких компонентов является силикокальций, который обеспечивает высокую скорость шлакообразования при сгорании на поверхности металла при высоких температурах.
ПРОКАТНОЕ ПРОИЗВОДСТВО
Технологический процесс прокатки и факторы безопасности
Прокатное производство характеризуется сложностью и разнообразием механического оборудования, в связи с чем в производственном процессе в основном имеют место опасные физические факторы; физико-химические факторы являются основными только при нагреве металла перед прокаткой, огневой зачистке поверхности проката и термообработке, холодной прокатке и нанесении защитных покрытий.
В прокатном производстве для нагрева слитков и заготовок перед прокаткой и для термической обработки полупродукта и готовой продукции применяют различные типы нагревательных устройств. Крупные слитки перед прокаткой на блюминге или слябинге нагревают в рекуперативных нагревательных колодцах (рис. 64) с различным направлением пламени. При расположении горелки в центре подины пламя направлено вверх. Ударяясь о крышку колодца, оно растекается по ее поверхности, омывает слитки сверху вниз, после чего дымовые газы уходят через каналы в
47
нижней части двух боковых стен. Такое расположение пламени при недостатке воздуха на горение топлива может привести к образованию взрывоопасных газовоздушных смесей и их взрыву при открывании крышки колодца.
Вновой конструкции нагревательных колодцев горелка расположена в верхней части камеры, вследствие чего направление движения пламени и отходящих газов совсем иное: пламя выходит из горелки в верхней части, омывает слитки, ударяясь о противоположную стенку камеры, изменяет направление и продукты сгорания удаляются внизу также с одной стороны. Поэтому в случае недостатка воздуха для горения газа остатки топлива уйдут в борова и будут выброшены через трубу в атмосферу, но уже в охлажденном виде. Таким образом исключается возможность взрыва газов непосредственно в рабочей камере нагревательного колодца.
Значительно повышают безопасность процесса нагрева слитков системы автоматизации работы нагревательных колодцев, которые регулируют температуру в колодцах и рекуператорах, необходимое соотношение объемов топлива и воздуха, давление газов в камере, отключение газа при открывании крышек колодца и переключение газовых и воздушных клапанов.
Вмногозонных методических печах, применяемых для нагрева заготовок, направление потока пламени и продуктов сгорания противоположно направлению движения металла. При недостатке воздуха для горения топлива возникает подсос воздуха через окно и загрузочное отверстие, в случае избыточного давления в печи происходит сгорание газа вне рабочего пространства и выбивание пламени из-под крышек окон. Конструктивные особенности нагревательных печей исключают вероятность взрыва газа в рабочем пространстве печи.
Определенную опасность представляет операция удаления шлака из нагревательных колодцев. С технологической точки зрения жидкое шлакоудаление является более предпочтительным, однако оно не обеспечивает полной безопасности этого процесса, так как при этом возможны экстремальные отклонения, обусловленные наличием расплавленного металла или шлака.
Таким образом, опасными факторами процесса нагрева слитков и заготовок являются выбивание пламени из-под крышек нагревательных устройств, особенно при перекидке клапанов регенеративных колодцев, выплески расплавленного шлака и взрывы при контакте расплавленного шлака с водой или влажным материалом.
Подача исходных материалов от нагревательных устройств к прокатным станам является в основном безопасной операцией.
Однако при транспортировке слитков с незастывшей сердцевиной слитковозами к приемному рольгангу блюминга или слябинга возможны выплески жидкого металла. Степень опасности производственного процесса при горячей прокатке металла значительно выше, чем при холодной, что объясняется высокой температурой прокатываемого металла Основными опасными факторами при холодной прокатке являются нарушения
режима прокатки, вызываемые разрушением обрабатываемого металла, поломками или неисправностью соединительных устройств, валков, нажимных механизмов,
48
направляющих проводок и др. При горячей прокатке дополнительными факторами являются температурный режим нагрева прокатываемого металла, режим прокатки, скорость его охлаждения при деформации и т д.
При резке металла на ножницах горячей и холодной резки опасными являются локальные зоны движущихся и вращающихся частей механизма В случае резки металла дисковыми пилами площадь опасной зоны резко возрастает.
Значительно повышает фактор опасности производственного процесса использование в потоке машин огневой зачистки металла, вместе с тем этот процесс оказывает большое влияние на улучшение условий труда, способствуя ликвидации опасных и вредных факторов на других стадиях процесса. При огневой зачистке металла возможен взрыв газов.
Остальные технологические операции (охлаждение, клеймение, складирование металла) особого влияния на уровень безопасности производственного процесса не оказывают, за исключением термической обработки.
Нарушения, экстремальные отклонения и меры безопасности
Нагревательные устройства
Использование в качестве топлива доменного, коксового и природного газов в нагревательных устройствах прокатных цехов сопряжено с опасностью образования взрывоопасных смесей и их воспламенения. Источниками воспламенения взрывчатой смеси в прокатном цехе являются открытое пламя, электрическая искра, нагретый металл и т .д. Взрывчатая смесь газов с воздухом обычно образуется при сравнительно низкой температуре. В прокатных цехах газ с горячим воздухом соприкасается лишь в горелочных устройствах нагревательных печей и колодцев, в остальных случаях газ и воздух могут смешиваться в холодном состоянии и поэтому всякое попадание воздуха в газ или газа в закрытое пространство с воздухом может привести к образованию взрывоопасной смеси
Наиболее часто наблюдаются взрывы в боровах нагревательных колодцев Если температура в борове выше 500° С (температура воспламенения газа), взрывчатая смесь не образуется, так как при этой температуре газ, смешиваясь с остатками воздуха, сгорает При температуре ниже 500° С и наличии в боровах воздуха образуется взрывчатая смесь, которая при дальнейшем поступлении в насадку регенератора взрывается При одновременной перекидке газовых и воздушных клапанов эта смесь может взорваться в сборном дымовом борове.
Взрывы в регенеративных колодцах при перекидке клапанов I предотвращают устранением подсосов воздуха в регенераторы В борова. Не допускается одновременный перевод газового и воздушного клапанов.
Воздушный клапан включают на 10—15 с позднее газового. Сушку и разогрев нагревательных колодцев проводят до тех пор, пока температура в газовых боровах и насадках не поднимается до температуры воспламенения газа, при этом газ, попав в боров, сразу же загружается, не успев образовать гремучею смесь.
49
Нарушением параметров безопасности в нагревательных устройствах является выбивание пламени и газов из-под крышек нагревательных колодцев и печей. Для предупрежения выбивания пламени и газов необходимо обеспечивать установленный режим горения топлива в рабочем пространстве, а также плотное прилегание крышки к стенкам печи. При сильном выбивании из окон печей пламени и газов дутье и тягу регулируют так, чтобы давление в рабочем пространстве печи на уровне пода при максимальной производительности не превышало 33 Па Для герметичности крышки люков газовых перекидных клапанов уплотняют
просмоленным асбестом. Борова уплотняют газонепроницаемой массой и засыпают просмоленной мелкой рудой и глиной с песком.
При применении рекуперативных нагревательных колодцев и методических печей вероятность взрыва газо-воздушных смесей меньше.
При посадке слитков в камеры колодцев и выдаче их существует опасность падения слитков на рабочую площадку или железнодорожные пути, что может привести к аварии. Для предотвращения падения слитков сменные керны клещей крана изготовляют из жаропрочной износостойкой стали или наплавляют их твердыми сплавами и периодически заменяют.
Для горения газа воздух в нагревательные колодцы и печи подают вентиляторами под давлением через инжекционные горелки. Во избежание взрывов газа в воздухопроводах и вентиляторах в случае внезапной остановки вентиляторов принимаются следующие меры. В случае необходимости отключения воздуха на подводах дутья в каждой горелке устанавливают задвижки, а на разводящем коллекторе—общую быстродействующую задвижку.
На воздуховодах перед каждой печью устанавливают автоматически действующие клапаны или другие приспособления для автоматической отсечки газа. На концах воздуховодов каждой нагревательной печи устанавливают свечи, выведенные наружу здания, через которые продувают воздухопровод после остановки вентилятора.
Подавать газ и дутье в горелки можно после того, как вентилятор начнет работать с полным числом оборотов. При применении горелок с предварительным смешиванием газа и воздуха в соотношениях, вызывающих опасность взрывов, смесь должна иметь избыток газа, а недостающий для горения воздух добавляется непосредственно в горелки печи. При этом обеспечивается непрерывность действия смесителей.
Для предупреждения взрыва в случае остановки смесителей подвод газовоздушной смеси оборудуют автоматически действующими обратными клапанами непосредственно после горелок. Предупреждение обратного удара пламени в горелках с предварительным смешиванием газа и воздуха, а также в инжекционных горелках достигается тем, что скорость выхода горючей смеси превышает скорость ее воспламенения.
50
Прокатные станы
При эксплуатации прокатных станов возможны следующие опасности: захват валками или вращающимися шпинделями и соединительными муфтами частей одежды и конечностей вальцовщика и механические повреждения отлетающими осколками прокатываемого металла и окалины Все соединительные шпиндели, муфты и коренные валы прокатных станов
ограждают с боков решетчатыми или сплошными щитами или кожухами, а на сортовых и проволочных станах муфты и коренные валы ограждают еще и сверху. На высокоскоростных станах, где возникает опасность разрыва соединительных муфт, предохранительные кожухи должны быть очень прочными, чтобы выдерживать удары кусков разорвавшихся муфт.
Соединительные шпиндели всех прокатных станов, кроме блюмингов и слябингов, обязательно ограждают. Шпиндели блюмингов и слябингов обычно ограждают прочным барьером и устраивают площадки с перилами для удобства обслуживания.
При отклонении параметров процесса прокатки от заданных, например неравномерном нагреве слитков и заготовок, неправильной калибровке или расточке валков, различной скорости вращения валков, возникает неравномерность деформации с различными проявлениями — искривление раската в горизонтальной и вертикальной плоскостях, разрушение металла и т д. Искривление концов раската может привести к возникновению ударов, поломке оборудования и травмированию персонала.
Устранение неправильного выхода раската из валков достигается соблюдением режима нагрева слитков и заготовок. Подавать для прокатки неравномерно нагретые заготовки недопустимо. Следует проводить тщательную настройку стана, устанавливать проводки и линейки в строго предусмотренном месте. Применять выводные проводки без боковых линеек недопустимо.
При выходе из последних клетей мелкосортных непрерывных и линейных станов раскат может отклониться от прямолинейного направления. Так как скорость прокатки в названных клетях достигает 60—70 м/с, такой раскат создает опасную ситуацию. Для ее устранения на отводящих рольгангах станов устанавливают борта надлежащей высоты, а рольганги ограждают высокими бортами.
На мелкосортных станах линейного типа прокатка с большой скоростью увеличивает опасность травмирования. В этом случае возможны нарушения процесса выходящий из валков металл сбивает проводки, трубки, линейки и ножи, застревает в валках и уходит в какую-либо сторону и вверх, заворачивается узлом или петлей. Поэтому рабочие места вальцовщиков для защиты от петли, создаваемой металлом между клетями, обязательно ограждают предохранительными стенками. Устья приемных желобов перекрывают так чтобы исключить возможность выброса прокатываемого металла за борт желоба.
На крупно- и среднесортных станах линейного типа для предотвращения выхода раската в сторону прокатное поле ограждается прочными сплошными
51
бортами с наклоном в сторону раската. При наличии длинных раскатов или петель и при отсутствии у станов достаточных площадей устраивают подвесные желоба или подземные карманы с уширением устья, а в необходимых случаях с установкой роликов.
Для обеспечения условий безопасности в процессе прокатки должна быть исправной валковая арматура (направляющие коробки с пропусками, выводные проводки, брусья, проводковые столы, линейки и др.), предназначенные для правильной подачи раската в валки и его выхода из валков. Валковая арматура является одним из важных средств безопасности, так как предупреждает возможность возникновения различных отклонений при прокатке — попадания раската на бурты валков, свертывания, искривления и неправильного движения раската при выходе из валков.
Прокатка на блюминге, слябинге, толстолистовых станах сопровождается выбросами частиц окалины с большой скоростью, осколков металла и брызг шлака. Отлетающие частицы разрушают остекление постов управления и могут травмировать операторов-вальцовщиков и находящийся у станов персонал.
Для удаления окалины с поверхности раската на подводящем рольганге устанавливают устройства гидравлического или механического действия с надежной защитой от отлетающей окалины.
Для защиты от отлетающих при прокатке частиц окалины, осколков металла и брызг шлака перед валками на станине устанавливают экраны — прочные сетчатые щиты или густые цепные завесы. С этой же целью вдоль линии стана, против проема в станине рабочих рольгангов устанавливают съемные щиты из густой, прочной сетки Промежуток между валками со стороны, противоположной соединительным шпинделям, закрывают предохранительным щитом Поломка валков, нажимных устройств и предохранительных стаканов блюминга
связана с возникновением больших усилий, превышающих допустимые, для предупреждения этих поломок необходимо строго соблюдать режим обжатий.
Для безопасного перехода через рольганги, транспортеры, конвейеры оборудуют переходные мостики, настил которых футеруют огнеупорным кирпичом для защиты от тепловых воздействий.
При холодной прокатке листовой стали возможны обрывы полосы как на заправочной, так и на рабочей скорости стана. Отлетающие куски листовой стали имеют высокую скорость разлета и могут поразить персонал стана. Для предупреждения обрыва полос при холодной прокатке следует повышать качество и пластические свойства катаной листовой стали, применяемой в качестве подката.
Для удаления паров технологической смазки в межклетевых промежутках и за последней клетью устанавливают вытяжные зонты.
ТЕМА 7. ОБЕСПЕЧЕНИЕ БЕЗОПАСНОЙ ЭКСПЛУАТАЦИИ ОБОРУДОВАНИЯ В ЧЕРНОЙ МЕТАЛЛУРГИИ И ТЕПЛОЭНЕРГЕТИКЕ
Безопасность эксплуатации систем под давлением и криогенной техники
К сосудам и аппаратам, работающим под давлением, относят баллоны, цистерны и бочки, компрессорные установки и воздухосборники при них, паровые и водогрейные котлы, трубопроводы (пара, горячей воды, газа и др. сред). При этом необходимо учитывать, что паровые и водогрейные котлы также относятся к аппаратам, работающим при высокой температуре и большом избыточном давлении.
Все сосуды (котлы и т. д.) до пуска в работу регистрируются в органах котлонадзора. Проходят техническое освидетельствование до пуска в работу и периодически в процессе работы в соответствии с технической документацией на сосуд.
Виды испытаний при техническом освидетельствовании:
•осмотр (внешний и внутренний);
•гидравлическое испытание.
Для обеспечения безопасной эксплуатации сосудов администрация предприятия назначает и обучает ответственных лиц по надзору за техническим состоянием и эксплуатацией сосудов и операторов, обслуживающих это оборудование.
Работы по ремонту, осмотру и техническому обслуживанию сосудов производятся с оформлением наряда-допуска.
Общие требования безопасности к котлам.
Проектирование, изготовление, реконструкция, наладка, ремонт и эксплуатация котлов должна производиться в соответствии с ДНАОП 0.00- 1.08-94 «Правила устройства и безопасной эксплуатации паровых и водогрейных котлов», ДНАОП 0.00-1.07-96 «Инструкция о порядке выдачи разрешения на изготовление, ремонт и реконструкцию объектов котлонадзора и осуществление надзора за выполнением этих работ» и ДНАОП 0.00-1.07-96 «Типовая инструкция для операторов (машинистов) паровых и водогрейных котлов».
Паровые и водогрейные котлы относятся к аппаратам , работающим при высокой температуре и большом избыточном давлении. Причинами взрыва этих котлов являются либо перегрев стенок котла (вследствие упуска воды), либо недостаточное охлаждение внутренних стенок из-за накопления накипи. Причиной взрыва также может быть внезапное разрушение стенок котла от появившихся на них трещин или усталостных образований (при превышении давления внутри котла против расчетного значения из-за неисправности предохранительных устройств). Очень часто причиной взрыва может быть образование взрывоопасных смесей в топочном пространстве котла и в газоходах.
Настоящие Правила устанавливают требования к устройству, изготовлению, монтажу, ремонту и эксплуатации паровых котлов, автономных пароперегревателей и экономайзеров с рабочим давлением не
более 0,07 МПа, водогрейных котлов и автономных экономайзеров с температурой воды выше 115°С.
Настоящие Правила распространяются на:
•паровые котлы, в том числе котлы-бойлеры, а также автономные пароперегреватели и экономайзеры;
•водогрейные и паро-водогрейные котлы;
•энерготехнологические котлы: паровые и водогрейные;
•котлы-утилизаторы: паровые и водогрейные;
•котлы передвижных и транспортабельных установок и энергопоездов;
•котлы паровые и жидкостные, работающие с высокотемпературными органическими теплоносителями (ВОТ);
•трубопроводы пара и горячей воды в пределах котла.
Соответствие котлов требованиям правил должно быть подтверждено изготовителем (поставщиком) оборудования сертификатом соответствия, выданным сертификационным центром Украины. Копия сертификата соответствия должна прилагаться к паспорту котла. Паспорт котла должен быть на украинском или, по требованию заказчика, на другом языке.
Проекты котлов, а также проекты их монтажа или реконструкции должны выполняться специализированными проектно-конструкторскими организациями, имеющими разрешение органов Госнадзорохрантруда.
Изменения проекта, необходимость в котором возникает в процессе изготовления, монтажа, эксплуатации, при ремонте, модернизации или реконструкции, должно быть согласовано с автором проекта, а для котлов, приобретённых за границей, с головной организацией по котлостроению.
Конструкция котлов и его основных частей должна обеспечивать надёжность, долговечность и безопасность эксплуатации на расчётных параметрах в течение расчётного ресурса безопасной работы котла (элемента), принятого в технических условиях, а также возможность технического освидетельствования, очистки, промывки, ремонта и эксплуатационного контроля металла.
Конструкция и гидравлическая схема котла, пароперегревателя и экономайзера должны обеспечивать надёжное охлаждение стенок элементов, находящихся под давлением. Температура стенок элементов котла, пароперегревателя и экономайзера не должна превышать значения, принятого в расчётах на прочность.
Участки элементов котлов и трубопроводов с повышенной температурой поверхности, доступные для обслуживающего персонала, должны быть покрыты тепловой изоляцией, обеспечивающей температуру наружной поверхности не более 55°С при температуре окружающей среды не более 25°С.
Устройство газоходов должно исключать возможность образования взрывоопасного скопления газов, а также должно обеспечивать условия, необходимые для очистки газоходов от отложений продуктов сгорания.
Нижний допустимый уровень воды в газотрубных (жаротрубных)
котлах должен быть не менее чем на 100 мм выше верхней точки поверхности нагрева котла.
Каждый котёл с камерным сжиганием топлива (пылевидного, газообразного, жидкого) или с шахтной топкой для сжигания торфа, опилок, стружек и других мелких производственных отходов должны быть снабжены предохранительными устройствами. Эти устройства следует устанавливать в стенке топки, последнего газохода котла, экономайзера и золоуловителя. Взрывные предохранительные устройства должны быть размещены и устроены так, чтобы было исключено травмирования людей. Количество, размещение и размеры проходного сечения взрывных предохранительных устройств определяется проектом котла.
Сварные швы должны быть с полным проплавлением и, как правило, стыковыми. Применение угловых сварных угловых соединений допускается при условии сплошного контроля УЗК или радиографией.
Каждый котёл должен иметь трубопроводы: подвода питательной или сетевой воды; продувки котла и спуска воды при остановке котла; удаления воздуха из котла при заполнении его водой и растопке; продувки пароперегревателя и паропровода; отбора проб воды и пара; ввода в
котловую воду корректирующих реагентов в период эксплуатации и моющих реагентов при химической счистке котла; отвода воды или пара при растопке или остановке; разогрева барабанов при растопке.
Изготовление, монтаж и ремонт котлов и их элементов должны выполнятся специализированными предприятиями или организациями, имеющими разрешение органов Госнадзорохрантруда Украины. Изготовление, монтаж и ремонт котлов и их элементов должны выполняться в полном соответствии с требованиями Правил и государственных стандартов.
Изготовление, монтаж и ремонт котлов и их элементов должны производиться по технологии, разработанной до начала работ организацией, выполняющей соответствующие работы.
К производству сварочных работ могут быть допущены лишь сварщики, аттестованные в соответствии с Правилами аттестации сварщиков и имеющие удостоверение для производства этих работ. Сварщики могут быть допущены только к сварочным работам тех видов, которые указаны в их удостоверении.
Контроль качества сварки и сварных соединений включает:
•проверку аттестации персонала;
•проверку сборочно-сварочного оборудования, приборов и инструмента;
•контроль качества основных материалов;
•контроль качества сварочных материалов и материалов для дефектоскопии;
•операционный контроль технологии сварки;
•неразрушающий контроль сварки;
•разрушающий контроль сварки;
• контроль исправления дефектов.
Виды неразрушающего контроля: внешний осмотр и измерения; радиографический контроль; рентгенно-телевизионный контроль; ультразвуковой (УЗК) контроль; капиллярный или магнитопорошковый; стилоскопирование (для аустенитных сталей) для определения легирующих элементов; измерение твёрдости ( после термообработки шва); прогонка металлического шара; гидравлическое испытание.
Гидравлическому испытанию с целью проверки плотности и прочности всех элементов котла, пароперегревателя и экономайзера, а также всех сварных и других соединений подлежат все котлы и их элементы после изготовления или после монтажа.
Минимальное значение пробного давления Ро при гидростатическом испытании котлов, пароперегревателей и экономайзеров, а также трубопроводов в пределах котла принимается:
а) при рабочем давлении Рраб не более 0,5 МПа Po =1,5 Pраб , но не менее 0,2 МПа;
б) при рабочем давлении Рраб более 0,5 МПа
Po =1,25 Pраб , но не менее Рраб +0,3, МПа.
При проведении гидравлического испытания барабанных котлов, а также их пароперегревателей и экономайзеров за рабочее давление принимается давление в барабане котла, а для котлов с принудительной циркуляцией без барабанных и прямоточных – давление питающей воды на входе в котёл, установленное конструкторской документацией.
Гидравлическое испытание должно производится водой с температурой не ниже 5°С и не выше 40°С. Время выдержки под пробным давлением должно быть не менее 10 мин.
После выдержки под пробным давлением давление снижают до рабочего, при котором производят осмотр всех сварных и других соединений. Давление воды при испытании должно контролироваться двумя манометрами, из которых один должен иметь класс точности не ниже 1,5.
Использование сжатого воздуха или газа для подъёма давления не допускается.
Объект считается выдержавшим испытание, если не будет обнаружено видимых остаточных деформаций, трещин или признаков разрыва, течи в соединениях и в основном металле.
Каждый котёл, автономный пароперегреватель и экономайзер должны поставляться заказчику с паспортом установленной формы. К паспорту должна быть приложена инструкция по монтажу и эксплуатации, содержащая требования к ремонту и контролю металла при монтаже и эксплуатации в период расчётного срока службы. Инструкция должна быть составлена на украинском языке или языке по требованию заказчика.
На каждом котле, автономном пароперегревателе и экономайзере должна быть прикреплена заводская табличка с маркировкой паспортных данных.
На табличке, например, парового котла должны быть нанесены следующие данные: наименование, товарный знак предприятия - изготовителя; обозначение котла по ГОСТ 3619-89; номер котла; год изготовления; номинальная производительность по пару, т/ч; рабочее давление на выходе, МПа; номинальная температура пара на выходе, °С.
Для управления работой, обеспечения безопасных условий и расчётных режимов эксплуатации котлы должны быть оснащены: устройствами, предохраняющими от повышения давления (предохранительными устройствами); указателями уровня воды; манометрами; приборами для измерения температуры среды; запорной и регулирующей арматурой; приборами безопасности; питательными устройствами. В качестве предохранительных устройств допускается применять: рычажно-грузовые предохранительные клапаны прямого действия; пружинные предохранительные клапаны прямого действия; импульсные предохранительные устройства.
На каждом паровом и водогрейном котле должно быть установлено не менее двух предохранительных устройств. На каждом паровом котле, за исключением прямоточных, должно быть установлено не менее двух указателей уровня воды прямого действия, а также манометр, показывающий давление пара. Манометр должен быть установлен на барабане котла, а при наличии у котла пароперегревателя - и за пароперегревателем, до главной задвижки. На прямоточных котлах манометр должен быть установлен за пароперегревателем, перед запорным органом. На котлах должны быть установлены автоматически действующие звуковые сигнализаторы верхнего и нижнего предельных положений уровней воды.
Паровое и водогрейное котлы при камерном сжигании топлива должны быть оборудованы автоматическими устройствами для прекращения подачи топлива в топку в следующих случаях: при погасании факела в топке; при отключении всех дымососов или прекращении тяги; при отключении всех дутьевых вентиляторов.
Стационарные котлы устанавливаются только в зданиях и помещениях, отвечающие требованиям СНиП 11-35-76 "Котельные установки". Установка котлов вне помещения допускается в том случае, если котёл спроектирован для работы в заданных климатических условиях. Устройство помещений и чердачных перекрытий над котлами не допускается (кроме котлов, установленных в производственных помещениях ). Устройство приямков в котельных не допускается. Выходные двери из котельного помещения должны открываться наружу.
Руководство предприятия должно обеспечить содержание котлов в исправном состоянии и безопасные условия их эксплуатации.
В этих целях администрация обязана:
• назначить ответственного за исправное состоянии и безопасную эксплуатацию котлов из числа ИТР, прошедших проверку знаний в установленном порядке;
• обеспечить ИТР правилами и инструкциями по безопасной эксплуатации
котлов;
•назначить необходимое количество лиц обслуживающего персонала, обученного и имеющего удостоверения;
•разработать и утвердить производственную инструкцию для персонала, обслуживающего котлы. Инструкция должна находиться на рабочем месте
ивыдаваться под расписку;
•установить объём и периодичность проверки знаний;
•организовать контроль за состоянием металла элементов котла;
•обеспечить выполнение ИТР правил, а обслуживающим персоналом - инструкций по безопасной эксплуатации котлов;
•обеспечить проведение технических освидетельствований котлов в установленные сроки;
•проводить периодически, не реже одного раза в год, обследование котлов с последующим уведомлением инспектора котлонадзора.
Кобслуживанию котлов могут быть допущены лица не моложе 18 лет, прошедшие медицинское обследование, обучение, аттестованные и имеющие удостоверение на право обслуживания котлов. Обучение и аттестация машинистов котельной, операторов котельной и водосмотров проводится по разрешению органов Госнадзорохрантруда. Индивидуальная подготовка персонала не допускается. Аттестация проводится с участием инспектора котлонадзора. Периодическая проверка знаний персонала, обслуживающего котлы, должна проводиться не реже одного раза в год.
Внеочередная проверка знаний проводится: при переходе на другое предприятие; в случае перевода на обслуживание котлов другого типа; при переводе котла на сжигание другого вида топлива; по решению администрации или по требованию инспектора Госнадзорохрантруда.
Котлы до пуска в работу должны быть зарегистрированы в органах Госнадзорохрантруда. Регистрация проводится на основании письменного заявления владельца котла с предоставлением необходимых документов. При передаче котла другому владельцу до пуска котла в работу он подлежит перерегистрации.
Каждый котёл до пуска в работу, периодически в процессе эксплуатации и в необходимых случаях подвергается техническому освидетельствованию. Техническое освидетельствование состоит из наружного, внутреннего осмотров и гидравлического испытания. Наружный
ивнутренний осмотр проводится не реже одного раза в 4 года, а гидравлическое испытание - не реже одного раза в 8 лет. Его проводит эксперт, имеющий разрешение органов Госнадзорохрантруда. Результаты испытания заносятся в паспорт котла лицом, производящим освидетельствование.
Владелец котла обязан самостоятельно проводить внешний и внутренний осмотр после каждой очистки внутренних поверхностей или ремонта элемента котла, после раскрытия барабана, коллектора, но не реже чем через 12 месяцев, а также перед предъявлением котла инспектору.
Внеочередное освидетельствование котлов должно быть проведено в следующих случаях: если котёл находился в бездействии более 12 месяцев; если котёл был демонтирован и установлен на новом месте; после ремонта котла с применением сварки или пайки; после достижения расчётного срока службы котла (для энергетических котлов этот срок службы равен 30 лет, а для остальных котлов – 20 лет); после аварии котла или его элементов; после решения инспектора Госнадзорохрантруда проводить внеочередное освидетельствование, а перед ним - техническое диагностирование, т. е. определение ресурса работоспособности котла (стоимость диагностики до 25% стоимости нового котла).
Приёмка в эксплуатацию вновь установленного котла должна осуществляться после его регистрации в органах Госнадзорохрантруда и технического освидетельствования. Пуск котла в работу производится по письменному распоряжению администрации предприятия после проверки готовности оборудования котельной установки к эксплуатации и организации его обслуживания.
На каждом котле, введенном в эксплуатацию, должна быть на видном месте прикреплена табличка с указанием следующих данных: регистрационный номер; разрешенное давление;
Общие требования безопасности к сосудам, работающим под давлением.
Проектирование, изготовление, реконструкция, наладка, ремонт и эксплуатация сосудов должна производиться в соответствии с ДНАОП 0.00- 1.07-94 «Правила устройства и безопасной эксплуатации сосудов, работающих под давлением» и ДНАОП 0.00-1.07-94 «Инструкция о порядке выдачи разрешения на изготовление, ремонт и реконструкцию объектов котлонадзора и осуществление надзора за выполнением этих работ».
Сосуд, работающий под давлением, – это герметически закрытая ёмкость, предназначенная для ведения химических, тепловых и других технологических процессов, а также для хранения и транспортирования газообразных, жидких и других веществ. Границей сосуда являются входные и выходные штуцера.
Данные правила устройства и безопасной эксплуатации сосудов, работающих под давлением, распространяются на:
•сосуды, работающие под давлением воды с температурой выше 115оС или другой жидкости с температурой, превышающей температуру кипения при давлении 0,07 МПа без учета гидростатического давления;
•сосуды, работающие под давлением пара или газа свыше 0,07 МПа;
•баллоны, предназначенные для транспортирования и хранения сжатых, сжиженных и растворённых газов под давлением свыше
0,07 МПа;
•цистерны и бочки для транспортирования сжиженных газов, давление паров которых при температуре до 50оС превышает 0,07
МПа;
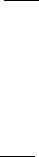
•цистерны и сосуды для транспортирования или хранения сжатых, сжиженных газов, жидкостей и сыпучих тел, в которых давление свыше 0,07 МПа создается периодически для их опорожнения;
•барокамеры.
Сосуды под давлением (в том числе и баллоны) могут взрываться от ударов, падения, соударения между собой, перегрева, повышения внутреннего давления, нарушения работы вентилей, наполнения другим газом. Очень часто причиной взрыва могут быть нарушение правил эксплуатации, хранения и перевозки сосудов. Например, при совместном хранении сосудов, наполненных разными газами, в помещении может образоваться взрывоопасная среда от смеси газов, даже незначительно просасывающихся через вентили. При хранении маслосодержащих веществ и кислородных баллонов может произойти взрыв при взаимодействии масла и кислорода.
Конструкция сосудов должна обеспечивать работоспособность, надежность, долговечность и безопасность в течение расчетного срока службы и предусматривать возможность проведения технического освидетельствования, полного опорожнения, очистки, промывки, продувки, ремонта, эксплуатационного контроля металла и соединений.
Сосуды, работающие под давлением, изготавливают сварными или литыми на предприятиях, имеющих разрешение Госнадзорохрантруда. На корпусе сосуда на видном месте должна быть прикреплена заводомизготовителем металлическая пластинка с нанесением клеймением следующих паспортных данных: наименование завода-изготовителя; заводской номер сосуда; рабочее давление; пробное давление; допустимая температура стенок сосуда.
Требования к изготовлению, реконструкции, монтажу, наладке, ремонту и к проведению сварочных работ аналогичны требованиям к котлам.
После изготовления все сосуды подлежат испытанию пробным давлением. Гидравлическому испытанию подлежат все сосуды после их изготовления или монтажа.
Гидравлическое испытание сосудов, за исключением литых, должно проводиться пробным давлением (МПа)
Po =1,25 Pраб [[σσ]]20 ,
t
где Рраб – расчетное давление сосуда, МПа;
[σ]20 ,[σ]t – допустимые напряжения для материала сосуда или его
элементов при 20оС и расчетной температуре t , МПа.
Гидравлическое испытание литых сосудов проводиться пробным давлением
Po =1,5 Pраб [[σσ]]20 ,
t
Гидравлическое испытание криогенных сосудов при наличии вакуума в изоляционном пространстве должно проводиться пробным давлением (МПа)
Po =1,25 Pраб −0,1
При заполнении сосуда водой воздух должен быть удален полностью. Температура воды (или другой жидкости) должна быть от +5 до +40оС, если в технических условиях не указано конкретное значение температуры.
Время выдержки под пробным давлением должно быть:
• с толщиной стенки до 50 мм |
– 10 мин; |
|
• с толщиной стенки от 50 до 100 мм |
– 20 мин; |
|
• |
с толщиной стенки свыше 100 мм |
– 30 мин; |
• |
для литых, неметаллических и многослойных |
– 60 мин. |
После выдержки под пробным давлением давление снижают до расчетного, при котором производят осмотр наружной поверхности сосуда, всех его разъемных и сварных соединений. Гидравлическое испытание допускается заменять пневматическим при условии контроля этого испытания методом акустической эмиссии. Значения пробного давления и результаты испытаний заносятся в паспорт сосуда лицом, проводившим эти испытания.
На каждый сосуд изготовитель оформляет следующие документы: паспорт (на украинском языке или другом по требованию заказчика); инструкцию по монтажу и эксплуатации; копию сертификата соответствия сосуда нормативным требованиям.
Для управления работой и обеспечения нормальных условий эксплуатации сосуды должны быть снабжены приборами для измерения давления и температуры среды; предохранительными устройствами; запорной арматурой; указателями уровня жидкости.
Сосуды устанавливают на открытых площадках в местах, исключающих скопление людей, или в отдельно стоящих зданиях.
Допускается установка сосудов:
•в помещениях, примыкающих к производственным зданиям при условии отделения их от здания капитальной стеной;
•в производственных помещениях в случаях, предусмотренных отраслевыми Правилами безопасности;
•с заглублением в грунт при условии обеспечения доступа к арматуре и зашиты стенок сосуда от почвенной коррозии и коррозии блуждающими токами.
Не разрешается установка сосудов в жилых, общественных и бытовых зданиях, а также в примыкающих к ним помещениям.
Требования к регистрации сосудов, техническому освидетельствованию, пуску в работу, а также надзору, содержанию, обслуживанию и ремонту аналогичны требованиям к котлам. Отличие только в том, что администрация назначает приказом два лица: ответственного по надзору за техническим состоянием и эксплуатацией сосудов, и ответственного за исправное состояние и безопасное действие сосудов. Техническое освидетельствование сосудов, зарегистрированных в экспертнотехническом центре (ЭТЦ) Госнадзорохрантруда, проводит эксперт ЭТЦ и
лицо, ответственное за исправное состояние и безопасную эксплуатацию сосудов (наружный и внутренний осмотр – один раз в 4 года, гидравлическое испытание – один раз в 8 лет). Предприятия – владельцы сосудов должны проводить самостоятельно их внутренний осмотр не реже чем через 2 года, за исключением сосудов, работающих со средой, вызывающей коррозию металла, которые должны подвергаться осмотру не реже чем через год.
Сосуд должен быть аварийно остановлен в следующих случаях:
•если давление в сосуде поднялось выше разрешённого и не снижается, несмотря на меры, принятые персоналом;
•при выявлении неисправности предохранительных устройств;
•при обнаружении в сосуде и его элементах неплотностей, выпучин, разрывов прокладок;
•при неисправности манометра и невозможности определить давление по другим приборам;
•при снижении уровня жидкости ниже допустимого в сосудах с огневым обогревом;
•при неисправности всех указателей уровня жидкости;
•при неисправности предохранительных блокировочных устройств;
•при возникновении пожара, непосредственно угрожающего сосуду. Порядок аварийной остановки и последующего ввода его в работу
должен быть указан в инструкции. Причины аварийной остановки сосуда должны записываться в сменный журнал.
Дополнительные требования к баллонам.
Баллоны вместимостью более 100 л каждый должен быть снабжен паспортом, а менее 100 л – паспорт выдается на партию. Боковые штуцера для баллонов, наполняемых водородом и другими горючими газами, должны иметь левую резьбу, а для баллонов, наполняемых кислородом и другими негорючими газами, –правую резьбу. Каждый вентиль баллонов для взрывоопасных горючих и вредных веществ 1 2 классов опасности по ГОСТ 12.1.007-76 должен иметь заглушки, накручивающиеся на штуцер.
На каждом баллоне должны быть выбиты следующие данные:
•товарный знак предприятия-изготовителя;
•номер баллона;
•фактическая масса пустого баллона;
•дата (месяц, число) изготовления и следующего освидетельствования;
•рабочее давление, МПа;
•пробное гидравлическое давление, МПа;
•вместимость баллона, л;
•клеймо ОТК предприятия-изготовителя;
•номер стандарта для баллонов вместимостью свыше 55 л.
После изготовления наружная поверхность баллона окрашивается в соответствующий цвет. Окраска баллонов и нанесение надписей некоторых газов приведены в таблице 3.1.
Таблица 3.1 – Окраска и нанесение надписей на баллонах
Наименование |
Окраска |
Текст надписи |
Цвет надписи |
Цвет полосы |
|
газа |
баллона |
||||
|
|
|
|||
Азот |
Черная |
Азот |
Желтый |
Коричневый |
|
Аммиак |
Желтая |
Аммиак |
Черный |
– |
|
Ацетилен |
Белая |
Ацетилен |
Красный |
– |
|
Водород |
Темно- |
Водород |
Красный |
– |
|
зеленая |
|||||
|
|
|
|
||
Бутилен |
Красная |
Бутилен |
Желтый |
Черный |
|
Нефтегаз |
Серая |
Нефтегаз |
Красный |
– |
|
Воздух |
Черная |
Сжатый |
Белый |
– |
|
воздух |
|||||
|
|
|
|
||
Кислород |
Голубая |
Кислород |
Черный |
– |
|
Сероводород |
Белая |
Сероводород |
Красный |
Красный |
|
Углекислота |
Черная |
Углекислота |
Желтый |
– |
|
Этилен |
Фиолетовая |
Этилен |
Красный |
– |
|
Все другие |
Красная |
Наименование |
Белый |
– |
|
горючие газы |
газа |
||||
|
|
|
|||
Все другие |
|
Наименование |
Желтый |
– |
|
негорючие |
Черная |
||||
газа |
|||||
газы |
|
|
|
||
|
|
|
|
Освидетельствование баллонов производится на предприятияхизготовителях, предприятиях-наполнителях, наполнительных станциях и испытательных пунктах. Пробное давление и время выдержки для стандартных баллонов – по стандартам, для нестандартных баллонов – по техническим условиям, но при этом пробное давление должно быть не менее 1,5 рабочего давления. Баллоны на предприятии-изготовителе, за исключением баллонов для ацетилена, после гидравлического испытания должны также подвергаться пневматическому испытанию давлением, равным рабочему давлению. При пневматическом испытании баллоны должны быть погружены в ванну с водой. Баллоны для ацетилена должны подвергаться пневматическому испытанию на предприятиях, наполняющих баллоны пористой массой.
Освидетельствование баллонов, за исключением баллонов для ацетилена, включает:
•осмотр внутренней и наружной поверхности баллонов;
•проверку массы и вместимости;
•гидравлическое испытание.
Проверка массы и вместимости бесшовных баллонов вместимостью до 12 л включительно и свыше 55 л, а также сварных баллонов, независимо от вместимости, не производится. Емкость баллона определяется по разности между весом баллона, наполненного водой, и весом порожнего баллона или при помощи мерных бачков.
При удовлетворительных результатах освидетельствования предприятие выбивает на баллоне свое клеймо круглой формы диаметром 12 мм, дату проведенного и следующего освидетельствования. Результаты освидетельствования баллонов емкостью более 100 л заносятся в паспорт баллонов. Клеймо на баллонах в этом случае не ставится.
Освидетельствование баллонов должно проводиться в отдельных специально оборудованных помещениях. Температура воздуха в этих помещениях должна быть не ниже 12оС.
Эксплуатация, хранение и транспортировка баллонов должна производиться в соответствии с требованиями инструкции, утвержденной на предприятии в установленном порядке.
Рабочие, обслуживающие баллоны, должны быть обученные по специальной программе в учебно-курсовых комбинатах, аттестованные с выдачей удостоверения на право обслуживать сосуды, и проинструктированные на предприятии.
Запрещено полностью вырабатывать газ в баллоне. Остаточное давление должно быть не менее 0,05 МПа. Наполнение баллонов газами должно производиться по инструкции, разработанной с учетом свойств газа, местных условий и требований инструкции по наполнению баллонов газами. Например, для пропана наполнение баллонов должно быть не более 0,425 кг на 1 л вместимости баллона, для этилена – 0,286 кг на 1 л, для углекислоты –
0,72 кг на 1 л.
Запрещается наполнять газом баллоны, у которых:
•истек срок назначенного освидетельствования;
•истек срок проверки пористой массы (для ацетиленовых баллонов);
•поврежден корпус баллона;
•неисправны вентили;
•отсутствует надлежащая окраска или надписи;
•отсутствует избыточное давление газа;
•отсутствуют установленные клейма.
Наполнение баллонов, в которых отсутствует избыточное давление газа, производится после предварительной их проверки в соответствии с инструкцией предприятия-наполнителя.
Баллоны с газами могут храниться как в специальных помещениях, так и на открытом воздухе. Помещения складов для баллонов должно удовлетворять требованиям к взрывоопасным помещениям. На открытом воздухе баллоны должны быть защищены от атмосферных осадков и солнечных лучей. При этом хранение в одном помещении баллонов с кислородом и горючими газами запрещено. Баллоны с газом, устанавливаемые в помещениях, должны находиться на расстоянии не менее 1 м от радиаторов отопления и других отопительных приборов и печей и не менее 5 м от источников тепла с открытым огнем. Баллоны хранятся как в вертикальном положении, так и в горизонтальном на специальных стеллажах. При хранении в вертикальном положении для предохранения от
падения баллоны должны устанавливаться в специально оборудованные гнезда, клетки или ограждаться барьером. Для хранения в горизонтальном положении применяют деревянные рамы или стеллажи. При хранении на открытых площадках разрешается укладывать баллоны в штабеля с прокладками из веревки, деревянных брусьев или резины между горизонтальными рядами. При укладке баллонов в штабеля высота последних не должна превышать 1,5 м. Вентили баллонов должны быть обращены в одну сторону.
Транспортирование баллонов производится при помощи специальных тележек или автомобильным рессорным транспортом в горизонтальном положении в специальных гнездах или стеллажах. Транспортирование баллонов производится с навернутыми колпаками.
Общие требования безопасности к компрессорным установкам.
Проектирование, изготовление, реконструкция, наладка, ремонт и эксплуатация компрессорных установок должна производиться в соответствии с НПАОП 0.00-1.13-71 «Правила устройства и безопасной эксплуатации стационарных компрессорных установок, воздуховодов и газопроводов», ГОСТ 12.2.016-81 «Оборудование компрессорное. Общие требования безопасности» и ГОСТ 12.2.003-91 «Оборудование производственное. Общие требования безопасности».
Компрессорные установки могут взорваться при несоблюдении требований эксплуатации двигателей установки и условий наполнения воздухосборника.
Основными причинами взрыва являются:
•перегрев поршневой группы, что вызывает активное разложение масла с выделением паров углеводородов, смесь которых с воздухом приводит к образованию взрывоопасной среды;
•применение легкоплавких масел, способных разлагаться при невысоких температурах;
•накопление статического электричества на корпусе компрессора или воздухосборника, что может привести к искрению от пылинок в засасываемом воздухе;
•превышение давления в воздухосборнике в случае неисправности предохранительного клапана.
Правилами устройства и безопасной эксплуатации стационарных компрессорных установок, воздуховодов предусматривается необходимость применения в двигательной установке только тугоплавких специальных компрессорных масел и водяного охлаждения, а также недопустимость засасывания запыленного воздуха и обязательное заземление агрегата для снятия статического заряда.
Компрессорное оборудование должно иметь звуковую и световую сигнализацию. Сигнализация должна включаться при выходе параметров сжатия газов, режимов работы системы охлаждения и смазки за пределы, установленные стандартами на конкретные виды компрессоров. Предохранительные, сигнализирующие и блокировочные устройства должны
срабатывать автоматически и обеспечивать последовательность выполнения технологических операций по сжатию газа и заданные параметры процесса сжатия газа, а также безопасный режим работы компрессорного оборудования и его систем.
Оснащение компрессорного оборудования предохранительными клапанами и пластинами (мембранами) регламентировано Правилами. Места их установки, размеры, пропускная способность, исполнения оговариваются в стандартах на конкретные виды компрессорного оборудования. На нагнетательном газопроводе последней ступени сжатия, а также на газопроводах отбора газа промежуточного давления должен быть установлен обратный клапан.
Органы управления, обеспечивающие аварийную остановку компрессорного оборудования, должны быть размещены на пультах управления для передвижных компрессоров. Для стационарных компрессоров органы управления должны быть размещены на пультах управления и продублированы у выходов из машинных залов или в других удобных и безопасных местах.
Безопасность эксплуатации трубопроводов.
Меры безопасности при эксплуатации промышленных трубопроводов регламентированы НПАОП 0.00-1.11-98 «Правила устройства и безопасной эксплуатации трубопроводов пара и горячей воды», НПАОП 0.00-1.20- 98 «Правила безопасности систем газоснабжения Украины», ГОСТ 14202-69 и отраслевыми нормативами.
Согласно нормативов установлены следующие десять групп веществ, транспортируемых по трубопроводам: вода, пар, воздух, горючие газы (включая сжиженные), негорючие газы (включая сжиженные), кислоты, щелочи, горючие жидкости, негорючие жидкости, прочие вещества.
Опознавательная окраска и цифровое обозначение укрупненных групп трубопроводов должны соответствовать указанным в таблице 3.2.
Таблица 3.2 – Опознавательная окраска и цифровое обозначение укрупненных групп трубопроводов
Цифровое обозначение |
Транспортируемая среда |
Окраска труб |
1 |
Вода |
Зеленый |
2 |
Пар |
Красный |
3 |
Воздух |
Синий |
4,5 |
Горючие и негорючие газы |
Желтый |
6 |
Кислоты |
Оранжевый |
7 |
Щелочи |
Фиолетовый |
8,9 |
Горючие и негорючие жидкости |
Коричневый |
0 |
Прочие вещества |
Серый |
Противопожарные трубопроводы, независимо от их содержимого (вода, пена, пар для тушения и др.), спринклерные и дренчерные системы на участках напорно-регулирующей арматуры и в местах присоединения
шлангов и других устройств для тушения пожара должны окрашиваться в красный цвет (сигнальный).
Опознавательную окраску трубопроводов следует выполнять сплошной по всей поверхности коммуникаций или отдельными участками. Ширина участков опознавательной окраски принимается в зависимости от наружного диаметра трубопроводов (с учетом изоляции): для труб диаметром до 300 мм – не менее четырех диаметров; для труб диаметром свыше 300 мм – не менее двух диаметров.
Для обозначения опасных по свойствам веществ, транспортируемых по трубопроводам, следует наносить предупреждающие цветные кольца (таблица 3.3).
Таблица 3.3 – Предупреждающие цветные кольца
Цвет колец |
Характеристика опасности транспортируемой среды |
Красный |
Легковоспламеняемость, огнеопасность, взрывоопасность |
Желтый |
Опасность или вредность (ядовитость, токсичность, способность |
|
вызывать удушье, термические или химические ожоги, |
|
радиоактивность, высокое давление или глубокий вакуум и др.) |
Зеленый |
Безопасность или нейтральность |
Если вещество обладает одновременно несколькими опасными свойствами, обозначенными различными цветами, на трубопроводы следует наносить одновременно кольца нескольких цветов. На вакуумных трубопроводах, кроме отличительной окраски, следует давать надпись «Вакуум».
По степени опасности для жизни и здоровья людей или эксплуатации предприятия вещества, транспортируемые по трубопроводам, делятся на три группы, обозначаемые соответствующим количеством предупреждающих колец (таблица 3.4).
Таблица 3.4 – Группы опасности веществ и количество предупреждающих колец
Группа |
Транспортируемое вещество |
Давление, |
Температура, |
|
(количество |
|
МПа |
оС |
|
колец) |
|
|
|
|
|
Перегретый пар |
До 2,2 |
250 |
|
|
Горячая вода, насыщенный пар |
От 1,6 |
Св. 120 |
|
|
Перегретый и насыщенный пар, |
От 0,1 до 1,6 |
120 – 250 |
|
1 (одно) |
горячая вода |
|
|
|
Горючие (в том числе |
До 2,5 |
От –70 до 250 |
||
|
||||
|
сжиженные газы) жидкости |
|||
|
|
|
||
|
Негорючие жидкости и пары, |
До 6,4 |
От –70 до 350 |
|
|
инертные газы |
|
|
|
2 (два) |
Перегретый пар |
До 3,9 |
350 – 450 |
|
Горячая вода, насыщенный пар |
От 8,0 до 18,4 |
Св. 120 |
||
|
|
Продукты с токсическими |
|
|
|
|
свойствами (кроме сильно |
До 1,6 |
От –70 до 350 |
|
|
действующих ядовитых |
|||
|
|
|
||
|
веществ и дымящихся кислот) |
|
|
|
|
Горючие (в том числе |
|
250 – 350 |
|
|
сжиженные) активные газы, |
От 2,5 до 6,4 |
||
|
легковоспламеняющиеся и |
и от –70 до 0 |
||
|
горючие жидкости |
|
|
|
|
Негорючие жидкости и пары, |
От 6,4 до 10,0 |
340 – 450 |
|
|
инертные газы |
и от –70 до 0 |
||
|
Перегретый пар |
Независимо от |
450 – 660 |
|
|
|
давления |
||
|
|
|
||
|
Горячая вода, насыщенный пар |
Св. 18,4 |
Св. 120 |
|
|
Ядовитые сильнодействующие |
Независимо от |
От –70 до 700 |
|
|
вещества и дымящие кислоты |
давления |
||
|
|
|||
3 (три) |
Прочие продукты с |
Св. 1,6 |
От –70 до 700 |
|
токсическими свойствами |
||||
|
|
|||
|
Горючие (в том числе |
|
|
|
|
сжиженные) активные газы, |
Независимо от |
350 – 700 |
|
|
легковоспламеняющиеся и |
давления |
||
|
|
|||
|
горючие жидкости |
|
|
|
|
Негорючие жидкости и пары, |
Независимо от |
450 – 700 |
|
|
инертные газы |
давления |
||
|
|
При необходимости конкретизировать вид опасности дополнительно к цветным предупреждающим кольцам должны применяться предупреждающие знаки согласно ГОСТ 12.4.026-76. Цвет надписей при нанесении их на фоне опознавательной окраски принимают белым – на зеленом, красном и коричневом фоне; черным – на синем, желтом, оранжевом, фиолетовом и сером фоне.
Требования к изготовлению трубопроводов пара и горячей воды, их реконструкции, монтажу, наладке, ремонту и к проведению сварочных работ аналогичны требованиям к котлам, а также аналогичны требования к их регистрации, техническому освидетельствованию, пуску в работу, а также надзору, содержанию, обслуживанию и ремонту. Отличие только в нормах и сроках технического освидетельствования. Техническое освидетельствование трубопроводов, зарегистрированных в экспертно-техническом центре (ЭТЦ) Госнадзорохрантруда, проводит эксперт ЭТЦ (внешний осмотр – один раз в 3 года, гидравлическое испытание (давлением 1,25 от рабочего, но не менее 0,2 МПа) – перед пуском в работу, после аварии, после ремонта или после отработки нормативного срока эксплуатации). Предприятия – владельцы трубопроводов должны проводить самостоятельно техническое освидетельствование в следующие сроки: наружный осмотр не реже одного раза в год; гидравлическое испытание трубопроводов на прочность и
плотность одновременно давлением 1,25 от рабочего (но не менее 0,2 МПа) перед пуском в эксплуатацию, после монтажа или ремонта с применением сварки, а также при пуске в работу трубопроводов после нахождения их на консервации более двух лет.
Проектирование, изготовление, реконструкция, наладка, ремонт и эксплуатация систем газоснабжения должна производиться в соответствии с НПАОП 0.00-1.20-98 «Правила безопасности систем газоснабжения Украины». Эти требования аналогичны рассмотренным требованиям. Отличие только в том, что объекты систем газоснабжения перед началом их сооружения, монтажа и наладки должны быть зарегистрированы в местных органах Госнадзорохрантруда (все остальные объекты регистрируются после монтажа перед вводом в эксплуатацию).
Безопасность эксплуатации установок криогенной техники.
Криогенная техника – это область техники, связанная с достижением и практическим применением криогенных температур. Под криогенными продуктами следует понимать вещества или смесь веществ, находящихся при криогенных температурах 0 – 120 К. К основным криогенным продуктам относятся: азот, кислород, водород, гелий, аргон, неон, криптон, ксенон, озон, фтор и метан.
При производстве, хранении, транспортировании и использовании криогенных продуктов образуются опасные и вредные производственные факторы, воздействию которых подвержен персонал, обслуживающий криогенное оборудование или находящийся рядом с ним. При непосредственном контакте человеческого тела с криогенной жидкостью, ее парами, охлажденной ими газовой средой, частями оборудования, трубопроводов, инструмента и конструкций под действием криогенной температуры происходит образование кристаллов льда в живых тканях, что может вызвать их разрыв. Контакт тела с криогенными продуктами также может вызвать ожог участков тела, глаз (вплоть до потери зрения) и обморожений в результате глубокого охлаждения участков тела. Практически все криогенные продукты токсичны (кроме криптона и ксенона).
При работе с криогенными жидкостями возникают вредные и опасные факторы, характерные для криогенных продуктов: низкая температура криогенных продуктов; самопроизвольное повышение давления криогенных продуктов при их хранении и транспортировке; уменьшение концентрации кислорода в зоне дыхания при разрушении криогенного оборудования или проливе криогенной жидкости; гидравлические удары, обусловленные появлением паровых полостей в трубопроводах и последующим заполнением их жидкостью; наличие в воздухе токсичных паров и газов криогенных продуктов, превышающих ПДК; контакт органических веществ и материалов с криогенными жидкостями-окислителями и контакт горючих криогенных жидкостей с кислородом или воздухом, что приводит к возгоранию, пожарам или взрывам.
При хранении и транспортировании криогенных жидкостей необходимо обеспечить высококачественную тепловую изоляцию (порошково-вакуумная или экранно-вакуумная). Сосуды для хранения и транспортирования криогенных жидкостей должны быть оборудованы предохранительными клапанами, разрывными мембранами, а работающие под избыточным давлением – манометрами. Должны соблюдаться нормы заполнения сосудов криогенными жидкостями. Наружная поверхность емкостей для криогенных жидкостей должна быть окрашена алюминиевой краской, иметь соответствующие надписи и отличительные полосы.
Сжиженные газы хранят и перевозят в стационарных и транспортных сосудах (цистернах), снабженных высокоэффективной тепловой изоляцией в соответствии с требованиями НПАОП 0.00-1.07-94 «Правила устройства и безопасной эксплуатации сосудов, работающих под давлением».
Для хранения и транспортирования криогенных продуктов изготавливают криогенные сосуды (по ГОСТ 16024-79Е) типа СК емкостью 6, 10, 16, 25 и 40 литров. Для хранения и транспортирования относительно небольших количеств криогенных продуктов (от нескольких литров до нескольких десятков литров) используют сосуды Дьюара. Сосуды Дьюара типа АСД изготавливают из алюминиевого сплава шаровой или цилиндрической формы емкостью 5, 16, 25 и 100 литров. Эти сосуды имеют двойную стенку. Межстенное пространство засыпано экранирующей изоляцией (аэрогель с бронзовой пудрой) и воздух из него откачан.
При работе с сосудами Дьюара следует учитывать, что взрывы сосудов Дьюара происходят вследствие плотно закрытой горловины сосуда: закупорки горловины льдом; нарушения вакуумной изоляции сосуда и резкого повышения температуры внутри сосуда.
Запрещается перевозить сосуды Дьюара в пассажирском лифте; допускать присутствие посторонних лиц на площадке, где находятся сосуды Дьюара во время заполнения жидкими газами; оставлять на отогрев сосуды Дьюара, потерявшие вакуум там, где могут находиться люди; в местах нахождения сосудов Дьюара курить, пользоваться открытым огнем, хранить горючие материалы и вещества. Запрещается также ремонтировать не отогретые сосуды и содержащие криогенные продукты.
Работу с криогенными жидкостями следует выполнять в чистой одежде и средствах индивидуальной защиты. От радиаторов отопления и других нагревательных приборов сосуды с криогенными жидкостями должны находиться не ближе 1 м; от печей и других источников открытого огня – не менее 5 м.
3.2.3 Безопасность при погрузочно-разгрузочных работах и на транспорте
Анализ причин производственного травматизма в промышленности показывает, что около 30% несчастных случаев на предприятиях связано с эксплуатацией транспортных средств, которые включают как рельсовый, так и безрельсовый транспорт ( автомобили, электрокары, автопогрузчики) а также транспортирующие подъемно-транспортные машины.
Погрузочно-разгрузочные и транспортные работы следует выполнять в соответствии с требованиями Закона Украины «О перевозке опасных грузов»
(№1644-14 от |
06.04.2000), ГОСТ 12.3.002-75, ГОСТ 12.3.009-76, |
||
ГОСТ 12.3.010-82, |
ГОСТ 12.3.020-80 |
и |
нормативно-технической |
документации, утвержденной органами государственного надзора. Безопасность погрузочно-разгрузочных работ и транспортных операций на предприятиях обеспечивают инженерно-технические работники, ответственные за безопасное выполнение работ по перемещению грузов, безопасную эксплуатацию и содержание в исправном состоянии подъемнотранспортного оборудования.
К погрузочно-разгрузочным работам (обвязке, зацепке и перемещению грузов) допускаются рабочие не моложе 18 лет, обученные по соответствующей программе и аттестованные комиссией предприятия. Повторная проверка знаний этих рабочих производится не реже одного раза в год. Рабочие, допущенные к выполнению погрузочно-разгрузочных работ и транспортных операций, подчиняются лицу, ответственному за безопасность работ по перемещению грузов.
В зависимости от опасности обращения с грузами при погрузке, транспортировке и выгрузке грузы делятся на четыре группы:
•малоопасные грузы (металлы, лесо- и стройматериалы и др.);
•опасные грузы вследствие габаритных размеров:
•пылящие и горячие грузы (цемент, мел, известь, асфальт и др.);
•опасные грузы (по ГОСТ 19433-88 «Грузы опасные. Классификация и маркировка»).
Копасным грузам (по ГОСТ 19433-88) относятся вещества и предметы, которые при транспортировании, погрузочно-разгрузочных работах и хранении могут послужить причиной взрыва, пожара или повреждения транспортных средств, зданий или сооружений, а также гибели, увечья, отравления, ожогов, облучения или заболевания людей или животных. Опасные грузы подразделяются на 9 классов и подклассы:
1) класс 1 – взрывчатые вещества, которые по своим свойствам могут взрываться, вызывать пожар с взрывчатым действием, а также устройства, содержащие взрывчатые вещества и средства взрывания, предназначенные для производства пиротехнического эффекта. Этот класс делится на 4 подкласса в зависимости от взрывчатых свойств веществ;
2) класс 2 – газы сжатые, сжиженные и растворенные под давлением,
отвечающие хотя бы одному из следующих условий: избыточное давление в сосуде при температуре 20оС равно или выше 0,1 МПа, абсолютное давление паров при температуре 50оС равно или вы ше 0,3 МПа, критическая температура ниже 50оС; растворенные под давлением; сжиженные переохлаждением. Этот класс делится на 4 подкласса в зависимости от воспламеняющихся и ядовитых свойств газов;
3)класс 3 – легковоспламеняющиеся жидкости, смеси жидкостей, а также жидкости, содержащие твердые вещества в растворе или
суспензии, которые выделяют легковоспламеняющиеся пары, имеющие температуру вспышки в закрытом сосуде 61оС и ниже. Этот класс делится на 3 подкласса в зависимости от температуры вспышки в закрытом сосуде;
4)класс 4 – легковоспламеняющиеся вещества и материалы (кроме взрывчатых), способные во время перевозки легко загораться от внешних источников воспламенения в результате трения, поглощения влаги, самопроизвольных химических превращений, а также при нагревании. Этот класс делится на 3 подкласса в зависимости от условий воспламенения;
5)класс 5 – окисляющие вещества и органические перекиси, которые
способны легко выделять кислород, поддерживать горение, а также могут в соответствующих условиях или в смес и с другими веществами вызывать самовоспламенение и взрыв. Этот класс делится на 2 подкласса в зависимости от их способности гореть;
6)класс 6 – ядовитые и инфекционные вещества, способные вызвать смерть, отравление или заболевание при попадании внутрь организма или при соприкосновении с кожей и слизистой оболочкой. Этот класс делится на 2 подкласса в зависимости от характеристики веществ;
7)класс 7 – радиоактивные вещества. Этот класс делится на 3 подкласса в зависимости от характеристики радиоактивности веществ;
8)класс 8 – едкие и коррозионные вещества, которые вызывают повреждение кожи, поражение слизистых оболочек глаз и дыхательных путей, коррозию металлов и повреждение транспортных средств, сооружений или грузов, а также могут вызвать пожар при взаимодействии с органическими материалами или некоторыми химическими веществами. Этот класс делится на 3 подкласса в зависимости от вида веществ;
9)класс 9 – вещества с относительно низкой опасностью при транспортировании, не отнесенные ни к одному из предыдущих классов, но требующие применения к ним определенных правил перевозки и хранения. Этот класс делится на 4 подкласса в зависимости от характеристики веществ.
Взависимости от класса опасности опасные грузы должны иметь знак опасности (по ГОСТ 19433-88) с указанием характеристики опасности и мер предосторожности. Знаки опасности наносятся на упаковке груза на видном месте.
По массе одного места грузы делятся на три категории: 1 – массой
менее 80 кг, а также сыпучие, мелкоштучные и т.п.; 2 – массой от 80 до 500 кг; 3 – массой более 500кг.
Согласно требованиям ГОСТ 12.3.009-76 «Работы погрузочноразгрузочные. Общие требования безопасности» на предприятиях должны быть составлены карты технологических процессов на погрузочноразгрузочные работы. В этих картах должны учитываться следующие требования безопасности: 1) механизация при погрузочно-разгрузочных работах грузов 2-й и 3-й категорий, а также для грузов первой категории при транспортировании грузов на расстояние более 25 м по горизонтали и для сыпучих материалов – на расстоянии свыше 3,5 м по вертикали; 2) специальная упаковка, носилки и тележки для переноски и перевозки стеклянной тары с агрессивными жидкостями. Правила складирования грузов следующие: высота штабеля не должна превышать 6 м для неразборной тары и 4,5 м – для складной тары; 3 м – для грузов в ящиках при ручной погрузке и 6 м – при механизированной, для барабанов с карбидом кальция – не более двух ярусов , для корзин с бутылями агрессивных жидкостей – в один ряд; ширина главного прохода в помещениях закрытых складов должна быть не менее 3 м. При выполнении работ с грузами третьей (пылящие и горючие) и четвертой (опасные) групп следует применять соответствующие СИЗ. Следует соблюдать совместимость перевозимых грузов и правила укладки грузов на транспортное средство.
Поднимать и переносить грузы вручную допускается в исключительных случаях (при невозможности применения подъемнотранспортных средств) на расстояние не более 25 м. Предельная норма переноски грузов вручную по ровной и горизонтальной поверхности на одного человека не должна превышать: 10 кг для подростков женского пола от 16 до 18 лет; 16 кг – для подростков мужского пола от 16 до 18 лет; 20 кг – для женщин старше 18 лет; 50 кг – для мужчин старше 18 лет. Допускать подростков к переноске тяжестей разрешается только при условии, что эти операции связаны с выполнением основной работы по специальности и занимают не более 1/3 всего их рабочего времени.
Перемещать баллоны разрешается только на тележках или специальных носилках, а бутыли с опасными жидкостями – в плетеных корзинах. Подъем этих грузов на высоту вручную запрещен. Переносить материалы на носилках разрешается в исключительных случаях по горизонтальному пути на расстояние не более 50 м, запрещается переносить материалы на носилках по лестницам и стремянкам.
Для перемещения грузов на короткие расстояния можно применять роликовые ломы. При подъеме груза нужно одной рукой удерживать лом, а другой – нажимать на груз. При перемещении грузов с помощью катков необходимо соблюдать следующие условия: катки должны изготовляться из дуба или клена диаметром не менее 50 мм, стальные – из отходов труб диаметром не менее 25 мм, катки должны быть одинаковой длины и диаметра; подкладывать очередной каток под перемещаемый груз следует осторожно, извлекая из-под груза после полного его освобождения.
Груз массой до 50 кг разрешается выгружать, спуская по покатам или слегам, перенося вручную или на носилках, а массой более 50 кг – перемещая по трапам или слегам при помощи веревок или специальных тележек.
Безопасность эксплуатации подъемно-транспортного оборудования.
Требования к эксплуатации регламентируются требованиями НПАОП 0.00- 1.03-03 «Правила устройства и безопасной эксплуатации грузоподъемных кранов», ГОСТ 12.2.053-91 «Краны-штабелеры. Требования безопасности» и др. Общими требованиями безопасности являются: обеспечение надежности конструкции оборудования (выбор соответствующего материала и запаса прочности, защита от тепловых воздействий и коррозии), наличие предохранительных устройств (ограничители грузоподъемности, высоты подъема груза и скорости, концевые выключатели, тормоза, ловители, аварийные выключатели и др.), периодическое техническое освидетельствование оборудования и соответствующая подготовка персонала.
Подъемно-транспортное оборудование до пуска в работу регистрируются в органах Госнадзорохрантруда и допускаются к эксплуатации только после испытания и технического освидетельствования. Подъемно-транспортное оборудование проходит техническое освидетельствование: перед пуском в работу и периодически в процессе работы.
Виды испытаний:
•осмотр всех механизмов и несущих конструкций;
•статическое испытание грузом, превышающим грузоподъемность машины на 25%, для проверки ее прочности и устойчивости против опрокидывания (груз поднимают на высоту 100 – 200 мм для кранов стрелового типа и на 200 – 300 мм для передвижных консольных и мостовых кранов и выдерживают в течение 10 мин, затем груз опускают и проверяют отсутствие остаточных деформаций, трещин и других повреждений);
•динамическое испытание грузом, превышающим грузоподъемность машины на 10%. При динамическом испытании проводят повторные
подъем и опускание груза для проверки действия механизмов и тормозов.
Различают частичное освидетельствование (один раз в год) и полное (один раз в три года). При частичном о свидетельствовании оборудование подвергают осмотру, а при полном - осмотру, статическому и динамическому испытанию.
Для обеспечения безопасной эксплуатации подъемно-транспортного оборудования администрация предприятия назначает и обучает:
•ответственное лицо по надзору за подъемно-транспортным оборудованием;
•лиц, ответственных за безопасное производство работ по перемещению грузов;
• крановщиков, слесарей, подкрановых рабочих.
Ремонтные работы на подъемно-транспортном оборудовании производятся с оформлением наряда-допуска.
К управлению грузоподъемными механизмами и машинами допускаются лица не моложе 18 лет, прошедшие обучение и аттестацию. Работы с применением грузоподъемных кранов должны выполняться под руководством ответственного лица, назначенного администрацией предприятия. Для управления работой крана применяется знаковая сигнализация рукой или флажком. Машинист крана обязан выполнять команды по подъему-опусканию или перемещению груза, подаваемые только ответственным лицом. Только команда «Стоп» выполняется при подаче ее любым работающим.
Электропогрузчики и автопогрузчики должны осматриваться ежесменно водителем. При эксплуатации погрузчиков запрещается захватывать груз вилами с разгона путем врезания; поднимать груз при наклоне рамы с вилами от себя; поднимать и опускать груз или менять наклон рамы при движении; поднимать груз выше допустимой высоты. Для автопогрузчиков с крановой стрелой высота подъема груза не ограничивается. При работе на вилочном погрузчике необходимо, чтобы груз был прижат к вертикальной части захватной вилки, на обе лапы груз должен распределяться равномерно и выходить за пределы вилки не более 1/3 ее длины. Груз должен укладываться не выше защитного устройства, а при транспортировании крупногабаритного груза, который выходит за защитное устройство, должно быть выделено лицо для сопровождения погрузчика.
Эксплуатация внутризаводского транспорта. Для обеспечения безопасности разграничивают пути движения пешеходов и пути перемещения транспорта. Для этого на каждом предприятии должна быть составлена и доведена до всех работающих план-схема движения транспортных средств и пешеходов, обозначаются переходы. На территории предприятия устанавливаются необходимые дорожные знаки.
Скорость движения железнодорожного транспорта на территории предприятия не должна превышать 10 км/ч, а при въезде в здание – 3 км/ч. В местах пересечения железнодорожных путей с дорогами должны устанавливаться предупредительные знаки, а при интенсивном движении – шлагбаумы.
Габариты приближения транспортных средств до строений и сооружений должны быть не менее 3 м, а до выходных дверей из помещений
– не менее 6 м. Складировать грузы в штабеля высотой до 1,2 м разрешается на расстоянии не менее 2 м от наружной головки рельса, а при большей высоте штабеля – не менее 2,5 м. При движении железнодорожного транспорта должны подаваться звуковые сигналы – гудками локомотива или ручными свистками. Переходить железнодорожные пути пешеходы должны под прямым углом, убедившись в отсутствии движущегося поезда.
Скорость движения автомобильного транспорта на прямых участках дорог не должна превышать 12 км/ч, а в местах сужения дороги – 5 км/ч;
внутри цехов и складов по главным проходам – 5 км/ч, а в узких местах – 3 км/ч. В кузове грузового автомобиля разрешена перевозка людей в том случае, если кузов специально оборудован для перевозки людей.
Ширина проезда для электрокарного транспорта должна быть не менее 1,8 м при одностороннем движении и 3 м – при двустороннем. При движении в помещениях, на перекрестках дорог, в местах движения пешеходов и переездов через железнодорожные пути скорость движения электрокар не должна превышать 3 км/ч.
Эксплуатация внутрицехового транспорта. Движущиеся части конвейеров (барабаны, натяжные устройства, ролики и др.), к которым возможен доступ работающих, должны ограждаться. В зоне возможного нахождения людей должны ограждаться канаты, блоки и груз натяжных устройств, загрузочные и приемные устройства, нижние выступающие части конвейера и т.п. На технологической линии, состоящей из нескольких последовательно установленных и одновременно работающих конвейеров или из конвейеров в сочетании с другими машинами (питателями, дробилками и т.п.), приводы конвейеров и всех машин должны быть сблокированы так, чтобы в случае внезапной остановки какой-либо машины или конвейера предыдущие машины или конвейеры отключались, а последующие продолжали работать до полного схода с них транспортируемого груза. Должна предусматриваться возможность отключения каждого механизма с места обслуживания. Конвейеры в головной и хвостовой части должны быть оборудованы аварийными кнопками «Стоп». Конвейеры с открытой трассой длиной более 30 м должны быть оборудованы дополнительными выключающимися устройствами, позволяющими остановить конвейер в аварийных ситуациях с любого места со стороны прохода для обслуживания.
Приводы механических тележек должны быть ограждены, а головки рельсовых путей не должны выступать над уровнем пола. Пульт управления тележкой должен располагаться в месте с хорошим обзором. В местах движения тележки через дверные проемы должен обеспечиваться проход шириной не менее 700 мм.
Рольганги не должны деформироваться под нагрузкой, конструкция их должна исключать провал груза между роликами и падение груза вбок. В конце пути рольганга устанавливается ограждающее устройство, препятствующее падению груза.
При движении электрокар в помещениях должны быть обозначены пути их проезда и скорость движения электрокар не должна превышать 3
км/ч.
На территории цеха устраивают безопасные пути движения, которые обозначают указателями и оборудуют ограждениями, переходными мостиками и другими средствами защиты.
Безопасная эксплуатация электроустановок
Основные нормативные документы:
1.Правила устройства электроустановок. Шестое издание, переработанное и дополненное / М.: - Энергоатомиздат, 1985.
2.Правила технической эксплуатации электроустановок потребителей
–М.: Энергоатомиздат, 1989.
3.ОНАОП 0.00-1.21-98 Правила безопасной эксплуатации электроустановок потребителей.
Электрооборудование должно соответствовать требованиям действующих нормативных актов и иметь сертификат соответствия.
Паспорт, инструкция и другая документация должны быть переведены на украинский язык.
Основные требования к персоналу: работники, обслуживающие электроустановки, должны знать правила в объеме требований, определяемых занимаемой должностью и профессией, и иметь соответствующую квалификационную группу по электробезопасности (I, II, III, IV, V), и соответствующее удостоверение. Удостоверение о проверке знаний ведется работником комиссии по проверке знаний предприятия, организации.
Перечень работ с повышенной опасностью утверждается руководителем предприятия.
Результаты проверки знаний фиксируются в специальном журнале, страницы которого пронумерованы, прошнурованы и скреплены печатью предприятия.
Срок хранения журнала – 3 года после последней записи.
ОТ при оперативном обслуживании электроустановок
Оперативное обслуживание включает:
1.Систематический надзор за состоянием и режимом работы электрооборудования и сооружений.
2.Обнаружение дефектов оборудования, которые образовались при эксплуатации, и принятие мер по их устранению.
3.Выполнение мероприятий, обеспечивающих безопасность ремонтных и профилактических работ.
4.Выполнение переключений в распределительных устройствах (РУ).
5.Передача информации о работе вышестоящим звеньям и выполнение их указаний.
Оперативная работа проходит как в форме дежурства персонала ( например, на подстанциях ), так и в составе оперативно-выездных бригад.
Оперативные работники, обслуживающие электроустановку единолично, должны иметь группу по электробезопасности не ниже IV в электроустановках напряжением выше 1000 В и III – в электроустановках напряжением до 1000 В.
Остальной электротехнический персонал может проводить осмотр под надзором одного из представителей дежурного или оперативно-ремонтного персонала с указанными группами по электробезопасности.
При работе запрещается приближаться к токоведущим частям ближе, чем указано в ПТБ от 0,6 м для 6-35 кВ до 5 м при 750 кВ.
Для предотвращения поражения напряжением нельзя приближаться к месту замыкания на землю ближе чем на 4 м в ЗРУ и 8 м в ОРУ можно только для специальных оперативных переключений и освобождения людей от тока при использовании основных защитных средств. Отключать и включать коммутационные аппараты с ручным приводом необходимо в диэлектрических перчатках для предотвращения поражения напряжением прикосновения.
Двери помещений электроустановок ( щитов, сборок и т.п. ) должны быть постоянно заперты, ключи выдаются под расписки электротехническому персоналу, дежурному, оперативному и ремонтному.
Выполнение работ
Работы в электроустановках подразделяются на три категории ( в отношении мер безопасности ):
- со снятием напряжения;
-без снятия напряжения на токоведущих частях и вблизи них;
-без снятия напряжения вдали от токоведущих частей, находящихся под напряжением.
Кработам, выполняемых со снятием напряжения, относятся работы, которые производятся в электроустановке, в которой с токоведущих частей снято напряжение и доступ к любым токоведущим частям невозможен.
Кработам, выполняемым без снятия напряжения на токоведущих частях и вблизи них, относятся работы, проводимые непосредственно на них или на расстояниях от токоведущих частей, меньших, чем допускают ПТБ. Эти работы выполняют не менее 2 работников. Старший с группой IV , остальные – III.
Работой без снятия напряжения вдали от токоведущих частей, находящихся под напряжением, считаются работы, при которых исключено случайное приближение работающего к токоведущим частям. К этим работам относят работы на корпусах, оболочках, за ограждениями, на расстояниях, разрешенных ПТБ.
При работах без снятия напряжения на токоведущих частях или без них необходимо оградить другие токоведущие части, работать в средствах защиты и применять инструмент с изолирующими рукоятками.
Установка и снятие предохранителей, как правило, производят при снятом напряжении.
До начала работ и при их проведении необходимо выполнять определенные организационные и технические мероприятия, обеспечивающие безопасность труда.
Корганизационным мероприятиям относят:
1.Утверждение перечней работ, выполняемых по нарядам, распоряжениям и в порядке текущей эксплуатации.
2.Назначение ответственных лиц за безопасное ведение работ. Этими ответственными лицами являются по существу все участники работы, начиная от руководителя, выдающего наряд или распоряжение, вплоть до
члена бригады. Только мера ответственности у низ разная и эта мера указана в должностных обязанностях или инструкциях и подкреплена письменным указанием руководителя предприятия ( приказом ), в котором говорится, что этот работник имеет право быть руководителем, этот – допускающим, этот имеет право единоличного осмотра установки и т.д.
Ответственными за безопасность работ, выполняемых в электроустановках, являются:
-работник, выдающий наряд, распоряжение;
-работник, дающий разрешение на подготовку рабочего места;
-работник, подготавливающий рабочее место, допуск;
-работник, допускающий к работе ( далее допускающий );
-руководитель работ;
-работник, наблюдающий за безопасным выполнением работ ( далее наблюдающий );
-члены бригады.
3. Следующее организационное мероприятие – это оформление работ нарядом, распоряжением или утверждением перечня работ, выполняемых в порядке текущей эксплуатации.
Наряд – это задание на безопасное ведение работ повышенной опасности на специальном бланке. Составляется наряд в двух экземплярах и после оформления один хранится в папке нарядов, а другой – у производителя работ после допуска бригады к работе. Если наряд передается по телефону, то он оформляется в трех экземплярах: один экземпляр заполняет лицо, выдающее наряд, а два – лицо, принимающее его по телефону. Наряд выдается на срок не более 15 календарных дней со дня начала работы. Наряды, работы по которым закончены полностью, хранятся в течение 30 суток.
Все наряды и распоряжения регистрируются в специальном журнале. Журнал должен быть пронумерован, прошнурован и скреплен печатью. Срок его хранения после последней записи – 6 месяцев.
На менее сложные, но опасные работы может выдаваться разовое устное или письменное распоряжение. Форма его произвольная, но в нем должны быть указаны время, место, содержание работы, меры безопасности и ответственные лица. Распоряжение фиксируется в журнале.
По распоряжению могут выполняться следующие виды работ:
-работы без снятия напряжения вдали от токоведущих частей, находящихся под напряжением, продолжительностью не более одной смены;
-аварийно-восстановительные работы продолжительностью до 1 часа;
-работы со снятием напряжения в электроустановках напряжением до 1000 В продолжительностью не более одной смены;
-уборка коридоров и помещений ЗРУ;
-уборка территории ОЗУ и т.п.
В порядке текущей эксплуатации могут производиться:
-работы без снятия напряжения вдали от токоведущих частей, находящихся под напряжением ( уборка ЗРУ, территории ОРУ, ремонт осветительной аппаратуры и замена ламп, расположенных вне камер и ячеек, уход за щетками 2 двигателей и их замена и т.п.);
-работы со снятием напряжения в электроустановках напряжением до 1000 В ( ремонт магнитных пускателей, пусковых кнопок, автоматических выключателей, рубильников, реостатов при условии ее установки вне щитов
исборок, смена предохранителей, ремонт осветительной проводки, двигателей и т.п.).
4. Следующее организационное мероприятие – это подготовка рабочего места и допуск к выполнению работ.
Подготовка рабочего места и допуск могут проводиться только с разрешения оперативных работников ( дежурным персоналом не ниже IV группы ). Подготовку рабочих мест выполняют два работника, имеющих право оперативных переключений в данной электроустановке.
Допускающий вместе с руководителем работ должны проверить выполнение технических мероприятий по подготовке рабочего места.
Допускающим может быть лицо не ниже IV группы в установках свыше 1000 В из дежурного или оперативно-ремонтного персонала.
Допускающий должен:
1)проверить соответствие бригады и их удостоверения;
2)провести инструктаж;
3)доказать бригаде, что напряжение отсутствует показом установленных заземлений и проверкой отсутствия напряжения с последующим прикосновением рукой к токоведущим частям.
После инструктажа допускающего бригаду должен проинструктировать руководитель работ.
Без проведения инструктажа допуск бригады к работе запрещается. Проведение инструктажа и допуска оформляется подписями допускающего и руководителя работ с указанием даты и времени.
Допуск оформляется в обоих экземплярах наряда, из которых один остается у руководителя работ ( наблюдающего ), а второй – у допускающего.
При работе по распоряжениям время допуска регистрируется по нарядам и распоряжениям.
Допускающий отвечает за полноту принятых мер безопасности и их соответствия наряду, за правильный допуск к работе и инструктирование на рабочем месте.
5. Следующее организационное мероприятие – это надзор во время выполнения работ.
Надзор выполняет производитель работ или наблюдающий ( IV группа ). Производитель работ и наблюдающий должны все время находиться на месте работы.
Наблюдающему запрещено совмещать надзор с выполнением другой работы.
Оставаться в закрытых и открытых РУ одному руководителю работ или членам бригады без руководителя работ не разрешается.
6.Следующее организационное мероприятие – это оформление перерывов в работе, перевод на другое рабочее место.
Смысл этих мероприятий в том, что без надзора производителя работ и руководителя бригада удаляется с рабочего места.
При перерывах в работе на протяжении рабочего дня ( на обед, по условиям производства работ ) бригада всем составом удаляется с рабочего места. Двери помещения РУ и ограждений электроустановок закрываются на замок.
Члены бригады не имеют права возвращаться на рабочее мест отсутствии руководителя работ ( наблюдающего ).
Допуск бригады к работе после такого перерыва осуществляется руководителем без оформления в наряде.
При перерывах в работе по окончании рабочего дня бригада всем составом выводится с рабочего места, все закрывается на ключ. Окончание работы каждого дня оформляется в наряде за подписью руководителя ( наблюдающего ).
Повторный допуск на следующий день на подготовленное рабочее место осуществляет допускающий.
Повторный допуск оформляется в наряде.
Перевод бригады на новое место в электроустановки свыше 1000 В осуществляет допускающий. Перевод на другое рабочее место оформляется записью в наряде.
В электроустановках до 1000 В этот перевод производится без оформления в наряде.
7.Следующее организационное мероприятие – это оформление окончания работы.
При этом последовательно выполняются: - вывод бригады с рабочего места;
- снятие временных ограничений и плакатов; - снятие заземлений;
-установка на место постоянных ограждений и плакатов;
-закрытие на замок дверей, помещений.
После осмотра оборудования, места работы, проверки отсутствия людей, посторонних предметов и инструмента на рабочих местах и т.п. руководитель оформляет закрытие наряда записью в наряде и в журнале учета работ по нарядам и распоряжениям.
8. Следующее организационное мероприятие – это включение электроустановок после полного окончания работ.
Разрешение на включение электроустановки дает оперативный работник после получения сообщения от всех допускающих и руководителей работ о полном окончании работ на данной установке.
Технические мероприятия, обеспечивающие безопасность работ
При работах, выполняемых со снятием напряжения, должны быть выполнены следующие технические мероприятия в следующем порядке:
1. Произведены необходимые отключения и приняты меры, исключающие самопроизвольное или ошибочное включение.
2 Вывешены запрещающие плакаты на приводах ручного и на ключах дистанционного управления коммутационной аппаратурой.
3.Проверка отсутствия напряжения на токоведущих частях, которые должны быть заземлены для защиты людей от поражения электрическим током.
4.Установка заземлений ( включены заземляющие ножи, установлены переносные заземления ).
5.Ограждены, при необходимости, рабочие места и оставшиеся под напряжением токоведущие части и вывешены на ограждениях плакаты безопасности.
Эти мероприятия выполняются персоналом ( дежурным или оперативно-ремонтным ), обслуживающим данную электроустановку. При этом отключение должно проводиться со всех сторон, откуда может быть подано напряжение, в том числе и вторичные обмотки трансформаторов для
предотвращения обратной трансформации. Отключение должно обеспечить видимый разрыв ( отсоединение шин, проводов, снятие предохранителей ). В этом разрыве и отсутствии шунтирующих перемычек необходимо воочию убедиться. После этого приводы коммутационных аппаратов, ограждения, двери и т.д. должны быть заперты на замки, отключены цепи управления. На приводах отключенных аппаратов вывешиваются плакаты «Не включать! Работают люди». На лестницах, конструкциях, по которым разрешено подниматься для проведения работ «Влазить здесь!», а на остальных «Не влезай! Убьет».
Обязательным этапом перед наложением заземления является проверка отсутствия напряжения, указателем напряжения или измерительной штангой, работоспособность которых необходимо проверить непосредственно перед измерением.
Непосредственно после проверки отсутствия напряжения устанавливаются заземления. Переносные заземления сначала нужно присоединить к заземляющему устройству, а затем, после проверки отсутствия напряжения, установить на токоведущие части. Снимать заземление необходимо в обратном порядке.
Установки и снятие переносных заземлений производят с использованием изолирующей штанги и диэлектрических перчаток. В установках свыше 1000 В устанавливают заземление 2 человека III и IV группы, а снимать заземление может 1 человек с III группой.
Включать заземляющие ножи может 1 человек с IV группой из дежурного или оперативно-ремонтного персонала.
Освидетельствование безопасного состояния электроустановок
Периодичность освидетельствования – один раз в три года. Это освидетельствование производится комиссией предприятия в составе:
-председатель;
-начальник энергетической службы;
-начальник отдела ОТ.
Комиссия составляет акт, который утверждает руководитель предприятия. Этот акт регистрируется и сохраняется на предприятии. Копии актов направляют в:
-орган Госнадзороргантруда;
-Госэнергопотребнадзор;
-отдел ОТ Госадминистрации.
Если установка выработала свой ресурс, то освидетельствование производит ЭТУ Госнадзороргантруда.
Руководитель предприятия обязан:
-назначить ответственного за исправное состояние и безопасную эксплуатацию из числа ИТР;
-обеспечить необходимое количество электротехнических работников;
-утвердить Положение об энергетической службе предприятия, а также должностные инструкции и инструкции по ОТ;
-установить необходимый порядок работ и наблюдений за электроустановками;
-обеспечить проверку знаний работников в установленные сроки;
-обеспечить проведение противоаварийных, приемно-сдаточных и профилактических испытаний и измерений;
-обеспечить проведение технического освидетельствования электроустановок.
Специалисты служб ОТ обязаны контролировать безопасную эксплуатацию электроустановок и должны иметь IV группу по электробезопасности.
Запрещается возлагать на энергослужбу обязанности, не входящие в ее профессиональную компетенцию.
ТЕМА 8. ПОЖАРНАЯ БЕЗОПАСНОСТЬ В ОТРАСЛИ
Наличие на объектах черной металлургии большого количества легковоспламеняющихся и горючих жидкостей и газов, а также кокса, угля, мазута и других горючих материалов, хранящихся, транспортируемых и используемых в различных технологических процессах, создает потенциальную опасность загораний, пожаров и взрывов. Поэтому проблема обеспечения взрывной и пожарной безопасности объектов черной металлургии является весьма актуальной и имеет большое народнохозяйственное значение. Возникновение пожара на производстве наносит большой урон не только коллективу цеха и предприятия, где произошел пожар, но и другим предприятиям, использующим продукцию (например, лист) в качестве исходной заготовки для производства готового изделия (например, труб большого диаметра).
Пожарную опасность представляют все основные производства предприятий черной металлургии. Определенную сложность на объектах черной металлургии вызывает категорирование в соответствии с требованиями ОНТП 24-86 доменных, сталеплавильных, прокатных и других цехов, имеющих большие площади. В указанных цехах пожароопасные помещения (кабельные подвалы, маслоподвалы, туннели и т.д.), расположенные ниже нулевой отметки, как правило, занимают более 10% общей площади здания и значительно превышает 3500 м2. В связи с этим здание по пожарной опасности должно быть отнесено к категории В и выполнено не ниже II степени огнестойкости. В соответствии с СНиП 2.01.02-85 в зданиях II степени огнестойкости колонны должны иметь предел огнестойкости не менее 0,75 ч, что для цехов черной металлургии невыполнимо. Применение железобетонных колонн исключается из-за наличия мостовых кранов, создающих значительные нагрузки, а нанесение на металлические колонны огнезащитных покрытий дорого и практически невыполнимо из-за больших площадей цехов. Поэтому нормативными документами разрешено при определении категорий пожарной опасности цехов черной металлургии не включать площади пожароопасных подвальных помещений в состав общей площади цеха при условии выполнения следующих мероприятий:
•перекрытия над подвалом, включая его несущие конструкции, должно иметь предел огнестойкости не менее 2,5 ч;
•все пожароопасные помещения в подвале должны быть оборудованы установками автоматического тушения пожаров;
•в подвалах и туннелях перед лестницами, ведущими в помещения категории Г и Д первого этажа, следует предусматривать тамбур-шлюзы;
•противодымная вытяжная вентиляция из подвальных помещений должна иметь выбросы непосредственно наружу или через отдельные шахты,
имеющие предел огнестойкости не менее 1 ч.
При выполнении данных условий все основные цеха (доменные, сталеплавильные, прокатные и др.) относятся к категории Г. Однако по
пожароопасным свойствам применяемых в помещениях веществ и материалов некоторые помещения могут иметь и более высокую категорию. Например, к категории А в черной металлургии относят станции получения защитного газа и ацетилена, компрессорные горючих газов, газоповысительные, газорегуляторные, газораспределительные пункты, установки термической обработки в среде взрывоопасного защитного газа, отделения восстановительного отжига металлических порошков в среде взрывоопасного газа-восстановителя и др. К категории Б в черной металлургии относятся производства, где применяются и образуются горючие пыли: отделение дробления угля, подземные углеприемные ямы, закрытые галереи для транспортировки угля, установки подачи ПУТ в печь, отделения приготовления экзотермических смесей, склады сажи, дробильные цехи руды с содержанием серы более 12% и др. К категории В в черной металлургии относятся помещения, где применяют или хранят горючие вещества: склады мазута, масел, маслоподвалы, станции централизованной смазки, помещения масляных трансформаторов, маслоохладительные установки, маслотуннели, склады угля, бункерные эстакады с подбункерными помещениями доменных печей, отделения приготовления шихты, электрокабельные и электромашинные помещения и др. К категории Д в черной металлургии относятся склады руды (с содержанием серы до 12%), цехи мокрого обогащения руд, водонасосные, насосные грануляции шлака, цехи холодной обработки металла (кроме магния и титана), копровые цехи и др. Для устранения причин пожаров и взрывов в черной металлургии проводятся технические, эксплуатационные, организационные и режимные мероприятия (раздел 3.3).
Пожарная опасность доменного производства характеризуется наличием горючих газов (коксового, доменного, природного), горючих жидкостей, кокса, а также применением пылеугольного топлива (ПУТ) для вдувания в горн доменной печи. Определенную опасность представляет наличие жидкого чугуна и шлака. Во избежание образования взрывоопасных смесей в межконусном пространстве загрузочного устройства в него должен подаваться пар или инертный газ. Подача пара или инертного газа в межконусное пространство должна быть сблокирована с загрузочным устройством так, чтобы без подачи пара (газа) в межконусное пространство механизмы загрузки не работали. Помещение, в котором расположена распределительная установка для вдувания ПУТ, должно иметь естественную и принудительную вентиляцию. Распределительная установка и пылепроводы должны быть оборудованы подводом инертного газа. Расходные емкости для ПУТ закрытого типа должны быть оборудованы предохранительными клапанами. Воздухонагреватели доменных печей должны быть оборудованы приборами контроля температуры кожуха в купольной и подкупольной частях. При нагреве кожуха до температуры выше 150оС немедленно должны быть приняты меры по устранению причин, приведших к его перегреву. На газопроводах воздухонагревателей ближе к горелкам должны устанавливаться автоматические быстродействующие
клапаны безопасности, срабатывающие при падении газа или воздуха ниже установленных пределов. Клапаны должны быть сблокированы с сигнализаторами падения давления газа и воздуха. Сигнализаторы должны быть звуковые и световые. При нагреве воздухопроводов горячего дутья до температуры выше 200оС немедленно должны быть приняты меры по устранению причин, приведших к их перегреву. В течение всего режима горения должен осуществляться контроль за наличием пламени в камере горения. В случае отрыва или затухания пламени подача газа должна быть немедленно прекращена. Температура ПУТ в верхней части бункера должна контролироваться контрольно-измерительными приборами с подачей звукового и светового сигналов при самовозгоравнии пыли в бункере. Вдувание ПУТ и мазута в доменную печь при неисправной отсекающей и запорной арматуре и неисправных контрольно-измерительных приборах запрещается. Доменные печи должны быть оборудованы приборами контроля температуры кожуха по всей высоте печи, показания которых должны быть выведены на пульт управления печью. Для контроля за прогаром воздушных фурм они должны быть оборудованы сигнализирующими устройствами. Работа на прогоревших фурменных приборах запрещается.
Пожарная опасность сталеплавильного производства характеризуется наличием большого количества жидкого металла, а также наличием горючих отходящих газов, кабельных коммуникаций, маслоподвалов и маслотуннелей. В сталеплавильных цехах могут происходить взрывы и выбросы жидкого металла в результате загрузки в сталеплавильные печи и конвертеры влажного металлолома и шихты. Загрузка металлолома, например, в конвертеры осуществляется одной или двумя порциями (совками) и сразу после этого производится заливка чугуна. После заливки чугуна вся масса металлолома оказывается под жидким чугуном, в результате чего происходит интенсивное испарение влаги и выброс расплавленного металла. Выбросы жидкого металла могут происходить также и в том случае, когда в жидкий металл вводят влажные раскислители и легирующие материалы. При прогаре футеровок сталеплавильных агрегатов и фурменных аппаратов также возникает вероятность взрыва с выбросом жидкого металла при контакте расплавленного металла с влажными материалами. При выбросе расплавленный металл может быть источником воспламенения горючих материалов и способствует снижению несущей способности конструкций здания цеха. Несмотря на то, что нормативными документами в зданиях IIIа степени огнестойкости допускается применение незащищенных металлических колонн, на объектах черной металлургии в местах возможного пролива (выброса) жидкого металла целесообразно производить защиту несущих металлических колонн на высоту 1,5 – 2,0 м от уровня пола. Защиту колонн целесообразно выполнять огнеупорным кирпичом или бетоном. Предел огнестойкости защищенной колонны должен быть 2 – 2,5 ч. Также нижняя часть здания сталеплавильного цеха должна быть выполнена из железобетонных панелей. Для обеспечения пожарной
безопасности кабельного хозяйства необходимо, в первую очередь, предусмотреть мероприятия, исключающие возможность попадания жидкого металла в кабельные и масляные подвалы и туннели, так как это неизбежно вызовет пожар, а, следовательно, и остановку всего производства. Кроме этого, для обеспечения пожарной безопасности кабельных коммуникаций, маслоподвалов и маслотуннелей применяют технические, эксплуатационные, организационные и режимные мероприятия (раздел 3.3). При проектировании сталеплавильных цехов необходимо уделять внимание взрывоопасным помещениям. Так, газоочистки технологических газов мартеновских, электросталеплавильных печей и конверторов расположены в помещениях, относящихся к категории А в соответствии с ОНТП 24-86. Поэтому в них необходимо соблюдать все требования по обеспечению пожарной и взрывной безопасности, предусмотренные для взрывоопасных помещений (раздел 3.3). Следует отметить, что в электросталеплавильном производстве значительную пожарную опасность представляют печные масляные трансформаторы, которые располагают вблизи печей для того, чтобы кабельная линия от низкой стороны трансформатора до головки электродержателя была короткой. При этом кабели или гибкие ленты токопроводов защищают от действия прямого теплового излучения, например, применением асбестовых щитов, или даже применением водоохлаждаемых токопроводов. Наиболее опасными местами токопроводов являются контакты. Поэтому для снижения контактного переходного сопротивления эти соединения следует выполнять с помощью сварки. В качестве профилактических мероприятий в трансформаторных камерах необходимо предусматривать стационарные установки тушения пожара и автоматическую пожарную сигнализацию. Пожаротушение устраивают не автоматического действия (из-за возможных ложных срабатываний, которые могут вызвать короткое замыкание на проходящих в камере голых шинопроводах). Установка пожаротушения имеет ручной дистанционный пуск. Пожарная сигнализация выдает сигнал на пульт управления печью и, как правило, в пожарное депо.
Пожарная и взрывная опасность прокатного производства на предприятиях черной металлургии определяется следующими факторами:
•наличием широко развитой сети кабельного хозяйства;
•наличием большого количества масла в маслоподвалах. В них находятся резервуары для хранения масел, станции подачи технологической смазки (их производительность на крупных станах достигает 1200 л/мин и более), насосно-аккумуляторные станции для гидроприводов стана, станции густой смазки и другие агрегаты маслохозяйства;
•наличием сети масляных гидроприводов, в которых постоянно поддерживается избыточное давление масла около 20 МПа, обратных маслопроводов, а также машин для промасливания прокатанной полосы перед сматыванием ее в рулон;
•применением горючих (взрывоопасных) газов в нагревательных печах и колодцах, при резке металла. Кроме того, взрывоопасный водород образуется в травильных ваннах при обработке металла;
•применением взрывоопасного защитного газа (водородно-азотной смеси) при отжиге металла в безокислительной среде. Для приготовления защитного газа вблизи прокатного стана работает станция защитного газа, помещения которой взрывоопасны;
•применением огнеопасных лаков, красок и других горючих покрытий и огнеопасных растворителей при создании антикоррозионных, влагостойких, теплозащитных, декоративных и других покрытий на изделиях готового проката;
•наличием нагретого металла на станах горячей прокатки.
Сучетом больших площадей прокатных и трубных цехов особое внимание при проектировании должно уделяться мероприятиям по обеспечению безопасной эксплуатации людей в случае пожара. При размещении вспомогательных помещений в этих цехах выходы из них должны предусматриваться непосредственно в цех, а не через какие-либо рядом расположенные другие помещения (т.к. согласно СНиП 2.01.02-85 предусматривать выхода для эвакуации через два соседних помещения не допускается). При этом в число эвакуационных выходов не допускается учитывать ворота, предназначенные для въезда железнодорожного транспорта. Учитывают только специальные калитки, расположенные рядом с этими воротами. Мастерские ревизии подшипников относят к категории Б и классу зоны В-Iа. Постоянное наличие в мастерской ЛВЖ и горючих жидкостей предъявляет повышенные требования по обеспечению пожарной
безопасности, изложенные в разделе 3.3. В помещении мастерской допускается наличие не более 30 м3 керосина. При этом все резервуары с керосином должны быть оборудованы несгораемыми крышками и аварийным резервуаром для слива жидкости в случае пожара. Мастерские
ревизии подшипников, а также установки для промывки подшипников в керосине площадью 500 м2 и более должны оборудоваться автоматическими установками пожаротушения. При меньшей площади мастерских они должны оборудоваться автоматической пожарной сигнализацией. Пожарную опасность в прокатных и трубных цехах представляют термические печи. В качестве защитного газа в ряде случаев в них применяется водородно-азотная смесь (95% водорода и 5% азота). Помещения цехов, в которых расположены печи, работающие с использованием водорода, должны быть оборудованы автоматическими газосигнализаторами с устройством световой и звуковой сигнализации. Эти печи должны быть герметичными. Затворы колпаковых печей должны исключать возможность выхода водорода наружу и подсоса воздуха в рабочее пространство печи. Печь должна быть оборудована прибором, измеряющим расход водорода. При падении давления под муфелем или под колпаком (для вакуумно-водородных печей) должна автоматически прекращаться подача водорода и включаться продувка инертным газом. При этом должна срабатывать звуковая и световая
сигнализация. Наличие большого количества масла на прокатных станах вызывает необходимость установки в непосредственной близости от станов стационарных или передвижных воздушно-пенных огнетушителей. Однако в настоящее время все большее распространение получает оборудование прокатных станов стационарными установками пожаротушения (пенными или углекислотными) с ручным и дистанционным включением. Данный вид противопожарной защиты является наиболее эффективным и предпочтительным. Внутренний противопожарный водопровод в помещениях прокатных и трубных цехов следует предусматривать в соответствии с требовании СНиП 2.04.01-85 «Внутренний водопровод и канализация зданий».
ПЕРЕЧЕНЬ РЕКОМЕНДОВАННОЙ ЛИТЕРАТУРЫ
по курсу «ОХРАНА ТРУДА В ОТРАСЛИ»
1.Протоєрейський О. С, Запорожець О. І. Охорона праці в галузі: Навч. посіб. – К.: Книжкове вид-во НАУ, 2005. – 268 с.
2.Русаловський А. В. Правові та організаційні питання охорони праці: Навч. посіб. – 4-те вид., допов. і перероб. – К.: Університет «Україна»,
2009. – 295 с.
3.Третьяков О.В., Зацарний В.В., Безсонний В.Л. Охорона праці: Навчальний посібник з тестовим комплексом на CD/ за ред. К.Н. Ткачука. – К.: Знання, 2010. – 167 с. + компакт-диск.
4.Гогіташвілі Г. Г., Карчевські Є.-Т., Лапін В. М. Управління охороною праці та ризиком за міжнародними стандартами: Навч. посіб. – К.:
Знання, 2007. – 367 с.
5.Катренко Л.А., Кіт Ю.В., Пістун І. П. Охорона праці. Курс лекцій. Практикум: Навч. посіб. – Суми: Університетська книга, 2009. – 540 с.
6.Охрана труда и жизнедеятельности /В.И. Николин, В.И. Крот, В.В. Зубков, В.А. Темнохуд – Донецк: ДонГТУ, 2000. – 334 с.