
Варгасов Пестов_Обработка поверхности
.pdf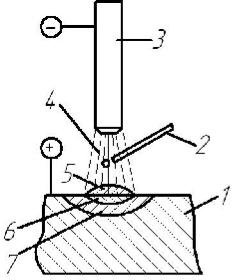
61
ческой дуги. Наплавку осуществляют для восстановления изношенных деталей и создания на поверхности детали слоя, обладающего повышенной прочностью, антикоррозионной стойкостью, жаропрочностью и другими свойствами.
Рис.4.9. Схема электродуговой наплавки. 1 - деталь; 2 – наплавочный металл; 3 – электрод; 4 – электрическая дуга; 5 – наплавленный металл; 6 – зона проплавления; 7 – зона термического влияния.
Важнейшие преимущества наплавки состоит в том, что возможно нанесение слоя большой толщины, высокая производительность процесса, относительная простота технологии. К недостатку метода относится возможная деформация изделия.
В качестве основного материала при наплавке применяют углеродистые и легированные стали разных классов. Основным требованием, которое ограничивает применение сталей, является свариваемость.
Проблема свариваемости состоит в том, что в зоне, примыкающей к наплавленному слою, происходит изменение структуры и свойств основного металла под влиянием теплоты процесса наплавки. В этой зоне, называемой зоной термического влияния, сталь имеет максимальную твердость и наибольшую чувствительность к трещинам.
Для оценки свариваемости используют показатель, называемый углеродный эквивалент. При наплавке углеродистой и низколегированной стали углеродный эквивалент используют как показатель, выражающий свариваемость. Углеродный эквивалент зависит от химического состава стали и его расчета можно воспользоваться следующим уравнением:
СЭ = C + 1/6Mn + + 1/15(Ni + Cu) + 1/5(Cr + Mo + V), |
(4.7) |
62
где в правой части указано содержание в стали химических элементов в процентах.
Свариваемость считается удовлетворительной, если СЭ ≤ 0,4. Повышение углеродного эквивалента стали сопровождается повышением твердости в зоне термического влияния. Поэтому при наплавке углеродистой и легированной сталей углеродный эквивалент служит показателем, используемым для оценки сварочных свойств основного металла, а также для выбора режима предварительного подогрева.
Изложенный подход относится к проблеме появления, так называемых, холодных трещин замедленного разрушения. Однако при наплавке в большинстве случаев проблему составляет предотвращение образования горячих трещин, механизм возникновения которых состоит в следующем. Во время кристаллизации наплавленного металла на границе зерен образуется легкоплавкая эвтектика, наличие которой на границах зерен становится причиной возникновения трещин под влиянием усадочной деформации. Для оценки чувствительности к горячим трещинам предложен показатель HCS (склонность к горячим трещинам):
HCS = [С(S+ P + Si/25 + Ni/100)/(3Mn+Cr+Mn+V)] ·103 |
(4.8) |
Условием возникновения горячих трещин при наплавке является
HCS>2.
Для осуществления наплавки применяют все известные способы сварки: газовая, электродуговая и плазменная.
При газовой наплавке используют тепло, выделяющееся при горении ацетилена, а при электродуговой тепло, выделяющееся при горении электрической дуги.
Электродуговая наплавка осуществляется различными способами: ручная, наплавка под слоем флюса, наплавка в среде защитных газов.
Электродуговая наплавка, покрытая электродами, основана на использовании электродов в виде стержней с покрытием, которое служит для защиты жидкого металла от взаимодействия с воздухом.
При дуговой наплавке покрытыми электродами или автоматической наплавке под флюсом электродное покрытие или флюс превращаются в шлак, химическое взаимодействие которого с металлом ванны обеспечивает его рафинирование. Кроме того, шлак защищает ванну от взаимодействия с воздухом. Кроме рафинирования металла и влияния
63
на формирование валика роль шлака состоит в предотвращении быстрого охлаждения наплавленного металла.
Наплавка плавящимся электродом в среде защитного газа характеризуется тем, что дуга возникает между основным металлом и электродным наплавочным материалом. В качестве защитного газа чаще всего используется аргон. С целью стабилизации дуги при наплавке стали, к аргону добавляют до 20 % углекислого газа.
Защитные газы оказывают различное влияние на легирование наплавленного металла. При наплавке низкоуглеродистой стали влияние защитного газа практически отсутствует. Содержание углерода в наплавленном металле бывает обычно несколько ниже, чем в наплавочной проволоке, вне зависимости от состава защитного газа. Между тем при наплавке аустенитной коррозионно-стойкой стали содержание углерода в наплавленном металле превышает его содержание в проволоке, причем эта разница более значительна при наплавке в CO2, чем при наплавке в смеси CO2 с аргоном.
Наплавка неплавящимися электродами в среде инертного газа характеризуется тем, что дуга, за счет теплоты которой происходит плавление наплавочного присадочного металла, возникает между основными металлом и вольфрамовым электродом. Процесс аргонодуговой наплавки протекает в условиях подачи наплавочного прутка и его плавление дугой. Применение механизированных средств подачи наплавочного материала с постоянной скоростью позволяет осуществить наплавку в автоматическом или полуавтоматическом режиме.
Плазменная наплавка включает возникновение между основным металлом и электродом горелки электрической дуги, обеспечивающей переход в плазменное состояние рабочего газа, подаваемого в зону дуги. При этом из сопла горелки истекает высокотемпературная плазменная струя, обеспечивающая плавление наплавочного металла. При наплавке этим способом две проволоки, последовательно подключенные к источнику питания переменного тока, подаются с постоянной скоростью в сварочную ванну под плазменной горелкой, где происходит их быстрое расплавление под действием теплоты плазмы в сочетании с нагревом электросопротивлением самих проволок при протекании переменного тока.
Под влиянием термического цикла наплавки в изделиях могут возникать остаточные напряжения, вызывающие деформацию и образование трещин как в основном, так и наплавленном металле и создающие угрозу разрушения конструкций в целом. В таких случаях по-
64
сле наплавки необходима обработка, обеспечивающая релаксацию остаточных напряжений.
Наиболее распространенными видами такой обработки являются отжиг для снятия напряжений, механическая релаксация напряжений и проковка.
Отжиг для снятия напряжений заключается в нагреве изделий после наплавки до заданий температуры и выдержки при температуре отжига заданное время. В зависимости от марки стали температура отжига составляет 595 – 760 ºC, а продолжительность выдержки 1 час на 25 мм толщины изделия.
Механическая релаксация напряжений состоит в том, что на изделие, имеющее внутренние остаточные напряжения, действуют постоянной нагрузкой, после снятия которой происходит релаксация напряжений.
Проковка – локальная пластическая деформация поверхностного слоя наплавленного металла специальным инструментом (молотом) с целью релаксации напряжений.
Наплавленные изделия часто подвергают последующей механической обработке для получения заданных размеров. Механическая обработка резанием сопровождается снятием слоя наплавленного металла (припуска на механическую обработку), в котором могут быть сосредоточены остаточные напряжения, и, как следствие, это приводит к деформации изделия. Поэтому изделия, которые после наплавки требуют механической обработки, следует подвергать термообработке для устранения остаточных напряжений.
Резание и шлифование оказывают определенное механическое и тепловое на обрабатываемую поверхность, что создает опасность возникновения трещин особенно в твердом и хрупком наплавленном металле либо сплаве. Поэтому механическую обработку твердого и хрупкого наплавленного материала, например стеллита, следует осуществлять так, чтобы при механической обработке возникали минимальные нагрузки.
Напыление. Напыление состоит в образовании покрытия на поверхности детали путем динамического осаждения на основном материале расплавленных капель или оплавленных частиц напыляемого материала, образующегося при нагреве порошка, расплавлении проволоки или прутка различными источниками нагрева. Широкое разнообразие способов напыления обеспечивает получение покрытий, отличающихся по своим свойствам. Технологии нанесения покрытий в зависимости от применяемого источника тепловой энергии можно разделить на три ос-
65
новных вида: газопламенное напыление, при котором используется теплота, выделяющаяся при сгорании смеси газа с кислородом; электрическое нанесение покрытий, основанное на использовании теплоты, выделяющейся при горении электрической дуги и детонационное, при котором используется энергия взрыва.
При газопламенном напылении напыляемый материал, имеющий форму прутка или проволоки, а иногда в виде порошка, подают через центральное отверстие горелки и расплавляют пламенем горящего газа. Расплавленные частицы металла подхватываются струей сжатого воздуха и в мелкораспыленном виде направляются на поверхность изделия.
Горелка с приводом позволяет точно регулировать подачу проволоки. При напылении порошком последний поступает в горелку из бункера через отверстие, разгоняется потоком газа и на выходе из сопла попадает в пламя, где происходит его нагрев и плавление.
В качестве горючего газа в большинстве случаев используют ацетилен, однако можно также применять пропан и водород.
При полном сгорании ацетилена в среде кислорода протекает следующая химическая реакция:
2C2H2 + 5O2 = 4CO2 + 2H2O + 1262,86 кДж. |
(4.9) |
В соответствие с этой реакцией, для полного сгорания на одну часть по массе ацетилена необходимо 2,5 части кислорода, однако на практике это соотношение равно 1,1. При сгорании смеси такого состава образуется нейтральное пламя, так как во время горения в него поступает кислород из окружающего воздуха.
При газопламенном напылении проволокой на расстоянии 50 – 60 мм от сопла температура пламени составляет 1500ºC; по мере дальнейшего увеличения расстояния она постепенно снижается: на расстоянии 100 мм температура составляет 500ºC. Поэтому газопламенном способе напыление осуществляют материалами с относительно низкой температурой плавления: алюминий, цинк, олово медь.
Электродуговое напыление состоит в том, что через два канала в горелке непрерывно подают две проволоки диаметром 1,5 – 3,2 мм, между концами которых возбуждается электрическая дуга и происходит расплавление проволоки. Расплавленный металл подхватывается струей сжатого воздуха или другого газа, истекающего из центрального сопла, и в мелкодисперсном виде переносится на поверхность изделия. Распыление и транспортирование расплавленного металла осуществля-
66
ется обычно сжатым воздухом, однако при напылении коррозионностойкими сталями и алюминиевыми сплавами используют азот.
Температура дуги зависит от вида транспортирующего газа, состава электродной проволоки, технологического режима и других параметров. Так при использовании металлических электродов, силе тока 280 А достигается температура 6000±200ºC. Поэтому при электродуговом напыления могут применяться практически любые электропроводящие материалы.
Основным преимуществом электродугового напыления является его высокая производительность. Кроме того, по сравнению с газопламенным напылением электрометаллизация позволяет получать более прочные покрытия, которые лучше соединяются с основой.
Технология детонационного напыления заключается в том, что в камеру водоохлаждаемого ствола установки подается кислород и ацетилен в строго определенных количествах. Затем в камеру потоком азота подается порошок напыляемого материала, например карбид вольфрама с добавлением небольшого количества металлического порошка. Газовую смесь поджигают электрической искрой и в результате взрыва смеси образуется ударная волна, которая разогревает и разгоняет частицы порошка в направлении к поверхности изделия.
Во время взрыва порошковый материал приобретает большую кинетическую энергию, так что скорость частиц на расстоянии 75 мм от среза ствола установки составляет ~820 м/с. При размещении поверхности изделия на указанном расстоянии порошок в момент столкновения с поверхностью разогревается до температуры 4000ºC. За один цикл напыления получают покрытие толщиной ~6 мм. Процесс организован таким образом, чтобы точно повторялся с частотой 3 – 4 цикла в секунду.
Высокая скорость движения частиц и их разогрев при детонационном напылении обеспечивают получение покрытия высокой плотности и прочности сцепления с основой. При этом температура основного материала остается низкой, исключающей его деформацию и иные физические изменения.
Независимо от способа напыления, процесс формирования покрытия в целом зависит от отдельных физико-химических процессов, происходящих при напылении. Для понимания этих процессов необходимо знать особенности формирования при нагреве частиц напыляемого материала, их движение от сопла горелки до поверхности детали, условия соударения с ней, структуру покрытия. На эти процессы оказывают
67
влияние следующие факторы: метод напыления, размеры и форма частиц, физико-химические свойства напыляемых материалов.
Как уже отмечалось выше, любой способ напыления предполагает движение нагретых до жидкого состояния частиц в газовой струе от среза сопла до поверхности изделия. Таким образом, движение расплавленных частиц в воздушной струе сопровождается взаимодействием их поверхности с кислородом и азотом окружающего воздуха. Частицы напыляемого металла или сплава в той или иной мере могут быть подвержены окислению, в результате чего к моменту столкновения с поверхностью основного материала на частицах образуется тонкая оксидная пленка. Так при электродуговом напылении углеродистой сталью, содержащей 0,4% углерода, в покрытии содержится 10,5% оксидов и 1,5% нитридов. Большое содержание оксидов обнаруживается при напылении покрытий из цветных металлов (Cu, Zn и др.)
Интенсивный нагрев частиц напыляемого материала приводит к изменению химического состава напыляемого материала. Например, при напылении сталью содержание углерода уменьшается в три раза, а содержание легирующих элементов, таких как Mn, Si, Cr , на 20 – 40%.
Некоторые материалы после напыления могут изменять свою структуру в результате фазовых превращений, происходящих при нагреве до высокой температуры и быстром охлаждении напыляемых частиц. Таким образом, строение как самого напыленного слоя, так и переходного слоя между основным материалом и покрытием всегда является неоднородным по составу и свойствам.
Соединение напыленного покрытия с основой осуществляется преимущественно за счет механического сцепления напыляемых частиц с выступами и впадинами на поверхности основы, образованными предварительной механической обработкой. Этот механизм адгезии покрытия иногда называют анкерным эффектом.
Кроме механического сцепления, прочность сцепления покрытия с основным материалом обеспечивается за счет ряда других механизмов, включая диффузию компонентов покрытия в основной материал, сплавление и химическое взаимодействие.
5. Защитные покрытия деталей.
При разработке конструкции изделий в машиностроительной промышленности одним из важных условий создания изделий высокого качества является правильное решение вопросов защиты отдельных де-
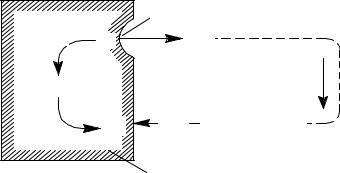
68
талей и всего изделия от коррозии, а также декоративного оформления изделия с учетом требований дизайна.
Понятие коррозии определяется как реакция взаимодействия металлического материала с окружающей средой, которая вызывает измеряемое изменение самого материала и может привести к нарушению служебных свойств металлической детали или всего изделия в целом. Реакция материала с окружающей средой могут иметь электрохимическую или химическую природу. Электрохимическая коррозия протекает только при наличии водной среды и разности потенциалов между металлом и средой. Гальванический элемент, созданный таким образом, обеспечивает появление электрического тока, протекающего между “неблагородным” электродом-анодом и благородным (катодом), который эвивалентен потере массы. Потеря массы, связанная по закону Фарадея с током, ведет к равномерной коррозии поверхности. Так плотность тока 1 мА/см соответствует, например, у железа коррозии примерно 12 мм или в год. Схема процесса электрохимической коррозии для сплавов на основе железа представлена на рис. 5.1.
|
|
3 |
|
1 |
Fe |
Fe2+ |
|
2e - |
|
|
5 |
|
H 2 |
|
|
2 |
2e- |
2H+ |
H++ OH- =H2O |
|
|
4 |
|
Рис. 5.1. Схема электрохимического коррозионного процесса в среде раствора (гальванический микроэлемент), 1 – металл, 2 – поток
электронов, 3 – анод, 4 – катод, 5 – ток.
Скорость коррозии зависит от, так называемого, электродного потенциала металла. Электродные потенциалы отсчитываются от произвольно выбранного потенциала, принятого за нулевой. Поскольку большинство электролитов содержат ионы водорода, то в качестве электрода сравнения используют нормальный водородный электрод, т.е. электрод на котором происходит реакция Н 2Н + 2е.
Электродные потенциалы некоторых металлов при температуре 25ºС представлены в таблице 5.1.
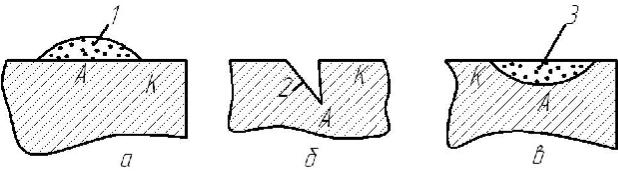
69
Таблица 5.1. Электродный потенциал некоторых металлов
металл |
Au |
Ag |
Cu |
H |
Pb |
Ni |
Fe |
Cr |
Zn |
электродный |
1,5 |
0,8 |
0,34 |
0 |
-0,13 |
-0,25 |
-0,44 |
-0,74 |
-0,76 |
потенциал, В |
|
|
|
|
|
|
|
|
|
Таким образом, напряжение, возникающее между различными металлами можно определить, сравнив соответствующие разности потенциалов.
Для электрохимической коррозии должны быть различные предпосылки. Так часто предпосылкой электрохимической коррозии является контакт разнородных металлов (контактная коррозия). Металлы с разной способностью к растворению образуют в этом случае электродную пару, т.е. анодные и катодные области. В этом коррозионном процессе более благородный металл служит катодом, а менее благородный (металл с меньшим электродным потенциалом) – анодом. Примечательно то, что такие пары возникают не только при контакте деталей, но и в случае контакта составляющих микроструктуры, например феррита и цемента в стали. Коррозионные пары могут возникать и из-за наличия напряженных участков поверхности. Обладая большей энергией, зона с внутренними напряжениями, например граница, скопления дислокаций и т.д., может играть роль анода, тогда как зона свободная от напряжений служит катодом.
Другой предпосылкой коррозии является концентрационная (щелевая) коррозия, которая возникает из-за разной концентрации электролита. Так у анода концентрация ионов металла может быть меньше чем у катода. Например, соприкасающиеся с воздухом богатые с кислородом участки металла являются катодами, тогда как участки с загруженным доступом кислорода играют роль анодов и подвергаются коррозии.
Рис.5.2.Схема концентрационных пар. А - анод; К - катод; 1- загрязнения поверхности; 2 – трещина; 3 – оксид.
Рассмотренные выше и другие механизмы коррозии ведут к различным видам коррозии: равномерной или локальной.
70
Наиболее распространенным видом коррозии является равномерная коррозия поверхности, которая возникает при равномерном распределении анодных и катодных областей по их месту расположения и величине на поверхности металла. Коррозия в этом случае часто останавливается, когда при данных условиях на поверхности металла образуется защитный слой, состоящий из продуктов коррозии, который препятствует дальнейшему доступу коррозионной среды к поверхности металла. Это явление называют пассивацией.
При образовании на поверхности относительно небольших анодных областей в каждом окружении создаются условия для локальной коррозии. Такие условия могут создаваться, например, при образовании концентрационных пар.
Одним из видов локальной коррозии является межкристаллитная коррозия (МКК), которая часто наблюдается в коррозионно-стойких сталях из-за снижения. Нестабильность границ зерен создает благоприятные условия для образования вторичных фаз, ликвации и диффузии. Следовательно, при некоторых условиях на границах зерна может снижаться концентрация тех элементов, которые способствуют повышению коррозионной стойкости, и повышается концентрация вредных примесей. В таких условиях границы зерен становятся участками преимущественного проникновения коррозии, распространение которой в глубь металла сопровождается разрушением по границам зерна.
МКК в коррозионно-стойких сталях сопровождается образованием карбида хрома (Cr23C6) по границам зерна, вследствие чего вблизи границ образуется зона пониженного содержания хрома, большая часть которого поглощается карбидом.
К числу элементов, способствующих развитию МКК аустенитной коррозионно-стойкой стали, относятся углерод, молибден, фосфор и некоторые другие.
К локальным видам коррозии можно отнести также коррозионное растрескивание под напряжением, когда образование и развитие трещин является следствием одновременного воздействия коррозионной среды и механической нагрузки. Коррозионное растрескивание под напряжением наблюдается лишь при наличии в растворе специфичных определенных для данного металла ионов и не возникает в чистых металлах.
Коррозионное растрескивание под напряжением может развиваться в двух формах, в том числе в виде межзеренных трещин и внутризеренных трещин, пересекающих зерно. При работе деталей при малой нагрузкой в среде со слабыми агрессивными свойствами возникают