
Варгасов Пестов_Обработка поверхности
.pdf51
многоатомных слоев адсорбанта на поверхности адсорбента. Процессы хемосорбции сопровождаются образованием химических связей между атомами адсорбанта и адсорбента. В любом случае абсорбция приводит к уменьшению поверхностной энергии и сопровождается выделением тепла, называемая теплотой адсорбции, которая тем больше, чем прочнее связь между атомами адсорбента и адсорбанта. Теплота физической адсорбции составляет 10 – 20 кДж/моль, теплота хемосорбции превышает 80кДж/моль;
3.диффузию – перемещение адсорбированных атомов в кристаллической решетке обрабатываемого металла. Диффузия происходит в направлении уменьшения концентрации адсорбированных атомов и ведет к его равномерному распределению по объему. Процесс диффузии возможен только при наличии хорошей растворимости атомов диффундирующего элемента в обраба-
тываемом металле и достаточно высокой температуре, которая обеспечивает необходимую скорость диффузии атомов.
Поверхностный слой детали после химико-термической обработки, отличающийся по химическому составу называют диффузионным слоем, а сталь с неизменившимся химическим составом называют сердцевиной.
Под общей толщиной диффузионного слоя понимают кратчайшее расстояние от поверхности насыщения до сердцевины. Эффективной толщиной диффузионного слоя называют часть общей толщины диффузионного слоя, которая определяется кратчайшим расстоянием от поверхности насыщения до мерного участка, характеризуемого установленным предельным значением базового параметра. В качестве базового параметра принимают или концентрацию диффундирующего элемента, или какой-либо структурный признак, или какой-либо показатель механических свойств, например, микротвердость. Качественной и количественной характеристикой химико-термической обработки является толщина диффузионного слоя, распределение концентрации диффундирующего элемента по толщине слоя, фазовый состав и свойства слоя. Рост толщины диффузионного слоя подчиняется следующей зависимости:
XО = k·τ0,5 |
(4.5) |
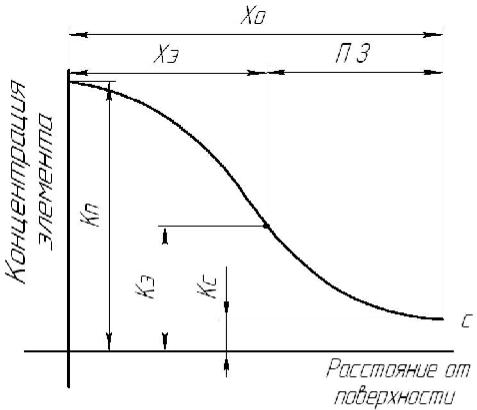
52
где XО – толщина диффузионного слоя, k – константа, зависящая от
конкретных условий проведения химико-термической обработки, τ – время обработки.
Рис.4.7. Схема диффузионного слоя. ПЗ – переходная зона, С – сердцевина, Хо – общая толщина диффузионного слоя, Хэ – эффективная толщина диффузионного слоя, Кс – концентрация элемента в сердцевине, Кп – концентрация элемента у поверхности, Кэ – концентрация элемента, установленная для эффективной толщины.
Цементация стали. Цементацией (науглераживанием) называют технологический процесс химико-термической обработки, заключающаяся в диффузионном насыщении поверхности углеродом при нагревании в соответствующей среде – карбюризаторе. Цементацию проводят при температурах аустенитного состояния стали, т.к. растворимость углерода в γ-Fe железе значительно выше, чем в α-Fe.
Цементации подвергают детали из сталей с низким содержанием углерода (15, 20) и низколегированные стали (15Х, 18ХГТ, 20ХНМ). Различают два основных вида цементации: твердая и газовая. В качестве твердого карбюризатора используют древесный уголь и активато-
ры BaCO3 или Na2CO3.
При нагреве карбюризатора до 930 – 950ºС происходит образование атомарного углерода в результате реакций:
53
2C + O2 → 2CO BaCO3 + C → BaO + 2CO
2CO → CO2 + C
Наиболее эффективна цементация при использовании в качестве карбюризатора метана (СH4) – газовая цементация.
При цементации атомарный углерод адсорбируется поверхностью детали и диффундирует в решетку γ-железа. По достижении предела растворимости углерода в γ-железе, определяемого линией SE на диаграмме Fe – Fe3С на поверхности образуется слой с концентрацией углерода ~ 1,0 – 1,2%. После завершения выдержки при температуре цементации слой насыщенный углеродом имеет переменную концентрацию углерода по толщине, убывающую от поверхности к сердцевине детали. В связи с этим в процессе медленного охлаждения и эвтектоидного превращения в структуре цементованного слоя появляются три характерные зоны: заэвтектоидная, состоящая из перлита и цементита, эвтектоидная, состоящая из пластинчатого перлита и доэвтектоидная, состоящая из перлита и феррита.
За эффективную толщину цементованного слоя принимают сумму заэвтектоидной, эвтектоидной и половины доэвтектоидной зон (до содержания углерода 0,4%), что соответствует твердости HRC 50. В зависимости от продолжительности выдержки эффективная толщина цементированного слоя составляет от 700 до 1500 мкм.
Легирующие элементы, присутствующие в стали, оказывают влияние на структуру цементованного слоя. В случае цементации сталей, легированных карбидообразующими элементами, возможно образование двухфазного слоя из легированного аустенита и карбидов легирующих элементов. После охлаждения соответственно образуются легированный феррит и карбиды. Однако на толщину цементованного слоя, легирующие элементы в том количестве, в котором они присутствуют в цементуемых сталях, практически не влияют.
Окончательные свойства цементованных деталей достигаются в результате термической обработки, выполняемой после цементации. Этой термической обработкой можно измельчить зерно сердцевины и цементированного слоя, получить требуемую высокую твердость цементированного слоя и высокий комплекс свойств сердцевины.
В большинстве случаев, особенно при обработке наследственно мелкозернистых сталей, применяют закалку при температуре 820 – 850
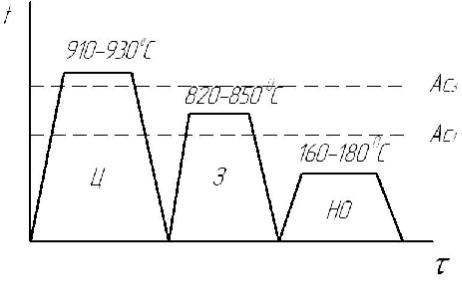
54
°С (рис.3.8). Это обеспечивает измельчение зерна и закалку цементированного слоя и перекристаллизацию и измельчение зерна сердцевины.
В результате термической обработки поверхностный слой приобретает структуру мелкоигольчатого мартенсита и изолированных участков остаточного аустенита. Большое значение имеет прокаливаемость цементованного слоя, под которым понимают способность стали образовывать структуру мартенсита с твердостью HRC 59 – 62 на заданном расстоянии от поверхности. Образование в цементованном слое карбидов легирующих элементов снижает прокаливаемость. Недопустимо образование карбидной сетки, которая резко повышает хрупкость слоя.
Рис.4.8. Схема технологического решения цементации и последующей термической обработки.
Заключительной операцией термической обработки цементованных деталей является низкий отпуск при температуре 160 – 180°C, превращающий мартенсит закалки в поверхностном слое в мартенсит отпуска и снижающий уровень остаточных напряжений.
При одинарной закалке легированных сталей в структуре в структуре цементрванного слоя сохраняется значительное количество (~50%) остаточного аустенита, который снижает твердость. Такие стали, после закалки, рекомендуется обрабатывать холодом, что позволяет превратить большую часть остаточного аустенита в мартенсит, в результате чего повышается твердость. Так, например, твердость хромоникелевой стали после цементации и закалки составляет HRC 52, а после обработки холодом повышается до HRC 60 – 62.
Цементация с последующей термической обработкой повышает предел выносливости стальных деталей и снижает чувствительность к
55
концентраторам напряжений. Так, после цементации на глубину 1000 мкм, закалки и отпуска стали 12ХН3А предел выносливости образцов без концентраторов напряжений увеличился от 560 до 750 МПа. Кроме того цементованные стальные детали обладают высокой износостойкостью и контактной прочностью.
Азотирование стали. Азотированием называют процесс диффузионного насыщения поверхностного слоя стальной детали азотом при нагреве ее до температуры 500 – 650°С в диссоциированном аммиаке.
В соответствии с диаграммой фазового равновесия Fe - N в сплавах железа с азотом при относительно небольшой концентрации азота (N<11%) образуются следующие фазы: твердый раствор азота в α- железе (α-фаза), γ´-фаза – твердый раствор на основе нитрида железа Fe4N (5,7 – 6,1 % N), ε-фаза – твердый раствор на основе нитрида желе-
за Fe3N (8 – 11,2 % N).
При температуре выше 591°C существует γ-фаза, которая представляет собой твердый раствор азота в γ-железе, которая при температуре 591°C претерпевает эвтектоидное превращение. Эвтектоид α+γ´ содержит 2,35 % N. При закалке γ-фаза испытывает мартенситное превращение γ→α´, α´ - азотистый мартенсит.
При азотировании углеродистых и низколегированных сталей структура диффузионного слоя состоит из нескольких зон в зависимости от концентрации углерода в полном соответствии диаграммой Fe – N. Азотированный слой состоит из поверхностной нитридной зоны (ε,γ´), зоны γ´-фазы и зоны α-фазы с избыточными нитридами – Fe4N или нитридами легирующих элементов. При переходе от одной зоны к другой в азотированном слое происходит резкий перепад концентрации азота, который устанавливается при температуре азотирования и сохраняется после охлаждения.
Размер кристаллов нитридов зависит от температуры азотирования. При низких температурах азотирования (~500°C) образуются кластеры из атомов азота с низкой энергией раздела, поскольку сохраняется когерентность решеток. Однако в области вокруг кластера происходит искажение и деформация решетки. При более высоких температурах (~550 °C) продолжается рост размеров кластеров и начинается образование пластинчатых нитридов толщиной 2 – 4 нм. Образование таких нитридов приводит к нарушению когерентности. Дальнейшее повышение температуры выше 550 °C сопровождается образованием более крупных нитридов (~ 20нм). Азотирование при температурах 550 – 650 °C ведет к коагуляции и сферодизации нитридов.
56
Растворение азота в железе не вызывает значительного повышения твердости. Высокой твердостью обладают лишь γ´-фаза и мартенсит α´. Наиболее высокую твердость имеет поверхность, азотирование которой осуществляется при температурах, когда образуются кластеры азота полностью когерентные с α-фазой, эффективно блокирующие движение дислокаций. Азотирование при температурах, при которых образуются достаточно крупные кристаллы нитридов, приводит к понижению твердости.
Азотированию подвергают легированные стали, содержащие Cr, V, Mo и др. элементы. Однако наибольший эффект упрочнения наблюдается при азотировании сталей содержащих алюминий: 38ХЮ, 38ХМЮА. При высоком содержании азота под слоем ε-фазы формируется область легированной алюминием γ´-фазы с высокой твердостью.
Технологический процесс азотирования состоит из следующей последовательности технологических операций.
1.Предварительная термическая обработка состоит из закалки и высокого отпуска и предназначена для получения структуры сорбит и заданного комплекса механических свойств в сердцевине изделия.
2.Механическая обработка резанием с целью получения заданной точности размеров детали.
3.Шлифование и доводка с целью получения заданной точности и шероховатости поверхности детали.
4.Нанесение защитных покрытий на участки детали, не подлежащих азотированию.
5.Азотирование при заданной температуре и заданное время с целью получения азотированного слоя заданной толщины и твер-
дости.
После такой обработки общая толщина азотированного слоя на легированных сталях составляет 200 – 500 мкм, твердость HV 1000 – 1200. Причем твердость азотированного слоя стали выше, чем цементованного и сохраняется при нагреве до температур 450 – 550 °C.
Износостойкость азотированной стали выше, чем цементованной и закаленной. В азотированном слое возникают остаточные напряжения сжатия, величина которых на поверхности составляет 600 – 800 МПа. Это повышает предел выносливости на 30 – 40 %. Однако контактная усталостная прочность у азотированной стали ниже, чем у цементованной.
Нитроцементация. Нитроцементацией называют процесс диффузионного насыщения поверхностного слоя стали одновременно углеро-
57
дом и азотом при температуре 840 – 860 °C в газовой среде, состоящей из углеродосодержащего газа и аммиака.
Эффективность нитроцементации объясняется тем, при одновременной диффузии углерода и азота скорость диффузии углерода увеличивается, что позволяет получить заданную глубину диффузионного слоя за меньшее время.
Для осуществления нитроцементации сталей используют контролируемую эндотермическую атмосферу, к которой добавляют 1,5 – 3,5 % природного газа и 1,0 – 3,5 % аммиака. Продолжительность процесс составляет 4 – 10 ч. Оптимальное суммарное содержание углерода и азота зависит от марки стали и колеблется в пределах 1,0 – 1,65 %. После нитроцементации следует закалка непосредственно из печи. После закалки проводят низкий отпуск при температуре 160 – 180 °C.
При оптимальных условиях технологического процесса нитроцементации структура диффузионного слоя состоит из мелкоигольчатого мартенсита, небольшого количества мелких равномерно распределенных карбонитридов и остаточного аустенита. Толщина нитроцементованного слоя составляет 200 – 800 мкм и не должна превышать 1000 мкм. При большей толщине слоя в нем образуются дефекты, снижающие его комплекс свойств.
Цианирование. Цианированием называют процесс диффузионного насыщения поверхностного слоя стали одновременно углеродом и азотом при температуре 820 – 950°C в расплавленных солях, содержащих группу CN.
При цианировании нагрев осуществляют в расплавах цианистых солей NaCN, KCN. В зависимости от температуры процесса различают высокотемпературное (930 – 950°C) и низкотемпературное (500-600ºС) цианирование. При низкотемпературном цианировании поверхность насыщается преимущественно азотом. Низкотемпературному цианированию обычно подвергают окончательно обработанные детали. Глубина слоя обычно составляет 0,01-0,04 мм, твердость 1000HV.
После высокотемпературного цианирования на глубину h = 0,6-0,8 мм в течении 3-10 часов требуется закалка с низким отпуском. Твердость после термообработки составляет 59-62 HRC.
Процесс цианирования по сравнению с цементацией требует меньшего времени для получения слоя заданной толщины, характеризуется меньшими деформациями деталей сложной формы, а диффузионный слой обладает высоким сопротивлением износу и коррозии.
58
Диффузионная металлизация. Диффузионной металлизацией называется процесс диффузионного насыщения поверхностных слоев стали разными металлами: кремнием, алюминием, хромом и другими.
В результате диффузионного насыщения поверхности кремнием (силицирование) повышается коррозионная стойкость, жаростойкость, твердость и сплавов. Известно, что кремний при растворении в железе обладает наибольшим твердорастворным упрочняющим эффектом. Диффузионный силицированный слой является раствором кремния в α- железе, отличается повышенной пористостью. Наибольший эффект достигается при силицировании сталей легированных Cr, Al и Ti.
Хромирование – насыщение поверхности стальных изделий хромом. Хромирование производят в вакуумных камерах при температуре 1420ºС. За 18-24 часа выдержки получают хромированный слой толщиной 2,0-2,5 мм с концентрацией Cr в поверхности до 70%. Твердость слоя составляет 1200-1300 HV. Хромирование используют для упрочнения деталей, работающих на износ в агрессивных средах.
Алитирование – процесс диффузионного насыщения поверхности изделий алюминием с целью повышения жаростойкости и коррозионной стойкости. При алитировании на поверхности образуется слой FeAl толщиной 0,2-0,5 мм. В результате алитирования сталь приобретает высокое сопротивление окислению при высоких температурах, так как при нагреве алитированных деталей на поверхности в результате взаимодействия с кислородом пленка Al2O3, предохраняющая металлы от окисления.
Борирование – насыщение поверхности металлов бором с целью повышения твердости и износостойкости. При борировании стали упрочнения достигается за счет образования боридов FeB и Fe2B толщи-
ной 100 – 200 мкм и твердостью NV 1800 – 2000.
4.3. Поверхностная закалка.
При поверхностной закалке на некоторую (заданную) глубину закаливается только поверхностный слой, тогда как сердцевина детали остается не закаленной. Назначение поверхностной закалки – повышение твердости, износостойкости и выносливости деталей. Наибольшее распространение получил метод закалки поверхности при нагреве токами высокой частоты (ТВЧ).
При нагреве ТВЧ используется явление индукции. Деталь устанавливается в индуктор, представляющий несколько витков водоохла-
59
ждаемой трубки. При пропускании через индуктор переменного электрического тока высокой частоты, создается магнитное поле, вызывающее появление в обрабатываемом изделии индуцированного тока той же частоты. Индуцированный ток вызывает нагрев поверхности детали. Толщина нагретого слоя может быть определена по формуле:
h = 4,46·105 (ρ/μf )0,5 |
(4.6) |
где ρ - удельное электросопротивление, μ - магнитная проницаемость, f - частота тока.
Глубина проникновения тока увеличивается с повышением температуры и наиболее сильно возрастает выше точки Кюри (768 °C), вследствие резкого уменьшения магнитной проницаемости при переходе стали из ферромагнитного состояния и увеличения ρ. Одновременно уменьшается скорость нагрева.
Скорость нагрева ТВЧ в зависимости от частоты составляет 50300°C/с. Глубина нагретого слоя составляет обычно 2-5 мм. Чем больше скорость нагрева, тем выше температура аустенизации. Так, например, при печном нагреве стали 45 температура закалки составляет 840860ºС, а при нагреве ТВЧ со скоростью 250 °C/с – 880 - 920ºС.
Охлаждающая среда для закалки подается через спрейер. После закалки с нагревом ТВЧ детали подвергают низкому отпуску при температуре 160-200ºС.
Структура на поверхности детали мартенсит отпуска, а в сердцевине сохраняется феррито-перлитная структура. Для улучшения механических характеристик перед закалкой ТВЧ проводят термоулучшение или нормализацию.
При поверхностной закалке значительно повышается предел выносливости. Повышение предела выносливости объясняется образованием в закаленном слое остаточных напряжений сжатия. Это особенно важно для таких деталей как оси и валы, работающих на изгиб и кручение, у которых максимальные напряжения растяжения возникают в поверхностных слоях.
Для поверхностей закалки применяют конструкционные термоулучшаемые станки 40, 45, 45Х, 40ХН и другие, которые после закалки имеют высокую твердость (HRC 50-60) и не склонны к хрупкому разрушению.
Таким образом, индукционный нагрев ТВЧ позволяет: сократить длительность термической обработки, а следовательно, увеличить производительность труда; существенно уменьшить окисление и обезугле-
60
роживание поверхности, что уменьшает величину припуска на чистовую обработку; уменьшить деформацию изделий в процессе термической обработки.
В некоторых случаях для термического упрочнения поверхности применяют нагрев поверхности с использованием лазера – квантового генератора светового диапазона. Применение лазеров для термической обработки поверхности основано на превращении световой энергии в тепловую.
Под воздействием лазерного излучения за короткий промежуток времени (10-3 – 10-7) с поверхность детали нагревается до высокой температуры. След воздействия луча лазера имеет сферическую форму и состоит из центральной оплавленной зоны и периферийной – зоны термического влияния.
Для лазерной обработки используют технологические лазеры импульсного и непрерывного действия. При импульсном излучении нагрев осуществляется в точке, при непрерывном – в полосе шириной до 3 мм. Глубина нагретого слоя при нагреве лазером непрерывного действия составляет от 0,3 до 1,0 мм, а при использовании импульсного ла-
зера 0,1-0,15 мм.
Механизм лазерной термической обработки поверхности заключается в фазовых превращениях материала после его скоростного нагрева до температур выше фазовой перекристаллизации с последующим быстрым охлаждением за счет теплопроводности материала детали. При лазерной закалке сталей зона оплавления выявляется микроструктурно в виде белого нетравящегося слоя и представляет собой очень дисперсный мартенсит очень высокой твердости. Непосредственно под белым слоем располагается слой крупноигольчатого мартесита и далее зона неполной закалки – мартенсит и феррит. При увеличении скорости луча до нескольких сотен метров в секунду белый оплавленный слой не образуется.
Лазерная термическая обработка позволяет повысить твердость и низкостойкость деталей из конструкционных и инструментальных сталей. В результате лазерной закалки без оплавления возрастает предел выносливости при изгибе и предел контактной выносливости.
4.4. Наплавка и напыление
Наплавка – это нанесение слоя расплавленного металла на оплавленную металлическую поверхность путем плавления присадочного материала теплотой кислородно-ацетиленового пламени или электри-