
Варгасов Пестов_Обработка поверхности
.pdf71
межзеренные трещины, а при больших нагрузках в сильных агрессивных средах создаются условия для зарождения и роста внутризеренных трещин.
Одним из видов локальной коррозии является точечная коррозия. Точечная коррозия, имеющая форму поверхностных язвин, отличается тем, что при определенных условиях она может развиваться на микроскопических участках даже при пассивном состоянии большей части поверхности.
Точечная коррозия возникает в растворах, содержащих анионы хлора, брома, иода и катионы таких металлов как железо и медь. При возникновении зародыша точечной коррозии концентрация анионов хлора в образовавшейся язвине становится выше, чем в окружающей среде, что ускоряет рост язвин из-за снижения плотности водородных ионов (величины pH).
Еще одним видом коррозии является высокотемпературная коррозия. Во время эксплуатации при высоких температурах в условиях интенсивного течения химических и испарительных процессов на поверхности деталей часто образуется слой продуктов коррозии. Высокотемпературная коррозия включает окисление, жидкостную коррозию при высокой температуре и анодную коррозию на высокотемпературных участках при наличии температурного градиента.
Для повышения стойкости металла к высокотемпературному окислению необходимо: образование плотной и равномерной оксидной пленки и стойкость образующейся оксидной пленки к растрескиванию и отслоению. Этими особенностями обладают стали легированные хромом. Стали и сплавы с высоким содержанием хрома имеют высокую стойкость к высокотемпературному окислению в связи с тем, что хром обеспечивает быстрое образование плотной защитной пленки, состоящей из оксида Cr2О3.
5.1 Технологии металлических и оксидных покрытий.
Металлические и оксидные покрытия по своему распространению одно из ведущих мест. Несмотря на сложность нанесения, они широко применяются во всех отраслях промышленности благодаря ряду ценных специфических свойств – механической прочности, антикоррозионной стойкости и другим. В основном они применяются для покрытия мелких и средних размеров деталей.
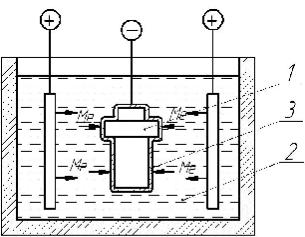
72
Рис.4.4. Схема электрохимического способа нанесения покрытия. 1 – деталь, 2 – электролит, 3 – покрытие
По своему назначению металлические покрытия делятся на три группы: защитные, защитно-декоративные и специальные..
Защитные покрытия предназначены для защиты деталей от коррозии в различных условиях эксплуатации. Защитно-декоративные покрытия предназначены для придания изделиям декоративного вида с одновременной защитой их от коррозии. Часто это многослойные покрытия. Специальные покрытия предназначены для придания изделиям определенных физико-механических свойств.
Используется несколько способов нанесения металлических и оксидных покрытий: электрохимический, химический, диффузионный и другие.
Электрохимический способ нанесения покрытий на поверхности деталей заключается в осаждении металла при пропускании электрического тока между анодом из металла, наносимого на изделие и катодом (обрабатываемым изделие).
При электрохимическом осаждении металлов на поверхности детали, прошедшие соответствующую предварительную обработку погружают в электролит и подключают как катод. Ионы металла поступают в раствор из анодов. В ванне происходят реакции: на аноде Ме → Ме+ + е-, на катоде Ме + е- → Ме.
Одним из основных требований, предъявляемых к качеству покрытия, является равномерность распределения металла на поверхностях детали.
Равномерность покрытия зависит от электрохимических свойств электролита, свойств осаждаемого металла, конфигурации детали и режима процесса электролиза. Необходимо учитывать, что на поверхности деталей распределение силы тока происходит неравномерно: плот-
73
ность тока больше на острых углах, краях, гранях и меньше во внутренних полостях, углублениях и впадинах. Вследствие этого покрытия на деталях получается различной толщины. Поэтому для обеспечения равномерности покрытия применяют профилированные, вспомогательные и экранирующие аноды. Во вторых, при конструировании изделий важно учитывать изменение частоты поверхности при электрохимическом покрытии.
В третьих, в процессе подготовительной или электрохимической обработке изделий из высокопрочных сталей часто возникает коррозионное растрескивание. В связи с этим, детали из высокопрочных сталей перед гальваническим покрытием подвергают специальной термообработке для уменьшения внутренних напряжений (t = 200ºС, τ = 1 час) или обработке для создания на поверхности сжимающих напряжений. Кроме того, высокопрочные стали чувствительны к водородному охрупчиванию под действием атомарного водорода, возникающего на катоде в результате реакции H+ + e- → H. Чтобы удалить водород эти детали необходимо термообработать после нанесения покрытия. Обычно термообработка проводится при температуре 200 С в течении 1-6 час.
Таблица 5.2.Изменение шероховатости поверхности детали после нанесения покрытия.
|
шероховатость поверхности Ra, мкм |
||
Вид покрытия |
|
|
|
до нанесения по- |
после нанесения |
||
|
|||
|
крытия |
покрытия |
|
Никелирование |
5,0 – 0,32 |
5,0 – 0,32 |
|
Хромирование |
5,0 – 0,63 |
5,0 – 0,63 |
|
Цинкование |
1,25 – 0,32 |
5,0 – 0,63 |
|
Кадмирование |
1,25 – 0,32 |
2,5 – 0,63 |
|
Лужение |
2,5 – 0,32 |
2,5 – 0,32 |
|
Фосфатирование |
5,0 – 1,25 |
10 – 2,5 |
|
|
|
|
Кроме того, высокопрочные стали чувствительны к водородному охрупчиванию под действием атомарного водорода, возникающего на катоде в результате реакции H+ + e- → H. Чтобы удалить водород эти детали необходимо термообработать после нанесения покрытия. Обычно термообработка проводится при температуре 200 С в течении 1-6 час.
74
Кгруппе горячих способов нанесения металлических покрытий относятся горячее лужение, цинкование, металлизация распылением и диффузионные покрытия.
Горячее лужение и цинкование осуществляется погружением очищенной и флюсованной детали в расплав металла. Цинковое покрытие благодаря хорошему растворению цинка в железе состоит из нескольких сплошных железоцинковых слоев. Покрытие железа цинком – типично анодное покрытие, которое защищает металл двояко: изолируя металл от внешней среды и электрохимически.
Металлизация распылением представляет собой процесс нанесения расплавленного и распыленного металла на различные поверхности под действием сжатого воздуха. Для нанесения такого покрытия применяют специальные распылители-металлизаторы.
Структура металлизационного покрытия отличается значительной пористостью. Покрытия такого вида применяются в основном как защитные (медь и цинк по стали).
В последнее время стало широко применяться оплавление гальванических оловянных покрытий. Эта операция устраняет пористость, чем способствует уменьшению толщины оловянного покрытия с 9 мкм до 3 мкм при одинаковом эффекте.
Коксидным покрытиям относятся: оксидирование стали (воронение), меди и ее сплавов, анодное оксидирование алюминия, оксидирование титана и его сплавов.
Защитная пленка таких покрытий состоит из нерастворимых соединений и оксидов металла. В процессе образования пленки (особенно
врастворах) поверхность защищаемого металла разрыхляется, и ионы металлов непосредственно участвуют в создании оксидных защитных пленок.
Толщина защитных пленок примерно равна 1 мкм за исключением анодирования и воронения в щелочном растворе, где толщины могут доходить до 400 мкм при анодировании и 10 мкм при щелочном воронении.
Если при электрохимическом нанесении покрытий рост покрытия происходит от поверхности детали, то рост пленки у большинства оксидных покрытий происходит от поверхности в глубину металла.
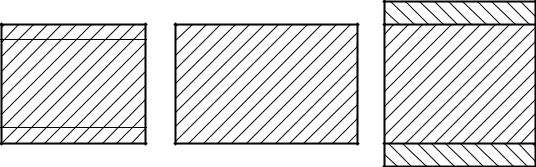
75
Оксидное |
Гальваническое |
покрытие |
|
покрытие |
ДЕТАЛЬ |
Рис. 5.4. Схема образования оксидной пленки.
Таблица 5.3. Характеристика металлических и оксидных покрытий.
Вид покрытия |
Характеристика покрытия |
Кадмиевое |
Покрытие анодное для деталей из стали и меди в усло- |
|
виях морского и влажного тропического климата. Сталь- |
|
ные детали при кадмировании наводораживаются, сни- |
|
жая прочность. Хрупкость может быть устранена отжи- |
|
гом при температуре 150-200 С. |
Цинковое |
Нормальный электродный потенциал цинка – 0,76в. |
|
Покрытие анодное в условиях морского и тропического |
|
климата. Применяется с обязательной обработкой в хро- |
|
матных растворах. Стальные детали (пружины, крепеж и |
|
другие) наводараживаются, что приводит к снижению |
|
прочности. Хрупкость устраняется отжигом. |
Никелевое |
Нормальный электродный потенциал никеля – 0,25 в. |
|
Покрытие катодное для стали и анодное для меди и ее |
|
сплавов. Твердость гальванического покрытия НВ 185- |
|
420. |
Хромовое с подслоем |
Покрытие катодное для алюминия и анодное для меди. |
никеля (блестящее) |
Не тускнеет на воздухе, длительно сохраняет декоратив- |
|
ные свойства. |
Хромовое с подслоем |
Нормальный электродный потенциал – 0,71 в. Покры- |
меди и никеля (бле- |
тие катодное для алюминия и анодное для меди и стали. |
стящее) |
Толщина покрытия 50 мкм устойчиво в различных кли- |
|
матических условиях. Применяется для деталей конфигу- |
|
рации. |
Оксидное для стали |
Защитный эффект незначителен. Применяется для за- |
|
щиты мелких деталей. Качество защиты улучшается с |
|
увеличением частоты обработки и пропиткой в масле. |
|
Толщина покрытия 0,5-1,0 мкм |
Анодизационное для |
Покрытие изоляционное, электрическая прочность до |
алюминия и его спла- |
650 ОМ; после пропитки лаком – до 1400 ОМ. Толщина |
вов |
покрытия 0,3 – 60 мкм. |
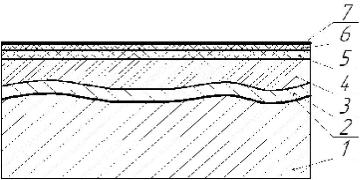
76
Наиболее сложным процессом получения оксидных покрытий является анодное оксидирование алюминия и его сплавов. Анодные пленки состоят из основной тонкой части ~ 1 мкм и пористой гидроокисной пленки ~ 100 мкм.
Наиболее широкое распространение получили следующие виды анодирования: в серной кислоте на толщину 5-15 мкм, в щавелевой кислоте на толщину 10-60 мкм.
Некоторые характеристики основных видов металлических и оксидных покрытий приведены в таблице 5.3.
4.2 Лакокрасочные покрытия.
Лакокрасочные покрытия являются наиболее доступным и эффективным способом защиты металлических изделий от коррозии. Выгодно отличаясь от других видов защитных покрытий своей дешевизной, простотой нанесения и надежностью, лакокрасочные покрытия нашли широкое применение в промышленности. В настоящее время более 80% всех металлических изделий защищают от коррозии лакокрасочными покрытиями.
Для получения лакокрасочного покрытия, обладающего одновременно надежными защитными свойствами и хорошим внешним видом, применяют способ многослойного нанесения лакокрасочных материалов (система покрытия).
Рис.5.5. Схема защитного покрытия стали. 1 – сталь; 2 – фосфатный слой; 3 – грунт; 4 – шпатлевка; 5 – первый слой эмали; 6 – второй слой эмали; 7 – лак.
Подбирая лакокрасочные материалы с хорошей адгезией, используя в системах одновременно защитные свойства одного материала и декоративные свойства другого, можно получить многослойные комбинированные системы лакокрасочных покрытий, превышающие по стойкости металлические и другие виды покрытий.
77
Схемы систем защитно-декоративных и специальных покрытий приведены в таблице.
Таблица 5.4. Схемы систем покрытий.
Защитно-декоративные по- |
Защитные и специальные |
|||
крытия |
|
покрытия |
|
|
поверхности |
поверхности |
цветные и |
при эксплуата- |
Цветные ме- |
с грубой об- |
с чистой об- |
черные ме- |
ции в помеще- |
таллы |
работкой |
работкой |
таллы |
ниях |
|
Грунт |
Грунт |
Грунт |
Эмаль |
Лак |
Шпаклевка |
Эмаль |
Эмаль |
|
|
Эмаль |
2 слоя |
2-3 слоя |
|
|
|
|
|
|
|
2 слоя |
|
|
|
|
Лак |
|
|
|
|
Главными составными частями всякого лакокрасочного покрытия является пленкообразующее вещество и пигмент. Защитные свойства лакокрасочного покрытия обусловлены тем, что на поверхности защищаемого материала образуется сплошная пленка, которая, изолируя поверхность материала от окружающей среды, препятствует проникновению к ней агрессивных веществ и тем самым предохраняет металл от коррозии. Природа окрашиваемого металла определяет адгезию. По признаку убывающей адгезионной способности металлы можно расположить в следующий убывающий ряд: никель – сталь – медь – латунь – алюминий – олово – свинец. Наличие на поверхности окрашиваемого металла оксидов или окалины усиливают дальнейший процесс коррозии. Различные загрязнения, влага, пыль снижают прилипаемость покрытия.
Технология нанесения лакокрасочных покрытий состоит из следующих последовательных операций: подготовка поверхности металла, нанесение покрытий, сушка и отделка покрытий.
Подготовка поверхности металла состоит в удалении дефектов поверхности, удалении продуктов коррозии, обезжиривании и специальной подготовке (фосфатирование, оксидирование, пассивация).
78
Таблица 5.5.Оптимальная толщина покрытий.
Тип покрытия |
|
Толщина одного слоя, мкм |
|
||
|
|
|
|
|
|
|
Грунт |
|
Эмаль, краска |
|
Лак |
Перхлорвиниловые |
10 – 40 |
|
15 – 25 |
|
10 – 15 |
Масляные |
10 – 15 |
|
20 – 25 |
|
10 – 20 |
Нитроэпоксидные |
- |
|
15 – 20 |
|
- |
Алкидностирольные |
10 – 15 |
|
20 – 25 |
|
15 – 20 |
Полиуритановые |
10 – 15 |
|
15 – 20 |
|
10 – 15 |
Эпоксидные |
10 – 20 |
|
20 – 30 |
|
10 – 20 |
Фенольные |
10 – 15 |
|
20 – 25 |
|
- |
|
|
|
|
|
|
Процесс нанесения лакокрасочного покрытия включает в себя грунтование, шпатлевание, шлифование шпатлевки, окрашивание. Грунт является основой всякого покрытия. Правильно выбранный грунт обеспечивает хорошую адгезию с поверхностью и хорошее сцепление с последующими слоями лакокрасочного покрытия. Шпатлевание производится с целью выравнивания поверхности. Шпатлевка улучшает внешний вид покрытия, но в тоже время снижает его механическую прочность. Поэтому покрытия, эксплуатируемые в жестких условиях воздействия агрессивных сред, наносятся без шпатлевки.
Окрашивание осуществляется следующими способами: воздушным распылением, распылением в электрическом поле, окунанием, валиками, методом электрофореза, кистью и другими.
Операция сушки заключается в повышении температуры с целью превращения низкого лакокрасочного материала в твердую пленку. Применяются следующие виды сушки: конвекционная, терморадиационная, сушка в электрическом поле.
К операции отделка покрытия относится выравнивание слоев покрытия и полирование последнего слоя покрытия. Эти операции выполняются с использованием пневматических шлифовальных машинок.
79
6. Износостойкие покрытия инструмента
6.1. Основные положения.
Все элементы Периодической системы подразделяются на группы электронных аналогов, атомы которых имеют аналогичные строения электронных оболочек:
-s-элементы, имеющие полностью заполненные внешние s- оболочки;
-d - и f - элементы, имеющие незаполненные d- и f - оболочки;
-sp-элементы, имеющие валентные s, p - электроны (неметаллы). Данной классификация поясняет деление всех тугоплавких соеди-
нений, применяемых в качестве покрытий, на три группы:
-металлоподобные тугоплавкие соединения, образуемые d- и f - переходными металлами (бориды, карбиды, нитриды);
-металлоподобные тугоплавкие соединения, образуемые между собой в основном d- и f-переходными металлами, а также вырожденными металлами из sp-групп электронных аналогов;
-неметаллические тугоплавкие соединения, образуемые взаимным сочетанием неметаллов (оксиды).
Наиболее широко в качестве износостойких покрытий применяются соединения тугоплавких d-переходных металлов IV-VI Периодической системы элементов с кислородом, углеродом и азотом [5]. Это связано с особенностями их кристаллохимического строения:
1.эти металлы имеют недостаток электронов на внутренних s, p и d орбиталях, и это приводит к тому, что они с достаточной легкостью могут приобретать электроны из любого источника, которым может служить междоузельные атомы углерода, азота и кислорода.
2.большинство переходных металлов имеют достаточно большие атомные радиусы и при образовании соединений с атомами C, N и O могут подчинятся правилу Хэгга, согласно которому отношение радиуса атома неметалла к радиусу атома металла меньше критического значения 0,59. Для соединений металлов IV группы (Ti, Zr, Hf) достаточно точно выдерживается правило Хэгга, что приводит к образованию простых структур, в которых превалирует связь металл-металл, а атомы C, H, O можно рассматривать как вставленные в решетку атомов металла.
3.большинство переходных металлов имеют широкие области гомогенности, что позволяет в зависимости от содержания кислорода, азота и углерода достаточно сильно изменять физико-механические свойства их карбидов, нитридов и оксидов.
80
4. переходные металлы и некоторые их соединения, в первую очередь соединения с простой кубической структурой типа NaCl (ZrC, ZrN, TiN, VC, TaC), отличаются очень высокими температурами плавления.
Соединения металлов IV-VI групп с кислородом, углеродом и азотом можно рассматривать и как наиболее устойчивые (в термодинамическом отношении) материалы для покрытий, способные противостоять твердо- и жидкофазным диффузионным реакциям, коррозии и окислению при высоких температурах. Свойства соединений тугоплавких металлов с О, N и С при обычных и повышенных температурах сильно зависят от многих факторов: состава (стехиометрии), наличия примесей, микроструктуры и текстуры, пористости и т.д.
6.2.Соединения, используемые в качестве покрытий.
Карбиды. Карбиды обладают рядом противоречивых свойств. В частности, строение монокарбидов с кубической решеткой соответствует структуре типа NaCl, вместе с тем электропроводность карбидов сравнима с электропроводностью металлов. Высокая твердость карбидов проявляется за счет ковалентной связи атома углерода с атомом метала.
Наибольшая склонность к образованию энергетически стабильных конфигураций sp3 проявляются у карбидов металлов IV группы (Ti, Zr, Hf). Это обусловлено большей донорской способностью этих металлов (особенно Ti) при относительно высоком содержании углерода в карбиде (до 20%). Стабильные конфигурации карбидов атомов металлов IV группы объясняется уменьшением общего числа нелокализованных электронов sp-переходов, смещения равновесия вправо и уменьшения общего числа нелокализованных электронов: sp2 + p ( sp3. Поэтому карбиды обладают повышенной жесткостью кристаллической решетки, определяющей их высокую твердость, теплостойкость и хрупкость [5].
При переходе к карбидам V группы донорская способность металлов этой группы снижается, что приводит к снижению статистического веса устойчивости sp3-конфигурации карбидов и соответственно уменьшает соответственно твердость этих карбидов. Область их гомогенности сужается, в составе наряду с карбидами МС образуются низшие карбиды М2С с гексагональной структурой. Так например, твердость TiC равна 31,7 ГПа, а твердость TaC – 17,4 ГПа, Nb2C – 21 Гпа
[5].
У карбидов тугоплавких металлов VI группы (Cr, Mo, W) содержание углерода падает до 6%, снижается число обобществленных электронов, поэтому статический вес атомов наиболее стабильной элек-