
Таблица 4.5 |
|
|
|
|
|
Выбор методов ремонта участков нефтепровода с расслоениями, |
|||||
примыкающими к сварному шву |
|
|
|||
|
|
|
|
|
|
Характеристики |
|
|
Метод ремонта |
|
|
дефекта |
рекомендуемый |
допустимый |
|||
|
|
|
|
|
|
Расслоения, не отнесенные при |
Ремонт |
не |
стенки |
|
− |
прочностном расчете к опасным |
трубы |
требу- |
|
|
|
Расслоения, не выходящие на по- |
ется |
|
|
Муфты |
№ 1, 2, |
ИСО |
|
|
|||
верхность, не примыкающие к |
|
|
|
3, 4, 5, 6 и 8, |
|
сварным швам и отнесенные при |
|
|
|
«Clock Spring» |
|
прочностном расчете к опасным |
Ремонт |
|
стенки |
|
|
Расслоение металла, примыкающее |
не |
|
|
||
к бездефектному сварному шву |
трубы |
требу- |
|
|
|
Расслоение металла, примыкающее |
ется |
|
|
Муфты № 6, 7 и |
|
Вырезка дефекта |
|||||
к поперечному сварному шву с не- |
|
|
|
8 |
|
допустимыми дефектами сварки (по |
|
|
|
|
|
СНиП и ВСН) |
ИСО |
|
|
Муфты |
№ 1, 3, |
Расслоение металла, примыкающее |
|
|
|||
к заводскому (продольному и спи- |
|
|
|
4, 5, 6 и 8, |
|
ральному) сварному шву с недопус- |
|
|
|
«Clock Spring» |
|
тимыми дефектами сварки (по |
|
|
|
|
|
СНиП и ВСН) |
|
|
|
|
|
|
|
|
|
|
|
4.5. ТЕХНОЛОГИЧЕСКИЕ МЕТОДЫ ОБЕСПЕЧЕНИЯ БЕЗОПАСНОСТИ ПРИ ВЫБОРОЧНОМ РЕМОНТЕ МАГИСТРАЛЬНЫХ НЕФТЕПРОВОДОВ С ПРИМЕНЕНИЕМ СВАРКИ
4.5.1. ЗАВАРКА ДЕФЕКТА (НАПЛАВКА)
Заварку поверхностных дефектов стенки труб нефтепроводов, находящихся под давлением, проводят на нефтепроводах с эквивалентом углерода металла труб и сварных соединений не выше 0,46 % и максимальной твердостью 220 единиц по шкале Бриннеля, при температуре окружающего воздуха не ниже минус 20 °С и положительной температуре металла труб. Эти требования значительно снижают вероятность растрескивания металла при сварке.
Непосредственную наплавку металла при заварке дефектов выполняют, если остаточная толщина стенки после разделки дефектов не менее 5 мм, максимальный размер дефек-
177

та (длина, ширина, диаметр) не более 2 Dt, внутреннее дав-
ление в процессе сварки не более 3,5 МПа, сечение нефтепровода полностью заполнено нефтью. Эти требования позволяют избежать прожога стенки трубы и взрыва паров нефти внутри трубы.
Расстояние от завариваемых дефектов до сварных швов выдерживают не менее 100 мм (для недопущения наложения зон термического влияния).
Перед сваркой дефектное место обрабатывают механическим способом (фрезой, шлифмашинкой, иглофрезами и др.). Кроме того, любой дефект (в том числе трещину) разделывают до размеров, допускающих полный провар корневого шва. Непосредственная заварка трещин без разделки не допускается. Это позволяет избежать непроваров в корне шва и снизить вероятность появления шлаковых включений в наплавленном металле.
Для получения наплавленного металла с нужными механическими свойствами, заварку поверхностных дефектов стенки труб нефтепроводов, находящихся под давлением, проводят постоянным током обратной полярности электродами с покрытием основного вида. Для наплавки первого, «корневого» слоя применяют электроды с покрытием основного вида, соответствующим по классификации ГОСТ 9467−75 типу Э50А (Е7016 по стандарту AWS А55). Сварочные электроды для сварки заполняющих слоев должны обеспечивать равнопрочность металла шва с основным металлом трубы.
Количество наплавляемых слоев должно быть не менее двух. При нанесении каждого последующего слоя происходит отжиг металла предыдущих слоев.
Первый наплавочный и контурный швы выполняют электродами диаметром до 3 мм включительно, на минимально допустимых для этих электродов значениях тока (во избежание сквозного проплавления металла). Последующие слои (заполняющие и облицовочные) можно наплавлять электродами диаметром до 5 мм (значение тока указано на этикетке или в сертификате на электроды).
Перед наложением каждого валика поверхность наплавленного металла очищают от шлака и брызг металла. После зачистки каждый валик или слой следует просмотреть невооруженным глазом, а потом с помощью лупы не менее 4-кратного увеличения.
Сварку выполняют на возможно короткой дуге. Перед гашением дуги кратер заполняют путем постепенного отвода
178
электрода и вывода дуги назад на 15−20 мм на только что наложенный шов. Последующее зажигание дуги производят на металле шва на расстоянии 12−15 мм от кратера.
Сварочную дугу в начале сварки зажигают на выводной планке (клинообразной стальной пластине толщиной не менее 4 мм), установленной на зачищенной поверхности нефтепровода в непосредственной близости от завариваемого дефекта, и плавно переносят на дефект. После этого планку сразу удаляют (до затвердения металла).
После завершения заварки дефекта поверхности облицовочного и контурного слоев обрабатывают шлифовальным кругом до ровной поверхности с усилением на швах 0,5− 1,0 мм.
4.5.2. ПРИВАРКА УСИЛИТЕЛЬНЫХ ЭЛЕМЕНТОВ
Ремонтные накладные усилительные элементы (заплаты и муфты) монтируются на действующем нефтепроводе без остановки перекачки при тех же условиях, которые были изложены при рассмотрении заварки (наплавки).
Механические свойства и химический состав металла заплаты и муфты должны быть близки к свойствам металла труб нефтепровода.
Для увеличения разгружающего эффекта от установки усилительных элементов (заплат, муфт, ИСО, манжет) рекомендуется при ремонте нефтепровода максимально снизить давление.
Приварку усилительных элементов на дефектный участок нефтепровода, находящегося под давлением перекачиваемой нефти, проводят в следующей последовательности:
подготовка усилительных элементов к монтажу (подгонка размеров, подготовка кромок под сварку, подготовка продольных пазов для установки подкладных пластин, очистка поверхностей в зоне сварки и прилежащих областях шири-
ной 10−15 мм);
монтаж элементов на поверхности нефтепровода с обеспечением необходимого натяга и зазоров;
прихватка смонтированных элементов к трубе; выполнение корневых швов; выполнение заполняющих слоев (валиков); выполнение облицовочного слоя;
пооперационный и окончательный контроль за монтажом и сварными швами.
179

Рис. 4.12. Схемы выполнения стыкового сварного шва с подкладной пластиной (а, б) и подготовка кромок под сварку (в): γ = 40÷60°; m = 1÷3 мм; q = 40÷50 мм; s = 12÷18 мм; с = 0,5÷3 мм
Перед установкой заплат и обжимных ремонтных муфт дефект типа потеря металла заполняют (зашпаклёвывают) твердеющей пастой на основе эпоксидной смолы или другого коррозионно-инертного материала до уровня поверхности трубы.
Монтаж заплат и обжимных муфт выполняют с натягом, обеспечивающим силовой контакт между усилительным элементом (заплатой, муфтой) и трубой.
Установку заплаты, технологических сегментов, муфты и подкладных колец, их фиксирование на трубе и обжатие осуществляют с помощью гидравлических съемных сборочных приспособлений. Нельзя наносить на трубопровод удары кувалдой или другими предметами.
Продольные швы всех усилительных элементов (технологических сегментов, муфт, технологических и подкладных колец) выполняют стыковыми швами на подкладных пластинах по одной из схем рис. 4.12. Приварка продольных швов муфты, колец и сегментов к стенке нефтепровода не допускается.
Металлическая подкладная пластина толщиной 1,5−2,0 мм и шириной 35−50 мм предварительно устанавливается по всей длине шва и выступает по длине с каждой стороны продольного шва на 25−40 мм. После сварки свободные концы подкладной пластины срезаются. В качестве материала подкладной пластины используется мягкая низкоуглеродистая сталь с углеродным эквивалентом не более 0,40 %.
На неприварных ремонтных муфтах все кольцевые угловые швы обыкновенные − с прямоугольной кромкой.
На приварных ремонтных муфтах все кольцевые угловые
180
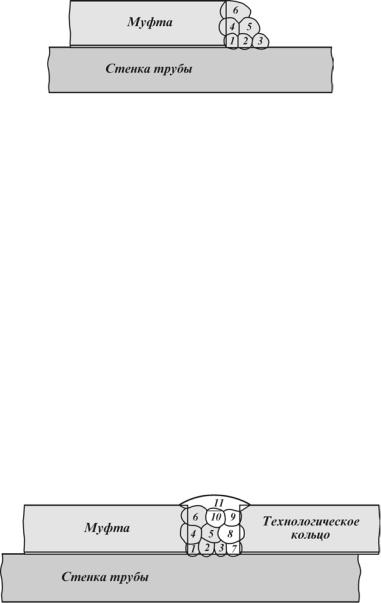
Рис. 4.13. Последовательность наложения слоев (1−6 ) при сварке муфты и ее элементов к стенке трубы нефтепровода
швы должны быть усиленными − с обратной разделкой кромки. Переход от шва к поверхности трубы должен быть плавным.
Сварку муфты и ее элементов к основной трубе кольцевыми угловыми швами рекомендуется проводить в следующем порядке (рис. 4.13):
на наружную поверхность по периметру трубы ручной дуговой сваркой последовательно по ширине шва наплавить 3− 4 валика, образующие предварительный первый слой шва;
на первый слой шва наплавить последующие валики, образующие второй слой шва;
наружный валик наплавить в последнюю очередь.
При выполнении угловых швов их форма должна исключать образование острых концентраторов напряжений, включая переходы от швов к поверхности трубы.
Сварку муфты и ее элементов к основной трубе кольцевыми стыковыми швами с применением технологических колец рекомендуется выполнить в следующем порядке (рис.
4.14):
установить муфту и выполнить кольцевой угловой шов (см.
рис. 4.13);
Рис 4.14. Последовательность наложения слоев (1–11) при приварке технологического кольца
181

к приваренной к стенке трубы муфте установить технологическое кольцо, обеспечив необходимые зазоры и натяг;
довести угловой шов до стыкового, наложив дополнительные заполняющие и облицовочные валики;
обработать шлифмашинкой поверхность стыкового шва. Сварку корневых слоев продольных и кольцевых угловых швов выполняют электродами с покрытием основного типа диаметром 2,5−3,25 мм. Могут быть применены электроды марок УОНИ13/ 55, ОК48.04, Гарант, LB-52U, FoxEV-50 и
другие, разрешенные в установленном порядке. Ориентировочные режимы сварки: первый слой 80−100 А,
последующие слои 110−140 А.
Сварку проводят постоянным током обратной полярности с контролем сварочного тока.
Во избежание температурных деформаций сварку продольных и кольцевых швов (длиной более 500 мм) рекомендуется выполнять обратноступенчатым способом, причем продольные швы − в направлении от центра муфты к ее краям.
Ремонт участков сварных швов, имеющих дефекты, осуществляют путем их шлифовки (вырубки) с последующей заваркой. Повторный ремонт одного и того же дефекта методом заварки не разрешается. Ремонт одного и того же сварного шва разными сварщиками не рекомендуется.
Муфта должна перекрывать дефект на расстояние, превышающее ширину зоны термического влияния сварки (ориентировочно 75 мм). Если длина одной секции муфты недостаточна для перекрытия дефекта, рекомендуется использовать многосекционную муфту.
В случае установки многосекционной муфты следует: сборку многосекционной муфты осуществлять последова-
тельно секциями; переход к монтажу каждой следующей секции разрешается только после выполнения сварочных работ на всех предыдущих секциях;
сварку внутренних кольцевых швов, соединяющих секции, во избежание приварки муфты к основной трубе, выполнять
Рис. 4.15. Защита от коррозии пространства под муфтой с помощью углового шва:
1, 2 − номера валиков в порядке выполнения
182
на металлической подкладной пластине толщиной 1,5−2,0 мм и шириной 35−50 мм, которую предварительно следует установить в пазы секции шириной 20−25 мм с помощью прихватки к одной из секции по всей длине шва (см. рис. 4.12,
б, в).
При установке муфты № 1 между муфтой и трубой должна находиться прокладка из композиционного материала или из мягкого металла толщиной 1,5−2,0 мм. В процессе монтажа муфта должна быть прижата к трубе силой, соответствующей внутреннему давлению в трубе (чтобы обеспечить необходимый натяг).
На концах всех приварных ремонтных муфт № 3, 4, 6 и заплаты с технологическими кольцами и сегментами допускается выполнять герметизирующие угловые швы, которые препятствуют проникновению влаги под технологические элементы (кольца и сегменты) и повышают эффективность изоляции муфты (рис. 4.15). Количество проходов (валиков) на герметизирующих швах должно быть не менее двух.
183