
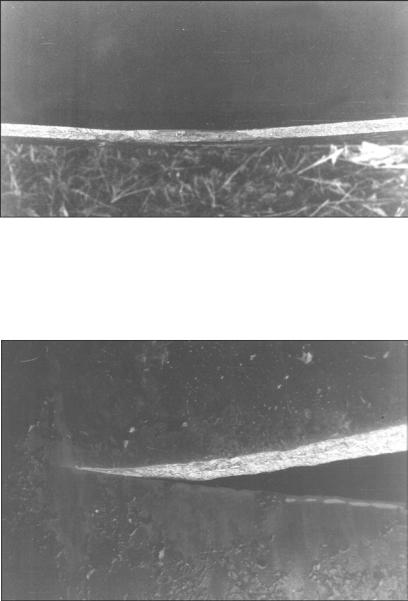
Рис. 6.13. В очаге разрушения (в центре) имеется расслоение металла
Требуется продолжение испытаний вырезанных из трубопроводов дефектных труб для накопления и обобщения результатов с целью усовершенствования нормативной базы по
Рис. 6.14. Смена механизма разрушения от хрупкого к вязкому при переходе трещины через сварной шов (трещина прошла справа налево)
284
оценке безопасности магистральных нефтепроводов при длительной эксплуатации.
6.3. ИСПЫТАНИЕ МЕТОДА ВЫБОРОЧНОГО РЕМОНТА ТРУБОПРОВОДА ФОРМОВАНИЕМ ИЗОЛЯЦИОННО-СИЛОВОЙ ОБОЛОЧКИ
В настоящее время известны два способа формования усиливающей оболочки на поверхности трубопровода, основанные на намотке высокопрочной проволоки (г. Челябинск, УралНИТИ) и стекловолокна, пропитанного эпоксидной смолой или другим составом. Стеклопластиковая оболочка была испытана на реальных трубопроводах и показала высокую прочность. Однако способ ремонта с помощью оболочки не нашел широкого применения, так как:
усиливающая оболочка оказалась проницаемой для влаги при длительной эксплуатации трубопровода на обводненных участках;
оболочка не была испытана на долговечность в условиях переменных нагрузок, приводящих к малоцикловым разрушениям трубопровода.
С водопроницаемостью можно бороться путем нанесения дополнительного водоотталкивающего слоя под оболочкой или снаружи нее. В первом случае на поверхность трубопровода вначале наносят слой праймера, а затем приступают к формованию усиливающей оболочки. Во втором случае усиливающую оболочку изолируют снаружи по той же технологии, что и трубопровод.
В данном разделе приводятся результаты испытаний усиливающей оболочки на ресурс в условиях малоциклового нагружения. Испытания проводились в ИПТЭР в 1996 г. В организации и проведении испытаний принимали участие Н.Х. Гаскаров, Р.Г. Ишмуратов, К.М. Гумеров, У.Н. Сабиров, Р.Х. Хажиев, Р.А. Башаров.
Для испытаний был изготовлен стенд трубы диаметром 720 мм и толщиной стенки 9 мм из стали марки 17ГС. К трубе приваривали эллиптические заглушки и резьбовые соединительные штуцера для подачи воды под давлением. На стенке трубы выполняли шлифмашинкой продольную канавку круглого сечения глубиной 6−6,5 мм и длиной 1500 мм. Дефект имитировал местное утонение стенки от коррозии. Остаточная толщина стенки трубы составляла 2,5−3 мм, что со-
285
ответствовало потере прочности до 70 %. Труба с таким дефектом разрушилась бы при давлении не выше 3,8 МПа.
На дефектном участке трубы формовали стеклопластиковую оболочку длиной 1800 мм с помощью устройства усиления нефтепровода УУН-720/ 820, предназначенного для работы в условиях трассы при выборочном ремонте. Перед намоткой поверхность трубы очищали от грязи, пыли, продуктов коррозии. Сплошная ржавчина и окалина были сохранены. Продольную канаву (искусственный дефект) на поверхности трубы предварительно зашпаклевали основным связующим, наполненным цементом. При намотке оболочки использовали стеклоровинги типа РБН-10-2570−78 в виде бобин массой 10−12 кг (10 штук). В качестве связующей основы применяли полиэфирную смолу ПН-1. Время формования усиливающей оболочки 4 ч. Толщина оболочки 12−14 мм.
На рис. 6.15 показана схема испытательного стенда, а на рис. 6.16 представлены поверхность трубы с дефектом перед намоткой стеклопластиковой оболочки и стенд после формования усиливающей оболочки.
Нагружение трубы осуществляли внутренним гидравлическим давлением в циклическом режиме с помощью насоса высокого давления. Цикл нагружения составлял 20−30 с, что соответствовало режиму малоциклового нагружения.
Характеристики (параметры) нагружения испытательного стенда приведены в табл. 6.13.
При данном режиме нагружения труба не разрушилась. Следов разрушения и необратимой деформации на поверхности трубы и стеклопластиковой оболочки визуальным обследованием не обнаружено.
|
Таблица 6.13 |
|
|
|
|
|
|
Номер |
Параметры нагружения |
Количество циклов и |
|
п/ п |
время нагружения |
||
|
|||
1 |
Давление от 1,0 до 6,4 МПа |
10 000 циклов |
|
2 |
Давление от 1,0 до 7,0 МПа |
100 циклов |
|
3 |
Давление от 1,0 до 7,5 МПа |
100 циклов |
|
4 |
Давление от 1,0 до 8,0 МПа |
100 циклов |
|
5 |
Давление 8,7 МПа |
Выдержка 24 ч |
|
6 |
Давление 9,7 МПа |
Выдержка 24 ч |
|
Примечания: 6,4 МПа соответствует рабочему давлению в трубопрово- |
|||
де; 8,7 МПа − испытательное давление, при котором напряжения в стенке |
|||
трубы равны 0,95 предела текучести стали; 9,7 МПа − максимальное заво- |
|||
дское испытательное давление, соответствующее 1,05 предела текучести |
|||
стали; |
10 000 циклов нагружения соответствуют эксплуатации трубопро- |
||
вода в течение 30 лет. |
|
||
|
|
|
|
286 |
|
|
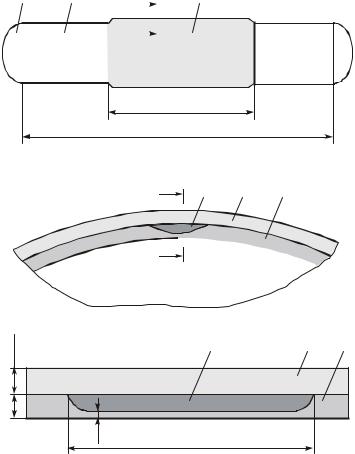
a 1 |
2 |
|
A |
|
3 |
||
|
|||||||
|
|
|
|
|
|
|
|
|
|
|
|
|
|
|
|
|
|
|
|
|
|
|
|
|
|
|
|
A |
|
|
|
|
|
|
|
|
|
|
|
1800
6000
бА-А
Б4 3 2
Б
в 14-12
Б-Б |
4 |
3 |
5 |
|
9 |
-23 |
1500 |
Рис. 6.15. Дефектная труба, усиленная высокопрочным стеклопластиком: а $ общий вид стенда; б $ поперечное сечение стенки трубы; в $ продольное сечение стенки; 1 $ днище; 2 $ труба; 3 $ усиливающая оболочка; 4 $ дефект, заполненный шпаклевкой; 5 $ стенка трубы
Таким образом, данный эксперимент показал, что стеклопластиковая оболочка, нанесенная по технологии [71], обеспечивает безопасность участков трубопроводов с коррозионными дефектами.
287

Рис. 6.16. Поверхность трубы с дефектом (а) перед намоткой стеклопластиковой оболочки и общий вид стенда (б) после формования усиливающей оболочки
288

б
Таблица 6.14
Относительные потери и затраты при различных способах восстановления дефектного участка нефтепровода (ориентировочные данные)
Метод ремонта |
Затраты на ремонт, % |
Замена участка |
100 |
Композитно-муфтовая технология («Бритиш |
63−88 |
Газ») |
16−24 |
Установка сварных ремонтных муфт |
|
Технология «Clock Spring» (часовая пружина) |
14−20 |
Формование изоляционно-силовой оболочки |
11−18 |
|
|
Метод выборочного ремонта по данной технологии является эффективным. Об этом свидетельствуют данные табл. 6.14, где приведены сравнительные затраты при ремонте разными способами.
6.4. ИСПЫТАНИЕ СВАРНЫХ РЕМОНТНЫХ МУФТ
Целью испытаний, описанных в настоящем разделе, является экспериментальная проверка безопасности ремонтных конструкций в виде сварных муфт различных конструкций. Испытания проведены при непосредственном участии сотрудников ИПТЭР К.М. Гумерова, Р.Т. Ишмуратова, И.К. Гумерова и сотрудников ОАО «Уралсибнефтепровод» Р.Х. Хажиева, З.А. Мустафина, Р.А. Башарова.
289
6.4.1. ИСПЫТАНИЕ ДВУХСЕКЦИОННОЙ УДЛИНЕННОЙ НЕПРИВАРНОЙ МУФТЫ
Подгот овка ст енда. Для испытаний выбрали трубу со следующими характеристиками: диаметр 720 мм, толщина стенки 9 мм, длина трубы 11 м, сталь марки 17ГС, предел текучести 370 МПа, предел прочности 550 МПа.
На стенке трубы шлифмашинкой нанесли продольный наружный надрез со следующими характеристиками: длина надреза 6,8 м; ширина надреза 35−40 мм, глубина надреза 5,4 мм. Надрез нанесли шлифовальным кругом так, чтобы ось вращения круга была параллельна оси трубы. При этом форма надреза была в виде кругового сегмента. Надрез имитировал коррозионную потерю металла наиболее опасной формы. Остаточная толщина стенки в вершине надреза 3,6 мм.
Муфта была изготовлена из такой же трубы (рис. 6.17). Вся муфта состояла из двух секций. Длина одной секции равна 3,5 м, общая длина муфты − 7 м.
Все сварные швы (продольные и кольцой) выполнены на подкладных пластинах толщиной 2 мм, шириной 30 мм. Кольцевой шов находится только между отдельными секциями. На концах муфты герметизирующие кольцевые швы отсутствовали.
Монтаж муфты проводили без внутреннего давления в трубе. При установке муфты использовали один центратор. Муфту монтировали на трубу по той же технологии, по которой вели аналогичные работы в полевых условиях.
Схема стенда для испытаний показана на рис. 6.18. Испытание проводили внутренним давлением. Давление
создавали водой.
Программа испыт аний предполагала следующие этапы.
1.Медленный подъем давления в трубе до 4,0 МПа (при этом давлении происходит пластическое деформирование металла в вершине дефекта).
2.Выдержка в течение 2 ч под давлением 4,0 МПа.
3.Нагружение внутренним давлением в циклическом ре-
жиме с параметрами: количество циклов |
N = 10; pmin |
= |
||
= |
0,1 МПа; pmax = 4,0 МПа. |
|
|
|
|
4. Нагружение внутренним давлением в циклическом ре- |
|||
жиме с параметрами: N = 10; pmin |
= |
0,1 МПа; pmax |
= |
|
= |
4,5 МПа. |
|
|
|
|
5. Нагружение внутренним давлением в циклическом ре- |
|||
жиме с параметрами: N = 10; pmin |
= |
0,1 МПа; pmax |
= |
|
= |
5,0 МПа. |
|
|
|
290 |
|
|
|
|
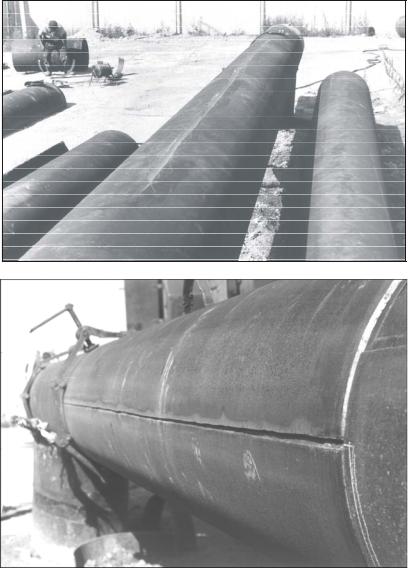
Рис. 6.17. Подготовка трубы с продольным искусственным дефектом и ремонтной муфты для испытаний
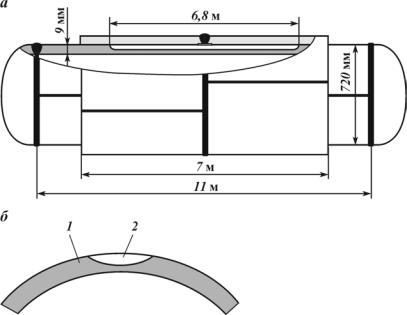
Рис. 6.18. Схема (а) для гидроиспытаний неприварной удлиненной муфты, установленной на трубу с дефектом (б) в виде широкого надреза:
1 $ стенка трубы; 2 $ надрез
|
6. Нагружение внутренним давлением в циклическом |
ре- |
|||||
жиме с параметрами: N |
= 10; pmin |
= |
0,1 |
МПа; |
pmax |
= |
|
= |
5,5 МПа. |
|
|
|
|
|
|
|
7. Нагружение внутренним давлением в циклическом ре- |
||||||
жиме с параметрами; N |
= 10; pmin |
= |
0,1 |
МПа; |
pmax |
= |
|
= |
6,0 МПа. |
|
|
|
|
|
|
|
8. Нагружение внутренним давлением в циклическом ре- |
||||||
жиме с параметрами: N |
= 10; pmin |
= |
0,1 |
МПа; |
pmax |
= |
|
= |
6,5 МПа. |
|
|
|
|
|
|
|
9. Нагружение внутренним давлением в циклическом ре- |
||||||
жиме с параметрами: N |
= 10; pmin |
= |
0,1 |
МПа; |
pmax |
= |
|
= |
7,0 МПа. |
|
|
|
|
|
|
10. И так далее до момента разрушения трубы (выхода воды).
Результ ат ы испыт аний. В полном объеме выполнены этапы 1−8 программы испытаний. Время одного цикла нагружения изменялось с увеличением pmax в пределах от 2 до 4 мин.
292
На этапе 9 труба разрушилась под муфтой при первом цикле нагружения; само разрушение (трещина) не вышло из-под муфты.
Выводы и рекомендации.
1. Неприварная обжимная многосекционная муфта упрочила трубу с дефектом на 27 % (труба с дефектом, но без муфты разрушилась бы при давлении не выше 5,5 МПа, с муфтой разрушилась при давлении 7,0 МПа).
2. Эффект упрочнения трубы с помощью муфты проявился неполностью. Причина этого заключается в том, что при монтаже муфты одним центратором плотного обжатия не достигается; между стенкой трубы и муфтой остается зазор, наблюдаемый визуально.
3. Технология выполнения продольных сварных швов на подкладных пластинах удовлетворяет требованиям прочности (муфта остановила развитие трещины вдоль трубы и не дала выйти наружу).
4. Необходимо усовершенствовать приспособления и технологию монтажа и обжатия муфты. Количество обжимных устройств должно быть не менее двух на 1 м муфты. Обжимное устройство должно обеспечивать равномерное по периметру трубы радиальное давление на трубу. Для этого необходимо пользоваться гидравлическим обжимными устройствами.
6.4.2. ИСПЫТАНИЕ ДВУХСЕКЦИОННОЙ УДЛИНЕННОЙ ПРИВАРНОЙ МУФТЫ
Подгот овка ст енда. После выполнения испытаний, описанных в разделе 6.4.1, концы муфты решили приварить к трубе, превратив неприварную муфту в приварную (см. рис. 4.7). Для этого к концам муфты пристыковали технологические кольца шириной 15 мм и выполнили кольцевые сварные швы без подкладных пластин (рис. 6.19). Под муфтой остался прежний дефект, ставший сквозным после первых испытаний.
Программа испыт аний предполагала следующие этапы:
1.Медленный подъем давления в трубе до 6,6 МПа (максимальное допустимое рабочее давление).
2.Выдержка в течение 30 мин под давлением 6,6 МПа.
3.Нагружение 100 циклами давления в диапазоне 3,0− 6,6 МПа.
293