

Рис. 15.28. График рейсов и кривая проходки
откладываются порядковые номера рейсов, а на оси ординат – значения глубины забоя скважины. Линия, соединяющая координаты полученных точек, называется кривой проходки. Фактиче- ская кривая проходки 1, построенная по промысловым данным, представляет собой ломаную линию.
В теоретических расчетах пользуются корреляционными зависимостями, полученными путем подбора эмпирических формул. В результате рассмотрения статистических данных, полученных при бурении глубоких скважин в различных геологических районах, установлено, что кривые проходки с достаточной точностью описываются формулой
Lz = Azm,
ãäå À è ò – опытные коэффициенты.
Значения опытных коэффициентов выбирают из условия равенства сумм глубин забоя скважины за все рейсы по фактической 1 и теоретиче- ской 2 кривым проходки (см. рис. 15.28).
Коэффициенты À è ò имеют значения: À > 1; 0 < m ≤ 1. Ïðè ò = 1 кривая проходки выражается линейной зависимостью, а объем спускоподъемных операций минимален. Уменьшение коэффициента ò указывает на возрастание объема спускоподъемных операций.
Пользуясь приведенной выше формулой и опытными значениями коэффициентов À è ò, можно определить:
ожидаемый объем спускоподъемных операций при бурении скважины заданной глубины
sñïî = 2s = 2Lê zê(ò + 1);
проходку на долото за z-é ðåéñ
hz = Lz – Lz–1 = Azm – A(z – 1)m = A[zm – (z – 1)m];
число рейсов за период бурения скважины до конечной глубины
zê = (Lê/À)1/ò;
среднюю проходку на долото
hñð = Lê/zê = À1/ò/ L(1ê−m)/ m .
535

15.13. КИНЕМАТИКА ПОДЪЕМНОГО МЕХАНИЗМА
Задача кинематики состоит в определении скоростей и ускорений подъемного механизма. Заданными величинами являются высота подъема, оснастка и размеры звеньев подъемного механизма, частота вращения и характеристика используемого двигателя.
При спускоподъемных операциях высота подъема h несколько превышает длину бурильной свечи l (здесь h ≈ 1,02l). Это обусловлено возможностью установки бурильной колонны на клинья либо элеватор. При спуске бурильная колонна приподнимается для освобождения клиньев либо элеватора, поэтому перемещения при спусках и подъемах бурильных свечей примерно одинаковые.
Изменения скорости за время подъема и спуска одной свечи изображаются тахограммой. Для подъемных механизмов характерна трехпериодная тахограмма подъема, имеющая трапецеидальную форму (рис. 15.29). В первый период происходит разгон барабана лебедки, чему соответствует ускоренное движение крюка со скоростью, возрастающей от нуля до на- чальной установившейся ví.ó. Характер изменения скорости крюка в период разгона зависит от привода лебедки и навыков управляющего ею бурильщика. Режим разгона буровой лебедки существенно не влияет на продолжительность подъема. Однако для снижения динамических нагрузок ускорение при разгоне должно быть минимальным. При линейном нарастании скорости, как показано на рис. 15.29, имеем
à |
= dv|dt = tg γ = const; v |
= a t ; h |
= v t |
= a t 2 |
/2, |
1 |
í.ó |
1 1 1 |
í.ó 1 |
1 1 |
|
ãäå à1 – ускорение крюка при разгоне, м/с2; γ – угол наклона кривой скорости; ví.ó – начальная установившаяся скорость крюка, м/с; h1 – путь крюка в период разгона, м; t1 – продолжительность разгона, с.
Второй период соответствует установившемуся движению крюка, при котором двигатель и барабан лебедки вращаются с постоянной частотой. Скорость подъема и период установившегося движения
vó = π Dz näâ/60 iòð iò.ñ,
ãäå Dz – диаметр навивки каната на барабан лебедки, м; iòð – передаточ- ное число трансмиссии лебедки; iò.ñ – кратность оснастки подъемного механизма.
Рис. 15.29. Тахограмма подъема
536
Вследствие изменения диаметра навивки при переходе каната на каждый последующий слой на тахограмме скорость подъема в период установившегося движения изображается ступенчатой прямой линией. В кинематических расчетах пользуются средней установившейся скоростью подъема
vñ.ó = (ví.ó + vê.ó)/2,
ãäå vê.ó – конечная установившаяся скорость подъема крюка, определяемая по диаметру последнего (конечного) слоя навивки каната.
Средняя установившаяся скорость подъема рассчитывается также по среднему диаметру навивки каната на барабан лебедки
vñ.ó = π Dñð näâ/60 iòð iò.ñ.
Исходя из средней установившейся скорости, для второго периода подъема
a2 = 0; vñ.ó = const; h2 = vñ.ó t2,
ãäå à2 – ускорение крюка, м/с2; t2 – продолжительность установившегося движения, с; h2 – путь крюка за период установившегося движения, м.
В третий период происходит торможение буровой лебедки, при котором конечная установившаяся скорость подъема снижается до нуля. При линейном изменении скорости торможения
a |
= const; v |
= a t ; h |
= v t /2 = a |
t2 |
/2, |
|
3 |
ê.ó |
3 3 3 |
ê.ó 3 |
3 |
3 |
|
ãäå à3 – замедление крюка при торможении, м/с2; vê.ó – скорость крюка в начале торможения, м/с; t3 – продолжительность торможения, с; h3 – путь крюка в период торможения, м.
Продолжительность подъема t = t1 + t2 + t3.
Для расчета продолжительности подъема на заданную высоту пользуются средней скоростью подъема, учитывающей изменение скорости крюка в период разгона и торможения лебедки:
t = h/vñð.
Средняя скорость на тахограмме подъема определяется из следующего равенства:
vñð t = vñ.ó(t + t2)/2, откуда
vñð = vñ.ó |
t +t2 |
= vñ.ó |
t +t −(t1 +t3 ) |
= vñ.ó 1− |
t1 |
+ t3 |
. |
2t |
2t |
|
2t |
||||
|
|
|
|
Последняя формула показывает, что средняя скорость крюка меньше средней установившейся скорости подъема. На рис. 15.29 средняя скорость крюка выражается высотой прямоугольной тахограммы, площадь которой равна площади действительной трапецеидальной тахограммы, имеющей общее с ней основание. Прямоугольная тахограмма является расчетной и на практике неосуществима, так как при этом ускорение и замедление достигают бесконечности: à = tg 90° = ∞.
Отношение средней установившейся скорости к средней скорости крюка называют коэффициентом заполнения тахограммы: λ = vñ.ó/vñð > 1.
537

Пользуясь коэффициентом λ, продолжительность подъема на заданную высоту можно определять по формуле
t = h/vñð = h λ/vñ.ó.
Коэффициент заполнения тахограммы зависит от типа привода подъемного механизма, скорости и высоты подъема крюка. Согласно опытным данным Уралмашзавода, указанная зависимость описывается формулой
v 2
λ =1+ñ ñh.ó .
В зависимости от типа используемого привода ñ = 2,4 – для электри- ческого, дизель-электрического и газотурбоэлектрического; ñ = 3,6 – для дизель-гидравлического и газотурбинного; ñ = 4,8 – для дизельмеханического.
Средняя скорость спуска
vñð.ñï = vmax ñï/λñï,
ãäå vmax ñï – максимальная скорость, достигаемая за период спуска; λñï – коэффициент заполнения тахограммы при спуске.
В практических расчетах согласно рекомендациям Уралмашзавода максимальная скорость спуска принимается в зависимости от длины све- чи l.
l, ì................. |
18 |
24 |
27 |
36 |
vmaõ, ì/ñ ....... |
2,5 |
2,9 |
3,1 |
3,6 |
Коэффициенты заполнения тахограммы: λñï = 2 – при свободном спуске; λñï = 1,5 – при использовании вспомогательного тормоза.
15.14. ДИНАМИКА ПОДЪЕМНОГО МЕХАНИЗМА
Динамические нагрузки в подъемном механизме буровых установок возникают при спускоподъемных операциях вследствие действия ускорения или замедления, а также упругих колебаний, создаваемых во время переходных процессов. Источники динамических нагрузок – толчки и удары, возникающие при подхвате колонны труб и переходах талевого каната на последующий слой навивки, а также из-за зазоров и монтажных смещений в сочленениях узлов и деталей подъемного механизма и его привода.
На динамику спускоподъемных операций значительно влияет состояние ствола скважины. Всевозможные уступы и каверны препятствуют равномерному движению колонны труб в скважине, поэтому в подъемном механизме возникают динамические нагрузки случайного характера. Систематическими являются динамические нагрузки, возникающие в период разгона и торможения лебедки. При прочих одинаковых условиях уровень динамических нагрузок, возникающих в процессе подъема, зависит от пусковых свойств двигателей и упругости системы, включающей силовые передачи, лебедку, талевый канат, вышку и колонну поднимаемых труб.
При спуске динамические нагрузки зависят от снижения скорости, регулируемой вспомогательным и основным тормозами лебедки, а также от упругости талевого каната, вышки и колонны спускаемых труб. Различие в
538
|
|
Ò à á ë è ö à 15.15 |
|
|
|
|
|
Нагрузка на крюке, кН |
Скорость подъема крюка, м/с |
Коэффициент динамичности |
|
Kä |
|||
|
|
||
150–250 |
1,32 |
2,00–1,88 |
|
250–700 |
1,12–0,99 |
1,88–1,43 |
|
700–1200 |
0,58–0,56 |
1,43–1,22 |
|
1200–1800 |
0,40–0,38 |
1,22–1,05 |
|
1800–2000 |
0,17–0,16 |
1,05–1,03 |
|
|
|
|
источниках и характере переходных процессов, распределении масс и упругости включаемых систем обусловливает количественные и качественные отличия динамических процессов, наблюдаемых в подъемном механизме буровых установок при подъеме и спуске колонны труб.
Опытный коэффициент динамичности учитывает динамические нагрузки в подземном механизме буровых установок
Kä = (Ðñò + Ðä)/Ðñò,
ãäå Ðñò – статическая нагрузка от собственного веса колонны труб и подвижной части талевого механизма; Ðä – динамическая нагрузка.
В результате экспериментальных исследований установлено, что коэффициент динамичности для отдельных звеньев и деталей подъемного механизма буровых установок изменяется от 1,02 до 2 в зависимости от скорости подъема, определяемой мощностью привода буровой лебедки и массой поднимаемой колонны. По мере увеличения массы колонны труб скорость подъема уменьшается и при этом снижается коэффициент динамич- ности.
Динамические нагрузки в звеньях подъемного механизма достигают наибольших значений в период подхвата колонны труб с ротора при подъеме и в начале торможения лебедки при спуске. В табл. 15.15 приведены коэффициенты динамичности для неподвижной ветви талевого каната, полученные по результатам инструментальных измерений на буровой установке Уралмаш.
16 |
ОБОРУДОВАНИЕ СИСТЕМЫ |
ГЛАВА |
ПРОМЫВКИ СКВАЖИН |
16.1. БУРОВЫЕ НАСОСЫ
В системе промывки скважин буровые насосы предназначены для следующего: нагнетания в скважину промывочной жидкости с целью очистки забоя и ствола от выбуренной породы (шлама) и выноса ее на дневную поверхность; охлаждения и смазки долота; создания гидромониторного эффекта при бурении долотами с насадками; приведения в действие забойных гидравлических двигателей.
К буровым насосам предъявляют следующие основные требования: подача бурового промывочного раствора должна быть регулируемой в
пределах, обеспечивающих эффективную промывку скважины;
539
мощность насоса должна быть достаточной для промывки скважины и привода забойных гидравлических двигателей;
скорость промывочной жидкости на выходе из насоса должна быть равномерной для устранения инерционных нагрузок и пульсаций давления, вызывающих осложнения в бурении, дополнительные энергетические затраты и усталостные разрушения;
насосы должны быть приспособлены для работы с абразиво- и маслосодержащими коррозионно-активными промывочными растворами различ- ной плотности;
узлы и детали, контактирующие с промывочным раствором, должны обладать достаточной долговечностью и быть приспособленными к удобной и быстрой замене при выходе из строя;
крупногабаритные узлы и детали должны быть снабжены устройствами для надежного захвата и перемещения при ремонте и техническом обслуживании;
узлы и детали приводной части должны быть защищены от промывоч- ного раствора и доступны для осмотра и технического обслуживания;
насосы должны быть приспособлены к транспортировке в собранном виде на далекие и близкие расстояния и к перемещению волоком в пределах буровой;
конструкция насосов должна допускать правое и левое расположение двигателей насосного агрегата;
надежность и долговечность насосов должны сочетаться с их экономичностью и безопасностью эксплуатации.
Технические условия на изготовление буровых насосов регламентируются ГОСТом.
С ростом глубины бурения значительно увеличиваются и мощности буровых насосов. Освоены и намечаются к производству новые модели буровых насосов, отвечающие возросшим требованиям бурения. Буровые насосы непрерывно совершенствуются: повышаются надежность и долговеч- ность, снижается масса и сокращаются материальные и трудовые затраты на их изготовление, эксплуатацию и ремонт. Это обусловило широкую номенклатуру моделей и модификаций буровых насосов, используемых в отечественной и зарубежной практике бурения эксплуатационных и разведочных скважин.
Рабочие органы буровых насосов преимущественно выполняются в виде поршней. Наиболее распространены двухпоршневые насосы двустороннего действия, на смену которым в последние годы приходят трехпоршневые насосы одностороннего действия. В насосах двустороннего действия жидкость перемещается в поршневой и штоковой полостях и за один двойной ход поршня совершаются два цикла всасывания и нагнетания. При одностороннем действии жидкость перемещается в поршневой полости рабочей камеры и за один двойной ход совершается один цикл всасывания и нагнетания.
В буровых насосах используются самодействующие пружинные клапаны тарельчатой конструкции. Всасывающие и нагнетательные клапаны взаимозаменяемы. Оси поршней параллельны и располагаются в горизонтальной плоскости по одну сторону от привода насоса. Ведущее звено буровых насосов, сообщающее движение поршням, выполняется в виде вращающегося эксцентрикового, кривошипного, пальцевого либо коленчатого вала.
540
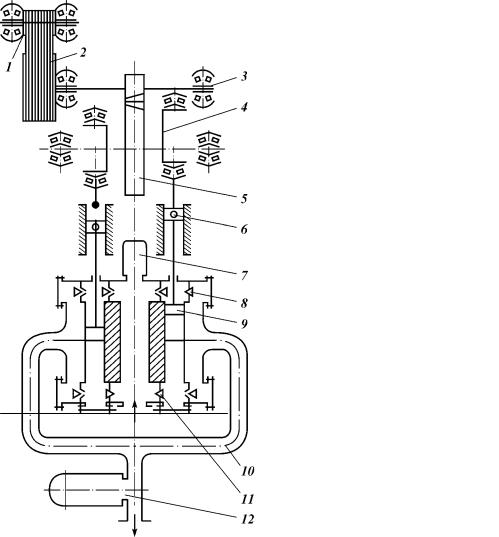
Ведущий вал приводится от трансмиссионного вала насоса посредством цилиндрической зубчатой пары. Промывочная жидкость перемещается по одноступенчатой и однопоточной схеме, через общую приемную линию
èодин отвод. Подача насоса изменяется с помощью сменных цилиндровых втулок либо изменением числа ходов насоса. Пульсации давления, вызываемые неравномерной скоростью поршней, снижаются до практически приемлемого уровня при помощи пневматических компенсаторов. В буровых насосных агрегатах используются преимущественно электродвигатели
èдизели, вращение которых передается трансмиссионному валу насоса
клиноременной либо цепной передачей.
ДВУХЦИЛИНДРОВЫЕ ПОРШНЕВЫЕ БУРОВЫЕ НАСОСЫ
Кинематическая схема бурового насоса двухстороннего действия приведена на рис. 16.1, а компоновка узлов – на рис 16.2. Эти буровые насосы горизонтальные, поршневые, двухцилиндровые, двойного действия, состоят из гидравлической и приводной частей, смонтированных на общей раме. Гидравлическая часть насоса У8-6М состоит из следующих основных узлов: двух литых стальных гидравлических коробок, соединенных между собой снизу приемной коробкой, а сверху корпусом блока пневмати- ческих компенсаторов. Приемная коробка насоса соединяет всасываемую трубу со всасывающими клапанами (рис. 16.3). Внутри гидравлических коробок устанавливают сменные цилиндровые втулки (рис. 16.4, 16.5), внутренний диаметр которых выбирают в зависимости от требуемого давления и подачи насоса. Наружные размеры всех втулок одинаковы.
Рис. 16.1. Кинематическая схема бурового насоса двухстороннего действия:
1 − приводной шкив двигателя; 2 − клиноременная передача; 3 − трансмиссионный вал; 4 − эксцентрик; 5 − зубчатая передача; 6 − ползун; 7 − всасывающий компенсатор; 8 − нагнетательный клапан; 9 − поршень; 10 − гидравлическая коробка; 11 − всасывающий клапан; 12 − компенсатор нагнетательного трубопровода
541

Рис. 16.2. Буровой насос двухстороннего действия:
1 − поршень; 2 − цилиндровая втулка; 3 − крышка цилиндра; 4 − упорный стакан; 5 − нагнетательный клапан; 6 − корпус клапанной коробки; 7 − надставка штока; 8 − øòîê; 9 − сальниковое уплотнение штока; 10 − корпус насоса; 11 − трансмиссионный вал; 12 − коренной вал; 13 – ведомая головка шатуна; 14 − шатун; 15 − ползун; 16 − направляющие ползуна
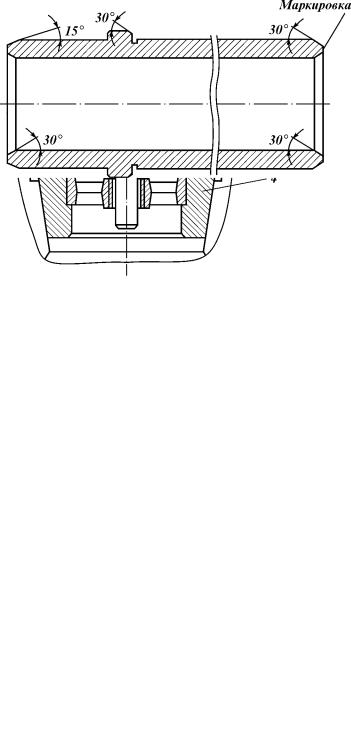
Рис. 16.3. Клапан насоса в сборе:
1 − втулка; 2 − пружина; 3 − тарелка клапана; 4 − седло в сборе
С целью повышения сроков службы втулок внутренняя поверхность их подвергается термической обработке. Цилиндровые втулки насоса уплотняются путем установки между буртиком цилиндровой втулки 1 и стаканом 4 двух комбинированных уплотнений 2, разделенных стальным кольцом 3 (см. рис. 16.5). Кольцо имеет по наружному и внутреннему диаметрам проточки с отверстиями. В случае износа уплотнения через специальное отверстие в гидравлической коробке раствор должен вытекать наружу, что и явится сигналом о неисправности уплотнения цилиндровой втулки. Цилиндровые втулки закрепляются с помощью стакана 5 и крышки 7 подтягиванием гаек 8. Цилиндровая крышка 7 уплотняется при помощи самоуплотняющихся манжет 6 è 9. Подтяжка уплотнения 2 цилиндровой втулки производится с помощью болта 10.
В цилиндровых втулках перемещаются поршни (рис. 16.6). Поршень состоит из сердечника с конической расточкой и привулканизированных к нему двух резиновых манжет. Поршень 13 насажен на конический хвостовик штока 14 и крепится к нему с помощью гайки 12 и контргайки 11 (см. рис. 16.5). Шток (рис. 16.7) соединен с надставкой штока (рис. 16.8), резь-
Рис. 16.4. Цилиндровая втулка насоса У8-6М
543

Рис. 16.5. Уплотнение цилиндровых втулок насоса У8-6М
Рис. 16.6. Поршень насоса:
1 − сердечник; 2 − уплотнение
Рис. 16.7. Шток поршня насоса
544