

Таблица 2.20
Характеристики спектра нагруженности трубопровода на выходе НПС
Время эксплуатации |
Январь − август |
Сентябрь − декабрь |
|
2000 г. |
2000 г. |
||
|
|||
∆t, лет |
0,67 |
0,33 |
|
pраб, МПа |
4,5 |
3,7 |
|
N 25 % |
9 |
4 |
|
N 50 % |
11 |
5 |
|
N 75 % |
5 |
1 |
|
N 100 % |
4 |
1 |
|
|
|
|
Спектр нагруженности удобно выразить в виде табл. 2.20. Здесь указаны следующие параметры: промежуток времени, для которого даны характеристики нагруженности; рабочее давление в этот промежуток времени; количество перепадов давления, где N25 % − количество перепадов давления, при котором снижение давления составляет от 0 до 25 %; N50 % − количество перепадов давления, при котором снижение давления составляет от 25 до 50 %; N75 % − количество перепадов от 50 до 75 % рабочего давления; N100 % − количество падений от 75 % до полного снятия давления.
Таким образом, основными параметрами нагруженности внутренним давлением являются: время ∆t, рабочее давле-
ние pраб, N25 %, N50 %, N75 %, N100 %.
Индексы N могут быть и другими в зависимости от выбранных диапазонов в шкале давления, например, N40 %, N60 %,
N80 %, N100 %.
Выше даны характеристики спектра нагруженности трубопровода на выходе НПС. Для оценки остаточного ресурса всего участка трубопровода необходимо располагать аналогичной характеристикой и для ряда других точек участка. В качестве таких точек следует выбрать начало, конец и наиболее низкие точки по рельефу. Можно выбрать также точки через каждые 5−10 км, включая начало и конец участка (выход из НПС и вход в следующую НПС). Все эти характеристики можно собрать по специальной методике, используя данные периодического опроса давления на всех НПС, поступающие в диспетчерские службы управлений, и раскладки соответствующих участков трубопровода. Затем давление в произвольной точке участка можно определять по формуле
p = p1 −(L − L1) p1−p 2 + γg(H1 − H),
L 2−L1
где p1, p2, p − давление соответственно в начале, конце и
98
произвольной точке участка; L1, L2, L − километровые отметки соответственно этих точек; Н1, Н2, Н − высотные отметки соответственно этих точек; γ − плотность перекачиваемой нефти; g = 9,8 м/ с2 − ускорение свободного падения.
Значения p1 и p2 регулярно поступают в диспетчерские службы; L1, L2, H1, H2 − фиксированные данные насосных станций в начале и конце участка; L, H − характеристики, известные из раскладки трубопровода.
Обработка значений p с целью получения характеристик спектра может производиться автоматически с помощью специальной программы.
Анализ нагруженности магистральных нефтепроводов практически не проводился (за исключением небольшого количества участков по нефтепроводу «Дружба»). Поэтому при оценке остаточного ресурса обычно считают, что в течение года может происходить до 356 перепадов до полного снятия давления, т. е. принимают N100 % = 356. При этом допускается значительный запас по долговечности.
До настоящего времени при проектировании нефтепровода и расчетном обосновании проектных параметров не учитывались возможные перепады давления из-за того, что в соответствующих нормативных документах (СНиП, ВСН, нормы проектирования) эти вопросы не нашли отражения.
2.7.2. ГИДРАВЛИЧЕСКИЕ ИСПЫТАНИЯ ТРУБОПРОВОДОВ
Магистральные нефтепроводы иногда подвергаются переиспытаниям высоким давлением с целью выявления опасных дефектов. До 1990 г. переиспытания проводили в обязательном порядке с определенной периодичностью. С внедрением метода диагностирования с применением внутритрубных дефектоскопов интерес к переиспытаниям значительно ослаб. Даже существует мнение, что переиспытания вредны для трубопровода, и поэтому от них надо отказаться.
Однако такой вывод делать преждевременно, так как внутритрубная диагностика представляет собой неуниверсальный метод диагностики, хотя и очень эффективный. Есть много других методов, которые в определенных условиях становятся более эффективными и даже незаменимыми.
Одним из таких случаев, например, являются трубопроводы, построенные с применением подкладных колец при сварке стыков. Только по Урало-Сибирским магистральным неф-
99
тепроводам протяженность таких трубопроводов более 2000 км [45]. В процессе очистки перед пропуском внутритрубных дефектоскопов эти кольца отрываются и становятся препятствием при пропуске снарядов. Кроме того, при отрыве подкладных колец поперечные сварные стыки получают повреждения. Поэтому в данном случае потребуется использование других методов диагностики, одним из которых и является переиспытание на прочность и герметичность.
Другой случай. Как было отмечено ранее, современная система магистральных нефтепроводов России может обеспечивать объем перекачки до 600 млн т нефти в год. Фактически объем перекачки не превышает 300 млн т. Поэтому значительная часть трубопроводов простаивает из-за отсутствия грузопотоков. Только по Уралосибирским магистральным нефтепроводам протяженность таких трубопроводов составляет около 20 % [45]. Когда нет потока нефти (или другой жидкости) пропуск внутритрубных дефектоскопов создает большие сложности. В таких случаях метод переиспытания в сочетании с другими методами контроля (например, акустическая эмиссия) может стать решением проблемы диагностики.
Таким образом, несмотря на значительные успехи внутритрубной диагностики, остаются участки трубопроводов, не приспособленные для пропуска внутритрубных дефектоскопов. Пока существуют такие участки, не следует отвергать метод периодических гидроиспытаний для выявления и ликвидации опасных дефектов. При этом важное значение имеет выбор режима переиспытаний и оптимальных параметров испытаний.
В разные периоды времени применяли различные режимы испытаний трубопроводов [29]. Но во всех случаях трубопровод испытывают в два этапа: испытания на прочность и испытания на герметичность. Испытания на герметичность проводят при рабочем давлении pраб. Испытания на прочность характеризуются тремя основными параметрами: испытательное давление pисп, количество циклов нагружения при испытании Nисп, время пребывания при испытательном давлении
τиспВ. табл. 2.21 приведены параметры испытаний трубопроводов, применяемые в разные годы [29].
На взгляд авторов, наиболее правильным был режим испытаний, принятый в 1940−1950 гг. В последующие годы испытательное давление снижалось. Это снижение компенсировалось увеличением времени выдержки под давлением.
100
Таблица 2.21
Параметры испытательного давления трубопроводов
Нормативный документ |
Испытательное |
Продолжи- |
|
Срок действия, |
||||
|
|
|
|
давление pисп |
тельность, ч |
|
годы |
|
Инструкция |
по |
сварке и |
|
|
|
|
1940−1950 |
|
укладке стальных трубо- |
1,5pраб |
2 |
|
|||||
проводов, |
Центроспец- |
|
|
|
|
|
||
строй, |
1940 |
|
|
(1,16−1,22)pраб |
|
|
1951−1955 |
|
ГОСТ 5870–51 |
|
3/4 |
|
|||||
ТУ 121–56 |
|
|
1,25pраб |
2 |
|
1956−1959 |
||
СН 83–60 |
|
|
1,1pраб |
6 |
|
1960−1963 |
||
СНиП |
III-Д10–62 |
1,1pраб |
6 |
|
1964−1972 |
|||
СНиП |
III-Д10–72 |
1,1pраб |
6 |
|
1973−1980 |
|||
СНиП |
III-42–80 |
|
1,1pраб |
− pзав |
24 |
|
1981−1996 |
|
СНиП |
III-42–80* |
|
1,1pраб |
− pзав |
24 |
|
1997 − по |
|
|
|
|
|
|
|
|
настоящее время |
|
Примечание. |
pраб − рабочее давление (для новых трубопроводов равно |
|||||||
проектному давлению, для длительно эксплуатируемых |
− |
разрешенному |
||||||
давлению); pзав − |
заводское испытательное давление труб. |
|
|
|||||
|
|
|
|
|
|
|
|
|
Существующие в настоящее время режимы испытаний имеют следующие недостатки.
Рекомендуемое значение нижнего предела испытательного давления 1,1pраб недостаточно, чтобы проверить безопасность нефтепровода, так как при переходных режимах (включая гидроудары) напряжение может повыситься на 20 % рабочего. Поэтому нижний уровень давления при испытаниях должно составлять не меньше 1,25pраб.
Верхний уровень давления при испытаниях трубопровода не должен достигать заводского испытательного давления pзав. Завод испытывает трубы под этим давлением в течении всего 20 с, а на трубопроводе время выдержки достигает 24 ч. Испытывая под давлением pзав в течении более 20 с, фактически выходят за ту область, где распространяются гарантии завода. Иными словами, трубы не рассчитаны на испытания под давлением pзав в течение более 20 с. Поэтому верхний предел испытательного давления трубопроводов не должен превышать 0,95pзав.
При экспертизе безопасности длительно эксплуатируемых магистральных нефтепроводов понятие «проектное давление» не должно быть определяющим. Проектное давление является основным и определяющим параметром для этапов проектирования и строительства трубопроводов. При длительной эксплуатации многие параметры изменяются (появляются дефекты, металл стареет). Основным параметром, определяющим безопасность нефтепроводов, должно быть допустимое давление pдоп. Поэтому рабочее давление не может быть
101
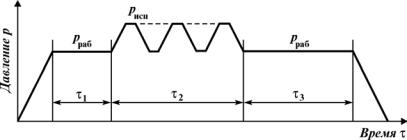
Рис. 2.20. Режим испытаний трубопровода согласно РД 39-30-859−83
выше допустимого давления, а испытательное давление трубопровода должно быть в пределах 1,25pдоп ÷ 0,95pзав. Значение pдоп должно быть рассчитано, исходя из технического состояния трубопровода.
Во многих случаях фактическое давление в трубопроводах значительно ниже проектного. С падением объемов перекачки нефти в некоторых направлениях встречаются случаи, когда рабочее давление на порядок меньше проектного. В таких случаях нет никакой необходимости выбирать высокие испытательные давления, тем более сопоставимые с заводским испытательным давлением.
На рис. 2.20 показан рекомендуемый режим испытаний в соответствии с документами [64, 72]. Испытания состоят из трех этапов.
Первый этап − заполнение участка трубопровода водой, подъем давления до рабочего уровня pраб, проверка системы, выдержка до стабилизации температуры воды в трубопроводе.
Второй этап − испытание на прочность. При этом давление поднимается до уровня pисп = 1,25pраб, выдерживается определенное время, затем опускается до рабочего давления pраб. Количество таких циклов Nисп = 3. Суммарное время пребывания трубопровода под испытательным повышенным давлением τисп = τ2 ≥ 24 ч. Цикличность давления повышает выявляемость дефектов.
Третий этап − выдержка под рабочим давлением в течение времени, достаточного для определения герметичности испытываемого участка, но не менее 12 ч. Герметичность контролируется по стабилизации показания манометра при отключенном насосе. Если имеется негерметичность, то давление в системе при отключенном насосе не стабилизируется.
102

Испытания трубопровода имеют как положительные, так и отрицательное стороны.
Положительно то, что при испытаниях наиболее опасные дефекты проявляются в виде разрывов. Те дефекты, которые не проявились при испытаниях, некоторое время не будут вызывать разрушения трубопровода.
Отрицательно то, что испытания являются наиболее тяжелым этапом «жизни» трубопровода, при котором скрытые повреждения продолжают накапливаться, а дефекты − расти. Рост этих дефектов подчиняется тем же законам малоциклового разрушения, что и при эксплуатации. Поэтому целесообразно режим испытаний выразить в виде параметров спектра нагружения.
Характеристики спектра нагруженности трубопровода |
||
при рабочем давлении |
4,5 МПа и испытаниях 15−16 мая 2000 г. |
|
|
(см. рис. 2.20) |
pисп = 5,63 МПа |
Давление ...................................................... |
pраб = 4,5 МПа |
|
N 20 %................................................................ |
0 |
3 |
N 100 % .............................................................. |
1 |
0 |
При испытаниях могут происходить разрушения трубопровода. На рис. 2.21 показан график изменения давления при одном разрушении в процессе испытаний. После разрушения необходимо выполнить ремонт − заменить дефектную трубу. Поэтому общее время испытаний увеличится. Но суммарное время пребывания трубопровода под испытательным повышенным давлением и количество циклов должно быть не меньше, чем при отсутствии разрушений. Время ремонта τрем должно включать суммарное время, необходимое для ликвидации повреждения и подъема давления до уровня рабочего.
Параметры спектра нагружения при испытании следующие:
Рис. 2.21. Режим испытаний, при которых происходит разрыв трубы
103
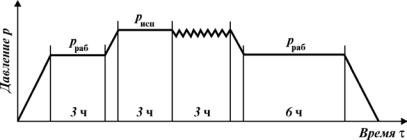
|
Рис . 2.22. Один из предлагаемых режимов испытаний |
|
|
Характеристики спектра нагруженности трубопровода |
|
|
при испытаниях 15 − 16 мая 2000 г. (см. рис. 2.21) |
|
Давление |
........................................................ pраб = 4,5 МПа |
pисп = 5,63 МПа |
N 20 %................................................................. |
0 |
2 |
N 100 % ............................................................... |
1 |
1 |
Спорным вопросом в режимах испытаний является то, что при каждом цикле перегрузки трубопровод получает повреждение. Три цикла перегрузки были введены с целью релаксировать напряжения в зонах концентрации напряжений и активизировать процесс релаксации. Это положительный момент, так как в зонах концентрации напряжений после снятия перегрузки напряжения становятся значительно меньше. Но вместе с этим за счет циклического воздействия перегрузки в этих же зонах металл ускоренно получает повреждение. Поэтому предлагается другой режим гидроиспытаний, показанный на рис. 2.22.
Смысл данного предложения состоит в том, что исключаются большие перепады давления при испытаниях и включается этап активизации релаксации напряжений за счет небольших колебаний давления.
Параметры спектра нагружения при испытаниях следующие.
|
Характеристики спектра нагруженности трубопровода |
|
|
при испытаниях 15 − 16 мая 2000 г. (см. рис. 2.22) |
|
Давление |
........................................................ pраб = 4,5 МПа |
pисп = 5,63 МПа |
N 5 % .................................................................. |
0 |
10 |
N 100 % ............................................................... |
1 |
0 |
Гидроиспытания трубопроводов могут преследовать следующие цели:
1. Приемочные испытания после строительства или капитального ремонта трубопровода. При этом испытания должны проводиться в соответствии с требованиями современных СНиП. За базовое давление принимается проектное давление.
104
2.Переиспытания с целью проверки безопасности трубопровода при выбранных режимах эксплуатации. За базовое давление принимается рабочее давление.
3.Испытания как метод диагностики. Допустимое давление заранее неизвестно, внутритрубная диагностика невозможна. Медленно повышается давление до наступления пер-
вого разрыва. Если это давление достаточно, то выполняется ремонт разрушенного участка, переиспытывается при том же давлении. При этом допустимое рабочее давление определяется по формуле pраб = pисп /1,5.
Кроме испытания участков действующих магистральных нефтепроводов имеется целое направление испытаний отдельных фрагментов и элементов трубопроводов, например:
сертификационные испытания демонтированных труб, соединительных деталей, трубной арматуры, ремонтных конструкций (для ремонта дефектных участков трубопроводов); поверочные испытания отбракованных и демонтированных дефектных катушек трубопроводов с целью определения их фактической прочности и остаточного ресурса и накопле-
ния информации об опасности различных дефектов; поверочные испытания устаревших элементов трубопро-
водов и соединительных деталей при экспертизе безопасности.
Все эти испытания в настоящее время широко применяются, так как некоторые расчетные методы нуждаются в экспериментальном подтверждении.
2.8. ДРУГИЕ ИСТОЧНИКИ ОПАСНОСТИ
Ранее были рассмотрены самые основные и общиедля всех магистральных нефтепроводов факторы, определяющие их безопасность.Наотдельных участках трубопроводов могут встретиться ситуации, когда безопасность определяется рядом дополнительных факторов. Рассмотрим несколько примеров.
1. Подводные переходы. Русла рек имеют склонность меняться с течением длительного времени. При этом на переходах трубопроводов через реки грунт иногда размывается изпод трубы. Это приводит к изменению сил, действующих на трубопровод, и появлению дополнительных механических напряжений в стенке трубопровода. Поэтому при оценке технического состояния и безопасности подводного перехода в первую очередь необходимо обследовать русловое положение реки на данном участке, выявить размытые участки, оп-
105
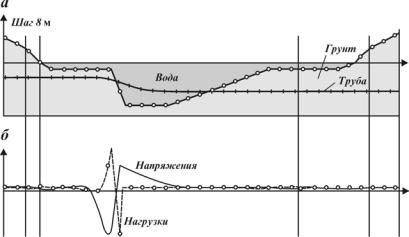
Рис. 2.23. Напряжения изгиба при размыве грунта на подводном переходе (указано положение верхней образующей трубопровода)
ределить дополнительные механические напряжения, оценить степень их опасности для трубопровода.
На рис. 2.23 показаны продольный профиль (а) подводного перехода и распределение осевых механических напряжений (б) в области размытого участка трубопровода. Диаметр трубы 720 мм, толщина стенки 10 мм, ширина реки 230 м, наибольшая глубина 3,7 м, верхняя образующая трубы переходит с глубины 1 м на глубину 2 м от поверхности трубы. Напряжение от изгиба в данном случае достигают 330 МПа, которого достаточно для образования гофра.
2. Опоры. На некоторых сильнопересеченных или горных участках трубопроводы прокладываются в наземном исполнении. При этом трубопровод устанавливается на специальные опоры. Но с течением времени опоры иногда получают повреждения по разным причинам, деформируются, нарушается контакт между опорой и трубопроводом. При этом напряжения в стенке трубопровода перераспределяются, некоторые участки оказываются перегруженными, создается опасность гофрообразования и разрушения трубопровода. На рис. 2.24 показаны некоторые такие случаи.
3. Концент рат оры напряжений. Трубопроводы имеют в своем составе задвижки, ответвления, приварные ремонтные муфты, заплаты, приварные крепежные детали, разнотол-
106

Рис. 2.24. Примеры дефектов опор:
а − растрескивание и разрушение; б − потеря контакта; в − смещение
щинные стыки и другие элементы. Все они объединяются тем, что создают концентрацию напряжений. На рис. 2.25 показана фотоупругая картина, соответствующая распределению напряжений в угловом сварном шве ремонтной муфты или накладной заплаты. На картине изохром (см. рис. 2.25, в) четко наблюдаются две зоны концентрации напряжений с вершинами в точках А и Б, которые могут стать очагами разрушения трубопровода
107