

4
ОБЕСПЕЧЕНИЕ БЕЗОПАСНОСТИ МЕТОДАМИ ВЫБОРОЧНОГО РЕМОНТА
Обнаружение дефектов и оценка их опасности являются важным, но только первым шагом в обеспечении безопасности магистральных нефтепроводов. Следующий шаг − проведение ремонтных работ. Причем ремонтные работы должны проводится с наибольшей эффективностью, желательно без остановки перекачки нефти.
Существует много способов ремонта в зависимости от ситуации и решаемой задачи. Но в основном все ремонтные работы на линейной части трубопроводов подразделяются на следующие две большие группы:
выборочный ремонт с целью восстановления работоспособности отдельных коротких участков с опасными дефектами; длина отдельного ремонтируемого участка обычно не превышает длины плети (трех труб);
капитальный ремонт протяженного участка трубопровода с целью замены изоляции или замены труб.
При организации и проведении ремонта на действующих магистральных нефтепроводах необходимо решать многие очень важные вопросы, связанные с обеспечением безопасности как на этапе ремонта, так и на этапе послеремонтной эксплуатации: выбор участков для ремонта; подготовка нефтепровода к ремонту; подготовка ремонтных бригад, специалистов, техники; аттестация сварочного оборудования, сварочных материалов, сварщиков, технологии сварки; классификация дефектов в связи с выбором методов ремонта; выбор технологий ремонта; согласование работ с контролирующими, смежными, вышестоящими организациями; обеспечение управляемости и связи; отработка внештатных ситуаций; оформление набора необходимой документации.
Рассмотрим некоторые из важнейших вопросов, связанных с выборочным ремонтом труб линейной части магистральных нефтепроводов.
157
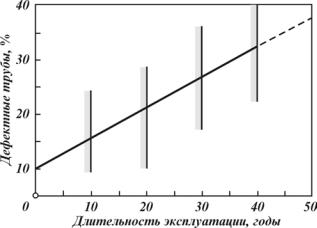
4.1. КЛАССИФИКАЦИЯ ДЕФЕКТОВ ДЛЯ РЕМОНТА НЕФТЕПРОВОДОВ
Результаты внутритрубной диагностики показывают, что процентное содержание дефектных труб на магистральных нефтепроводах велико и оно растет с увеличением срока эксплуатации. Эта зависимость, построенная по самым сдержанным данным, приведена на рис. 4.1.
Ранее приведенные данные (см. табл. 2.10) показывают, что на некоторых трубопроводах картина еще хуже. Например, отношение количества обнаруженных дефектов к количеству труб (длиной 11 м) на УБКУА достигает 80 %, а на ТУ-II превышает 100 %. В таких условиях ремонтировать все дефектные трубы становится бессмысленным; легче заменить весь трубопровод. Но, даже если построить абсолютно новый трубопровод, количество дефектных труб (с расслоениями, включениями, дефектами сварки) окажется порядка 10−30 % (экспертные данные). Поэтому ликвидировать все дефекты невозможно
Возникает задача − отобрать для ремонта только те дефекты, которые действительно представляют реальную опасность. Если общее количество опасных дефектов превышает определенный допустимый предел, экономически выгоднее
Рис. 4.1. Усредненная зависимость количества дефектных труб на магистральных нефтепроводах (по данным внутритрубной диагностики)
158
строить параллельную линию. Поэтому стоит важная задача − классифицировать обнаруженные дефекты по признакам, приближенным к нуждам эффективного ремонта (обеспечение наибольшей безопасности при наименьших затратах). Основными такими признаками являются:
необходимость дополнительного обследования дефектных участков, обнаруженных внутритрубными инспекционными снарядами;
степень опасности дефектов; возможность ремонта без остановки работы нефтепровода.
Дополнительный дефектоскопический контроль (ДДК)
Такой контроль проводят после пропуска внутритрубных снарядов и анализа полученной информации. Контроль осуществляют методом шурфовки нефтепровода на дефектных участках. Методы ДДК определяют эксперты и экспертные организации на основе нормативных требований.
ДДК проводят, когда для достоверной оценки опасности дефектов недостаточно информации, полученной внутритрубным обследованием. Выделить дефекты для ДДК и грамотно провести контроль − тоже непростые задачи. В последние годы участились случаи, когда аварии с разрывом трубопровода произошли именно после проведения ДДК до выполнения ремонта.
Необходимость выполнения дополнительного дефектоскопического контроля дефектов, обнаруженных внутритрубными снарядами, диктуется следующими обстоятельствами:
возможно расхождение данных внутритрубного обследования с реальными параметрами дефекта из-за технических особенностей дефектоскопа;
вероятно существование сочетания дефектов различных видов, не определяемых использованным набором внутритрубных снарядов;
прочность и остаточный ресурс дефектных участков зависят от ряда параметров, не контролируемых внутритрубными снарядами.
Дополнительному дефектоскопическому контролю подлежат:
дефекты, определенные как «опасные» по результатам расчетов прочности нефтепровода на дефектном участке;
дефекты, расчетные параметры которых определены недостаточно точно при внутритрубном обследовании нефтепровода;
159

дефекты, вид которых не определен по результатам внутритрубной диагностики.
При использовании ультразвуковых внутритрубных снарядов «Ультраскан» дополнительному дефектоскопическому контролю подлежат дефекты со следующими параметрами по данным внутритрубного обследования:
вмятины и гофры глубиной (высотой) более или равной 2t (t − номинальная толщина стенки трубы);
вмятины и гофры глубиной (высотой) более или равной толщине стенки, примыкающие к сварным швам;
расслоения металла, примыкающие к сварному шву; расслоения металла с выходом на поверхность стенки; риски и царапины на поверхности трубы длиной более
2 Dt;
коррозионные дефекты (потери металла) глубиной более 0,1 номинальной толщины стенки, примыкающие к сварным швам.
Выбор методов дополнительного дефектоскопического контроля − задача экспертов и экспертной организации.
По ст епени опасност и дефект ов для нормальной эксплуа-
тации нефтепровода обнаруженные дефекты делятся на три группы:
недопустимые дефекты; опасные дефекты; неопасные дефекты.
К недопустимым дефектам относятся: сквозные дефекты;
дефекты, создающие препятствие для нормальной эксплуатации нефтепровода по технологическим признакам (например, сужения поперечного сечения трубы выше допуска, застрявшие посторонние предметы внутри трубы и др.);
дефекты, являющиеся источником значительного риска аварии (усталостные трещины, опасные дефекты на подводных переходах и др.).
В частности, недопустимы следующие дефекты: сужения проходного диаметра более 85 % номинального;
вмятины и гофры с риской (трещиной) глубиной (риски или трещины) более 0,3 толщины стенки трубы;
вмятины и гофры с дефектами сварного шва общей дли-
ной (вмятины или гофра) более 2 Dt и максимальной глубиной более толщины стенки;
коррозия на внешней и внутренней поверхностях трубы глубиной более 0,8 толщины стенки;
160
риски (царапины) на внешней и внутренней поверхностях трубы глубиной более 0,65 толщины стенки.
трещины любого происхождения, расслоения с выходом на поверхность глубиной более 0,5 толщины стенки.
К недопустимым дефектам также следует отнести обнаруженные дефекты, степень опасности которых невозможно установить.
К опасным дефектам относятся:
дефекты, которые могут привести к разрушению нефтепровода при испытательном давлении, превышающем максимальное рабочее давление на 25 % (по критерию прочности); дефекты, которые могут привести к разрушению нефтепровода при эксплуатации в рабочем режиме за счет роста дефекта в межинспекционный период (критерий остаточного
ресурса).
К неопасным дефектам относятся все остальные обнаруженные дефекты. Причем одни и те же дефекты могут перейти из группы опасных в группу остальных (неопасных) при понижении допустимого рабочего давления.
Недопустимые дефекты нефтепровода подлежат немедленной ликвидации.
Участки нефтепровода с опасными дефектами подлежат обязательному ремонту. Режим эксплуатации до выполнения ремонта участков с опасными дефектами должен исключать возможность аварий на этих участках. Для этого существуют следующие способы:
ограничение рабочего давления наименьшим допустимым давлением на дефектных участках;
остановка перекачки продукта по дефектным участкам. Участки с неопасными дефектами не требуют обязательного ремонта в межинспекционный период при условии, что будет установлен контроль за их возможным развитием (мо-
ниторинг).
Ремонт с ост ановкой работ ы нефт епровода проводится в следующих случаях:
потеряна герметичность трубопровода на дефектном участке;
сужение проходного сечения нефтепровода на дефектном участке выходит за пределы допустимого;
невозможно обеспечить требуемую прочность дефектного участка другими способами;
невозможно обеспечить безопасность работ другими методами;
затруднено полное обследование обнаруженного дефекта.
161
Давление при ремонте нефтепровода должно быть не более 75 % по отношению к допустимому давлению дефектного участка.
4.2. МЕТОДЫ РЕМОНТА ДЕФЕКТНЫХ УЧАСТКОВ НЕФТЕПРОВОДОВ
На магистральных нефтепроводах возможны следующие апробированные методы ремонта дефектных участков [40, 67,
69, 71, 74, 75, 76]:
шлифовка (зачистка); заварка (наплавка); приварка заплаты;
установка сварной ремонтной муфты; композитно-муфтовая технология (КМТ); формование композитной изоляционно-силовой оболочки
(ИСО);
установка манжет «Clock Spring»; вырезка дефекта (замена катушки).
Шлифовка (зачист ка), как самостоятельный метод ремонта используется для восстановления работоспособности участков труб с дефектами типа потеря металла (коррозия, царапины, риски). Остаточная толщина стенки после шлифовки не должна выходить за рамки требований, соответствующих заданному рабочему давлению. Смысл шлифовки в том, что выравнивается поверхность трубы, тем самым снижается концентрация напряжений. Чаще применяют шлифовку как один из этапов технологии при использовании других методов ремонта (зачистка поверхности металла перед заваркой, разделка металла перед заваркой, исправление формы сварных швов шлифовкой, снятие усиления сварных швов перед установкой обжимной муфты, снижение концентрации напряжений на комбинированных дефектах типа вмятина + царапина и др.).
Заварка (наплавка) используется для исправления дефектов типа потеря металла коррозионного и механического происхождения. При ремонте нефтепровода без опорожнения заварка дефекта может быть применена при остаточной толщине стенки не менее 5 мм и выполнении соответствующих требований технологии.
Допускается применять заварку (шлифовку) как один из этапов технологии при использовании других методов ремонта (заварка некоторых дефектов перед установкой ремонтной
162
муфты, исправление дефектов сварных швов шлифовкой и заваркой).
Приварка заплат ы. Допускаются к применению приварные заплаты двух видов:
заплата круглая или овальная (эллиптическая); заплата овальная с технологическими сегментами.
До 80-х годов XX века использовались прямоугольные заплаты, привариваемые угловыми швами. Причем длинная сторона была ориентирована вдоль трубы. Долговечность таких заплат оказалась низкой из-за сильной концентрации напряжений на угловых швах. В последние годы произошли аварии на ранее отремонтированных участках с прямоугольными заплатами. Поэтому в настоящее время избегают протяженных угловых швов, ориентированных вдоль трубы.
Уст ановка сварной ремонт ной муфт ы. На нефтепроводах возможно применение большого многообразия сварных ремонтных муфт различных типов:
приварные и неприварные; обжимные и необжимные;
с наполнителем и без наполнителя (также составом наполнителя);
односекционные и многосекционные.
Н еприварные сварные ремонтные муфты можно использовать в случаях, если в процессе дальнейшей (после ремонта) эксплуатации нефтепровода исключена возможность разгерметизации трубы за счет роста дефекта изнутри трубы (рост коррозионного дефекта или усталостной трещины).
Приварные сварные ремонтные муфты допускается использовать в случаях, если в процессе дальнейшей (после ремонта) эксплуатации нефтепровода имеется вероятность разгерметизации трубы за счет роста дефекта (под муфтой).
Обж имные сварные ремонтные муфты допускается устанавливать в случаях, когда нет препятствий для плотного прилегания муфты к поверхности ремонтируемой трубы (отсутствуют гофры, заплаты, искривления трубы).
Н еобж имные сварные ремонтные муфты допускается устанавливать в случаях, когда имеются препятствия для плотного прилегания муфты к поверхности ремонтируемой трубы (выступы, гофры, старые заплаты, искривления трубы, недопустимые формы сварных швов).
Односек ционные сварные ремонтные муфты допускается устанавливать на участках нефтепровода с непротяженными по оси трубы дефектами (длиной не более 3 м) или в случаях, когда не требуется плотное обжатие трубы.
163
М ногосек ционные сварные ремонтные муфты допускается устанавливать на участках нефтепровода с протяженными по оси трубы дефектами (длиной более 3 м) или в случаях, когда установкой односекционной муфты не удается достичь плотного обжатия трубы из-за кривизны ремонтируемого участка нефтепровода.
При композит но-муфт овой т ехнологии ремонт выполня-
ется в соответствии с РД 153-39-030−98 [74, 75] (с 2001 года по РД 153-39.4-067−00). Допускается ремонтировать участки с несквозными дефектами следующих типов: гофры, вмятины, потеря металла коррозионного и механического происхождения, трещины, сварочные дефекты, комбинированные дефекты.
Усиление дефект ного участ ка изоляционно-силовой обо-
лочкой. Оболочка состоит из двух слоев: водоотталкивающего слоя (праймер, краска, пленка и др.) и силовой оболочки (композит на основе высокопрочного стекловолокна и твердеющего состава). Толщина композитной силовой оболочки должна быть (0,8 ÷ 1,1)t. Ремонт выполняют в соответствии с
РД 39 Р-00147105-010−97 [7].
Допускается ремонтировать участки с дефектами, не искажающими геометрической формы трубы (коррозия, расслоение металла, продольные царапины и трещины, дефекты на продольных и спиральных швах, вмятины глубиной до 20 мм). В процессе ремонта сварочные работы не используются.
Уст ановка ремонт ной манжет ы «Clock Spring» (часовая пружина). Манжета представляет собой многослойную оболочку, получаемую путем намотки на дефектный участок трубы рулонного высокопрочного композитного листа с применением быстровысыхающего двухкомпонентного адгезива и шпаклевки с высоким сопротивлением сжатию. Технология разработана фирмой «Clock Spring». Имеются отечественные аналоги разработки ВНИИСТ. Допускается ремонтировать участки нефтепровода с дефектами типа потеря металла, продольная трещина, расслоение с выходом на поверхность. При этом длина дефекта по оси трубы должна быть не более диаметра трубы.
При вырезке дефект а (замене кат ушки): дефектный уча-
сток трубы вырезается из трубопровода и заменяется на бездефектную катушку (трубу, секцию) [69]. Этот способ используется при:
авариях с разрывом трубы; недопустимом сужении проходного сечения нефтепровода;
164
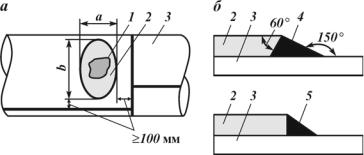
невозможности обеспечения требуемой прочности дефектного участка другими способами;
затрудненности полного обследования обнаруженного дефекта.
4.3. КОНСТРУКЦИИ СВАРНЫХ УСИЛИТЕЛЬНЫХ ЭЛЕМЕНТОВ
Заплата (рис. 4.2). Прочность и надежность накладных приварных заплат будут обеспечены при выполнении следующих условий.
Угловые точки по периметру должны быть исключены. Для этого форма заплаты должна быть круглой или овальной. При этом исключаются концентрации напряжений в угловых точках по периметру.
Протяженность угловых швов, ориентированных вдоль трубы, должна быть сведена к минимуму, поскольку такие участки наиболее напряжены. Для этого овальные заплаты должны быть ориентированы длинной стороной по окружности трубы.
Прочность угловых швов должна быть максимальной. Для этого необходимо предусмотреть обратную разделку кромок перед сваркой и выполнять швы в усиленном варианте, который впервыебылпредложен Р.С.Зайнуллиным (см.рис.4.2, б). При этом шов получается неравнокатетным, расстояние между вершинами концентраторов увеличивается, траектория возможного развития трещины удлиняется. Все это в совокупности увеличивает прочностьна 50−70 %, ресурс в 3−5 раз.
Рис. 4.2. Схема установки заплаты (а) и геометрия углового шва по периметру (б):
1 − дефект стенки трубы; 2 − заплата; 3 − стенка трубы; 4 − сварной шов усиленный; 5 − сварной шов обыкновенный равнокатетный
165
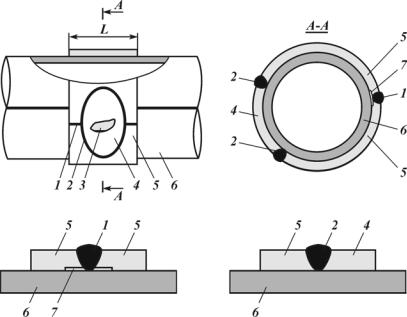
Заплата должна обеспечивать необходимую надежность при попадании продукта под заплату. Для этого размеры заплаты должны быть ограничены следующими значениями (D − диаметр, h − толщина стенки трубы):
размер по оси трубы а не более 150 мм; размер по окружности трубы b не более 0,3D; толщина стенки заплаты hзап = (1 ÷ 1,2)h.
При установке на трубу заплата должна перекрыть место повреждения стенки трубы не менее 20 мм по периметру.
Расстояние от заплаты до сварных швов нефтепровода должно быть не менее 100 мм. При этом сварные швы не будут приводить к ухудшению свойств металла в зонах термического влияния соседних швов.
Угловые швы по периметру заплаты должны иметь плавные переходы от шва к основному металлу.
Заплата с технологическим сегментом (рис. 4.3).
Рис. 4.3. Схема установки заплаты с технологическими сегментами:
1 − сварной продольный шов на подкладной пластине (без приварки к стенке); 2 − сварной шов с приваркой к стенке нефтепровода; 3 − дефект; 4 − заплата; 5 − технологические сегменты; 6 − стенка нефтепровода; 7 − подкладная пластина
166