

6
ОЦЕНКА БЕЗОПАСНОСТИ ЭЛЕМЕНТОВ ТРУБОПРОВОДОВ ЭКСПЕРИМЕНТАЛЬНЫМИ МЕТОДАМИ
Представленные в настоящей работе методы расчета напряжений, прочности и ресурса, а также методы ремонта были проверены экспериментально под руководством и при непосредственном участии авторов. В организации и выполнении всех экспериментов также принимали участие Р.Г. Ишмуратов, М.С. Салихов, И.К. Гумеров и сотрудники ИПТЭР и СУПЛАВ ОАО «Уралсибнефтепровод».
6.1. ЭКСПЕРИМЕНТАЛЬНОЕ ОПРЕДЕЛЕНИЕ ОСТАТОЧНОГО РЕСУРСА МЕТАЛЛОВ И СВАРНЫХ ШВОВ МАГИСТРАЛЬНЫХ
НЕФТЕПРОВОДОВ
При длительной эксплуатации магистральных нефтепроводов происходит изменение механических свойств металла труб и сварных швов (см. разделы 2.1 и 2.4). Определить изменились ли эти свойства практически невозможно из-за того, что нет точной информации об этих свойствах в исходном состоянии труб. Существуют сертификаты на поставленные трубы. Но, как показывает анализ, имеется значительный разброс свойств в исходном состоянии. Например, в табл. 6.1−6.3 приведены результаты статистического анализа некоторых сертификатных данных труб нефтепроводов УБКУА и Александровское − Анжеро-Судженск (ААС).
Видно, что разброс сертификатных параметров труб сопоставим с изменениями механических свойств металла труб и сварных швов в результате длительной эксплуатации. Поэтому, случайно отобрав для испытаний катушки труб из
264
Таблица 6.1
Сертификатные значения механических характеристик труб нефтепровода УБКУА
|
|
|
|
|
|
|
|
|
|
|
Значение |
|
|
|
|
|
Характеристика |
|
|
наимень- |
|
наибольшее |
|
среднее |
|||||||
|
|
|
|
|
|
|
|
шее |
|
|
|
|
|
|
|
Ударная вязкость основного ме- |
|
|
3,8 |
8,6 |
|
5,93 |
|
|
|||||||
талла КСU, кгс м/ см2 |
|
|
|
|
|
|
|
|
|
|
|
||||
Предел прочности основного ме- |
|
|
55 |
61 |
|
57,36 |
|
|
|||||||
талла |
σв , кгс/ мм2 |
|
|
|
|
|
|
|
|
|
|
|
|||
Предел текучести основного ме- |
|
|
37,5 |
42,5 |
|
39,62 |
|
|
|||||||
талла |
σт , кгс/ мм2 |
δ, % |
|
|
|
|
|
|
|
|
|
|
|||
Относительное удлинение |
|
|
23 |
30 |
|
25,56 |
|
|
|||||||
Примечание. |
Трубы поставки Челябинского трубопрокатного завода |
||||||||||||||
(ЧТПЗ) по ТУ 14-3-109−73. Диаметр 1220 мм, толщина стенки 12−15 мм. |
|||||||||||||||
Сталь марки 17Г1С. Нормативные значения σв = |
|
510 МПа, σт = 353 МПа. |
|||||||||||||
|
|
|
|
|
|
|
|
|
|
|
|
|
|
||
|
|
|
|
|
Таблица 6.2 |
|
|
|
|
|
|
|
|||
|
Сертификатные значения механических характеристик труб |
|
|
||||||||||||
|
нефтепровода ААС (подводный переход через р. Обь) |
|
|
||||||||||||
|
|
|
|
|
|
|
|
|
|
|
|
|
|||
Статистиче- |
|
Предел |
Предел |
|
|
|
|
Относи- |
|
Ударная вяз- |
|||||
ские |
прочности |
|
Отношение |
тельное |
|
кость |
|
|
|||||||
текучести |
удлинене- |
|
о |
С), |
|||||||||||
характеристи- |
|
δв, |
δт, кгс/ мм |
2 |
σт/σв |
|
|
ние δ, |
|
КСU(−40 |
|
||||
|
ки |
|
кгс/ мм2 |
|
|
|
|
|
кгс м/ см2 |
||||||
|
|
|
|
|
|
|
|
|
|
|
% |
|
|
|
|
Математиче- |
|
58,1 |
|
41,7 |
|
|
0,718 |
|
|
26,3 |
|
7,52 |
|
|
|
ское |
ожида- |
|
|
|
|
|
|
|
|
|
|
|
|
|
|
ние |
|
|
|
|
|
|
|
|
|
|
|
|
|
|
|
Дисперсия |
|
2,66 |
|
2,01 |
|
|
0,00038 |
|
|
3,01 |
|
1,84 |
|
|
|
Максимум |
|
62 |
|
46 |
|
|
0,768 |
|
|
30 |
|
11,5 |
|
|
|
Минимум |
|
55 |
|
39 |
|
|
0,672 |
|
|
20 |
|
4,5 |
|
|
|
Мода (наибо- |
|
57 |
|
42 |
|
|
0,724 |
|
|
26 |
|
7,7 |
|
|
|
леечастое |
|
|
|
|
|
|
|
|
|
|
|
|
|
|
|
значение) |
|
|
|
|
|
|
|
|
|
|
|
|
|
|
|
Примечание. Трубы поставки фирмы «GRANGES», Швеция. Количест- |
|||||||||||||||
во поставки 274 трубы. Диаметр 1020 мм, толщина стенки 16 мм. Гаранти- |
|||||||||||||||
руются предел текучести наименьший 37 кгс/ мм2, предел прочности наи- |
|||||||||||||||
меньший 52 кгс/ мм2. |
|
|
|
|
|
|
|
|
|
|
|
||||
|
|
|
|
|
Таблица 6.3 |
|
|
|
|
|
|
|
|||
|
Прочностные свойства сварных швов труб нефтепровода ААС |
|
|
||||||||||||
|
|
|
(фирма «GRANGES», Швеция) |
|
|
|
|
||||||||
|
|
|
|
|
|
|
|
||||||||
Статистические |
|
Предел прочности δв, |
|
|
Ударная вязкость |
|
|
||||||||
характеристики |
|
кгс/ мм2 |
|
|
КСU(−40 оС), кгс м/ см2 |
||||||||||
Математическое |
ожи- |
|
60,0 |
|
|
|
6,0 |
|
|
||||||
дание |
|
|
|
|
|
|
|
|
|
|
|
|
|
|
|
Дисперсия |
|
|
|
2,60 |
|
0,92 |
|
|
|||||||
Максимум |
|
|
|
64 |
|
|
|
|
8,6 |
|
|
||||
Минимум |
|
|
|
57 |
|
|
|
|
3,2 |
|
|
||||
Мода |
|
|
|
|
59 |
|
|
|
|
6,8 |
|
|
|||
|
|
|
|
|
|
|
|
|
|
|
|
|
|
|
|
265
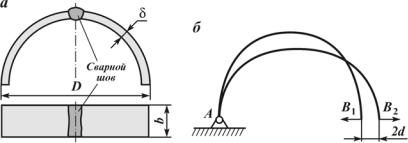
нефтепровода, можно в несколько раз ошибиться в определении степени старения металла труб и сварных швов.
В настоящее время методики оценки остаточного ресурса труб по результатам исследований механических свойств металла труб на стандартных образцах недостаточно разработаны. В связи с этим в данной работе сделана попытка разработать методику оценки остаточного ресурса труб на основе испытаний С-образных образцов, представляющих собой полукольца определенной ширины b, вырезанные из трубы диаметром D и толщиной стенки δ (рис. 6.1, а). Схема испытаний образцов на остаточный ресурс показан на рис. 6.1, б. Для этого использовали механизм, создающий возвратнопоступательное движение с регулируемой амплитудой. При испытаниях один конец полукольцевого образца (точка А) шарнирно закреплялся. Другой конец образца (точка В1 или В2) совершал колебательное движение в горизонтальном направлении с заданной амплитудой d.
К параметрам испытаний относятся следующие величины: амплитуда перемещения точки d; установленное базовое количество циклов N; сила (усилие), развиваемая при испытаниях Q.
Наибольший интерес вызывает исследование ресурса образцов со сварными швами при различных сочетаниях с дефектами по отношению к ресурсу образцов без дефектов. Ресурс бездефектных образцов из основного металла без сварных швов можно взять за условный эталон (базу сравнения).
Для изготовления образцов использовали катушку (часть трубы), вырезанную из нефтепровода УБКУА при ремонтных работах. Нефтепровод построен и принят в эксплуатацию в 1973 г. При этом использованы трубы размером 1220×12 мм
Рис. 6.1. Общий вид С-образных образцов (a ) и схема испытаний (б)
266
Таблица 6.4
Результаты испытаний на растяжение основного металла
Номер образца |
Ψ, % |
|
δ, % |
|
σт, |
|
σв, |
|
|
кгс/ мм2 |
|
кгс/ мм2 |
|||
1 |
51,55 |
|
20 |
|
40,374 |
|
61,369 |
2 |
59,43 |
|
20 |
|
40,374 |
|
61,531 |
3 |
56,39 |
|
19,230 |
|
41,989 |
|
61,531 |
4 |
53,97 |
|
20,769 |
|
40,374 |
|
61,369 |
5 |
52,39 |
|
20,769 |
|
40,479 |
|
61,528 |
|
|
|
Средние значения |
|
|
||
|
54,7 |
|
20,1 |
|
40,7 |
|
61,5 |
|
|
|
|
||||
|
|
|
|
|
|
|
|
производства ЧТПЗ. Сталь марки 17Г1С. Нормативные ха-
рактеристики стали данной марки по ТУ 14-3-109−73: σв = |
|||
= 510 МПа, σт = 353 МПа. По сертификату: предел прочно- |
|||
сти σв = |
56,5 кгс/ мм2, предел текучести σт = 39,7 кгс/ мм2, |
||
относительное сужение Ψ = |
24,0 %. На заводе трубы гид- |
||
роиспытаны под давлением 70 кгс/ см2 |
в течение 30 с. Рас- |
||
четное |
проектное рабочее |
давление |
нефтепровода равно |
50 кгс/ см2. |
|
|
Для определения фактических механических свойств металла в настоящий момент (после 26 лет эксплуатации) были проведены испытания образцов на растяжение по ГОСТ
1497−84 (табл. 6.4).
Из полученных данных видно, что произошло снижение относительного удлинения (запаса пластичности) основного металла приблизительно на 16 %, а пределы текучести и прочности остались практически на исходном уровне.
При выборе амплитуды перемещений при испытаниях С- образных образцов исходили из эквивалентности напряжений на трубопроводе и образцах.
Напряжения на С-образных образцах определяли методом тензометрирования и расчетным методом конечных элементов. Расчетный метод позволяет варьировать всеми характеристиками металла и образцов, а также параметрами нагружения в широких диапазонах.
При тензометрировании использовали пленочные тензорезисторы 2ПКП-10-100В, которые были наклеены клеем «Циакрин ЭО» на поверхность образца после соответствующей обработки. Схема наклейки тензорезисторов и расположение сварного шва показаны на рис. 6.2. Тензорезисторы наклеивали на внешнюю и внутреннюю поверхности С-образного образца. Тензорезисторы 7 и 8 смещены друг от друга на 70 мм, остальные пары наклеены один под другим. Измерения производили на тензометрическом приборе ИДЦ-1.
267
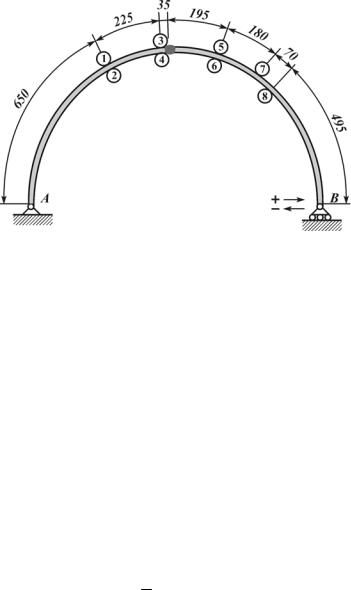
Рис. 6.2. Схема наклейки тензорезисторов (1–8 ) на С-образный образец
Измерение деформаций на С-образном образце проводили в следующей последовательности:
наклейка тензорезисторов на образец в ненагруженном состоянии;
установка образцав испытательный механизм без нагрузки; перемещение подвижного крепления образца последовательно от нейтрального положения на разные расстояния
сначала в одну сторону, а затем в другую.
После каждого измерения в нагруженном состоянии образец перемещался в нейтральное положение с контролем показаний тензометров во всех промежуточных положениях, в которых проводились измерения. Это позволило проверить состояние наклеенных тензорезисторов. В табл. 6.5 приведены показания тензометрического прибора на всех измеренных положениях образца. Положительное перемещение соответствует растяжению, отрицательное – сжатию образца.
Относительная деформация ε определяется по формуле
ε = 2 (εí − ε0 )10−6 ,
K
где K − коэффициент чувствительности тензорезисторов (для данной серии тензорезисторов K = 1,98); εн – показания при-
268
|
|
|
Таблица 6.5 |
|
|
|
|
|
||
Показания тензометров на соответствующих каналах |
|
|||||||||
|
|
|
|
|
|
|
|
|
|
|
Перемеще- |
|
|
|
Тензорезистор |
|
|
|
|||
ние |
|
|
|
|
|
|
|
|
|
|
1 |
2 |
3 |
4 |
|
5 |
|
6 |
7 |
8 |
|
d, мм |
|
|
||||||||
0 |
3280 |
2790 |
3620 |
2560 |
|
3190 |
|
2350 |
2380 |
1700 |
+49 |
3750 |
2270 |
4160 |
2000 |
|
3770 |
|
1790 |
2850 |
1230 |
+90 |
4120 |
1870 |
4570 |
1580 |
|
4190 |
|
1370 |
3190 |
880 |
+136 |
4590 |
1430 |
5090 |
1080 |
|
4750 |
|
870 |
3670 |
450 |
−45 |
2830 |
3180 |
313 |
2990 |
|
2700 |
|
2790 |
1950 |
2050 |
−89 |
2410 |
3590 |
2650 |
3450 |
|
2190 |
|
3240 |
1550 |
2430 |
−132 |
2000 |
3990 |
2180 |
3890 |
|
1730 |
|
3650 |
1150 |
2750 |
|
|
|
|
|
|
|
|
|
|
|
бора при нагруженном образце; ε0 − показания прибора при ненагруженном образце.
Измеренные относительные деформации приведены в табл. 6.6.
Линейные напряжения σ определяли с использованием диаграммы деформирования металла, которая показана на рис. 6.3. В области упругих деформаций можно использовать формулу σ = Eε, где E = 206 000 МПа − модуль упругости стали. Измеренные напряжения показаны в табл. 6.7.
|
|
|
|
|
|
|
Таблица 6.6 |
|
|
|
|
|
|
|
|
|
|
||||
|
|
Измеренные относительные деформации ε, % |
|
|
|
|
|||||||||||||||
|
|
|
|
|
|
|
|
|
|
|
|
|
|
|
|
|
|
|
|
||
Пере- |
|
|
|
|
|
|
|
Тензорезистор |
|
|
|
|
|
|
|
|
|||||
ме- |
|
|
|
|
|
|
|
|
|
|
|
|
|
|
|
|
|
|
|
|
|
|
|
|
|
|
|
|
|
|
|
|
|
|
|
|
|
|
|
|
|
|
|
щение |
1 |
|
|
2 |
|
3 |
|
4 |
|
5 |
|
6 |
|
|
7 |
|
8 |
||||
d, мм |
|
|
|
|
|
|
|
|
|
||||||||||||
|
|
|
|
|
|
|
|
|
|
|
|
|
|
|
|
|
|
|
|
|
|
+49 |
0,0475 |
−0,0525 |
0,0545 |
−0,0566 |
0,0586 |
−0,0566 |
|
0,0475 |
|
−0,0475 |
|||||||||||
+90 |
0,0848 |
|
−0,0929 |
0,0960 |
−0,0990 |
0,1010 |
−0,0990 |
|
0,0818 |
|
−0,0828 |
||||||||||
+136 |
0,1323 |
|
−0,1374 |
0,1485 |
−0,1495 |
0,1576 |
−0,1495 |
|
0,1303 |
|
−0,1263 |
||||||||||
− 45 |
−0,0455 |
|
0,0394 |
−0,0495 |
0,0434 |
−0,0495 |
0,0444 |
|
−0,0434 |
|
0,0354 |
||||||||||
− 89 |
−0,0879 |
|
0,0808 |
−0,0980 |
0,0899 |
−0,1010 |
0,0899 |
|
−0,0838 |
|
0,0737 |
||||||||||
− 132 |
−0,1293 |
|
0,1212 |
−0,1454 |
0,1343 |
−0,1475 |
0,1313 |
|
−0,1242 |
|
0,1061 |
||||||||||
|
|
|
|
|
|
|
|
|
|
|
|
|
|
|
|
|
|
|
|
|
|
|
|
|
|
|
|
|
Таблица 6.7 |
|
|
|
|
|
|
|
|
|
|
||||
|
|
|
Измеренные линейные напряжения σ, МПа |
|
|
|
|
|
|||||||||||||
|
(получены с использованием диаграммы деформирования) |
|
|
||||||||||||||||||
|
|
|
|
|
|
|
|
|
|
|
|
|
|
|
|
|
|
|
|||
Переме- |
|
|
|
|
|
|
|
Тензорезистор |
|
|
|
|
|
|
|
|
|||||
щение |
|
|
|
|
|
|
|
|
|
|
|
|
|
|
|
|
|
|
|
|
|
|
1 |
|
|
2 |
|
3 |
|
|
4 |
|
|
5 |
|
6 |
|
|
7 |
|
|
8 |
|
d, мм |
|
|
|
|
|
|
|
|
|
|
|
|
|
||||||||
+ 49 |
|
98,8 |
−109,4 |
113,7 |
|
−118,3 |
|
122,6 |
−118,3 |
98,8 |
|
|
−98,8 |
||||||||
+ 90 |
|
179,3 |
−196,9 |
203,6 |
|
−210,1 |
|
213,9 |
−210,1 |
172,8 |
|
−175,0 |
|||||||||
+ 136 |
|
266,8 |
−275,4 |
294,2 |
|
−295,8 |
|
303,9 |
−295,8 |
263,4 |
|
−256,6 |
|||||||||
−45 |
|
−94,6 |
81,9 |
−102,9 |
|
90,2 |
|
−102,9 |
92,3 |
|
−90,2 |
|
73,6 |
||||||||
−89 |
|
−186,1 |
170,7 |
−207,9 |
|
190,4 |
|
−213,9 |
190,4 |
−177,2 |
|
155,3 |
|||||||||
−132 |
|
−261,7 |
248,1 |
−288,9 |
|
270,2 |
|
−292,4 |
265,1 |
−253,1 |
|
222,6 |
|||||||||
|
|
|
|
|
|
|
|
|
|
|
|
|
|
|
|
|
|
|
|
|
|
|
|
|
|
|
|
|
|
|
|
|
|
|
|
|
|
|
|
|
|
269 |
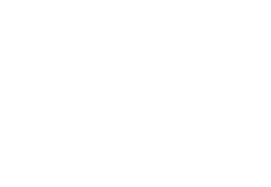
Рис. 6.3. Диаграмма деформирования металла трубы (УБКУА, сталь марки
17Г1С, размер 1220×12 мм)
Для проверки полученных экспериментальных результатов провели расчеты напряженно-деформированного состояния С-образных образцов при различных нагружениях. Расчетная программа основана на методе конечных элементов. На рис. 6.4 приведены расчетные значения деформаций в С-образном образце (толщиной 11,5 мм, шириной 60 мм, длиной по наружной поверхности 1850 мм) при различных значениях растяжения и сжатия образца.
На графиках по горизонтали отложены расстояния х от вершины образца (в одну сторону со знаком минус, а в другую − со знаком плюс), а по вертикали − значения напряжений σ. Каждый из графиков соответствует сжатию или растяжению образца на определенную величину d. Точки соответствуют результатам тензометрирования.
На рис. 6.5 приведены зависимости деформаций ε и напряжений σ на вершине образца, а также усилия Q от значения сжатия – растяжения d. По этой зависимости можно выбирать режимы испытаний С-образных образцов на остаточный ресурс.
Проектное рабочее давление нефтепровода УБКУА на
данном участке равно |
50 кгс/ см2 = |
4,9 МПа. При этом |
||||
кольцевые напряжения от внутреннего давления p |
||||||
σêö = |
ò (D − 2δ) |
= |
4,9 (1220 − 2 12) |
|
= 244,2 МПа. |
|
2δ |
2 12 |
|||||
|
|
|
||||
270 |
|
|
|
|
|
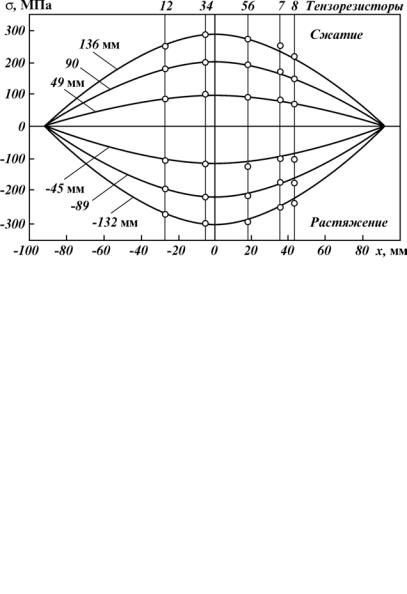
Рис. 6.4. Распределение напряжений на поверхности С-образного образца при сжатии-растяжении на различные значения d (сплошные линии соответствуют решению методом конечных элементов, точки – результатам тензометрирования)
Рис. 6.5. Зависимость напряжений и деформаций в вершине С-образного образца от параметров нагружения
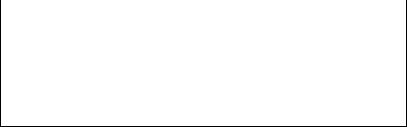
|
|
|
Таблица 6.8 |
|
|
|
|
Образцы со сварным швом без дефектов |
|
||||
|
|
|
|
|
|
|
Но- |
Ширина |
Толщина |
|
Наибольшая |
Количество |
Место |
мер |
стенки |
|
циклов до |
|||
об- |
образца, мм |
(номиналь- |
|
глубина де- |
разрушения |
разрушения |
разца |
|
ная), мм |
|
фекта |
N |
|
|
|
|
|
|||
2 |
60 |
11,5 |
|
Дефекта нет |
25 072 |
Зона |
|
|
|
|
То же |
|
сплавления |
6 |
60 |
11,5 |
|
29 520 |
То же |
|
7 |
59 |
11,5 |
|
« |
24 432 |
« |
Примечание. Среднее количество циклов до разрушения 26 341.
При испытаниях трубопровода и в моменты переключения режимов давление может превышать на 25 %. С учетом этого выберем напряжения испытаний 305 МПа.
Из графиков (см. рис. 6.5) находим, что напряжениям
± 305 МПа соответствуют следующие параметры нагружения: амплитуда перемещения d = 143 мм, усилие Q = −680÷ + 800 кН.
Были проведены испытания С-образных образцов с различным расположением сварного шва относительно середины образца и разными дефектами коррозии. Характеристики образцов и результаты испытаний их на остаточный ресурс приведены в табл. 6.8−6.11.
Испытания проводили до момента разрушения образцов. Испытательный стенд в процессе работы, вид испытанных образцов, вид излома показаны на рис. 6.6. Топография дефектов на некоторых образцах (№ 8, 9, 10) показана на рис. 6.7.
Таблица 6.9
Образцы с коррозионными дефектами в зоне сварного шва
|
Шири- |
Толщина |
|
Наибольшая |
Количест- |
|
||
Номер |
на |
стенки |
|
во |
Место |
|||
глубина дефекта, |
||||||||
образца |
образ- |
(номиналь- |
циклов |
разрушения |
||||
|
ца, мм |
ная), мм |
|
мм |
|
N |
|
|
|
|
|
|
|
||||
1 |
59 |
11,5 |
|
3,5 |
|
1 200 |
Зона |
|
|
|
|
|
|
|
|
сплавления |
|
3 |
60 |
11,5 |
|
4,3 |
|
1 637 |
То же |
|
4 |
59 |
11,5 |
3,5 (одиночная яз- |
4 549 |
« |
|||
|
|
|
ва), |
2,5 |
(общая |
|
|
|
|
|
|
коррозия) |
|
|
|
||
5 |
60 |
11,5 |
|
2,7 |
|
4 043 |
« |
|
|
|
|
|
|
|
|||
Примечание. Среднее количество циклов до разрушения |
2 857 (свар- |
|||||||
ной шов в вершине образца). |
|
|
|
|
|
|||
|
|
|
|
|
|
|
|
|
272 |
|
|
|
|
|
|
|
Таблица 6.10
Образцы с коррозионными дефектами, сварной шов смещен от вершины
Но- |
|
Ши- |
Толщи- |
Наиболь- |
Коли- |
|
|
|
|
на |
чест- |
|
|
||||
мер |
Особенно- |
рина |
стенки |
шая |
во |
|
Место |
|
об- |
сти образца, |
образ- |
(номи- |
глубина |
цик- |
|
разрушения |
|
разца |
мм |
ца, мм |
наль- |
дефекта, |
лов |
|
|
|
|
мм |
|
|
|
||||
|
|
|
ная),мм |
|
N |
|
|
|
|
|
|
|
|
|
|
||
8 |
Сварной |
63 |
11,5 |
1,5 |
|
16 368 |
|
Разрушение в |
|
шов смещен |
|
|
|
|
|
|
зонекорро- |
|
от середины |
|
|
|
|
|
|
зии на 108 мм |
|
образца на |
|
|
|
|
|
|
от середины |
|
271 мм. На |
|
|
|
|
|
|
образца и |
|
сварном |
|
|
|
|
|
|
153 мм от |
|
шве корро- |
|
|
|
|
|
|
сварного шва |
|
зии нет |
|
|
2,15 |
(ми- |
|
|
Разрушение |
9 |
Сварной |
60 |
11,5 |
12 720 |
|
|||
|
шов сме- |
|
|
нимальная |
|
|
насередине |
|
|
щен от се- |
|
|
толщина в |
|
|
образца в зо- |
|
|
редины об- |
|
|
зоне |
раз- |
|
|
не коррозии |
|
разца на |
|
|
рушения) |
|
|
на 240 мм от |
|
|
240 мм. |
|
|
|
|
|
|
сварного шва |
|
Сварной |
|
|
|
|
|
|
|
|
шов также |
|
|
|
|
|
|
|
|
подвержен |
|
|
|
|
|
|
|
|
коррозии |
|
|
2,35 (мини- |
|
|
Разрушение в |
|
10 |
Сварной |
61 |
11,5 |
15 600 |
|
|||
|
шов сме- |
|
|
мальная |
|
|
середине об- |
|
|
щен от се- |
|
|
толщина в |
|
|
разца в зоне |
|
|
редины на |
|
|
зоне раз- |
|
|
коррозии и |
|
|
250 мм |
|
|
рушения) |
|
|
на расстоя- |
|
|
|
|
|
|
|
|
|
нии 241 мм от |
|
|
|
|
|
|
|
|
сварного шва |
Примечание. Среднее количество циклов до разрушения |
14 896. |
|||||||
|
|
|
|
|
|
|
|
|
В процессе испытаний наблюдали следующее:
при испытании образцы бездефектные не нагревались (тепло рукой не ощущалось). Локализации деформации не происходило;
Таблица 6.11
Образцы без сварных швов и бездефектные
Номер |
Ширина |
Толщина |
Наибольшая |
Количество |
Место |
образ- |
стенки |
глубина |
циклов |
||
образца, мм |
(номиналь- |
разрушения |
|||
ца |
|
ная), мм |
дефекта, мм |
N |
|
|
|
|
|
|
|
11 |
60 |
11,5 |
0 |
106 300 |
В середине |
|
|
|
|
|
образца |
12 |
61 |
11,5 |
0 |
39 060 |
То же |
13 |
59 |
11,5 |
0 |
78 450 |
« |
Примечание. Среднее количество циклов до разрушения 74 603. |
|||||
|
|
|
|
|
|
|
|
|
|
|
273 |