
больше дефект, тем больший ток стекает в грунт, тем больше градиент электрического поля.
Определялись те места, где были зафиксированы всплески измеряемого потенциала на фоне монотонно меняющегося силового поля. Эти места отмечались как места с нарушением изоляции поверхности трубы.
Данные о местах нарушения изоляции (где градиент потенциала превышает установленную норму) приведены в табл. 2.1, из которой следует, что градиент потенциала превышает допустимое значение на суммарной протяженности 30 250 м. Это составляет не менее 20,1 % всей протяженности нефтепровода на данном участке длиной 150 км.
В табл. 2.2 приводится информация о наличии потенциала защиты трубы, из которой следует, что протяженность участков, не защищенных катодным потенциалом, составляет 5,5 %.
На рис. 2.2 приведено сопоставление участков нарушений изоляции с болотами. Анализ показывает, что из всех нарушений изоляции 10 180 м приходится на болота, что составляет приблизительно 28,8 % протяженности самих болот. На сухих грунтах протяженность участков с нарушенной изоляцией 20 060 м, что составляет приблизительно 18,8 % протяженности трубопровода на сухих участках. Таким образом, на болотных участках нарушений изоляции приблизительно в 1,5 раза больше, чем на сухих участках нефтепровода.
По результатам измерений потенциалов было выборочно проверено состояние изоляции на трубах непосредственно методом шурфовки. В табл. 2.3 приведены некоторые результаты наблюдений в шурфах.
Приведенные здесь результаты обследования состояния изоляции на нефтепроводе УБКУА относятся к 1990 г. За истекшее время состояние изоляции претерпело изменения. На некоторых участках был выполнен капитальный ремонт по замене изоляции. На других участках состояние изоляции с течением времени могло только ухудшиться.
Приведенные данные показывают, что изоляция магистрального нефтепровода находится далеко от идеального состояния. Обследование в таежных заболоченных участках чрезвычайно затруднено. Остаются необследованные участки. Добывать эти данные приходится вручную, пешим шагом, проводя многочисленные измерения в труднопроходимых местах. В зимнее время проходимость несколько увеличивается из-за замерзания болот, но появляются дополнительные трудности для работы регистрирующей аппаратуры. При этом данные измерений достаточно быстро устаревают. По-
48
Таблица 2.3
Результаты обследования нефтепровода в шурфах (километры указаны условно)
Километр |
Градиент |
|
|
потенциала, |
Результаты наблюдений |
||
по трассе |
|||
мВ/ 10 м |
|
||
|
|
||
46,580 |
−300 |
Изоляция повреждена при засыпке грунта |
|
|
|
(грунтом или механизмом), коррозия ме- |
|
|
−110 |
талла на месте повреждения |
|
48,610 |
Изоляция охрупчена, отслаивается от по- |
||
|
|
верхности трубы, воздействие корней де- |
|
|
+230 −100 |
ревьев, почвенная коррозия |
|
160 |
Пленочная изоляция отсутствует, труба об- |
||
|
|
лита битумом, имеются складки, имеется |
|
|
+15 −110 |
неизолированный участок длиной 60 мм |
|
157 |
Произошло отлипание пленки от поверхно- |
||
|
|
сти трубы, имеется продольный гофр плен- |
|
|
+400 −312 |
ки |
|
112 |
Отсутствует изоляция верхней и боковой |
||
|
|
части трубопровода, адгезия (прилипае- |
|
|
+36 −60 |
мость) неудовлетворительная |
|
103 |
Не изолирована полоса шириной 30 мм по |
||
|
|
всей окружности трубы, наблюдаются зна- |
|
|
|
чительные следы коррозии |
|
|
|
|
этому требуется разработать новые методы контроля за изоляцией, основанные на более современных принципах, используя, например, внутритрубную диагностику.
2.3. ДЕФЕКТЫ ТРУБ И СВАРНЫХ ШВОВ
Как показывает опыт анализа аварий, все разрушения трубопроводов происходили на дефектах металла труб и сварных швов. Другое дело, что некоторые из этих дефектов возникают из-за дефектов изоляции и отсутствия катодной защиты. Это видно из табл. 2.4, где приведен анализ причин
Таблица 2.4
Количественный анализ причины аварий на магистральных нефтепроводах России
Причина |
1990 г. |
1996 г. |
2000 г. |
(0,27 аварий |
(0,20 аварий |
(0,06 аварий |
|
|
на 1000 км) |
на 1000 км) |
на 1000 км) |
Коррозия металла |
34 |
22 |
33,3 |
Заводские дефекты (расслое- |
18 |
11 |
33,3 |
ния, включения, продольные |
|
(продольный |
|
сварные швы) |
|
шов) |
|
Брак строительно-монтажных |
24 |
56 |
33,3 |
работ (вмятины, гофры, попе- |
|
(кольцевые |
|
речные сварные швы) |
|
швы) |
|
Механические повреждения |
24 |
− |
− |
Повреждения сторонними ор- |
− |
11 |
− |
ганизациями |
|
|
|
|
|
|
|
|
|
|
49 |
разрушений магистральных нефтепроводов, произошедших в 1990 и 1996 гг. (до и после внедрения внутритрубной диагно-
стики) [48, 90].
Результаты обследования трубопроводов внутритрубными дефектоскопами показывают, что на нефтепроводах относительная доля дефектных труб велика, и она заметно растет с увеличением срока эксплуатации нефтепроводов:
Срок эксплуатации |
До 10 лет |
10−20 лет |
20−30 лет |
Свыше 30 лет |
нефтепровода........... |
||||
Количество дефект- |
9−24 |
10−28 |
17−36 |
22−40 |
ных труб, %.............. |
Не все дефекты металла труб и сварных швов могут привести к разрушению нефтепроводов при эксплуатации в проектных режимах. Дефекты, которые могут привести к разрушению в рабочих режимах, являются опасными. Степень опасности дефектов определяется расчетами. В табл. 2.5 приводятся данные о соотношении опасных дефектов, обнаруженных внутритрубным дефектоскопом «Ультраскан WM» в период 1995−1998 гг.
Эти данные отражают особенности дефектоскопа «Ультраскан WM» и первого издания расчетной методики от 1994 г. [51]. С применением дефектоскопов других типов и совершенствованием расчетной методики соотношение опасных дефектов меняется, в частности, снижается количество опасных дефектов типа расслоений металла и значительно возрастает количество опасных дефектов сварки. Это очень важно, так как любая ненужная вырезка дефектной трубы из нефтепровода влечет за собой большие потери, связанные с остановкой перекачки и опорожнением данного участка. Хотя технология замены дефектных труб отработана, эта операция остается самой дорогостоящей из всех методов выборочного ремонта.
Таблица 2.5
Статистика опасных дефектов, обнаруженных дефектоскопом «Ультраскан WM» на магистральных нефтепроводах страны до 1998 г.
Дефекты |
Количество опасных дефектов, % |
Потери металла (коррозия) |
42,8−59,2 |
Расслоения металла |
24,6−47,1 |
Расслоения металла, выходящие на |
1,5−2,6 |
поверхность |
6,2−7,7 |
Расслоения металла в околошовной |
|
зоне |
1,3−7,0 |
Риски |
|
|
|
50
Степень опасности дефектов зависит не только от типа дефекта и его размеров, но и от особенностей нагружения трубопровода. Например, при нормальной эксплуатации подземного нефтепровода наибольшую опасность представляют дефекты продольных сварных швов, механические царапины. При капитальном ремонте с заменой изоляции наибольшую опасность представляют дефекты кольцевых сварных швов, так как при этом предусматривается приподнимать нефтепровод с помощью трубоукладчиков.
В последние несколько лет участились аварии по следующему сценарию:
проводится внутритрубное обследование нефтепровода; выделяются недопустимые и сомнительные дефекты, тре-
бующие дополнительного обследования; проводится дополнительное дефектоскопическое обследо-
вание дефектов с шурфовкой; по результатам обследования в шурфах составляется план
ремонта дефектных участков нефтепровода; шурф временно засыпается грунтом до ремонтных работ;
разрушение наступает до запланированного срока ремонта.
Причина аварии заключается в том, что расчетная оценка опасности дефекта учитывает только внутреннее давление в трубопроводе, но никак не учитывает тот факт, что после шурфовки и засыпки грунт вокруг дефектной трубы подругому действует на трубопровод. После засыпки шурфа возникают дополнительные напряжения от усадки разрыхленного грунта. Поэтому очень важно развивать методы расчета, используя для этого все возможности (эксперименты, теоретические разработки, опыт различных научных центров).
В качестве примера рассмотрим более подробно один из наиболее характерных типов дефектов, представляющих собой опасность для длительно эксплуатирующихся магистральных нефтепроводов.
Пример 2.2. На рис. 2.3 показаны фрагменты дефекта, определенного по результатам внутритрубного обследования как потеря металла. Визуально измерительный контроль показал, что данный дефект примыкает к продольному сварному шву. Ширина дефекта 547 мм, остаточная толщина стенки 5,6 мм, глубина 6,1 мм, положение 104° (ниже горизонтального диаметра участка трубопровода). Толщина стенки бездефектного участка 11,7 мм. Дефект коррозионного происхождения на наружной поверхности.
51

Рис. 2.3. Фрагменты дефекта типа потеря металла, обнаруженного на нефтепроводе УБКУА
Причиной коррозии послужили косые гофры пленочной изоляции, образовавшиеся при намотке на трубу. В полость под пленкой попала влага, которая инициировала подпленоч-
52
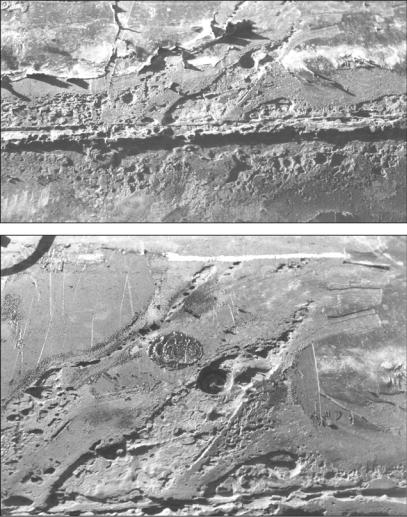
ную коррозию. Особенность данного случая в том, что электрохимзащита оказалась неэффективной, поскольку изоляционная лента не была нарушена, а все необходимые для коррозии компоненты находились под пленкой в гофре и под одним и тем же потенциалом с металлом трубы. Процесс коррозии происходил автономно, почти без участия грунта.
Гофр изоляционной пленки образовался в районе про-
53
дольного заводского шва, который имеет геометрическое усиление около 3 мм. Это усиление помешало плотному прижатию изоленты к поверхности трубы в окрестности сварного шва. В результате влага из-под гофра попала также в узкую полость вдоль сварного шва. На рис. 2.4 показано коррозионное состояние околошовной зоны продольного заводского шва, обследованное визуально и по макрошлифам.
По результатам осмотра данного дефекта можно отметить следующее:
дефектоскоп «Ультраскан WM» показывает качественно правильную картину о дефекте типа потеря металла.
количественные показатели дефекта (площадь, глубина) фактически выше на 20−50 %, чем указано в распечатке дефекта.
Следовательно, за истекшее время после проведения внутритрубной диагностики коррозионный процесс трубопровода продолжался. Поэтому при оценке фактической опасности дефектов типа потеря металла коррозионного происхождения необходимо учитывать поправку на время эксплуатации после диагностики, которая в данном случае составляет 25−30 % (т.е. глубина и размеры дефекта фактически больше в 1,25−1,3 раза по отношению к измеренным внутритрубным дефектоскопом).
Особое внимание следует обратить на продольные сварные швы, где коррозия происходит в узкой зоне вдоль границы сплавления. На распечатке дефекта информация о коррозии может не проявиться из-за рассеяния сигнала от неровной поверхности сварного шва. Опасность такой коррозии высока из-за действия нескольких неблагоприятных факторов одновременно:
уменьшение толщины стенки от коррозии и снижение прочности трубы;
наличие концентрации напряжений на переходе от сварного шва к основному металлу, что ускоряет коррозию (механохимический эффект);
охрупченность зон сплавления сварного шва и термического влияния;
неравновесная и неоднородная структура зоны термического влияния, что благоприятствует коррозии за счет образования дополнительных анодных зон;
затрудненность или невозможность контроля этих дефектов методами внутритрубной диагностики.
Тем не менее внутритрубная диагностика является чрезвычайно эффективным методом получения сведений о де-
54
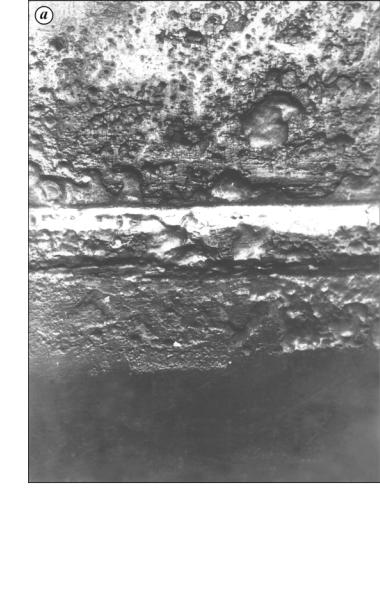
Рис. 2.4. Общий вид (а) и схема (б) коррозионного состояния продольного (заводского) сварного шва
фектах металла труб. Приведем основные сведения, получаемые данным методом на примере нескольких трубопроводов.
2.4.АНАЛИЗ РЕЗУЛЬТАТОВ ВНУТРИТРУБНОЙ ДЕФЕКТОСКОПИИ МАГИСТРАЛЬНЫХ
НЕФТЕПРОВОДОВ
Внутритрубное обследование магистральных нефтепроводов, проводимое с 1995 г., является наиболее эффективным способом контроля за их техническим состоянием. В настоящее время практически все магистральные нефтепроводы обследованы профилемерами «Калипер», основанными на электромеханическом принципе. Они способны обнаружить такие особенности геометрии трубопровода, как гофры, вмятины, изгибы, арматуру, отводы и др. По результатам обследования ликвидируют наиболее опасные дефекты, к которым относятся также все сужения с проходным диаметром менее 0,85 номинального значения.
Большая часть магистральных нефтепроводов обследована дефектоскопами «Ультраскан WM», которые основаны на ультразвуковом воздействии на стенку трубы по периметру. Эти дефектоскопы способны обнаружить такие дефекты стенки трубопровода, как коррозия, царапина, расслоение металла, положение и геометрию всех сварных швов, а также уточнить параметры тех дефектов, которые обнаружены профилемером. В настоящее время именно этим дефектоскопом получена наиболее полная картина о состоянии дефектности магистральных нефтепроводов.
На стадии разработки и начала внедрения находятся ультразвуковой дефектоскоп «Ультраскан CD» и магнитный дефектоскоп «MFL». Это наиболее сложные снаряды предназначены для обнаружения трудноуловимых трещиновидных дефектов, степень опасности которых велика, и определения состояния дефектности сварных швов. Объем информации, полученный этими дефектоскопами, пока невелик, но набирается опыт, и по перспективным планам все магистральные нефтепроводы должны быть обследованы ими.
Все внутритрубные дефектоскопы сосредоточены в Центре технической диагностики (ЦДТ) «Диаскан» (г. Луховицы, Московской области, филиал в Уфе), который проводит рабо-
56
ты по обследованию трубопроводов. Несмотря на очевидные успехи в области внутритрубной диагностики, имеются задачи, которые необходимо решить:
обследование напряженного состояния трубопровода вдоль трассы;
обследование механических свойств металла и сварных швов вдоль трассы, степени охрупченности металла от деформационного старения, коррозионного растрескивания и др.;
обследование потенциала электрохимической защиты трубопровода вдоль трассы;
обследование состояния изоляционного покрытия трубопровода.
Вслучае решения этих сложных задач безопасность трубопроводов может быть поднята на следующий уровень.
Вкачестве примера рассмотрим анализ результатов внутритрубной диагностики на одном из участков магистрального нефтепровода УБКУА длиной 150 км. Данные получены с
применением дефектоскопа «Ультраскан WM», обследование проводил ЦТД «Диаскан». Трубопровод был построен и принят в эксплуатацию в 1973 г. Использованы трубы производства Челябинского трубопрокатного завода. Проектное рабочее давление 50 кгс/ см2. Марка стали 17Г1С. Трубы прямошовные. Наружный диаметр 1220 мм. Толщина стенки труб на данном участке находится в пределах 12,0−15,2 мм. Изоляция пленочная. Имеется электрохимическая защита. Нефтепровод проходит через заболоченную местность. Общая протяженность болот по нефтепроводу приблизительно равна 38,4 км, что составляет 25,6 % длины участка нефтепровода.
При обследовании дефектоскопом «Ультраскан WM» идентификация дефектов происходит по отраженным ультразвуковым сигналам от внутренней и наружной поверхностей стенки трубы. Поэтому любые изменения во времени прихода отраженных сигналов фиксируются как «особенность», а расшифровка сигнала по специальной методике позволяет определить тип особенности и ее параметры. Привязка дефектов проводится к ближайшим точкам-ориентирам (маркерам, задвижкам, вантузам), а также к ближайшим поперечным сварным швам с точностью 0,25 м. Погрешность определения толщины стенки и глубины коррозии составляет не более 0,5 мм. Погрешность измерения размеров по окружности трубы не более 8 мм, в продольном направлении трубы не более 3,3 мм.
57