
Варгасов Пестов_Обработка поверхности
.pdf21
на металл поверхностного слоя. Для металлов, не претерпевающих при резании фазовых превращений, при повышении скорости резания следует ожидать снижения степени наклепа. Аналогично точению увеличение подачи и глубины резания при фрезеровании повышается степень наклепа.
Общие закономерности возникновения наклепа при лезвийной обработке сохраняются и при абразивной обработке: наклеп возрастает при увеличении нагрузки на абразивное зерно, что связано с увеличением глубины шлифования, размера и радиуса кромок абразивных зерен. При повышении частоты вращения круга нагрузка на абразивные зерна снижается, а количество теплоты, выделяющейся в зоне шлифования, увеличивается. Упрочнение поверхностного слоя при этом уменьшается.
2.2. Остаточные напряжения в поверхностном слое
Механические напряжения уравновешенные внутри тела и сохраняющиеся после снятия внешних воздействий принято называть остаточными. Возникновение остаточных напряжений в поверхностном слое при обработке резанием можно объяснить следующими причинами.
Во-первых, воздействие режущего инструмента на поверхность обрабатываемого материала приводит к пластической деформации поверхностного слоя и наклепу. Увеличение плотности дефектов кристаллической решетки при пластической деформации вызывает уменьшение плотности металла на величину 0,3 – 0,8%. Однако увеличение объема металла распространяется только на глубину пластически деформированного слоя и не затрагивает слои металла, лежащих ниже.
Увеличению объема пластически деформированного металла поверхностного слоя препятствуют связанные с ним недеформированные слои, в результате чего в наружном поверхностном слое возникают сжимающие, а нижележащих слоях – растягивающие остаточные напряжения.
Вторая причина возникновения остаточных напряжений в поверхностном слое состоит в том, что выделяющаяся в зоне резания теплота нагревает тонкие поверхностные слои металла до высоких температур, что вызывает увеличение его удельного объема. После прекращения воздействия режущего инструмента происходит быстрое охлаждение металла поверхностного слоя, сопровождающееся его сжатием, чему
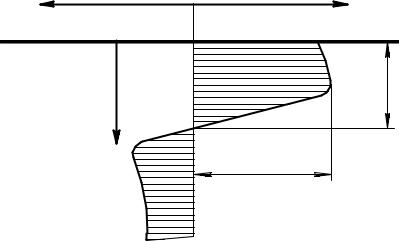
22
препятствуют нижележащие слои металла. В результате во внешних слоях металла развиваются остаточные напряжения растяжения.
В – третьих, при обработке металлов и сплавов, в которых при нагреве и охлаждении происходят фазовые превращения, происходит изменение объема. В этом случае в слоях металла со структурой, имеющей больший удельный объем, развиваются напряжения сжатия, а в слоях со структурой меньшего удельного объема – остаточные напряжения растяжения. Знак и глубина распространения остаточных напряжений, возникающих в результате фазовых превращений, определяется полнотой протекания фазовых превращений и соотношением удельных объемов фаз смежных слоев. При этом большое значение для формирования остаточных напряжений имеют химический состав и физикохимические свойства обрабатываемого материала.
Любая из названных причин образования остаточных напряжений при обработке резанием может преобладать. При этом она будет определять величину и характер распределения остаточных напряжений. Изменение режимов обработки меняет характер напряженнодеформированного состояния в зоне резания и мощность тепловой энергии. Поэтому изменяется как величина, так и знак остаточных напряжений в поверхностном слое.
Установлено, что многие механические свойства материалов зависят от наличия остаточных напряжений в поверхностном слое. Так, если в поверхностном слое существуют остаточные сжимающие напряжения (рис.2.2), то неглубокие трещины будут расти медленнее, чем в случае, если бы остаточные напряжения отсутствовали. Наоборот, если бы трещина попала в ту область поверхности, в которой действуют растягивающие напряжения, то трещина будет расти быстрее.
растяжение |
сжатие |
поверхность |
|
глубина |
|
|
σmax |
Рис. 2.2. Схема распределения остаточных напряжений |
23
Учитывая наличие в поверхностных слоях остаточных напряжений можно ввести понятие об эффективном напряжении, вызывающем разрушение:
σэфф = σприл + σост, |
(2.1) |
где σэфф – эффективное напряжение, σприл – приложенное напряжение, σост – остаточное напряжение.
При условии воздействия растягивающих остаточных напряжений σост < 0 σэфф < σприл, и поэтому разрушение будет развиваться при напряжении меньшем приложенного.
Влияние остаточных напряжений на эксплуатационные свойства деталей машин хорошо изучено. Так, анализ результатов исследований состояния поверхностного слоя и его влияние на износостойкость позволяют сделать вывод о том, что остаточные напряжения поверхностного слоя детали, возникающие в процессе ее обработки, не влияют на износостойкость. Этот вывод основан на экспериментальных результатах, которые показали, что в процессе трения и изнашивания в металле поверхностного слоя протекает такая интенсивная пластическая деформация, которая не может быть создана никакой механической обработкой. Таким образом, эта пластическая деформация полностью нейтрализует остаточные напряжения в поверхностном слое.
Однако остаточные напряжения оказывают существенное влияние на усталостную прочность деталей машин. Установлено, что при наличии в поверхностном слое остаточных напряжений сжатия предел выносливости повышается, а при наличии остаточных напряжений растяжения – снижается. Причем влияние остаточных напряжений на предел выносливости особенно велико, когда разница в прочности материала при растяжении и сжатии большая. Поэтому предел выносливости высокопрочных сталей зависит от величины и знака остаточных напряжений особенно сильно, в то время как у сталей низкой прочности, но обладающих высокой пластичностью эта зависимость проявляется в меньшей степени.
2.3. Шероховатость поверхности
Реальная поверхность детали создается в процессе ее изготовления и отличается от номинальной поверхности, так как всегда имеют
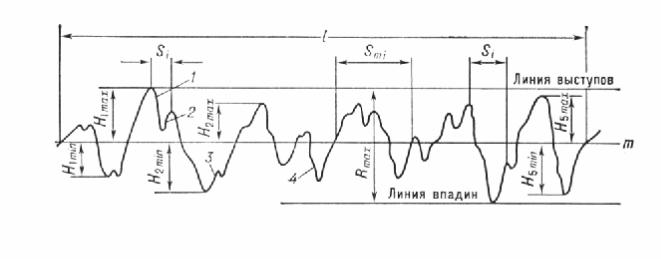
24
место неровности различной формы и высоты в виде выступов и впадин с относительно малым шагом – шероховатость.
Шероховатость поверхности принято определять по ее профилю, который образуется в сечении этой поверхности плоскостью, перпендикулярной к номинальной поверхности.
Для количественной оценки шероховатости в машиностроении применяют критерии Rz и Rа. Высота неровностей Rz определяется суммой средних арифметических абсолютных отклонений точек пяти наибольших минимумов и пяти наибольших максимумов профиля в пределах базовой длины. Критерий Ra определяется как среднее арифметическое абсолютных значений отклонений профиля в пределах базовой длины.
Рис.2.3. Схема профиля шероховатости поверхности
Сложность явлений, которые сопровождают процесс обработки резанием и многообразие факторов, влияющих на образование неровностей, обуславливает отступление их формы от геометрически правильной. При этом форма и размеры неровностей анизотропны. Высота неровностей поверхности, измеренная в направлении движения резания вдоль обработанных рисок характеризует продольную шероховатость поверхности. Высота неровностей, измеренная перпендикулярно к движению резания характеризует поперечную шероховатость поверхности. В связи с тем, что такие факторы, как форма режущего инструмента и величина подачи, отражаются только на поперечной шероховатости, величина поперечной шероховатости в два-три раза превышают продольную шероховатость. Вследствие этого оценку шероховатости поверхности детали производят на основании измерения поперечной шероховатости. Хотя при некоторых методах обработки (например,
25
фрезерование) продольная и поперечная шероховатости имеют одинаковые значения и могут измеряться в обоих направлениях.
На шероховатость поверхности детали, обработанной резанием, оказывает влияние большое количество факторов, связанных с особенностями обработки заготовки. В частности, форма и высота неровностей, а также характер расположения и направление неровностей зависят от метода и режима обработки, состава, структуры и механических свойств обрабатываемого материала, конструкции, свойств и геометрии режущего инструмента, типа и состояния металлообрабатывающего оборудования, свойств станочных приспособлений и вспомогательного инструмента. Однако все перечисленные причины, от которых зависит шероховатость обработанной поверхности, можно объединить в три основные группы: причины, связанные с геометрическими параметрами процесса резания, упругой и пластической деформацией обрабатываемого материала и возникновением вибраций режущего инструмента.
Формирование неровностей вследствие геометрических причин принято трактовать как копирование на обрабатываемой поверхности траектории движения и формы режущего лезвия инструмента. Величина, форма и взаимное расположение неровностей (рисок) определяется формой и состоянием режущих лезвий и теми параметрами режима резания, которые влияют на изменение траектории движения режущего лезвия относительно обрабатываемой поверхности. Установлено, что увеличение подачи, главного и вспомогательного углов резца в плане приводит к росту высоты неровностей, а возрастание радиуса закругления вершины резца снижает высоту шероховатости поверхности. Понижение шероховатости режущих поверхностей инструмента путем доводки способствует уменьшению шероховатости обработанной поверхности.
При обработке резанием мягких и пластичных материалов поверхностный слой сильно деформируется. При этом значительно изменяется форма неровностей и обычно шероховатость увеличивается. При обработке хрупких материалов часто наблюдается вырывание отдельных частиц металла, что также ведет к увеличению шероховатости.
Установлено, что скорость резания является одним из наиболее существенных факторов, влияющих на развитие пластической деформации при обработке резанием. При малых скоростях резания (1 – 5 м/мин) температура в зоне стружкообразования невелика, а отделение стружки происходит без заметной пластической деформации поверхностного слоя. Неровности на обработанной поверхности незначительны.
26
Увеличение скорости резания до ~ 40 м/мин приводит к значительной пластической деформации в зоне стружкообразования, повышению температуры и образованию на передней поверхности режущего инструмента, тек называемого, нароста. Это явление приводит к повышению шероховатости обработанной поверхности. Дальнейшее повышение скорости резания уменьшает нарост и понижает высоту неровностей обработанной поверхности. Таким образом, шероховатость обработанной поверхности в значительной степени связана с процессами образования стружки и в первую очередь с явлением нароста.
Такой элемент резания как подача также оказывает большое влияние на шероховатость обработанной поверхности, что связано не только рассмотренными выше геометрическими причинами, но и в значительной степени обусловлено деформацией поверхностного слоя.
Установлено, при оптимальных режимах резания влияние глубины резания на шероховатость влияет мало. Однако при глубине резания меньше подачи глубина оказывает геометрическое влияние на шероховатость. В этом случае уменьшение глубины резания снижает высоту неровностей.
В процессе обработки резанием возникают вынужденные колебания, вызываемые действием внешних сил, и автоколебаниями системы станок – заготовка – инструмент. Появление этих колебаний связано с целым комплексом причин, главной из которых является неустойчивость пластической деформации в зоне стружкообразования. Однако вынужденные колебания могут быть обусловлены и причинами механического характера, например, дефектами отдельных механизмов станка.
Рассмотрим модель возникновения автоколебаний, которые возникают из-за потери устойчивости пластической деформации при резании материалов.
Приложенные к материалу в зоне резания напряжения совершают работу пластической деформации стружкообразования. Эта работа с одной стороны расходуется на увеличение упругой энергии материала, а с другой превращается в теплоту. В этом случае мощность подводимой механической энергии должна отвечать, по крайней мере, двум очевидным условиям. Во-первых, она должна быть достаточной для восполнения энергетических затрат, связанных с идущими в материале атомными и дислокационными перестройками. Если это условие не выполняется, то действующие напряжения не способны обеспечить необходимую скорость деформации и стружкообразования соответственно. Во-вторых, подводимая к обрабатываемому материалу энергия
27
должна успевать поглощаться и рассеиваться им. При нарушении этого условия наступает потеря устойчивости пластической деформации и, как следствие, ее локализация.
Таким образом, пластическая деформация в зоне стружкообразования это неравновесный, необратимый и весьма диссипативный процесс. Условие неразрывности деформации материала сводится к необходимости поддержания скорости диссипации подводимой к материалу энергии на определенном, заданном режимом резания, уровне. В тех объемах деформируемого материала, где это условие не выполняется, скорость диссипации энергии становится меньше скорости ее нарастания, возникает критическое структурное состояние, деформация локализуется и зарождаются трещины.
Такая модель локализации деформации при стружкообразовании основана на том, что в пластически деформируемом материале скорость диссипации механической энергии связана с движением дислокаций. По мере увеличения деформации их зарождение и движение затрудняется, что связано с накоплением в зернах различного рода препятствий. При некоторой критической степени деформации скорость движения дислокаций и в месте с ней скорость диссипации механической энергии снижается до такого уровня, что для ее поддержания на прежнем уровне необходимо подключить дополнительные механизмы диссипации энергии. Такими механизмами могут быть двойникование, адиабатический сдвиг, образование зон изгиба и кручения (ротационные моды) и другие. Их включение приводит к локализации пластической деформации, т.е. ее неустойчивости. В качестве условия устойчивости можно воспользоваться выражением:
dD/dė > D/ė, (D > 0), |
(2.2) |
где D = D(ė) = σė – диссипативная функция, σ – напряжение пластического течения, ė – скорость пластической деформации. Подставляя D(ė) в (2.1) получаем условие:
∂σ/∂ė > 0, |
(σ > 0), |
(2.3) |
согласно которому деформация будет устойчивой тогда, когда напряжение σ возрастает с увеличением скорости деформации.
Однако, хорошо известно, что, если сила убывает с увеличением скорости, то могут развиваться автоколебания. Это означает, что некоторые скорости деформации порождают неустойчивость. Таким обра-
28
зом, автоколебания при резании являются проявлением неустойчивости пластической деформации в зоне стружкообразования и поддерживаются внешней силой в неравновесной диссипативной системе.
Колебания при резании являются дополнительными источниками увеличения шероховатости обработанной поверхности. Очевидно, что высота неровностей поверхности будет тем значительнее, чем больше амплитуда колебаний режущего инструмента относительно обрабатываемой поверхности.
3. Основы теории прочности твердых тел.
Служебные свойства материала принято характеризовать термином “конструктивная прочность”, под которым понимают работоспособность материала в изделии. Конструктивная прочность включает в себя комплекс свойств: прочность, надежность и долговечность.
Прочность материала – это способность сопротивляться деформации и разрушению при различных напряженных состояниях и схемах нагружения. Сопротивление пластической деформации характеризуется чаще всего пределом текучести, а в некоторых случаях пределом прочности. Уровень прочности определяет расчетные напряжения.
Надежность – это способность материала сопротивляться кратковременным нагрузкам превышающих расчетные. Для конструкционного материала надежность можно отождествить с сопротивлением материала развитию трещины.
Долговечность – это время, в течение которого материал может сопротивляться разрушению. Сопротивление износу ползучести, коррозии и т.д., характеризует долговечность материала.
Изменение методов и режимов механической обработки оказывает воздействие на отдельные характеристики качества поверхности, а соответственно и на эксплуатационные свойства деталей.
Различают хрупкое разрушение, сопровождающееся минимальным поглощением энергии и малой предшествующей пластической деформацией, и пластическое (вязкое) разрушение, при котором материал пластически деформируется. Хрупкое разрушение может происходить путем скола по определенным плоскостям кристалла, а также путем излома по границам зерен. Пластическое разрушение сопровождается значительной пластической деформацией, причем еще до момента фактического разрушения могут возникать внутренние повреждения на участках неоднородности структуры и в местах расположения дефектов.
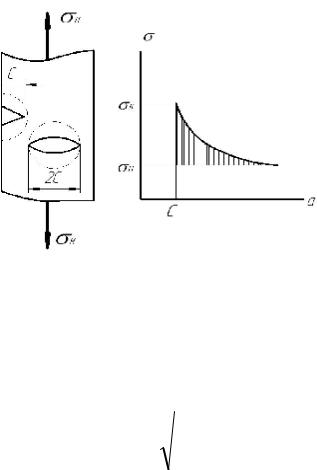
29
3.1. Хрупкое разрушение.
Можно выделить две особенности хрупкого разрушения: разрушающее напряжение часто оказывается значительно ниже рассчитанной прочности материала, во-вторых, измеренные разрушающие напряжения обнаруживают значительный разброс.
Экспериментально установлено, что разрушение хрупких тел возникает из-за множества тонких трещин, имеющихся на поверхности материала. Во всяком случае, получаемые низкие значения прочности указывают на существование поверхностных дефектов, иногда называемых трещинами Гриффитса.
Рис.3.1. Концентрация напряжений в пластине с трещиной.
Трещина вызывает концентрацию напряжений около ее вершины. Гриффитс пришел к выводу, что концентрация напряжений зависит от номинального напряжения σн, глубины трещины С и радиуса кривизны в вершине трещины r:
σ к = σ н × 2 |
|
С |
|
|
(3.1) |
|
r |
||||||
|
|
|||||
Коэффициент концентрации напряжения σк /σн |
может составлять |
102 ÷ 103. Таким образом, во время разрушения хрупких материалов, например, стекла, под действием растягивающего напряжения величины локального напряжения может достигать 700 кгс/мм2 при номинальном напряжении в пределах 3-10 кгс/мм2.
При распространении трещины выделяется энергия упругой деформации:

|
|
|
|
|
30 |
U |
|
= − |
πс2 |
σ 2 |
(3.2) |
|
д |
|
2E |
н |
Однако, образование новых поверхностей трещины требует затраты определенной энергии:
Un = 2cγ , |
(3.3) |
где g - удельная поверхностная энергия.
Трещина может самопроизвольно расти, если при этом суммарная энергия будет уменьшаться
d(U |
д |
+U |
n |
) |
= |
−πcσ 2 |
+ 2γ = 0 |
|
|
|
|
н |
(3.4) |
||||
|
dc |
|
|
Е |
||||
|
|
|
|
|
|
|||
|
|
|
|
|
||||
σ н = |
2γЕ |
|
|
(3.5) |
||||
|
|
|
|
πс |
|
|
|
Очевидно, что напряжение разрушения уменьшается при более глубоких поверхностных трещинах и возрастает у материалов с высоким модулем упругости и большой поверхностной энергией.
= πσ 2
Скр γ н , (3.6) 2 E
где Скр – критический размер трещины Гриффитса.
Проведенный анализ относится к простейшему случаю, когда трещина без какой-либо пластической деформации материала распространяется в тонкой пластине под действием растягивающего напряжения. Однако необходимо отметить, что второй закон термодинамики не допускает возможность превращения всей накопленной упругой энергии в поверхностную без рассеяния некоторой ее части. Поэтому в большинстве металлов наблюдается некоторая локальная пластическая деформация вдоль траектории распространения трещины. В этом случае уравнение (3.5) приобретает вид:
é |
Е ù |
1 |
|
|
||
2 |
|
|
||||
σ н = ê2(γ +ψ п ) |
|
|
ú |
, |
(3.7) |
|
π × |
|
|||||
ë |
сû |
|
|
|