
Варгасов Пестов_Обработка поверхности
.pdf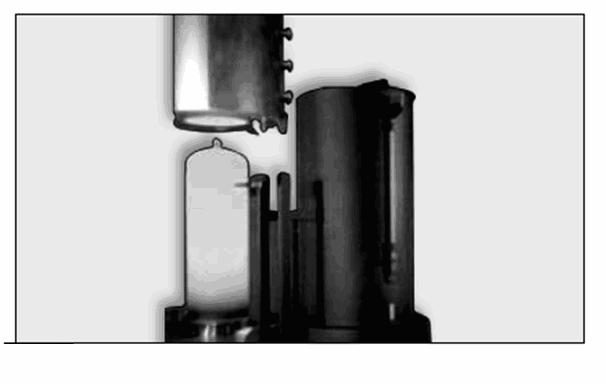
91
Рис. 6.3. Колпак установки CVD
Для крупносерийного производства применяются системы с несколькими рабочими позициями – для загрузки и выгрузки; для нагрева и нанесения покрытия; для охлаждения.
Материал, на который наносится покрытие, размещается на графитовых подставках (тарелках) с пазами (газовыми каналами), которые ставятся одна над другой в зону нанесения покрытия. Газ распространяется равномерно (без мертвых зон) и образует однородное покрытие с хорошей сцепляемостью с основным материалом. Методом CVD наносятся, в основном, покрытия TiN, TiCN (заменившее TiC) и Al2O3. Последнее керамическое покрытие, поскольку не является электропроводным, может быть нанесено только методом CVD.
Преимущества метода CVD (простота загрузки, отсутствие длительной подготовки и необходимости поворота изделий в технологическом процессе) делают его экономически выгодными при нанесении покрытий на большие партии малоразмерных изделий (пластин).
Упомянутый выше Р-CVD метод устраняет некоторые ограничения, присущие традиционному CVD-методу (рис. 6.4).
Для начала химических реакций используется не высокая температура, а наличие в рабочей камере плазмы. Плазма оказывает каталитическое воздействие и концентрирует энергию. В результате процессы могут протекать при более низких температурах. С помощью Р-CVD- метода, в зависимости от подводимого газа, можно наносить карбид-
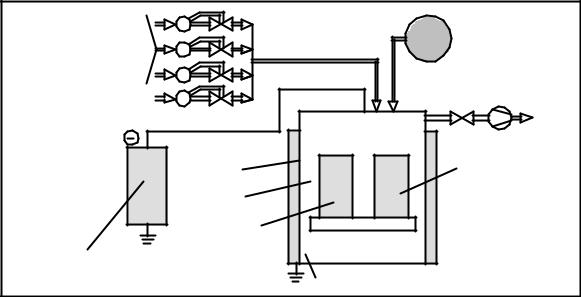
92
ные, нитридные и карбонитридные покрытия при температурах 400– 500°С. В отличие от обычных покрытий CVD в этом случае практически отсутствует снижение вязкости в граничной зоне между сплавом и покрытием. По сравнению с полученными по методу PVD эти покрытия имеют лучшую адгезию и меньшие внутренние напряжения. Кроме того, отпадает необходимость в особом расположении изделий для получения равномерного покрытия. Однако метод P-CVD пока не получил широкого распространения.
|
N 2 |
Емкость с TiCl4 |
|
Реакционные |
H2 |
||
|
|||
газы |
CH2 |
Вакуумный |
|
Инертный газ Ar |
насос |
||
|
|||
|
напряжение 400-650 В |
|
|
|
Нагрев |
450-6500 C |
|
|
Плазма |
10-1000 Па |
|
|
|
||
|
Изделие |
|
|
Импульсный источник |
|
||
постоянного тока |
|
Камера нанесения покрытия |
|
|
|
||
Рис. 6.4. Схема установки для нанесения покрытий методом плазменно- |
|||
го CVD. |
|
|
6.5. Установки для нанесения покрытий методом PVD
При PVD-методе материал покрытия внутри установки переводится из твердого состояния в газообразное с помощью различных физических процессов. Их можно разделить на две большие группы – процессы испарения и распыления. Испарение осуществляется за счет резистивного сопротивления, индукционного нагрева, электронно-лучевых пучков, низковольтной дуги, полого катода, катодной или анодной дуги, лазерного луча. Процессы могут проходить с дополнительной ионизацией или без нее, в среде реакционного газа или без него, с напряжением смещения или без него.
Распыление бывает диодное или магнетронное, при постоянном токе или токе высокой частоты, в среде реакционного газа или без него, с напряжением смещения или без него, с дополнительной модификаци-
93
ей магнитного поля (несбалансированной или с замкнутым полем) или без нее.
Для нанесения покрытий на инструмент в подавляющем большинстве случаев применяется один из трех методов ионного осаждения. К ним относятся:
∙испарение электронным пучком,
∙испарение электрической дугой,
∙распыление (магнетронное) ионной бомбардировкой.
Процессы протекают в среде инертного газа в присутствии реакционного газа (например, азота и/или ацетилена) при отрицательном напряжении смещения на покрываемом материале. Для улучшения переноса частиц в камере поддерживается пониженное давление (меньше 10-2 бар или около 1 Па) или высокий вакуум (10-5 бар или 10-3 Па).
Поскольку покрытие наносится только на поверхности, обращенные в сторону источника частиц, покрываемый материал должен совершать сложное планетарное движение. Для реализации такого движения материал помещают на специальные вращающиеся подставки. Каждый из сателлитов вращается вокруг своей оси, а ось сателлита вращается вокруг оси подставки. В результате каждое из гнезд под инструмент совершает движение, обеспечивающее равномерное нанесение покрытия.
Практически все современные установки работают по замкнутому циклу, включающему:
∙загрузку в очищенную камеру подставки с тщательно очищенным материалом (инструментом), на который будет наноситься покрытие;
∙откачивание воздуха из камеры;
∙нагрев камеры и материала внешним источником и ионной бомбардировкой (при положительном напряжении смещения на материале);
∙очистку материала ионным травлением (аргонно-ионным или металло-ионным) с последующим отсосом загрязнений (рис. 5);
∙испарение или распыление и ионизацию материала "мишени" (например, титана) с одновременной подачей энергии, рабочего газа (например, аргона) и реакционного газа (азота для образования нитридов, углеводорода для образования карбидов и кислорода для образования оксидов); перенос частиц (ионов, атомов, молекул, электронов, радикалов) в среде ионизированного газа (плазме); столкновение частиц с материалом и конденсацию (для
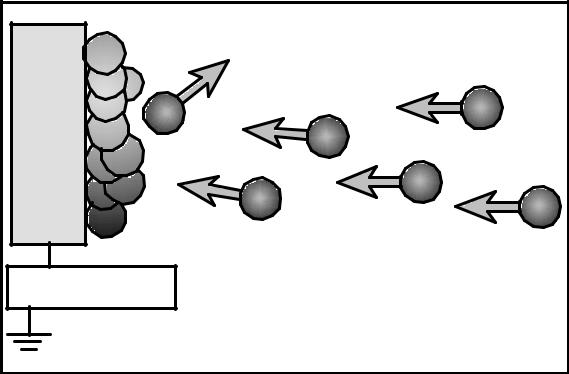
94
улучшения процесса применяется отрицательное напряжение смещения на материале); ∙охлаждение камеры и материала;
∙выгрузку подставки с материалом после выравнивания давления.
|
Загрязнения |
|
|
||
Материал |
|
|
Ar |
+ |
Ar+ |
|
|
|
|||
|
|
|
|
||
|
Ar |
+ |
|
Ar + |
|
|
|
|
Ar+ |
||
от 1 до 1000 В |
Напряжение |
|
|||
смещения |
|
|
|||
|
|
|
|
Рис.6.5. Схема ионной очистки поверхности Обязательным условием получения высококачественного покры-
тия является тщательная очистка материала перед нанесением покрытия, осуществляемая последовательной обработкой (отмывкой) в нескольких химических средах, частично с ультразвуковой обработкой. После этого следует промывка в чистой воде и сушка. Инструмент не должен иметь никаких следов термической обработки. Особое внимание уделяется также очистке внутренних каналов подвода СОЖ и "дегазации" мест пайки. Для подготовки поверхности под покрытие часто применяется микроструйная обработка.
В установках, использующих испарение электронным пучком, к катоду с тлеющей дугой подводится высокое напряжение (1–10кВ). В результате создается сфокусированный и ускоренный пучок электронов (около 200А), который направляется на мишень с металлическим материалом покрытия (рис. 6.6). Мишень установлена в центре горизонтально расположенного котла из графита, керамики или меди. К котлу подведено положительное напряжение. К противолежащей подставке с покрываемыми инструментами подведено отрицательное напряжение, называемое напряжением смещения.
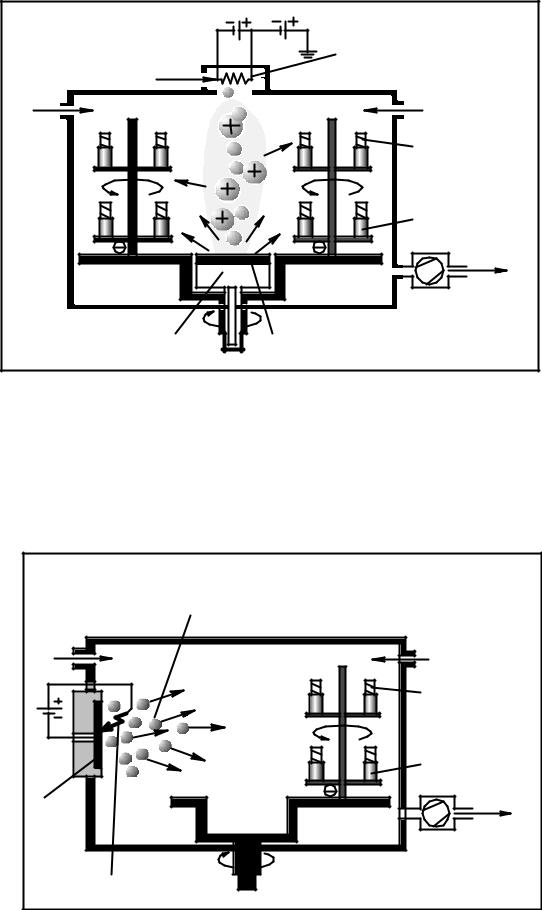
|
95 |
|
|
Источник потока |
|
|
электронов с |
|
Аргон |
тлеющим катодом |
|
Аргон |
Реакционный |
|
|
||
|
газ азот (N 2 ) |
|
|
Заготовки |
|
|
Держатели |
|
|
Вакуумный |
|
Испаритель |
насос |
|
Материал покрытия, |
||
|
||
|
например титан |
|
Рис.6.6. Метод испарения пучком электронов |
||
Положительные ионы испаренного вещества (например, титана) |
||
вступают в реакцию с реакционным газом (например, азотом) и обра- |
||
зуют материал покрытия (нитрид титана), который осаждается на по- |
||
крываемом инструменте. Камера покрытия изготавливается из нержа- |
||
веющей стали с двойными стенками с системами нагрева и охлаждения. |
||
Ионизированный |
|
|
испаренный металл |
||
Аргон |
Реакционный |
|
|
||
|
газ азот (N 2 ) |
|
|
Заготовки |
|
|
Держатели |
|
Мишень |
|
|
|
Вакуумный |
|
|
насос |
|
Дуга |
|
|
Рис.6.7 Метод испарения электрической дугой |
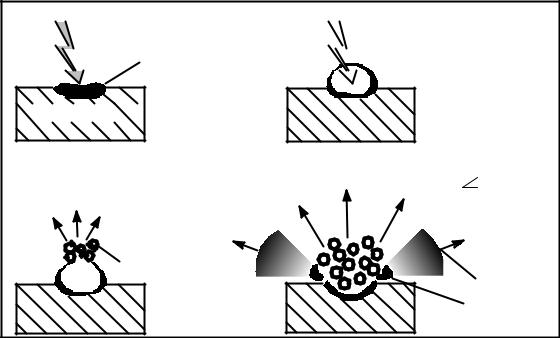
96
При использовании дугового испарения зажигается электрическая дуга (рис. 6.7). После поджига дуги ее перемещение по поверхности мишени, установленной в медном охлаждаемом катоде, управляется с помощью системы магнитов. Основная цель – обеспечить равномерное удаление материала с поверхности мишени и продлить срок ее службы. Катод устанавливается вертикально на стенки камеры, и к нему подводится отрицательное напряжение. В момент поджига дуги на поверхности мишени возникает местный расплав (рис. 6.8-1). Начинается испарение металла мишени (рис. 6.8-2 и 6.8-3), однако при испарении вместе с ионами материала также ускоряются неионизированные частицы металла (капли) (рис. 6.8-4), которые также осаждаются на поверхность инструмента.
|
|
|
|
Дуга |
|
|
|
|
|
|
|
Испарение материала |
|||
|
|
|
|
|
|
|
|
|
|
|
|||||
|
|
|
|
|
|
|
Расплав |
2. |
|
|
|
|
|
|
мишени в основании |
1. |
|
|
|
|
|
|
|
|
|
|
|
|
дуги (катодная точка) |
||
|
|
|
|
|
|
|
|
|
|
|
|
|
|
||
|
|
|
|
|
|
|
|
|
|
|
|
|
|
|
|
Мишень-катод |
|
|
|
Расплав растекается, |
|
Отрыв пузырьков пара и |
4. |
капли вылетают под 450 |
|
освобождение атомов и ионов |
|
|
|
|
|
|
3. |
Атом или ион |
|
|
|
|
Разлет капель |
|
|
|
|
Капли
Рис.6.8. Стадии образования пара и капель.
Наличие такой капельной фазы является основным недостатком дугового метода, так как капли ухудшают качество покрытия. Удаляются капли последующей обработкой после нанесения покрытия. Наибольшее количество капель образуется в момент поджига дуги.
На дуговых установках можно наносить композитные (состоящие из нескольких металлов) и многослойные покрытия. Для этого применяются различные мишени. На противоположных стенках камеры можно установить несколько мишеней из чистых металлов (например, титана и алюминия), а можно использовать одну мишень из их сплава. При недостатке места можно использовать комбинированные мишени, состоящие из нескольких "чистых", сведенных на одном катодном бло-
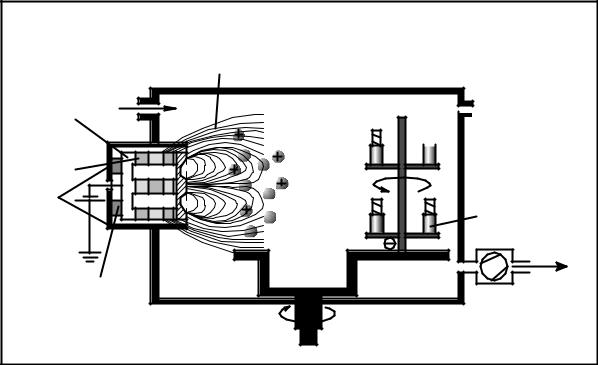
97
ке мишеней. Применение нескольких одинаковых мишеней увеличивает скорость нанесения покрытия.
Из установок, использующих метод распыления, наибольшее применение находят установки на основе магнетронов (MSIP – Magnetron Sputtering Ion Plating – ионное осаждение магнетронным распылением). При приложении высокого напряжения в атмосфере инертного газа (как правило, аргона) возникает тлеющий разряд (рис. 9). Ионы инертного газа из плазмы, обладающие высокой энергией, ударяются об мишень, включенную как катод. За счет ударного импульса материал распыляется, минуя промежуточную жидкую фазу.
|
|
|
Линии маг- |
|
|
Аргон |
|
нитного поля |
|
Катод |
|
|
||
|
|
|
||
Магнитная |
N |
S |
N |
|
система |
S |
N |
S |
|
Анод |
||||
|
|
|
||
|
N |
S |
N |
Изоляция
Мишень
Реакционный
газ азот (N2 )
Заготовки
Держатели
Вакуумный
насос
Рис.6.9. Метод магнетронного распыления
В этом случае, в отличие от установок с котлом, возможно произвольное расположение мишеней. С помощью магнитных полей (замкнутых и разомкнутых) путь электронов удлиняется (по спирали вдоль линий магнитного поля), увеличиваются плотность плазмы и ударная энергия. Позади мишени располагается магнитная система, определяющая распределение области распыления материала по всей поверхности мишени.
Для совмещения положительных свойств различных методов нанесения покрытий выпускаются установки, объединяющие эти методы. Распространены установки с несколькими дуговыми и двумя магнетронными катодами, позволяющие наносить покрытия TiAlN с поверх-
98
ностным слоем из снижающего трение покрытия металл-углерод. Существуют также универсальные установки, позволяющие совмещать дуговое и магнетронное распыление с CVD- и P-CVD- процессами. Таким образом, всегда есть возможность подобрать установку, реализующую тот метод нанесения покрытий, который является наиболее оптимальным для данных условий применения и заданного материала покрытия. Процессы нанесения покрытий методами PVD бурно развиваются в последние годы, что нельзя сказать о процессах CVD. Исключение составляют установки CVD для нанесения алмазных покрытий.
6.6. Наноструктурные покрытия высокопроизводительного инструмента
На современные высокопроизводительные режущие инструменты кроме традиционных покрытий в последнее время все чаще наносятся наноструктурные покрытия основе титана и алюминия (Ti, Al). По различным данным доля инструмента, с нанесенными покрытиями (Ti, Al) колеблется от 25% до 55% от общей доли покрываемого инструмента. Причина такой популярности — в уникальных свойствах самого покрытия на основе Ti и Al: высокая твердость (примерно 25–38 ГПа) при относительно небольших остаточных напряжениях (3–5 ГПа); высокая твердость при нагреве («горячая твердость»), определяющая незначительные потери твердости (около 30–40%) при температурах до 800°С; высокая стойкость к окислению (около 15–20 мкг/см2) при температуре 800°С, что эквивалентно скорости окисления покрытия TiCN при 400°С или покрытия TiN при 550°С; низкая теплопроводность (коэффициент относительного температурного расширения на 30% ниже, чем у покрытия TiN). Технология нанесения покрытий на основе Ti и Al является одной из наиболее быстро развивающихся. Даже за тот относительно небольшой период времени существования покрытия предложено достаточно большое количество решений по улучшению его свойств. Отметим некоторые из них:
∙комбинация дугового метода и метода магнетронного осаждения;
∙фильтрация микрокапель при дуговом методе;
∙оптимизация параметров процесса, таких как ток дуги, напряжение смещения, давления азота и т. д.;
∙оптимизация кристаллической структуры для улучшения стойкости к коррозии;

99
∙нанесение многослойных покрытий для увеличения вязкости и толщины покрытия;
∙добавление легирующих компонентов, таких как: хром и иттрий для увеличения окислительной стойкости; цирконий, ванадий, бор и гафний для увеличения износостойкости; кремний для увеличения твердости и стойкости к химическим реакциям. Наиболее важными направлениями совершенствования покрытий на основе Ti, Al представляются работы по нанесению нанослойных покрытий и увеличению доли алюминия.
Внастоящее время информация о технологиях нанесения нанопокрытий весьма скудна и обрывочна. Разработчики технологий основное внимание уделяют повышению главных эксплуатационных параметров деталей, на которые наносятся эти покрытия. Поэтому остановимся на тех свойствах, которые улучшаются или появляются при нанесении нанопокрытий.
Современные нанопокрытия состоят из разнородных слоев, чередование которых позволяет управлять свойствами покрытия. При определенной толщине нанослоев, может быть получено значительное увеличение твердости (рис. 6.10). Высокая твердость является следствием существенного различия модуля Юнга (модуля упругости) материалов субслоев.
Снижение твердости при малых толщинах слоев (около 6–7 Нм) объясняется «грубостью» границ между слоями. Если установка и технология нанесения покрытия позволяет получить «четкие» границы, то снижения твердости не наблюдается.
Рис. 6.10. Зависимость твердости нанопокрытия от периодичности нанослоев.
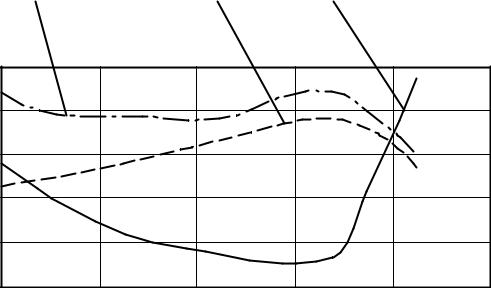
100
Расстояние между нанослоями изменяется в процессе эксплуатации инструмента из-за изменения температуры, что также снижает эффективность такого покрытия.
Ведущие изготовители установок для нанесения покрытий постоянно совершенствуют их с целью увеличения содержания алюминия в покрытии. Увеличение доли алюминия увеличивает твердость, износо- и теплостойкость. Покрытия, в которых доля алюминия не превышает 50%, обозначаются как TiAlN. Если доля алюминия составляет более 50%, то используется обозначение AlTiN. Однако существует предел содержания алюминия, после которого дальнейшее увеличение не дает никакого дополнительного преимущества и не имеет особого смысла. Таким пределом считают 67%, 75%, а в некоторых источниках —80% алюминия. Все зависит от того, какой из факторов является преобладающим (рис. 6.11). И в этом случае предел содержания алюминия определяется периодичностью нанослоев, которая может быть практически выдержана в реальных условиях нанесения покрытия в производстве. Единственным способом превышения предела содержания алюминия в покрытии является применение физически новых решений, например, нанокомпозитов.
|
|
|
Адгезия |
|
Твердость |
Износостойкость |
|
|
|
|
50 |
|
|
|
|
|
|
1,25 |
) |
|
|
|
|
|
|
|
|
3 |
|
|
40 |
|
|
|
|
|
|
|
мм |
Твердость, (ГПа) |
|
|
|
|
|
|
1 |
-2 |
|
|
|
|
|
|
|
Истираемый объем (х10 |
|||
30 |
|
|
|
|
|
|
0,75 |
||
|
|
|
|
|
|
|
|||
20 |
|
|
|
|
|
|
0,5 |
||
10 |
|
|
|
|
|
|
0,25 |
||
0 |
|
|
|
|
|
|
0 |
||
|
0 |
0,2 |
0,4 |
0,6 |
0,8 |
1 |
|
||
|
|
|
Содержание алюминия Al (%)=(Al)/(Al+Ti) |
|
|
|
|||
Рис. 6.11. Влияние количества алюминия на основные свойства покры- |
|||||||||
|
|
|
|
|
тия |
|
|
|
|