
Варгасов Пестов_Обработка поверхности
.pdf41
В идеальной однородной жидкости образование пустот происходит при больших растягивающих напряжениях порядка теоретической прочности. Реальные жидкости менее прочны. Низкая прочность реальных жидкостей связана с наличием в них так называемых кавитационных зародышей: микроскопических газовых пузырьков. Мельчайшие пузырьки газа или пара, двигаясь с потоком и попадая в область, где давление p < pкр, сильно расширяются. Исследования кавитации показывают, что пузырек вырастает за время 0,002 с до 6 мм в диаметре. В результате на участке потока с пониженным давлением создается «кавитационная зона», заполненная движущимися пузырьками.
После перехода в зону повышенного давления рост пузырька прекращается, и он начинает сокращаться. Сокращение кавитационного пузырька происходит с большой скоростью за время порядка 0,001 с и сопровождается гидравлическим ударом и звуковым импульсом. Если кавитационные пузырьки захлопываются вблизи от поверхности обтекаемого тела, то многократно повторяющиеся удары приводят к разрушению поверхности обтекаемого тела, например гребных винтов и других гидротехнических деталей.
Эрозионное изнашивание. При анализе процесса изнашивания деталей машин под термином эрозия понимают постепенное разрушение поверхности металлических изделий в потоке газа или жидкости, а также под влиянием воздействий электрических разрядов. Эрозионное воздействие высокоскоростного потока газа или жидкости слагается из трения и его ударов о макроскопические и микроскопические дефекты поверхности. В результате такого взаимодействия происходит нарушение межатомного взаимодействия и отделение от поверхности отдельных объемов материала. В зависимости от свойств поверхности материала возможны вырывы как отдельных объемов, так и зерен.
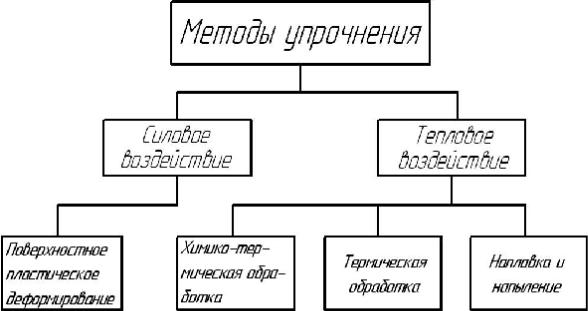
42
ЧАСТЬ 2. Технологии обработки поверхности
4.Упрочнение поверхности деталей машин.
Всовременной технологии машиностроения широко используются различные технологические методы воздействия на поверхностные слои деталей машин, целенаправленно изменяющие физикохимическое состояние этого слоя в процессе его упрочнения, что способствует повышению эксплуатационных характеристик деталей и надежности всего изделия.
Взависимости от вида воздействия на поверхность детали машин методы упрочнения можно условно разделить на следующие группы
(рис.4.1.)
Рис.4.1. Методы упрочнения поверхности деталей.
Выбор того или иного метода зависит от конструкции детали и технологических возможностей процесса упрочнения. Наибольшее применение в промышленности нашли методы силового и теплового воздействия на поверхностные слои деталей машин.
43
4.1. Упрочнение методами поверхностного пластического деформирования
Методы поверхностного пластического деформирования (ППД) основаны на обработке давлением, при которой деформируется только поверхностный слой металла. Основной целью ППД является повышение сопротивления материала усталости, повышение твердости, снижение шероховатости поверхности. ППД применяют на финишных операциях технологического процесса изготовления деталей машин взамен операций обработки резанием лезвийным и абразивным инструментом.
Используемые методы ППД можно разделить на две группы: статические и динамические. Статические методы основаны на постоянном взаимодействие инструмента и материала. Инструментом может быть ролик, шарик, диск. Динамические методы основаны на прерывистом взаимодействии материала и инструмента. В качестве инструмента используют бойки, шарики, ролики. Однако независимо от вида и способа воздействия инструмента на обрабатываемый материал происходит пластическая деформация поверхностного слоя.
При ППД механизм пластической деформации в основном остается обычным, т.е. деформация осуществляется за счет зарождения и скольжения дислокаций. При этом возрастает сопротивление пластической деформации, т.е. наблюдается деформационное упрочнение. К основным механизмам упрочнения при пластическом деформировании относятся: взаимодействие пересекающихся дислокаций, увеличение кривизны дислокаций, взаимодействие параллельных дислокаций.
Проходя через лес дислокаций, скользящая дислокация испытывает сильное торможение, так как пересечение двух дислокаций приводит к образованию на них ступенек. Таким образом, если скольжение идет в какой-либо одной плоскости, то для дислокаций из другой системы скольжения главным является упрочнение за счет пересечений.
По мере развития пластической деформации кривизна дислокаций увеличивается главным образом за счет переползания. При большой и хаотической кривизне отдельные подвижные участки, лежащие в плоскостях легкого скольжения, будут перемежаться с неподвижными участками. При больших плотностях дислокаций искривление их осей может дать существенный вклад в общее упрочнение, особенно в локальное упрочнение внутри клубков и сплетений.
Таким образом, взаимодействие дислокаций и искривление их осей приводит к значительному упрочнению, которое существенно зависит от плотности дислокаций, типа дислокационной структуры и характера распределения дислокаций. Другими словами, коллективные
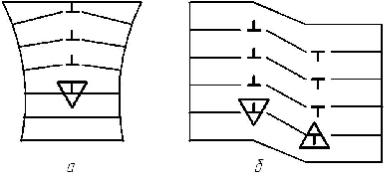
44
эффекты в системах дислокаций оказывают определяющее влияние на величину эффекта упрочнения, хотя и не влияют на вид зависимости напряжения от деформации. Экспериментальные данные и теоретический анализ с использованием различных моделей торможения дислокаций показывают, что напряжение течения растет пропорционально корню квадратному из общей плотности дислокаций:
∆σ = α·G·b√ρ |
(4.1) |
Однако можно отметить некоторые важные особенности деформации поверхности, которые заключаются в том, что кроме скольжения в поверхностном слое может реализоваться, так называемый, ротационный механизм, который заключается в повороте частей кристаллов относительно окружающего объема, что приводит к так называемой фрагментации. Это явление связано с тем, что при достижении плотностью дислокаций некоторого критического значения, дислокационная система приобретает новые физические свойства, отсутствующие у изолированных дислокаций. Так как энергия взаимодействия дислокаций при увеличении их плотности ρ растет быстрее, чем их собственная энергия, то при некоторой критической плотности силы взаимодействия между дислокациями становятся больше внешних сил, и независимые перемещения дислокаций становятся невозможными. Аналогично тому, как носителем сдвига в кристаллах является дислокация, элементарным носителем поворота в кристаллической решетке является дисклинация.
Рис.4.2. Дисклинация в кристалле. а) частичная дисклинация; б) диполь частичных дисклинаций.
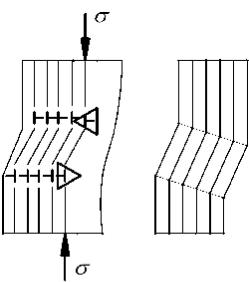
45
Рис.4.3. Движение дисклинации.
Установлено, что при пластической деформации в кристаллах всегда присутствуют или возникают источники внутренних напряжений. В металлах это границы и свободные поверхности, где чаще всего происходят ротации. Неоднородные напряжения можно представить как сумму средних напряжений и крутящего момента. Напряжения приводят к скольжению дислокаций, а крутящий момент к повороту в результате движения дислокаций.
Таким образом, ППД это сильно неравновесный процесс. Условие сплошности материала при пластической деформации сводится к необходимости поддержания скорости диссипации энергии подводимой к материалу механической энергии на определенном заданном уровне. Скорость диссипации энергии связана с движением и размножением дислокаций. По мере продолжения деформации движение дислокаций затрудняется из-за накопления в материале различных препятствий. При некоторой критической степени деформации скорость движения дислокаций, а, следовательно, и скорость диссипации энергии снижается до такого уровня, что для ее поддержания необходимо включение ротационного механизма пластической деформации и фрагментации кристаллов. Если носителями сдвига в кристаллах являются дислокации, то носителями ротаций являются дисклинации.
К основным методам ППД является обкатка шариками, выглаживание, вибрационно-упрочняющая обработка и упрочнение взрывом.
Обкатку роликами и шариками осуществляют с использованием различных приспособлений к токарным и строгальным станкам.
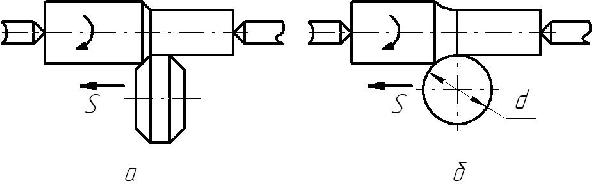
46
Рис.4.4. Схема ППД при обкатке роликами (а) и шариками (б).
Давление роликов или шариков создают механическим или гидравлическим способом. Обкатку применяют для обработки деталей типа тел вращения: осей, валов. Режим упрочняющей обработки устанавливают по следующим параметрам: давление на ролик, форма и размеры шарика, величина продольной подачи, скорость обработки. Так при заданных величинах подачи и скорости обкатки давление на деформирующий элемент можно найти так:
P = 2a2σT |
(4.2) |
где а – глубина наклепанного слоя; σT - предел текучести материала.
Выглаживание применяют для упрочнения изделий с твердостью до HRC 65. Выглаживание может заменить операции шлифования, полирования и доводки. Этот метод рационален для обработки стальных закаленных деталей, а также деталей, поверхность которых покрыта ка- ким-либо способом.
Выглаживание выполняют специальными инструментами, оснащенных сфероидальным или конусообразным элементами из сверхтвердых материалов: эльбор, алмаз, твердые сплавы при этом значительно уменьшается шероховатость и происходит упрочнение поверхностного слоя.
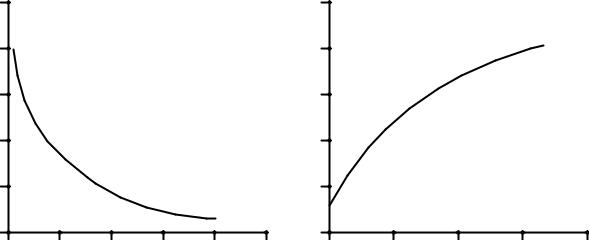
|
|
|
|
|
|
|
|
47 |
Ra |
|
|
|
Í ×10 -7 |
Ïà |
|
|
|
|
|
|
|
100 |
|
|
|
|
0.32 |
|
|
|
1300 |
|
|
|
|
0.24 |
|
|
|
1200 |
|
|
|
|
0.16 |
|
|
|
1100 |
|
|
|
|
0.08 |
|
|
|
1000 |
|
|
|
|
50 |
100 |
150 |
200 |
900 |
500 |
1000 |
1500 |
|
P, Í |
P, Í |
|||||||
|
à |
|
|
|
|
á |
|
|
Рис.4.5. Зависимость шероховатости (а) и микротвердости (б) от силы выглаживания.
Процесс обработки деталей машин дробью заключается в металлическом деформировании поверхности за счет кинетической энергии контактирующего с ней потока дроби. Эффективность обработки при этом зависит от материала и конфигурации деталей, энергии деталей, энергии удара, длительности процесса обработки и других факторов. Твердость поверхностного слоя деталей возрастает на 40% при глубине слоя порядка 0,5 мм. Дробеструйной обработке подвергаются детали сплошной конфигурации – пружины, зубчатые колеса, корпуса и т.п. При обработке сварных швов дробеструйный наклеп обеспечивает повышение долговечности сварных соединений. Эффективность обработки может быть повышена при ее сочетании с предварительной термической или химико-термической обработкой деталей.
К динамическим методам ППД также относится вибрационная обработка. Использование вибрационного пластического деформирования обеспечивает формирование регулярного микрорельефа и снижения шероховатости.
Для осуществления ультразвуковой вибрационной обработки часто используют ультразвуковые генераторы и магнитострикционные преобразователи, с помощью которых рабочий инструмент (шарик) воздействует на поверхность с заданной частотой (~ 20-27 кГц).
Ультразвуковое контактное пластическое деформирование (микроковка) является эффективным способом реализации всех преимуществ ковки при минимальных технологических затратах. Площадь
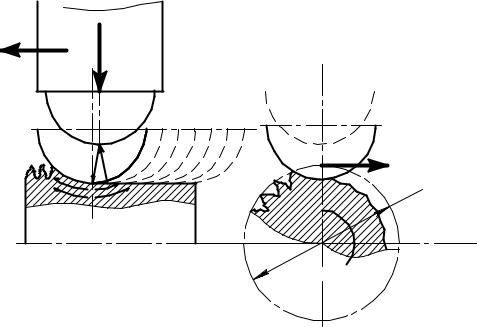
48
контакта инструмента с деталью мала, но совершается более 20000 ударов секунду и поэтому производительность обработки достаточно высока. Усилие прижатия инструмента мало (~ 20-30 Н), однако в момент контакта инструмента с деталью развивается усилие достаточное для локального пластического деформирования поверхности.
Сущность ультразвуковой упрочняющей обработки состоит в следующем. Деталь, закрепленная в кулачках вращающегося патрона токарного станка и инструмент - индентор ультразвукового преобразователя, закрепленного в резцедержателе станка, взаимодействуют с ультразвуковой частотой. При каждом периоде колебаний инструмент ударяет по поверхности детали.
S |
P |
V |
D |
n
Рис. 4.6. Схема ультразвуковой ударной обработки.
Материал детали имеет твердость ниже, чем твердость индентора, и последний при каждом ударе внедряется в поверхность детали. При соответствующей скорости вращения шпинделя V и подачи S происходит сплошное последовательное деформирование поверхности детали с соответствующим значительным уменьшением шероховатости и созданием упрочненного слоя. Учитывая высокую скорость деформации при ультразвуковой ударной обработке, можно ожидать, что упрочнение здесь происходит не только за счет увеличения плотности дислокаций, но и за счет фрагментации зерен поверхностного слоя. Многочисленные микрорентгеноспектральные исследования поверхностных слоев обработанных стальных деталей показывают, что средние размеры фрагментов составляют 70 – 80 нм, при глубине упрочненного слоя 10 – 20 мкм.
49
4.2. Химико-термическая обработка.
Химико-термической обработкой (ХТО) называют процесс насыщения поверхности металла или сплава тем или иным элементом (C, N, Аl, Gr, Si и др.) при высокой температуре, в результате чего происходит изменение химического состава, микроструктуры и свойств поверхностных слоев детали.
При химико-термической обработке атомы насыщающего элемента образуют твердые растворы и химические соединения, которые создают около себя искажения и изменение ближнего порядка расположения атомов. Взаимодействие дислокаций с этими искажениями приводит, как правило, к торможению дислокаций и упрочнению. Рассмотрим основные причины торможения дислокаций в твердых растворах и объемными частицами другой фазы.
В неупорядоченном твердом растворе искаженные области решетки вокруг атомов растворенного элемента, находящихся в плоскости скольжения, затрудняют движение дислокации. Чем больше фактор размерного несоответствия атомов растворенного элемента и основы, тем сильнее эти атомы тормозят дислокации.
Вклад в упрочнение атомов, находящихся в твердом растворе замещения, например в стали, можно оценить по формуле:
∆σ = αG∑[δк(с/сmax)к], |
(4.3) |
где α – коэффициент, определяемый экспериментально, G - модуль сдвига, δк = (rк - rFe)/ rre – параметр несоответствия радиуса атома легирующего элемента rк, по отношению к радиусу атома железа rre, (с/сmax)к – приведенная атомная концентрация легирующих элементов.
Межфазная граница также является эффективным барьером для скользящих дислокаций, так как при переходе через межфазную границу изменяется не только ориентировка атомных плоскостей, но и тип решетки. В металлических сплавах вторая фаза, которая может возникнуть в результате химико-термической обработки, чаще распределена в виде дисперсных включений внутри основной фазы.
Если расстояние ℓ между частицами второй фазы достаточно велико, дислокация под действием напряжения выгибается между ними. При этом вклад в упрочнение дисперсных фаз можно оценить по формуле:
50
∆σф = Gb/ℓ |
(4.4) |
С уменьшением расстояния между частицами в соответствии с формулой (4.4) возрастает напряжение, необходимое для проталкивания между ними дислокаций, и может наступить момент, когда более легким путем оказывается прохождение дислокации через тело частиц, т.е. происходит перерезание частиц. Так как решетка частицы, как правило, отличается от решетки матрицы, в частице создается сильное нарушение упаковки атомов вдоль плоскости сдвига. Внутри частицы возникает высокоэнергетическая поверхность раздела, что является одной из причин торможения дислокаций. Частицы больших размеров и высокопрочные частицы дислокациями не перерезаются.
Образование частиц второй фазы, состоящих только из атомов второго компонента В или какого-либо химического соединения АmВn обычно уменьшает энергию системы и поэтому энергетически выгодно. Такое фазовое превращение происходит в каком-то ограниченном объеме – отдельном зерне. Но взаимодействие с соседними зернами не позволяет ему свободно изменяться. Возникают внутренние напряжения. При этом частицы второй фазы должны иметь форму, приводящую к минимальным внутренним напряжениям. Установлено, что такой формой обладают параллельные пластины или иглы. Именно в виде пластин часто образуются карбиды и нитриды.
Таким образом, еще одна важная причина торможения дислокаций - существование в матрице дальнедействующего поля упругих напряжений вокруг частиц. Они возникают из-за разности в удельных объемах или разницы в коэффициентах термического расширения частицы и матрицы, из которой выделяется частица.
При любом виде химико-термической обработки насыщение поверхности атомами какого-либо элемента происходит при нагреве детали до определенной температуры в среде содержащей насыщающий элемент в активном состоянии.
Химико-термическая обработка включает три последовательные стадии:
1.образование активных атомов в насыщающей среде вблизи поверхности или непосредственно на поверхности детали;
2.адсорбцию образовавшихся активных атомов поверхностью детали. Различают физическую (обратимую) и химическую адсорбцию (хемосорбцию). При химико-термической обработке оба типа адсорбции накладываются один на другой. Физическая адсорбция приводит к образованию как моноатомных, так и