
Варгасов Пестов_Обработка поверхности
.pdf11
Из-за направленности ковалентной связи координационное число и коэффициент компактности ковалентных кристаллов всегда меньше чем у металлических кристаллов. Например, координационное число алмаза равно 4, а плотность упаковки всего 0,34. Белое олово с его частично металлическими, а частично ковалентными связями имеет плотность упаковки всего 0,55.
Наиболее распространенным примером ионных кристаллов являются соединения CaO, FeO, Li, F, MgO, MnS, NaCl и др. В каждой их этих структур число атомов металла равно числу неметаллических атомов. Кроме того, отношение радиусов ионов таково, что каждый катион могут окружать не более шести атомов. Соединения, содержащие более крупные катионы, обычно имеют координационное число 8.
У многих материалов кристаллическая решетка может изменяться при определенных условиях. Способность материала образовывать несколько кристаллических структур (модификаций) называют полиморфизмом. Полиморфизм широко распространен среди технических материалов и имеет большое значение при их обработке.
Таблица 1.1. Металлы с полиморфным превращением.
Металл |
Тип решетки |
Температура превра- |
|
|
|
|
щения, ºС |
Ti |
ГП |
↔ ОЦК |
882 |
|
|
|
|
Fe |
ОЦК |
↔ ГЦК |
911 |
|
ГЦК |
↔ ОЦК |
1392 |
1.3. Дефекты кристаллического строения.
Идеальная кристаллическая решетка представляет собой многократное повторение элементарных кристаллических ячеек. Однако для реального кристаллического тела характерно наличие большого количества дефектов строения, нарушающих периодичность расположения атомов в кристаллической решетке. Эти дефекты оказывают существенное влияние на многие свойства кристаллических материалов.
Дефекты кристаллического строения принято классифицировать по их размерам. Различают три типа дефектов кристаллического строения: точечные, линейные, планарные.
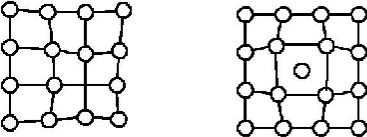
12
Точечные дефекты. Локальные несовершенства кристаллической структуры характерны для большинства кристаллов. Обычно они проявляются в виде вакансий и межузельных атомов. (Рис.1.8.)
а б Рис.1.8. Точечные дефекты. а - вакансия; б - межузельный атом.
Прежде всего, точечные дефекты можно представить как неправильности кристаллизации, например, нарушения соответствия между числом имеющихся атомов и числом возможных мест в кристаллической решетке. На практике такие несовершенства могут возникать в результате теплового возбуждения, смещающего атомы из их мест в идеальной решетке.
Вокруг вакансии или межузельного атома кристаллическая решетка искажена. Точечный дефект можно рассматривать как центр сжатия или расширения в упругой среде. В г.ц.к. решетке вокруг вакансии ближайшие соседи смещены в сторону вакансии на величину около 2%. Поскольку вакансия стремиться стянуть решетку вокруг себя, то ее можно рассматривать как центр всестороннего растяжения, а межузельный атом как центр напряжений сжатия.
Вакансии и межузельные атомы играют важную роль в процессе диффузии. Если имеется вакантное место в кристаллической решетке, то диффузия осуществляется путем последовательного перескока в него соседних атомов. Такой процесс перемещения атомов в кристалле называют самодиффузией.
К точечным дефектам можно отнести и атомы примесей замещения и внедрения. Так, примесный атом, близкий по объему с основным атомом решетки, может располагаться в узле решетки, вытесняя оттуда основной атом и создавая атом замещения. При этом атом замещения создает вокруг себя упругие напряжения двух типов в зависимости от симметрии и размеров атомов растворителя и растворяемого элемента. Обычно примесный атом с той же формой симметрии и размера, что и у основной решетки, не создает существенных напряжений. Поэтому он слабо взаимодействует с другими дефектами и не оказывают заметного упрочняющего воздействия. В другом случае, когда форма и размеры
13
атомов растворителя и растворяемого элемента не совпадают, то возникают значительные напряжения, величина которых зависит от характера различия.
Атом примеси замещения может диффундировать по решетке при помощи вакансионного механизма перескоков на место подошедшей вакансии. Такой процесс движения атомов примесей называют гетеродиффузией.
Все соображения о распределении примесных атомов замещения и о создаваемых ими полях напряжений справедливы и для атомов внедрения. Однако примесные атомы внедрения имеют относительно большую подвижность. Роль примесных атомов внедрения возрастает при переходе к решеткам с меньшим координационными числами.
Линейные дефекты. Наиболее важным видом несовершенств, определяющим механические свойства материалов, являются линейные дефекты - дислокации. Дислокация представляет собой линейный дефект, выявляющийся лучше всего при рассмотрении кристалла после незавершенного сдвига.
На рис. 1.9 показан кристалл в виде параллелепипеда, верхняя часть которого сдвинута относительно нижней на одно межатомное расстояние. Причем зафиксировано положение, когда сдвиг охватил не всю плоскость скольжения от левой грани параллелепипеда до правой, а лишь часть плоскости скольжения. Дислокация, таким образом, является границей незавершенного сдвига.
Одна из вертикальных атомных плоскостей в верхней части кристалла уже не имеет продолжения в нижней части кристалла. Такую «лишнюю», неполную атомную плоскость называют экстраплоскостью. Область несовершенства кристалла вокруг края экстраплоскости называется краевой дислокацией.
Если дислокация вводится в кристалл чистым сдвигом – так, как показано на рисунке, то вектор сдвига называется вектором Бюргерса, который определяет величину и направление смещений атомов в той области, где сдвиг уже произошел, т.е. определят степень искаженности решетки, связанную с присутствием дислокации.
По мере развития процесса скольжения, элементарные ячейки верхней части кристалла сдвигаются. Однако в результате того, что скольжение происходит на один полный период, большинство ячеек в нижней части кристалла сохраняют первоначальную структуру. Продолжающийся процесс скольжения вызовет движения дислокации в кристалле, приводя к распространению сдвигового смещения.
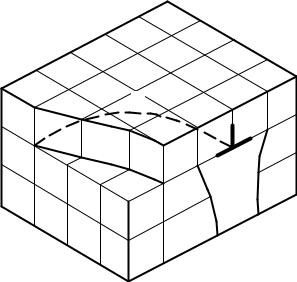
14
Ä
Рис.1.9. Дислокация, образовавшаяся в результате незавершенного сдвига.
В общем виде, величину пластической деформации, вызванную движением дислокаций можно оценить по формуле:
ε = ρ·b·ℓ, |
(1.5) |
где ρ – плотность дислокаций, движущихся в любой из возможных плоскостей скольжения, b – вектор Бюргерса (вектор сдвига), ℓ - длина свободного пробега дислокаций.
Очевидно, что для продолжения пластической деформации необходимо увеличивать количество дислокаций их размножением. Однако увеличение плотности дислокаций сдерживает их зарождение, что приводит к увеличению напряжения необходимого для продолжения пластического деформирования. Это явление называют деформационным упрочнением, величину которого можно оценить по формуле:
Δσ = G·b·ρ0,5, |
(1.6) |
где G – модуль сдвига, b – вектор Бюргерса, ρ – плотность дислокаций.
Плотность дислокаций ρ равна суммарной длине дислокаций ∑ℓ в единице объема V:
Ρ = ∑ℓ/V |
(1.7) |
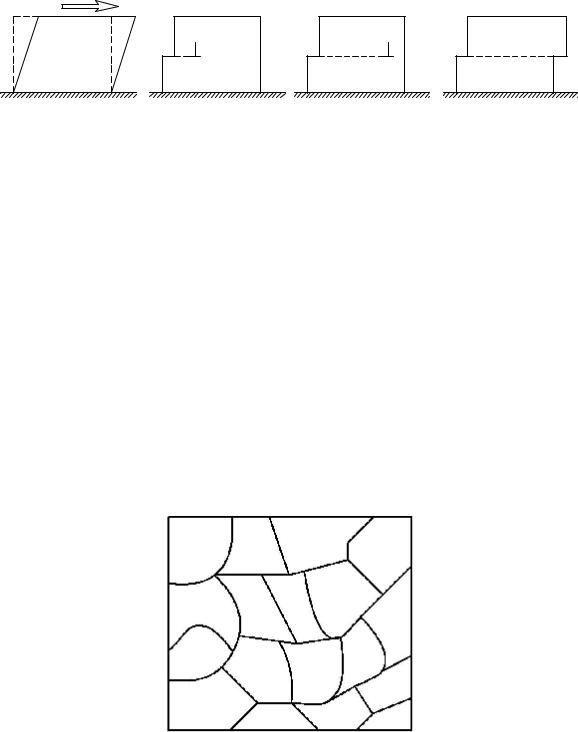
15
В металлических монокристаллах ρ~104 – 106 см-2, поликристаллах ρ~10-7 – 10-8 см-2, в деформированных кристаллах ρ~10-11 – 10-12.
τ
а б в г Рис. 1.10. Схема сдвига, обусловленного движением дислокации: а –
упругая деформация, б – зарождение дислокации, в – скольжение дислокации, г – аннигиляция дислокации
Планарные дефекты. Применяемые в технике материалы обычно являются поликристаллическими. Если твердое тело содержит более одного кристалла, то возникают области несогласованности в местах соприкосновения соседних кристаллов. Каждый отдельный кристалл называют зерном, а область несогласованности – границей зерен.
Границы с разориентацией соседних зерен менее 10° относят к малоугловым, а с большей разориентацией – к большеугловым.
Малоугловые границы образованы системами дислокаций и располагаются внутри зерен, разделяя их на субзерна. Границы зерен, выросшие из разных центров при кристаллизации и фазовых превращениях в твердом состоянии, чаще всего бывают большеугловыми.
Рис.1.11. Схема строения поликристалла.
Ориентировка плоскостей кристалла и, следовательно, свойства фактически претерпевают скачок при переходе через границу зерен. Этот скачок свойств при переходе через границу оказывается важным фактором, определяющим поведение материала при механических на-
16
грузках. Так границы являются эффективными барьерами для движущихся дислокаций. Упрочнение границами в поликристалле может быть описано формулой Петча Холла:
Δσ = К/d0,5, |
(1.8) |
где К – коэффициент, d – средний диаметр зерна.
В целом можно сделать вывод, что с помощью границ можно создать значительное упрочнение, хотя и связанное с уменьшением пластичности. Для этого границы должны быть непроницаемыми для дислокаций и расположены близко друг к другу. Упрочнение оказывается тем более эффективным, чем меньше вероятность размножения дислокаций и число работающих систем скольжения. Таким образом, наибольший эффект упрочнения может наблюдаться в ультрамелкозернистых и нанокристаллических материалах.
Атомы в границах зерен имеют повышенную энергию по сравнению с атомами внутри зерна, так как атомы, расположенные вдоль границы имеют меньшие координационные числа, чем атомы, расположенные в решетке кристалла. Кроме того, плотность дефектов в границах зерен значительно больше, чем в зернах и поэтому границы зерен характеризуются повышенной энергией и образуют эффективные диффузионные каналы, способствующие перемещению атомов в твердом теле (зернограничная диффузия).
1.4. Структура поверхности.
Находящиеся на свободной поверхности атомы характеризуются меньшим координационным числом, т.к. с внешней стороны они лишены соседей. Следовательно, поверхностные атомы будут иметь более высокую энергию по сравнению с находящимися во внутренних слоях. Эта избыточная энергия может быть названа поверхностной энергией.
В зависимости от положения поверхности к кристаллографическим плоскостям кристалла различают поверхности трех видов: сингулярные, вицинальные и несингулярные.
Сингулярные поверхности совпадают с кристаллографическими плоскостями с малыми индексами. Особенность сингулярных поверхностей состоит в том, что они являются совершенно гладкими в атомном масштабе и не имеют ступенек. К таким поверхностям относятся, например, поверхности, совпадающие, например, с плоскостью (111) в ГЦК кристаллах.
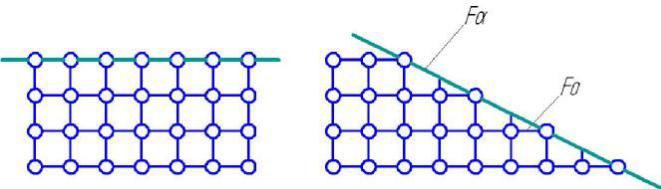
17
Вицинальные поверхности располагаются в небольшом диапазоне разориентаций около сингулярной ориентации, т.е. образуют небольшие углы с кристаллографическими поверхностями, имеющие малые индексы. Эти поверхности не идеально плоские и на них имеются ступени.
а |
б |
Рис.1.12. |
Сингулярная (а) и вицинальная (б) поверхности. |
Удельная поверхностная энергия вицинальной поверхности Fα отличается от энергии Fo сингулярной поверхности незначительно. Если ln – длина одной ступени, а l – ее высота, то величина Fα, приходящаяся на единицу длины основной сингулярной поверхности составит:
Fα = Fo + |
R |
×tgα |
, |
(1.9) |
|
l |
|||||
|
|
|
|
где R – энергия, связанная с наличием одной ступени.
При температуре абсолютного нуля ступени вицинальной поверхности являются гладкими. С повышением температуры на них образуются изломы, выступы и впадины, в результате чего вацинальная поверхность приобретает сложное строение.
Несингулярные поверхности характеризуются высокой плотностью ступеней. Они пересекаются с кристаллографическими плоскостями под достаточно большим углом.
Приведенная классификация поверхностей весьма условна, поскольку ограничивается кристаллографическим рассмотрением и не учитывает других особенностей поверхностей. Реальная поверхность отличается от описанных выше наличием на ней большого количества кристаллографических дефектов. Основными типами дефектов, присущих любой поверхности являются точки выхода дислокаций, следы выхода границ, вакансий и т.д. (Рис.1.13). Таким образом, неупорядоченность на поверхности кристаллов больше, чем неупорядоченность внутри кристалла.
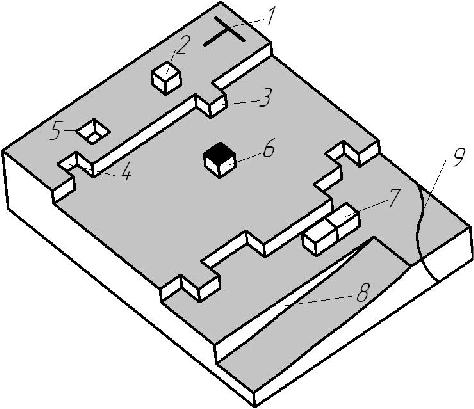
18
Важным свойством поверхности является адсорбция (поверхностное поглощение). Адсорбция – это способность вещества концентрировать на своей поверхности другие вещества, находящегося в контакте с поверхностью. Если молекулы адсорбата на поверхности адсорбента сохраняют свою индивидуальность, имеет место физически обратимая адсорбция. При химической адсорбции (хемосорбции) молекулы адсорбента образуют поверхностное химическое соединение с адсорбентом; обычно этот процесс является необратимым.
Рис.1.13. Схема строения реальной поверхности.
1 – выход краевой дислокации; 2 – адатом; 3 - адатом на ступени; 4 – вакансия на ступени; 5 – вакансия; 6 – примесный атом; 7 – пара адатомов; 8 – выход винтовой дислокации; 9 – выход границы;
Особенность твердой поверхности состоит в том, что не все участки ее обладают одинаковыми адсорбционными свойствами. Так, различные микровыступы обладают значительно более высокой способностью к адсорбированию, чем гладкие участки. Такие активные центры занимают незначительную часть поверхности твердого тела, тем не менее, их значение очень велико. Кроме того, вследствие анизотропии по-
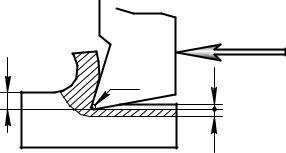
19
верхностной энергии кристаллических тел адсорбция может идти неодинаково на различных гранях кристалла.
Адсорбционные явления играют весьма значительную роль во многих практически важных случаях. Хорошо, например, известно адсорбционное понижение прочности, или эффект Ребиндера, выражающийся в том, что очень малое количество поверхностноактивного вещества способно вызывать в короткий срок резкое ухудшение механических характеристик металла. В частности, некоторые металлы в присутствии адсорбированных поверхностно-активных веществ утрачивают пластичность и разрушаются хрупко.
2. Формирование поверхностного слоя при обработке
Важнейшие эксплуатационные свойства деталей машин зависят не только от их размерной точности, но и от состояния их поверхностей, которое определяется совокупностью характеристик: структуры, шероховатости, остаточных напряжений, твердости и др.
2.1. Упрочнение поверхностного слоя при обработке резанием
При обработке заготовок резанием в материале поверхностного слоя происходит пластическая деформация, которая сопровождается изменением структуры. Во-первых, наблюдается вытягивание зерен в направлении действия растягивающих напряжений, во-вторых, при больших деформациях поверхностного слоя наблюдается фрагментация зерен, в-третьих, увеличивается плотность дислокаций, и образуются их скопления. При этом увеличивается удельный объем металла и понижается его плотность, повышается прочность и снижается пластичность. Совокупность изменений структуры и свойств металла при пластической деформации называют наклёпом.
|
|
Ððåç |
t |
r |
à |
|
||
|
|
á |
Рис. 2.1. Схема формирования наклепанного слоя: t – глубина резания, а – величина упругой деформации металла, б - глубина наклепанного слоя.
20
Основным фактором, определяющим изменение строения и свойств металлов в результате наклепа, является накопление энергии в деформированных металлах и сплавах. Эта накопленная (латентная) энергия деформирования определяет необратимые изменения кристаллического строения.
Необратимые изменения строения структуры при деформировании в свою очередь определяются зарождением дефектов решетки – вакансий и, главным образом, дислокаций, что следует из рассмотренного ранее дислокационного механизма пластической деформации.
Многочисленные исследования металлических кристаллов показали, что в процессе деформирования происходят следующие изменения строения.
При малых степенях деформации почти вся поглощенная энергия расходуется на создание дефектов кристаллического строения устойчивых при данной температуре. Хотя с повышением величины деформации (увеличением затраченной работы) образование дефектов кристаллического строения и продолжается, часть дефектов исчезает в ходе процесса деформации, так как увеличение затраченной работы понижает энергию активации процесса аннигиляции дислокаций в связи с локальным выделением тепла и повышением температуры.
При механической обработке в зоне резания одновременно действуют значительные усилия резания, создающие наклеп, и теплота, вызывающая разупрочнение металла. Таким образом, конечное состояние металла поверхностного слоя будет определяться соотношением скоростей протекания процессов упрочнения и разупрочнения.
Степень и глубина наклепанного слоя изменяются в зависимости от метода и режима механической обработки, геометрии режущего инструмента и других факторов. Однако всякое изменение режима резания, вызывающее увеличение силы резания и степени пластической деформации, ведет к увеличению наклепа. Рост продолжительности воздействия усилий резания на металл поверхностного слоя приводит к увеличению глубины наклепанного слоя. Глубина наклепанного слоя (б) обычно составляет 30 – 100 мкм.
Экспериментально установлено, что в процессе обработки точением наклеп поверхностного слоя повышается при увеличении подачи и глубины резания, с возрастанием радиуса режущего лезвия и при переходе от положительных передних углов резца к отрицательным.
Влияние скорости резания проявляется через изменение теплового воздействия, продолжительности воздействия силы резания и нагрева