
методичка основи управління якістю
.pdfЯк приклад, можна навести спосіб забезпечення виконання планових завдань за рахунок інтенсифікації праці робітників, що в підсумку приведе до збільшення кількості помилок в їх роботі і, відповідно, бракованої продукції. Занадто інтенсифікація праці також призведе до інших можливих негативних наслідків, таких, як, наприклад, травматизм, плинність кадрів, і т. п.
У даному випадку для забезпечення підвищення продуктивності виробничого процесу слід запроваджувати заходи організаційного характеру, замінити обладнання на більш продуктивне, механізувати працю робітників тощо.
Із сказаного вище видно, що всякі конкретні цілі, які не відповідають передбаченню розвитку числових характеристик стійкого процесу в майбутньому, або стосуються характеристик нестійкого процесу є нереальними.
Наприклад, безглуздо наказовим порядком встановлювати нормативи спізнення потягів на залізничному транспорті, якщо не запроваджуються організаційні, технічні, та інші заходи, спрямовані на покращення характеристики процесу перевезень. Час запізнення і ймовірність його реалізації є об’єктивними характеристиками процесу, визначаються його властивостями, які можуть бути покращенні тільки шляхом удосконалення характеристик елементів процесу, тобто зменшенням їх варіацій.
Якщо процес не знаходиться під контролем, має нестійкий характер, неможливо робити передбачення характеристик його розвитку. Треба спочатку визначити та ліквідувати спеціальні чинники, які викликають нестабільність процесу, а потім працювати з стійким процесом.
Загальні чинники, як правило, діють на працівника ззовні і можуть значно погіршувати результати його праці. І на ці зовнішні фактори в багатьох випадках сам працівник не може впливати. До таких зовнішніх чинників, які мотивують або демотивують працівника можна віднести оплату, організацію та умови праці, психологічний клімат у колективі, зацікавленість працівника в роботі, можливості його самореалізації. Вплив на ці фактори є компетенцією менеджерів, які організують виробничий процес.
Такі відомі фахівці в галузі якості, як Едвард Демінг та Джозеф Джуран [8], висловили думку, що приблизно в 5 −15 % випадків винуватцями браку є безпосередні виконавці роботи, а в 85 −95 % випадків провина лежить на менеджерах, які організували цей виробничий процес.
Вміння оцінювати характеристики якості процесу обслуговування є однією з важливих конкурентних переваг організації.
Для збереження або підвищення конкурентоспроможності системи часто необхідно зменшити варіацію її характеристик. Звичайно, це можна зробити шляхом детального розгляду та усунення деяких загальних чинників, які викликають розсіювання параметрів процесу.
Сказане вище можна коротко охарактеризувати наступним чином:
підвищення якості результату будь-якої діяльності має здійснюватись стабілізацією процесу шляхом ідентифікації і усунення спеціальних
21
чинників з метою зробити цей процес контрольованим, та наступним зменшенням його варіацій.
Якість є зменшенням ризику непередбаченого. Зменшення варіацій результату процесу якраз і зменшує такий ризик для споживача. При цьому результат процесу, як випадкова величина, оцінюється своїм математичним очікуванням (для нормального розподілу це середнє значення), та ймовірністю знаходження величини в заданому інтервалі, що можна зробити через визначення середньоквадратичного відхилення.
Також слід додати такі узагальнення.
Якщо виробнича система знаходиться під впливом спеціальних чинників, наявність яких робить процес нестабільним, то результат такого процесу передбачити з певною ймовірністю неможливо. Тому неможливо правильно оцінювати результати удосконалень, які вносяться в систему з метою покращення результату. Такі удосконалення, як зміни в структурі організації, навчання персоналу, робота з субпідрядниками, придбання нового більш ефективного обладнання, які інколи є дуже дорогими, можуть не принести бажаних наслідків у вигляді зменшення варіацій результату.
Доки процес знаходиться в нестабільному, некерованому стані, неможливо передбачити його результат.
Коли спеціальні чинники виявлені і їх дія на виробничу систему нейтралізована, залишаються тільки загальні чинники, і менеджери можуть запроваджувати дії по покращенню системи. У цьому випадку процес знаходиться під дією стабільної системи загальних чинників і якість результату повністю визначається характеристиками елементів системи, варіаціями їх параметрів, тобто тим, яким чином сама система і процеси в ній були спроектовані і побудовані [8].
Стає очевидним, що для успішного вирішення проблеми покращення якості роботи будь-якої виробничої системи необхідно навчитись відрізняти стабільну систему від нестабільної, виявляти наявність спеціальних чинників.
Яким же чином можна відрізнити присутність спеціального чинника від дії стабільної системи загальних причин.
Шухарт запропонував і обґрунтував робочий інструмент, який допомагає відрізняти ці дві ситуації [2, 8]. Це контрольні карти. Принцип побудови і використання контрольних карт буде розглянутий далі.
Загальна методологія покращення якості результату функціонування виробничої системи складається з трьох фаз:
1.Стабілізація процесу (приведення його у контрольований стан) шляхом ідентифікації і усунення спеціальних чинників.
2.Покращення самого виробничого процесу шляхом зменшення варіацій діяльності окремих його компонентів. Для цього послідовно виявляються і усуваються найбільш впливові загальні чинники.
3.Моніторинг процесу для стабілізації показників якості результату діяльності виробничої системи.
Слід сказати, що контрольні карти мають велике значення у кожній з трьох фаз.
22
5. МЕХАНІЗМ ПОСТІЙНОГО ПОЛІПШЕННЯ ЯКОСТІ
Для реалізації фаз 1 та 2 поліпшення якості результату процесу, наведених вище, може бути застосований наступний алгоритм, який по суті відповідає циклу Шухарта-Демінга:
1.Виявлення та відбір проблеми – визначення й опис поточного та бажаного станів (виявлення невідповідності);
2.Аналіз проблеми – виявлення ключових причин та їх ранжування по важливості (пошук причин виникнення невідповідності);
3.Розробка та документування можливих коригувальних дій;
4.Вибір послідовності та планування реалізації окремих коригувальних дій
–розробка плану реалізації коригувальних дій та оцінки змін;
5.Реалізація плану коригувальних дій та оцінка їх результативності;
6.Вибір нової проблеми для розв’язання та повторення дій за пунктами 1–5. Відправною точкою роботи по покращенню якості є виявлення симптомів
неякісності – матеріального чи нематеріального проявлення відхилень від належної якості.
Задачею роботи є покращення якості шляхом розробки рішення, яке б усунуло даний тип неякісності, що проявляється зафіксованими симптомами.
Рішення неможливо знайти без визначення причин неякісності. Таким чином, вирішення проблеми можна розбити на два етапи [8]:
1.Визначення причини неякісності за симптомами;
2.Розробка рішень з ліквідації причин неякісності.
Усвою чергу визначення причин неякісності за симптомами виконується
втакій послідовності:
1.Детально визначаються симптоми проблеми і формулюється проблема;
2.Симптоми аналізуються;
3.Формулюються теорії щодо можливих причин виникнення цих симптомів;
4.Теорії перевіряються на практиці;
5.Результати перевірки аналізуються та робляться висновки.
Для цього необхідно виконати таку роботу:
1.Визначити точно кожний з симптомів у порядку частоти їх появи;
2.Використати принцип Парето, який детально описаний далі;
3.Розробити план збирання та аналізу даних;
4.Зібрати дані;
5.Проаналізувати дані;
6.Зробити висновки та оформити результати роботи.
Зі сказаного вище видно, що збирання даних є фундаментальним компонентом контролю якості і що контроль якості базується на статистиці.
Для аналізу даних з метою виявлення спеціальних чинників, які викликають нестабільність виробничої системи та симптоми неякісності, японськими гуртками якості використовуються сім елементарних методівінструментів, які отримали назву «сім інструментів якості». В довільній послідовності це є:
23
1.Таблиці даних, контрольні листки – для збирання даних;
2.Гістограми – для ілюстрації варіації параметра;
3.Карти контролю – для оволодіння процесом та контролю його протікання;
4.Діаграма Парето – для визначення важливих чинників;
5.Діаграма «причини-наслідки» (Ішикави) – для визначення походження проблем;
6.Діаграми кореляції – для виявлення взаємозв'язків між параметрами процесу;
7.Групування даних – вибір з усієї сукупності однорідних даних деяких за певною ознакою або згідно з визначеним принципом.
Далі розглянемо ці інструменти більш детально.
6.ІНСТРУМЕНТИ ЯКОСТІ
6.1.Таблиці даних. Контрольні листки
Збирання даних має виконуватися з максимально можливою точністю, тому що дані повинні правдиво відображати реальність. Якщо це не так, є велика загроза прийняти неправильні рішення на базі неправдивих даних і марно витратити час і гроші.
Звичайно, дані розміщують на документах, що називаються контрольними листками, у вигляді таблиці. Основною вимогою до таблиць даних є ясність сприйняття та легкість використання. Таблиці даних виконують п’ять основних функцій:
1.Перевірка закону розподілу контрольованого параметра;
2.Реєстрація видів дефектів;
3.Локалізація дефектів;
4.Визначення причин дефектів;
5.Кінцевий контроль.
Згідно з цими функціями можуть існувати відповідні типи таблиць даних. Метою збирання даних під час контролю якості є:
•Контроль та регулювання виробничого процесу;
•Аналіз відхилень від установлених вимог;
•Контроль продукції.
Приклад контрольного листка для побудови гістограми розподілу напрацювання на відмову деталі автомобіля наведений на рис.5.
6.2.Гістограми
Гістограма є графічним зображенням результатів вимірювання деякого параметра. Вона представляє собою стовпцевий графік, побудований на основі отриманих за певний період даних. Звичайно, гістограми будують за таблицями даних.
24
Графічно гістограма являє собою сукупність прямокутників, які мають загальну базу та розташовані сторона до сторони. Бази прямокутників однакові. Вони представляють собою цілі числа або інтервали вимірювання. Висота кожного прямокутника пропорційна кількості випадків вимірювання в даному інтервалі.
Метою побудови гістограми є графічне зображення табличної інформації, яке дозволяє миттєво оцінити характер розподілу експериментальних даних.
Цілочислові бази можуть представляти собою дні, місяці, роки і т. п. По вертикалі відкладають кількість однорідних подій, які мали місце в цей день або місяць, наприклад, кількість скарг по днях тижня, кількість запитів клієнтів по днях, починаючи з моменту виходу реклами і т. д.
Якщо вимірюваний параметр є безперервною величиною, спочатку визначають розмах розподілу як різницю між максимальним та мінімальним значеннями параметра, а потім розбивають цю величину на ряд інтервалів – класів або розрядів.
Є різні рекомендації щодо вибору кількості інтервалів. Наприклад, їх кількість може становити 10 % загальної кількості даних. Кількість інтервалів може наближатися до квадратного кореня від загальної кількості даних, якщо така не перевищує 100.
Дані для побудови гістограми розподілу напрацювання на відмову деякої деталі автомобіля наведені в таблиці на рис.5. Гістограма розподілу напрацювання на відмову цієї деталі показана на рис.6. На цій гістограмі частота попадання в розряд визначається як відношення кількості випадків попадання в розряд до загальної кількості випадків.
Номер |
Інтервал |
Середнє |
Реєстрація кількості |
Кількість |
Частота |
інтерва |
розрядів, |
значення |
попадань в інтервал |
попадань в |
попадання |
лу |
пробіг, |
інтервалу, |
|
інтервал |
в |
|
тис. км |
тис. км |
|
|
інтервал, f |
1 |
2 |
3 |
4 |
5 |
6 |
1. |
20…30 |
25 |
// |
2 |
0,0123 |
2. |
30…40 |
35 |
/// |
3 |
0,0185 |
3. |
40…50 |
45 |
////////// |
10 |
0,0617 |
4. |
50…60 |
55 |
//////////////// |
16 |
0,0988 |
5. |
60…70 |
65 |
/////////////////////////// |
27 |
0,1667 |
6. |
70…80 |
75 |
///////////////////////////////// |
33 |
0,2037 |
7. |
80…90 |
85 |
////////////////////////////////// |
34 |
0,2099 |
8. |
90…100 |
95 |
/////////////////////// |
23 |
0,1420 |
9. |
100…110 |
105 |
/////////// |
11 |
0,0679 |
10. |
110…120 |
115 |
/// |
3 |
0,0185 |
Всього |
|
|
|
∑xi =162 |
∑ f = |
|
|
|
|
|
=1.0000 |
Рис.5. Приклад контрольного листка для побудови гістограми розподілу напрацювання на відмову деталі автомобіля
25
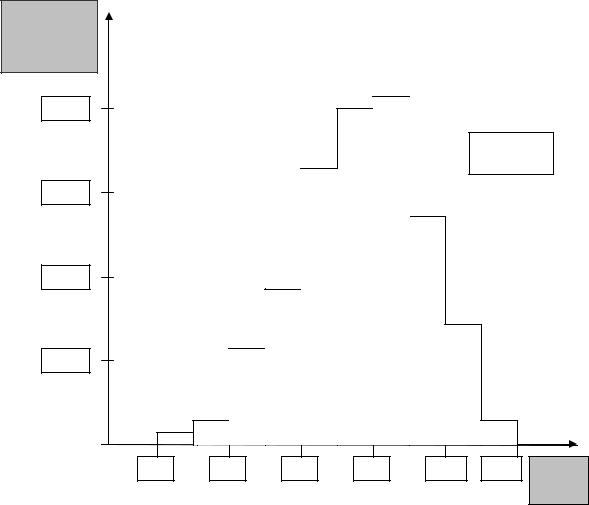
Для однієї вибірки даних можна побудувати багато гістограм з різною кількістю інтервалів. Всі ці гістограми матимуть подібний вигляд.
За формою гістограми можна прийняти робочу гіпотезу щодо належності даного розподілу до того чи іншого закону розподілу. Наприклад, для випадку, наведеного на рис.5 – нормального розподілу. Але ця гіпотеза потребує подальшої математичної перевірки. Для визначення причин варіації параметра необхідно вміти аналізувати гістограми. Коректний аналіз можна зробити у випадку, коли вибірка перевищує 50 даних.
Нормальний розподіл має форму дзвона. Такий розподіл є характеристикою регулярного виробництва. Але все ж таки він може не задовольняти необхідним вимогам до продукту. У деяких випадках середнє значення не відповідає бажаному, в інших – дисперсія є дуже великою.
За законами, близькими до нормального, розподіляються поступові відмови, річні, добові та міжремонтні пробіги, простої автомобілів у технічному обслуговуванні та капітальному ремонті. Але напрацювання на раптові відмови та простої у поточних ремонтах розподіляються за законами, близькими до експоненціального.
Частота |
|
|
|
|
|
|
попадання в |
|
|
|
|
|
|
інтервал |
|
|
|
|
|
|
0,20 |
|
|
|
|
|
|
|
|
|
|
|
n = 162 |
|
0,15 |
|
|
|
|
|
|
0,10 |
|
|
|
|
|
|
0,05 |
|
|
|
|
|
|
20 |
40 |
60 |
80 |
100 |
120 |
Пробіг |
|
|
|
|
|
|
тис.км |
Рис.6. Гістограма розподілу напрацювання на відмову деталі автомобіля |
26
Гістограми будуються здебільшого для аналізу значень виміряних параметрів, але може використовуватись і для отримання розрахункових значень. Завдяки простоті побудови та наочності гістограми використовуються в різних сферах .
Гістограми можуть використовуватись для вирішення таких задач:
•аналіз часу знаходження в СТО, супермаркеті, перукарні, майстерні, лікарні, банку, тощо;
•аналіз часу реагування групи обслуговування (в будь-якому місці) від моменту отримання замовлення від клієнта;
•аналіз часу обробки рекламації від моменту її отримання, тощо;
•аналіз терміну виконання замовлення (за контрольний норматив береться термін згідно укладеного договору);
•аналіз значень показників якості (розмір, маса, механічні характеристики, вихід продукції при контролі готової продукції, під час контролю перебігу процесу в різних сферах діяльності і т. п.);
•аналіз чистого часу операції, процесу, тощо;
•аналіз кількості бракованих виробів, кількості дефектів, кількості помилок, тощо.
6.3.Контрольні карти
Контрольна карта – це графічний засіб оцінки певної ознаки якості, виміряні значення якої наносяться на графік відповідно до порядку отримання їх у часі.
Принцип побудови і використання контрольних карт полягає в наступному.
Розглянемо найбільш загальний довільний виробничий процес, який має місце в будь-якому комерційному підприємстві, до яких відносяться і автосервісні підприємства (станції технічного обслуговування автомобілів – СТОА), і результатом якого є певна сума виручки, наприклад, за день.
Керівник підприємства для контролю за результатами діяльності своєї фірми будує графік змін денної виручки в часі (рис.15). При цьому на горизонтальній осі позначаються дні, а по вертикальній відкладається величина денної виручки. Такі графіки називають картами поточних значень контрольованого параметру – у даному випадку денної виручки.
В кінці декількох тижнів спостережень, на протязі яких не було якихось особливих змін виручки, керівник підрахував середнє значення денної виручки і позначив його на графіку у вигляді горизонтальної лінії. При цьому стало помітно, що точки спостережень розташовувались відносно рівномірно вище і нижче середньої лінії.
Продовжуючи спостереження, через деякий час керівник зареєстрував стабільне зниження денної виручки на протязі дев’яти днів поспіль, що на графіку контролю мало вигляд розташування дев’яти послідовних точок нижче середньої лінії.
27
Це явище здалося йому аномальним і навело на думку, що звичайний процес роботи підприємства був деформований наявністю якогось спеціального чинника.
Після детального вивчення ситуації виявилось, що один з автомеханіків організував у себе в гаражі власну майстерню і домовлявся з клієнтами щодо виконання їх замовлень не на СТОА, де він працював, а в себе за меншу ціну. При цьому, не сплачуючи податків, він отримував більше, ніж за цю ж роботу на СТОА. Клієнту ж також це обходилось значно дешевше, ніж на автосервісному підприємстві. Після звільнення цього працівника і заміни його іншим, ситуація була взята під контроль і процес стабілізувався, що знайшло свої відображення на карті контролю поточних значень денної виручки.
Контрольні карти вперше були запропоновані відомим американським фахівцем у галузі якості УолтеромШухартом [2,8], тому носять його назву.
На контрольних картах Шухарта наносять три горизонтальні лінії: центральну лінію, а також верхню та нижню контрольні границі.
Центральна лінія відображає деяке усереднення поточних значень контрольованого параметру. Звичайно, це середнє арифметичне, але може бути і медіанним значенням [7].
Верхня та нижня контрольні границі розташовані на відстані ±3σ , де σ є середньоквадратичним відхиленням. Раніше було показано, що за таких умов при нормальному розподілі випадкової величини 99,73 % її поточних значень будуть знаходитись між нижньою та верхньою контрольними границями. Тобто тільки приблизно в трьох випадках з тисячі контрольована величина вийде за межі цих контрольних границь.
Правило Шухарта полягає в тому [2,8], що спеціальний чинник, наявність якого робить виробничу систему нестабільною, є присутнім тоді, коли
значення контрольованого параметру виходить за межі будь-якої з контрольних границь. Інші дослідники внесли свої доповнення в методологію використання контрольних карт для виявлення присутності спеціального чинника. Так згідно з критеріями Нельсона сигналом наявності спеціального чинника також є розташування 9 точок поспіль з однієї сторони центральної лінії, або безперервне збільшення чи зменшення контрольованої величини в 6 послідовних точках. Описані вище ситуації показані на рис.15.
Також корисно навести правила , які були встановлені Шухартом ще в 1956 році для компанії Вестерн Електрик [2].
Згідно з цими правилами система постачає статистичний сигнал наявності спеціального чинника, що свідчить про нестабільність системи, якщо на графіку контролю поточних значень контрольованого параметру мають місце такі варіації:
•1 точка вище лінії +3σ;
•2 точки з 3 вище лінії +2σ;
•4 точки з 5 вище лінії +σ;
•8 послідовних точок вище середньої лінії;
•8 послідовних точок нижче середньої лінії;
28
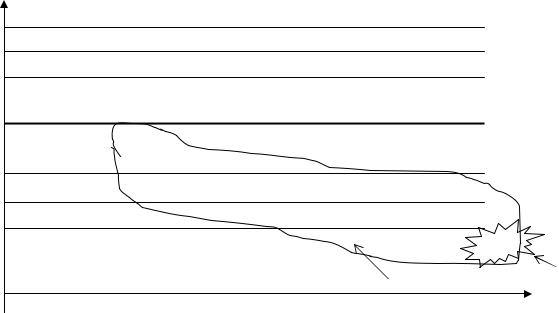
•4 точки з 5 нижче лінії -σ;
•2 точки з 3 нижче лінії -2σ;
•1 точка нижче лінії -3σ.
Виручка Верхня контрольна границя +3σ
+2σ +σ ♦
Середня лінія
♦♦
-σ |
|
♦ |
|
♦ |
|
|
|
|
|
|
-2σ |
|
|
|
♦ |
|
♦ |
|
♦ |
|
|
-3σ |
|
|
|
|
|
|
♦ |
|
♦ |
|
Нижня контрольна границя -3σ |
|
|
|
|
|
♦ |
||||
|
|
|
|
|
|
|
|
Статистичний сигнал |
||
|
|
|
|
|
|
|
|
|
Дні |
|
1 |
2 |
3 |
4 |
5 |
6 |
7 |
8 |
9 |
10 |
11 |
Рис.7. Приклад контрольної карти Шухарта
Слід зазначити, що середнє значення може бути розраховане тільки для стабільної системи за відсутності спеціального чинника. При цьому використовують не менше, ніж 25, краще 100 значень. У деяких випадках при вивченні процесів, які мають місце в системах обслуговування, зробити це важко, а іноді і неможливо, тому що кожна послуга може мати свої особливі риси, які не оцінюються однаковими значеннями контрольованого параметру. Також достатньої для статистичного аналізу сукупності абсолютно однакових послуг може просто не існувати.
Разом з тим, досвід показує, що всі ці правила не завжди дають правильну відповідь. Це викликано, перш за все, тим фактом, що реально в природі не існують абсолютно стабільні системи. Таке поняття вводиться як математична абстракція, яка з певною точністю може допомогти розв’язати практичну задачу. Також не можна визначити природу спеціальних чинників. В кінці кінців, у разі знищення всіх чинників, які за цією методологією можна називати спеціальними, залишаються звичайні чинники, які теж сприяють наявності варіацій в системі. І далі для покращення показників стабільної системи найбільш суттєві із звичайних чинників виявляються і їх дія нейтралізується, що приводить до зменшення варіацій в системі і покращення якості результату її роботи.
29
Існують три основні типи контрольних карт:
1.Контрольні карти Шухарта.
2.Контрольні карти приймального контролю.
3.Адаптивні контрольні карти.
Взалежності від кількості врахованих вибіркових спостережень контрольні карти поділяються на :
•Контрольні карти з пам’яттю (контрольні карти кумулятивних сум CUSUM, контрольні карти експоненційно зважених ковзних середніх EWMA, контрольні карти ковзних середніх та ковзних розмахів, контрольні карти трендів);
•Контрольні карти без пам’яті (контрольні карти Шухарта).
Контрольні карти класифікують в залежності від типу статистичних показників та сфери використання .
Контрольні карти Шухарта залежно від типу статистичних показників поділяють на такі види:
1.Контрольні карти для кількісних ознак даних:
•Контрольна карта середніх значень x і розмахів варіації R: ( x − R )– карти ;
•Контрольна карта середніх значень x і середньоквадратичних відхилень S: ( x − S ) – карти;
•Контрольна карта медіан ~x і розмахів варіації R: ( ~x − R ) – карти;
•Контрольна карта індивідуальних спостережень х та ковзних розмахів
MR: (х – MR) – карти.
2.Контрольні карти для альтернативних ознак даних:
•Контрольна карта часток невідповідностей, дефектів (р – карта);
•Контрольна карта кількості дефектів, дефектних виробів (np – карта);
•Контрольна карта кількості невідповідностей на одиницю продукції
(с – карта );
•Контрольна карта середньої кількості невідповідностей на одиницю продукції (u – карта).
До найпоширеніших приймальних контрольних карт належать:
•приймальні контрольні карти середніх значень x і розмахів варіацій R;
•приймальна контрольна карта часток невідповідностей продукції р;
•приймальна контрольна карта кількості дефектів с.
У залежності від мети використання існують наступні види контрольних
карт:
•Контрольна карта для регулювання технологічних процесів;
•Контрольна карта для аналізу технологічних процесів.
Контрольні карти в залежності від виду врахування в часі результатів спостережень за перебігом процесу поділяються на два види:
1)Одновимірні контрольні карти;
2)Багатовимірні контрольні карти .
30